As I navigate the ever-evolving world of manufacturing, I’ve come to appreciate the delicate balance between efficiency and protection, especially when it comes to sensitive components.
Low-pressure injection molding is advantageous because it minimizes damage to sensitive parts, improves production efficiency, and reduces costs through lower material consumption and energy usage. It also offers high design flexibility for complex structures.
Understanding these benefits in detail can truly illuminate how low-pressure injection molding can transform your manufacturing processes.
Low-pressure injection molding reduces energy consumption.True
It operates at lower pressures and faster curing times, saving energy.
How Does Low-Pressure Injection Protect Sensitive Components?
Sensitive components like electronics require careful handling during manufacturing to avoid damage.
Low-pressure injection protects sensitive components by utilizing reduced pressure levels (1.5 to 40 bar) that prevent damage and ensure excellent sealing and buffer protection.
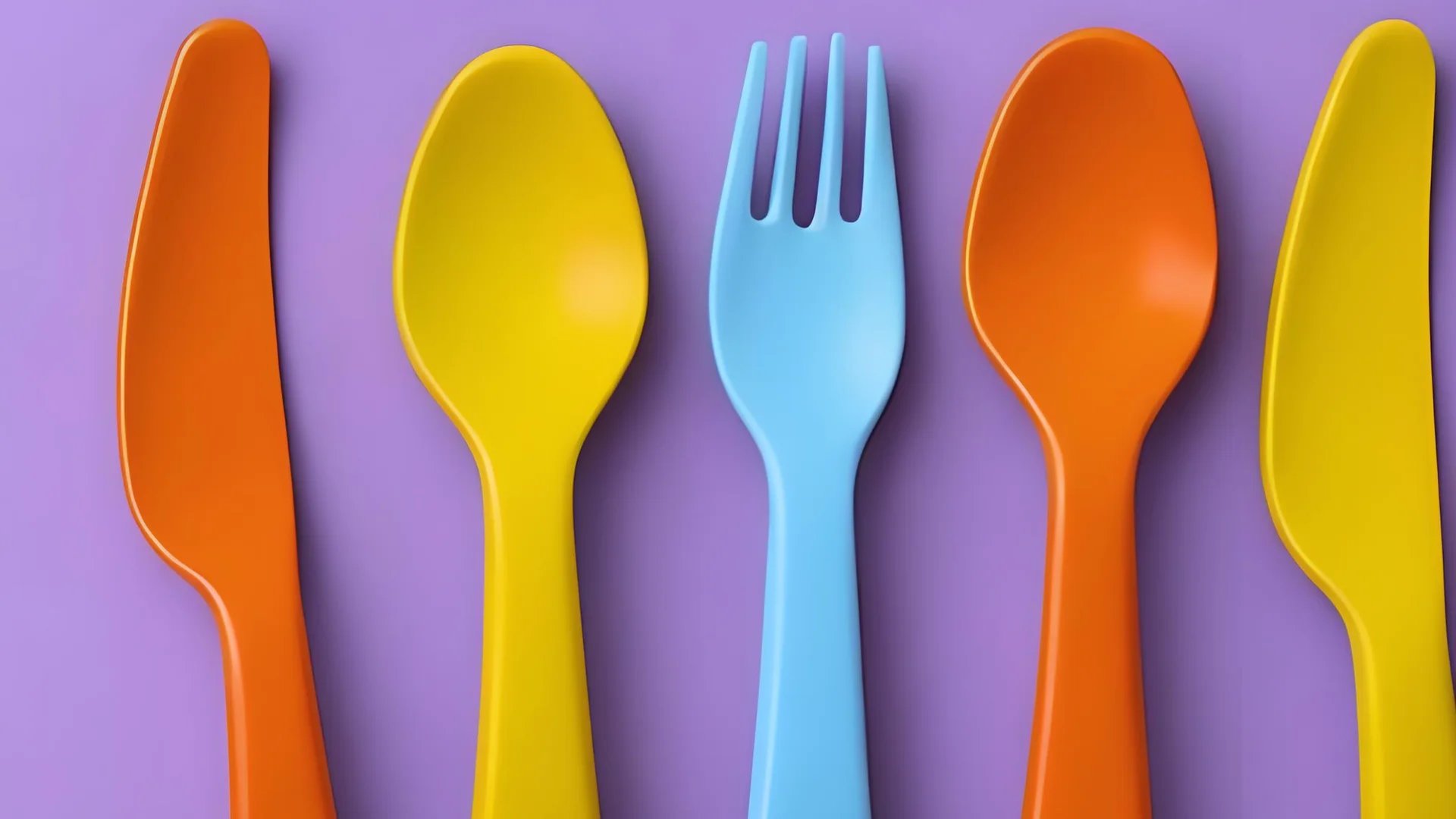
Understanding Low-Pressure Injection
In the realm of injection molding, pressure plays a critical role in the process. Traditional high-pressure injection molding can expose sensitive components to forces that might compromise their integrity. However, low-pressure injection uses significantly lower pressure levels, typically ranging from 1.5 to 40 bar. This reduction in pressure is pivotal for protecting delicate electronic components like printed circuit boards1, sensors, and mobile phone batteries.
Advantages of Low-Pressure Environments
-
Destructive Packaging Prevention: The reduced pressure environment ensures minimal stress on components during the molding process. Unlike traditional methods, low-pressure injection greatly reduces the risk of damage or deformation to precision parts.
-
Excellent Sealing Capabilities: Upon melting, the materials used in low-pressure injection exhibit superior adhesion properties. This characteristic allows for a tight encapsulation, providing effective sealing against water, dust, and corrosion. Such features are particularly beneficial in applications like automotive electronics where environmental resistance is critical.
-
Buffer Protection: Materials employed in low-pressure injection possess inherent flexibility. This flexibility acts as a buffer during physical impacts, significantly lowering the likelihood of internal component damage and enhancing the product’s durability.
Real-World Applications
In industries such as consumer electronics, automotive, and even aerospace, the demand for reliable and robust products is ever-growing. Low-pressure injection meets these demands by offering a protective environment for manufacturing components that are not only sensitive but also integral to the product’s functionality.
For instance, the production of waterproof connectors or automotive sensors benefits immensely from the sealing and protective qualities of low-pressure injection. The encapsulation ensures that even under extreme conditions, the components remain functional and reliable.
Conclusion
While traditional methods have their place, the specific needs of sensitive components call for a more nuanced approach in manufacturing. Low-pressure injection offers this by combining reduced pressure environments with excellent sealing and buffer protection capabilities, ensuring components remain intact and reliable throughout their lifecycle. By understanding these advantages, manufacturers can better align their production processes with industry standards and consumer expectations for durability and reliability.
Low-pressure injection uses 1.5 to 40 bar pressure.True
Low-pressure injection operates within 1.5 to 40 bar, protecting components.
Traditional injection molding uses less pressure than low-pressure.False
Traditional molding uses higher pressure, unlike low-pressure's reduced levels.
Can Low-Pressure Injection Enhance Production Efficiency?
Low-pressure injection molding promises to streamline production with faster cycles and reduced material waste.
Low-pressure injection molding enhances production efficiency by shortening mold development and molding cycles, allowing for faster product turnaround.

Understanding the Short Mold Development Cycle
Low-pressure injection molding leverages the benefits of cast aluminum molds over traditional steel molds. Cast aluminum molds are not only easier to manufacture but also significantly reduce the complexity involved in mold design and development. This translates into a shorter mold development cycle, accelerating the time it takes to get a product from concept to production. In industries where time-to-market is critical, this can provide a competitive advantage.
Faster Molding Cycle for Increased Output
One of the standout features of low-pressure injection molding is its rapid curing process. The time it takes for the material to cure and form is notably short, ranging from just 5 to 50 seconds. This is considerably faster than many traditional injection molding processes, which often require longer curing times. As a result, manufacturers can produce more units in less time, meeting the demands of high-volume production with ease.
Comparative Analysis: Traditional vs. Low-Pressure Injection
Let’s examine how low-pressure injection stacks up against traditional methods in terms of production efficiency:
Aspect | Traditional Injection Molding | Low-Pressure Injection Molding |
---|---|---|
Mold Development Time | Longer | Shorter |
Curing Time | Longer | Shorter (5-50 seconds) |
Material Waste | Higher | Lower |
Energy Consumption | Higher | Lower |
Impact on Large-Scale Production
For large-scale manufacturing operations, the ability to maintain a fast-paced production line without compromising quality is paramount. Low-pressure injection molding supports this by allowing for rapid production cycles and efficient use of materials. With less downtime between cycles and reduced energy requirements, manufacturers can sustain high output levels while maintaining cost-effectiveness.
Exploring Further2
The versatility of low-pressure injection molding doesn’t end with efficiency improvements. It also offers unique advantages in product design flexibility and cost reduction, making it a compelling choice for various industries. By continuing to explore these facets, companies can further optimize their manufacturing processes.
Low-pressure injection reduces mold development time.True
It uses cast aluminum molds, which are faster to develop than steel.
Traditional injection molding has shorter curing times.False
Low-pressure injection offers faster curing times, from 5 to 50 seconds.
How Does Low-Pressure Injection Reduce Manufacturing Costs?
In today’s competitive manufacturing landscape, cutting costs without compromising quality is a priority for businesses.
Low-pressure injection reduces manufacturing costs by saving material, lowering energy consumption, and using cost-effective molds. This method streamlines production by eliminating additional processes, ultimately enhancing efficiency and profitability.

Material Consumption Savings
One of the most significant ways low-pressure injection reduces manufacturing costs is through efficient material usage. The precision control over the injection amount means less waste and substantial savings on raw materials. Unlike traditional methods that may lead to material overflow or spillage, low-pressure injection allows for exact volume usage, ensuring minimal waste.
Energy Consumption Reduction
By operating at lower pressure levels and faster curing times, low-pressure injection drastically cuts down energy requirements. Traditional injection molding can require extended heating and curing times, consuming significant amounts of energy. Low-pressure techniques eliminate the need for prolonged oven usage, thus saving energy and reducing overall operational costs.
Cost-Effective Mold Usage
The molds used in low-pressure injection are typically made from cast aluminum, which is not only less expensive than steel molds but also easier and quicker to produce. This cost-effective approach reduces initial mold investment and allows for rapid changes in design and production, adapting to market demands swiftly.
Streamlined Production Processes
Low-pressure injection reduces the need for additional steps such as potting shells or complex cooling systems. This method simplifies the manufacturing process by eliminating these secondary processes and the associated costs of equipment, labor, and space. Without the need for additional curing time or specialized storage, products can be moved through the production line more efficiently.
By integrating low-pressure injection molding3, manufacturers can not only cut costs but also improve their production’s environmental footprint due to reduced energy and material wastage. This balance between economic and ecological benefits makes low-pressure injection an attractive choice for modern manufacturers.
Low-pressure injection saves on raw material costs.True
Precision control minimizes waste, reducing material expenses.
Energy consumption is higher in low-pressure injection.False
Lower pressure and faster curing reduce energy use, saving costs.
What Design Flexibility Does Low-Pressure Injection Offer?
Low-pressure injection molding revolutionizes design possibilities, allowing for innovative and complex product structures.
Low-pressure injection provides unmatched design flexibility by allowing for complex geometries and the use of multiple materials, catering to diverse product needs.

Complex Geometries Made Easy
One of the standout advantages of low-pressure injection4 is its ability to mold complex structures with ease. Traditional methods often struggle with intricate designs, but the low-pressure technique seamlessly handles irregular shapes, providing designers with more creative freedom. This capability is crucial in industries where design intricacies are non-negotiable, such as automotive and aerospace sectors.
For instance, consider the challenge of manufacturing an automotive dashboard with various embedded components and curves. Low-pressure injection ensures that these complex designs are achievable without compromising on structural integrity or performance.
Multiple Material Composites
Another significant benefit is the capability to perform composite injection molding. This process allows the combination of different materials within a single product, which is particularly advantageous for products requiring both strength and aesthetic appeal. By integrating materials such as fabrics or skins with plastic substrates, manufacturers can create products that are not only functional but also visually appealing.
A practical application of this is seen in consumer electronics, where a sleek outer fabric layer can be combined with robust plastic internals to achieve both style and durability.
Enabling Product Innovation
The ability to mold complex shapes and utilize multiple materials opens doors for innovation across various sectors. Products that were once deemed too challenging or costly to produce can now be realized efficiently and economically. This flexibility in design not only caters to current market demands but also anticipates future trends, giving manufacturers a competitive edge.
For example, in the realm of wearable technology, devices can be designed to fit ergonomically while incorporating advanced functionalities, thanks to the adaptable nature of low-pressure injection.
In summary, low-pressure injection’s design flexibility is a game-changer, offering unparalleled opportunities for creating sophisticated and multifaceted products that meet diverse consumer expectations.
Low-pressure injection handles irregular shapes easily.True
It allows for molding complex structures without difficulty.
Multiple materials can't be combined in low-pressure injection.False
It supports composite injection, combining different materials.
Conclusion
Embracing low-pressure injection molding can elevate your manufacturing quality while enhancing protection and efficiency.
-
Explore how low-pressure injection benefits printed circuit boards.: Low Pressure Molding (LPM), a variation from conventional injection molding, allows for gentle encapsulation of delicate electronic assemblies. ↩
-
Uncover broader benefits of this method beyond efficiency gains.: High Strength: The skin material bonds seamlessly with the plastic base, ensuring there is no risk of separation. · High Molding Efficiency: The … ↩
-
Discover in-depth insights into the cost-saving advantages of low-pressure injection.: High Strength: The skin material bonds seamlessly with the plastic base, ensuring there is no risk of separation. · High Molding Efficiency: The … ↩
-
Discover how it simplifies manufacturing intricate designs effectively.: Low-pressure molding is a revolutionary manufacturing method that offers protection, customization, efficiency, eco-friendliness, and cost-effectiveness. ↩