Ever wonder why injection molding costs can seem like a rollercoaster ride?
Selecting the appropriate material for injection molding influences costs by affecting material properties, cycle time, and tool wear. Different materials require varied processing, impacting production speed and efficiency.
I remember when I first started dealing with material selection, it felt like being a kid in a candy store—so many options, each with its own perks and pitfalls. Diving into the specifics of how material properties affect costs isn’t just about numbers; it’s about understanding the dance between durability, performance, and price. By strategically choosing materials, you can ensure quality while also keeping an eye on profitability. It’s all about finding that sweet spot where your product not only stands out but also fits within budget constraints.
Material choice directly affects injection molding cycle time.True
Different materials have varying cooling and processing times, impacting cycle duration.
All materials have the same impact on tool wear in injection molding.False
Materials vary in abrasiveness and hardness, affecting tool wear differently.
- 1. What Are the Most Common Materials Used in Injection Molding?
- 2. How Do Material Properties Influence Mold Design and Costs?
- 3. How Does Production Volume Affect Material Selection?
- 4. How Does Material Choice Affect Post-Processing Requirements?
- 5. Can Sustainable Materials Reduce Long-Term Costs in Injection Molding?
- 6. What Are the Cost Implications of Material Waste in Injection Molding?
- 7. Conclusion
What Are the Most Common Materials Used in Injection Molding?
Have you ever wondered what materials form the backbone of the injection molding world?
Common materials in injection molding include ABS, Polypropylene, Polystyrene, and Nylon, each chosen for their unique properties suitable for various industries like automotive, electronics, and consumer goods.
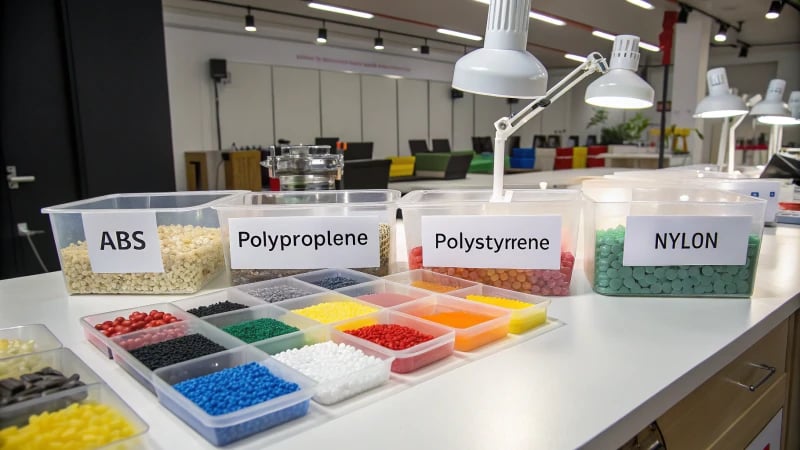
Acrylonitrile Butadiene Styrene (ABS)
ABS was my go-to choice when I worked on a project that required a durable yet visually appealing surface. Its excellent impact resistance and toughness made it perfect for automotive parts and electronics housings. I remember how relieved I was when the product passed all the durability tests with flying colors, thanks to ABS’s versatility. Learn more about product designers1.
Property | Value |
---|---|
Density | 1.04 g/cm³ |
Impact Resistance | High |
Heat Resistance | Up to 100°C |
Polypropylene (PP)
Polypropylene has been a staple in my design toolkit, especially for projects that needed a lightweight yet strong material. I once designed a line of kitchen containers, and PP’s ability to withstand fatigue made it ideal for the hinges, ensuring longevity even with daily use. Discover more about plastic containers2.
Polystyrene (PS)
I often turn to Polystyrene when clarity and cost-effectiveness are top priorities. It’s a bit more brittle, but for products like CD cases and food packaging where rigidity is key, it’s unbeatable. A mass production project for a client came in under budget, largely due to PS’s affordability. Explore its use in mass production3.
Nylon (Polyamide)
When it comes to strength and thermal resistance, Nylon is unmatched. In one challenging project, I designed gears that had to withstand both friction and heat—Nylon was the hero of that story, providing the durability we needed without compromising performance. Discover more about Nylon’s applications4.
Comparing Material Properties
Here’s a quick comparison of these materials:
Material | Impact Resistance | Heat Resistance | Cost |
---|---|---|---|
ABS | High | Moderate | Moderate |
PP | Moderate | Low | Low |
PS | Low | Low | Very Low |
Nylon | Very High | High | High |
Understanding these properties can be a game-changer in your design process. I’ve learned that choosing the right material not only ensures that the product meets functional and aesthetic requirements but also helps manage costs effectively.
ABS has high heat resistance up to 100°C.True
ABS is known for its moderate heat resistance, up to 100°C.
Nylon is more brittle than Polystyrene.False
Nylon is less brittle and known for its strength and wear resistance.
How Do Material Properties Influence Mold Design and Costs?
I remember my first big project in mold design, where choosing the right materials felt like solving a complex puzzle. Each piece mattered more than I initially realized.
Material properties affect mold design and costs by influencing complexity, cycle time, wear resistance, and part quality, helping optimize production efficiency and expenses.
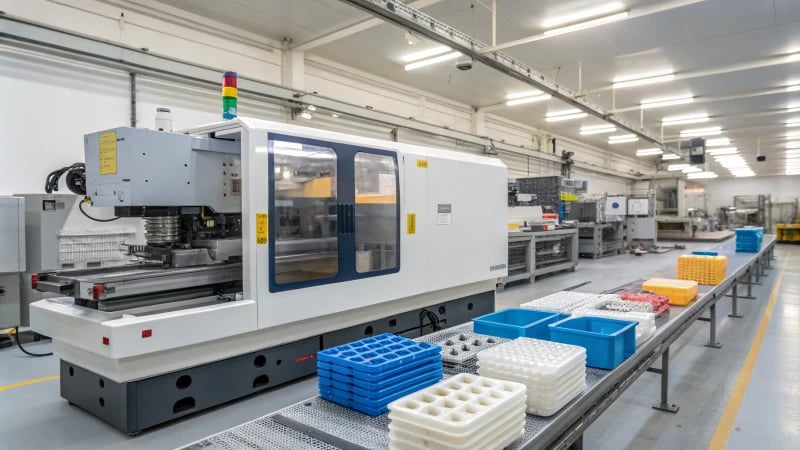
Understanding Material Properties
In the world of mold design, I’ve learned that material properties are like the DNA of a project. They determine everything from how complex a mold needs to be, to how long each cycle will take. I vividly recall a project where thermal conductivity was our main concern. The material we chose required such an intricate cooling system that it felt like designing a miniature air conditioning unit inside the mold. It wasn’t just about getting it right; it was about understanding how deeply these properties affect every aspect of the process.
Property | Influence on Mold Design |
---|---|
Thermal Conductivity | Affects cooling system requirements |
Melting Temperature | Determines processing temperatures and cycle times |
Shrinkage Rate | Influences dimensional accuracy and tolerances |
Impact on Production Efficiency
I remember a time when we opted for a material with a lower melting temperature5, hoping to save on energy costs. What a relief it was to see the cycle times shorten, almost like watching your favorite show on fast-forward! But then came the realization that this choice increased wear on our molds, leading to more frequent maintenance.
It’s always a balancing act, isn’t it? When materials boast higher wear resistance, it’s like giving your molds a longer lease on life. It means fewer interruptions for repairs and a smoother production line, which is every designer’s dream.
Cost Implications of Material Selection
Material selection can feel like a game of chess, with each move potentially altering the outcome significantly. Investing in high-performance materials might seem daunting with their upfront costs due to specialized tooling and complex mold designs6, but it’s like buying peace of mind. These materials often pay off by enhancing product quality and reducing defect rates.
Choosing materials that align with your specific production goals can lead to significant savings. I’ll never forget the project where opting for a faster injection molding cycle7 material increased our throughput without sacrificing quality. It was a lesson in how crucial it is to weigh each material’s unique benefits against your project’s requirements and budget constraints.
Materials with higher thermal conductivity increase mold cost.True
High thermal conductivity requires efficient cooling systems, raising complexity and cost.
Low shrinkage rate materials reduce mold expenses.False
Low shrinkage rates enhance part quality but can increase mold costs due to tighter tolerances.
How Does Production Volume Affect Material Selection?
Ever wondered how production volume can steer your material selection journey? It’s like picking the right tools for a big project—essential for balancing cost, quality, and efficiency.
Production volume affects material selection by influencing cost-effectiveness; high volumes can justify investing in durable materials due to economies of scale, guiding choices between custom and standard options.
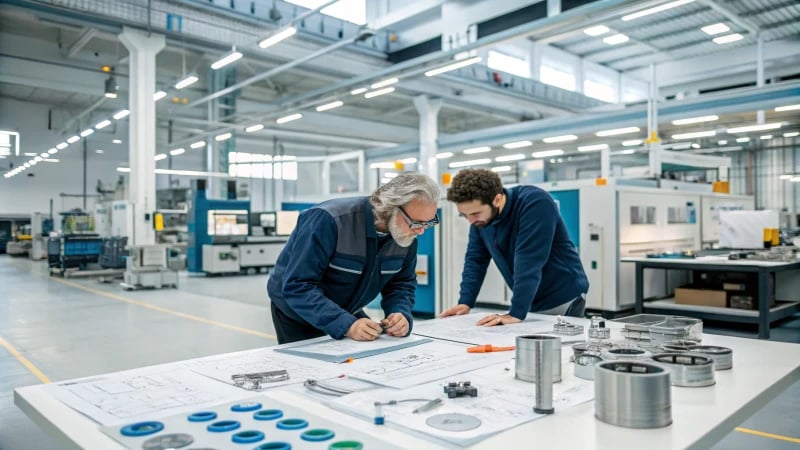
The Economics of Scale
You know that feeling when buying in bulk at a warehouse club saves a ton of money? That’s the economics of scale8 in action. In manufacturing, as production ramps up, the cost per unit tends to drop. This means I can often afford to choose higher-quality materials for large runs—something I couldn’t justify for smaller batches. I’ve learned that this approach not only saves money but also boosts efficiency, much like when my team and I decided to switch to a premium plastic for a high-volume project, and it significantly improved our product’s performance.
Balancing Cost and Quality
It’s a bit of a balancing act, isn’t it? For low-volume projects, I might be tempted to go for less expensive materials to keep within budget. But here’s the catch: skimping on quality can backfire. On the flip side, with high-volume production, I can opt for top-notch materials that enhance durability and customer satisfaction. I remember one time when we chose a costlier alloy for a project—it was a leap of faith that paid off with rave reviews from our customers.
Custom vs. Standard Materials
Deciding between custom and standard materials often feels like choosing between a tailored suit and off-the-rack clothing. For big production runs, custom materials can offer advantages like increased performance or aesthetic appeal. They can really give my designs that extra edge. However, for smaller batches, standard materials are usually the way to go—they’re easier on the wallet and get us to market quicker. I recall a project where the decision to stick with standard materials allowed us to launch in record time.
Volume | Material Type | Advantages |
---|---|---|
Low | Standard | Lower cost, faster sourcing |
High | Custom | Tailored properties, better performance |
Influence on Manufacturing Techniques
Different production volumes require varied manufacturing techniques. For example, injection molding might be the go-to choice for large volumes due to its cost-effectiveness, while 3D printing could be perfect for smaller runs because of its flexibility and lack of tooling costs. Each technique has its own material compatibility constraints. I’ve had moments when choosing the right method felt like solving a puzzle—each piece had to fit perfectly to ensure success.
Understanding how production volume impacts material selection is key to optimizing our manufacturing processes and ensuring top-notch product quality across different scales of production. By considering these factors carefully, I’ve managed to maximize efficiency and minimize costs in my projects. Exploring further9 these aspects has certainly led to better-informed decisions and successful product outcomes.
High production volume reduces per-unit material cost.True
Economies of scale lower costs as production volume increases.
Low-volume production always uses custom materials.False
Low-volume often uses standard materials due to cost efficiency.
How Does Material Choice Affect Post-Processing Requirements?
Ever wonder why some projects feel like a breeze while others have you elbow-deep in post-processing?
Material choice in 3D printing significantly influences post-processing. Various materials like PLA and ABS necessitate specific finishing techniques, such as sanding or chemical smoothing, to attain the desired quality and appearance.
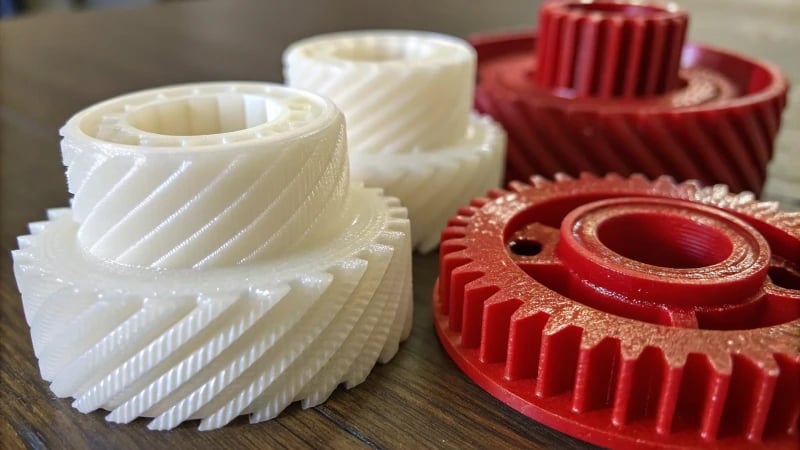
Material Characteristics and Their Impact
I remember the first time I dove into 3D printing, I was like a kid in a candy store, fascinated by the endless possibilities. But soon, I learned that material choice is no small decision. Take PLA10, for instance. It’s like the trusty old friend who’s always there when you need them. It’s easy to print with, but if you want that silky smooth finish, you’ll need to put in the elbow grease with precise sanding. Then there’s ABS11, which feels like a high-maintenance buddy. It requires some patience but rewards you with a smooth surface if you’re willing to use acetone smoothing.
Material | Ease of Printing | Post-Processing Technique |
---|---|---|
PLA | High | Sanding |
ABS | Medium | Acetone Smoothing |
PETG | Medium | Heat Treatment |
The Role of Surface Finish Requirements
Once, I had a project where a high-gloss finish was non-negotiable. I had to choose my material carefully. ABS12 became my go-to because it responds beautifully to vapor smoothing, leaving an ultra-smooth surface that almost makes the object look like it’s from a sci-fi movie.
Comparing Cost and Time Efficiency
I’ve often found myself in meetings discussing whether we should go for a cheaper material upfront or one that saves time later on. It’s like choosing between a budget vacation with lots of layovers or a direct flight that’s pricier but oh-so-much easier. For example, PLA is quick and cost-effective initially but can be labor-intensive if you’re chasing high detail. ABS is moderate in cost and pretty efficient with chemical smoothing. PETG13, on the other hand, offers durability but demands more time due to its heat treatment requirements.
- PLA: Quick and cost-effective but labor-intensive for high detail
- ABS: Moderate cost; efficient with chemical smoothing
- PETG: Durable but time-consuming
Understanding these factors helps me—and hopefully you too—streamline production by selecting materials that align with specific post-processing capabilities and requirements.
PLA requires precise sanding for a smooth finish.True
PLA is easy to print but needs careful sanding for smoothness.
ABS cannot achieve a high-gloss finish.False
ABS can achieve a high-gloss finish using vapor smoothing.
Can Sustainable Materials Reduce Long-Term Costs in Injection Molding?
Imagine transforming your manufacturing approach with sustainable materials, not just for the environment, but for your wallet too. Intrigued?
Sustainable materials in injection molding can offset higher initial costs by reducing waste, improving energy efficiency, and increasing product longevity, ultimately lowering long-term expenses.
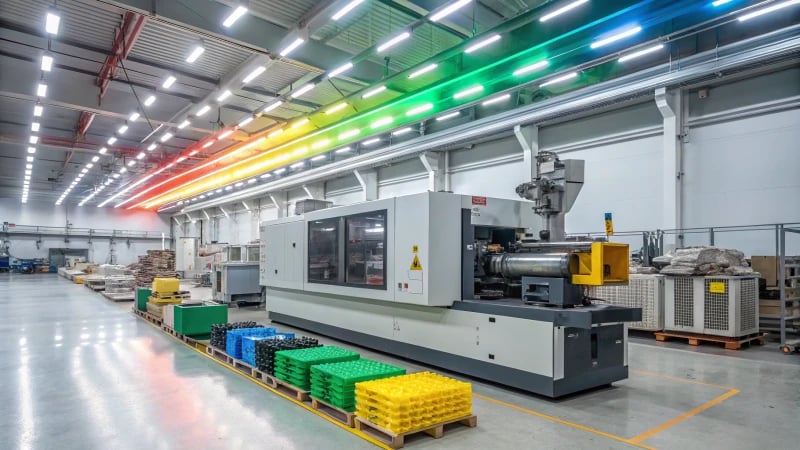
The Economics of Sustainable Materials
I remember the first time I faced the decision of investing in sustainable materials. The upfront cost was daunting, but the potential savings down the line were too promising to ignore. Sustainable materials often lead to reduced waste during production, and let me tell you, watching those savings accumulate is satisfying.
Take bioplastics, for example. They’re derived from renewable sources and can significantly slash our carbon footprint. This not only aligns with environmental regulations14 but also keeps us safe from fines or taxes due to excessive emissions.
Energy Efficiency and Waste Reduction
Switching to sustainable materials like recycled plastics was a game-changer for me. It meant operating at lower processing temperatures, which surprisingly translated into major savings over extensive production runs.
A study showed that using recycled PET (rPET) saved up to 30% energy compared to virgin PET. It was a big win for us as we strived to meet our sustainability goals15. Going green was not just an image; it was a tangible shift in our operations.
Material | Energy Savings | Waste Reduction |
---|---|---|
Recycled PET | 30% | Significant |
Bioplastics | 20% | Moderate |
Durability and Product Longevity
The first time we used durable sustainable materials, I was skeptical. But when those parts extended product life and reduced replacement frequency, I knew we were onto something.
The added bonus? Our customers were thrilled with the quality and longevity of their products. This led to increased brand loyalty, directly impacting long-term profitability. Plus, using materials that meet industry standards16 brought tax incentives and rebates our way—an unexpected but welcome surprise!
Market Trends and Consumer Preferences
In today’s market, I’ve noticed that consumers are increasingly drawn to products with a minimal environmental impact. Integrating sustainable materials isn’t just about staying relevant; it’s about leading the charge.
A recent survey showed that 70% of consumers are willing to pay more for sustainable products. This is a clear signal of the shifting market demand towards environmentally responsible manufacturing practices. Staying updated with market trends17 has been crucial for us to remain competitive and responsive to these changes.
Bioplastics reduce carbon footprint in production.True
Bioplastics are derived from renewable sources, reducing emissions.
Recycled PET uses more energy than virgin PET.False
Recycled PET saves up to 30% energy compared to virgin PET.
What Are the Cost Implications of Material Waste in Injection Molding?
Ever wonder how much material waste is actually costing your injection molding operations?
Material waste in injection molding raises costs through increased raw material use and disposal fees. Optimizing design and processes can reduce waste, improving profitability.
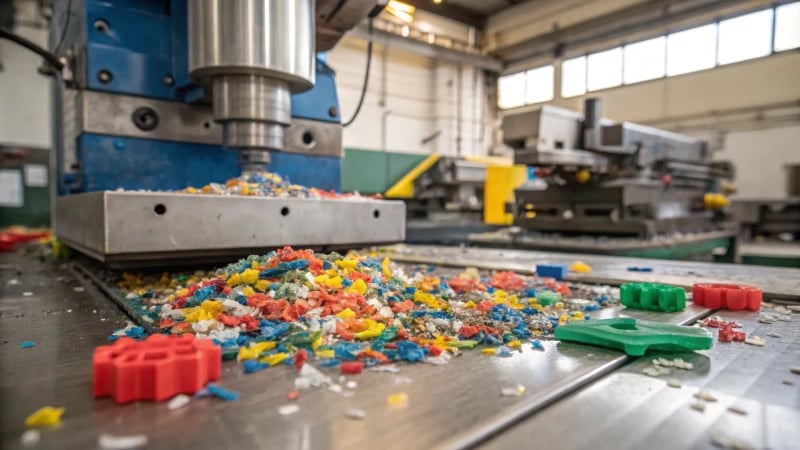
Understanding Material Waste in Injection Molding
I remember the first time I walked into a bustling injection molding factory. The sound of machines, the rhythm of production—it was mesmerizing. But what really caught my attention was the sheer volume of material waste. It made me realize how even small inefficiencies could snowball into significant costs.
Material waste can occur at any stage, whether it’s from design errors18 or production hiccups. Sometimes, it’s just about using a bit too much material to ensure quality. But those bits add up, impacting three key areas:
- Raw Material Costs: Imagine buying a few extra pounds of raw materials every day. Over time, these costs can drain your budget.
- Disposal Costs: It’s not just about throwing away the waste; it’s about the fees for environmental compliance and logistics.
- Production Inefficiencies: Waste slows down everything—like traffic on a busy highway—ramping up labor costs.
Strategies to Reduce Material Waste
- Optimize Product Design: Advanced CAD techniques19 can make all the difference. I’ve seen designs that look like art yet use minimal material.
- Utilize Recycling Processes: Incorporating recycling isn’t just green; it’s smart business. Reusing materials can drastically cut down on raw material needs.
- Regular Maintenance: Keeping machinery in top shape is like regular tune-ups for your car—less breakdowns, more precision, less waste.
Cost Area | Impact of Waste | Mitigation Strategy |
---|---|---|
Raw Material Costs | Increases purchasing costs | Use recycled materials |
Disposal Costs | Higher environmental fees | Implement recycling systems |
Production Inefficiencies | Slows down operations | Invest in efficient machinery |
Leveraging Technology for Waste Reduction
Technology is our best ally in the fight against waste. Using modern solutions like IoT20 sensors and machine learning has been a game-changer for many. These tools provide real-time data monitoring, enabling immediate adjustments to minimize waste. Plus, machine learning algorithms can predict and prevent waste by analyzing past production data.
By adopting these tools, we don’t just save on costs; we contribute to a sustainable future—a goal that resonates with me personally, as it aligns with global environmental initiatives. It’s rewarding to see how technology not only boosts efficiency but also supports sustainability efforts.
Material waste raises raw material costs in injection molding.True
Excess material use leads to buying more than necessary, increasing costs.
IoT sensors increase material waste in injection molding.False
IoT sensors help monitor and reduce waste by providing real-time data.
Conclusion
Material selection in injection molding significantly impacts costs, efficiency, and product quality. Understanding material properties helps optimize production while balancing durability and budget constraints.
-
Discover how ABS is utilized in various product designs, offering insights into its versatility and advantages. ↩
-
Learn why polypropylene is a preferred choice in packaging, highlighting its chemical resistance and durability. ↩
-
Explore the cost benefits of using polystyrene for large-scale manufacturing projects. ↩
-
Understand the role of nylon in automotive applications, focusing on its strength and thermal resistance. ↩
-
Discusses how melting temperatures influence molding efficiency, providing guidance on selecting suitable materials for cost-effective production. ↩
-
Explains how high-performance materials impact mold design, offering strategies for balancing initial costs with long-term benefits. ↩
-
Highlights the advantages of faster cycles in injection molding, helping readers understand potential improvements in production efficiency. ↩
-
Exploring this link will provide insight into how increasing production volumes can reduce costs per unit, allowing for better material choices. ↩
-
Discover how different production volumes necessitate varied manufacturing techniques and how this influences material selection. ↩
-
Explore why PLA is popular in 3D printing and its effects on post-processing. ↩
-
Learn about the acetone smoothing process for achieving smooth finishes on ABS prints. ↩
-
Learn about the acetone smoothing process for achieving smooth finishes on ABS prints. ↩
-
Discover effective post-processing techniques specifically for PETG materials. ↩
-
Understanding current regulations helps manufacturers avoid penalties and align with legal requirements, ultimately saving costs associated with non-compliance. ↩
-
Exploring examples of sustainability goals can inspire strategies that align with broader corporate objectives, enhancing brand reputation and operational efficiency. ↩
-
Knowing industry standards ensures compliance and may offer tax incentives, improving the financial feasibility of using sustainable materials. ↩
-
Understanding consumer preferences helps businesses tailor their offerings to meet market demand, potentially allowing for premium pricing and increased sales. ↩
-
This link offers insights into how common design errors can cause material waste, enabling readers to identify and avoid costly mistakes. ↩
-
Explore advanced CAD techniques that optimize mold designs, helping to reduce material usage and associated costs. ↩
-
Discover how IoT applications can enhance manufacturing efficiency by monitoring and minimizing material waste. ↩