I remember the first time I saw a perfectly polished mold; it was like staring into a shiny new world.
Mirror polishing in injection molds improves product aesthetics and quality by creating smooth surfaces that minimize friction and defects, essential for high-gloss, clear, or precise components in electronics, automotive, and medical devices.
When I dove deeper into the art of mirror polishing, I realized it’s not just about the shine. Imagine crafting a smartphone case where every reflection is crystal clear, or an automotive part that fits seamlessly without a hitch. The applications are vast, and so are the techniques. I had to master everything from understanding abrasive types to controlling polishing speeds. Knowing these intricacies not only boosted my confidence but also my designs’ reliability. If you’re looking to elevate your mold-making skills, understanding these nuances can be a game-changer.
Mirror polishing reduces friction in injection molds.True
Ultra-smooth surfaces from mirror polishing minimize friction.
Mirror polishing is unnecessary for automotive parts.False
It is essential for high-gloss, precise automotive components.
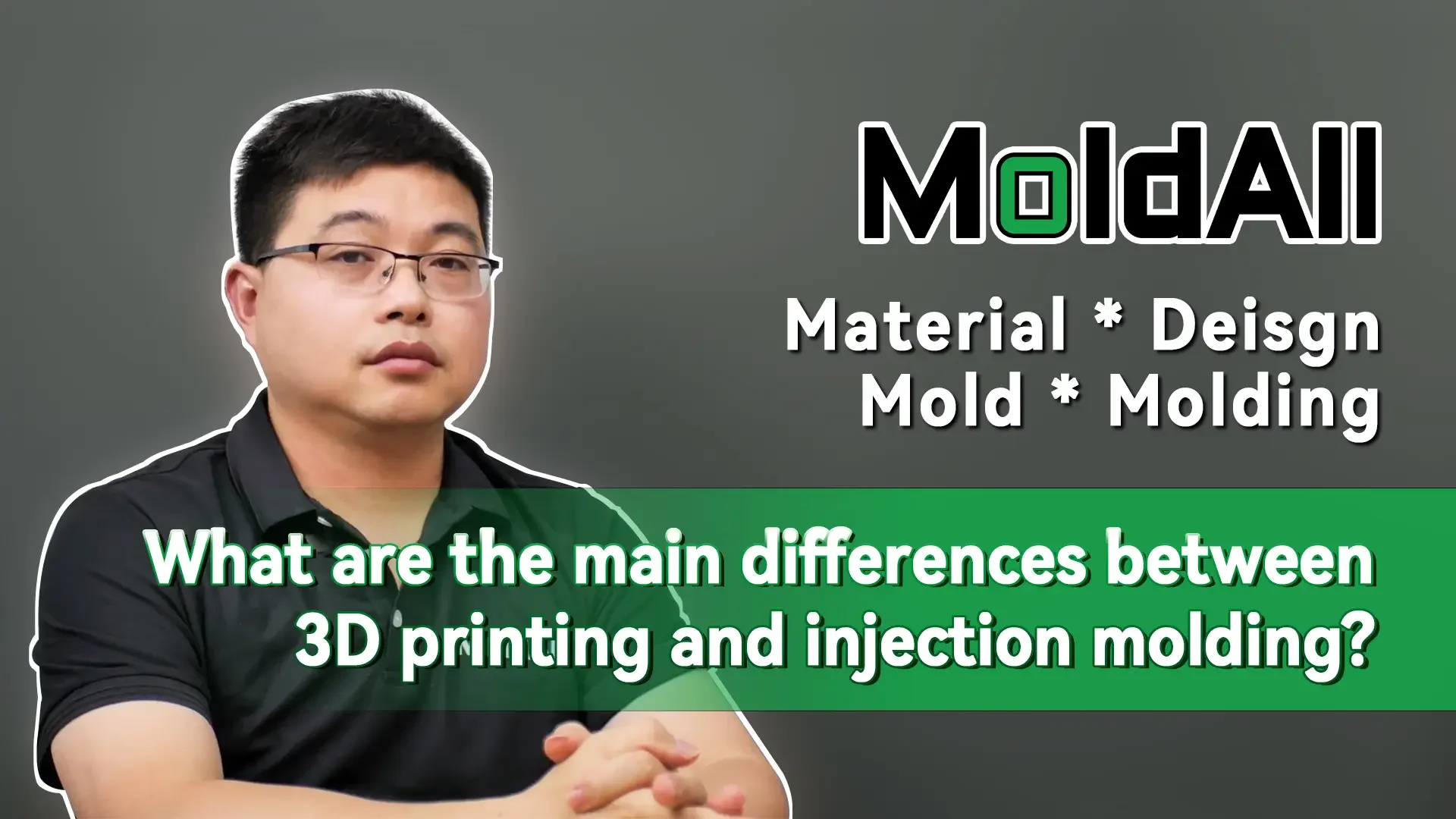
- 1. How Does Mirror Polishing Impact Product Quality?
- 2. What Are the Must-Have Tools for Achieving a Mirror Polish?
- 3. Which Industries Benefit Most from Mirror Polishing?
- 4. How can you achieve optimal surface finish standards?
- 5. What Challenges Are Commonly Faced in Mirror Polishing?
- 6. Conclusion
How Does Mirror Polishing Impact Product Quality?
Imagine taking a product from ordinary to extraordinary with just the right finishing touch. That’s where mirror polishing works its magic, transforming surfaces into something truly captivating.
Mirror polishing enhances product quality by providing a smooth, reflective finish, improving visual appeal, functionality, and longevity, crucial for premium goods and precise mechanical parts.
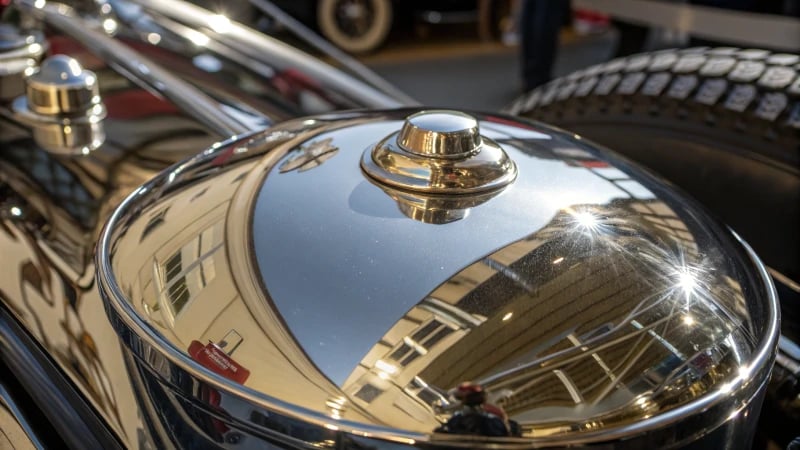
The Role of Aesthetics in Product Quality
I remember the first time I held a mirror-polished gadget in my hands—it was like holding a piece of art. Mirror polishing dramatically elevates a product’s visual appeal. A perfect, gleaming finish not only draws in consumers but also makes them feel like they’re getting something of higher value. Especially in industries like consumer electronics, where how a product looks can make or break a sale, a polished surface creates that premium impression everyone craves.
Moreover, achieving that flawless finish isn’t just about beauty; it’s about precision. Mirror polishing smooths out any surface irregularities, giving products a sleek, modern look that’s hard to resist.
Feature | Impact on Quality |
---|---|
Smooth Finish | Reduces surface defects |
High Reflectivity | Enhances visual appeal |
Functional Benefits of Mirror Polishing
There’s more to mirror polishing than meets the eye—it’s not just about looks. I once worked on a project where reducing friction was crucial, and mirror polishing came to the rescue. This technique is vital for mechanical components, as less friction means less wear and tear, extending a product’s life. For example, in mold design, polished surfaces make it easier to release molded parts, boosting production efficiency.
Benefit | Example Application |
---|---|
Reduced Friction | Precision gears in machinery |
Corrosion Resistance | Marine components |
Durability and Resistance Enhancement
The durability factor can’t be overstated. I’ve seen firsthand how polishing can make materials more resistant to corrosion and contamination—critical for industries using metals like stainless steel in harsh environments. The smooth surface prevents particles from sticking around, which means products last longer.
Considerations for Implementing Mirror Polishing
But let’s be real—mirror polishing isn’t always a breeze. It takes time, effort, and sometimes a bit more cash to get it right. I’ve had to weigh these factors carefully against the potential quality improvements more than once.
Getting mirror polishing just right demands precision and expertise. Choosing the correct technique and equipment is crucial to achieving the results you want. Checking out industry standards and best practices is always a good move when diving into this process.
For more about techniques and best practices, explore resources on surface finishes1.
Mirror polishing enhances product visual appeal.True
Mirror polishing creates a shiny, smooth finish that increases consumer interest.
Mirror polishing increases product corrosion susceptibility.False
Polishing actually reduces corrosion by creating a smoother, less porous surface.
What Are the Must-Have Tools for Achieving a Mirror Polish?
Remember the thrill of seeing your own reflection on a freshly polished surface? That glossy finish is more than just eye-catching—it’s a testament to craftsmanship.
Achieving a mirror-like polish requires grit sandpapers, polishing compounds, buffing wheels, and rotary tools, essential for transforming metal surfaces into reflective finishes.
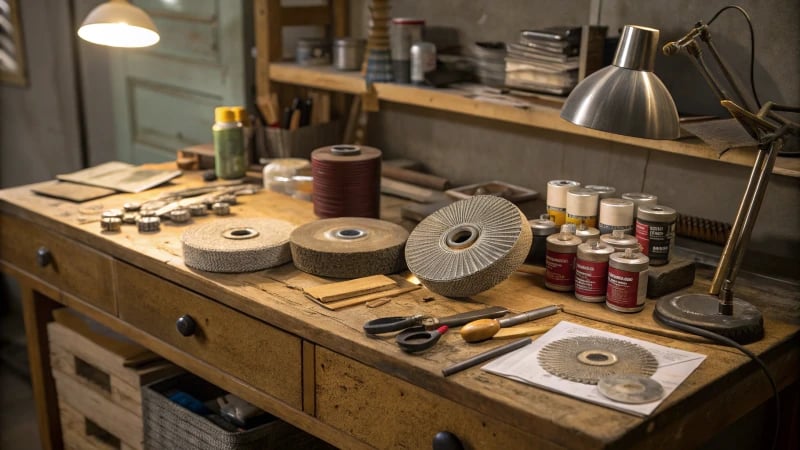
Understanding the Basics of Mirror Polishing
Mirror polishing isn’t just a skill; it’s an art form that I’ve grown to appreciate over the years. It involves moving through stages from coarse sanding to that final, brilliant sheen. Each step has its own set of tools that are critical to getting that perfect finish.
Must-Have Tools for Mirror Polishing
1. Sandpapers and Abrasive Pads
My journey into the world of mirror polishing began with the humble sandpaper. Starting with coarser grits like 400, I learned to gradually shift to finer ones, such as 2000. This progression is crucial for preparing the surface for the high polish. Abrasive pads also saved my day when working around those tricky corners.
Grit Type | Usage Stage |
---|---|
400 | Initial |
800 | Intermediate |
2000 | Final |
2. Polishing Compounds
Diving deeper into polishing, I discovered the magic of different compounds. While coarse ones helped in eradicating scratches, finer compounds brought out that spectacular shine. Consider using a rouge compound2 for that ultimate glossy finish.
3. Buffing Wheels and Pads
When it came to applying these compounds, buffing wheels were my best friends. Depending on what I was working with, I’d pick wool wheels for metals to get that smooth, mirror-like surface.
4. Rotary Tools
Rotary tools are the unsung heroes in my toolkit, equipped with attachments like felt tips and brushes. They offer precision in applying pressure and reaching those intricate spots.
Advanced Techniques and Considerations
Mastering mirror polishing is not solely about having the right tools; it’s about technique too. Maintaining consistent pressure and using the correct angles made all the difference for me—consider proper angle application3. Plus, never underestimate the power of safety gear—it’s a non-negotiable part of my routine when using rotary tools.
The subtle mastery of each tool and technique dramatically influences the quality of your mirror finish. I’d recommend dabbling in advanced techniques or testing different materials to see how they respond to these polishing methods.
Additional Tips
- A clean workspace can prevent debris from ruining your hard work.
- Keep a checklist of your tools and compounds—it makes the process much smoother.
- Regular maintenance of your equipment isn’t just smart; it’s essential for keeping everything in top shape.
Getting that perfect mirror polish is like crafting a masterpiece with your own hands. With patience and practice, anyone can achieve results that rival professional standards.
Sandpapers are used only in the final stage of polishing.False
Sandpapers are used in multiple stages, starting from coarse to fine grits.
Rouge compounds are used for a high-gloss finish.True
Rouge compounds are indeed used to enhance the shine in the final stage.
Which Industries Benefit Most from Mirror Polishing?
Ever wondered why some products just seem to shine brighter and last longer? Mirror polishing might be the secret ingredient.
Industries such as automotive, aerospace, medical, and consumer electronics benefit from mirror polishing, enhancing product aesthetics, functionality, durability, and reducing friction.
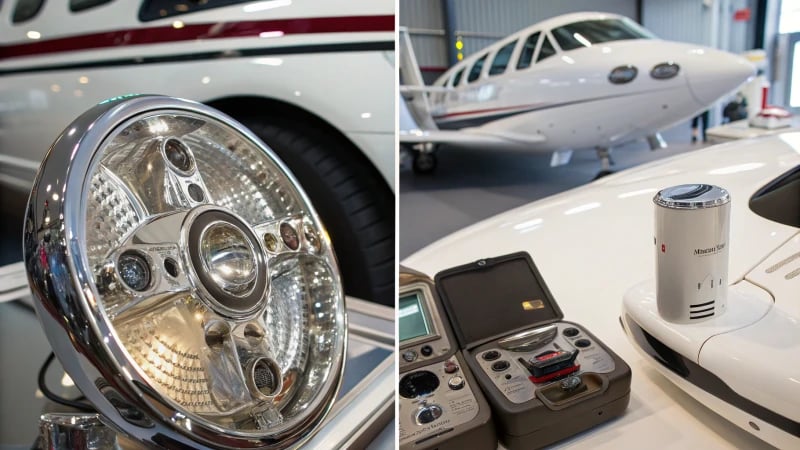
Automotive Industry
I remember the first time I realized the magic of mirror polishing in the automotive world. I was at a car show, and there was this sleek sports car with polished wheels that seemed to capture everyone’s attention. It wasn’t just about looking good; those polished surfaces reduced aerodynamic drag, boosting fuel efficiency. Plus, the polished components like wheels and engine parts4 were built to resist corrosion, which is key for any car’s lifespan.
A table showcasing the benefits of mirror polishing in automotive applications:
Benefit | Application |
---|---|
Aerodynamic Gains | Body Panels |
Corrosion Resistance | Wheels & Exhausts |
Enhanced Aesthetics | Interior Trim |
Aerospace Industry
In my time working with some aerospace components, I learned how crucial mirror polishing is for aircraft. Those jet engines with polished surfaces? They’re not just pretty to look at—they help reduce friction and wear. That means longer service intervals and better efficiency. And when it comes to precision, mirror-polished lenses in optics systems5 are non-negotiable for clarity.
Medical Industry
I’ve always found the medical applications of mirror polishing fascinating. Imagine a surgeon holding a scalpel that’s as smooth as glass—ensuring sterility and ease of cleaning. That’s critical to reducing infection risks during surgery. Similarly, implants such as joint replacements6 are mirror-polished to ensure they glide smoothly within the body.
Consumer Electronics
Every time I pick up my smartphone, I appreciate the smooth, polished finish that not only feels good in my hand but also stands up to daily wear and tear. In consumer electronics, this isn’t just about aesthetics. Polished casings and internal components ensure sleek design and smooth operation.
Table: Mirror Polishing in Electronics
Component | Purpose |
---|---|
Outer Casing | Aesthetics & Durability |
Internal Parts | Smooth Operation |
Display Edges | Enhanced Visual Appeal |
Beyond these industries, mirror polishing finds its way into countless applications, each uniquely benefiting from this versatile technique that marries beauty with function.
Mirror polishing reduces aerodynamic drag in vehicles.True
Polished surfaces reduce drag, improving fuel efficiency in vehicles.
Mirror polishing is not used in the medical industry.False
Mirror polishing ensures sterility and smoothness in surgical instruments.
How can you achieve optimal surface finish standards?
Ever stared at a glossy gadget and wondered how it got that flawless finish? Let me take you on a journey where precision meets art in achieving top-notch surface finishes in manufacturing.
To achieve optimal surface finish standards, use the right machining tools and materials, adjust settings, and consistently monitor the production process to meet desired quality benchmarks.
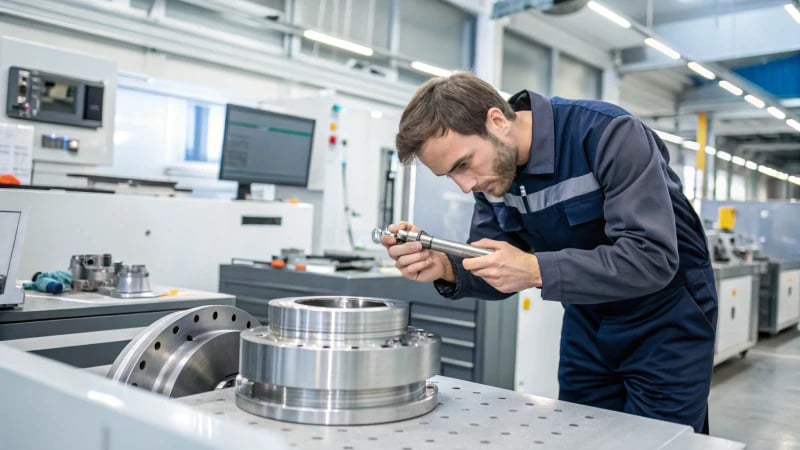
Understanding Surface Finish Parameters
When I first started in the manufacturing world, the concept of surface finish was like a foreign language. But soon, I realized that these parameters — roughness, waviness, and lay — were crucial. Roughness, for instance, refers to those tiny bumps and valleys on a surface that you might not notice with the naked eye but are critical in our line of work. Measuring these in Ra (average roughness) or Rz helped me understand the textures we were dealing with.
- Roughness (Ra): Think of this as the average deviation of the surface from perfection.
- Waviness: These are larger deviations, like gentle waves across the surface.
- Lay: The direction of the predominant pattern on the surface.
Selecting the Right Tools
In my journey, selecting the right tools has been a game-changer. High-quality cutting tools with suitable coatings make all the difference. Whether it’s high-speed steel or carbide tips, ensuring these tools are sharp and well-maintained is key to avoiding unwanted marks on the material. I’ve learned this the hard way—trust me, nothing’s more frustrating than seeing a project marred by improper tooling.
Tool Type | Material Use | Advantages |
---|---|---|
High-Speed Steel | General use | Affordable, versatile |
Carbide | Harder metals | Durable, heat-resistant |
Diamond-Coated | Abrasive tasks | Superior finish, long-lasting |
Optimizing Machining Parameters
Adjusting machining parameters like speed, feed rate, and depth of cut can be like fine-tuning an instrument. I’ve spent countless hours getting this balance just right to avoid excessive tool pressure which can lead to surface irregularities. Regularly monitoring and adjusting these settings ensures that we maintain optimal conditions. Check out machining parameter guidelines7 for more insights.
Material Considerations
Different materials have different personalities. Softer ones like aluminum demand a gentler approach compared to tougher alloys. Selecting the right material for your project’s desired finish and function is crucial. Don’t forget to consider thermal properties too; they can seriously impact surface quality during machining.
Incorporating Quality Control
Implementing robust quality control measures was one of my best moves. Utilizing precision instruments like profilometers or optical microscopes to regularly check surface roughness helps keep everything in check. Recording and analyzing this data can highlight trends or areas for improvement.
Employing methods such as Statistical Process Control (SPC techniques8) has allowed me to maintain process stability and product quality over time.
By diving into these strategies, I’ve been able to meet both aesthetic and functional demands consistently in manufacturing environments. It’s a blend of science and art, one that keeps me engaged and always striving for perfection.
Roughness is measured in Ra and Rz units.True
Ra and Rz are standard units for measuring surface roughness.
Diamond-coated tools are ideal for general use.False
Diamond-coated tools are best for abrasive tasks, not general use.
What Challenges Are Commonly Faced in Mirror Polishing?
Ever tried to get that perfect mirror finish only to feel like you’re chasing a mirage? I’ve been there, and let me tell you, it’s no walk in the park.
Mirror polishing faces challenges such as surface imperfections, material quirks, and equipment issues, which require appropriate abrasives, precise temperature control, and consistent pressure for effective resolution.
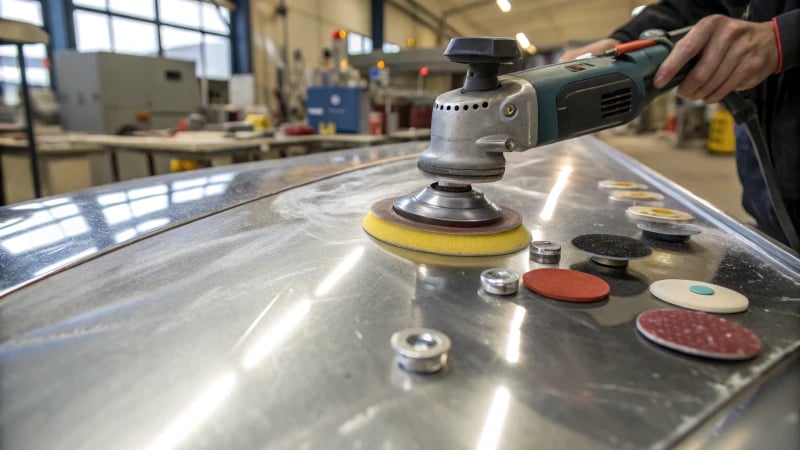
Surface Imperfections
Surface imperfections are a major hurdle in mirror polishing. I remember my first big project—an important prototype where the mirror finish was crucial. These pesky surface imperfections like scratches and pits crept in, ruining the aesthetic quality. To tackle these, it’s essential to use progressively finer abrasives and ensure meticulous surface preparation. Consistent pressure9 throughout the process helps prevent new imperfections from forming.
Material Properties
Every material has its own personality, if you will. Different materials pose unique challenges. For instance, soft metals like aluminum are easily scratched due to their softness, while harder ones like stainless steel demand more force due to their hardness. I once spent an entire weekend trying to polish a piece of glass, only to realize I hadn’t accounted for its brittleness and sensitivity to temperature.
Understanding the unique properties of each material—hardness, thermal conductivity—is critical. This knowledge allows you to select suitable abrasives and tailor your approach for each project.
Material | Challenges |
---|---|
Aluminum | Easily scratched, soft |
Stainless Steel | Hard, requires more force |
Glass | Brittle, temperature-sensitive |
Equipment Limitations
The tools of our trade can be our best friends or worst enemies. Polishing equipment must be well-maintained and suited for the task at hand. I once had an old polishing pad that wore unevenly—ruined a whole batch before I caught on! Issues like uneven pad wear or inadequate speed settings can hinder the process. Regular maintenance and selecting equipment with adjustable features can alleviate some of these equipment limitations10.
Temperature Control
Temperature control is another tricky beast during polishing as fluctuations can lead to thermal expansion or contraction, resulting in warping or stress on the material. I’ve learned through some trial and error (and a few warped pieces) that keeping a close eye on temperature is crucial.
Consistently monitoring temperature and using cooling methods such as water or air jets has saved me countless headaches by mitigating these effects.
Cooling methods11 are commonly employed in industrial settings.
Operator Skill
Finally, I can’t overstate how crucial skill is in this game. The operator’s skill level plays a significant role; even with perfect tools and materials, a lack of experience can lead to subpar results. Investing time in specialized courses paid off tenfold in mastering techniques like pressure application and speed control.
Training and practice are vital for mastering these techniques effectively.
Soft metals are more prone to scratches in polishing.True
Soft metals like aluminum are easily scratched, requiring careful handling.
Temperature control is unnecessary in mirror polishing.False
Temperature fluctuations can cause warping; control is essential for quality.
Conclusion
Mirror polishing enhances aesthetics and functionality in injection molds, crucial for industries like automotive and electronics, by providing smooth surfaces that reduce friction and improve durability.
- Discover various surface finishing methods to optimize product quality and functionality. ↩
- Find out which rouge compounds are recommended by professionals for achieving superior shine on metal surfaces. ↩
- Learn about the optimal angles for using rotary tools to maintain even pressure and avoid surface damage. ↩
- Discover how mirror polishing improves engine efficiency and longevity by reducing friction and corrosion. ↩
- Learn about the role of polished surfaces in enhancing optical precision and performance in aerospace applications. ↩
- Explore how mirror polishing reduces friction in medical implants, improving patient comfort and implant lifespan. ↩
- Provides detailed guidelines for selecting appropriate machining parameters based on material type, helping enhance surface finish quality. ↩
- Explains how SPC techniques can be used to maintain consistent quality and improve surface finish during production processes. ↩
- This link explores how consistent pressure can improve polishing outcomes and minimize surface imperfections. ↩
- Learn about common equipment issues in polishing and how to select the right tools for your project. ↩
- Discover effective cooling methods to maintain ideal temperatures during the polishing process. ↩