Ever face a big problem with injection molding? I want to share what I have learned about common challenges. Together, we will probably find ways to get past them.
Injection molding limitations include difficulty with complex shapes, material constraints, size restrictions, and potential high costs. Overcoming these involves optimizing design, selecting suitable materials, and utilizing advanced technologies to enhance efficiency and product quality.
During my time in product design, I have faced many challenges with injection molding. Complex shapes sometimes seem impossible to create. Managing material quirks often disrupts the process. These limitations often feel really daunting. I’m ready to help you solve each of these problems. We will discover solutions together. Transform these obstacles into stepping stones. This very important change will lead to smoother production lines.
Injection molding can create complex shapes without issues.False
This claim is false; injection molding often struggles with complex shapes due to design limitations.
High costs are a significant limitation of injection molding.True
This claim is true; one of the main challenges of injection molding is its high cost, impacting production efficiency.
What are the common defects in injection molded products?
Injection molded products might be a little tricky sometimes, right? I’ve noticed many problems during production. Knowing these defects is very important for anyone in design or manufacturing. Let’s explore this together!
Common problems in injection molded products include short shots, warpage and surface defects like flow lines. Flash, burn marks and color variations also occur. Identifying these issues helps improve product quality. Manufacturing probably becomes more efficient too.
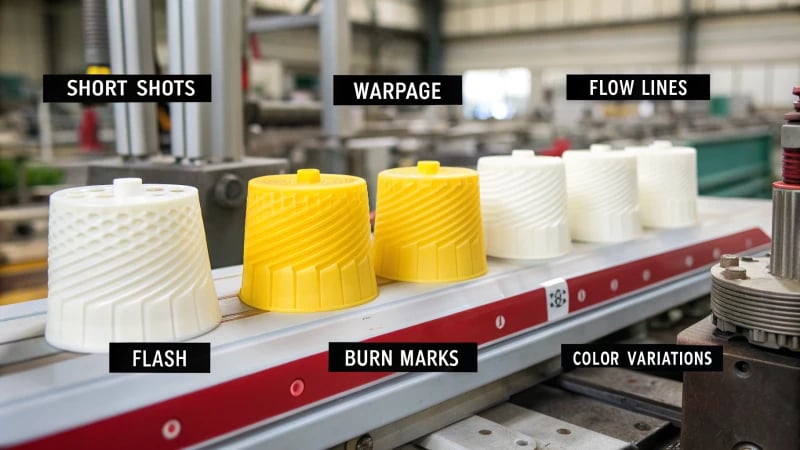
Common Defects in Injection Molded Products
Injection molding is an intriguing but tricky way to create products. Over time, I noticed that knowing the usual problems really saves time and money. Here’s what I discovered:
-
Short Shots
A common defect occurs when the mold does not fill completely, leaving voids or unfilled areas. This often results from:- Complex shapes that hinder material flow.
- Insufficient injection pressure.
- Poor design of the gates and runners.
-
Warpage
Warping happens when there is uneven cooling of the molded part, leading to distortion. Factors include:- Thick and thin areas in the mold design.
- Temperature variations in the cooling process.
- Improper mold design leading to uneven shrinkage.
-
Surface Defects
Various issues can arise on the product surface:- Flow Lines: Visible lines due to the flow of the molten plastic. These often indicate poor material flow.
- Sink Marks: Dents or depressions on the surface caused by insufficient material filling, especially in thicker areas.
-
Flash
This defect occurs when excess material escapes from the mold cavity during injection, creating thin projections on the edges of parts. Causes include:- High injection pressure.
- Worn or damaged molds.
-
Burn Marks
These dark marks appear due to overheating of the plastic material in the mold. Common reasons for burn marks include:- Trapped air that heats up during injection.
- Slow injection speed that causes material degradation.
-
Color Variations
Inconsistent coloring can result from:- Incomplete mixing of colorants or additives.
- Variations in processing temperatures that affect color distribution.
Strategies to Mitigate Defects
Identifying these issues is just the start! Over the years, I used many methods to overcome them:
Defect | Mitigation Strategy |
---|---|
Color Variations | Better mixing techniques and monitoring processing conditions closely is crucial. |
Understanding these defects and applying smart solutions really improves production quality.
For those interested in learning more, check out this guide1 or explore advanced simulation techniques2. You won’t regret it!
Short shots occur when the mold is not completely filled.True
Short shots leave voids in molded products due to incomplete filling, often from poor design or insufficient pressure.
Warpage is caused by even cooling of the molded part.False
Warpage results from uneven cooling, leading to distortion in injection molded products, not even cooling.
How can design optimization improve injection molding outcomes?
Have you ever thought about how design changes improve your injection molding processes? Explore ways to transform product quality and boost production efficiency. Use focused strategies that truly matter.
Design optimization improves injection molding results by refining mold designs. It enhances material flow and increases production speed. Manufacturers use techniques like simulation analysis. Automated processes also help them. These methods effectively solve common problems. They really improve the quality of the product.
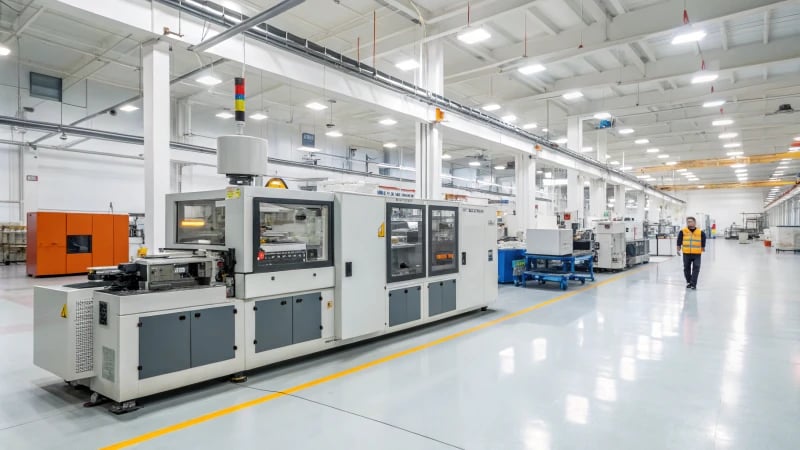
Understanding Design Optimization in Injection Molding
Design optimization transforms injection molding methods. I remember my first mold design task – it felt exciting yet challenging to improve efficiency while keeping product quality intact. By carefully changing both product and mold designs, many common issues in the injection molding process could be resolved.
Addressing Limitations of Product Shape Complexity
Complex product shapes sometimes bring big challenges. Intricate designs can lead to problems like short shots, where molds do not fill completely. I faced situations where difficult cross-hollow structures caused these incomplete fillings. It felt like a complex puzzle to solve.
To tackle these issues, I discovered:
- Optimizing mold design with hot runner systems often improved melt flow. This helped the material fill tricky cavities more easily.
- Using simulation analysis technology revealed potential problems during design. I adjusted designs before starting production.
Overcoming Material Limitations
Choosing materials is very critical in injection molding. High-viscosity materials can feel like pushing thick syrup through a straw! These materials lead to slower production due to long filling times, which is very frustrating.
To solve this, I learned:
- Adding additives to materials improved fluidity. It made stubborn materials easier to handle.
- Adjusting injection parameters like temperature and pressure based on the material helped smoother filling and lowered defects.
Material Type | Challenges | Solutions |
---|---|---|
High-viscosity | Difficult flow in molds | Add lubricants and modify processes |
Temperature-sensitive | Risk of degradation during molding | Use stabilizers for better control |
Addressing Size Limitations
Size limits often bring restrictions due to machine capabilities. Large items need a lot of clamping force, while tiny parts require extreme precision.
- Selecting the right injection molding machine for specific products became crucial. I learned from experience to choose machines that met unique size demands.
- For large items, employing multi-stage injection technology improved flow and cooling management. It made the process feel less like a struggle.
Enhancing Production Efficiency
Production efficiency feels like a roller coaster – a mix of ups and downs. To make things smoother, I found:
- Automated production systems drastically streamline processes. They greatly cut down the need for manual work, relieving our team.
- Through careful experiments, I optimized each phase of the injection cycle. This shortened cycle times while maintaining quality.
Cycle Phase | Optimization Strategies |
---|---|
Clamping | Use quick mold change systems |
Injection | Optimize speeds and pressures |
Cooling | Employ advanced cooling techniques |
Cost Management Strategies
Cost challenges in injection molding often feel overwhelming, especially with expensive equipment and material waste. To overcome these challenges, I started:
- Standardizing mold components, which really reduced design and manufacturing costs. It was great for our budget.
- Introducing a material recycling system to reuse waste materials. This minimized expenses and supported sustainability.
Conclusion Without Conclusion
in summary, effective design optimization is more than just a strategy; it boosts the quality of injection molded products and tackles challenges directly. Focusing on mold design, material properties, production efficiency and cost management can lead to amazing results in injection molding processes. If you’re interested in learning more advanced methods, explore advanced techniques3 or check out cost-effective strategies4.
Design optimization reduces the risk of short shots in molding.True
By refining mold design, manufacturers can enhance melt flow, minimizing short shots during the injection molding process.
High-viscosity materials always lead to production delays.False
While high-viscosity materials can slow down production, proper adjustments and additives can improve flow and mitigate delays.
How Do Materials Shape the Limitations of Injection Molding?
Join me on a journey through the fascinating world of injection molding. The materials we choose affect our production dreams. These choices impact everything, from complexity to efficiency.
Materials heavily influence the limits of injection molding. They impact product complexity, size constraints and efficiency in production. Understanding material properties allows designers to lower defects. Designers also simplify processes with this knowledge. This understanding really leads to improved manufacturing results.
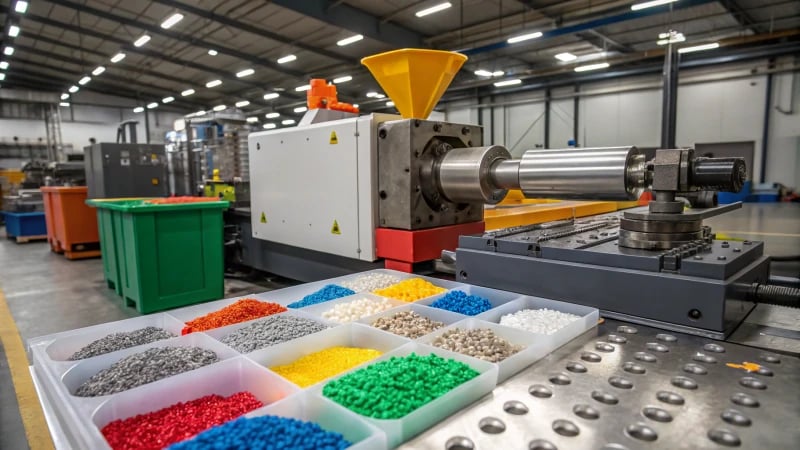
Material Limitations in Injection Molding
Injection molding relies heavily on the materials used. These materials shape not only the end product but also the production journey. Designers must understand material properties to tackle challenges and improve product quality.
Complexity of Material Properties
Injection molding encourages creativity but has specific rules. Thermoplastic materials are popular for their flexibility. However, high viscosity materials present challenges. I once worked with a high-viscosity polymer. We needed to change our entire approach because of it. The machinery required more pressure, becoming a serious task.
- High Viscosity Materials: These require strong machinery to handle high pressure. Such machines are not always available.
- Temperature-Sensitive Materials: We struggled with biodegradable plastics. The perfect temperature was crucial and hard to achieve.
Exploring material properties helps avoid problems like short shots5. It leads to a smooth filling process.
Size Constraints Based on Material Type
Size decisions often rely on material choices. Different materials have various size limits. Here’s a breakdown of how size limits vary:
Material Type | Size Limitations |
---|---|
Thermoplastics | Generally suitable for medium to large parts; size is limited by machine capabilities. |
Thermosetting Plastics | Often used for smaller parts due to curing requirements; larger sizes may lead to uneven curing. |
High-Viscosity Materials | Can only be used in specific applications where high clamping force and precise temperatures are maintained. |
Once, I designed an automotive part. Size restrictions demanded special machines with high clamping forces. It was challenging!
Impact on Production Efficiency
Material choice influences injection molding efficiency. High-viscosity materials need more force and lengthen injection cycles.
The cycle time includes:
- Clamping Time
- Injection Time
- Cooling Time
- Ejection Time
We used automated monitoring systems once. They tracked and adjusted parameters in real-time, greatly improving our production.
Strategies for Overcoming Material Limitations
To manage material limitations, I use several strategies:
- Material Modification: Flow-enhancing additives turn high-viscosity materials into easier tasks.
- Optimized Process Parameters: Adjusting temperature and pressure based on material type results in better outcomes; higher temperatures work well for high-melting materials.
Understanding material impacts allows us to improve product design and manufacturing for very successful outcomes.
Thermoplastics are the most versatile materials for injection molding.True
Thermoplastics are widely used in injection molding due to their adaptability and ease of processing, making them suitable for various applications.
High-viscosity materials reduce injection molding efficiency.True
High-viscosity materials require more force and longer cycle times, negatively impacting overall production efficiency in injection molding processes.
What are the real costs of overcoming injection molding challenges?
Ever thought about the secret costs behind issues in injection molding? Let’s dive into this complicated financial puzzle. We’ll discover how manufacturers handle these challenges. They strive for very high quality and efficiency.
Overcoming challenges in injection molding involves various costs. Equipment requires investment. Choosing materials involves expenses. Efficiency improvements demand resources. Waste control needs strategies. Labor incurs expenses. Operational costs last long-term. Understanding these aspects helps manufacturers control budgets. Quality remains a priority.
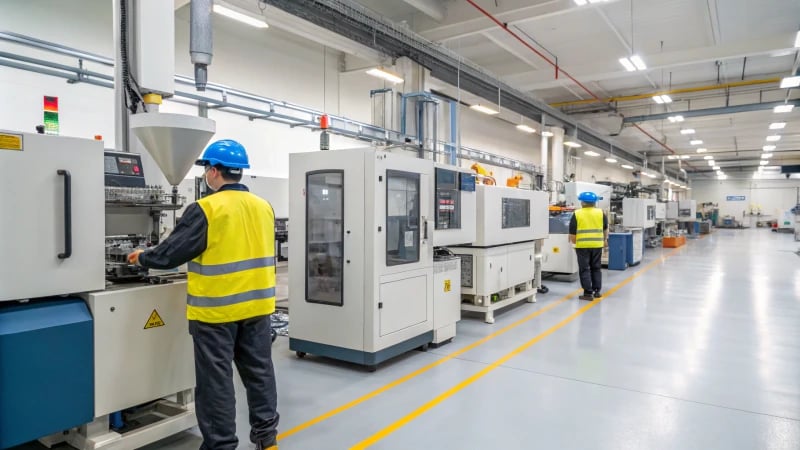
Understanding the Cost of Overcoming Injection Molding Challenges
Overcoming challenges in injection molding is essential for maintaining quality and efficiency, but it comes with significant financial implications. These costs can be categorized into several key areas:
1. Equipment and Tooling Costs
The initial investment in high-quality injection molding machines and molds can be substantial. Precision machines that can handle complex designs often cost hundreds of thousands of dollars. Additionally, specialized molds for intricate parts can add tens of thousands more.
Equipment Costs Breakdown:
Item | Estimated Cost Range |
---|---|
Standard Injection Molding Machine | $50,000 – $250,000 |
Precision Injection Molding Machine | $250,000 – $1,000,000 |
Custom Mold Design | $10,000 – $100,000 |
*For further insights into the types of machines available, check out this comprehensive guide6.
2. Material Costs
Material selection plays a pivotal role in injection molding costs. High-viscosity or temperature-sensitive materials often require additional processing steps to ensure quality. Modifications such as adding lubricants or stabilizers can lead to increased material costs.
3. Production Efficiency
Improving production efficiency can mitigate some costs associated with injection molding challenges. For example, implementing automation can enhance cycle times and reduce labor costs. However, this comes with its own set of upfront expenses.
Cost Savings through Automation:
Automation Type | Estimated Cost | Potential Savings |
---|---|---|
Robotic Arms | $20,000 – $100,000 | Up to 30% in labor costs |
Quick Mold Change Systems | $5,000 – $50,000 | Reduced downtime |
*Learn more about automation technologies in manufacturing with this informative article7.
4. Waste Management Costs
During the injection molding process, waste generation is inevitable, whether it’s excess material from the gates or defective parts. Strategies to minimize waste, such as optimizing mold design or using hot runner systems, are essential.
- Explore waste reduction techniques8 to optimize your production process and save on material costs.
5. Labor Costs
As processes become more complex due to overcoming challenges, the need for skilled labor increases. Investing in training programs can significantly impact labor costs. Skilled operators can manage multiple machines and reduce errors during production.
6. Long-term Operational Costs
While initial investments may be high, the long-term operational costs are also critical to consider. These include maintenance of machinery and molds, which can vary significantly based on usage and complexity.
Long-term Cost Considerations:
Cost Type | Frequency | Estimated Annual Cost |
---|---|---|
Maintenance of Machines | Monthly | $5,000 – $20,000 |
Mold Replacement | Every 2-5 years | $10,000 – $100,000 |
By strategically analyzing these cost implications, manufacturers can make informed decisions that balance quality and efficiency while managing their budget effectively. This proactive approach helps in navigating the challenges that come with injection molding processes.
High-quality injection molding machines can cost up to $1 million.True
Precision machines for complex designs can range from $250,000 to $1 million, highlighting the significant investment required.
Automation in injection molding always reduces overall costs.False
While automation can lower labor costs, it requires upfront investment and may not guarantee overall cost reduction depending on specific circumstances.
Conclusion
Explore the limitations of injection molding, including shape complexity, material constraints, size restrictions, production inefficiencies, and costs while discovering effective strategies for overcoming these challenges.
-
Discover practical solutions to prevent defects in your injection molded products and enhance quality control processes. ↩
-
Learn about advanced techniques that can be applied in injection molding to reduce common defects and improve outcomes. ↩
-
Discover advanced design optimization strategies that can significantly enhance your injection molding outcomes. ↩
-
Explore cost-effective methods to enhance your injection molding processes through design optimization. ↩
-
Understanding how material properties impact injection molding will help you choose the right materials for your projects, improving quality and efficiency. ↩
-
Explore comprehensive insights on managing injection molding costs effectively. ↩
-
Understand how automation can enhance productivity and reduce costs in injection molding. ↩
-
Discover effective waste management practices that can save costs in production. ↩