In the intricate dance of mold design, the mold base sets the rhythm.
Selecting the right mold base is crucial for mold design, impacting structural integrity, thermal performance, pressure resistance, cooling efficiency, lifespan, and cost-effectiveness, much like a house foundation influences overall stability and durability.
Reflecting on my own experiences, I remember the first time I had to make this choice. The impact was far-reaching—affecting everything from the durability of the molds to the smoothness of production cycles. Understanding these nuances can empower you to make decisions that not only enhance your designs but also boost your production efficiency and product quality.
The mold base affects cooling times in mold design.True
The choice of mold base influences thermal performance, affecting cooling.
Mold base choice has no impact on manufacturing costs.False
Choosing a mold base affects structural integrity and manufacturing costs.
- 1. What Are the Types of Mold Bases Available?
- 2. How does mold base material influence durability?
- 3. How Does a Mold Base Affect Thermal Management?
- 4. How do mold base costs vary with different choices?
- 5. Can Mold Base Selection Affect Product Aesthetics?
- 6. What Should You Consider When Choosing a Mold Base?
- 7. Conclusion
What Are the Types of Mold Bases Available?
Ever wondered what makes a mold base just right for your project? Let’s dive into the world of mold bases and discover how each type can transform your manufacturing process.
Mold bases, crucial for mold manufacturing, include standard, custom, hot runner, and stripper plate types, each designed to meet specific production needs for efficient manufacturing.
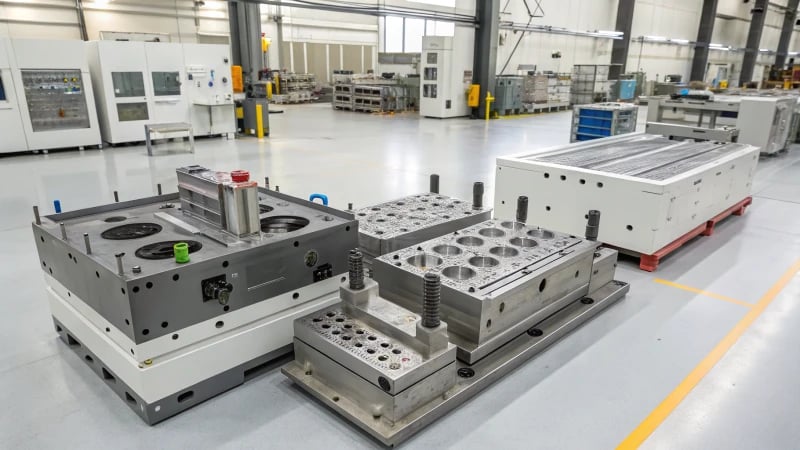
Standard Mold Bases
Let me take you back to my early days in manufacturing. I remember working on my first big project where budget constraints were a real challenge. That’s when I discovered the magic of standard mold bases. They’re like the reliable, no-frills option in the mold world—pre-fabricated, cost-effective, and readily available1. Perfect for when you need something quick and efficient without the need for fancy customizations.
Custom Mold Bases
Then there are those projects that feel like crafting a bespoke suit; they demand a personal touch. Custom mold bases are my go-to when the design requires that extra bit of flair or functionality. I get to play around with materials and designs, tailoring every aspect to the project’s unique needs. It’s like being a sculptor, chiseling out exactly what’s needed from the raw material.
Hot Runner Mold Bases
I’ll never forget the time I faced a tight deadline for an injection molding project. Enter hot runner mold bases—these are game-changers! By keeping the plastic molten until it hits the cavity, they drastically reduce waste and improve cycle times. It’s like having a fast lane on a highway; everything just moves smoother and quicker.
Stripper Plate Mold Bases
Finally, there are those delicate projects where precision is key, and that’s where stripper plate mold bases shine. I once worked on a project involving tiny, intricate parts that required careful handling during ejection. These bases provide precise ejection mechanisms that protect fragile components, ensuring nothing gets damaged in the process.
Mold Base Type | Key Features |
---|---|
Standard | Cost-effective, readily available |
Custom | Tailored design, material flexibility |
Hot Runner | Efficient cooling, reduced waste |
Stripper Plate | Precise ejection, protects intricate features |
Choosing the right mold base is like picking the right tool for the job—each has its strengths and fits different scenarios. Consider your project-specific needs2 like design complexity, production volume, and budget constraints carefully to ensure optimal performance and cost-efficiency.
Standard mold bases are ideal for unique specifications.False
Standard mold bases are used for general applications, not unique specs.
Hot runner mold bases reduce waste in injection molding.True
Hot runner systems keep plastic molten, reducing waste and increasing efficiency.
How does mold base material influence durability?
Imagine spending countless hours designing a product, only to see it fail due to mold issues. Choosing the right mold base material can make all the difference in ensuring durability and efficiency.
Mold base material affects durability by influencing mechanical strength, thermal management, and wear resistance. Selecting appropriate material enhances mold longevity and boosts production efficiency.
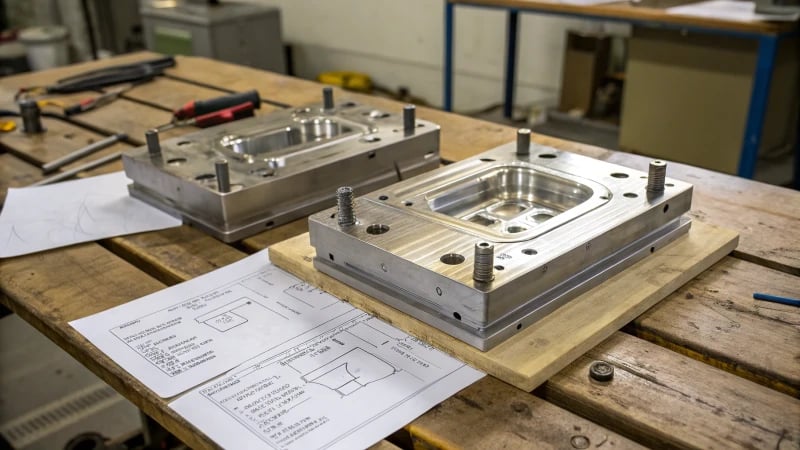
Understanding Mold Base Materials
When I first started in the world of mold design, I was fascinated by how something as seemingly simple as material choice could drastically affect a mold’s lifespan. I’ve learned that the choice of mold base material3 is indeed pivotal for durability. Steel and aluminum are common contenders, each with their own charm and challenges. Steel, with its robust nature, often wins in high-volume production runs, while aluminum shines during prototyping with its lightweight and excellent thermal conductivity.
Mechanical Properties
Back in my early days, I had a project where the wrong choice of material nearly doubled our production time. That’s when I realized how mechanical properties like hardness and tensile strength are crucial. For instance, P20 tool steel offers a sweet spot between hardness and machinability—an ideal choice when balancing durability and cost is key. Here’s a quick reference table based on what I’ve found:
Material | Hardness | Thermal Conductivity | Cost |
---|---|---|---|
P20 Steel | High | Medium | $3/kg |
H13 Steel | Very High | Low | $8/kg |
Aluminum | Low | High | $2.5/kg |
Thermal Conductivity
I remember a time when a colleague shared how switching to aluminum4 cut their cycle times significantly. It made me appreciate thermal conductivity even more; it dictates how quickly molds heat up and cool down, influencing cycle times and durability. Materials with high thermal conductivity can indeed reduce cycle times with their faster cooling capabilities.
Wear Resistance
Wear resistance is another factor that I learned the hard way. In high-pressure environments, using materials like hardened steel is non-negotiable—they keep molds intact over numerous cycles. This means less maintenance, which is always a win in my book.
Application-Specific Considerations
Different projects call for different needs, a lesson I learned designing molds for everything from rugged automotive parts to sleek consumer electronics. For instance, automotive components demand hard steels to withstand tough conditions. In contrast, lightweight materials5 excel in consumer electronics, where precision and reduced weight matter more.
In conclusion, understanding these factors helps designers like me—and perhaps you too—in choosing materials that strike the right balance between cost and durability, ultimately optimizing the manufacturing process.
Steel molds offer superior wear resistance over aluminum.True
Steel is known for its strength and wear resistance, making it ideal for high-volume production.
Aluminum molds have higher thermal conductivity than steel molds.True
Aluminum's high thermal conductivity allows for faster heating and cooling cycles.
How Does a Mold Base Affect Thermal Management?
Ever wondered how a simple mold base can make or break your injection molding process?
Mold bases enhance thermal management in injection molding by promoting efficient heat transfer and cooling, ensuring even temperature distribution to reduce cycle times and improve product quality.
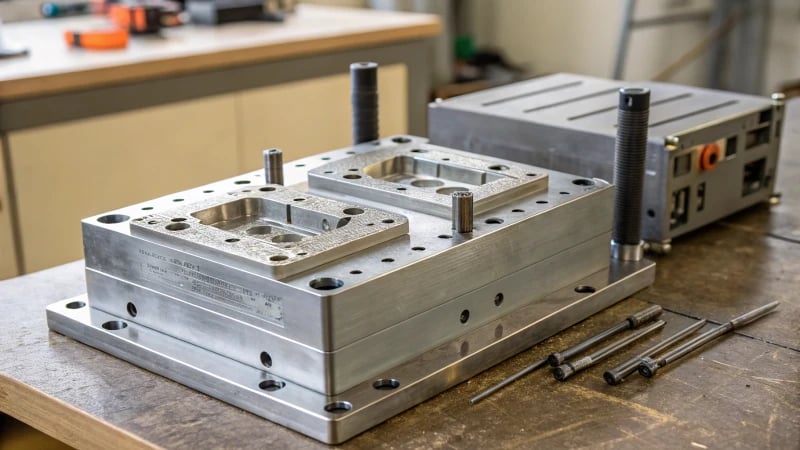
Understanding Mold Base Functionality
When I first started in the industry, I didn’t realize just how pivotal mold bases were. They’re not just the backbone holding everything together—they’re essential for keeping things cool and running smoothly. The mold base ensures a consistent temperature across the board, which is key to avoiding stress and defects in our end products. Imagine trying to bake a cake in an oven that heats unevenly—it’s a recipe for disaster!
Importance of Heat Transfer
Speaking of baking, I remember trying to bake cookies without evenly distributing the dough on the tray—they came out uneven and some were burnt! Similarly, the right material and design for a mold base ensure optimal heat transfer. Choosing materials like aluminum alloys6 can significantly improve cooling efficiency, much like using a good baking sheet ensures evenly baked cookies.
Material | Thermal Conductivity (W/mK) | Cost |
---|---|---|
Aluminum | 205 | $2.5/kg |
Steel | 50 | $1.5/kg |
Copper | 401 | $8/kg |
Cooling Channels Design
I’ve learned that designing strategic cooling channels is like installing efficient plumbing in a house. These channels allow coolant to flow seamlessly, dissipating heat quickly and evenly. It’s this meticulous design that prevents hotspots and keeps everything working like a well-oiled machine.
Impact on Product Quality
With all these factors in play, a well-thought-out mold base can ensure even temperature distribution throughout the process. This uniformity helps maintain the accuracy and quality of the final product, much like ensuring your paintbrush strokes are even when painting a masterpiece. Avoiding defects like warping or sink marks is just as crucial as preventing drips or smudges on your canvas.
Understanding these aspects allows us to tweak our designs for better thermal management, ultimately leading to superior product quality and efficiency. For those looking to delve deeper into cooling strategies7, exploring advanced techniques is a must.
Mold bases reduce cycle times in injection molding.True
Efficient heat transfer through mold bases enhances cooling, reducing cycle times.
Steel has higher thermal conductivity than aluminum.False
Aluminum has higher thermal conductivity (205 W/mK) than steel (50 W/mK).
How do mold base costs vary with different choices?
Choosing a mold base is like picking the perfect partner for your project—it can make or break your budget!
Mold base costs vary by material, size, and complexity. Pre-made bases are cheaper, whereas custom bases, designed for specific requirements, are more expensive.
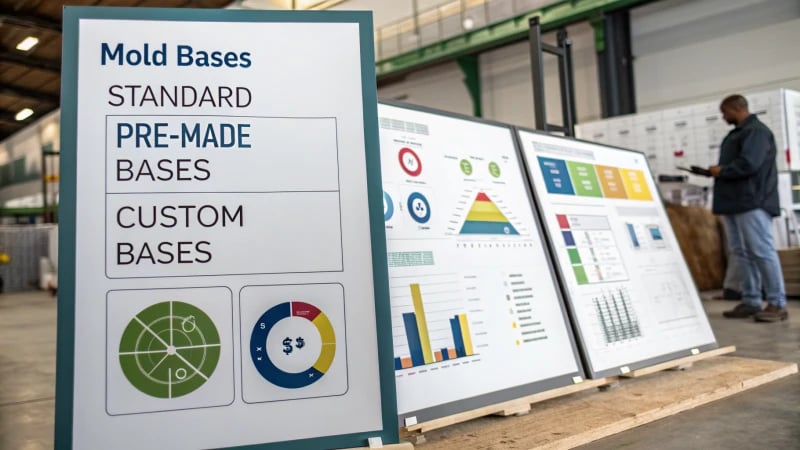
Key Factors Influencing Mold Base Costs
-
Material Selection: I remember my first big project where I had to choose between steel and aluminum8. Steel was a reliable choice with its durability and resistance, but aluminum tempted me with faster cooling times, which could speed up production. It’s a tough choice, often guided by your project’s specific needs.
Material Cost Durability Cooling Time Steel High Excellent Moderate Aluminum Moderate Good Fast -
Standard vs. Custom Bases: I once thought about taking the standard route to save costs, but for a complex design9, the custom base was the only way to go. It was more expensive, but the tailored fit made it worthwhile.
-
Size and Complexity: When I had to work on a large project, I learned that bigger isn’t always better—it’s more expensive! More material and intricate machining drove up costs, so precision became my best friend in keeping things efficient.
-
Manufacturing Process: CNC machining is the norm in my world, but boy, can it get pricey with intricate designs! Balancing complexity and cost is always a juggling act.
-
Supplier Relationships: Over the years, building good rapport with suppliers has saved me not just dollars but headaches too. Getting multiple quotes is a must—it’s surprising how much you can save!
-
Geographical Factors: Working in Canada, I’ve noticed that proximity to suppliers affects logistics significantly. Shipping those hefty mold bases isn’t cheap, so I always factor in regional pricing variations.
In my experience, choosing the right mold base is a strategic decision that influences both upfront costs and long-term production efficiency. Exploring your options carefully ensures you optimize your budget without skimping on quality.
Steel mold bases are more expensive than aluminum ones.True
Steel is durable and wear-resistant, increasing its cost compared to aluminum.
Custom mold bases are cheaper than standard ones.False
Custom bases are pricier due to tailored specifications for complex designs.
Can Mold Base Selection Affect Product Aesthetics?
Ever wondered how the right mold base can transform your product’s look? It’s like choosing the perfect canvas for a masterpiece.
Mold base selection significantly impacts product aesthetics, influencing surface finish, texture, and appearance, thus affecting consumer perception and product appeal.
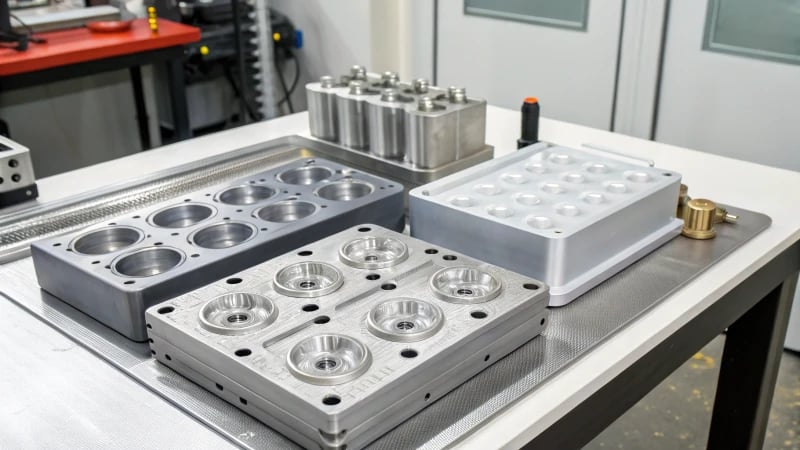
The Importance of Material Choice
Choosing the right material for the mold base is like picking the right fabric for a designer dress—it’s all about the finish! When I started in this industry, I quickly learned that materials like P20 steel and aluminum don’t just change how a product cools; they dictate its entire look. Imagine trying to achieve a sleek, glossy finish with a material that just won’t cooperate. The differences in thermal properties can lead to subtle but significant variations in texture.
Material | Surface Finish | Cost |
---|---|---|
P20 Steel | Smooth | Moderate |
Aluminum | Matte | Low |
Stainless Steel | Glossy | High |
Precision and Tolerance
I remember the first time I understood the true meaning of precision in mold making—it was like seeing the world through a new lens. A mold with tight tolerances isn’t just a technical achievement; it’s the difference between a product that meets design expectations and one that doesn’t. Especially in high-stakes industries like electronics10, where every curve and contour counts, precision ensures consistency and visual appeal.
Impact on Texture
Textures can make or break a product’s aesthetic. I always picture it as the final touch an artist adds to a painting. If the mold base can’t hold intricate textures, then you’re left with a product that feels unfinished. A high-quality steel mold can capture these details beautifully, much more so than softer materials like aluminum. In my experience with consumer electronics, achieving that premium feel often hinges on these tiny details.
Considerations for Large-Scale Production
The thrill of watching a production line churn out hundreds of parts can quickly fade if those parts aren’t consistent in quality. Here, the durability of the mold base is your best friend. A robust base not only maintains consistency across batches but also cuts down on maintenance woes. I’ve seen how investing in high-grade materials upfront saves headaches later by reducing defects and ensuring each product looks its best.
In essence, selecting the right mold base isn’t just about technical specs; it’s about crafting an aesthetic experience that resonates with consumers. Understanding these dynamics empowers designers like me to make choices that not only enhance product appeal but also keep us competitive in a crowded market.
P20 steel mold base results in a smooth surface finish.True
P20 steel's thermal properties facilitate a smooth surface finish.
Aluminum molds are more durable than stainless steel.False
Stainless steel is more durable than aluminum, especially in molds.
What Should You Consider When Choosing a Mold Base?
Picking the right mold base is like choosing the perfect partner for your project—it affects everything from efficiency to final product quality. Let’s dive into what really matters.
When selecting a mold base, consider material compatibility, thermal conductivity, size, complexity, and budget to ensure efficient and high-quality injection molding.
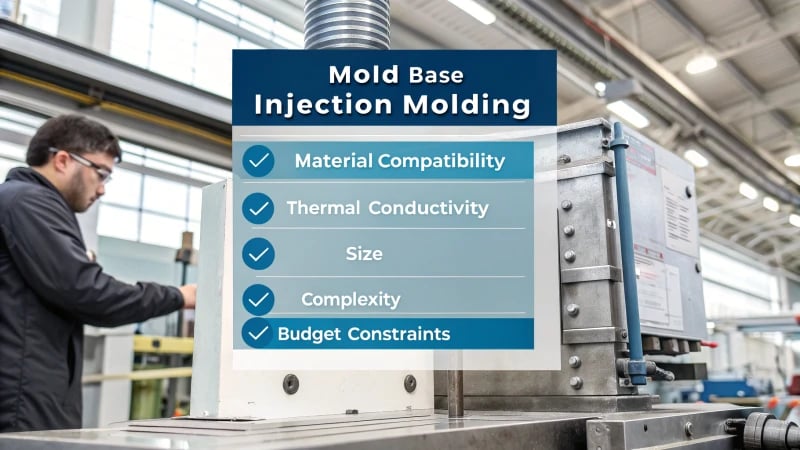
Material Compatibility
I remember my early days in mold design when I faced the challenge of picking between steel and aluminum bases. Steel was tough and could handle high volumes, which was tempting. But then I had a project that required delicate detailing—a classic case where aluminum’s flexibility saved the day.
Material | Advantages | Disadvantages |
---|---|---|
Steel | Durable, High strength | Heavy, Expensive |
Aluminum | Lightweight, Cost-effective | Less durable, Lower strength |
Thermal Conductivity
The thermal properties of your mold base can make or break your production schedule. I once worked with beryllium copper molds11, and the rapid heating and cooling cycles were game changers in meeting tight deadlines.
Size and Complexity
I learned a valuable lesson when a project overshot its budget due to an oversized mold base. Bigger isn’t always better; it’s crucial to align the size and complexity with your project’s needs.
Budget Constraints
Balancing quality with cost is a constant juggle. I’ve found that using cost analysis tools12 helps in making those tough decisions between premium materials and budget limitations.
Additional Considerations
- Precision Requirements: High precision molds need tighter tolerances.
- Supplier Reputation: Trustworthy suppliers ensure consistent quality.
- Maintenance Needs: Consider ease of maintenance for longevity.
Weaving these considerations into your decision-making process will help you select a mold base that fits your specific needs and goals. For more insights and best practices, explore various industry resources13.
Steel mold bases are ideal for intricate designs.False
Steel is durable but not as flexible as aluminum for intricate designs.
High thermal conductivity reduces mold cycle times.True
Materials like beryllium copper quicken heating/cooling cycles, boosting efficiency.
Conclusion
Choosing the right mold base is crucial for mold design, impacting durability, thermal performance, cost efficiency, and product quality in manufacturing processes.
-
Explore this link to understand why standard mold bases are a popular choice for cost-effective and quick projects. ↩
-
This link provides insights on evaluating project-specific needs to select the appropriate mold base type. ↩
-
Discover which materials provide the best balance of cost, strength, and thermal properties for durable mold bases. ↩
-
Explore why aluminum’s high thermal conductivity can lead to faster cycle times and increased production efficiency. ↩
-
Learn why lightweight materials are advantageous for precision molds in consumer electronics manufacturing. ↩
-
Discover which materials offer superior heat transfer capabilities for mold bases. ↩
-
Learn about innovative cooling strategies to enhance thermal management in molds. ↩
-
Explore different materials used in mold bases and their cost implications to make an informed decision. ↩
-
Learn how custom mold bases can enhance complex designs despite higher costs. ↩
-
Understand why visual appeal is critical in consumer electronics and how it influences market success. ↩
-
Discover why beryllium copper is preferred for its thermal properties in molds, enhancing efficiency. ↩
-
Learn about tools that assist in cost analysis for choosing mold materials and bases effectively. ↩
-
Access detailed resources and articles that offer deeper insights into best practices for mold base selection. ↩