Micro-injection molding technology is revolutionizing manufacturing, and I’m excited to share its latest advancements with you!
Micro-injection molding technology has seen remarkable breakthroughs with the introduction of ultrasonic and laser machines that enhance efficiency and precision. These innovations are not just technical feats; they have real-world implications across industries like medical devices, electronics, automotive, and aerospace.
But what does this all mean for us? Understanding how these innovations translate into practical applications can profoundly influence industry practices. Let’s explore the transformative impacts of these technologies together!
Ultrasonic micro molding reduces energy use by 90%.True
Ultrasonic machines convert sound waves into heat, cutting energy use significantly.
How Do Ultrasonic and Laser Micro Injection Molding Machines Work?
The latest in micro-injection molding, ultrasonic and laser technologies redefine precision and efficiency in manufacturing.
Ultrasonic and laser micro injection molding machines offer enhanced precision and reduced energy consumption. Ultrasonic machines convert sound waves into heat to melt plastics, while laser machines use concentrated light for the same purpose, pushing the molten material into molds with a plunger.
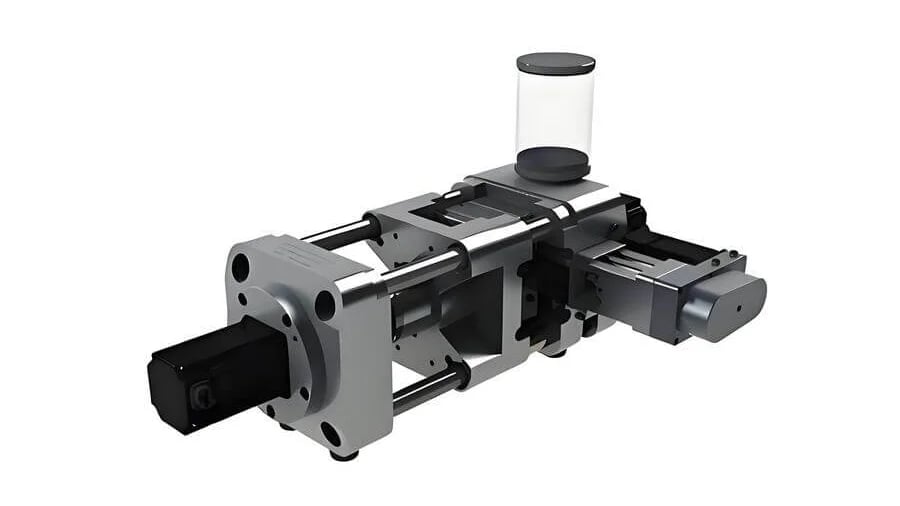
The Mechanism Behind Ultrasonic Micro Injection Molding
Ultrasonic micro injection molding machines operate by converting ultrasonic energy into heat. This process involves high-frequency sound waves that generate frictional heat, melting plastic particles without the need for traditional screws and heaters. This technique allows for lower injection pressure and eliminates material retention time, reducing degradation and boosting production efficiency.
The absence of screws also means that the energy consumption is significantly minimized, with reductions up to 90% compared to conventional methods. This not only makes ultrasonic technology a sustainable choice but also ensures high molding precision1, which is crucial for producing tiny components such as micro gears and MEMS devices.
Understanding Laser Micro Injection Molding
In contrast, laser micro injection molding machines utilize laser beams as the energy source for plasticization. The laser precisely heats and melts the plastic, which is then pushed into the mold cavity by a plunger device. This method excels in applications requiring high molding precision and specific material properties, making it suitable for sectors like medical devices and electronics.
Laser molding offers advantages in rapid prototyping2 due to its ability to provide precise control over the melting and molding stages. It allows for customization in terms of material properties, which can be critical for specialized applications.
Technological Advances and Their Impact
Both ultrasonic and laser technologies benefit from recent advancements such as higher injection speeds and improved metering accuracy. A key development is the introduction of a variable mold temperature control system, which ensures optimal mold conditions at different stages of the injection process.
For example, during the filling phase, maintaining a higher mold temperature prevents premature solidification, ensuring the melt’s fluidity. Conversely, rapid cooling during the final stages reduces cycle time and enhances overall efficiency. The inclusion of a vacuum exhaust system further aids in maintaining product quality by effectively removing gases that could lead to defects such as cavitation.
With these innovative features, ultrasonic and laser micro injection molding machines are revolutionizing manufacturing3 across various fields, paving the way for new applications and improved production methodologies.
Ultrasonic molding uses sound waves for heating.True
Sound waves generate frictional heat to melt plastics, avoiding traditional heaters.
Laser molding requires traditional screws and heaters.False
Laser molding uses concentrated light to melt plastics, eliminating screws and heaters.
What Are the Key Benefits of High-Speed Injection Molding?
High-speed injection molding is revolutionizing precision manufacturing with its rapid, efficient production capabilities.
High-speed injection molding enhances productivity by reducing cycle times and minimizing product defects. It ensures consistent quality through precise control of injection parameters, benefiting industries like automotive and electronics with faster, more reliable production of complex parts.
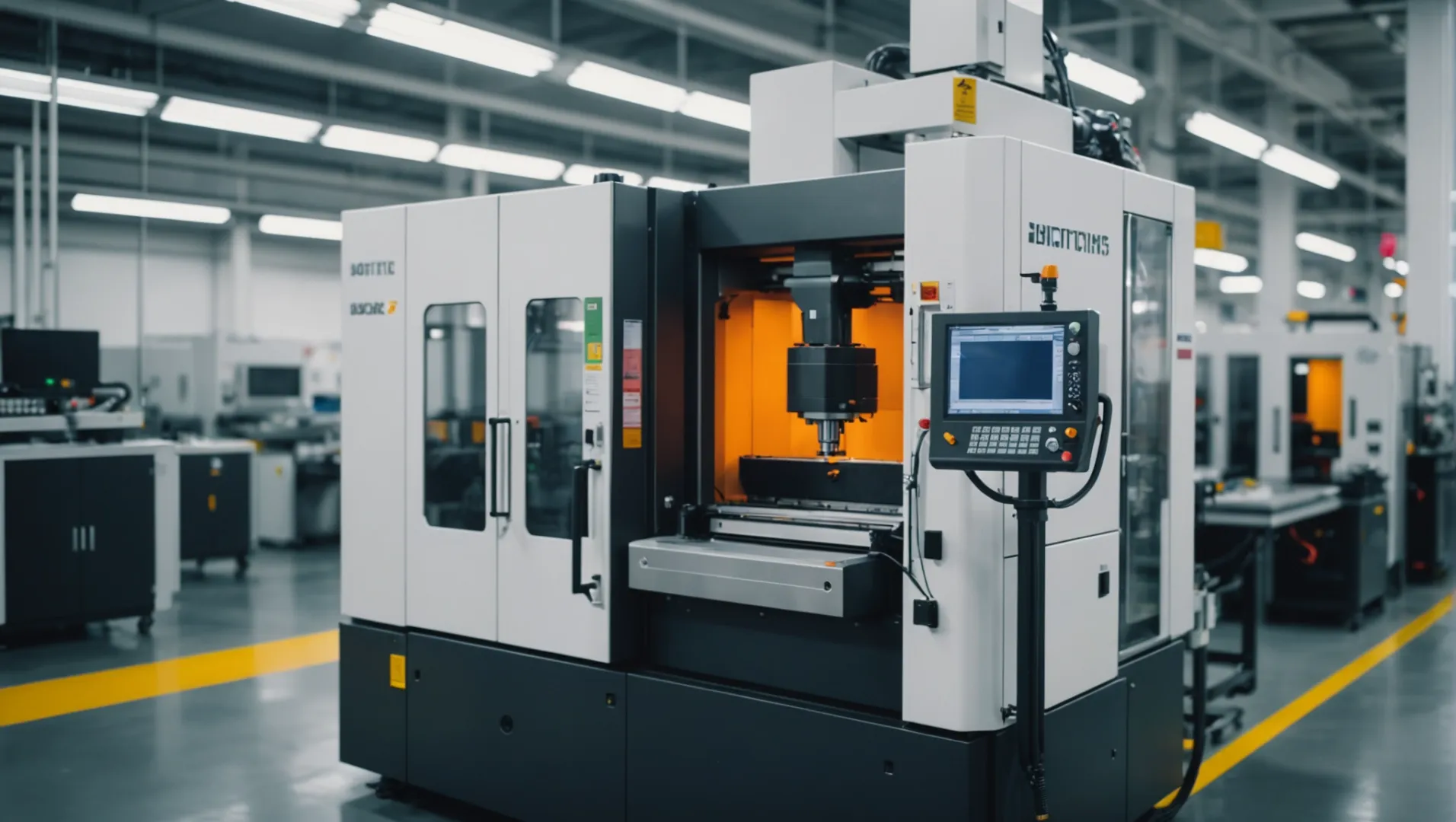
Boosting Production Efficiency
High-speed injection molding significantly reduces cycle times, which directly impacts production efficiency. By rapidly injecting the plastic melt into molds, manufacturers can increase output without compromising quality. This speed is particularly beneficial in industries requiring mass production of small parts, such as the automotive sector4, where components like micro sensors and actuators are produced in large quantities.
Ensuring Product Quality
The ability to maintain high injection speeds without sacrificing accuracy is crucial for minimizing defects. With precise control over parameters like injection speed and pressure, high-speed injection molding achieves consistent quality. This is especially important in the electronics industry5, where the precision of microchip packaging and connectors affects device performance.
Enhancing Material Efficiency
High-speed injection molding also contributes to material efficiency by reducing waste. Faster cycle times mean less material degradation, leading to fewer defects and rejections. This benefit extends to sectors like the medical field6, where the precise molding of medical devices such as micro catheters and drug delivery systems is critical for patient safety and effectiveness.
Supporting Complex Geometries
The technology supports the creation of complex geometries that would be challenging or impossible with traditional methods. High-speed machines can fill intricate mold designs quickly, ensuring full material distribution even in micro-sized cavities. This capability is vital in the aerospace industry7, where lightweight, complex parts like micro antennas and valves are essential for performance.
Table: Key Benefits of High-Speed Injection Molding
Benefit | Description |
---|---|
Increased Production Speed | Faster cycle times lead to higher output. |
Consistent Product Quality | Precise control reduces defects and maintains quality standards. |
Material Efficiency | Reduced material degradation and waste. |
Complex Geometry Molding | Ability to fill intricate molds for sophisticated part designs. |
High-speed injection molding reduces cycle times by 50%.True
It significantly cuts cycle times, boosting production efficiency.
High-speed injection molding increases material waste.False
It reduces waste by minimizing material degradation and defects.
How Is Micro-Injection Molding Transforming the Medical Device Industry?
Micro-injection molding is revolutionizing medical device manufacturing with its precision and efficiency.
Micro-injection molding is pivotal in creating intricate medical devices such as micro catheters, needles, and drug delivery systems. It allows for the production of components with exceptional precision, essential for minimally invasive procedures and innovative drug therapies.
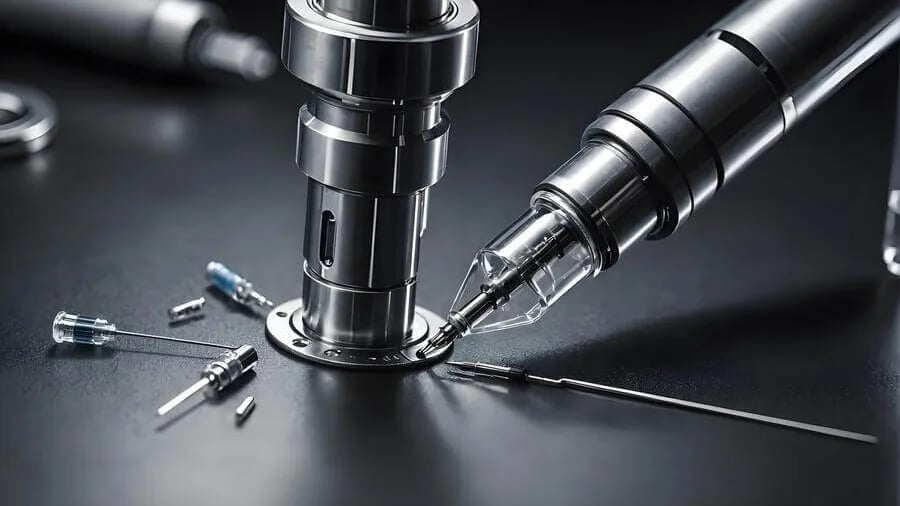
Revolutionizing Medical Device Manufacturing
Micro-injection molding technology is at the heart of a transformative shift in medical device production. By enabling the creation of complex, miniaturized components, it meets the demands of modern healthcare, where precision and biocompatibility are paramount.
Advancements in Device Precision and Functionality
The capability to produce highly intricate parts with micro-injection molding has opened new avenues in medical device design. For example, micro catheters and micro needles benefit from this technology, which allows for components with precise geometries and smooth finishes, crucial for minimally invasive procedures8. These advancements help reduce patient trauma and recovery time.
Additionally, the development of devices like vascular stents and pacemaker shells relies heavily on the precision afforded by micro-injection molding. These components must meet stringent standards for durability and performance under challenging physiological conditions.
Enhancing Drug Delivery Systems
Micro-injection molding also plays a significant role in advancing drug delivery mechanisms. The technology allows for the production of micro capsules and sustained-release devices that can precisely control drug dosage and release rates. This precise control improves therapeutic outcomes while minimizing side effects, a crucial factor in patient-centric care.
For instance, micro drug capsules designed through this process can be engineered to degrade at specific rates within the body, providing consistent drug delivery9 over extended periods. This capability is especially beneficial in chronic disease management, where maintaining steady drug levels is critical.
Supporting Innovation in Biocompatible Materials
The compatibility of materials used in micro-injection molding is another critical aspect of its transformative impact on medical devices. Innovations in mold materials and processing techniques ensure that components not only meet physical specifications but are also safe for human use. This is vital for implantable devices that must interact safely with body tissues.
New processing methods, such as micro-cutting and laser processing, enhance the quality and functionality of these molds, ensuring that they can produce components with high strength and wear resistance.
Conclusion
As we delve deeper into the capabilities of micro-injection molding, it’s clear that its influence extends beyond mere manufacturing. This technology is reshaping the possibilities for medical innovation, driving forward new standards in patient care and treatment efficacy. With continuous advancements, its potential to further transform the medical landscape remains immense.
Micro-injection molding improves drug delivery precision.True
It allows precise control of dosage and release rates.
Micro-injection molding is unrelated to minimally invasive devices.False
It produces intricate parts crucial for such procedures.
What Role Does Micro-Injection Molding Play in Automotive Innovation?
Micro-injection molding is revolutionizing the automotive industry by enabling the production of lightweight, high-precision components.
Micro-injection molding plays a critical role in automotive innovation by producing miniaturized components like sensors and micromotors, which enhance vehicle performance and fuel efficiency.
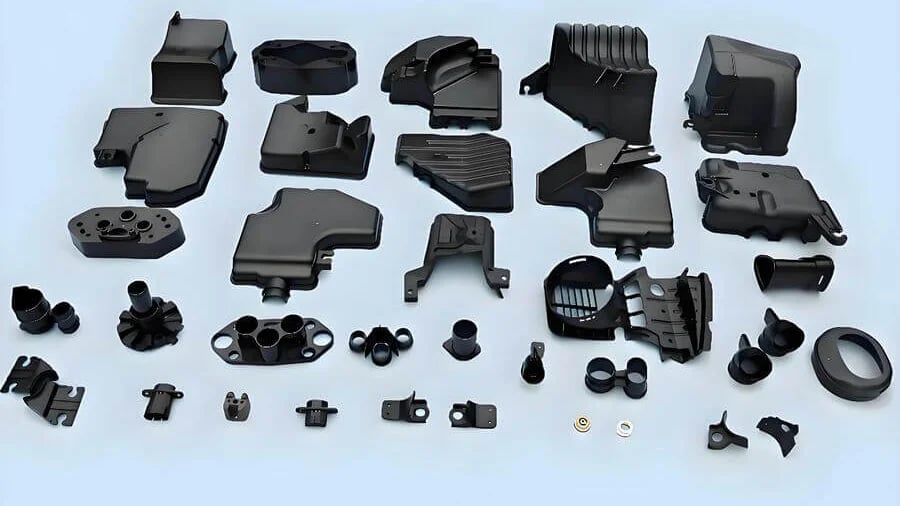
Advancements in Automotive Components
Micro-injection molding is pivotal in creating intricate automotive components that require high precision and miniaturization. This technology allows for the efficient production of parts such as sensors, micromotors, and micro buckles, which are integral to modern vehicle designs. These components not only reduce the overall weight of vehicles but also improve fuel economy and performance.
Fuel Efficiency Enhancements
By enabling the creation of smaller and lighter parts, micro-injection molding helps in minimizing the weight of cars, directly impacting their fuel efficiency. For instance, miniaturized fuel injectors10 can precisely manage fuel flow, optimizing engine performance and reducing fuel consumption.
Innovations in Interior Design
The ability to produce intricate micro buckles and decorative parts enhances the aesthetic appeal of vehicle interiors while maintaining functionality. These components often require high precision to ensure a perfect fit and finish, which micro-injection molding can deliver.
Role in New Energy Vehicles
In the realm of new energy vehicles, micro-injection molding is instrumental in manufacturing components like battery shells and electrode brackets. These parts are crucial for enhancing battery safety and performance, addressing one of the primary challenges in electric vehicle (EV) development.
Improving Battery Technology
Micro-injection molding allows for the creation of battery shells that provide excellent protection for internal components, ensuring durability and longevity. Similarly, precision-molded electrode brackets support better conductivity and stability within battery systems.
Technological Breakthroughs Supporting Automotive Innovation
The latest advancements in micro-injection molding technology, including ultrasonic and laser machines, are particularly beneficial for the automotive industry. These machines offer high precision and speed, essential for producing complex automotive components efficiently.
- Ultrasonic Micro Injection Molding: Reduces energy consumption by up to 90% while maintaining high molding precision.
- Laser Micro Injection Molding: Ideal for parts with stringent requirements regarding precision and material properties.
These technological innovations support the growing demand for compact, reliable automotive parts that cater to next-generation vehicle technologies like autonomous driving and connectivity.
Micro-injection molding improves fuel efficiency.True
It produces lighter components, reducing vehicle weight and fuel use.
Micro-injection molding is not used in EV battery parts.False
It's crucial for making battery shells and electrode brackets in EVs.
Conclusion
Micro-injection molding is not just a technological marvel; it’s paving the way for incredible innovations across various fields. Embracing these advancements could redefine your approach to manufacturing.
-
Explore why ultrasonic technology enhances precision in micro manufacturing.: One of the advantages of processing micro-parts by ultrasonic compression molding is the cost and simplicity of the tooling and associated … ↩
-
Learn how laser technology improves molding precision and customization.: It enables manufacturers to meet the demands for small, exact components while ensuring scalability for high-volume production. In this … ↩
-
Understand how these technologies are transforming manufacturing processes.: This study explores the interfacial friction in ultrasonic micro-injection moulding by using different polymer feedstock shapes. ↩
-
Explore how high-speed molding benefits automotive parts production.: forteq is a leading specialist in high-precision injection molding. We offer customers the same high quality regardless of the molded part’s complexity. ↩
-
Discover its impact on precision and reliability in electronics.: Electronics injection molding involves converting raw plastic material – in pellet or granular form – into molded electronic parts. ↩
-
Learn about its role in producing safe, effective medical products.: Fortify’s medical device injection molding services can mold medical device components in high-quality, medical-grade plastics, so you can mold parts in end- … ↩
-
Understand its significance in creating lightweight, complex aerospace components.: Top-end performance and adhering to exacting standards are vital in aerospace injection molding. Ensinger Precision Components delivers on both. ↩
-
Explore how these procedures reduce recovery time and patient trauma.: 7 Benefits of Minimally Invasive Surgery · 1. Many Procedures are Available · 2. Smaller Incisions · 3. Less Scarring · 4. Increased Accuracy, Decreased Risk of … ↩
-
Learn how controlled release improves therapeutic outcomes.: The drug delivery system enables the release of the active pharmaceutical ingredient to achieve a desired therapeutic response. Conventional drug delivery … ↩
-
Discover how micro-injection molding optimizes fuel injector efficiency.: 3. Automotive. Micro injection molding is also used in the production of automotive components such as fuel injectors, airbags, and sensors. The process allows … ↩