When embarking on a manufacturing journey, understanding the timeline for plastic injection molds can feel like a daunting task. Let’s unravel this together!
The lead-time for a plastic injection mold typically ranges from a few weeks to several months, depending on factors such as mold complexity, design requirements, and the manufacturer’s production capacity.
While this general timeline provides a starting point, understanding the specifics can significantly impact your planning and execution phases. Let’s dive deeper into how different elements shape these timelines.
Mold complexity significantly impacts lead-time.True
Complex molds require intricate design and manufacturing, extending timelines.
How Does Mold Complexity Affect Lead-Time?
Understanding the role of mold complexity is crucial in anticipating project timelines.
Mold complexity significantly impacts lead-time due to intricate designs requiring extended design and manufacturing processes.
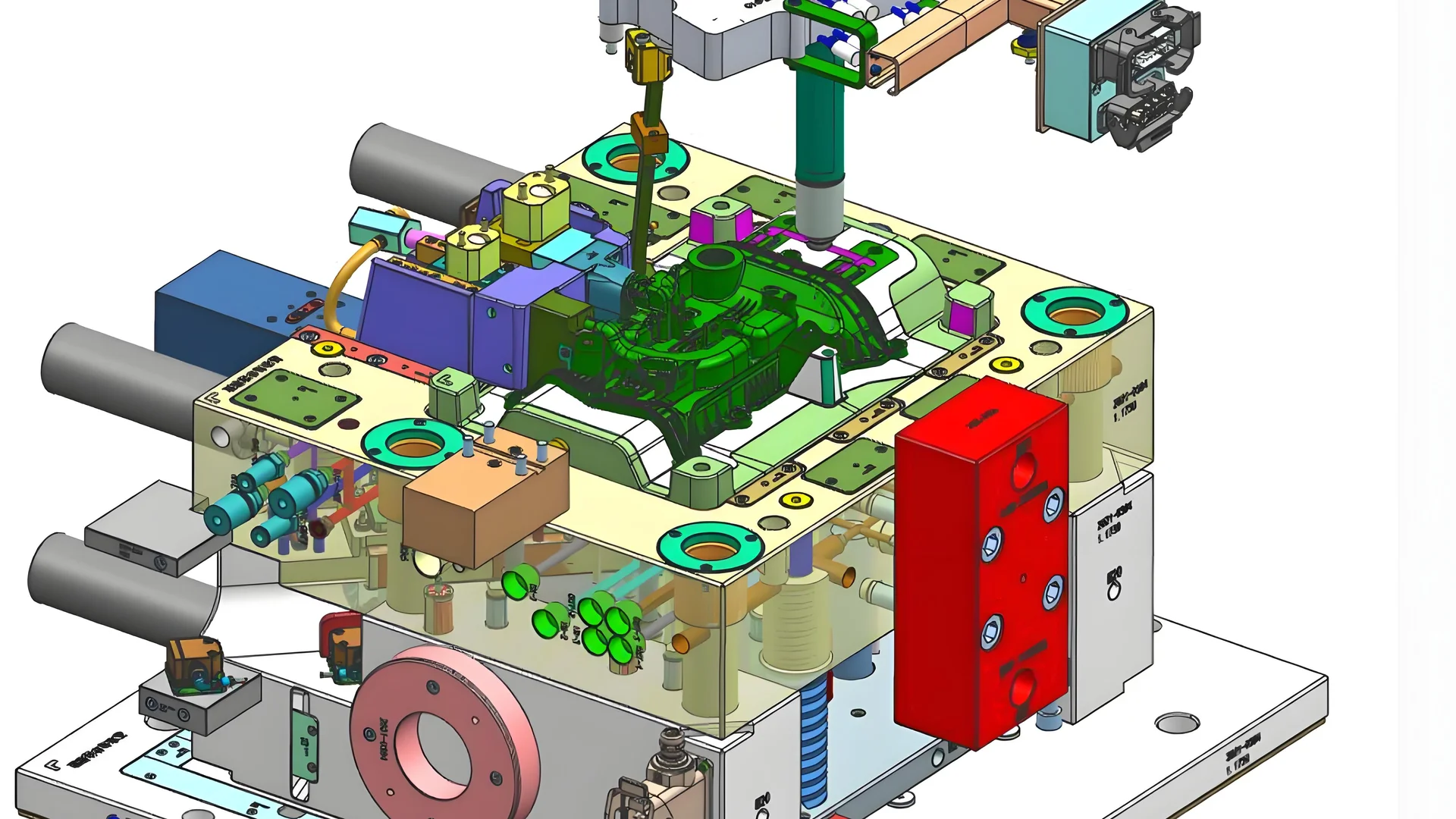
The Impact of Mold Complexity on Lead-Time
Mold complexity plays a pivotal role in determining the lead-time for plastic injection molds. Simple molds, characterized by straightforward designs and minimal intricacies, generally have shorter lead-times. These molds are easier to design and manufacture, often completed within weeks. For instance, molds for basic plastic items like bottle caps or simple containers typically have uncomplicated designs.
Conversely, complex molds require considerably more time. They often involve multiple moving parts, precise surface finishes, and integrated cooling systems. Such complexities necessitate detailed design processes and meticulous manufacturing techniques, thereby extending the lead-time significantly. Consider automotive parts molds as an example—they demand high precision and intricate features, making their preparation cycle extend to several months.
Design Requirements and Their Role
Design requirements directly influence mold complexity and thus the lead-time. Standard designs with minimal customization can be executed more rapidly, while unique specifications or advanced features prolong the process. Customization demands thorough planning and verification, often necessitating multiple simulations to ensure adherence to stringent standards.
Manufacturer’s Expertise and Production Capabilities
The expertise and capacity of the mold manufacturer also affect the lead-time. Experienced manufacturers with advanced equipment and skilled personnel are better equipped to handle complex mold designs efficiently. They utilize advanced process flows1 that significantly reduce lead-times compared to smaller or less experienced manufacturers who might struggle with intricate requirements.
Material Availability and Its Effects
Availability of materials can further complicate the timeline. If specialized materials are required and are not readily available, procurement delays can occur. This scenario is common when specific high-strength or corrosion-resistant materials are needed, which might only be sourced from select suppliers, leading to extended lead-times.
Factors Affecting Lead-Time | Impact Level |
---|---|
Mold Complexity | High |
Design Requirements | Moderate |
Manufacturer Expertise | High |
Material Availability | Moderate |
Understanding these factors helps in anticipating potential delays and planning accordingly to mitigate their impact on project timelines. Therefore, effective communication2 between all parties involved is crucial for aligning expectations and ensuring smooth execution.
Complex molds increase lead-time significantly.True
Complex molds involve intricate designs and manufacturing, extending lead-time.
Simple mold designs require months to complete.False
Simple molds are often completed within weeks due to straightforward designs.
What Are Common Design Challenges in Mold Fabrication?
Designing molds is a complex task that poses numerous challenges for manufacturers.
Common design challenges in mold fabrication include achieving precision in complex designs, meeting specific material requirements, and ensuring efficient cooling and ejection systems.
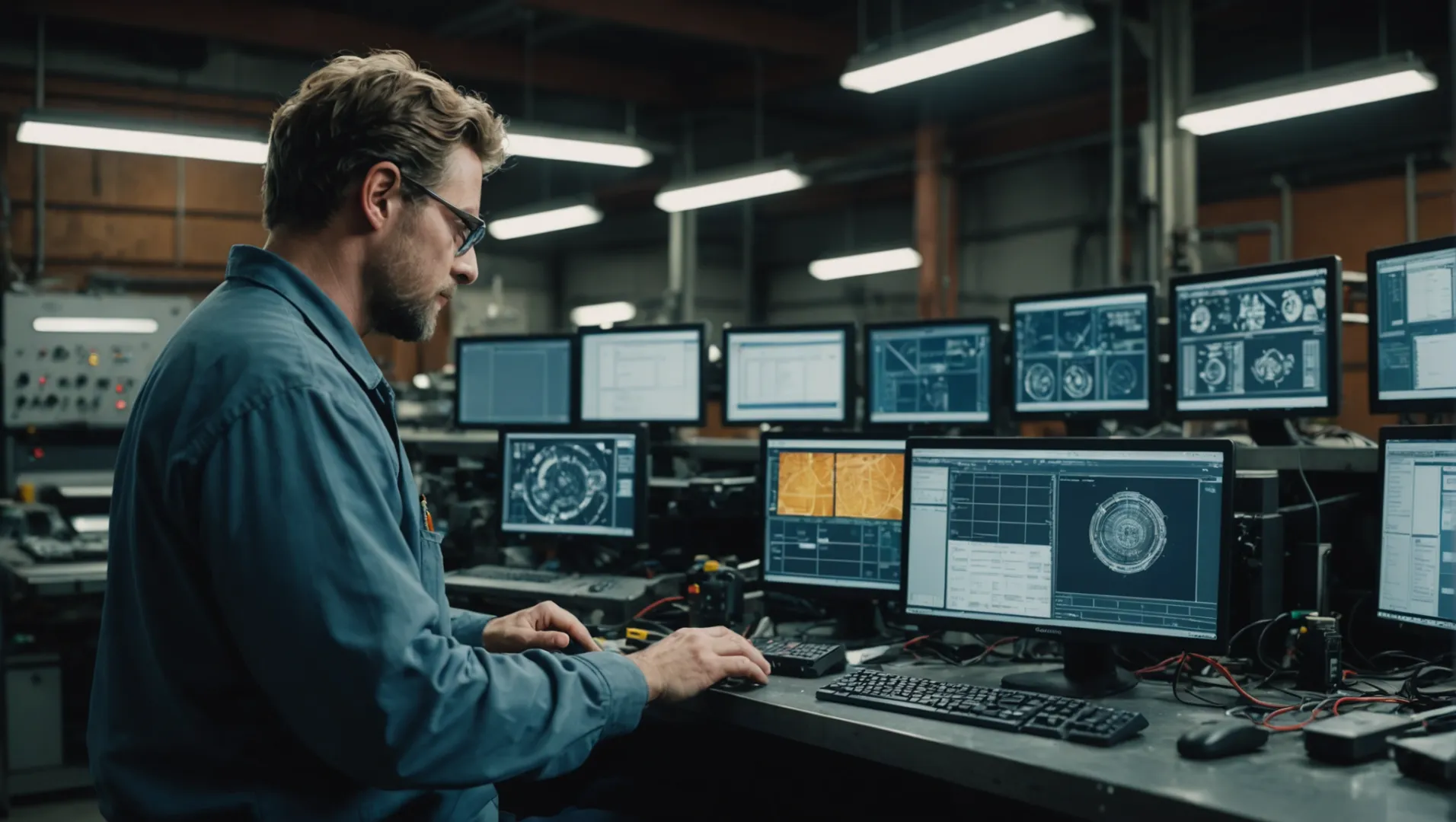
Precision in Complex Designs
One of the foremost challenges in mold fabrication is achieving high precision, especially when dealing with complex designs. These designs often involve intricate geometries or tight tolerances that demand meticulous planning and execution. For instance, molds used in automotive parts require a high level of precision due to their complex structures and performance demands.
Precision not only ensures the final product meets the required specifications but also minimizes waste and reduces the need for post-production adjustments. Utilizing advanced design software3 and simulation tools can aid in visualizing potential issues early in the design phase, allowing for necessary adjustments before actual production begins.
Material Specifications and Availability
Selecting the right materials that meet specific project requirements while being readily available can be daunting. Some projects may require specialized materials like high-strength or corrosion-resistant steels, which can sometimes be scarce or costly. This challenge is compounded by the fact that material choice directly impacts the mold’s durability, performance, and production efficiency.
To mitigate this issue, manufacturers often collaborate closely with suppliers to ensure timely procurement and may need to adjust design specifications to accommodate available materials. This partnership is crucial in avoiding delays and ensuring that the molds meet all necessary standards.
Cooling and Ejection System Efficiency
Another significant challenge is designing effective cooling and ejection systems. Efficient cooling systems are vital for maintaining cycle times and ensuring the quality of the molded product. Poorly designed systems can lead to longer cooling times, increased cycle times, and defects in the final product.
Additionally, the ejection system must be designed to remove the molded part without causing damage or deformation. This often involves carefully planning the placement of ejector pins and considering the use of advanced ejection technologies4 to enhance efficiency.
Integration of Advanced Technologies
Integrating new technologies like CAD/CAM/CAE software and automation into the mold fabrication process presents both opportunities and challenges. While these technologies can greatly enhance precision and efficiency, they require significant investment and expertise to implement effectively.
Manufacturers must balance the cost of adopting these technologies with the potential benefits they bring in terms of reduced lead times, improved product quality, and greater flexibility in design. Exploring case studies5 of successful technology integration can provide valuable insights into best practices and potential pitfalls.
Precision is crucial in mold fabrication.True
High precision ensures product meets specifications and reduces waste.
Material choice doesn't affect mold performance.False
Material impacts durability, performance, and efficiency of molds.
How Do Manufacturer Capabilities Influence Mold Timelines?
Manufacturer capabilities play a pivotal role in determining how quickly a mold can be prepared.
Manufacturer capabilities, including experience, production capacity, and technology, significantly impact mold timelines. Efficient manufacturers with advanced equipment and skilled teams can drastically shorten preparation cycles.
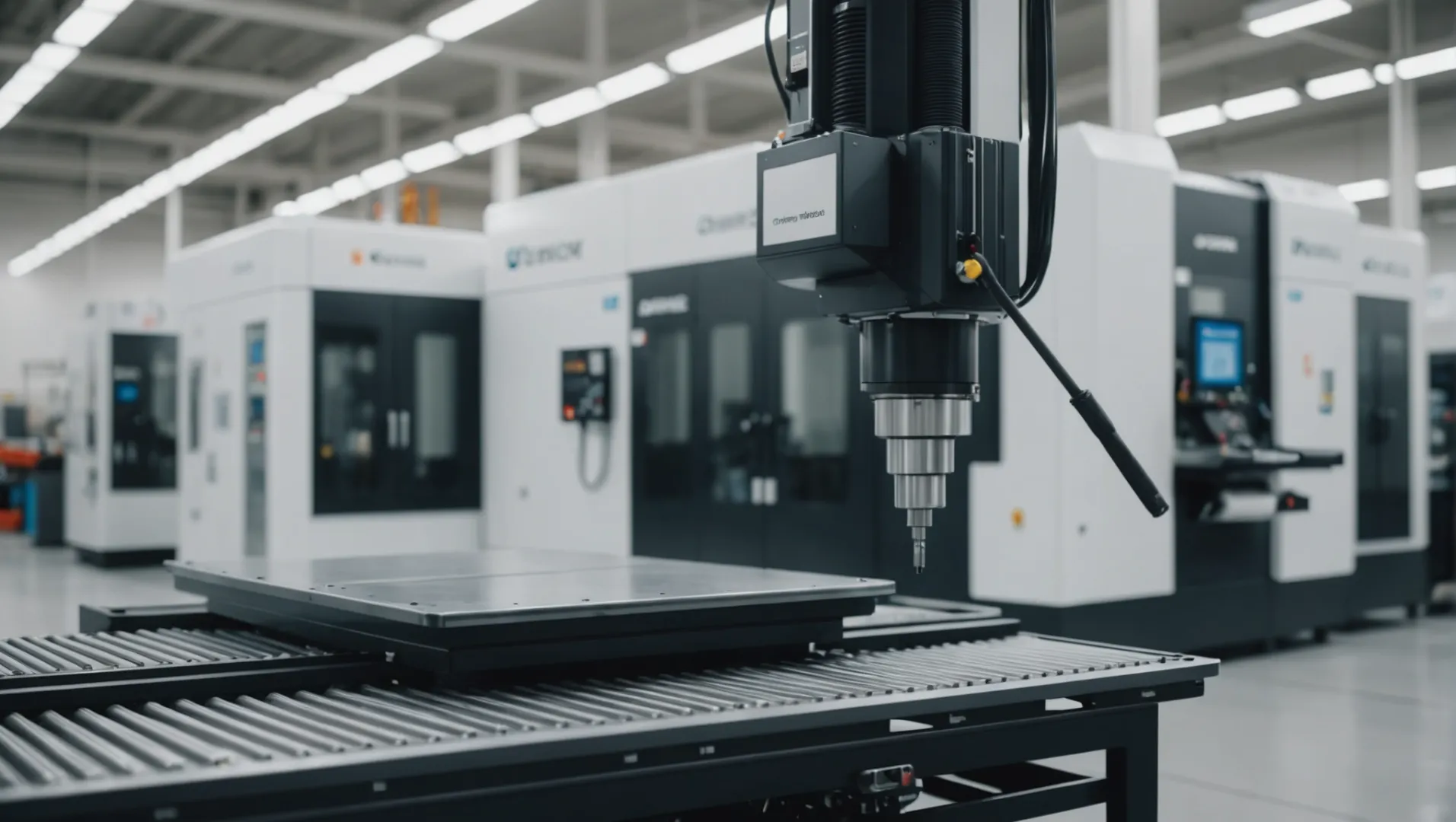
Experience and Expertise Matter
Experienced manufacturers often have streamlined processes and a wealth of knowledge that can be invaluable in expediting mold preparation. These companies have likely encountered a variety of design challenges over the years and developed effective solutions. For instance, a manufacturer with a history of producing complex automotive molds will be adept at handling intricate designs and tight tolerances, thereby reducing potential delays.
Production Capacity and Efficiency
The production capacity of a manufacturer directly correlates with their ability to handle large volumes or complex projects. Companies equipped with state-of-the-art machinery and efficient workflow systems can process orders more swiftly. For example, utilizing high-speed machining centers can enhance precision while cutting down processing times.
A table illustrating the impact of different capacities might look like this:
Production Capacity | Impact on Timeline |
---|---|
Low | Extended timelines due to bottlenecks |
Medium | Moderate timelines with occasional delays |
High | Shorter timelines with streamlined processes |
Technology and Innovation
Adoption of advanced technologies such as CAD/CAM systems and simulation software enables manufacturers to preemptively solve design issues. Using advanced technology6 not only aids in reducing errors but also minimizes the need for costly redesigns, thereby saving time.
Technical Workforce
The expertise and skill level of the technical team play a crucial role in influencing timelines. A skilled workforce can manage unexpected challenges effectively, ensuring that projects remain on schedule. Additionally, training programs that keep the team updated on the latest industry trends and technologies can also enhance overall efficiency.
Supply Chain Management
Efficient manufacturers maintain strong relationships with suppliers to ensure the timely availability of materials. This is particularly crucial when special materials are required for mold production. Delays in material procurement can significantly affect the preparation cycle, so proactive supply chain strategies are essential to minimize disruptions.
By focusing on these key areas, manufacturers can not only meet but often exceed client expectations regarding mold preparation timelines.
Experience reduces mold preparation delays.True
Experienced manufacturers streamline processes, reducing potential delays.
Low production capacity shortens mold timelines.False
Low capacity extends timelines due to bottlenecks and inefficiencies.
What Strategies Can Shorten Mold Preparation Cycles?
In the fast-paced world of manufacturing, reducing mold preparation time is crucial for meeting tight deadlines and maintaining competitive advantage.
To shorten mold preparation cycles, consider advance planning, optimizing the design process, improving production efficiency, and ensuring timely material supply.
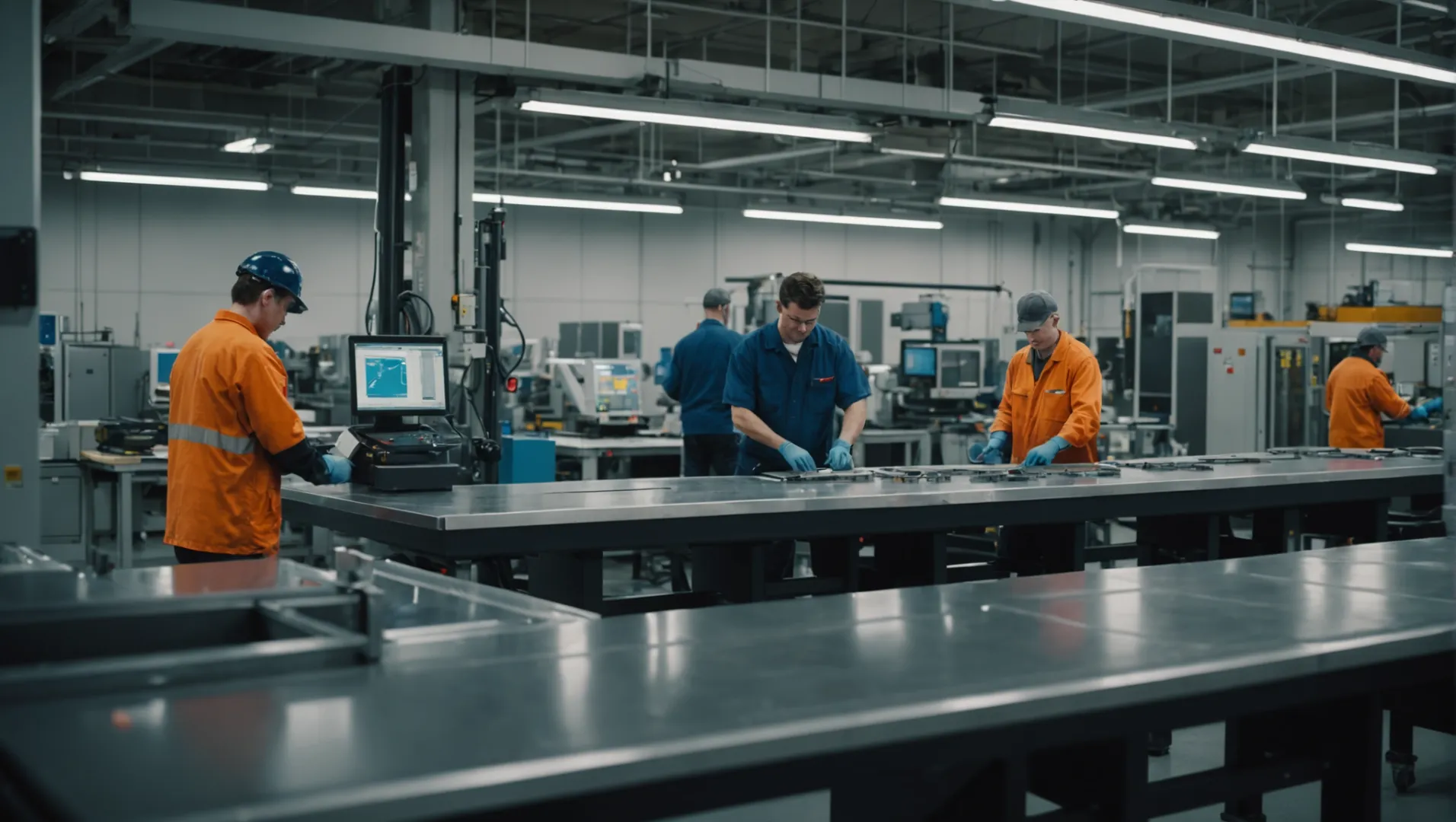
Advance Planning and Communication
Effective communication with mold manufacturers at the start of a project is key. By clearly conveying design requirements and expected delivery timelines, manufacturers can pre-plan essential tasks such as material procurement and equipment setup.
For instance, if a customer promptly provides detailed product specifications to the manufacturer, it allows for early preparation in mold design7 phases, cutting down subsequent production time.
Optimize the Design Process
Leveraging advanced design tools like CAD/CAM/CAE can streamline the design phase. These technologies enhance precision, minimize errors, and reduce the number of revisions needed.
Using simulation software to anticipate potential issues in the injection molding process8 can prevent costly modifications later. This proactive approach not only saves time but also improves mold quality.
Improve Production Efficiency
Manufacturers can significantly cut down mold preparation times by refining production schedules, optimizing machining processes, and enhancing equipment usage.
Incorporating high-speed machining centers boosts processing speed and accuracy. Additionally, employing parallel processing techniques allows multiple operations to occur simultaneously, thus accelerating the overall manufacturing timeline.
Ensuring Timely Material Supply
Having a robust supply chain ensures that all necessary materials are available when needed. This requires forging strong relationships with suppliers to secure timely delivery of specialized or scarce materials.
For example, securing contracts with specific steel suppliers9 ensures that high-strength, corrosion-resistant materials are ready for use without delay, thus preventing hold-ups in the production schedule.
Advance planning reduces mold preparation time.True
Early communication with manufacturers allows for efficient task pre-planning.
Simulation software increases mold preparation time.False
Simulation software identifies issues early, reducing revisions and saving time.
Conclusion
Effective planning and understanding of the factors influencing mold preparation can optimize production timelines. Embrace advanced tools and collaborate with experienced manufacturers for success.
-
Discover how advanced techniques speed up complex mold production.: The F-PAIM process can be divided into two types: the short-shot method and the overflow method. These methods differ depending on whether the mold cavity is … ↩
-
Learn why clear communication is vital for managing mold timelines.: For any plastic part manufacturing business, or for any other industry for that matter, communication plays a key role to success. ↩
-
Discover top software solutions enhancing mold design precision.: Which software is best for automated Mold Design? I’m beginner to injection mold designs. I have already tried Inventor and other AutoDesk … ↩
-
Learn about innovative ejection solutions improving mold efficiency.: Laser Welder Yields Fast, Precise Mold Repair. Intralox’s integration of the Alpha Laser ALFlak has significantly improved their tool room efficiency when it … ↩
-
Gain insights from successful technology adoption in mold making.: MoldMaking Technology publishes monthly case studies that offer detailed insights into the real-world application of various technologies … ↩
-
Explore CAD/CAM benefits in streamlining design and production processes.: Modular CAD/CAM software allows different software functionalities to be available independently of one another. ↩
-
Discover more about impactful mold design strategies.: A few key mold design strategies can go a long way in improving your mold building operations and customer support. ↩
-
Learn how simulation software aids injection molding processes.: Moldex3D is the world leading CAE product for the plastic injection molding industry. With the best-in-class analysis technology, Moldex3D can help you carry … ↩
-
Find reliable suppliers for high-quality mold-making steel.: DME has served mold makers worldwide for over seven decades, and we’re still your best choice for precision machined steel plates, mold base steel and custom … ↩