The world of medical devices is a high-stakes arena where precision meets compassion.
Medical injection molded products must meet strict requirements such as material safety, biocompatibility, high precision, hygiene standards, and robust physical properties. Challenges include complex molding processes, quality control, and navigating regulatory landscapes.
Understanding these requirements is just the beginning; let’s unravel the deeper complexities that shape these vital products.
Material safety ensures no harm to human tissues.True
Medical materials must be stable and non-reactive to prevent harm.
- 1. How Do Material Safety and Biocompatibility Impact Medical Injection Molding?
- 2. What Role Does Product Precision Play in Medical Device Manufacturing?
- 3. Why Are Hygiene Standards Crucial for Medical Injection Molded Products?
- 4. How Do Regulatory Changes Affect the Injection Molding Process in Healthcare?
- 5. Conclusion
How Do Material Safety and Biocompatibility Impact Medical Injection Molding?
Material safety and biocompatibility are crucial in medical injection molding, affecting patient safety and product effectiveness.
Material safety ensures that medical injection molded products are chemically stable and do not harm human tissues, while biocompatibility guarantees that these materials do not provoke adverse reactions, making them essential for safe and effective medical devices.
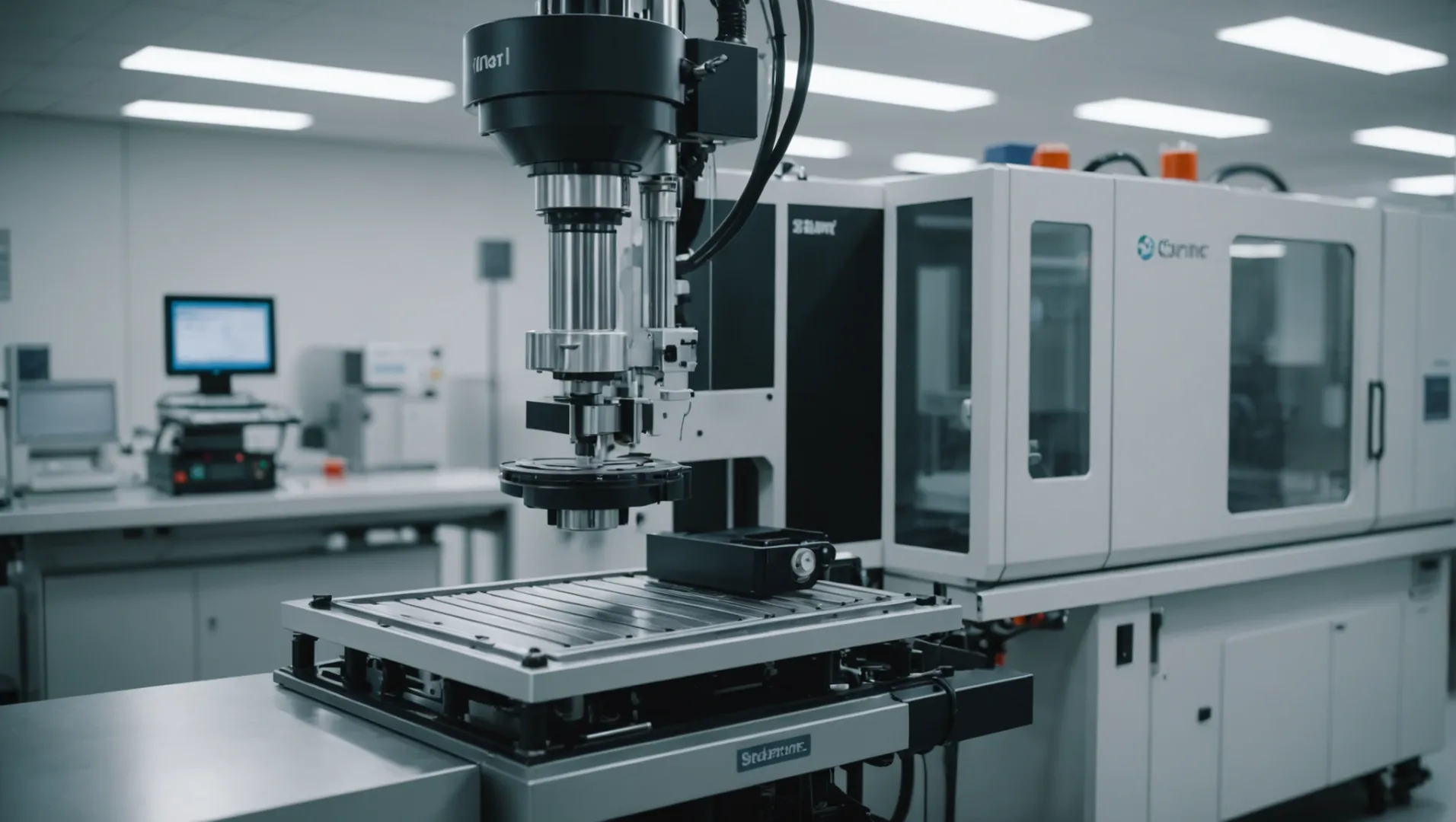
Material Safety: The Foundation of Trust
In the realm of medical injection molding1, material safety acts as a cornerstone ensuring that the products are suitable for use within or on the human body. The primary concern is chemical stability, which prevents harmful substances from leaching into tissues or reacting with drugs. For instance, polycarbonate (PC) and polyetheretherketone (PEEK) are widely favored due to their excellent chemical inertness. They do not interact with bodily fluids, thereby preventing allergic reactions or toxicity.
Biocompatibility: Harmonizing with the Body
Biocompatibility is equally vital as it dictates how well a material can function in harmony with the body’s systems. When manufacturing items like artificial joints or pacemaker housings, the materials must not cause inflammation or rejection. This requirement means that the chosen substances must blend seamlessly with human tissue without inciting negative biological responses.
Consider an example: an injection-molded part designed for an artificial joint must not only fit perfectly in terms of dimensions but also sustain long-term contact with tissue without degrading. The failure to meet these criteria can lead to serious medical complications such as infection or device failure.
The Interplay Between Safety and Biocompatibility
The interdependence of material safety and biocompatibility is crucial. While a material might be chemically stable, it also needs to align biologically with human physiology. For instance, the use of titanium2 in implants exemplifies this balance; it’s not only inert but also biocompatible, integrating well with bone tissue.
A table below highlights the key attributes of commonly used materials:
Material | Chemical Stability | Biocompatibility | Common Uses |
---|---|---|---|
Polycarbonate (PC) | High | Moderate | Surgical instruments, housings |
PEEK | High | High | Implants, dental devices |
Titanium | High | High | Bone implants, dental roots |
Challenges in Maintaining Standards
Maintaining these standards poses challenges such as evolving regulatory requirements and technological advancements. Companies must continuously adapt to ensure that their products meet both safety and biocompatibility standards while remaining innovative. Moreover, regulatory bodies3 impose rigorous testing and certification processes to ensure compliance, demanding ongoing vigilance from manufacturers.
Polycarbonate is highly biocompatible for medical devices.False
Polycarbonate is moderately biocompatible, not highly biocompatible.
PEEK is used in dental devices due to its high stability.True
PEEK's high chemical stability makes it suitable for dental devices.
What Role Does Product Precision Play in Medical Device Manufacturing?
Precision in medical device manufacturing ensures functionality, safety, and compliance with stringent industry standards.
Product precision is crucial in medical device manufacturing, affecting the dimensional accuracy and shape fidelity of components. This ensures proper function and safety, preventing malfunctions that could impact patient health.
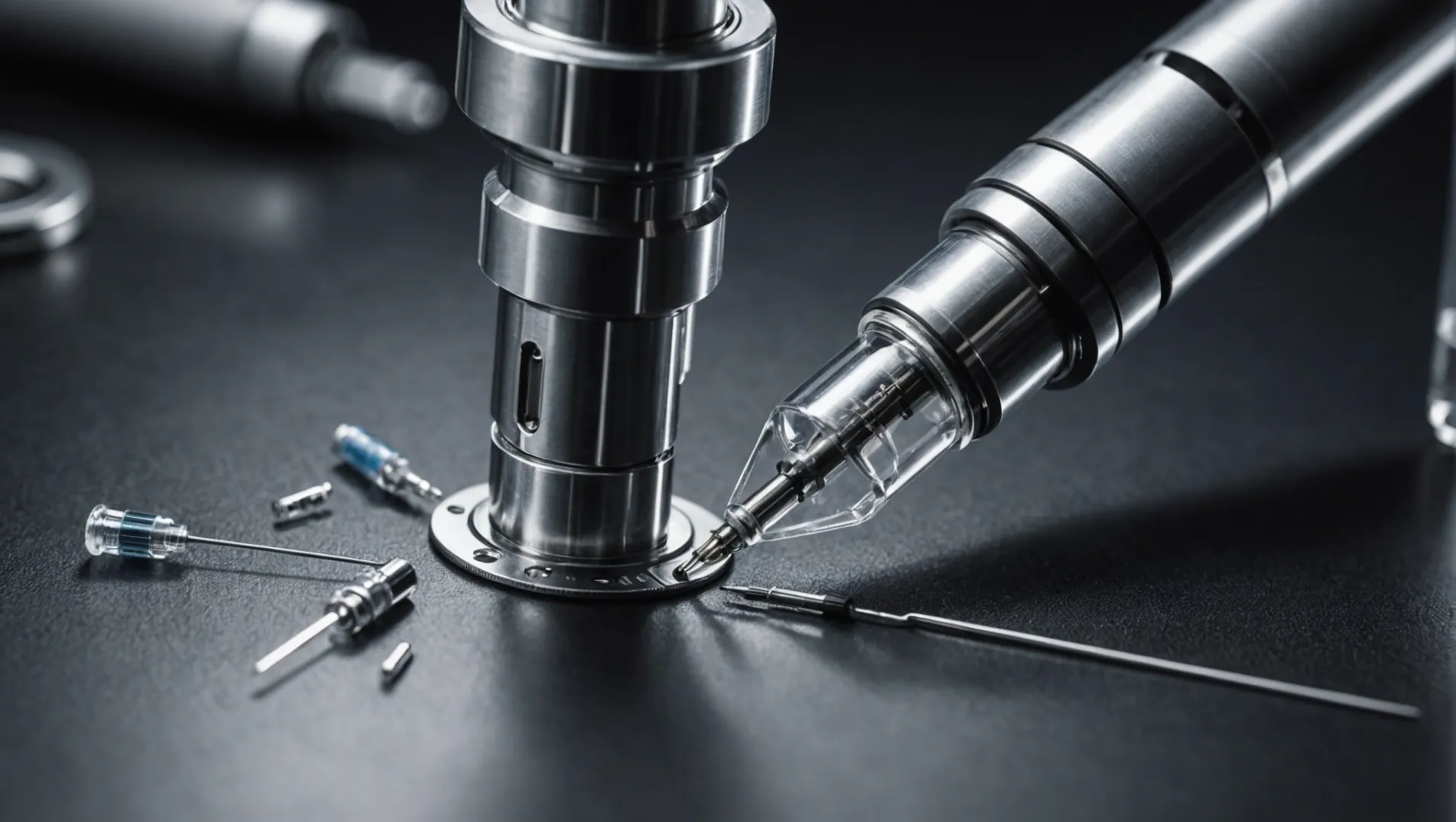
Importance of Dimensional Accuracy
In medical devices, dimensional accuracy is non-negotiable. The precision of components such as the piston and syringe of a syringe must be maintained within tight tolerances to ensure that medications are delivered correctly without leaks or dosage errors. Similarly, the connectors in infusion sets must fit precisely to prevent any disconnection during use. This level of precision is crucial for patient safety and the effectiveness of treatment.
Example: The dimensional tolerance for a syringe piston might be specified to less than 0.01mm to prevent leakage during use. Such precision requires advanced manufacturing techniques and strict quality control measures.
Shape Accuracy and Its Implications
Shape accuracy ensures that the physical form of medical components meets exact design specifications. Any deviation could lead to malfunction or interfere with the device’s performance, potentially putting patients at risk. For complex structures like endoscopes or dental instruments, maintaining shape accuracy is critical to ensure the tool performs as intended during medical procedures.
Example: Endoscope parts require precise curvature to navigate body cavities without causing damage. This necessitates rigorous adherence to shape specifications during manufacturing.
Challenges in Achieving Precision
Achieving high precision in medical device manufacturing is fraught with challenges:
-
Complex Structure Molding: Many devices feature intricate designs requiring high-precision molds and advanced techniques. For instance, microfluidic chips used in diagnostics demand meticulous mold design and process control.
-
Quality Control: Maintaining consistent precision across production batches requires robust quality assurance systems. Advanced technologies like three-dimensional scanning can detect even minute deviations but come with high costs.
-
Regulatory Oversight: Medical devices must comply with stringent regulatory standards that dictate precision levels. Compliance requires significant investment in both technology and personnel training.
By addressing these challenges, manufacturers can ensure their products meet the necessary precision standards, ultimately safeguarding patient health and enhancing therapeutic outcomes.
For further insights on maintaining high precision, explore high-precision manufacturing techniques4 or latest advancements in quality control5.
Dimensional tolerance for syringes is under 0.01mm.True
Such precision prevents leakage, ensuring safe medication delivery.
Shape accuracy is less critical than dimensional accuracy.False
Both are equally crucial to prevent device malfunctions and ensure safety.
Why Are Hygiene Standards Crucial for Medical Injection Molded Products?
In the medical industry, hygiene standards are paramount, particularly for injection molded products that ensure patient safety and product efficacy.
Hygiene standards in medical injection molding ensure products are sterile, easy to clean, and free from contaminants, safeguarding patient health.
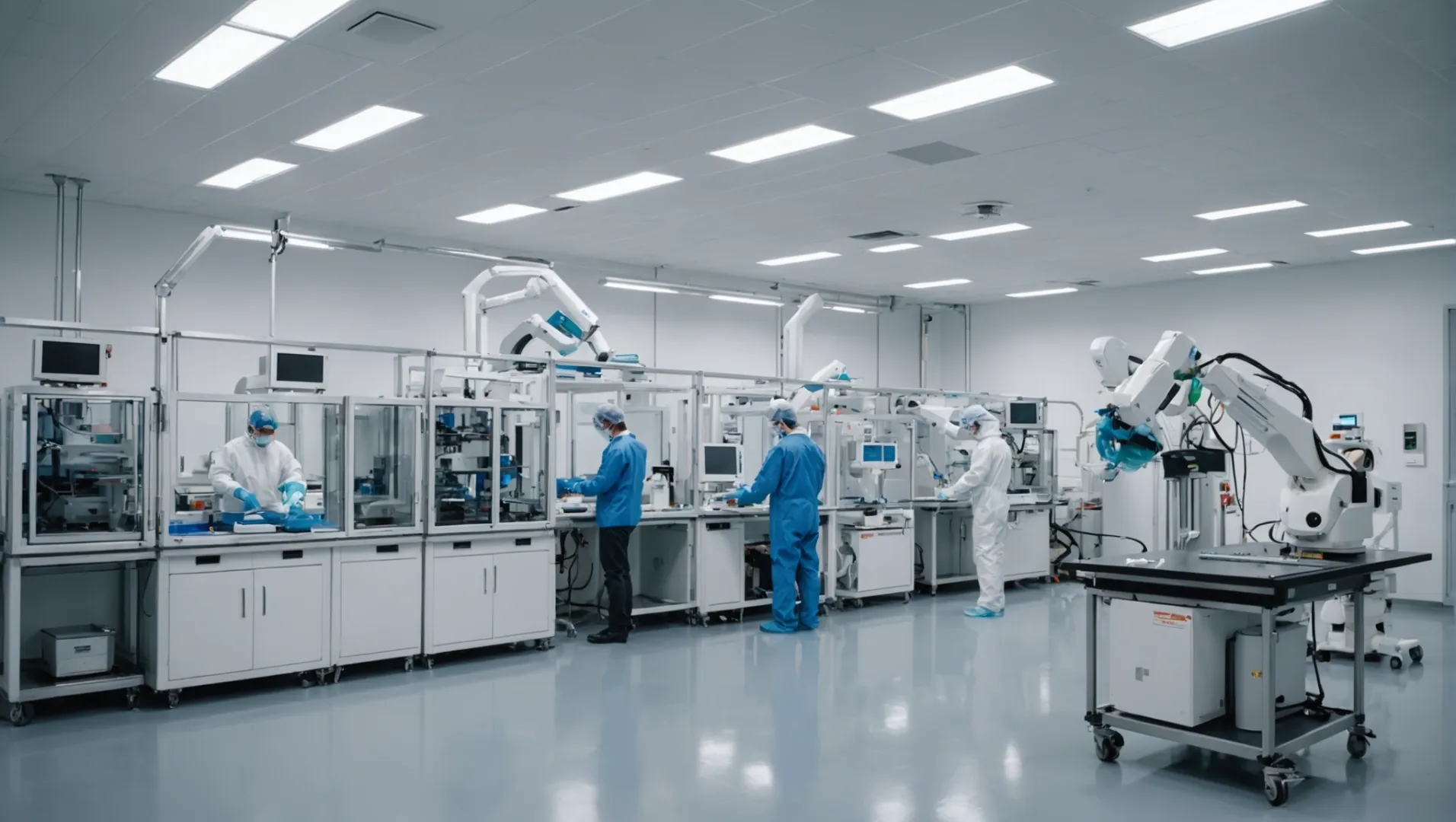
Understanding the Importance of Sterility
Maintaining sterility in medical injection molded products is vital to prevent microbial contamination. These products often come into direct contact with sensitive areas of the human body, such as internal tissues and body fluids. Therefore, ensuring that surgical instruments and implants remain sterile during production, packaging, and transportation is non-negotiable.
Sterility is achieved through rigorous manufacturing processes6 that include controlled environments and the use of biocompatible materials. For example, polycarbonate (PC) and polyetheretherketone (PEEK) are materials known for their stability and non-reactivity, making them suitable choices.
The Role of Cleanability in Hygiene
While sterility is crucial, products that don’t require direct contact with body fluids still need to be easily cleanable. This requirement ensures that even after multiple uses, products can be disinfected effectively to prevent cross-contamination.
Smooth surfaces without pores or cracks are essential for easy cleaning. This is particularly important for products like syringes and infusion sets where residues could harbor bacteria if not thoroughly cleaned. Designing with easy cleanability in mind reduces infection risks significantly.
Challenges in Meeting Hygiene Standards
Achieving these high hygiene standards is not without challenges. The process demands strict quality control and advanced detection technologies like non-destructive testing to identify any potential defects early on. Moreover, the ever-evolving regulatory landscape requires continuous adaptation and compliance with updated standards to ensure ongoing safety and efficacy of medical devices.
Table: Key Hygiene Standards for Medical Injection Molded Products
Hygiene Standard | Description |
---|---|
Sterility | Prevention of microbial contamination through controlled production methods |
Easy Cleanability | Design features enabling thorough cleaning to prevent cross-contamination |
Quality Control | Rigorous inspection processes to ensure hygiene standards are met |
Meeting these stringent hygiene standards not only ensures the safety of the products but also builds trust with healthcare professionals and patients alike, emphasizing the role of meticulous design and manufacturing practices in healthcare settings.
Sterility prevents microbial contamination in medical products.True
Sterility ensures products are free from microbes, safeguarding health.
Quality control is optional for medical injection molded products.False
Quality control is essential to meet hygiene standards and ensure safety.
How Do Regulatory Changes Affect the Injection Molding Process in Healthcare?
Navigating regulatory changes is crucial for healthcare manufacturers, impacting every aspect of the injection molding process.
Regulatory changes in healthcare impact injection molding by altering material requirements, process standards, and certification protocols. These changes demand continuous adaptation from manufacturers to ensure compliance and maintain product quality.
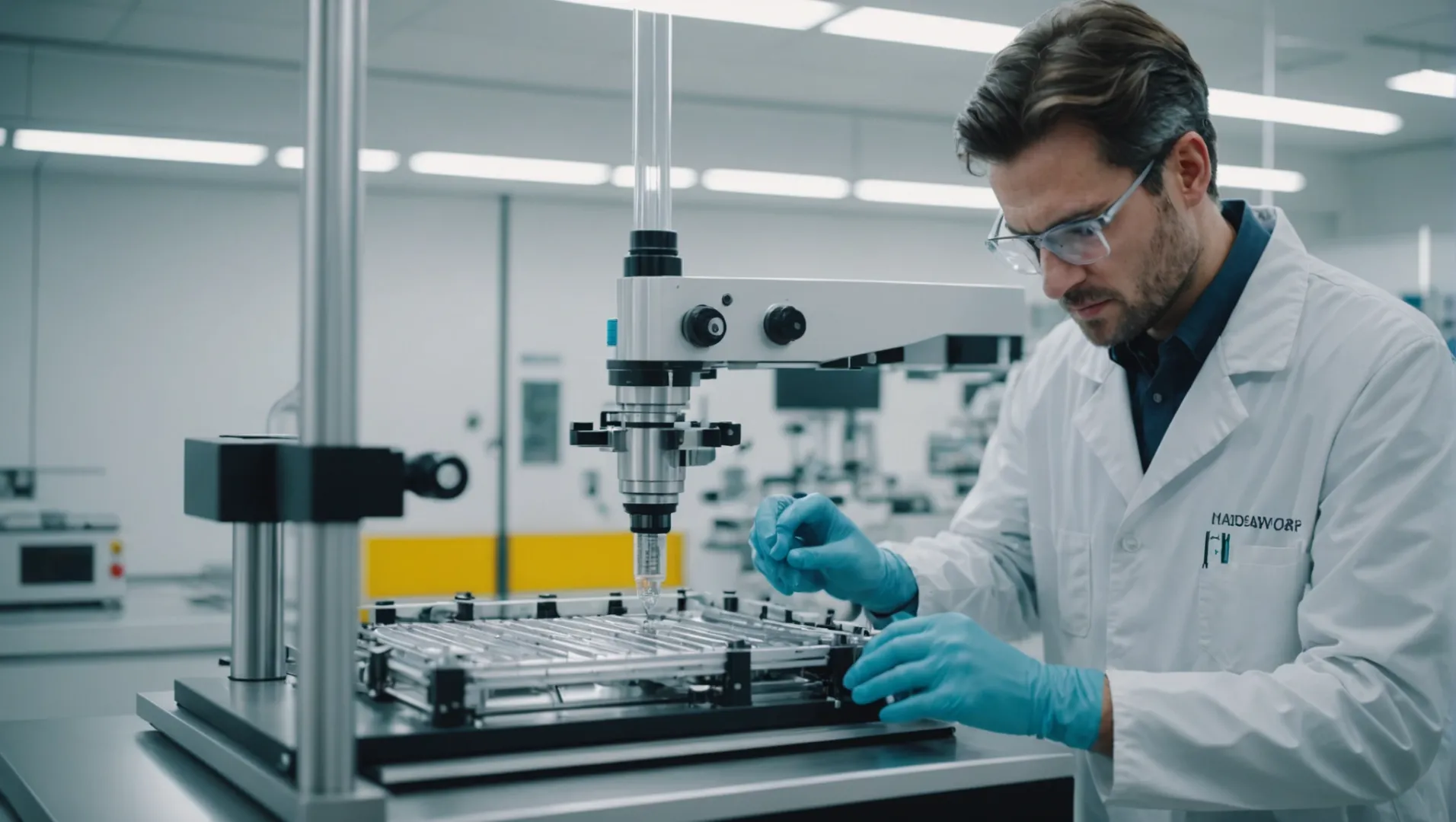
Understanding Regulatory Impact on Material Selection
In the healthcare sector, regulatory guidelines7 are pivotal in determining which materials can be used in injection molding processes. These guidelines often emphasize the need for materials with specific chemical stability and biocompatibility. For instance, regulations might mandate the use of materials like polyetheretherketone (PEEK) due to its non-reactive nature with human tissues. Any shift in these guidelines could require manufacturers to reassess their material choices, ensuring that all products remain safe for patient use.
Evolving Standards and Process Adjustments
Regulatory bodies frequently update standards related to the dimensional accuracy and structural integrity of medical devices. Injection molding processes must adapt to these evolving standards to prevent issues such as leakage or structural failure. For example, a change in the tolerance level for a syringe’s piston might necessitate recalibrating molds or modifying process parameters to achieve new precision targets.
Certification Protocols and Compliance Challenges
The regulatory landscape in healthcare is marked by stringent certification protocols. Changes in these protocols can significantly impact the injection molding process. Companies are often required to update their quality management systems and undergo additional product testing or audits to maintain certifications. This can involve substantial investment in both time and resources, compelling manufacturers to keep abreast of regulatory developments to avoid costly delays.
Impact on Research and Development
Regulatory changes often drive innovation within the healthcare industry by pushing companies to explore new technologies and methodologies. For instance, the need for compliance with updated sterility standards may lead manufacturers to invest in advanced antimicrobial technologies or novel cleaning methods for their products. While this fosters innovation, it also requires a flexible approach to R&D, ensuring that new solutions align with current regulatory expectations.
Understanding the nuances of how regulatory changes affect injection molding is crucial for healthcare manufacturers aiming to remain competitive and compliant in an ever-evolving industry landscape.
PEEK is commonly used in medical injection molding.True
PEEK's chemical stability and biocompatibility make it ideal for medical use.
Regulatory changes rarely affect material selection.False
Regulatory guidelines often dictate which materials can be used safely.
Conclusion
Navigating the challenges of medical injection molding is vital for patient safety. Continuous innovation and adherence to rigorous standards can pave the way for successful outcomes.
-
Understand the process and significance of medical injection molding.: Medical injection molding is a manufacturing process that produces plastic medical devices and components. It involves melting plastic resin pellets and … ↩
-
Learn why titanium is ideal for medical implants.: When comparing metals for implantation, titanium has a modulus of elasticity closer cortical bone than other choices. While still different by more than a … ↩
-
Stay updated on essential regulatory standards for medical devices.: This module is intended to provide an overview of the regulatory requirements for medical devices or what is sometimes referred to as Devices 101. ↩
-
Discover methods to achieve exceptional precision in medical device components.: ARCH Medical Solutions provides the concentricity, balance, flatness, and machined-to-weight precision necessary for devices that rotate at high speeds. ↩
-
Learn about cutting-edge quality control technologies for precision assurance.: 1. Advanced Manufacturing Technologies · 2. Digital Transformation · 3. Regulatory Compliance and Quality Assurance · 4. Sustainability Practices ↩
-
Learn how controlled environments ensure sterility in medical product manufacturing.: The controlled environment of a clean room for medical devices can help ensure that dust and other particulate matter do not contaminate the … ↩
-
Gain insights into up-to-date material regulations impacting medical device safety.: Standard for plastic injection molding in the medical industry include ISO 13485, ISO 10993, and ISO 14644. Medical devices are also divided … ↩