Have you ever felt the frustration of a production line halted by material issues? I know I have. Injection molding can be a tricky dance, especially when it comes to maintaining fluidity. Let’s explore how we can master this process together!
To maintain material fluidity in injection molding, focus on selecting suitable materials with good flow properties, controlling temperature and pressure settings precisely, and optimizing mold design. These practices ensure efficient mold filling and reduce defects.
While these initial steps provide a foundational understanding, further insights into specific techniques, such as optimizing process parameters and mold maintenance, can significantly enhance your production efficiency. Let’s delve deeper into these essential practices.
Material drying reduces injection molding defects.True
Drying removes moisture, preventing increased viscosity and defects.
What Role Does Material Selection Play in Fluidity?
Choosing the right material is crucial for achieving optimal fluidity in injection molding processes.
Material selection influences fluidity significantly in injection molding. Choosing plastics with inherent good flow properties, considering molecular weight distribution, and ensuring proper drying are essential steps. These practices help reduce processing challenges and enhance the quality of molded products.
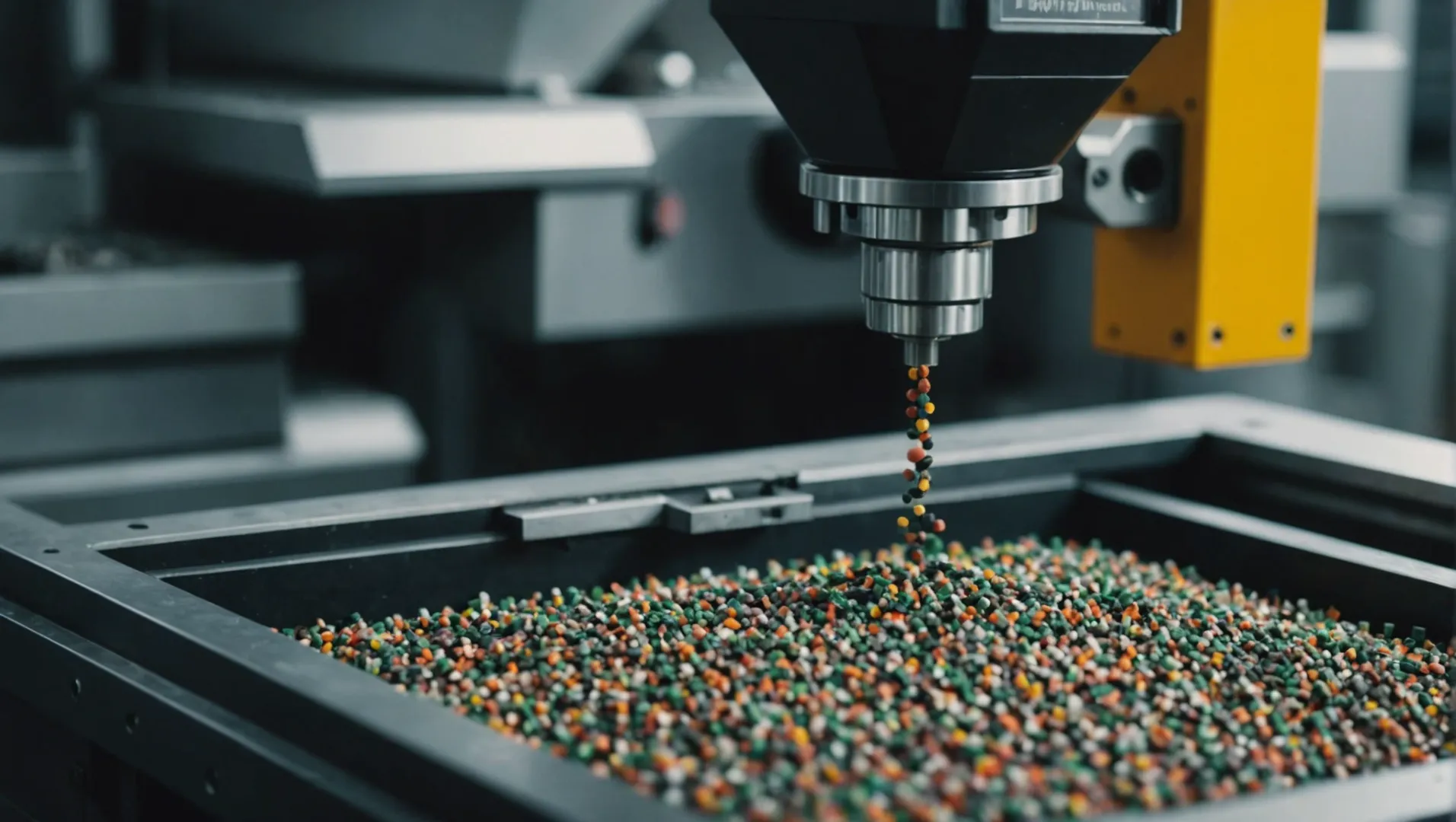
The Impact of Material Properties on Fluidity
In the realm of injection molding, material properties1 play a pivotal role in determining how well a material flows during the process. Materials such as polyethylene and polypropylene are renowned for their excellent fluidity due to their lower viscosity, making them ideal for products requiring intricate designs and thin walls. On the contrary, engineering plastics like polycarbonate may pose challenges due to their higher viscosity but can be optimized for specific applications where strength and rigidity are paramount.
Selecting the right material often starts with understanding its molecular structure. A narrow molecular weight distribution is advantageous as it typically results in a more predictable and manageable flow behavior. This regular molecular structure allows the material to transition smoothly through the molding stages, minimizing potential defects such as short shots or incomplete filling.
Importance of Material Drying
Moisture is a silent adversary in the injection molding process. Many plastic materials are hygroscopic, meaning they absorb moisture from the environment, which can drastically affect their flow properties. Moisture within the material leads to increased viscosity, causing issues like splay marks and poor surface finishes.
Proper drying techniques—such as oven drying, hot air drying, or vacuum drying—are essential to ensure that materials reach the mold in optimal condition. The drying parameters should be tailored to each material’s unique requirements to avoid thermal degradation while effectively removing moisture.
Balancing Material Costs and Performance
While choosing materials with excellent fluidity can simplify the injection molding process, it is also crucial to balance this choice with cost and performance considerations. High-flow materials may come at a premium, so it’s important to assess whether their benefits justify their cost in the context of your specific product requirements.
In scenarios where cost constraints exist, exploring alternatives such as modifying existing materials with additives or employing advanced processing techniques may offer a viable solution without compromising too heavily on fluidity or product quality.
By thoroughly understanding and selecting materials based on their fluidity characteristics, manufacturers can streamline their injection molding processes, improve product quality, and potentially lower production costs. The choice of material serves as a foundation upon which other optimizations, like temperature control and mold design, build upon for enhanced production efficiency.
Polyethylene has lower viscosity than polycarbonate.True
Polyethylene's lower viscosity enhances fluidity, unlike polycarbonate.
Moisture reduces viscosity in hygroscopic materials.False
Moisture increases viscosity, hindering material flow in molding.
How Can Temperature Control Improve Material Flow?
Temperature control is crucial in injection molding, influencing material fluidity and overall production efficiency.
Effective temperature control enhances material flow by reducing viscosity, ensuring consistent mold filling, and minimizing defects in injection molding processes.

Importance of Barrel Temperature Management
The barrel temperature plays a pivotal role in controlling the viscosity of plastic materials. By adjusting the temperature across different sections of the barrel, manufacturers can ensure optimal fluidity for injection molding.
- Gradient Heating: Typically, the barrel’s temperature near the hopper is set lower to prevent premature melting and material bridging, whereas the temperature closer to the nozzle is higher to ensure complete melting.
- Material-Specific Settings: Each material requires specific temperature settings. For instance, polyethylene2 might need lower temperatures compared to polycarbonate due to its inherent fluidity differences.
Impact of Mold Temperature on Flow
Mold temperature directly affects the cooling rate of materials, thus influencing their flow characteristics.
- Increased Mold Temperature: Elevating mold temperature can be particularly beneficial for materials with low fluidity or products with thin walls. It allows the material to fill the cavity more easily before solidifying.
- Balancing Act: While higher mold temperatures improve flow, they can also prolong cycle times and increase energy consumption. Therefore, finding a balance tailored to material and product needs is critical.
Role of Injection Pressure and Speed
Temperature adjustments often go hand-in-hand with tweaks in injection pressure and speed to optimize flow.
- Pressure Adjustments: Higher injection pressure can facilitate better flow but must be moderated to avoid mold damage or product defects like flash.
- Speed Considerations: Faster injection speeds can aid flow, especially in complex or thin-walled parts, though they may also introduce issues like gas marks.
Integrating Temperature Control with Process Parameters
Successful temperature control requires an integrated approach with other process parameters. This holistic view ensures consistent material flow and product quality:
- Holding Pressure and Time: These factors help maintain flow post-injection, compensating for any viscosity increases as the material cools.
- Mold Maintenance: Regular upkeep ensures that temperature control measures are effective, as clean molds facilitate better heat transfer and flow.
In conclusion, meticulous temperature control in injection molding is not only about setting numbers on a machine but understanding and adapting to the nuanced interplay between temperature and other critical process variables.
Higher mold temperature improves material flow in injection molding.True
Elevating mold temperature enhances flow, especially for low-fluidity materials.
Lower barrel temperature prevents premature melting in injection molding.True
Setting lower temperatures near the hopper avoids early melting and bridging.
What Are Effective Mold Design Strategies for Better Flow?
Mold design is critical in ensuring efficient flow and reducing defects in injection molding.
Effective mold design strategies, including gate and runner optimization, and regular maintenance, enhance material flow by minimizing resistance and ensuring even distribution.
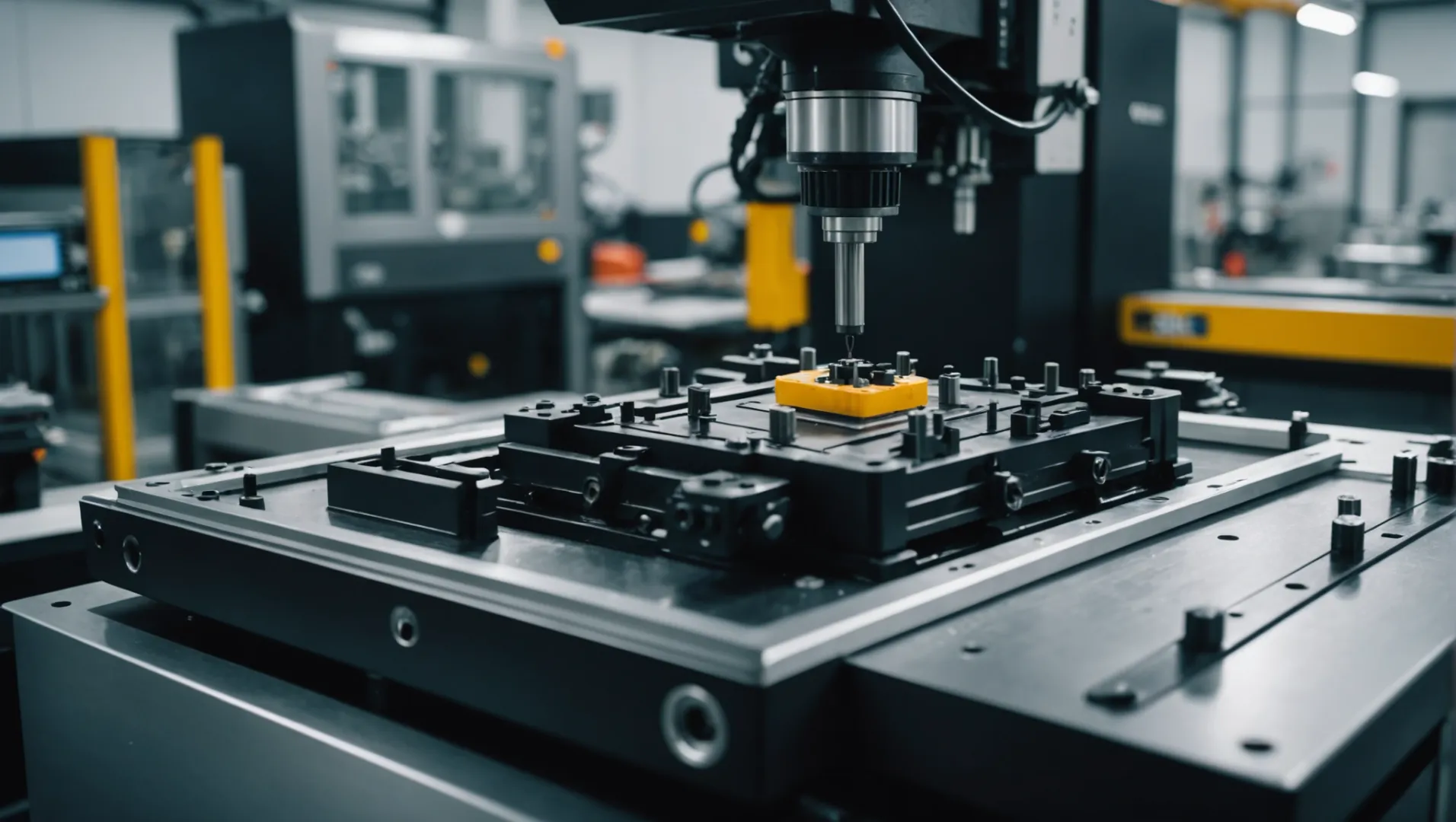
Gate Design: The Entry Point to Success
One of the most influential elements in mold design is the gate. The gate’s size, shape, and position can significantly impact the flow of materials. A larger gate can lower flow resistance, improving fluidity. Different gate shapes like fan gates or latent gates allow materials to fill the mold cavity evenly. For instance, a fan gate spreads the material over a broader area, ideal for large parts, while a pin-point gate is perfect for small, precise components.
Runner Design: Streamlining the Flow Path
Runners are the pathways that guide molten material into the mold cavities. Optimizing the runner system is essential to reduce material resistance during flow. Typically, circular or trapezoidal runners offer minimal flow resistance. The dimensions should align with material characteristics and injection machine capabilities. A well-designed runner layout ensures uniform distribution across cavities, enhancing the filling effect.
Runner Shape | Resistance Level | Recommended Use |
---|---|---|
Circular | Low | High-flow materials |
Trapezoidal | Medium | General use |
Rectangular | High | Low-flow materials or specialized use |
Mold Maintenance: Ensuring Longevity and Quality
Regular mold maintenance is crucial for preserving accuracy and surface quality. Cleaning dirt and residue prevents flow obstructions, while lubrication reduces friction resistance. Proper rust prevention methods ensure long-term usability. Maintaining the mold’s integrity supports consistent material flow and product quality.
Explore more about gate design strategies3
Leveraging Additives for Enhanced Flow
Additives can further improve fluidity in injection molding by altering the material’s properties. Lubricants decrease friction, while plasticizers reduce viscosity, enhancing flow without compromising performance. However, the choice of additives should align with product specifications to avoid negative impacts.
Learn about runner design optimizations4
These mold design strategies play a pivotal role in optimizing material flow and ensuring high-quality production outcomes. By focusing on these aspects, manufacturers can significantly reduce defects and improve efficiency.
Larger gates increase flow resistance in mold design.False
Larger gates actually decrease flow resistance, improving material fluidity.
Regular mold maintenance improves product quality.True
Maintenance prevents obstructions and ensures consistent material flow.
Can Additives Enhance Material Fluidity in Injection Molding?
Additives play a crucial role in enhancing the fluidity of materials used in injection molding, improving efficiency and reducing defects.
Additives such as lubricants and plasticizers can significantly enhance material fluidity in injection molding by reducing viscosity and friction, facilitating better flow and mold filling. However, their selection depends on specific product requirements and material characteristics to avoid adverse effects on performance.

Understanding Additives in Injection Molding
Additives are essential components in the injection molding process, designed to modify the properties of plastic materials. They can enhance fluidity, ease processing, and improve final product quality. When used correctly, additives help reduce viscosity5 and improve the flow properties of materials, making them invaluable in achieving efficient production runs.
Types of Additives That Improve Fluidity
-
Lubricants: These additives reduce the friction between polymer chains, enabling smoother flow through the mold. They are especially useful in materials that naturally have higher viscosity, such as polycarbonate. By decreasing friction, lubricants can prevent issues like material overheating and mechanical stress.
-
Plasticizers: These substances work by integrating into the polymer matrix, increasing flexibility and reducing viscosity. This makes the material easier to process at lower temperatures, which can be beneficial for heat-sensitive plastics. However, choosing the right plasticizer is crucial to maintain the balance between fluidity and mechanical properties.
-
Flow Enhancers: These are specialized additives designed to optimize the material’s flow characteristics without altering its structural integrity. They can be particularly useful for complex mold designs where uniform distribution is critical.
Considerations for Using Additives
While additives offer significant benefits, their use must be carefully considered:
- Compatibility: Not all additives are compatible with every type of polymer. It’s essential to select additives that blend well with the base material to avoid negative impacts on mechanical properties or product appearance.
- Concentration: Overusing additives can lead to issues such as reduced strength or altered color of the final product. Therefore, it’s important to adhere to recommended concentrations for optimal results.
- Product Requirements: The choice of additive should align with the specific requirements of the end product, such as transparency, durability, or flexibility.
Examples and Case Studies
-
Polypropylene Production: In scenarios where polypropylene (PP) is used for thin-walled packaging applications, additives like slip agents are employed to enhance flow characteristics, reducing cycle time and improving surface finish.
-
Automotive Components: The automotive industry often uses plasticizers in the production of components like dashboards and interior trims to ensure that materials remain flexible yet robust under temperature variations.
By understanding the types and roles of additives in injection molding, manufacturers can make informed decisions that enhance productivity and product quality, meeting both technical specifications and market demands.
Lubricants reduce polymer viscosity in injection molding.True
Lubricants decrease friction between polymer chains, enhancing flow.
Overusing additives improves product strength and color.False
Excessive additives can weaken strength and alter product color.
Conclusion
By implementing these strategies, you’ll boost your injection molding efficiency and product quality. Reflect on your practices and consider these expert tips to optimize your manufacturing process.
-
Explore how different material properties affect fluidity.: In the injection molding process, polymer fluidity is considered the most relevant factor to the infiltration status. We assume that the appropriate additives, … ↩
-
Learn specific temperature settings for polyethylene to enhance flow control.: With plastic injection molding, HDPE has a melt temperature between 200°C and 300°C and a mold temperature between 10°C and 80°C. A higher mold … ↩
-
Discover various gate designs for optimal material distribution.: This approach involves creating gate recesses and strategically placing gates on non-cosmetic surfaces. By utilizing methods such as direct-valve gating or … ↩
-
Find out how to optimize runners for better material flow.: Runner Balance Analysis: Use a runner balance analysis to optimize the runner layout, ensuring an even distribution of plastic flow into the mold cavities. ↩
-
Discover how lubricants effectively reduce polymer viscosity and enhance flow.: The 5 denotes the weight of the oil, which correlates to the viscosity. Lower weight equates to lower viscosity, which means it flows easier. ↩