Ever wondered how to make injection molding not just efficient, but truly exceptional?
Enhance injection molding with lean principles: streamline processes, reduce waste, improve quality, foster continuous improvement, engage teams, and utilize advanced technology for efficient production.
As I dove into the world of lean manufacturing, I realized that understanding these principles is just the beginning. It’s when you start applying them—like enhancing teamwork or utilizing the latest monitoring tools—that the magic happens. Let me share how I transformed my processes using lean techniques, turning challenges into opportunities for growth.
Lean principles reduce waste in injection molding.True
Lean focuses on eliminating non-value-adding activities, reducing waste.
Employee involvement is irrelevant in lean manufacturing.False
Employee involvement is crucial for fostering continuous improvement in lean.
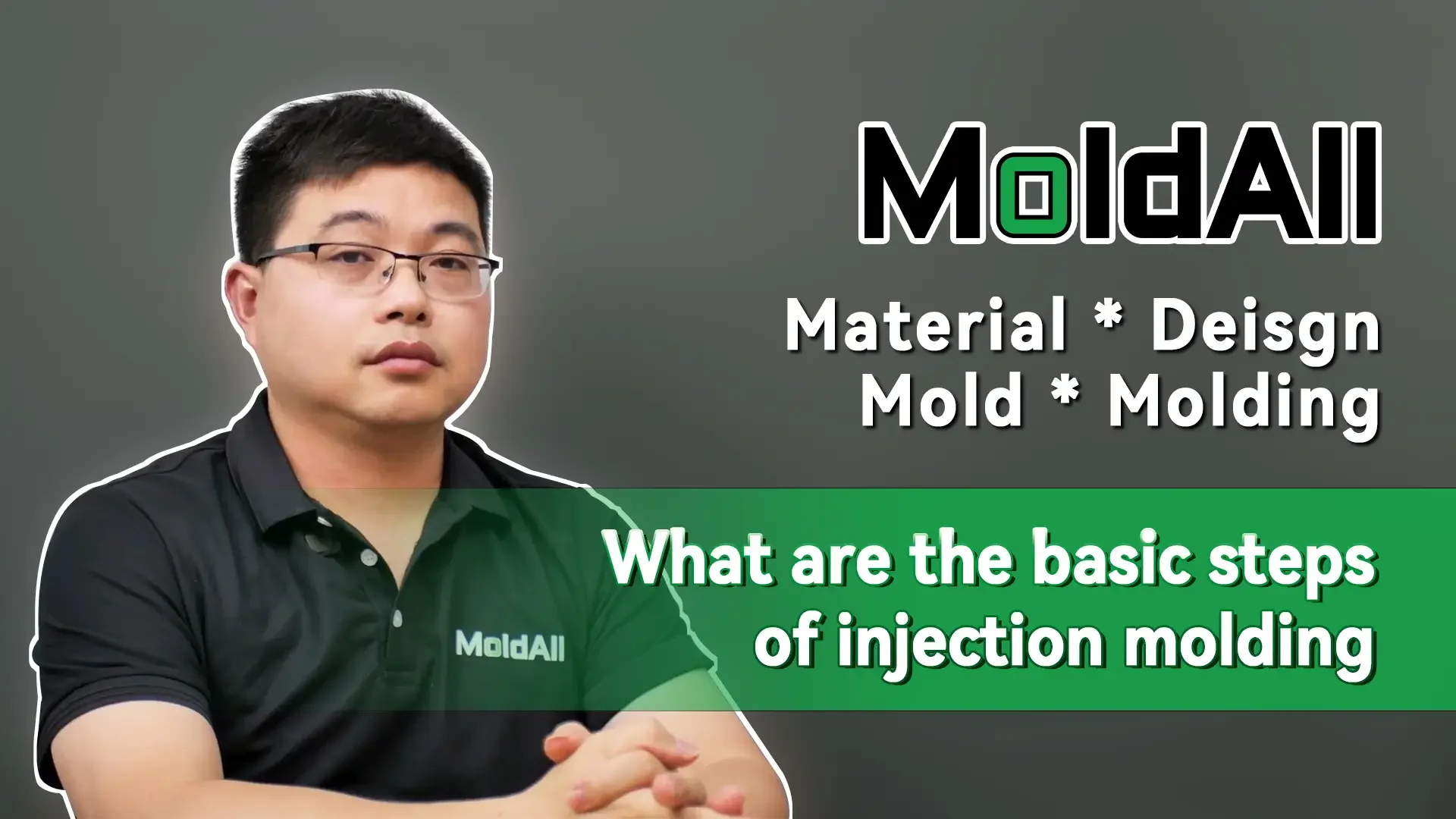
- 1. How Can Lean Manufacturing Transform Your Production Process?
- 2. How Can Waste Reduction Boost Injection Molding Efficiency?
- 3. What Role Does Employee Involvement Play in Lean Manufacturing?
- 4. How Can Technology Aid in Implementing Lean Practices in Injection Molding?
- 5. What Are Common Challenges in Adopting Lean Principles for Injection Molding?
- 6. How Do Continuous Improvement Strategies Impact Injection Molding Quality?
- 7. Conclusion
How Can Lean Manufacturing Transform Your Production Process?
Navigating the world of Lean Manufacturing can feel like unlocking a treasure trove of efficiency secrets. It’s like finding that missing puzzle piece that makes everything click into place.
Lean Manufacturing transforms production by reducing waste and enhancing efficiency through five principles: defining value, mapping the value stream, creating flow, establishing pull, and pursuing perfection.
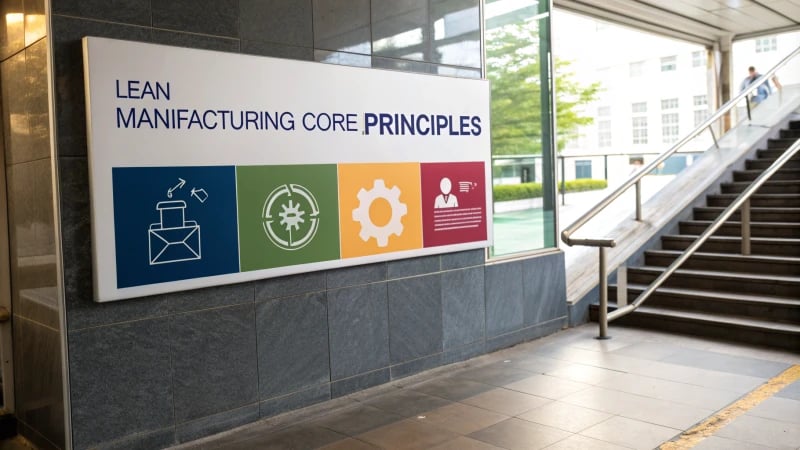
Defining Value
Imagine a world where every product meets your exact needs—no fluff, just function. That’s what defining value in Lean Manufacturing is all about. I remember the first time I realized how much unnecessary work went into creating features no one asked for. It was like trimming the fat from a steak; suddenly, everything was leaner and more satisfying.
By honing in on what truly matters to the customer, companies not only cut costs but also make their customers happier. That’s a win-win if you ask me.
Customer Need | Feature Provided |
---|---|
Aesthetic | Sleek Design |
Functional | Durability |
By focusing on value, companies can streamline production, reduce costs, and improve customer satisfaction1.
Mapping the Value Stream
This principle is like taking a highlighter to your entire process and marking out what’s really pulling its weight. In my earlier days, I’d often get lost in tasks that seemed important but added no real value. Mapping helps identify those steps that are just taking up space and energy.
- Value-added steps: These are your bread and butter, the tasks that directly enhance product quality.
- Non-value-added steps: Like old clutter in the attic, these need to be minimized or tossed out.
Once you see your processes clearly, prioritizing improvements becomes almost instinctual, leading to better process improvements2.
Creating Flow
Creating flow reminds me of a perfectly choreographed dance where everyone knows their next move without missing a beat. I learned this the hard way when projects got bogged down in endless backlogs. Balancing workloads and smoothing out bottlenecks is crucial for keeping everything moving seamlessly.
- Continuous Flow: Picture a river that flows without breaks—smooth and constant.
- Work Balancing: Think of it like splitting a pizza evenly; no one wants to be left hungry.
The result? Faster production times3 and smarter use of resources, turning chaos into harmony.
Establishing Pull
Switching from a push to a pull system was like flipping a switch from chaos to calm in our inventory. It’s about producing based on what people actually need rather than guessing. I once worked on a project where we produced so much extra stock it was like drowning in plastic parts.
- Just-in-Time (JIT): Only create what’s needed at the moment it’s needed, just like cooking only as much pasta as you’ll eat.
- Kanban System: This is your traffic light system—signals tell you when it’s time to start or stop.
With pull systems, inventory woes become a thing of the past, making inventory management4 a breeze.
Pursuing Perfection
The idea of never being finished can be exhausting, but pursuing perfection is about small continuous tweaks. When I first encountered Kaizen, it felt daunting until I realized it was more about building momentum than reaching an endpoint. Think of it as constantly sharpening your tools so they’re ready for anything.
- Kaizen: This philosophy is like taking baby steps that eventually lead to giant leaps.
- Feedback Loops: Constant evaluations that keep you honest and your processes on point.
By striving for perfection, you’re not just improving; you’re ensuring your business stays on top of its game with a sustainable competitive advantage5.
Lean Manufacturing focuses on minimizing waste.True
Lean Manufacturing aims to reduce waste and improve efficiency.
Creating flow in Lean Manufacturing increases production time.False
Creating flow reduces production time by ensuring smooth processes.
How Can Waste Reduction Boost Injection Molding Efficiency?
From transforming scrap into savings, waste reduction is key to making injection molding not only greener but also more efficient and cost-effective.
Reducing waste in injection molding enhances efficiency by lowering material costs, accelerating production, and improving product quality, leading to cost savings and sustainable practices.
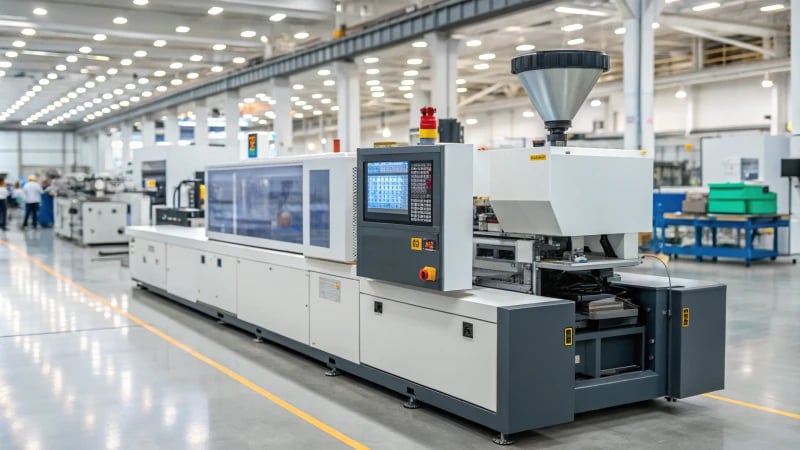
Material Usage Optimization
I remember the first time I saw a runnerless mold in action. It was like watching magic happen. The usual heap of plastic waste was gone, and what emerged was a clean, efficient process. Reducing waste isn’t just about being eco-friendly—it’s about slashing those raw material costs too. By optimizing the design of molds6, we can minimize excess material and improve the flow, which is crucial in keeping expenses down.
For example, using runnerless molds can significantly cut down on waste produced during the molding process. This approach eliminates the need for additional trimming and reduces post-production scrap.
Cycle Time Reduction
Every second counts in manufacturing. I once had a project where a few tweaks to the cooling system cut cycle times by a whopping 20%. Designing molds that allow for efficient cooling and ejection of parts can drastically reduce the time each part spends in the mold. A well-designed cooling system7 ensures uniform temperature distribution, which not only speeds up production but also reduces defects.
Quality Improvements
Precision in material usage directly translates into higher quality products. The fewer defects we have, the fewer rejections and reworks we need to deal with. I find that employing real-time monitoring systems is a game-changer. These systems keep tabs on production metrics, allowing us to address any deviations immediately and maintain consistent quality across batches.
Cost Savings and Sustainability
Cutting down on waste saves money on materials and reduces energy consumption. It’s a win-win situation—less energy means lower costs and a smaller carbon footprint. Sustainability initiatives8 are becoming a key focus in our industry, and waste reduction aligns perfectly with these goals.
Implementing lean manufacturing principles can drive more sustainable operations, hitting both economic and environmental targets. I’ve seen firsthand how these strategies transform not just the bottom line but also contribute to a cleaner, more responsible way of doing business.
Strategy | Benefit | Example |
---|---|---|
Runnerless Molds | Reduced Material Waste | Less Trimming Required |
Efficient Cooling Systems | Faster Cycle Times | Uniform Temperature |
Real-time Monitoring | Improved Product Quality | Fewer Defects |
By integrating these practices, manufacturers like us can craft a more efficient, cost-effective, and sustainable production process that meets modern demands for quality and environmental responsibility. I often think back to my early days in the industry and marvel at how far we’ve come, all thanks to innovations in waste reduction.
Runnerless molds reduce material waste in injection molding.True
Runnerless molds eliminate excess material, reducing waste and scrap.
Waste reduction increases energy consumption in molding processes.False
Reducing waste decreases energy use by minimizing material processing.
What Role Does Employee Involvement Play in Lean Manufacturing?
Ever wondered how getting employees involved in lean manufacturing can transform your operations? Let’s dive into the essential role they play in driving efficiency and fostering innovation.
Employee involvement in lean manufacturing is crucial as it fosters continuous improvement, boosts problem-solving, and enhances productivity by engaging employees to identify inefficiencies and streamline processes.
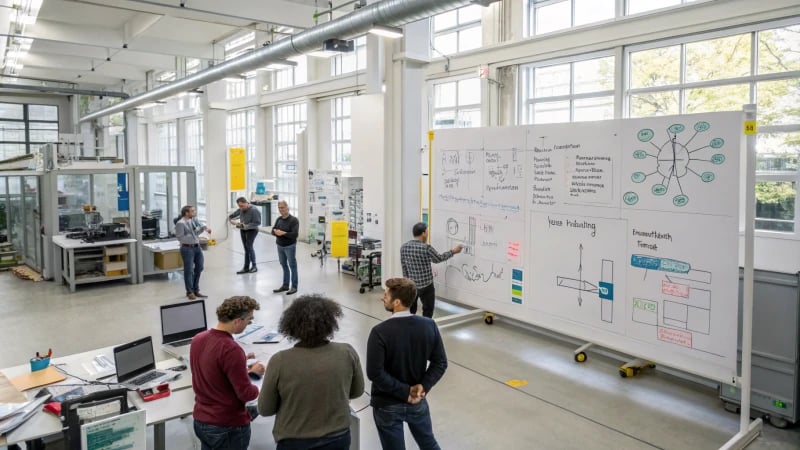
The Foundation of Lean Manufacturing
When I first got involved in lean manufacturing, it was like stepping into a new world focused on cutting waste and boosting productivity. It’s all about creating an environment where everyone feels empowered to spot inefficiencies and suggest improvements. I remember a time when one of my colleagues pointed out a bottleneck in our assembly line that we hadn’t noticed before. This kind of proactive engagement is what lean manufacturing thrives on. By engaging employees9 at every level, you can foster a culture where continuous improvement becomes second nature.
Benefits of Employee Engagement
-
Enhanced Problem-Solving
I’ve seen firsthand how employees who are directly involved in the day-to-day operations bring valuable insights that can lead to innovative solutions. I recall a brainstorming session where an idea from the production floor completely changed how we approached a recurring issue.
-
Increased Productivity
When people feel their voices are heard and appreciated, their motivation to refine processes naturally ramps up. Reflecting on some case studies about employee motivation10, it’s clear that such engagement leads to remarkable productivity gains.
Tools for Employee Involvement
In my experience, implementing the right tools can make a significant difference in how smoothly lean practices are adopted.
Tool Name | Purpose |
---|---|
Kaizen Events | Short-term projects to implement rapid changes |
Gemba Walks | Observational tours to identify waste |
Suggestion Systems | Platforms for employees to propose ideas |
These tools have been pivotal in creating an atmosphere where everyone feels they can contribute actively, resulting in a more inclusive workplace.
Encouraging a Culture of Continuous Improvement
Creating a culture of continuous improvement isn’t just a strategy—it’s a commitment. I learned this the hard way when I first tried to push changes without fostering the right environment. It’s essential to ensure employees feel comfortable suggesting changes and that they’re recognized for their contributions. Resources like continuous improvement frameworks11 provide valuable guidance on nurturing such an environment.
By exploring various perspectives on employee involvement in lean manufacturing, I’ve discovered strategies that align with operational needs and promote a collaborative atmosphere. Building this culture requires all levels of management to back and encourage employee participation, which ultimately leads to better outcomes for everyone involved.
Employee involvement reduces waste in lean manufacturing.True
Engaged employees identify waste areas, crucial for lean practices.
Gemba Walks are unrelated to employee involvement.False
Gemba Walks involve employees in observing and identifying waste.
How Can Technology Aid in Implementing Lean Practices in Injection Molding?
Ever wonder how technology can completely transform the way we approach lean practices in injection molding? Let me take you on a journey through the fascinating innovations that are shaping the future of manufacturing.
Technology supports lean injection molding by using automation, real-time analytics, and advanced quality systems to streamline processes, minimize waste, and consistently improve product quality.
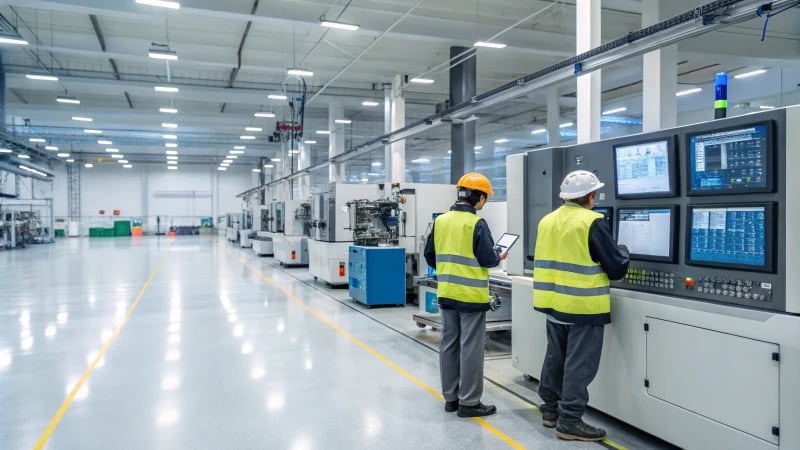
The Role of Automation
I remember the first time I saw a robotic arm in action at a mold factory. It was mesmerizing, watching it handle repetitive tasks with such precision and grace. These robotic systems12 aren’t just about replacing human effort; they’re about enhancing it. By taking over the mundane tasks, they free up skilled workers like me to focus on more complex and creative challenges. This shift doesn’t just speed up production and reduce errors—it transforms the entire workplace dynamic.
Table: Benefits of Automation in Injection Molding
Benefit | Description |
---|---|
Increased Efficiency | Speeds up production cycles with less downtime |
Enhanced Precision | Reduces defects and rework |
Labor Optimization | Frees workers for complex tasks |
Harnessing Real-Time Data Analytics
There was this one project where we hit a snag—machines weren’t performing as expected, and it was a scramble to figure out why. Enter real-time data analytics. By monitoring everything from energy usage to cycle times, we could pinpoint exactly where things were going awry. With real-time data13, we gained insights that helped us tweak processes on the fly, preventing defects before they even had a chance to occur. It’s like having a crystal ball that keeps our standards high and our operations smooth.
Table: Key Metrics in Data Analytics
Metric | Importance |
---|---|
Cycle Time | Identifies efficiency bottlenecks |
Energy Consumption | Optimizes energy usage |
Quality Control | Ensures consistency in product standards |
Advanced Quality Control Systems
I’ll never forget the relief of catching a potential defect early thanks to advanced quality control. Using technologies like infrared thermography14 and 3D scanning, we can assess products without destroying them, ensuring they meet every specification. This proactive approach not only reduces scrap rates but also boosts our confidence in the reliability of what we produce.
These technologies are a game-changer in lean practices, ensuring every resource is used wisely and that only top-notch products reach the market. By integrating these advancements, we not only cut costs and waste but also raise our product standards, aligning perfectly with lean manufacturing goals.
Automation reduces cycle times in injection molding.True
Automation enhances precision and reduces human error, speeding up production.
Real-time data analytics increases material waste.False
Real-time data helps optimize processes, preventing defects and reducing waste.
What Are Common Challenges in Adopting Lean Principles for Injection Molding?
Stepping into the world of lean principles for injection molding is like diving into a new adventure—exciting but with its own hurdles. Knowing what to expect can make the journey smoother and more rewarding.
Challenges in adopting lean principles for injection molding include employee resistance, lack of understanding, cultural barriers, and the complexity of adapting lean tools to suit specific needs.
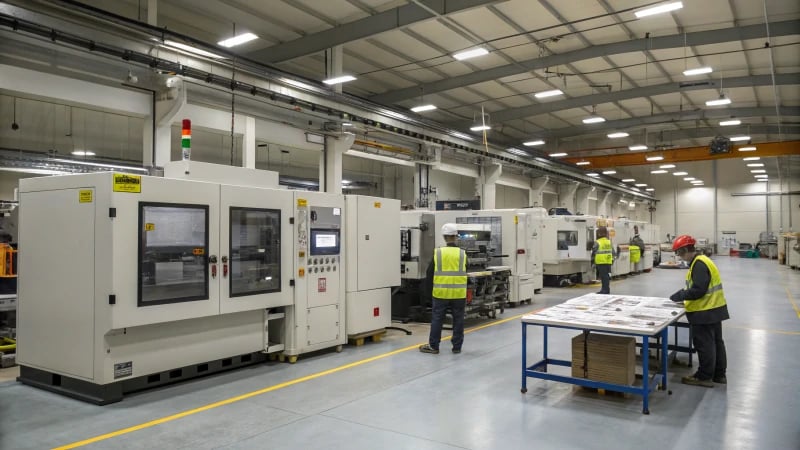
Resistance to Change
I remember when I first started implementing lean principles. The initial pushback was palpable; change can be daunting, especially when you’re used to a certain way of doing things. In our team, there was a genuine fear of job loss, and the pressure was tangible. It’s vital to approach this with empathy and understanding.
Addressing Resistance:
- Training & Education: We found that regular workshops and training sessions were invaluable in demystifying lean concepts and easing fears.
- Involvement: Engaging everyone in the transition process was key. It turned out that when team members felt involved, their buy-in increased, and resistance naturally waned.
Lack of Understanding
Lean methodologies like Kaizen or 5S were initially foreign concepts to many of us. Without a proper grasp, these tools can easily be misapplied, leading to inefficient operations. I learned this the hard way in my early days.
Solutions:
- Comprehensive Training: Investing in thorough lean training for all levels of staff is essential. This not only equips everyone with the necessary skills but also boosts confidence in applying these tools effectively.
- Expert Guidance: Bringing in a lean expert provided us with clarity and direction that I didn’t even realize we needed until we had it.
Adapting Lean Tools
The unique requirements of injection molding meant that standard lean tools needed some tweaking. For instance, Just-in-Time15 production often clashed with long lead times for mold changes, something that caught us by surprise initially.
Lean Tool | Challenge in Molding | Adaptation Strategy |
---|---|---|
5S | Tool storage complexity | Custom storage solutions |
Kanban | Variable demand | Flexible Kanban sizes |
Adaptation Tactics:
- Customize Tools: We had to modify lean tools to fit the unique aspects of injection molding, which turned out to be more flexible than I expected.
- Pilot Programs: Testing adapted tools on a small scale before full implementation helped us avoid potential pitfalls.
Cultural Barriers
Cultivating a lean culture involved overcoming existing cultural barriers. Shifting from hierarchical decision-making to a more collaborative approach was challenging yet rewarding. Leadership commitment was crucial.
Overcoming Barriers:
- Leadership by Example: Leaders modeling lean behaviors made a significant difference in how initiatives were received.
- Continuous Feedback: Establishing mechanisms for feedback allowed us to refine our practices continuously.
Adopting lean principles in injection molding isn’t easy, but it’s definitely worth it. With the right strategies, these challenges can be effectively managed, paving the way for enhanced efficiency and productivity.
Resistance to lean principles leads to fear of job loss.True
Employees fear job loss due to changes lean principles introduce.
Lean tools like 5S are always applicable in injection molding.False
Lean tools often need adaptation for specific injection molding needs.
How Do Continuous Improvement Strategies Impact Injection Molding Quality?
Ever wondered how some products just seem to have that flawless finish every time? It’s all about continuous improvement in the world of injection molding, where quality is king.
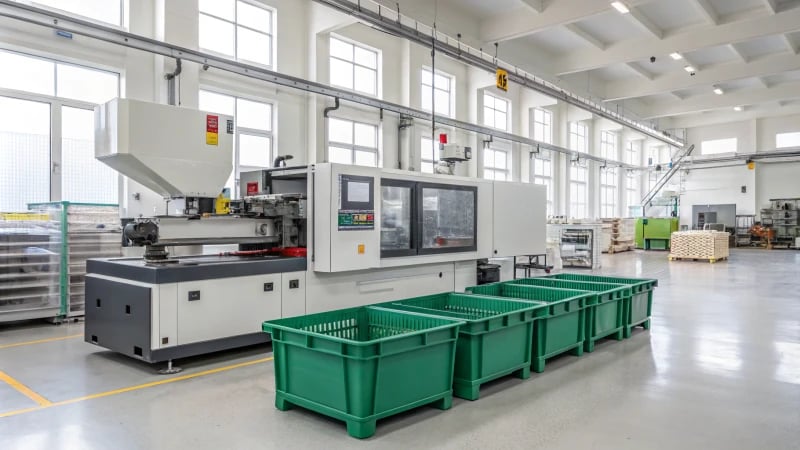
The Role of Lean Manufacturing in Injection Molding
Let me share a little story. I once worked on a project where we were constantly battling material shortages and excess. Then we embraced Lean manufacturing, and it felt like a light bulb moment. Suddenly, our processes were smoother, and the quality of our molds improved dramatically. Lean focuses on reducing waste and enhancing efficiency. We adopted just-in-time (JIT) inventory management, which cut down on material waste and ensured components were always at hand when needed.
Key Principles of Lean
- Value: Ever had a customer who knows exactly what they want? Defining value from their perspective is crucial.
- Flow: Imagine the seamless flow of a river—that’s how production should be.
- Pull: Picture your inventory like a stocked kitchen pantry; only take what you need.
- Perfection: The quest for perfection is endless, but the fewer defects and inefficiencies, the better.
These principles became our guiding light, helping us refine operations and consistently deliver top-quality products.
Six Sigma’s Influence on Quality Control
I remember the first time I dove into Six Sigma—it was like learning a new language, but the payoff was worth it. This data-driven approach pinpointed exactly where things were going wrong. With the DMAIC (Define, Measure, Analyze, Improve, Control) methodology, we systematically improved our processes.
Phase | Objective |
---|---|
Define | Identify the problem and project goals |
Measure | Quantify current process performance |
Analyze | Determine root causes of defects |
Improve | Implement solutions to enhance processes |
Control | Sustain improvements with ongoing monitoring |
The Impact of Continuous Improvement on Operational Efficiency
Continuous improvement isn’t just a buzzword—it’s a game-changer. We built a culture where everyone felt empowered to suggest improvements. That led to innovations in mold design and production techniques. Take advanced analytics tools; they’re our secret weapon for boosting operational efficiency16.
By refining processes continuously, we managed to slash cycle times and defect rates while cutting down production costs. This not only improved our injection-molded products but also made our customers happier by delivering reliable components.
Embracing Technology for Process Optimization
Technology was the cherry on top of our improvement strategies. Incorporating AI and machine learning felt like adding a superpower to predict defects before they even happened. Predictive maintenance tools kept our equipment running smoothly, minimizing downtime and enhancing process optimization17. Real-time adjustments became second nature, ensuring high-quality standards were maintained throughout the production cycle.
As technology evolves, its role in continuous improvement will only grow stronger, pushing the injection molding industry to set new standards for quality and efficiency.
Lean manufacturing reduces waste in injection molding.True
Lean techniques like JIT inventory management minimize material waste.
Six Sigma does not use statistical analysis for quality control.False
Six Sigma uses statistical analysis to identify and eliminate defects.
Conclusion
Applying lean manufacturing principles to injection molding enhances efficiency, reduces waste, and improves product quality through continuous improvement, employee involvement, and advanced technology integration.
-
Discover how focusing on customer-defined value enhances satisfaction and loyalty, pivotal for sustaining business success. ↩
-
Explore various techniques for optimizing processes and reducing waste, crucial for efficient production systems. ↩
-
Learn strategies for accelerating production while maintaining quality standards, key to operational efficiency. ↩
-
Understand how pull systems reduce inventory costs and improve responsiveness to customer demand. ↩
-
Find out how ongoing enhancements keep companies competitive in evolving markets. ↩
-
Explore how optimized mold design can minimize material waste, leading to significant cost reductions and efficiency improvements. ↩
-
Learn about efficient cooling system designs that can reduce cycle times and improve overall molding efficiency. ↩
-
Discover sustainable practices that align with waste reduction goals, enhancing both environmental and economic outcomes. ↩
-
Discover how engaging employees can enhance lean manufacturing by improving efficiency and productivity. ↩
-
Learn from real-world examples how employee motivation directly impacts productivity. ↩
-
Find frameworks that help build a strong culture of continuous improvement. ↩
-
Discover how robotic systems optimize injection molding by reducing cycle times and enhancing precision, leading to significant cost savings and increased productivity. ↩
-
Explore how real-time data analytics boosts manufacturing efficiency by providing actionable insights into operations, ensuring consistent quality and optimal resource use. ↩
-
Learn how advanced quality control technologies like infrared thermography ensure product reliability by providing real-time feedback for immediate corrective actions. ↩
-
Investigating JIT challenges can help tailor production strategies that align better with molding processes. ↩
-
Discover strategies for boosting operational efficiency within manufacturing processes. ↩
-
Understand how advanced technologies are utilized to optimize manufacturing processes. ↩