Do you ever wonder about the creation of everyday plastic items? This is an intriguing process called injection molding. It transforms raw materials into the items people use every day.
The injection molding process starts with preparing raw materials. Next, workers install and preheat the mold. Injection of the material into the mold follows. Then, pressure holds the material in place. Cooling and solidification occur shortly after. Finally, the piece is removed from the mold. Every step is important. Each step really impacts the quality of the plastic parts.
I think back to my time in the manufacturing world and recall the first moment I saw an injection molding machine working. The precision and speed truly amazed me! This process involves more than just machines. It includes creativity and craftsmanship. Every step is important, from choosing the right materials to cooling and removing the mold. Each step really matters for quality. I discovered that knowing these steps avoids common mistakes. It also improves product design. This understanding makes the whole experience more rewarding.
Injection molding transforms raw materials into products.True
This claim is true as injection molding converts plastic pellets into usable items through a specific process.
Cooling is the final step in the injection molding process.True
This claim is true; cooling solidifies the injected material before demolding.
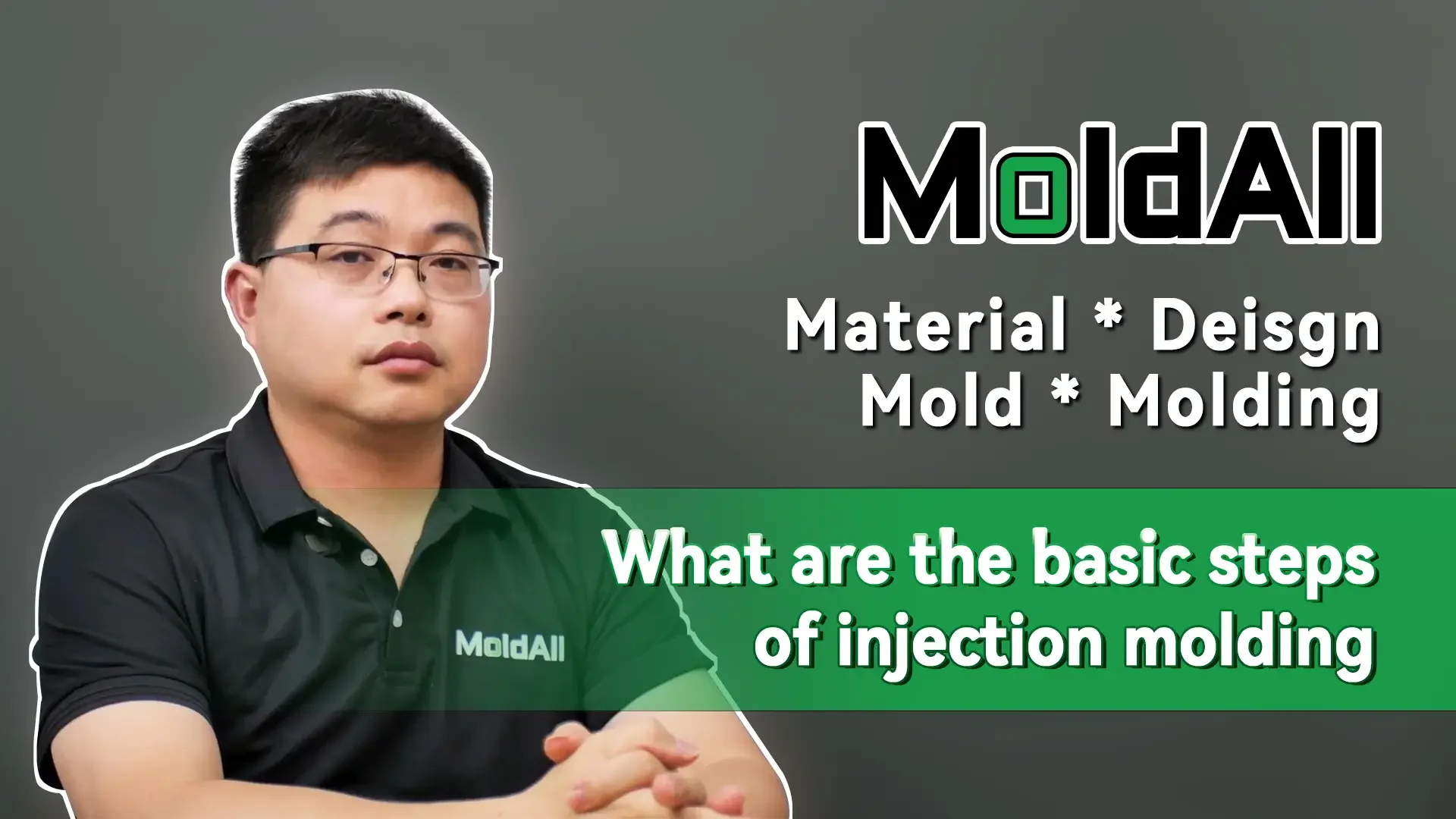
- 1. What Materials Are Best for Injection Molding?
- 2. How Does Mold Design Affect Product Quality?
- 3. What Are Common Defects in Injection Molding and How Can I Avoid Them?
- 4. How Can I Optimize the Injection Molding Process for Efficiency?
- 5. Understanding the Injection Molding Process
- 6. Conclusion
What Materials Are Best for Injection Molding?
When I first started learning about injection molding, selecting the correct materials felt confusing. Many options exist. Understanding the importance of choosing the right material is vital. It can determine the success of my projects. Let’s explore this topic together!
When thinking about injection molding materials, polypropylene (PP), polyethylene (PE), polystyrene (PS) and polycarbonate (PC) are very noteworthy. These materials have specific properties like durability and heat resistance. Picking the right material is important for good performance. Production efficiency also depends on choosing correctly.
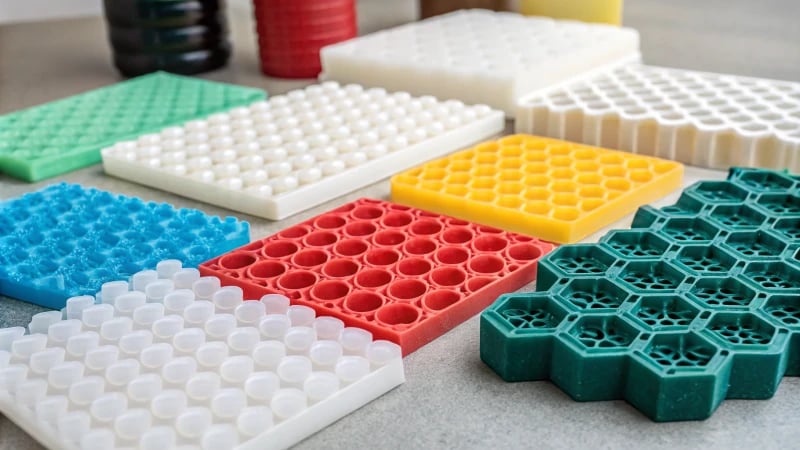
Understanding Injection Molding Materials
Choosing the right material for injection molding is sometimes very challenging. In the beginning, I looked at many options and tried to find the best one for my product. The material you choose impacts your product’s performance. It also affects the whole production process.
Common Thermoplastics in Injection Molding
Out of all the materials, thermoplastics are my regular choice. Here’s a brief overview of some popular choices:
Material | Properties | Applications |
---|---|---|
Polypropylene (PP) | Lightweight, chemical resistant | Packaging, automotive parts |
Polyethylene (PE) | Durable, flexible, moisture resistant | Toys, containers |
Polystyrene (PS) | Rigid, good insulation | Disposable cutlery, packaging |
Polycarbonate (PC) | High impact resistance, clear | Safety glasses, electronic housings |
Factors to Consider When Choosing Materials
During material selection, I think about several important factors:
- Mechanical Properties: These include strength, flexibility and impact resistance. Different uses need different mechanical properties. I once worked on a project for consumer electronics that needed strong materials.
- Thermal Properties: Heat resistance is crucial for products exposed to high temperatures. I find nylon very reliable because it handles heat well.
- Chemical Resistance: For products that face harsh chemicals, a material with good chemical resistance is necessary. Polypropylene is my frequent choice due to its great durability.
Performance Attributes of Thermoplastics
Performance attributes guide my final decisions:
- Durability: Polycarbonate is used by me for products needing strong durability. It’s perfect for long-lasting items.
- Heat Resistance: Nylon and PPS have been very useful for high-heat projects.
- Cost Effectiveness: Although polycarbonate is expensive, polypropylene gives a good mix of cost and functionality.
Specialized Applications of Injection Molding Materials
Advanced materials are sometimes needed for special uses:
- Nylon: Its strength and flexibility make it ideal for car parts and consumer goods.
- ABS (Acrylonitrile Butadiene Styrene): This material is strong and impact resistant. It suits electronic housings and LEGO bricks.
- PVC (Polyvinyl Chloride): Its durability is great for building materials.
Conclusion on Material Selection
To conclude, choosing the right material needs a clear understanding of performance needs. I often look at material databases1 or industry rules to decide. Every project is special. The right material is crucial for bringing your vision to life.
Polypropylene is commonly used for automotive parts in molding.True
Polypropylene's lightweight and chemical resistance make it ideal for automotive applications in injection molding.
Nylon is unsuitable for high-temperature applications.False
Nylon actually has excellent thermal stability, making it suitable for high-temperature applications in injection molding.
How Does Mold Design Affect Product Quality?
Did you ever think about how something like mold design could ruin a product? Let’s explore the world of injection molding. This technology really affects product quality. It is crucial.
Mold design greatly affects product quality. It influences dimensional accuracy, surface finish and defect rates in injection-molded items. Proper execution in the design process is crucial. Manufacturers improve durability and functionality. Defects decrease. Mold design is fundamental to quality.
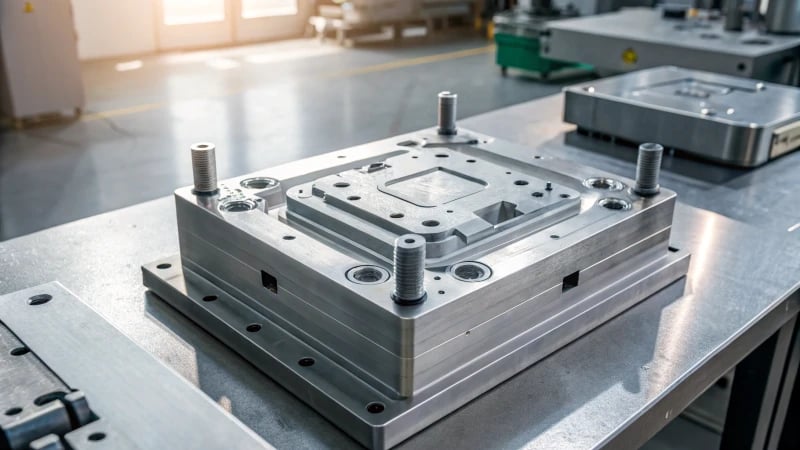
Overview of Injection Molding Process
My journey in product design often reminds me of the amazing power of injection molding. This method turns raw plastic into the beautiful, useful products we use daily. The process heats and melts plastic granules, then injects them into a closed mold cavity using high pressure. After cooling, the product takes the mold’s shape. It’s like magic!
Key Steps in Mold Design Impacting Quality
-
Raw Material Selection
The adventure begins with choosing the right plastic. I recall the first time I chose materials; it felt really overwhelming. Plastics like polypropylene (PP)2 and polycarbonate (PC)3 have unique characteristics. The choice affects performance, strength and heat resistance. It really matters. -
Mold Installation and Preheating
Proper mold installation is extremely crucial. It’s like setting the stage for a performance. Preheating keeps the mold at a consistent temperature. This helps the molten plastic flow easily and reduces stress. A perfect finish is very important. -
Injection Process Control
Every detail matters during injection. Pressure and speed are key. They decide if the mold cavity fills completely or if defects appear. Once, I ignored these parameters, resulting in a poor batch. This taught me how vital it is to maintain optimal conditions. It was a significant lesson. -
Pressure Holding Stage
This stage is about keeping pressure to prevent shrinkage marks when cooling. If it’s not set correctly, inaccuracies can ruin the product. Trust me, spending time to get this right is very important! -
Cooling and Solidification
Cooling time is another crucial step. I experienced issues when I rushed and got warped pieces. Timing is essential; it finds the balance for uniform solidification while avoiding demolding troubles. Never hurry this stage. -
Demolding Techniques
Finally, demolding is a step that can ruin or save your product. The right technique avoids damage; sometimes trimming or surface finishing is required for that polished look everyone strives for.
Impact of Mold Design on Product Quality
Mold design affects more than just looks; it directly influences important quality factors:
Factor | Importance |
---|---|
Dimensional Accuracy | Ensures parts fit together correctly in assembly |
Surface Finish | Affects aesthetic appeal and customer satisfaction |
Strength | Determines durability and functionality |
Defect Rate | Lower defect rates mean higher overall quality |
Conclusion
In conclusion, each step from selecting raw materials to demolding is crucial in mold design’s impact on product quality. Each part must work together in harmony; understanding these elements has been extremely valuable in my design career.
Mold design directly influences product strength and durability.True
The design of the mold affects how well the final product can withstand stress, impacting its overall strength and longevity.
Improper cooling can lead to excessive product deformation.True
Cooling time is critical; inadequate cooling may cause the product to deform, affecting its quality and usability.
What Are Common Defects in Injection Molding and How Can I Avoid Them?
I work as a product designer. Understanding the injection molding process is very important. My experience shows this firsthand. Challenges are common and knowing these defects changes everything. It really helps improve production quality.
Common defects in injection molding include flow lines, sink marks, short shots, and warping. Each defect arises from specific issues during production but can be mitigated through careful design and process control. Understanding these challenges can significantly enhance your production quality.
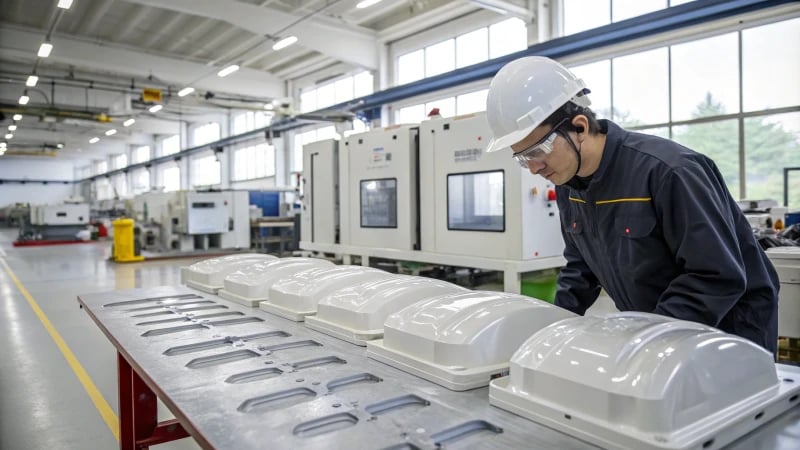
Overview of Common Defects in Injection Molding
Injection molding is a fascinating process. However, when issues arise, it might feel intimidating. I recall when I first saw flow lines on a prototype I put a lot of effort into. Those patterns seemed like a personal setback, yet they gave me crucial lessons about the process. In this guide, I wish to share some common defects I’ve seen and how to prevent them. This way, you might not have to learn the hard way like I did.
Injection molding can encounter several defects that compromise product quality. Understanding these issues is essential for improving manufacturing processes. Common defects include flow lines, sink marks, short shots, and warping. Let’s break down these defects and explore how they can be avoided.
1. Flow Lines
Flow lines appear as streaks on the surface of molded parts, often caused by variations in the melt flow rate or temperature. These can detract from the product’s aesthetic quality.
Prevention Tips:
- Ensure consistent melt temperatures and flow rates during the injection process.
- Optimize the design of the mold to facilitate smoother flow of the plastic.
For further information, check out flow line mitigation techniques4.
2. Sink Marks
Sink marks are depressions that occur on the surface of a molded part, typically where thicker sections of material cool more slowly.
Prevention Tips:
- Use appropriate cooling channels to ensure uniform cooling throughout the mold.
- Reduce the thickness of the molded section or modify the mold design to distribute material evenly.
Learn more about avoiding sink marks by visiting sink mark solutions5.
Key Steps in Injection Molding Process
To effectively prevent these defects, understanding the injection molding process is crucial. Here’s a brief overview of key steps:
Step | Description |
---|---|
Raw Material Preparation | Selecting and drying plastic materials to avoid bubbles. |
Mold Installation | Properly installing and preheating the mold for consistent results. |
Injection Process | Controlling parameters like pressure and speed to ensure complete fill. |
Pressure Holding | Maintaining pressure to compensate for material shrinkage during cooling. |
Cooling and Solidification | Ensuring adequate cooling time to avoid stress and deformation. |
Demolding | Carefully ejecting products to prevent damage. |
3. Short Shots
Short shots occur when the mold does not fill completely, leaving parts of the product unformed.
Prevention Tips:
- Increase injection pressure to ensure complete filling of the mold.
- Verify that the material is adequately heated to achieve proper flow.
For more insights, check out short shot prevention strategies6.
4. Warping
Warping refers to distortion of the molded part due to uneven cooling or stress within the material.
Prevention Tips:
- Ensure uniform cooling throughout the mold and utilize appropriate cooling channels.
- Design parts with consistent wall thickness to minimize internal stress.
Explore detailed techniques for preventing warping in our guide on warping solutions7.
By sharing my experiences, I hope you can steer clear of some of these challenges and succeed in your injection molding work!
Flow lines are caused by inconsistent melt temperatures.True
Inconsistent melt temperatures lead to flow variations, resulting in visible streaks known as flow lines on molded parts.
Warping can be prevented by using thicker mold designs.False
Using thicker mold designs can actually increase the risk of warping due to uneven cooling and internal stress.
How Can I Optimize the Injection Molding Process for Efficiency?
Improving the injection molding process is crucial for increasing production efficiency. This also really helps produce high-quality products. Some strategies have worked really well for me. I will share them with you.
To improve the injection molding process, pay close attention to mold design. Control process parameters effectively. Use automation where possible. Regular maintenance of equipment is very important. Equipment maintenance is really crucial.
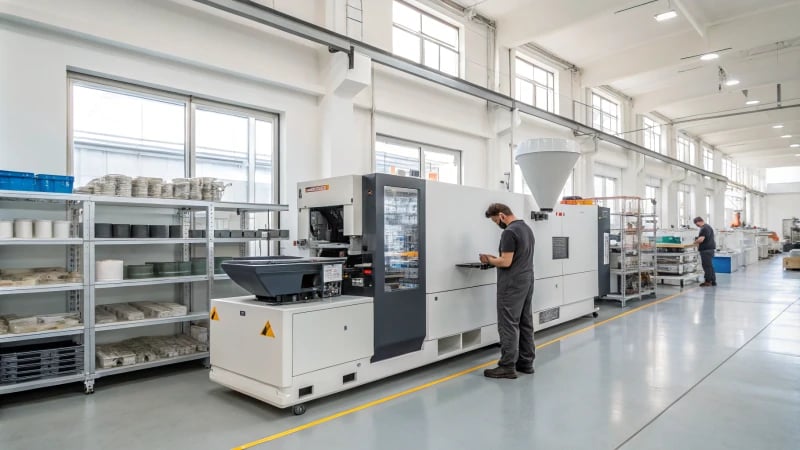
Understanding the Injection Molding Process
To truly understand how to improve the injection molding process, I needed to study its main parts deeply. Every step is crucial for creating high-quality plastic parts. Understanding these details showed me where I could achieve big efficiency gains.
Overview of the Injection Molding Process
Injection molding is like a perfect orchestra. Every part must work in harmony to produce a great final product. This complex manufacturing method efficiently creates plastic objects. It starts with melting plastic and ends with a cooled product shaped like the mold. Here are the key steps I learned:
Step | Description |
---|---|
Raw Material Preparation | Choosing the right plastic material based on product requirements such as strength and heat resistance. Proper drying is crucial to avoid defects. |
Mold Installation & Preheating | Ensuring that the mold is correctly installed and preheated helps in achieving better fill and reduces internal stress in the final product. |
Injection Process | This is the core step where melted plastic is injected into the mold under high pressure, affecting product quality through parameters like speed and pressure. |
Pressure Holding Stage | Maintaining pressure after injection helps prevent shrinkage marks, which can significantly impact the final product’s appearance and accuracy. |
Cooling and Solidification | Effective cooling is vital. Using cooling channels ensures that the product solidifies correctly without causing stress or difficulty in demolding. |
Demolding | Correct ejection methods prevent damage to the final product and ensure smooth production flow. |
Key Optimization Strategies
-
Optimize Raw Material Usage: I choose high-quality materials that match product needs. Using recycled scrap has really lowered my costs. This approach has changed the game.
-
Improve Mold Design: Advanced mold designs have greatly increased flow and cooling efficiency for me. A good mold design cuts cycle times; everyone wants shorter cycles.
-
Control Process Parameters: Adjusting things like injection speed and pressure has improved product quality and reduced cycle times in my work. Regular checking is very essential.
-
Regular Maintenance: Regular maintenance keeps machines running smoothly, preventing unexpected breakdowns that disrupt production schedules.
-
Use Automation and Robotics: Automation has streamlined my processes, reducing manual work while raising precision in tasks like loading and unloading.
-
Train Staff: Ongoing training for operators is very important; when my team knows best practices, we operate machines better and catch issues before they grow.
Measuring Efficiency Gains
To measure how well my optimizations work, I focus on key performance indicators (KPIs) like:
- Cutting cycle times
- Reducing scrap rates
- Improving product quality measures (defects per million opportunities)
- Saving costs on materials
For more details on specific techniques that have worked for me in improving injection molding efficiency, check out advanced molding techniques8.
Conclusion and Ongoing Evaluation
Optimization is an endless journey; regularly reviewing operations and asking for team feedback highlights new improvement areas. As the injection molding field develops, staying updated on the latest advancements and practices is crucial for success.
Proper mold design can reduce injection molding cycle times.True
Investing in advanced mold designs enhances flow and cooling, leading to shorter cycle times and improved efficiency in the injection molding process.
Automation in injection molding eliminates all production errors.False
While automation improves precision and reduces manual labor, it does not guarantee the elimination of all production errors due to potential system malfunctions or material issues.
Conclusion
This article outlines the essential steps in the injection molding process, emphasizing the importance of each stage for achieving high-quality plastic products.
-
Learn about advanced materials used in specialized injection molding applications to meet demanding requirements. ↩
-
Clicking this link will provide deeper insights into injection molding techniques that enhance product quality, which could be beneficial for your projects. ↩
-
This link offers academic resources about mold design principles that could enhance your understanding and practices in manufacturing. ↩
-
This link will provide you with comprehensive insights on common injection molding defects and effective prevention strategies to enhance your manufacturing processes. ↩
-
Exploring this resource will deepen your understanding of sink marks and offer practical solutions for your injection molding projects. ↩
-
Learn strategies for avoiding short shots, ensuring your molds are filled completely during production with this informative article. ↩
-
This guide provides valuable techniques for preventing warping, ensuring your molded parts maintain their intended shape and quality. ↩
-
This link provides essential strategies for enhancing injection molding processes, helping you increase productivity while maintaining quality. ↩