In the world of manufacturing, the longevity of injection molds is a topic that truly resonates with me.
The lifespan of an injection mold is influenced by factors like the quality of mold materials, design efficiency, proper molding processes, and diligent maintenance. High-grade materials and meticulous upkeep can extend its life from tens of thousands to millions of cycles.
While understanding these foundational factors offers a direct path to enhancing mold durability, delving deeper into each aspect can reveal nuanced insights that significantly impact overall production efficiency. Let’s explore these determinants in detail and discover strategies to maximize your mold’s potential.
High-quality mold materials extend mold lifespan.True
High-grade materials resist wear and deformation, enhancing longevity.
How Does Mold Material Impact Its Longevity?
The choice of mold material is crucial in determining the lifespan of an injection mold.
High-quality mold materials, such as durable steel, enhance mold longevity by resisting wear and deformation, allowing it to withstand numerous injection cycles.
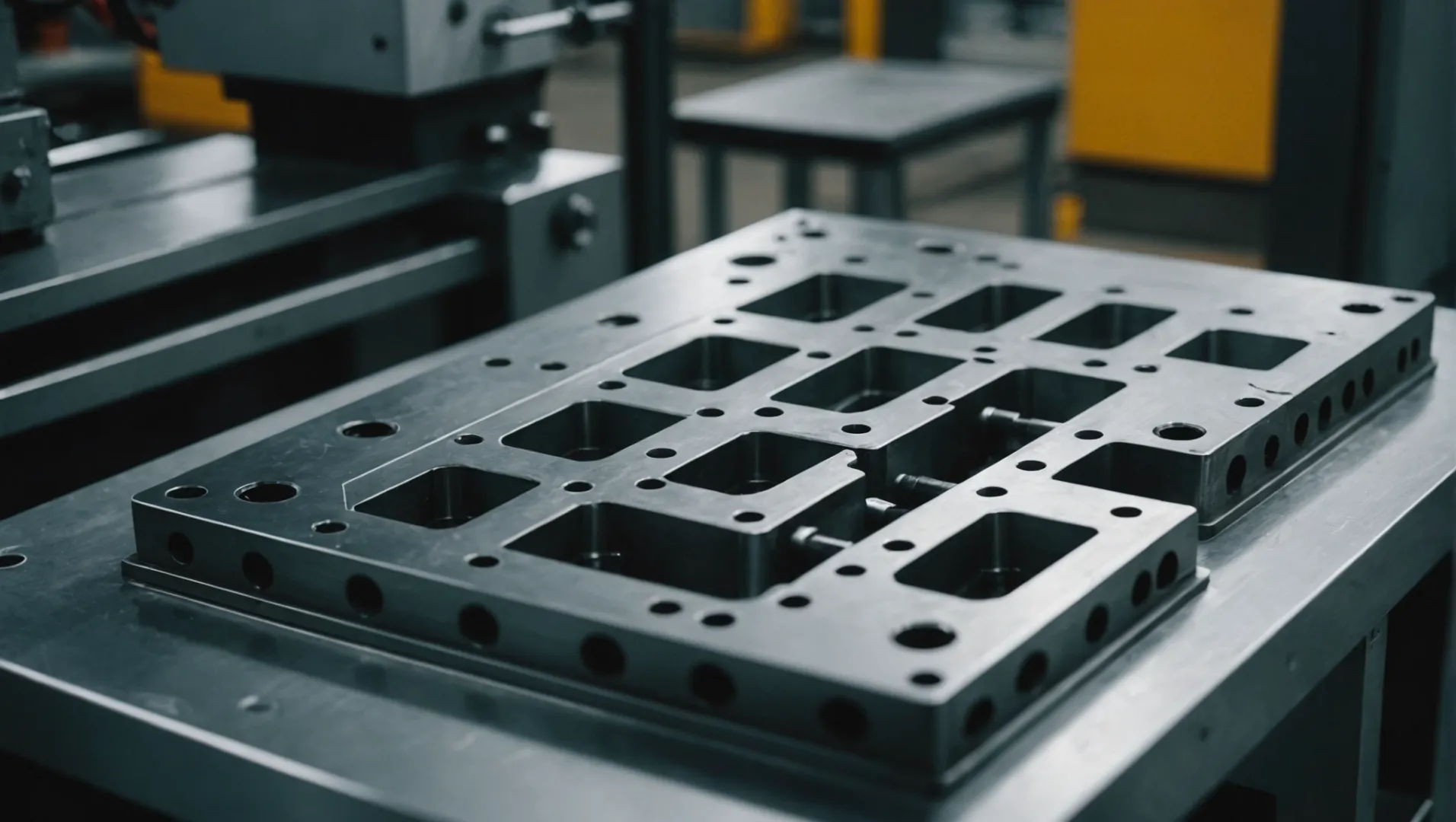
The Significance of Material Quality
Selecting the right mold material1 is paramount to its longevity. Materials like high-hardness steel provide excellent wear resistance and toughness, which are essential for enduring the immense pressures and friction involved in injection molding. For instance, imported high-performance steels can push the mold’s life expectancy to hundreds of thousands of cycles or beyond.
Comparing Material Types
When comparing various mold materials, a clear distinction emerges between high-quality and ordinary options. While superior materials like tool steel offer enhanced durability and resistance to deformation, standard materials may falter after just tens of thousands of cycles. This disparity is not only a matter of cost but a strategic choice for long-term reliability.
Material Type | Advantages | Typical Lifespan |
---|---|---|
High-quality steel | High hardness, wear resistance, toughness | Hundreds of thousands of cycles |
Standard steel | Cost-effective but less durable | Tens of thousands to lower hundreds |
Real-World Examples
In industries where precision and longevity are critical, using top-tier materials can significantly reduce downtime and maintenance costs. Consider a manufacturer utilizing high-grade steel molds: their investment translates into fewer replacements and less frequent repairs, thus optimizing production efficiency.
Balancing Cost and Durability
While opting for high-quality materials may incur higher initial costs, the long-term benefits often justify the investment. Companies must weigh the upfront expense against potential savings in maintenance and production continuity. By investing in superior materials, businesses can achieve a more sustainable operation model.
Understanding how mold material impacts longevity not only aids in better decision-making but also aligns production practices with strategic goals. This knowledge empowers manufacturers to optimize both cost efficiency and product quality over the lifespan of their molds.
High-quality steel molds last hundreds of thousands of cycles.True
High-quality steel offers superior wear resistance, increasing mold lifespan.
Standard steel molds are more durable than high-quality steel molds.False
Standard steel is less durable, lasting tens of thousands of cycles.
Why Is Mold Design Crucial for Durability?
When it comes to injection molds, design isn’t just an aesthetic choice—it’s a key factor in longevity.
Mold design is crucial for durability because it ensures even stress distribution and optimal cooling, preventing premature wear. A well-designed mold enhances structural integrity, maintaining performance over numerous cycles.
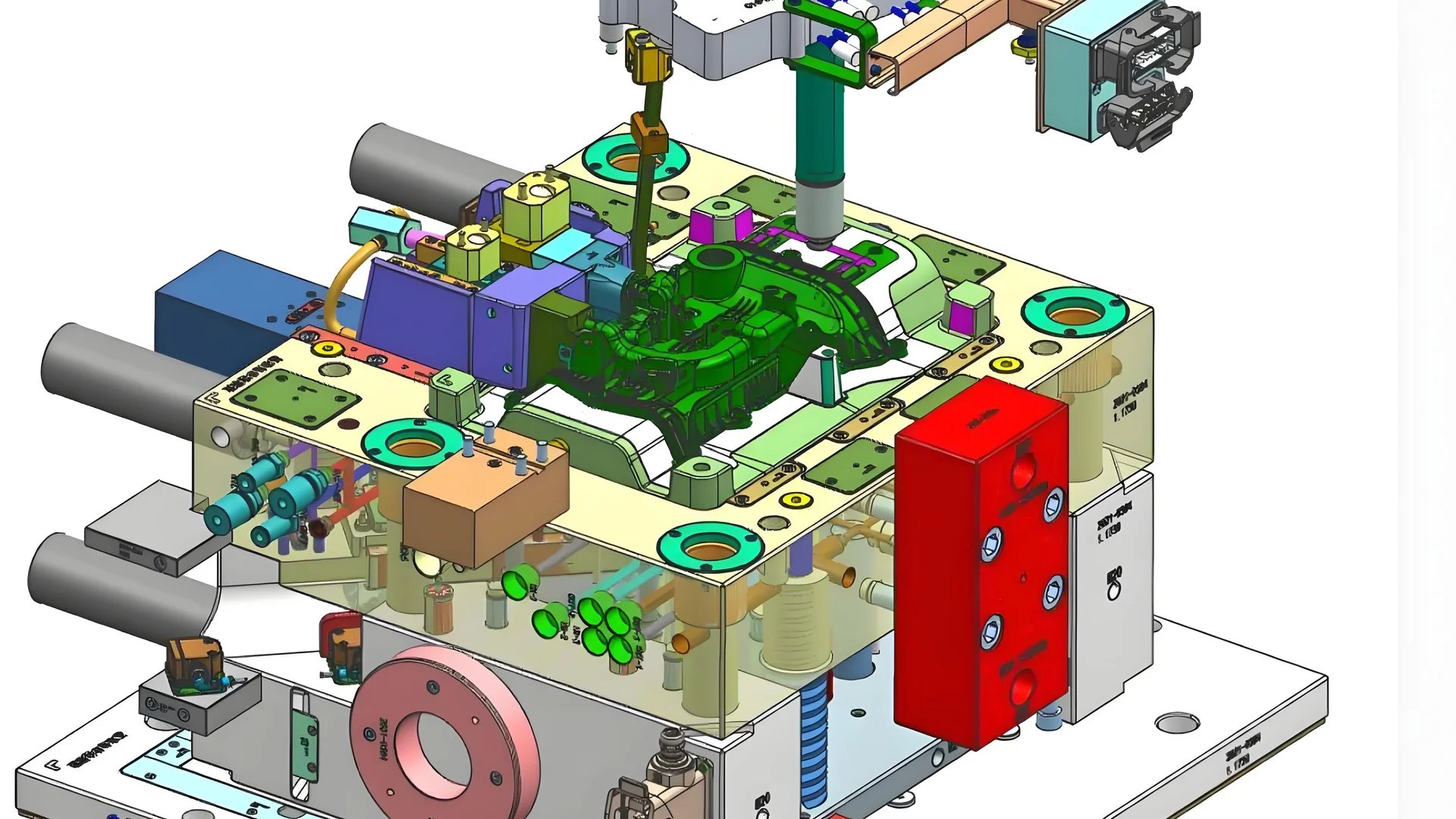
The Art of Even Stress Distribution
A well-engineered mold design is pivotal in ensuring that stress is distributed evenly during each injection cycle. Uneven stress can lead to early fatigue and wear, significantly reducing the mold’s lifespan. By incorporating reinforcing ribs2 and optimizing the flow channel design, manufacturers can alleviate localized stress concentrations, promoting a more uniform distribution.
For instance, in scenarios where the flow of material is not adequately controlled, certain sections of the mold may bear more pressure, leading to deformation or cracking. This is particularly evident in complex mold designs where multiple cavities exist.
Importance of Cooling System Efficiency
Another critical aspect of mold design is the implementation of an efficient cooling system. Molds operate under high temperatures, and without a proper cooling mechanism, they are susceptible to thermal fatigue. This not only affects the immediate output quality but also accelerates wear.
A well-conceived cooling system can regulate mold temperature, preventing adverse effects such as warping or premature aging. For example, a poorly designed cooling system may result in uneven cooling rates across the mold surface, leading to stress fractures over time.
Material Considerations in Mold Design
Selecting appropriate materials that align with the mold design is equally essential. High-quality steel with excellent hardness and toughness characteristics can withstand repeated cycles without significant wear. However, the design must account for material properties like expansion and contraction under thermal conditions.
In contrast, using ordinary materials might lead to problems such as increased wear or deformation after a fewer number of cycles. Consequently, designers must carefully consider material choice in conjunction with design elements to maximize durability.
Case Study: Successful Mold Design Implementation
Consider a company manufacturing automotive parts that revamped its mold design to include advanced cooling channels and reinforced structural elements. This redesign resulted in molds that not only lasted longer but also improved production efficiency due to reduced downtime for repairs.
This case highlights the tangible benefits of thoughtful mold design beyond longevity—it can lead to significant cost savings and operational efficiency enhancements. By exploring best practices3 in mold design, companies can realize these advantages.
Even stress distribution prevents mold wear.True
Even stress distribution reduces localized fatigue, extending mold lifespan.
Poor cooling leads to mold thermal fatigue.True
Inefficient cooling causes uneven temperatures, leading to thermal damage.
What Role Does the Injection Molding Process Play in Mold Life?
The injection molding process is pivotal in determining the lifespan of a mold.
The injection molding process directly influences mold life through critical parameters like pressure, temperature, and speed. Proper calibration and maintenance ensure reduced wear, optimal performance, and extended mold longevity.
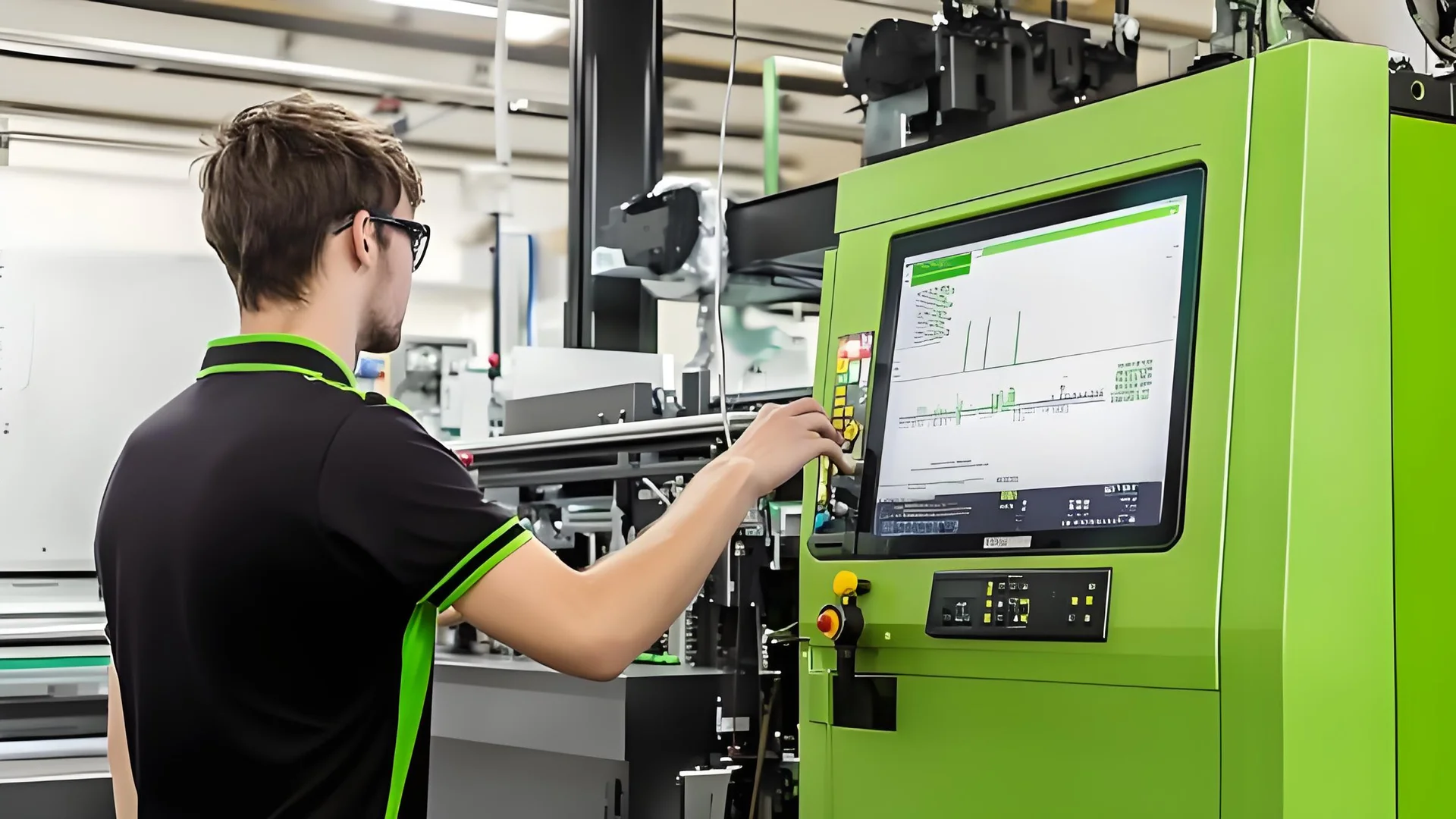
Understanding Injection Molding Parameters
Injection molding is a complex process that relies on fine-tuning several parameters. Among these, injection pressure4, temperature, and speed play significant roles in determining the lifespan of a mold.
- Injection Pressure: High pressure can accelerate wear and deformation of the mold. It’s vital to calibrate pressure settings to balance between product quality and mold preservation.
- Temperature: Excessive temperatures can soften mold materials, leading to reduced strength and wear resistance. Maintaining optimal thermal conditions is crucial for mold durability.
- Speed: Fast injection speeds can cause undue stress on the mold, potentially leading to premature failure.
Importance of Regular Machine Maintenance
Regular maintenance of the injection molding machine is equally crucial for extending mold life. Consistent care ensures the machine operates within ideal parameters, reducing the risk of sudden breakdowns or errors that could damage the mold. Maintenance routines often include:
- Cleaning: Removing any residues from previous cycles that might affect subsequent operations.
- Lubrication: Ensuring moving parts are well-lubricated to prevent unnecessary friction and wear.
- Inspection: Regular checks to identify any early signs of wear or damage that could be rectified before escalating.
Case Study: The Impact of Parameter Optimization
In a case study involving an automotive part manufacturer, optimizing the injection molding parameters led to a 20% increase in mold life. By meticulously adjusting injection pressure and temperature, they were able to reduce mold wear significantly. This not only extended the mold’s lifespan but also resulted in more consistent product quality.
Implementing a strategic approach to parameter control and machine maintenance can significantly enhance mold longevity, thereby reducing costs associated with frequent replacements and downtime. These practices ensure a balance between high-quality production and sustainable operations.
High injection pressure accelerates mold wear.True
Excessive pressure can deform and wear out the mold faster.
Regular maintenance has no effect on mold life.False
Maintenance prevents breakdowns, extending the mold's lifespan.
How Can Effective Maintenance Practices Extend Mold Lifespan?
Mold maintenance is a critical yet often overlooked aspect of extending the lifespan of injection molds.
Regular cleaning, lubrication, and inspection are essential maintenance practices that can significantly extend the lifespan of an injection mold. Addressing wear or damage promptly, and employing systematic maintenance routines, prevent minor issues from escalating and ensure optimal mold performance throughout its service life.
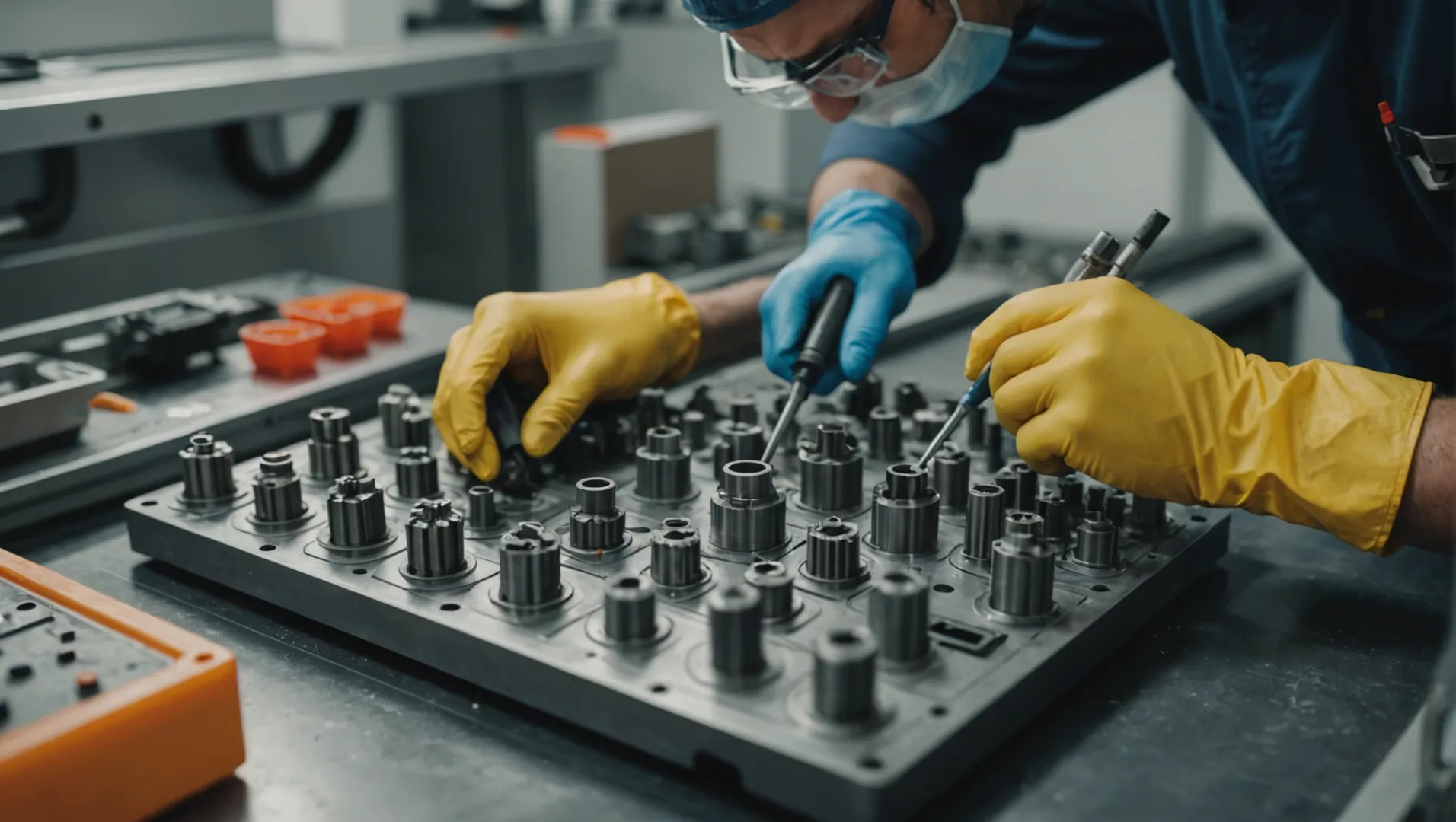
Regular Cleaning Practices
One of the most fundamental maintenance practices is regular cleaning. This involves removing residue and buildup from the mold surface, which, if left unattended, can lead to defects in production and increase wear on the mold. For instance, plastic or other material residues can cause surface irregularities, ultimately affecting the quality of the products and shortening the mold’s life.
Cleaning Checklist
Step | Action Description |
---|---|
Surface Wiping | Remove dust and minor residues with soft cloths |
Deep Cleaning | Use solvents or approved cleaners for tough grime |
Inspection | Check for surface scratches or material buildup |
Importance of Lubrication
Lubricating moving parts of a mold is crucial to prevent friction and wear. The choice of lubricant should be based on the mold material and operating conditions. Applying the right type of lubricant can reduce friction between components, thus minimizing wear and extending mold life.
Timely Inspections
Routine inspections are necessary to identify early signs of wear or potential failure. These inspections should cover aspects such as:
- Checking for cracks or deformations in the mold structure.
- Verifying the alignment and fit of different components.
Such inspections allow for timely repairs, like replacing worn inserts5 or fixing minor damages before they develop into major problems.
Systematic Maintenance Schedule
Establishing a maintenance schedule ensures that all necessary checks and repairs are conducted regularly. This schedule should be tailored to the specific usage patterns and operational demands of each mold. For example, molds used in high-volume production might require more frequent inspections compared to those used less intensively.
Addressing Wear Promptly
Minor wear and tear are inevitable; however, addressing these issues promptly can prevent them from escalating. Techniques such as surface polishing6 or component replacement can restore mold integrity without significant downtime.
By adopting a proactive approach to maintenance, manufacturers can enhance the durability and efficiency of their injection molds, ensuring consistent quality and reducing long-term costs.
Regular cleaning prevents mold defects.True
Regular cleaning removes residues that cause surface irregularities.
Skipping lubrication extends mold lifespan.False
Lubrication reduces friction, preventing wear and extending mold life.
Conclusion
By focusing on high-quality materials, thoughtful design, precise process control, and routine maintenance, manufacturers can extend mold life and enhance production efficiency.
-
Explore detailed insights into material quality’s role in mold longevity.: Molds on precision machines demonstrated a 20% increase in lifespan, with average life expectancies reaching up to 1.1 million cycles. Quality … ↩
-
Discover how reinforcing ribs improve mold strength and reduce stress.: Both ribs and gussets provide stability in parts without having to increase wall thickness, and are particularly beneficial for parts with already thin walls. ↩
-
Learn effective strategies for designing durable molds.: Design Tips for Injection Molding · 2. Take Into Account the Part Tolerance · 3. Choose the Right Wall Thickness · 4. Add Draft Angles to Your Design · 5. Add … ↩
-
Learn how correct pressure settings reduce mold wear.: It is one of the most important factors that determine the quality and consistency of the final product. The injection pressure required for a … ↩
-
Guides on replacing inserts help prevent extensive mold damage.: Most of them are done in the press. We have quick change that can be done from the side of mold. Normally going from a logo to a IML insert. ↩
-
Learn how polishing restores mold surfaces effectively.: Assuming the surface has been burned with an EDM finish, we recommend using a #6302 Gesswein stone to begin the polishing process. ↩