Have you ever wondered what goes into creating those colorful plastic products we see every day?
The process for making masterbatch for injection molding typically involves preparing raw materials, mixing them thoroughly, preparing wax liquids, extruding granules, cooling, and drying them before final packaging. Each step must be tailored to the specific type and application of the masterbatch.
Although this overview provides a snapshot of the masterbatch production process, diving deeper into each step reveals nuances that are critical for achieving optimal results. Explore further to understand best practices and quality control measures that can refine your manufacturing processes.
Extrusion granulation ensures uniform additive distribution.True
Extrusion granulation mixes materials thoroughly, ensuring even additive spread.
What Are the Key Ingredients in Masterbatch Production?
Understanding the key ingredients in masterbatch production is crucial for achieving superior quality in injection molding.
The essential ingredients in masterbatch production include polymers, pigments, additives, and various carrier resins. Each component is selected based on the desired properties of the final product, such as color, durability, or thermal resistance. Proper selection and preparation of these ingredients ensure optimal performance and quality of the masterbatch.
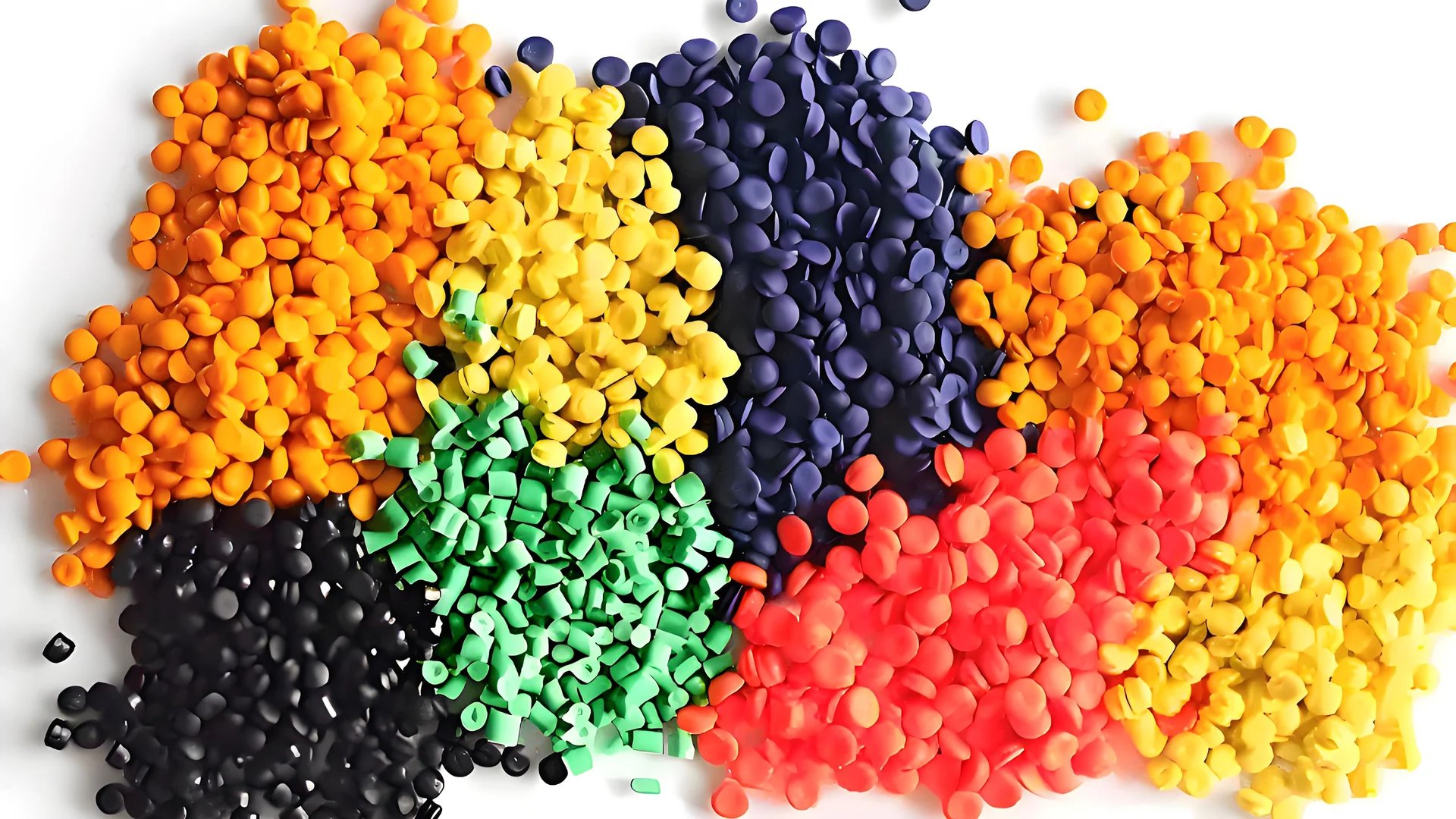
Core Components of Masterbatch
In masterbatch production, the components are meticulously chosen to enhance the properties of the final product. Here’s a breakdown of the fundamental ingredients:
-
Polymers: These form the backbone of the masterbatch. Commonly used polymers include polyethylene (PE), polypropylene (PP), and polyethylene terephthalate (PET). Each polymer brings unique characteristics suitable for specific applications.
-
Pigments: To add color to plastics, pigments are crucial. They are available in various forms such as organic, inorganic, and carbon black. The choice of pigment depends on factors like color fastness, heat stability, and lightfastness.
-
Additives: These are incorporated to impart specific properties like UV stability, flame retardancy, or anti-static features. Additives must be compatible with the polymer matrix to ensure uniform distribution.
-
Carrier Resins: These are used to disperse pigments and additives evenly within the masterbatch. They must be compatible with both the base polymer and other ingredients to maintain consistency.
The Role of Additives
Additives enhance performance by providing additional functionalities. For instance:
-
Antioxidants prevent degradation during processing and extend the lifespan of plastics.
-
UV Stabilizers protect plastics from ultraviolet radiation, preventing discoloration and brittleness.
-
Flame Retardants are essential for applications where fire resistance is critical, ensuring safety standards are met.
Understanding Ingredient Interactions
The interaction between these ingredients is vital for ensuring a high-quality masterbatch. For example, mixing SK2008PETG with chain extenders enhances mechanical properties, while antioxidants prevent thermal degradation during production processes1.
Detailed Case Study: PET/PETG Masterbatch
Consider the production method for PET/PETG ultra-transparent injection molding demolding masterbatch:
-
Raw Material Preparation
- 60-80kg SK2008PETG raw material
- 5-8kg polyester demolding wax
- 8-10kg self-prepared demolding wax
- 2kg chain extender
- 500g antioxidant
- 1kg homogeneous nucleating agent
- 300g high temperature resistant color powder
- 5kg dimethyl silicone oil
-
Mixing & Extrusion
- The SK2008PETG is ground into powder, mixed with other ingredients, and processed through a granulator host to ensure thorough incorporation.
-
Wax Preparation & Integration
- Wax and silicone oil are melted and integrated into the granulator screw, ensuring a consistent texture.
Masterbatch production is a nuanced science where ingredient choice and preparation directly impact performance. By understanding each component’s role, manufacturers can optimize their processes to produce superior quality products.
Polymers form the backbone of masterbatch production.True
Polymers like PE, PP, and PET are essential for masterbatch structure.
Additives are not used in masterbatch production.False
Additives enhance properties like UV stability and flame retardancy.
How Does Wax Liquid Preparation Affect Quality?
Wax liquid preparation is a pivotal step in masterbatch production, impacting the final product’s performance and quality.
Proper wax liquid preparation ensures uniform distribution and integration of components, enhancing the masterbatch’s performance in injection molding. Precise temperature control and thorough mixing are critical to maintaining consistency and quality.
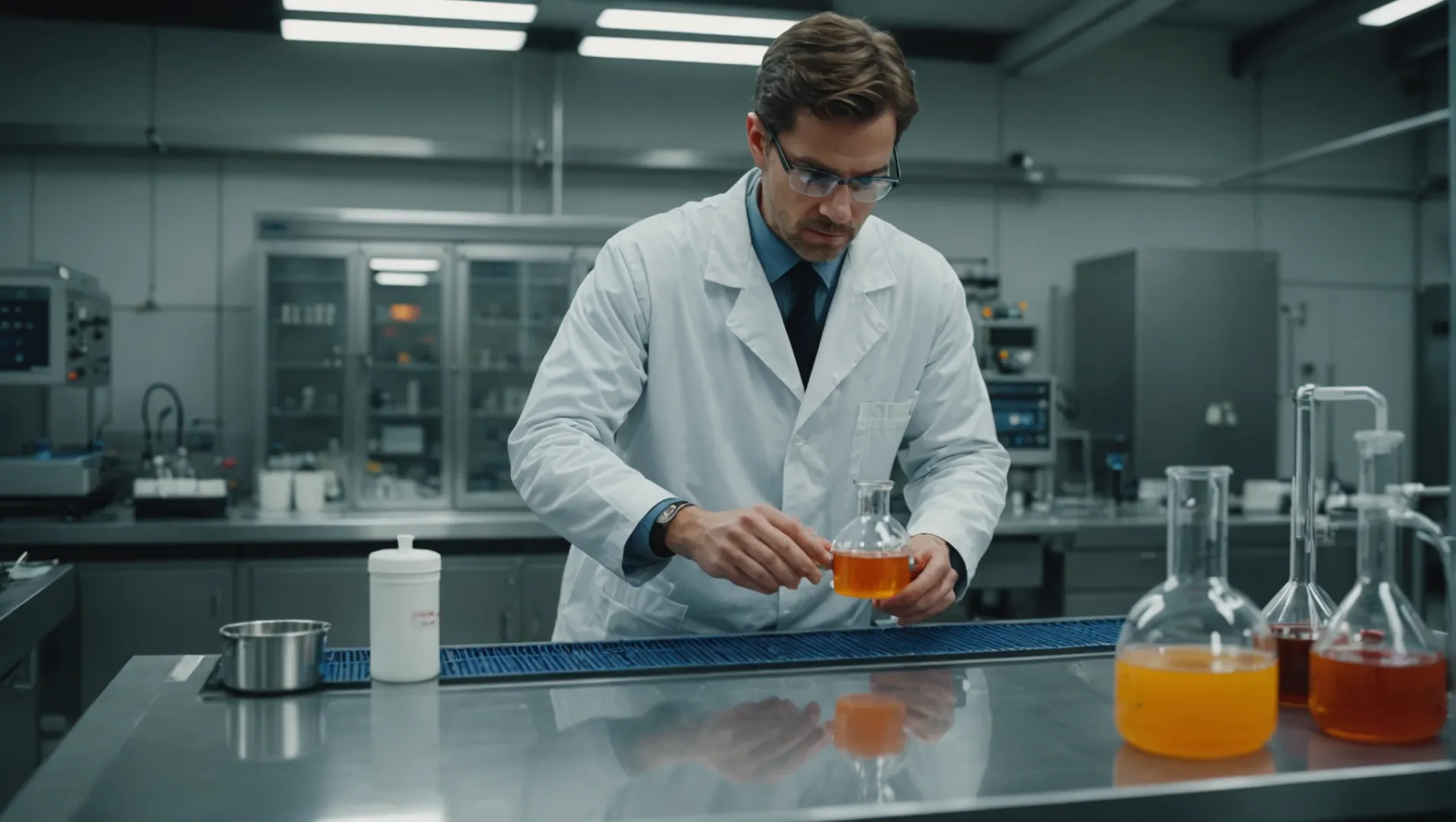
Importance of Wax Liquid Preparation
In the production of PET/PETG ultra-transparent injection molding demolding masterbatch2, the wax liquid preparation phase is integral. This step involves thoroughly stirring all wax components with dimethyl silicone oil before introducing them into the preheating tank. This meticulous blending ensures that the wax melts evenly, which is crucial for maintaining homogeneity in the granules.
Temperature Control
Temperature control during the wax liquid preparation stage can significantly affect the quality of the masterbatch. The preheating tank is typically set to 115 degrees Celsius, ensuring that the wax is completely melted before it’s pumped into the granulator screw. Precise temperature management prevents partial melting or overheating, both of which can lead to defects in the masterbatch, such as uneven texture or compromised structural integrity.
Mixing Techniques
The method of mixing wax with other components also plays a vital role in quality assurance. A liquid plunger pump is often used to introduce the melted wax into the granulator screw, ensuring consistent flow and integration with other materials. This step is crucial to prevent clumping or uneven distribution, which can lead to inconsistencies in the final product’s properties.
Impact on Final Product
Properly prepared wax liquid contributes to a masterbatch with superior dispersion characteristics, improving the aesthetic and functional qualities of the end plastic product. It ensures that additives such as antioxidants and nucleating agents are evenly distributed, enhancing the durability and clarity of the injection-molded items.
Understanding these nuances in wax liquid preparation allows manufacturers to fine-tune their processes, optimizing the quality and performance of their masterbatches for various applications.
Temperature control affects masterbatch quality.True
Proper temperature ensures wax melts completely, preventing defects.
Mixing techniques are irrelevant to product quality.False
Proper mixing ensures even distribution, enhancing product consistency.
Why Is Extrusion Granulation Crucial in Masterbatch Making?
Extrusion granulation is a pivotal process in masterbatch manufacturing, ensuring uniformity and quality of the final product.
Extrusion granulation is crucial in masterbatch making as it ensures uniform distribution of additives, enhances processing efficiency, and achieves desired physical properties in the final product. This step involves mixing, melting, and forming the mixture into granules, which are essential for consistent performance during injection molding.

Understanding the Role of Extrusion Granulation
In the realm of masterbatch manufacturing3, extrusion granulation serves as a cornerstone for achieving product uniformity and enhancing processing capabilities. This process involves the transformation of raw materials into a homogenous blend through a series of precise heating and mechanical actions.
Extrusion granulation begins with the blending of essential raw materials, such as polymers, pigments, and additives. These components are fed into an extruder, where they are subjected to controlled heat and pressure. The use of special threaded components within the extruder ensures thorough mixing and melting, leading to the formation of a continuous stream that is subsequently cut into granules.
Advantages of Extrusion Granulation
-
Uniform Distribution of Additives: One of the primary benefits of extrusion granulation is its ability to ensure even distribution of additives throughout the polymer matrix. This uniformity is crucial for maintaining the desired color and functional properties across all batches.
-
Enhanced Processing Efficiency: The granules produced through extrusion offer enhanced flow characteristics, making them easier to handle and process during subsequent manufacturing stages. This efficiency is particularly valuable when dealing with high-volume production environments.
-
Improved Physical Properties: The extrusion process allows for better control over the physical properties of the masterbatch, such as tensile strength and impact resistance. By optimizing these properties, manufacturers can tailor their products to meet specific application requirements.
Challenges and Considerations
While extrusion granulation offers numerous advantages, it also presents certain challenges that must be addressed. For instance, maintaining optimal temperature and pressure settings is critical to prevent degradation of sensitive additives.
Moreover, troubleshooting common extrusion issues4 such as die buildup or inconsistent output can require expertise and careful monitoring. Implementing advanced control systems can aid in mitigating these challenges by providing real-time feedback and adjustments.
Conclusion
By understanding the intricacies of extrusion granulation, manufacturers can harness its potential to produce high-quality masterbatches that meet rigorous industry standards. As technology advances, continuous improvements in extrusion techniques promise even greater efficiencies and capabilities in masterbatch production.
Extrusion ensures even additive distribution in masterbatches.True
Extrusion granulation guarantees uniform additive distribution, enhancing product consistency.
Masterbatch extrusion requires no temperature control.False
Temperature control is vital to prevent degradation of additives during extrusion.
What Quality Control Measures Are Essential in Masterbatch Production?
Ensuring consistent quality in masterbatch production requires rigorous quality control measures to guarantee the performance and reliability of the final product.
Key quality control measures in masterbatch production include raw material inspection, process monitoring, quality testing of finished products, and adherence to safety standards. Implementing these measures helps maintain product consistency and performance.

Raw Material Inspection
The foundation of any high-quality masterbatch lies in the thorough examination of raw materials5. Ensuring that each batch of raw materials meets specific standards is crucial. For example, SK2008PETG raw material should be inspected for purity and consistency before use. Variations can lead to deviations in the final product’s performance.
Process Monitoring
Continuous monitoring of the manufacturing process ensures that each step, from mixing to granulation, adheres to established parameters. This includes keeping a close eye on temperature settings during wax liquid preparation and ensuring that the extrusion granulation process is executed precisely. Real-time data collection and analysis can help identify issues promptly, reducing the risk of defects.
Quality Testing of Finished Products
Post-production testing is essential for validating the quality of the masterbatch. Tests should include checking the color consistency, particle size distribution, and thermal stability. Using techniques such as spectrophotometry for color analysis ensures that each batch meets aesthetic requirements.
Adherence to Safety Standards
Compliance with industry safety standards protects both the workers and the end-users. This involves regular safety audits and ensuring that all equipment meets regulatory requirements. Implementing protocols for safe handling and storage of chemicals is also vital.
Incorporating these quality control measures into the production process not only enhances product quality but also boosts efficiency and minimizes waste. For instance, by consistently applying these checks, manufacturers can reduce the likelihood of costly recalls or reworks, ultimately supporting a sustainable production model.
Raw material inspection is crucial for masterbatch quality.True
Inspecting raw materials ensures purity and consistency, vital for quality.
Process monitoring is unnecessary in masterbatch production.False
Continuous process monitoring ensures adherence to parameters, reducing defects.
Conclusion
Masterbatch production requires precise execution to ensure quality. By understanding these processes, manufacturers can enhance efficiency and product outcomes.
-
Discover how polymer-additive interactions affect masterbatch quality and performance.: Ideally, additive needs to interact strongly with the polymer matrix, minimizing their surface energy. Some of these dispersion problems can be overcome … ↩
-
Learn about specialized methods for PET/PETG masterbatch production.: The invention discloses a PET / PETG ultra-transparent injection molding demolding master batch and a preparation method thereof. The PET / PETG ultra- … ↩
-
Discover how extrusion ensures consistency and quality in masterbatch manufacturing.: After adding the carrier, the color masterbatch is obtained by extrusion and granulation. Phase transfer requires organic solvents and … ↩
-
Learn how to tackle typical challenges in the extrusion process effectively.: Main motor speed is too low;. Main motor bearing temperature is too high;. Main motor winding temperature is too high; ; Instrument air pressure … ↩
-
Learn why raw material inspection is critical for quality assurance.: Raw material inspection is a critical aspect of ensuring product quality and reliability. This comprehensive guide delves into the nuances of this essential … ↩