MANUFACTURING
blog & article
read our latest newsletter
Whether you’re curious about material selection, product design, mold design, mold making and injection molding, feel free to ask us anything. Our team is ready to provide the guidance and insights you need.
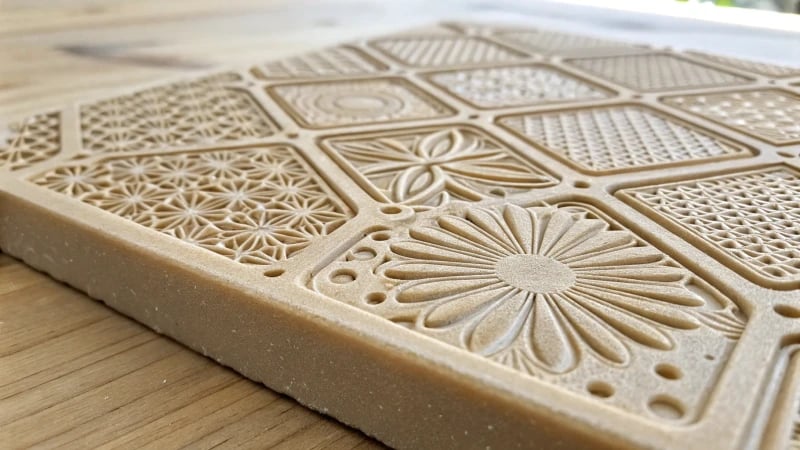
How Can You Texture Injection Molded Surfaces Effectively?
This article delves into the various techniques for effectively texturing injection molded surfaces. Methods such as chemical etching, laser texturing, electrospark machining (EDM), and physical vapor deposition (PVD) are explored in detail. Each technique offers unique benefits tailored to different ...
MANUFACTURING

What Are the Mechanics Behind a Three-Plate Mold?
Three-plate molds are essential tools in plastic manufacturing, consisting of a fixed plate, an intermediate runner plate, and a moving plate. This design allows for improved efficiency and quality control by enabling flexible sprue systems and precise melt flow paths. ...
MANUFACTURING
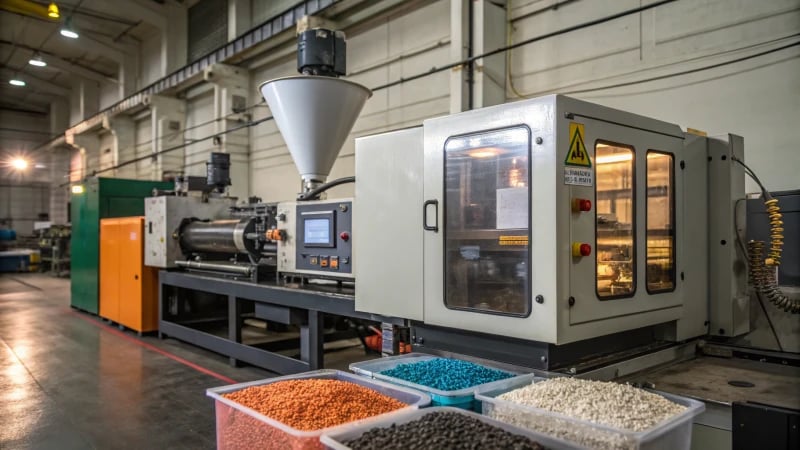
Is Bakelite Suitable for Injection Molding?
Bakelite can be effectively used in injection molding, but it presents unique challenges due to its thermosetting properties. This article explores the essential requirements for successful Bakelite molding, including precise temperature control during both the injection and curing phases. Adequate ...
MANUFACTURING
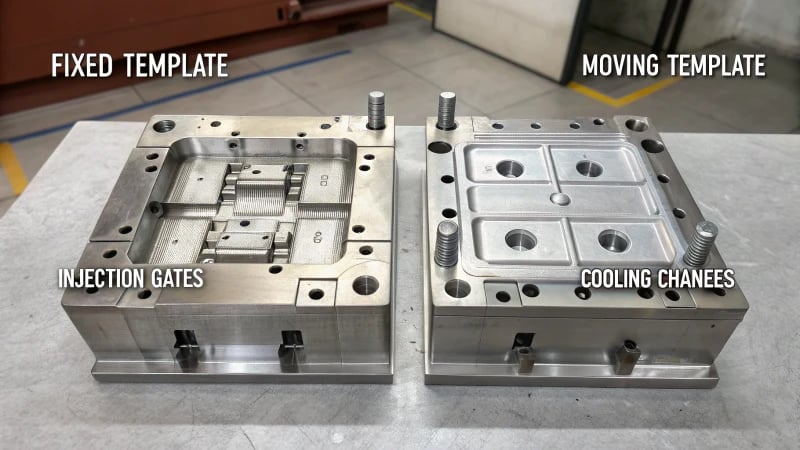
How Does a Two-Plate Mold Function in Injection Molding?
Two-plate molds are essential in injection molding, featuring a moving and fixed template that forms the cavity for molten plastic. Their straightforward design allows for efficient production of various plastic components, including consumer electronics cases, toys, and containers. While they ...
MANUFACTURING
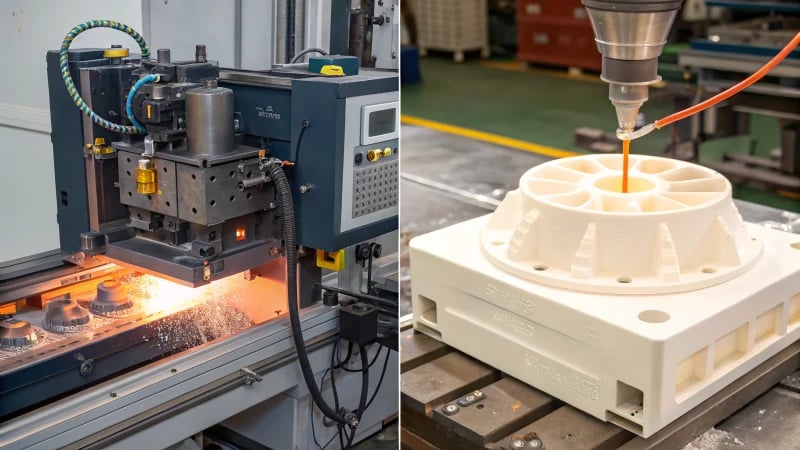
Injection Molding vs. Rotational Molding: What’s the Difference?
This article explores the differences between injection molding and rotational molding, two key manufacturing processes for plastic parts. Injection molding is best suited for high-volume production of intricate designs, utilizing molten plastic injected into precise molds under high pressure. In ...
MANUFACTURING
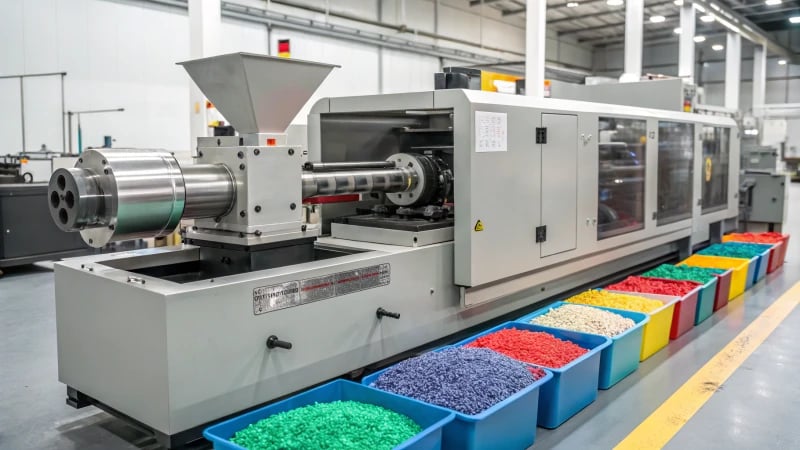
How Does Bakelite Injection Molding Differ from Other Plastic Injection Molding?
This article explores the distinct characteristics of Bakelite injection molding compared to other plastic processes. Key differences include a 1:1 screw compression ratio for Bakelite versus 1:3-1:4.5 for thermoplastics, and the fusing process of Bakelite at higher temperatures (150-180°C) compared ...
MANUFACTURING
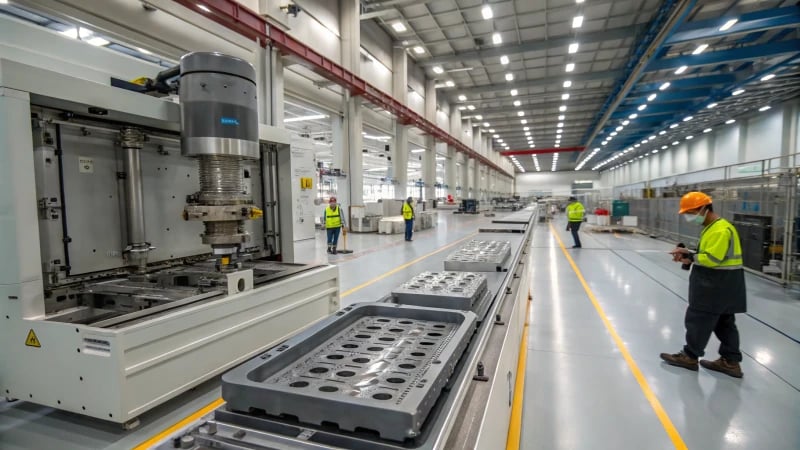
How Efficiently Can an Injection Molding Machine Operate with 6 Cavity Molds?
This article explores the efficient operation of injection molding machines using 6-cavity molds. Key factors include adequate clamping force to prevent defects like flash, sufficient injection capacity to fill all cavities uniformly, proper mold mounting for compatibility with machine specifications, ...
MANUFACTURING
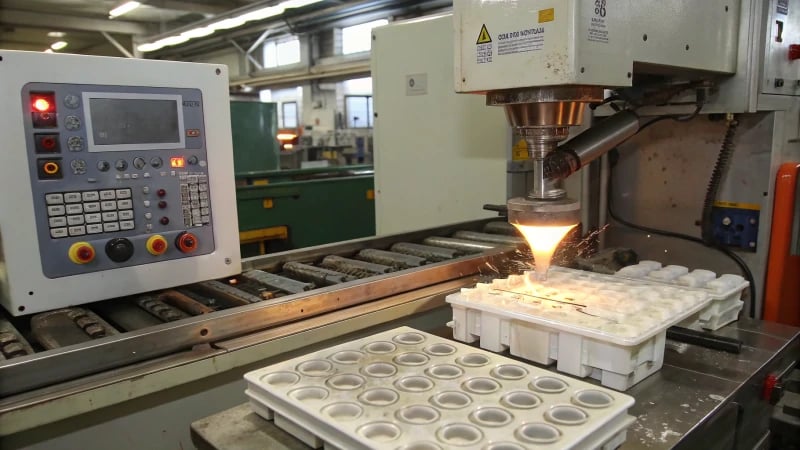
How Does an Injection Molding Machine Create Button Molds?
This article explores how injection molding machines produce button molds. It details the importance of mold design, including cavity shape and ejection systems, as well as material selection like ABS and polypropylene. The injection molding process involves melting plastic pellets, ...
MANUFACTURING
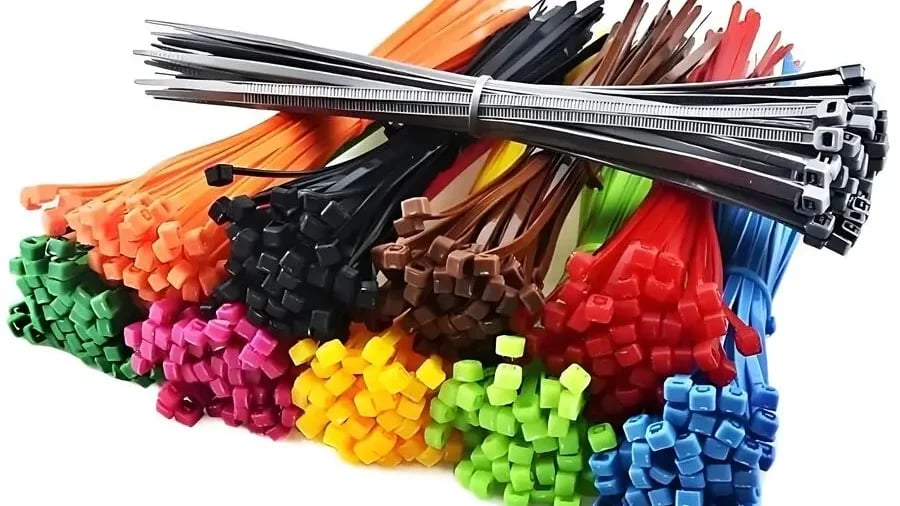
How Does an Injection Molding Machine Produce a Nylon Cable Tie?
This article explores how injection molding machines create nylon cable ties. It details the importance of mold design, material selection (Nylon 6/6), and the injection molding process. Each step is crucial for producing durable and flexible cable ties that meet ...
MANUFACTURING

How Can Injection Molding Machines Be Used to Manufacture Phone Cases?
Discover how injection molding machines manufacture phone cases by heating plastic pellets, injecting them into molds, and maintaining strict quality control. This process involves precise mold design, material selection like TPU or PC, and rigorous inspections to ensure each case ...
MANUFACTURING
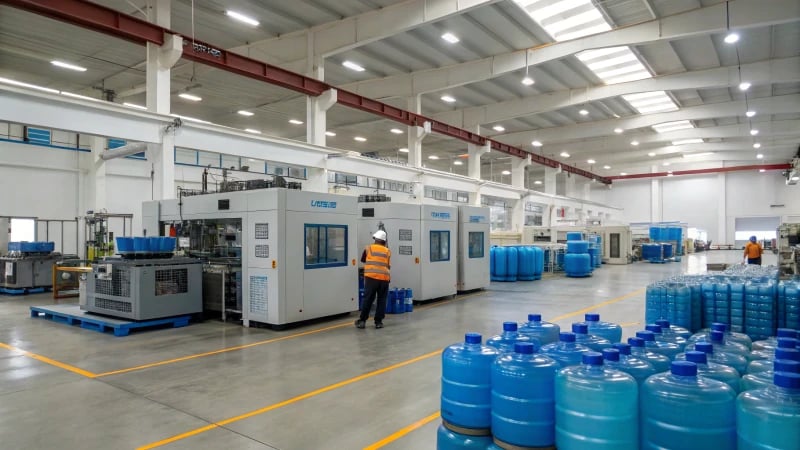
How Do Injection Molding Machines Produce Water Tanks?
This article explores how injection molding machines produce water tanks, detailing the intricate processes involved from mold design to material selection. It highlights the importance of choosing suitable thermoplastics like HDPE and PP for their durability and chemical resistance. The ...
MANUFACTURING
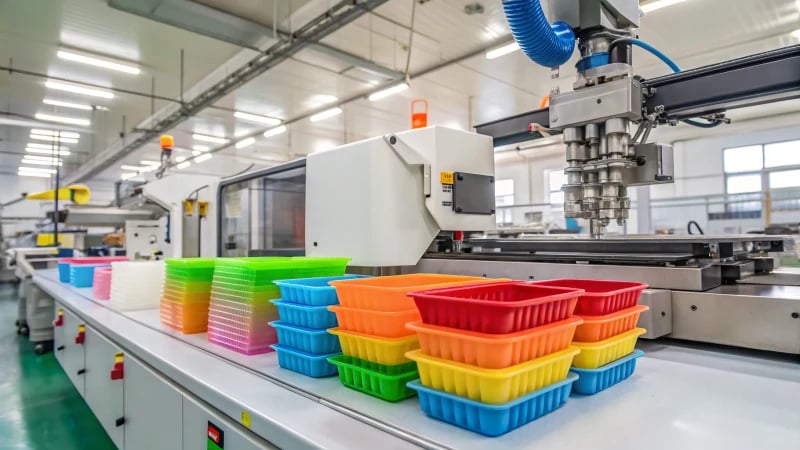
How Can Injection Molding Revolutionize the Production of Food Containers?
Injection molding is transforming the production of food containers by enhancing efficiency and sustainability. This process utilizes food-grade plastics like polypropylene and high-density polyethylene to create durable, safe containers that comply with FDA regulations. Key considerations include selecting appropriate materials, ...
MANUFACTURING
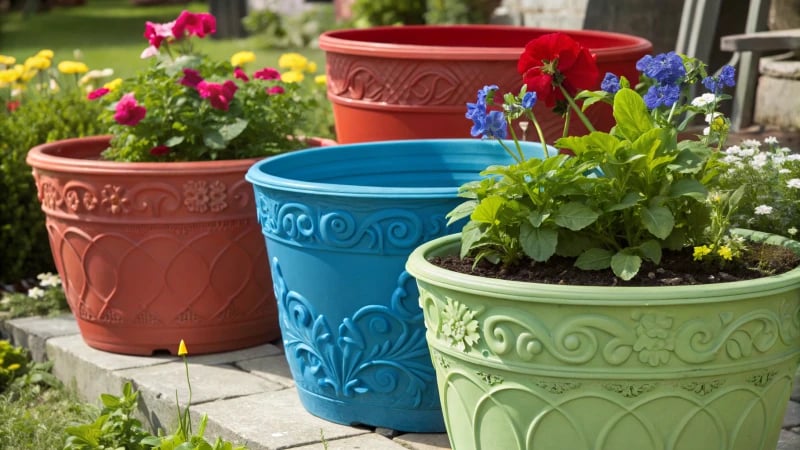
How Can Injection Molding Machines Be Used to Manufacture Flower Pots?
This article explores how injection molding machines are utilized to manufacture flower pots. It details the process of designing custom molds, selecting appropriate materials like polypropylene and HDPE, and the efficient injection-molding method that produces consistent, high-quality pots. The advantages ...
MANUFACTURING
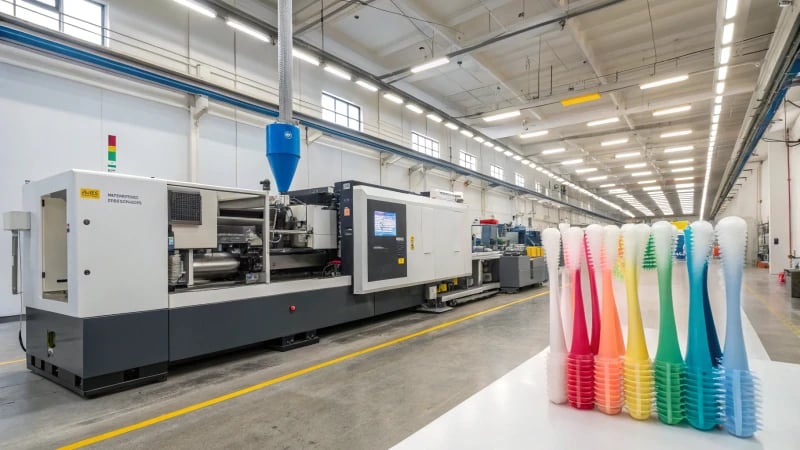
How Are Toothbrushes Made Using Injection Molding Machines?
This article explores the fascinating process of toothbrush manufacturing through injection molding. It details how complex molds are designed to create ergonomic handles and heads, the selection of thermoplastic materials like polypropylene for durability and flexibility, and the precise injection ...
MANUFACTURING
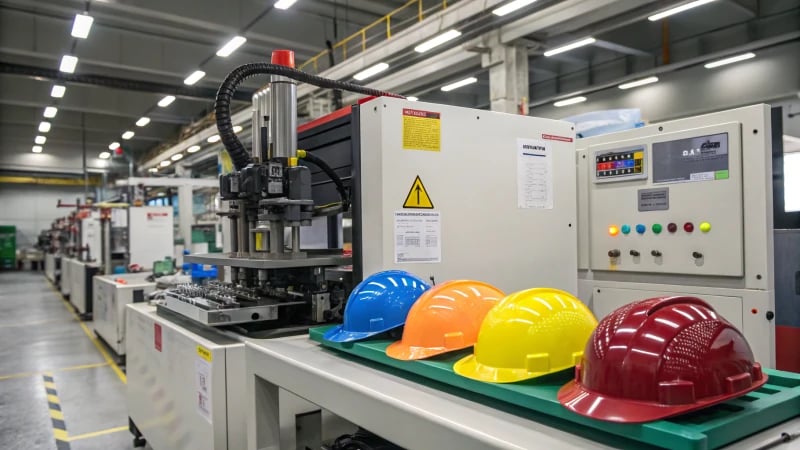
How Can an Injection Molding Machine Be Used to Make Helmets?
This article explores how injection molding machines are used to manufacture helmets. It covers material selection, including polycarbonate and ABS for their impact resistance and cost-effectiveness. The importance of mold design is highlighted, detailing how molds must conform to the ...
MANUFACTURING
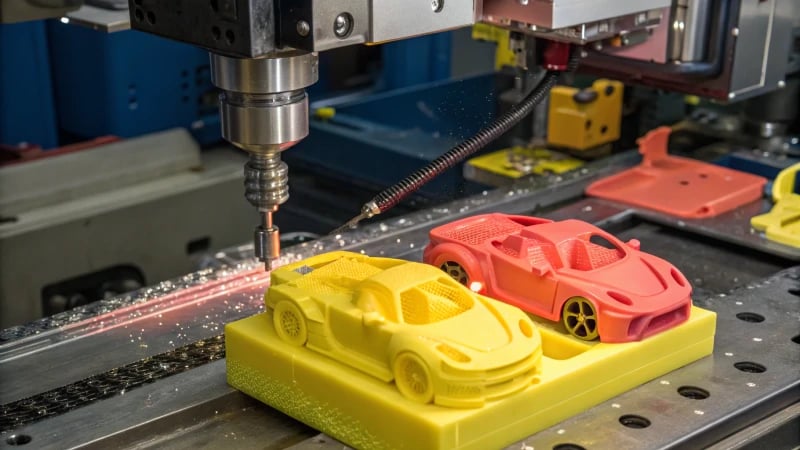
How Can an Injection Molding Machine Create a Toy Car?
This article explores how injection molding machines manufacture toy cars. It details the critical steps involved: designing molds for car bodies, wheels, and axles; selecting appropriate plastics like ABS and PMMA; executing the injection molding process by melting pellets and ...
MANUFACTURING
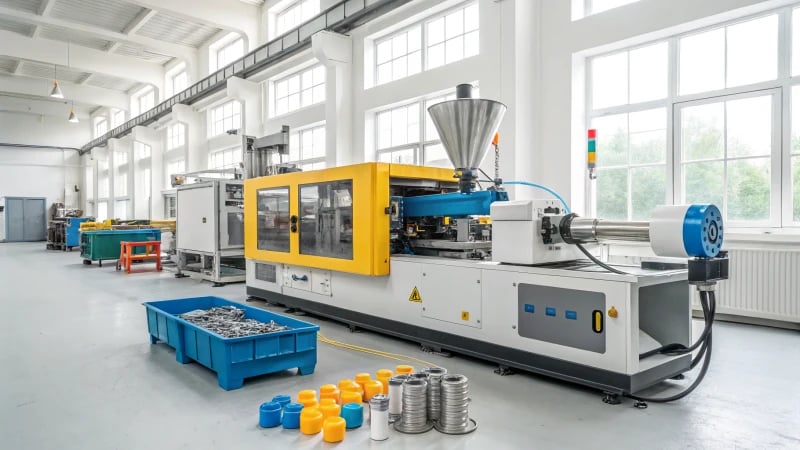
Can Injection Molding Machines Produce Both PPR and PVC Fittings?
This article explores how injection molding machines can produce both PPR (polypropylene random copolymer) and PVC (polyvinyl chloride) fittings. It highlights the advantages of using injection molding for each material, detailing the unique process requirements for optimal production. For PPR, ...
MANUFACTURING
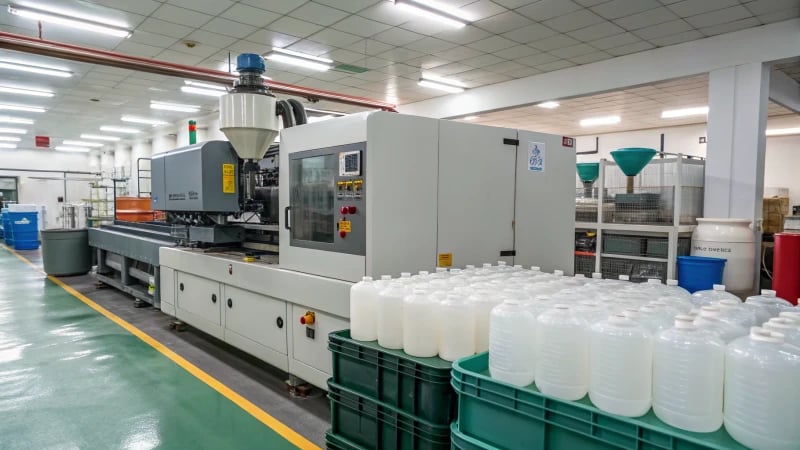
Die Casting vs. Injection Moulding: What Are the Key Differences?
This article explores the key differences between die casting and injection moulding, two essential manufacturing processes. Die casting primarily uses non-ferrous metals like aluminum and zinc, requiring high temperatures and pressures to create strong, precise components. In contrast, injection moulding ...
MANUFACTURING
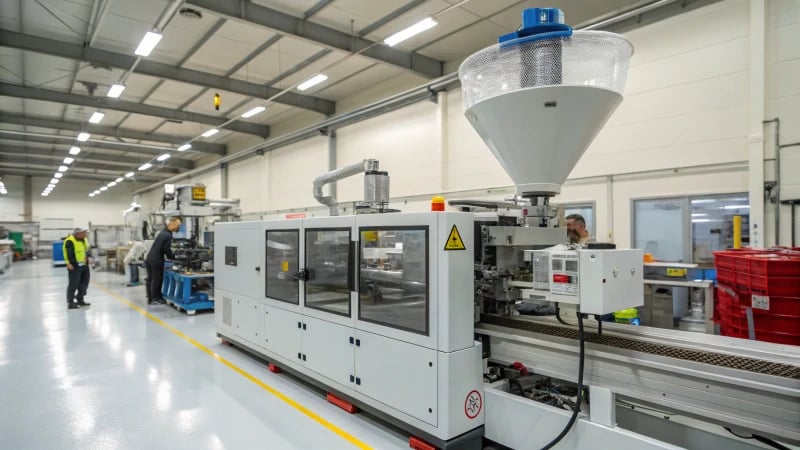
How Efficiently Can an Injection Molding Machine Produce PVC Fittings?
This article explores how injection molding machines produce PVC fittings with efficiency. It highlights the importance of material compatibility, custom mold design, and process control in achieving high-quality outputs. Additionally, it addresses challenges such as heat stability and the need ...
MANUFACTURING
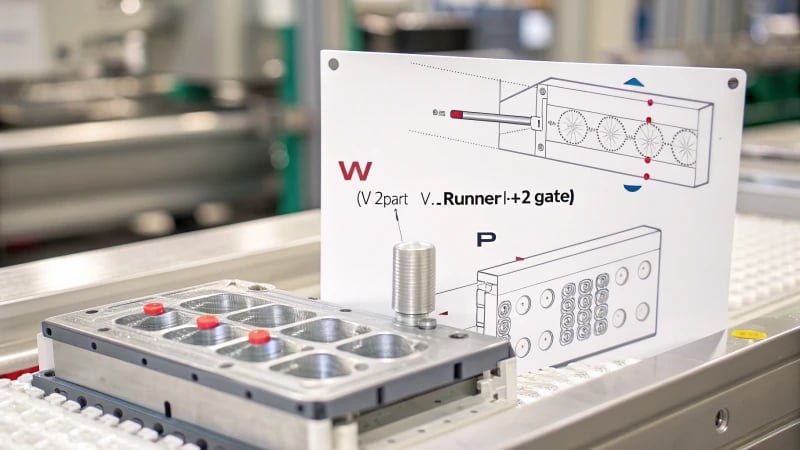
What Are the Steps to Calculate Shot Weight in Injection Molding?
Calculating shot weight in injection molding is essential for optimizing material use and product quality. This guide outlines the steps to determine shot weight using theoretical methods—calculating part volume with geometric formulas—and practical approaches like machine metering systems or weighing ...
MANUFACTURING
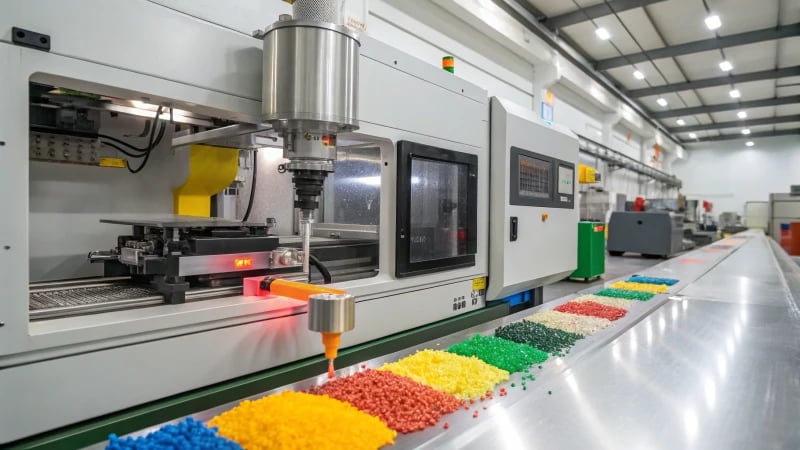
How Do Plastic Injection Molding Machines Create Eyeglasses?
This article explores how plastic injection molding machines are used to manufacture eyeglass frames. It details the importance of precise mold design and material selection, highlighting polycarbonate's benefits for durability and style. While frames are efficiently produced through this process, ...
MANUFACTURING
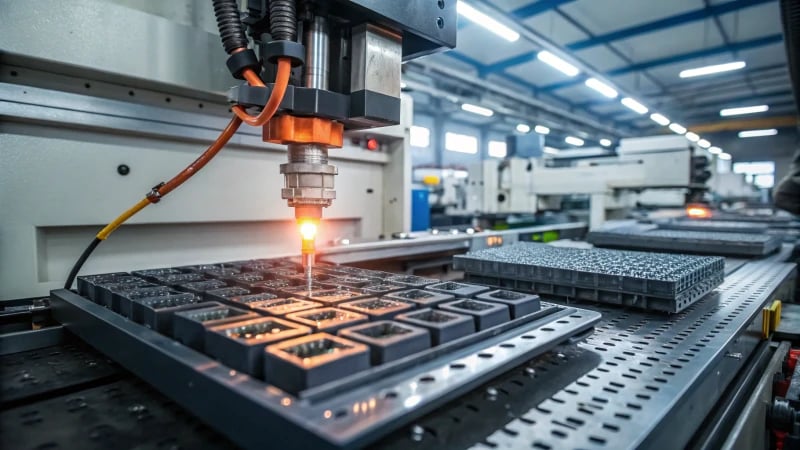
How Does an Injection Molding Machine Create a Keyboard?
This article explores the intricate process of how injection molding machines manufacture keyboards. It details the steps involved in creating keycaps and bases using materials like ABS and polycarbonate. From designing molds to selecting appropriate materials, melting plastics, and assembling ...
MANUFACTURING
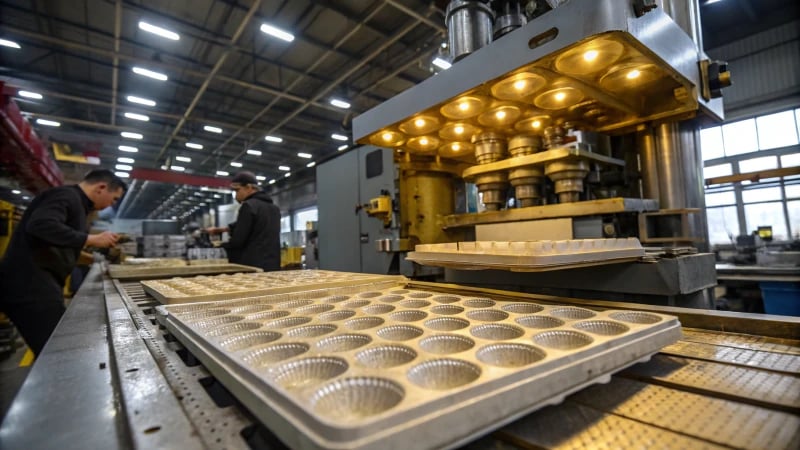
How Can You Produce an Egg Tray Using an Injection Molding Machine?
Discover the fascinating process of producing egg trays with injection molding. This article delves into essential aspects such as mold design, including cavity shape and ejection systems, material selection between polystyrene and polypropylene, and the detailed steps of the injection ...
MANUFACTURING
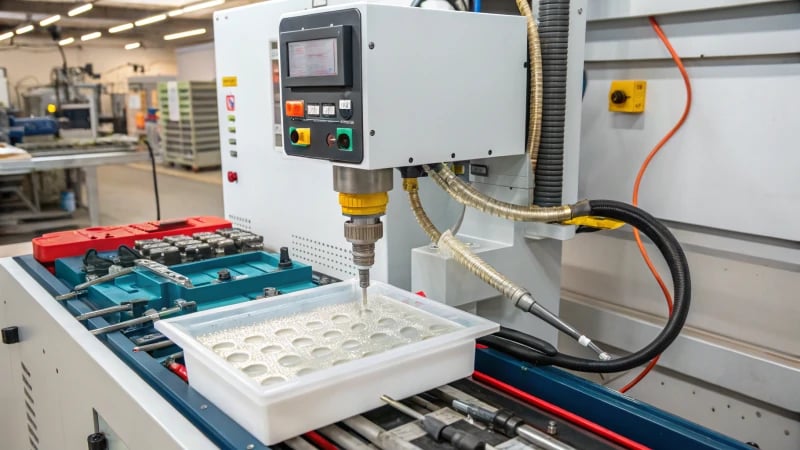
How Do Injection Molding Machines Manufacture Rulers?
The process of manufacturing rulers through injection molding involves several intricate steps. It begins with designing a custom mold that shapes the ruler and engraves precise measurements. The right thermoplastic material, such as Acrylonitrile Butadiene Styrene (ABS) or Polypropylene (PP), ...
MANUFACTURING
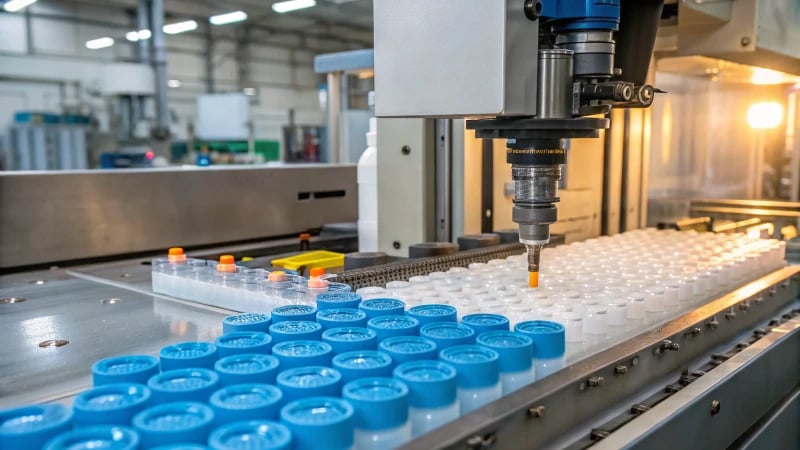
How Do Injection Molding Machines Produce Bottle Caps?
The process of producing bottle caps using injection molding involves designing precise molds, selecting suitable materials like polypropylene, and employing an injection machine to shape the caps. Quality control is crucial to ensure each cap meets industry standards. After molding, ...
MANUFACTURING
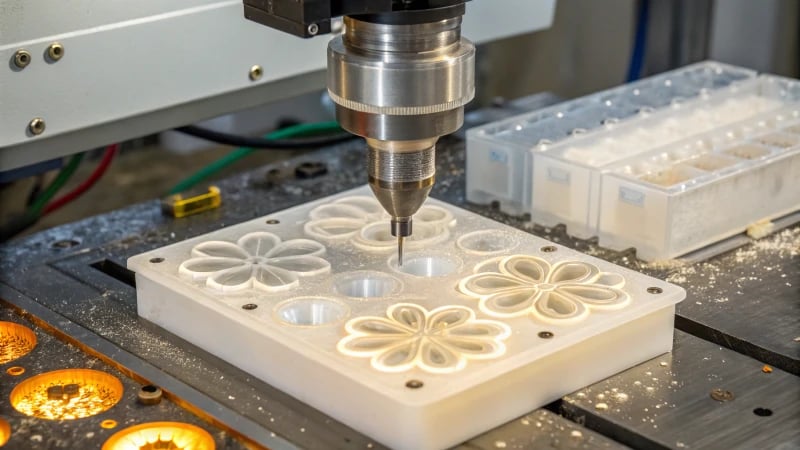
How Do Injection Molding Machines Create Plastic Flowers?
This article explores how injection molding machines bring plastic flowers to life. It delves into the importance of mold design, material selection, and the operational process involved in creating these lifelike floral components. The piece highlights the significance of choosing ...
MANUFACTURING
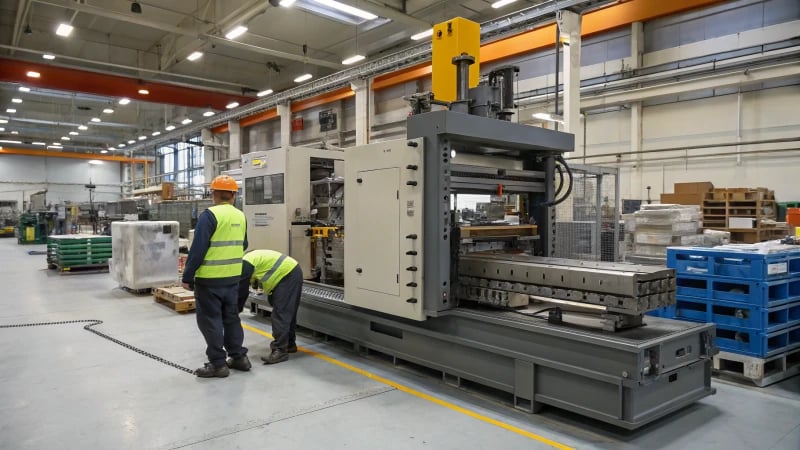
What Size Injection Molding Machine is Needed for an Air Conditioning Shell?
Selecting the appropriate injection molding machine for air conditioning shells involves evaluating several factors including shell dimensions, structural complexity, material type, and mold cavity count. Machines generally require clamping forces between 650 to 1350 tons. Larger or more complex shells ...
MANUFACTURING
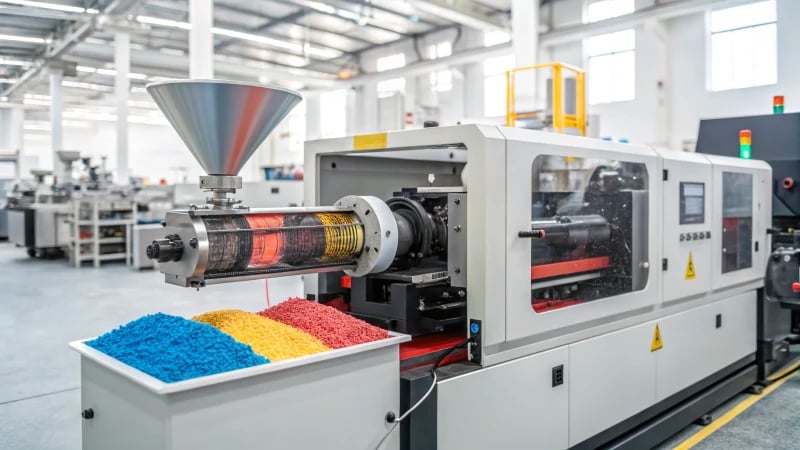
How Much Capacity Does a Plastic Injection Molding Machine Have?
This article explores the essential factors determining the capacity of plastic injection molding machines: clamping force, shot volume, and production rate. Clamping force is vital for maintaining mold integrity during injection; small machines typically exert 5-10 tons while large industrial ...
MANUFACTURING

How Can an Injection Molding Machine Produce Plastic Spoons?
This article explores the fascinating process of producing plastic spoons using injection molding machines. It details how these machines melt plastic pellets and inject molten plastic into spoon-shaped molds under high pressure. The method ensures high precision and efficiency while ...
MANUFACTURING
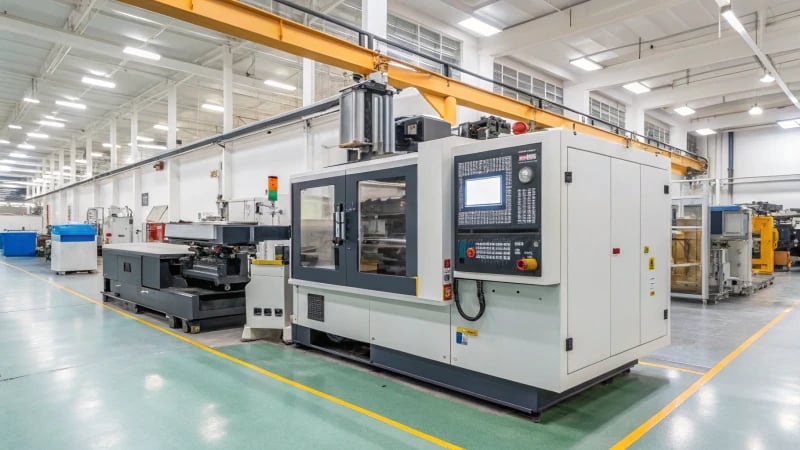
How Do You Determine the Capacity of a Plastic Injection Molding Machine?
Understanding the capacity of plastic injection molding machines involves three key factors: clamping force, shot volume, and production rate. Clamping force, measured in tons, ensures molds remain closed during injection to prevent defects. Shot volume indicates the maximum amount of ...
MANUFACTURING