Do you ever think about how to create a Lifter and slider that lasts a long time?
To build a long-lasting lifter and slider, use materials with enough strength and wear resistance. Such materials should have good toughness and thermal stability. Machinability is important, too. These properties help the components withstand pressure and friction. They also keep accuracy and performance at high temperatures.
I remember the first time I tried creating a lifter and slider for my own project. It was not just about picking random materials. I needed to understand why each property was important. Materials must be tough enough to handle strong pressure during use. For example, P20 steel stays strong against scratches. I also learned about wear resistance. Chromium in H13 steel forms a protective layer. This layer keeps everything in good shape even after many uses.
Toughness is also very important. The first time my parts survived an unexpected hit without breaking, I realized how important toughness is. It reminded me of life’s surprises. We sometimes face challenges but stay strong. Having inner strength really matters.
Thermal stability is vital, too. Imagine staying calm when things heat up! High-temperature materials like H13 steel do not lose strength easily. They remain strong under heat. Machinability is crucial as well. If the process is smooth, the result is better. Each piece needs to fit perfectly, like puzzle pieces at last coming together.
Understanding these material properties improved my design. It taught me about strength, resilience and precision. I learned life lessons in the workshop.
Slant tops require high thermal stability materials.True
Thermal stability ensures slant tops maintain performance under heat.
Machinability is irrelevant for slider materials.False
Machinability is crucial for shaping sliders to precise dimensions.
Why is Hardness Crucial for Lifter and Sliders?
Have you ever wondered why your car’s engine runs smoothly or your laptop avoids getting too hot? It’s all because of the small, durable parts inside.
Hardness is very important for lifters and sliders. It offers resistance to wear and deformation. This resistance keeps them working well and strong under very high-pressure situations.
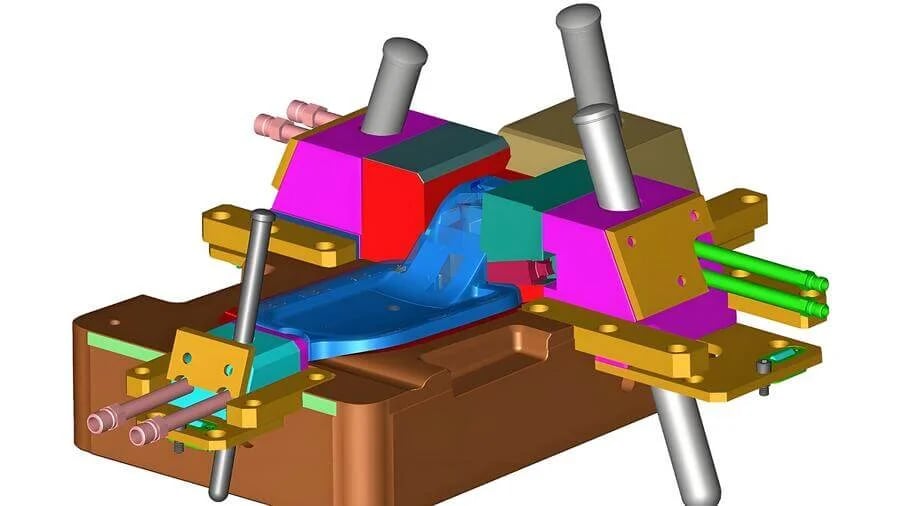
Importance of Hardness in Lifter and Sliders
I entered the mold design field and quickly understood the role of lifters and sliders in injection molding processes1. These little components endure great pressure as they direct molten plastic into shape. They need to be hard to avoid bending. Imagine trying to create a precise item but your tools wear out early. That would be really frustrating.
Material Hardness Requirements
My first project used P20 steel, which many see as a rite of passage in the industry. After heat treatment, P20 achieves an excellent hardness of HRC45 to 55. This hardness resists wear from fillers like glass fibers that mix with plastic.
Material | Hardness (HRC) | Example Usage |
---|---|---|
P20 Steel | 45 – 55 | General molds |
H13 Steel | High | High-temp plastics |
Wear Resistance Improvement
Hardness matters, but surviving friction is key. Materials like H13 steel have chromium, forming a strong oxide layer. This layer acts as armor, keeping dimensions accurate and ensuring dimensional accuracy2.
Impact of Toughness on Hardness
Toughness is also vital. Materials must be strong and flexible. Forgetting toughness leads to fractures from impacts in fast processes. Balancing hardness with toughness avoids these costly mistakes.
Fatigue Resistance
These components work tirelessly every day. Fatigue causes cracks and failures if materials lack toughness. Changing the microstructure relieves stress through methods like dislocation motion, helping components last longer.
Thermal Stability and Machinability
Heat complicates things. High temperatures may weaken some materials; however, H13 steel retains its strength when hot, making it suitable for high-temperature plastics.
Thermal Expansion Compatibility
Fit is crucial. If materials’ thermal expansion doesn’t match other parts, issues arise—parts might seize or gaps might form. Choosing compatible materials is very important for smooth operation.
Machinability Aspects
Good machinability is necessary because I’ve spent hours shaping these components. Materials need to cooperate during machining; complex shapes might need Electric Discharge Machining (EDM)3. Materials must suit this process or surface defects risk the entire mold.
Understanding hardness in lifters and sliders brings advantages in mold applications. Each factor is a guide for selecting materials; every detail matters—nothing should be left to chance.
P20 steel's hardness is HRC45-55 after treatment.True
P20 steel achieves this hardness range through proper heat treatment.
H13 steel lacks wear resistance in high-temp plastics.False
H13 steel forms a stable oxide layer, enhancing wear resistance.
How Does Wear Resistance Affect Mold Performance?
Ever wondered why some molds last longer and work better than others? The secret often rests in wear resistance. This is a key factor in determining mold performance and longevity.
Wear resistance is very important for mold performance. It reduces wear and tear. This helps molds last longer. Precision remains high. Mold can withstand pressure, friction and high temperatures. Efficiency stays high over time. Accuracy remains stable.
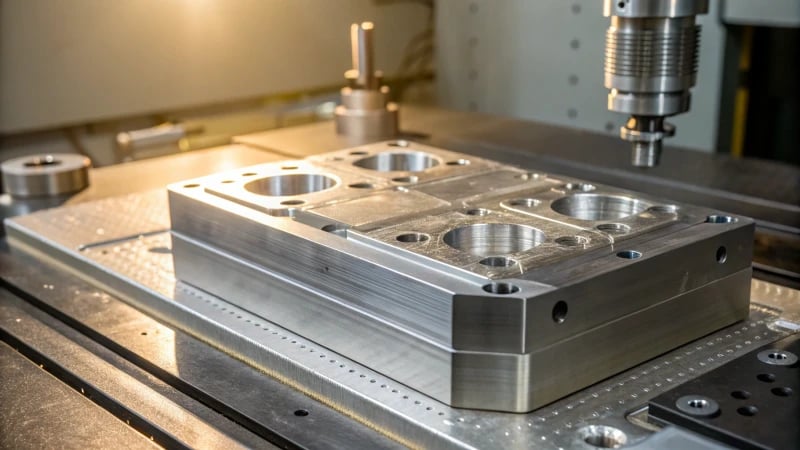
The Importance of Hardness and Wear Resistance
In injection molding, components like the lifter and slider must endure constant pressure and friction. To prevent surface abrasion and deformation4, these parts require materials with sufficient hardness, typically around HRC45 – 55. For example, P20 steel can achieve this range after heat treatment, effectively resisting wear from filler materials like glass fibers.
Improving Wear Resistance in Mold Materials
During mold operations, frequent contact between components demands high wear resistance. Alloying elements such as chromium in H13 steel form hard carbides, which enhance wear resistance. This results in components maintaining their dimensional accuracy over extended use.
Toughness: A Key Partner to Wear Resistance
Aside from wear resistance, good toughness is essential. Imagine a mold part surviving high-speed impacts without breaking. Toughness allows this to happen. Materials with excellent toughness can absorb impacts without fracturing. They also resist fatigue cracking from cyclic stress over time.
Thermal Stability and Its Role
Mold temperatures can reach up to 300°C in high-temperature plastic molding. Materials like H13 maintain their strength and hardness5 at such temperatures, ensuring the mold operates smoothly. Moreover, matching the thermal expansion coefficients of different mold parts prevents misalignment due to temperature fluctuations.
Property | Role in Mold Performance |
---|---|
Hardness | Resists deformation under pressure |
Wear Resistance | Minimizes wear from friction |
Toughness | Absorbs impact forces without breaking |
Thermal Stability | Maintains performance at high temperatures |
Machinability | Facilitates efficient production processes |
Machinability: Balancing Toughness and Hardness
Mold materials should possess good machinability to achieve the desired shape efficiently. Steels that balance hardness and toughness allow for smooth cutting with minimal tool wear, enhancing production efficiency6. In complex shapes, EDM performance is crucial, requiring materials that support stable electrical discharge channels without compromising surface quality.
Understanding these factors guides my material choices. I focus on wear resistance and other important properties to craft molds that are efficient, durable, and precise for specific applications.
P20 steel achieves HRC45-55 after heat treatment.True
P20 steel is heat-treated to reach this hardness range, enhancing wear resistance.
Toughness is not important in mold materials.False
Toughness helps absorb impacts and resist fatigue cracking, crucial for mold durability.
Why is Toughness Important in Material Selection?
Do you ever think about why certain materials manage stress and pressure so well?
Toughness is vital when choosing materials. It allows components to withstand stress and impacts. Materials do not crack easily. This extends their lifespan. Reliability increases, particularly in difficult environments. Components last longer under tough conditions.
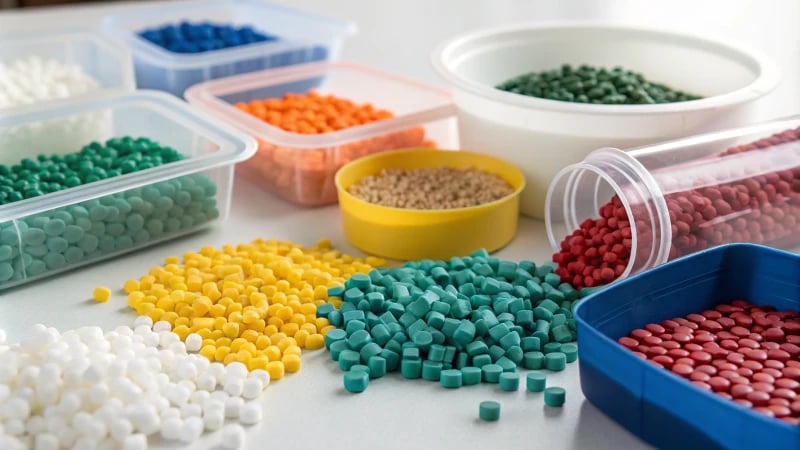
Understanding Toughness in Materials
Let’s explore toughness. I first learned about it during a project. The task was to design a component that withstands heavy impacts. Toughness measures how much energy a material absorbs before breaking. It differs from hardness, which resists surface damage. Toughness acts like the spine, helping a material stay firm under pressure.
The Balance Between Toughness and Hardness
Toughness and hardness work together in interesting ways. They are like the yin and yang of material traits. Hardness7 is vital for preventing scratches or dents. But, too much hardness leads to brittleness. I once worked with P20 steel. It balanced toughness with hardness perfectly, resisting cracks under stress and standing up to surface wear.
Material | Hardness (HRC) | Toughness |
---|---|---|
P20 Steel | 45-55 | High |
H13 Steel | 50-60 | Moderate |
Impact and Fatigue Resistance
Materials often face repeated impacts and stress, especially with injection molds. In one project, components opened and closed nonstop. Toughness8 was essential as it helps materials resist fatigue over time, staying strong even after repeated use.
Role of Toughness in Different Industries
- Automotive: Cars need tough parts to handle vibrations and impacts. Toughness means safety in crashes.
- Construction: Toughness allows buildings to stand against wind and earthquakes, ensuring structures don’t fall under pressure.
Material Toughness vs. Thermal Stability
In high temperatures, toughness remains vital. Consider H13 steel; it performs well in heat, such as in hot die casting applications where matching thermal stability with toughness prevents thermal cracks.
Enhancing Toughness through Alloying
Chromium and molybdenum improve toughness by refining grain structure—this technique amazes me! These elements reduce stress points, stopping cracks from spreading while also increasing wear resistance by forming a protective layer.
Explore how alloying affects material properties9 across different engineering fields.
Understanding toughness isn’t just theory; it’s practical and vital in many fields for reliable performance under stress while balancing hardness for durability.
Toughness measures energy absorption before breaking.True
Toughness is defined as a material's ability to absorb energy and plastically deform without fracturing.
High hardness always ensures better toughness.False
Excessive hardness can lead to brittleness, reducing toughness, which balances wear resistance with flexibility.
Why is thermal stability crucial in high-temperature environments?
Have you ever thought about how materials survive extremely hot temperatures without breaking?
Thermal stability is very important in high-temperature environments. It keeps materials strong and hard. This prevents them from wearing out and helps them last longer. Very crucial.
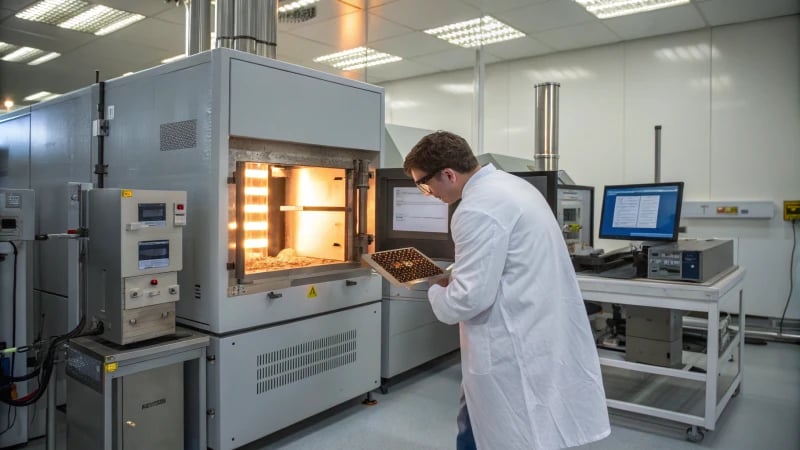
The Role of Thermal Stability
Imagine an industry where the heat is very intense, like a sauna. Materials must survive this heat without breaking down. Thermal stability is the superpower that keeps materials’ physical and chemical qualities unchanged. It is crucial in industries such as automotive, aerospace, and plastics. Even a tiny material fault in these fields can result in huge problems.
Thermal stability is a measure of a material’s ability to retain its essential characteristics under heat stress10.
High Temperature Strength Maintenance
Picture designing an injection mold. You require materials that remain solid when heated. Consider hot work die steel H13. It withstands temperatures up to 300°C while keeping its strength, making it suitable for injection molds. Its key features are good hardness and wear resistance, which help fight surface wear and keep processes running well.
Material | Hardness (HRC) | Max Temperature (°C) |
---|---|---|
P20 Steel | 45 – 55 | 250 |
H13 Steel | 50 – 60 | 300 |
Matching Coefficient of Thermal Expansion
Think of shoes that don’t quite fit. That happens when materials expand at different rates when heated. If thermal expansion rates don’t match, parts can jam or leave gaps. Such mismatches can cause big issues, especially in critical environments.
A key factor in maintaining performance is the matching of the thermal expansion coefficient between different materials to avoid component failure11.
Improvements Through Alloying
I’ve observed that elements like chromium and molybdenum work wonders by creating stable carbides that increase wear resistance and improve toughness. Plus, they raise fatigue resistance, ensuring durability under cyclic loads.
Practical Implications
Thermal stability means more than just surviving heat; it’s also about thriving over time. For example, machinability is vital for efficient production12. If a material’s cutting edge fades at high temperatures, costs and downtime might increase.
Example: During mold operations where excessive expansion caused chaos if tilt top or slider materials expanded excessively compared to other parts, it may result in operational inefficiencies or even damage.
Understanding these effects lets experts like me pick wisely for lasting performance by balancing strength, wear resistance, and machinability.
Thermal stability ensures material machinability at high temps.True
Maintaining machinability prevents increased costs and downtime.
P20 steel maintains hardness up to 300°C.False
P20 steel's maximum temperature is 250°C, not 300°C.
Why is good machinability crucial for mold components?
Machinability could seem technical. However, it is the key to efficient mold-making. This is very true. I have witnessed how it changes production and quality.
Good machinability in mold parts means faster production, cost savings and less tool wear. Precision in creating complex forms and high-quality finishes is important. These elements are very essential for smooth and efficient mold work.
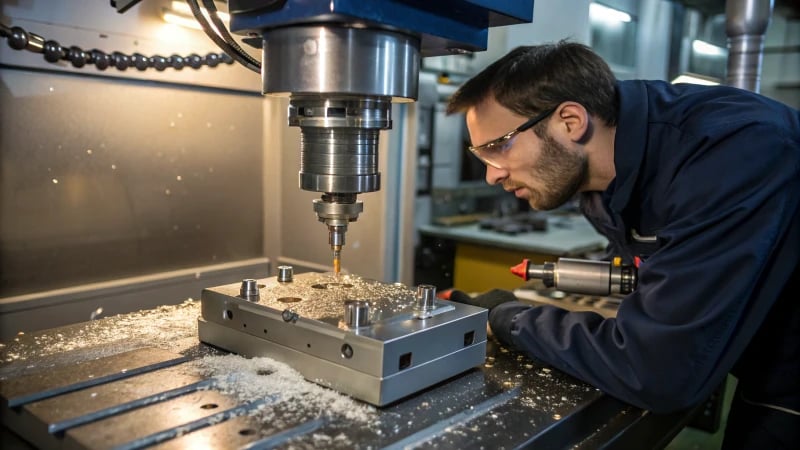
Importance of Good Machinability
Machinability involves how easily we can shape materials using common methods like turning, milling, and grinding. A colleague once struggled with a stubborn material. It wouldn’t cut cleanly, causing delays and frustration. For mold components, good machinability13 is essential. It helps achieve both fast production and excellent quality.
Benefits of Good Machinability
-
Production Efficiency: I recall a project where we changed to a material with better machinability. Everything suddenly fit together very well. Operations sped up, machine downtime decreased, and deadlines were easier to meet. Materials like P20 steel let machines work quicker and last longer without too much wear.
-
Cost Reduction: It’s very satisfying to see costs drop when machining times decrease. Less time means lower labor and energy expenses. Tools last longer because of less wear, which saves on replacements.
-
Precision and Surface Finish: Achieving precise dimensions feels like hitting a bullseye in darts—highly satisfying! Good machinability helps molds meet exact specifications, ensuring they perform smoothly over time.
Factor | Impact on Machinability |
---|---|
Hardness | Excessive hardness can increase tool wear. |
Toughness | Balances resistance to impact with ease of cutting. |
Thermal Properties | Stability under heat affects cutting performance. |
Machining Processes in Mold Making
Different processes suit various needs in mold making:
-
Turning and Milling: These processes shape basic features. The machinability of a material affects how efficiently we remove excess while maintaining tight tolerances.
-
Grinding: This process achieves perfect finishes necessary for glassy smoothness without damaging tools.
-
EDM: This process is invaluable for complex designs; good material will keep a stable discharge channel to avoid problems like surface burns or cracks.
Choosing materials with good machinability is more than a technical decision; it’s a strategic choice that ensures our molds perform reliably and efficiently while maintaining quality standards.
Good machinability reduces mold production time.True
Materials with good machinability allow faster machining, reducing production time.
High hardness always improves machinability.False
Excessive hardness increases tool wear, negatively affecting machinability.
Conclusion
This article discusses essential materials for lifters and sliders in mold operations, emphasizing hardness, wear resistance, toughness, thermal stability, and machinability for optimal performance.
-
This link explains why injection molding processes are crucial for manufacturing durable components. ↩
-
Learn how maintaining dimensional accuracy extends component life. ↩
-
Discover how EDM is used for complex component shaping without defects. ↩
-
Learn how abrasion affects mold components during injection molding to improve material selection. ↩
-
Discover how certain materials maintain strength at high temperatures for reliable mold performance. ↩
-
Explore materials that balance machinability and durability for efficient mold production. ↩
-
This link provides insights into how hardness complements toughness in materials, enhancing durability and wear resistance. ↩
-
Explore how impact resistance helps materials withstand sudden forces without cracking. ↩
-
Learn how alloying elements enhance toughness by altering grain structures and preventing crack propagation. ↩
-
Understanding this can guide engineers in selecting materials that withstand heat without degrading. ↩
-
Exploring this helps prevent failures due to incompatible material expansions. ↩
-
Learning this aids in maintaining production efficiency even under extreme conditions. ↩
-
Discover which materials offer the best machinability properties, balancing hardness and ease of cutting. ↩