Are you looking to enhance product durability and protection in your manufacturing processes? Low-pressure injection molding might be the solution you need.
Low-pressure injection molding is a process that uses hot melt materials injected at low pressure to encapsulate and protect sensitive components, offering benefits like enhanced durability and precision. It’s widely used in industries such as automotive, electronics, and medical devices.
While the basics of low-pressure injection molding highlight its capacity for delicate component handling, the depth of its applications and advantages is truly expansive. Continue reading to discover how this process can revolutionize your manufacturing approach.
Low-pressure injection molding uses high pressure to mold parts.False
Low-pressure injection molding operates at 1.5 to 40 bar, not high pressure.
How Does Low-Pressure Injection Molding Work?
Curious about how low-pressure injection molding operates to safeguard delicate electronics and more? Dive in to learn its process.
Low-pressure injection molding involves injecting hot melt material at low pressure into a mold, quickly solidifying to protect sensitive components. This method allows for gentle encapsulation without damaging delicate parts, making it ideal for electronics and other precision items.
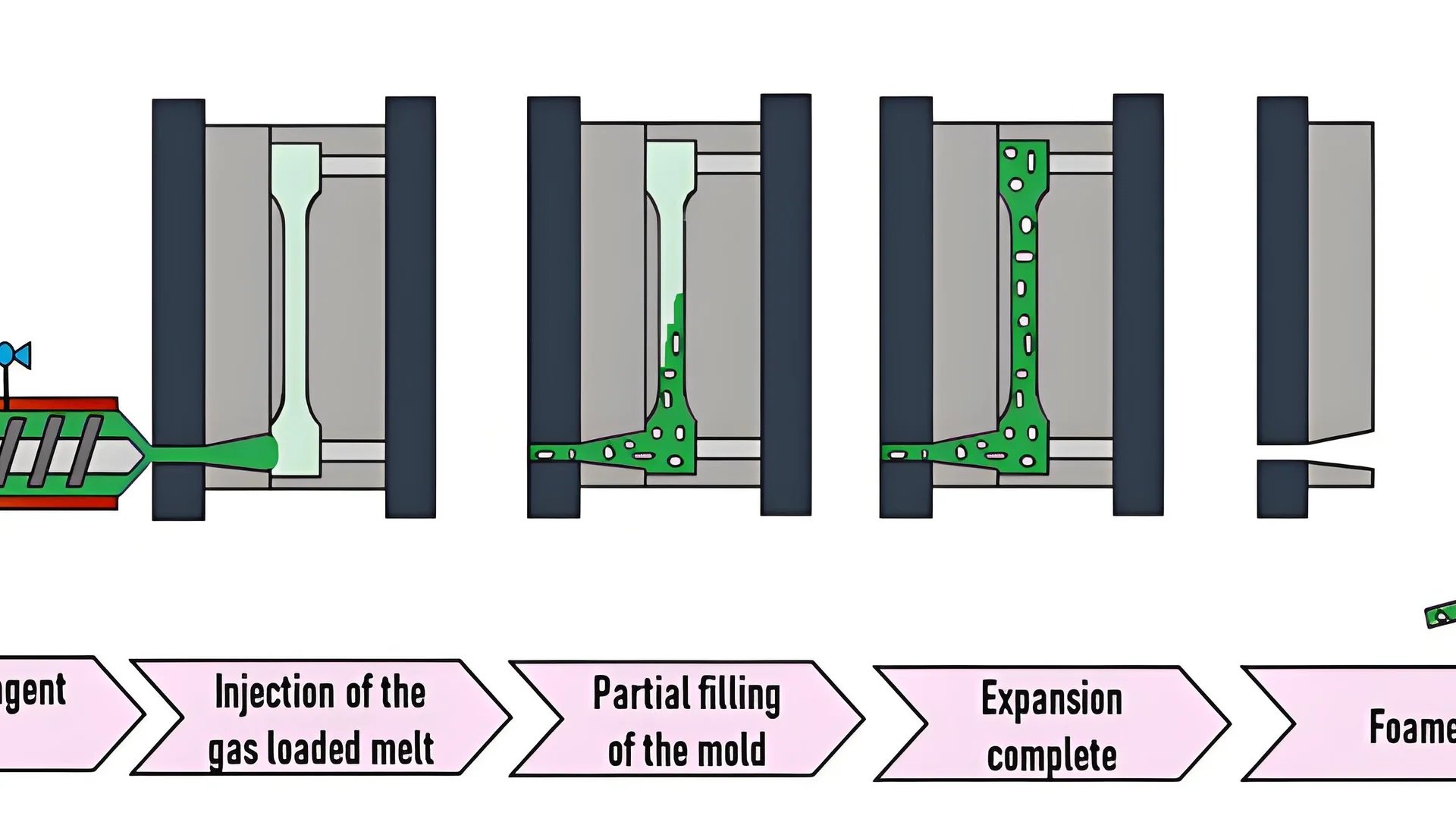
Understanding the Principle
Low-pressure injection molding is a packaging process1 that utilizes the fluidity and rapid solidification of hot melt materials. At pressures between 1.5 to 40 bar, the material is injected into molds where it solidifies within seconds, typically between 5 to 50 seconds. This quick curing process enhances production efficiency while maintaining product integrity.
The Step-by-Step Process
1. Mold Preparation
The mold design is pivotal, considering factors such as shape, size, and structure of the product alongside the characteristics of the molding material. Typically, cast aluminum molds are employed due to their ease of development and processing, facilitating shorter development cycles.
2. Workpiece Placement
The workpiece intended for encapsulation is carefully placed within the mold. This positioning ensures precision during the molding process.
3. Injection Molding
The hot melt material, having been melted, is then injected into the mold cavity at low pressure. This ensures no damage occurs to the workpiece, making it particularly suitable for packaging sensitive components like electronics.
4. Curing
Once injected, the material cures rapidly within the mold. This short curing time significantly boosts production efficiency.
5. Demolding
Finally, the mold is opened, and the fully formed product is removed, ready for use or further assembly.
Why Choose Low-Pressure Injection Molding?
This process is ideal for applications demanding gentle handling of components, offering benefits such as:
- Protection against external elements like moisture and dust
- Enhanced durability and longevity of encapsulated components
- Minimal risk of component damage during encapsulation
Low-pressure injection molding is thus a valuable tool in various industries, where product integrity and efficiency are paramount.
Low-pressure injection molding uses pressures between 1.5 to 40 bar.True
The process utilizes low pressure, typically between 1.5 to 40 bar, for gentle encapsulation.
Low-pressure injection molding damages delicate electronics.False
The method is designed to protect delicate components, not damage them.
What Are the Key Advantages of Using Low-Pressure Injection Molding?
Discover how low-pressure injection molding can revolutionize manufacturing with enhanced efficiency and precision.
Low-pressure injection molding offers advantages like improved product protection, cost efficiency, and faster production cycles. It’s ideal for encapsulating delicate electronic components, providing reliable sealing, and enhancing product aesthetics while ensuring environmental safety.

Improved Product Protection
One of the primary advantages of low-pressure injection molding is its ability to offer superior protection to delicate components. By using low injection pressure, typically between 1.5 to 40 bar, the process minimizes the risk of damaging sensitive electronics or fragile components. This makes it particularly suitable for industries like automotive and electronics, where protecting components such as sensors and PCBs is crucial.
Cost Efficiency
Low-pressure injection molding is often more cost-effective compared to traditional high-pressure methods. This is due to the reduced need for complex tooling and the lower material costs associated with using hot melt materials. The process also shortens the development cycle, making it an attractive option for manufacturers looking to improve their bottom line. Learn more about the economic benefits of low-pressure molding2.
Faster Production Cycles
The rapid solidification of hot melt materials in low-pressure injection molding significantly speeds up production times. With curing times as short as 5 to 50 seconds, manufacturers can achieve higher throughput without compromising on quality. This efficiency is beneficial across various industries, including automotive and medical, where time-to-market is critical.
Enhanced Environmental Safety
Low-pressure injection molding uses eco-friendly materials, reducing the environmental impact of manufacturing processes. The use of cast aluminum molds, which are easier to recycle, further enhances the sustainability aspect. Additionally, the process eliminates the need for adhesives and solvents, promoting a safer work environment.
Versatility in Applications
From automotive interiors to electronic connectors, low-pressure injection molding is versatile in its applications. It enables manufacturers to produce high-strength components with improved aesthetics and durability. In the automotive sector, for example, the process allows for the seamless integration of surface materials with plastic substrates, enhancing both form and function.
Key Advantages | Description |
---|---|
Product Protection | Protects sensitive components without damage |
Cost Efficiency | Reduces tooling and material costs |
Faster Production Cycles | Accelerates curing times and increases throughput |
Environmental Safety | Uses eco-friendly materials and eliminates harmful chemicals |
Versatility | Suitable for various industries and applications, enhancing component strength and aesthetics |
Reliability in Extreme Conditions
Another significant advantage is its reliability under extreme conditions. The process provides robust sealing that withstands harsh environmental factors such as moisture, dust, and temperature fluctuations. This is especially beneficial in aerospace and new energy sectors, where components are exposed to challenging environments. For detailed insights on how this technology supports extreme conditions3, explore further.
Low-pressure injection molding uses eco-friendly materials.True
The process uses materials that reduce environmental impact, enhancing sustainability.
High-pressure injection molding is faster than low-pressure.False
Low-pressure injection molding speeds up production with rapid curing times.
Which Industries Benefit Most from Low-Pressure Injection Molding?
Low-pressure injection molding is a game-changer for industries requiring precision and protection in manufacturing processes.
Industries such as automotive, electronics, and medical benefit significantly from low-pressure injection molding due to its ability to protect delicate components without damage. This process offers enhanced durability, environmental resistance, and production efficiency, making it indispensable for sectors demanding high reliability and precision.
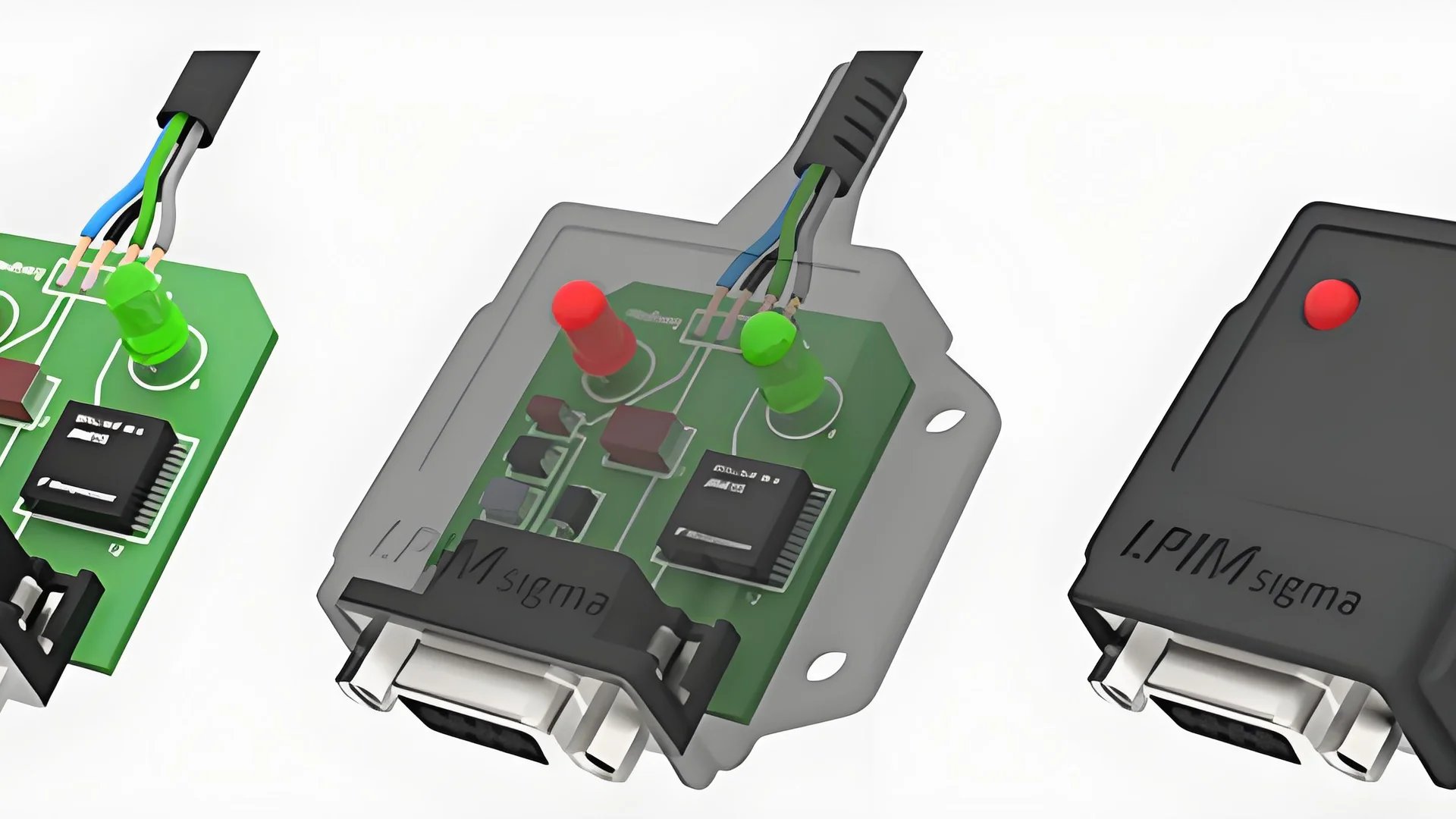
Automotive Industry
The automotive industry relies heavily on the precision and protection offered by low-pressure injection molding. One of the critical applications is in the automotive electronic component packaging4, where sensors, connectors, and control modules are encapsulated. This process ensures that these components remain functional amidst harsh conditions by providing waterproofing, dustproofing, and impact resistance. Additionally, low-pressure injection molding is employed in manufacturing automotive interior parts5. It allows surface materials to be seamlessly combined with plastic substrates, enhancing both aesthetics and comfort while reducing the need for additional adhesives.
Electronics Industry
In the electronics industry, the demand for robust protection against environmental factors is paramount. Low-pressure injection molding serves this need by offering effective packaging for components such as PCBs and batteries. It shields them from moisture, dust, and static electricity without compromising internal structures. Furthermore, it plays a crucial role in electronic connector sealing6, ensuring connectors have superior waterproof and dustproof capabilities, which increases their lifespan and reliability.
Medical Industry
The medical industry benefits from low-pressure injection molding by meeting stringent manufacturing requirements for components like sensors and micromotors. This process ensures precision and reliability while safeguarding these components. Moreover, it is vital in medical device packaging7, where it enhances production efficiency and maintains hygiene standards. The ability to quickly encapsulate devices like syringes ensures high-quality output essential for medical applications.
Aerospace and New Energy Sectors
Low-pressure injection molding is also pivotal in aerospace applications where devices must withstand extreme conditions. It provides critical protective packaging that assures performance at high altitudes. In the new energy sector, components like batteries require robust protection against environmental stressors. The process provides excellent insulation and impact resistance, crucial for maintaining safety and functionality in energy systems.
Automotive interiors use low-pressure injection molding.True
This process enhances aesthetics and comfort by combining materials seamlessly.
Low-pressure molding is not used in medical devices.False
It's crucial for encapsulating devices like syringes, ensuring quality.
How Does Low-Pressure Injection Molding Enhance Product Safety and Reliability?
Enhancing product safety and reliability is crucial in manufacturing, especially for sensitive components. Discover how low-pressure injection molding achieves this.
Low-pressure injection molding enhances product safety and reliability by offering robust protection against environmental factors, reducing the risk of damage during encapsulation, and improving structural integrity. Its precise process minimizes stress on components, making it ideal for sensitive electronics and medical devices.
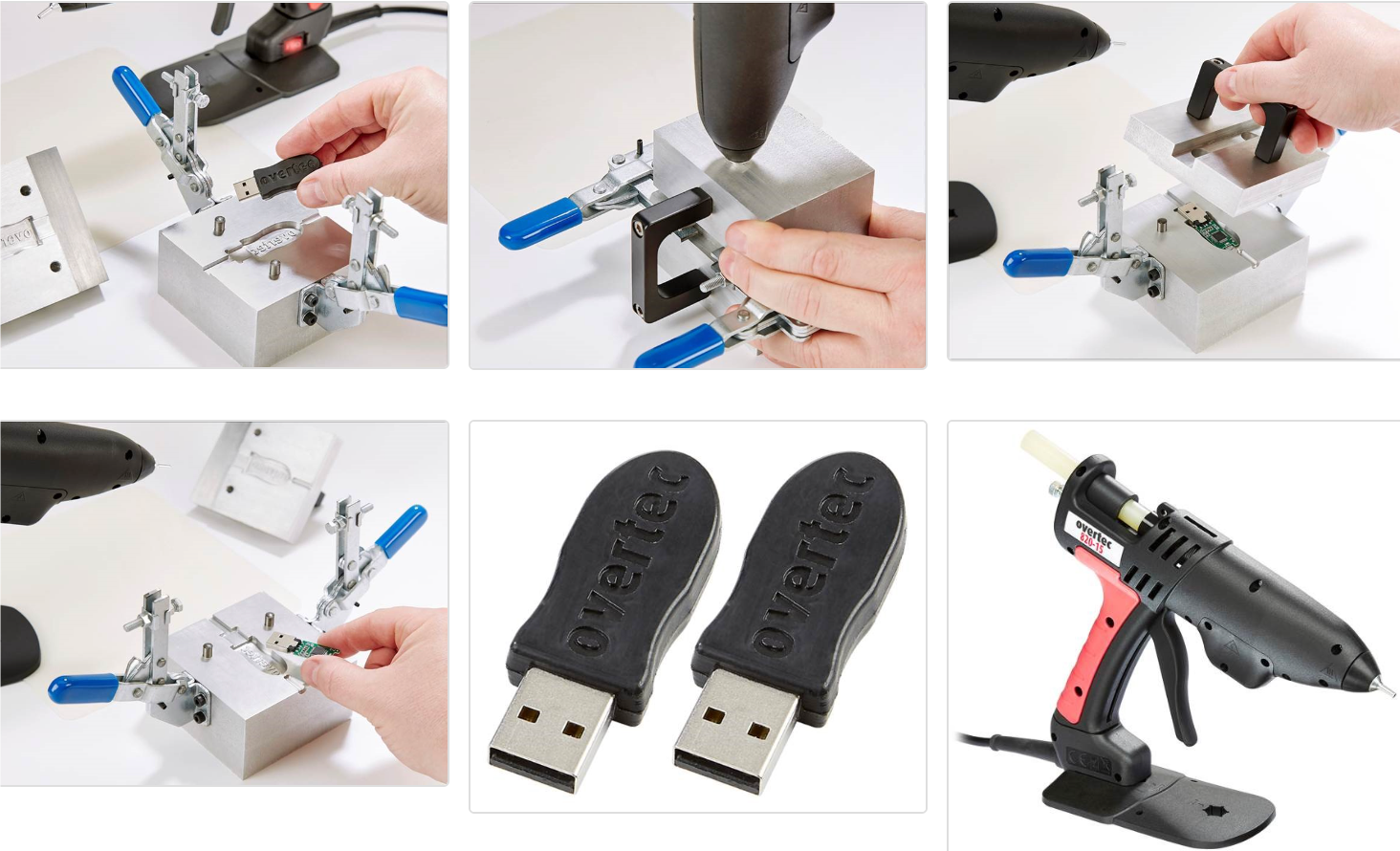
Understanding the Mechanism
Low-pressure injection molding operates at pressures ranging from 1.5 to 40 bar, which significantly reduces the risk of damage during the encapsulation of sensitive components. This method utilizes hot melt materials that flow smoothly into the mold, quickly solidifying to form a protective barrier. The low-pressure8 nature of the process is particularly beneficial for delicate electronics, ensuring minimal stress and maintaining component integrity.
Application in Sensitive Industries
Automotive Sector
In the automotive industry, electronic components such as sensors and connectors demand high reliability due to their exposure to harsh conditions. Low-pressure injection molding provides a protective shield against dust, moisture, and vibration, enhancing the longevity and safety of these components. For instance, it is used in the packaging of car seat sensors, offering impact resistance and durability.
Electronics Industry
For electronic components like PCBs and mobile phone batteries, this process prevents environmental damage without affecting internal structures. It offers excellent protection9 against static electricity and humidity, crucial for maintaining performance standards in consumer electronics.
Medical Field
Medical devices often require high-precision manufacturing to ensure patient safety. Low-pressure injection molding meets these demands by securely encasing components like catheter connectors and sensors, protecting them from contamination while ensuring stable operation.
Advantages Over Conventional Methods
Feature | Low-Pressure Injection Molding | Traditional Molding Methods |
---|---|---|
Pressure Applied | 1.5 to 40 bar | Up to 1000 bar |
Component Stress | Minimal | Higher |
Environmental Protection | Superior | Moderate |
Precision & Accuracy | High | Variable |
The reduced pressure not only minimizes the physical stress on components but also enhances their overall durability. This is vital for applications where component failure could lead to significant safety hazards.
Ensuring Reliability Through Design
The use of cast aluminum molds in the process allows for a high degree of design flexibility, enabling manufacturers to create precise molds tailored to specific product needs. This ensures a snug fit for each component, minimizing movement and potential wear during use. By leveraging the fluidity and rapid solidification properties of hot melt materials, manufacturers can achieve consistent quality and reliable performance across various applications.
Future Prospects
With growing demand in sectors like aerospace and new energy industries, low-pressure injection molding is set to expand its role in enhancing product reliability and safety. The ability to offer efficient protection without compromising the function or form of components makes it an invaluable asset in modern manufacturing strategies.
Low-pressure injection molding uses pressures up to 40 bar.True
The process operates at pressures between 1.5 and 40 bar, reducing damage risk.
Traditional molding methods apply less pressure than low-pressure molding.False
Traditional methods use up to 1000 bar, much higher than low-pressure molding.
Conclusion
Low-pressure injection molding is pivotal for enhancing durability and protection across industries. Its precise, efficient methodology supports advanced manufacturing needs, offering reliability for sensitive components.
-
Explore the foundational principles governing low-pressure injection molding.: As the name would suggest, parts are molded at lower pressures, allowing for gentle encapsulation of delicate electronic assemblies. ↩
-
Explore cost-saving strategies in manufacturing.: Low-Pressure Injection Molding Technology Boasts Faster Cycles, Better Parts … iMFLUX is transforming the future of plastic injection molding. ↩
-
Learn how it enhances reliability under harsh conditions.: Low pressure injection molding is a process where molten plastic material is injected into a mold cavity at relatively low pressures. ↩
-
Explore detailed insights into automotive component protection methods.: The application of low-pressure injection molding in the automotive field is not limited to the packaging protection of electronic devices, PCB boards, wire … ↩
-
Learn how low-pressure injection molding enhances car interiors.: Compared with traditional manual coating, low-pressure injection molding has the advantages of high production efficiency, environmental protection and good … ↩
-
Discover reliable sealing techniques for electronic connectors.: Low Pressure Molding (LPM), a variation from conventional injection molding, allows for gentle encapsulation of delicate electronic assemblies. ↩
-
Understand the advantages of using this method in medical packaging.: Low pressure injection molding process: placing the PVC skin or knitted fabric into the mold before injecting the plasticized molten plastic (generally modified … ↩
-
Discover detailed insights into low-pressure injection molding techniques.: Low Pressure Molding (LPM) is a slight variation from conventional injection molding. As the name would suggest, parts are molded at lower pressures. ↩
-
Learn how this process safeguards electronic components effectively.: Low Pressure Molding (LPM), a variation from conventional injection molding, allows for gentle encapsulation of delicate electronic assemblies. ↩