Injection molding is more than just a process; it’s an art that demands finesse and precision. In my journey through plastics manufacturing, I’ve realized how crucial it is to master the flow rate of liquid plastic.
The best techniques for controlling liquid plastic flow rate in injection molding include mechanical structure adjustments, electrical control methods, and intelligent control systems. Each technique offers unique benefits and is suited to different operational needs and precision requirements.
But wait—before you dive into the nitty-gritty of these methods, let me share what I’ve learned through my own experiences in the field. Understanding these techniques can empower you to optimize your production process effectively.
Mechanical adjustments are cost-effective for flow control.True
Mechanical methods like adjustable feed pipes offer low-cost flow control.
How Does Mechanical Structure Adjustment Affect Flow Rate?
Mechanical structure adjustments are pivotal in managing flow rates during injection molding processes.
Mechanical structure adjustments, such as adjustable feed pipe devices and throttle valve adjustments, influence flow rate by physically altering the path or speed of liquid plastic. These methods offer simplicity and cost-effectiveness but vary in precision and suitability for different molding scenarios.
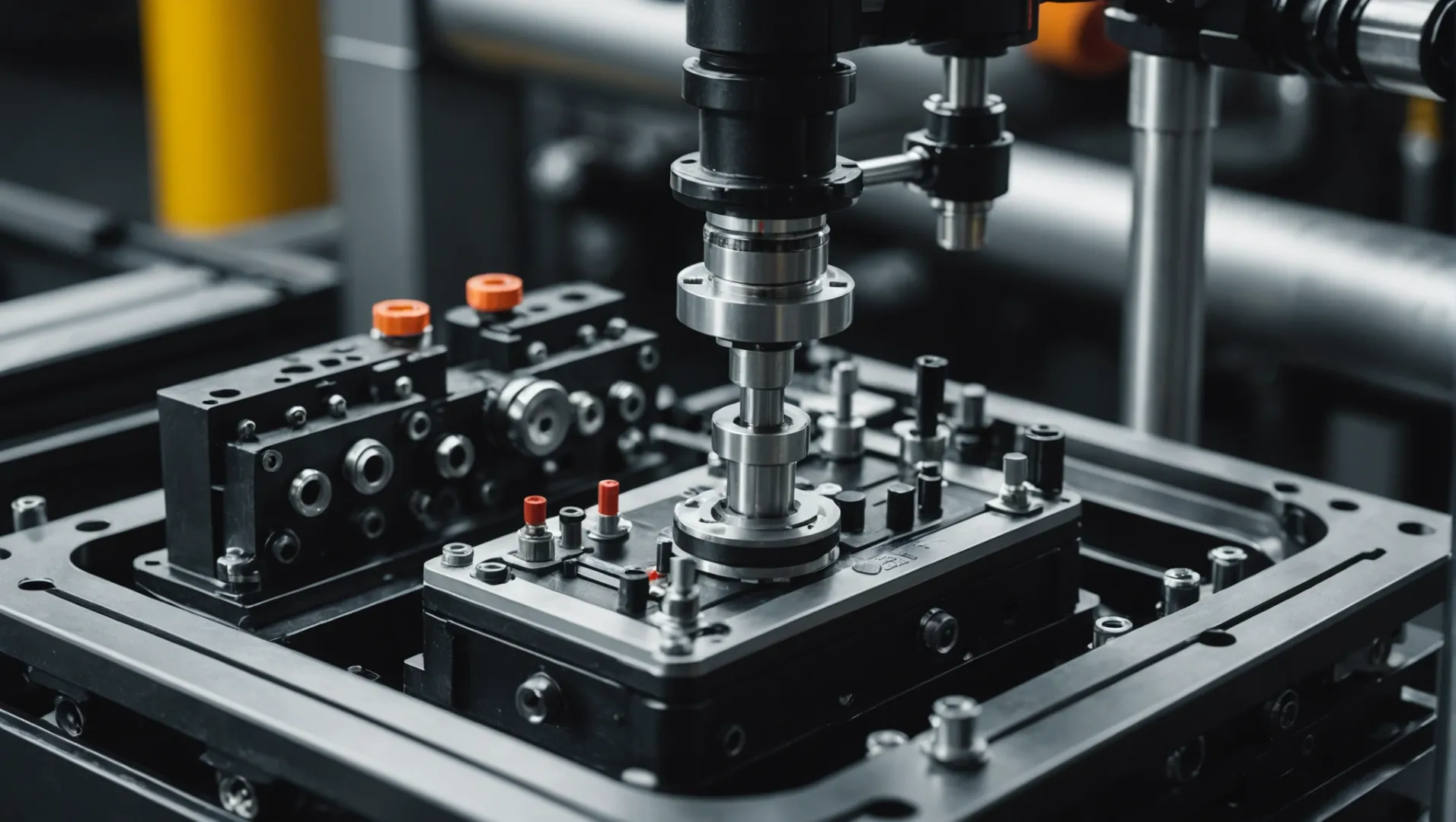
Understanding Mechanical Structure Adjustments
Mechanical structure adjustment in injection molding involves modifications to the physical components that guide liquid plastic, directly influencing flow rate. Two primary techniques include the adjustable feed pipe device1 and throttle valve adjustment2.
Adjustable Feed Pipe Device
This device modifies the gap between two semicircular blocks along the feed pipe. By rotating one block, the gap size changes, thereby controlling the flow speed. This method is simple and cost-effective, particularly suitable for applications where precise flow control isn’t critical.
Advantages:
- Simple design
- Cost-effective implementation
Limitations:
- Limited precision in flow control
- Not ideal for high-accuracy demands
Throttle Valve Adjustment
Throttle valves adjust flow by altering their opening, with types including needle and ball valves. These valves allow for flexible, real-time flow adjustments based on production needs. However, they require regular maintenance to ensure optimal performance.
Advantages:
- Flexible real-time adjustments
- Suitable for varying production requirements
Limitations:
- Requires precise operation and maintenance
- Complex setup compared to basic mechanical adjustments
Comparing Mechanical Adjustments to Other Methods
While mechanical adjustments provide an accessible entry point into flow rate management, they often lack the precision of electrical control methods3 or intelligent systems4. When selecting a method, consider the trade-off between cost, complexity, and control accuracy.
Mechanical methods are beneficial for less demanding applications but may fall short in environments requiring high precision or automated adjustments.
Adjustable feed pipe devices offer precise flow control.False
These devices are simple and cost-effective but lack precision.
Throttle valve adjustments require regular maintenance.True
Throttle valves need maintenance to ensure optimal performance.
What Are the Advantages of Electrical Control Methods?
Electrical control methods in injection molding offer precision and flexibility, enhancing production efficiency.
Electrical control methods, including inverter and servo motor control, provide high accuracy, stability, and adaptability in adjusting the flow rate of liquid plastic during injection molding. These methods enable precise and real-time adjustments, making them ideal for high-end production requirements despite their higher cost and maintenance needs.
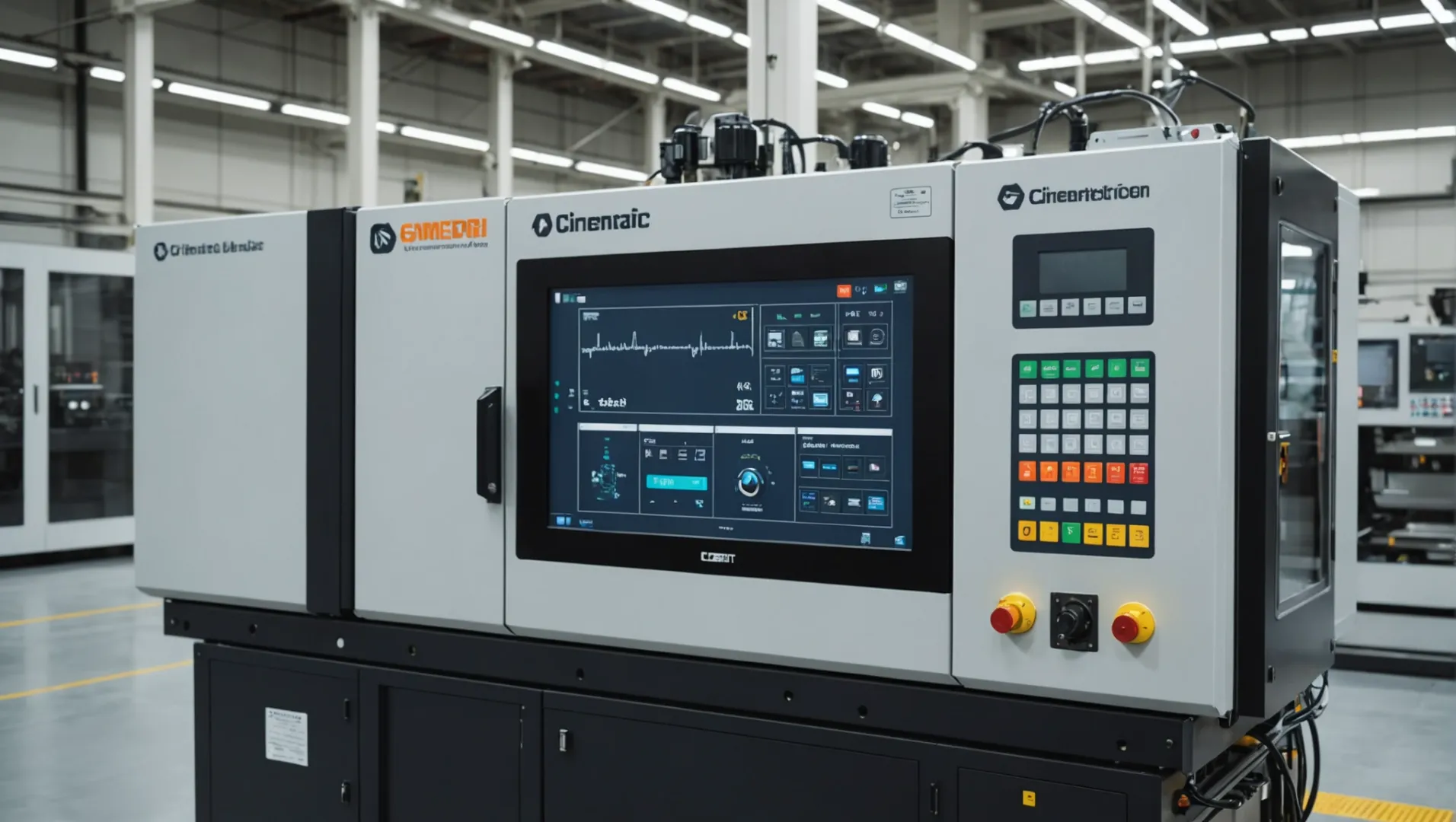
Precision and Accuracy
One of the primary advantages of electrical control methods in injection molding is their exceptional precision and accuracy. Techniques such as inverter control5 and servo motor control6 allow for meticulous adjustments of the motor speed, directly influencing the screw or plunger’s movement in the injection molding machine. This capability enables the achievement of specific flow rates required for complex and high-quality products.
Method | Control Accuracy | Cost | Maintenance Requirement |
---|---|---|---|
Inverter | High | High | Moderate |
Servo Motor | Very High | Very High | High |
Flexibility and Real-Time Adjustment
Electrical control methods offer unparalleled flexibility. With inverter controls, the flow rate can be modified in real-time to accommodate various production needs. This feature is particularly beneficial when dealing with diverse product lines or when fine-tuning processes to reduce waste and improve efficiency. The ability to make quick adjustments on-the-fly makes these methods invaluable in dynamic production environments.
Stability and Reliability
Both inverter and servo motor controls are known for their stability. The inherent design of these systems allows for consistent performance, minimizing fluctuations that could affect product quality. This stability is crucial in maintaining uniformity across batches, thus ensuring high standards in manufacturing processes.
Considerations for Implementation
While electrical control methods bring significant advantages, they also come with considerations that must be addressed:
- Cost: The initial investment for installing inverter or servo motor systems can be substantial.
- Maintenance: Regular maintenance by skilled professionals is required to ensure optimal performance.
- Technical Expertise: Skilled technicians are necessary for system setup, calibration, and ongoing adjustments.
Despite these challenges, the benefits of precision, flexibility, and stability make electrical control methods a compelling choice for manufacturers aiming for high precision and efficiency in injection molding.
Inverter control offers high precision in injection molding.True
Inverter control allows precise motor speed adjustments, enhancing accuracy.
Servo motor control is less accurate than inverter control.False
Servo motor control offers very high accuracy, surpassing inverter control.
Can Intelligent Control Systems Improve Injection Molding Quality?
Intelligent control systems are revolutionizing the injection molding process by enhancing precision and efficiency.
Intelligent control systems enhance injection molding quality by enabling precise, real-time adjustments to flow, pressure, and temperature, improving product consistency and reducing defects.
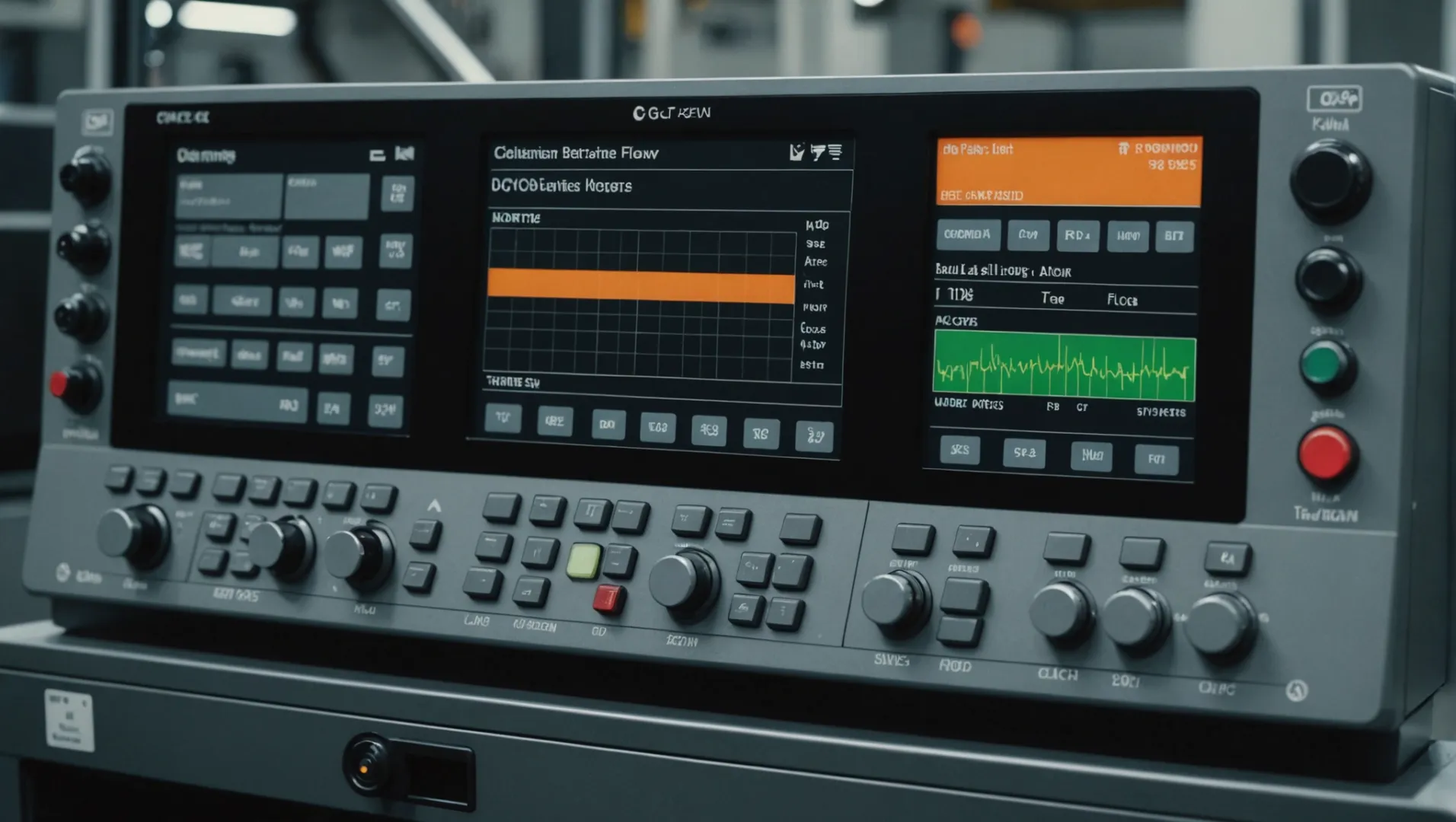
Understanding Intelligent Control Systems in Injection Molding
Intelligent control systems integrate advanced technologies to manage various parameters during the injection molding process. These systems utilize sensors and algorithms to provide real-time feedback7, enabling machines to adapt quickly to changes in material properties or environmental conditions. This flexibility leads to significant improvements in product quality and operational efficiency.
Key Components of Intelligent Control Systems
-
Proportional Valve Control: This involves using proportional pressure and flow valves to continuously adjust the flow and pressure of liquid plastic. The valves operate based on electrical signals, allowing for precise control that adapts to different stages of the injection process. This method is particularly effective for applications requiring high accuracy and quick response times.
-
Closed-loop Control System: Closed-loop systems incorporate sensors to monitor key parameters like flow rate, pressure, and temperature. The data is fed back to the control unit, which adjusts the machine’s operating parameters accordingly. This real-time feedback loop ensures consistent quality by minimizing deviations from set production standards.
Component | Functionality |
---|---|
Proportional Valve | Adjusts flow and pressure proportionally to input signals. |
Sensors | Monitor real-time parameters such as temperature, pressure, and flow. |
Control Unit | Processes sensor data to adjust machine settings automatically. |
Advantages of Intelligent Control Systems
- Precision: Achieves high accuracy in controlling liquid plastic flow, reducing material waste and improving final product quality.
- Adaptability: Can adjust parameters in response to changes in material properties or external conditions, ensuring consistent output.
- Efficiency: Enhances production efficiency by minimizing downtime and reducing defect rates.
Considerations for Implementation
While intelligent control systems offer numerous benefits, they come with challenges such as high initial costs and the need for skilled personnel for maintenance and troubleshooting. Selecting the right system depends on factors like production volume, complexity of products, and budget constraints.
To explore more on how these systems can be integrated into existing setups, consider investigating injection molding technology advancements8.
Conclusion
Intelligent control systems are pivotal in transforming traditional injection molding operations by boosting quality and efficiency. By harnessing the power of real-time data processing and advanced control mechanisms, manufacturers can achieve superior product consistency and meet the increasing demand for high-quality plastic products.
Intelligent systems reduce defects in injection molding.True
Real-time adjustments improve consistency, reducing defect rates.
Proportional valves are not used in intelligent control systems.False
Proportional valves adjust flow and pressure precisely in these systems.
Which Method Is Best for Your Specific Manufacturing Needs?
Choosing the right flow control technique in injection molding can significantly impact your manufacturing efficiency and product quality.
To determine the best method for your specific manufacturing needs, consider factors such as precision requirements, budget constraints, and operational complexity. Mechanical adjustments are cost-effective but less precise, while electrical and intelligent systems offer higher accuracy at a higher cost.
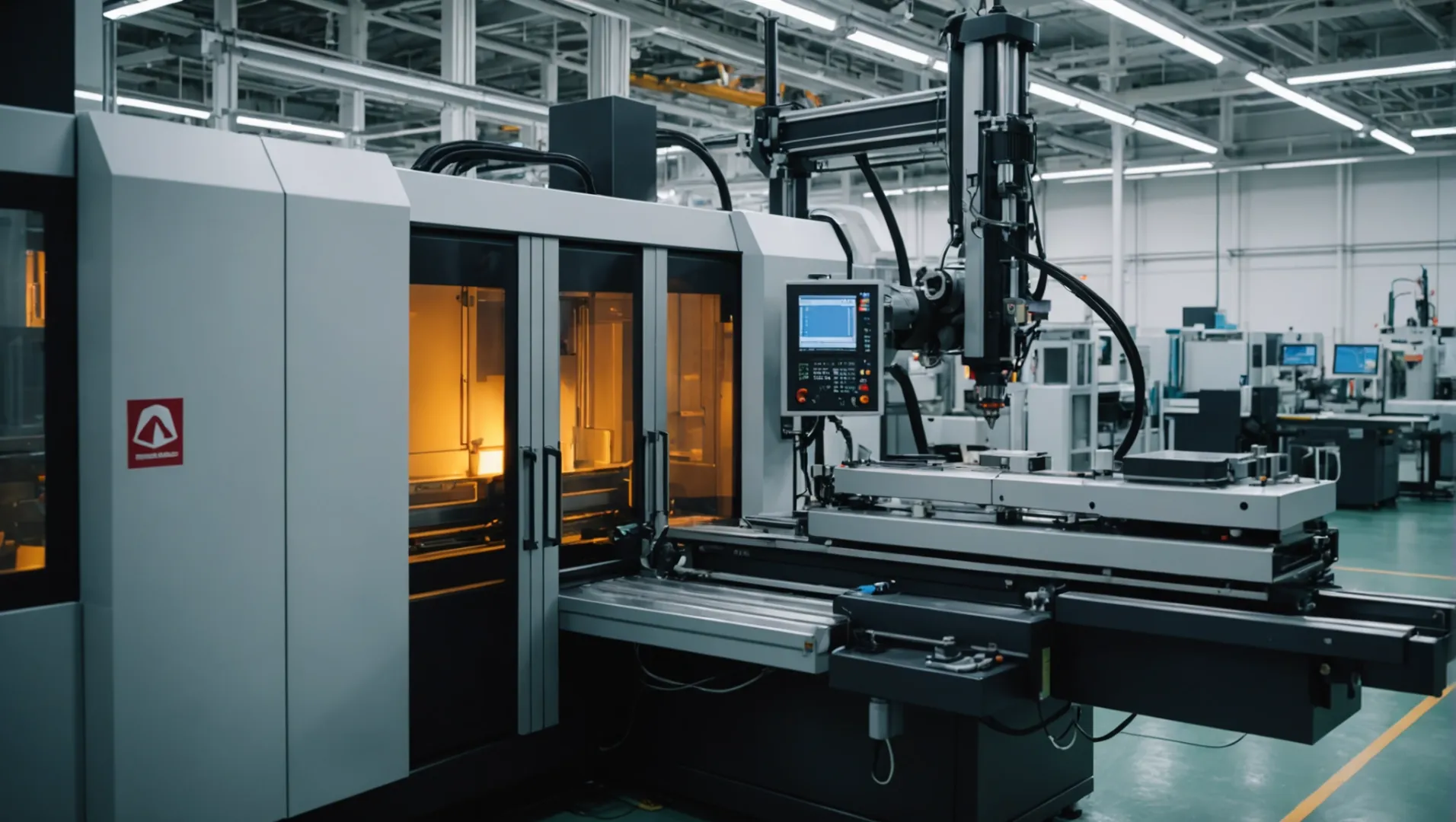
Evaluating Precision and Budget Constraints
When selecting a flow control technique, you need to assess how critical precision is for your manufacturing process. If your products require high accuracy, methods like servo motor control9 or closed-loop control systems10 might be ideal despite their higher costs. However, if you’re working with a tighter budget or producing less precision-critical items, mechanical adjustments such as adjustable feed pipe devices11 can offer a cost-effective solution.
Method | Precision | Cost | Ideal for |
---|---|---|---|
Mechanical Adjustments | Low to Medium | Low | Basic flow control needs |
Electrical Controls | Medium to High | Medium to High | Flexible, real-time adjustments |
Intelligent Systems | High | High | Complex, high-quality requirements |
Considering Operational Complexity
The complexity of your operation also plays a crucial role in deciding which method to implement. Electrical controls like inverter control12 offer flexible adjustments but require professional maintenance. On the other hand, intelligent systems, though complex, offer unparalleled automation and quality improvements by adapting to varying process stages automatically.
Assessing the Importance of Maintenance and Expertise
Maintenance and the availability of skilled technicians should also influence your decision. Systems requiring high expertise, such as those employing proportional valve control13, may necessitate investing in skilled personnel or training existing staff. In contrast, mechanical methods have simpler maintenance needs but may require more frequent manual adjustments.
Conclusion: Balancing Needs and Resources
Ultimately, the choice of method should align with your manufacturing goals and resources. Weigh the benefits of precision and automation against your budgetary limits and operational capacity to find the most suitable flow control technique for your needs.
Mechanical adjustments offer high precision in flow control.False
Mechanical adjustments provide low to medium precision, not high.
Intelligent systems require skilled maintenance personnel.True
Complex intelligent systems necessitate skilled technicians for maintenance.
Conclusion
Choosing the right technique for controlling liquid plastic flow can significantly enhance your injection molding efficiency. Reflect on your operational needs and make informed decisions to implement the most suitable method.
-
Understand how adjustable feed pipes control injection molding flow rate.: An injection molding machine comprises four main components: the base, the hopper, the barrel, and the clamping unit. ↩
-
Learn about throttle valves’ role in adjusting liquid plastic flow.: Described throttle valve gear comprises the choke valve piston that is used to reduce the flow of described material and is used for elastomeric material and/or … ↩
-
Discover precise control techniques using electrical systems.: The electrical control system serves as the nerve and memory center to program and sequence the machine cycles. ↩
-
Explore advanced systems for improved process control.: By harnessing the reams of data produced in modern plastics processing facilities, artificial intelligence can improve machine performance. ↩
-
Learn how inverter control enhances precision in flow rate adjustments.: An inverter control, on the other hand, is a type of control system that uses an inverter to adjust the speed of a motor. It is commonly used in … ↩
-
Understand the role of servo motors in precise flow rate management.: The servo motor on the servo-driven pump machine only operates if the hydraulics demand oil flow. During the time when no axis is operating, … ↩
-
Learn how real-time feedback enhances injection molding precision.: Matics provides real-time production monitoring that enables injection molding operations to aggregate and analyze the KPIs they need to optimize their … ↩
-
Explore the latest innovations in injection molding.: A great innovation for injection molding is structural foam molding. This process combines injection molding and gas-assisted injection molding … ↩
-
Learn why servo motors are ideal for high-precision manufacturing.: The benefits of incorporating servo systems in injection molding are undeniable. Precision, energy efficiency, speed, versatility, and reduced noise levels ↩
-
Understand how closed-loop systems enhance quality and stability.: Instead, the part is 90 to 95 percent filled during injection, and then fully packed out during pack and hold. This prevents the melt from smacking the tool and … ↩
-
Discover how adjustable feed pipes offer budget-friendly flow control.: The injection molding process works by adding plastic pellets or metal powder to the injection molding machine’s hopper. Next, the hopper pours … ↩
-
Explore how inverter control allows flexible flow rate adjustments.: An inverter control, on the other hand, is a type of control system that uses an inverter to adjust the speed of a motor. It is commonly used in … ↩
-
See how proportional valves provide precise flow and pressure management.: Injection molding operations demand high speed motion and tight pressure control. … proportional valve that controls flow and pressure to an injection cylinder. ↩