I still remember the first time I tackled designing a screw boss—it was a true test of patience and precision!
Designing an effective screw boss involves optimizing wall thickness, diameter, draft angle, and material selection to ensure support and fastening without compromising part integrity or manufacturability.
Over the years, I’ve come to realize that each design element plays a crucial role. Understanding these intricacies can be the difference between a seamless assembly and a frustrating rework. Let’s dive deeper into each aspect, with detailed guidelines and insights that can elevate your screw boss designs to meet industry standards.
Wall thickness is crucial for screw boss design.True
Proper wall thickness ensures structural integrity and prevents failure.
Material selection doesn't affect screw boss effectiveness.False
Material choice impacts durability and compatibility with the molded part.
- 1. How Does Wall Thickness Affect Screw Boss Design?
- 2. What Are the Best Materials for Screw Bosses?
- 3. How Do Draft Angles Influence Molded Part Performance?
- 4. How Does Diameter Influence Screw Boss Effectiveness?
- 5. How Can I Ensure Screw Bosses Meet Industry Standards?
- 6. What Are Common Mistakes in Screw Boss Design and How to Avoid Them?
- 7. Conclusion
How Does Wall Thickness Affect Screw Boss Design?
Ever wondered how something as simple as wall thickness can make or break your design?
Wall thickness in screw boss design is vital for structural strength, molding material flow, and cooling times, ensuring stress management and defect minimization.
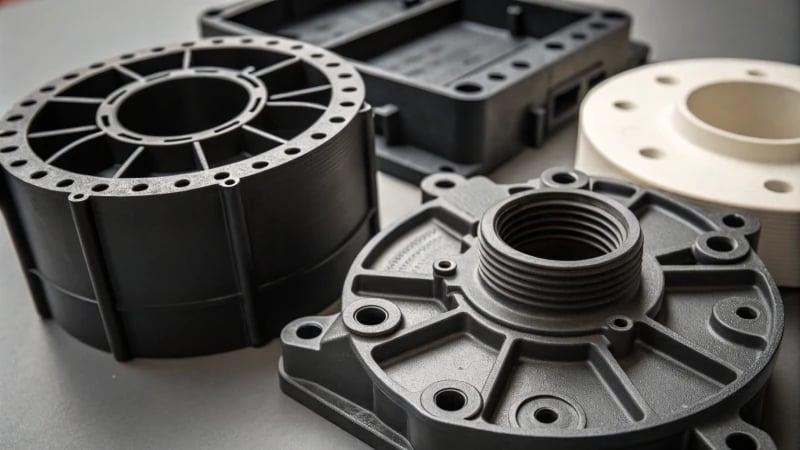
The Role of Wall Thickness in Structural Integrity
When I first dove into designing screw bosses, I quickly learned how critical wall thickness could be. Imagine you’re building a tower of blocks; the sturdiness depends on how well those blocks are arranged and balanced. Similarly, a screw boss needs just the right wall thickness to stand strong against mechanical stresses. Too thin, and you’re flirting with cracks that could spell disaster. Too thick, and you might find yourself dealing with pesky sink marks or voids.
Wall Thickness | Structural Integrity | Potential Issues |
---|---|---|
Thin | Low | Risk of cracking |
Optimal | Balanced | Durable |
Thick | High | Sink marks, voids |
Impact on Material Flow and Cooling
I remember one of my early projects where I underestimated the impact of wall thickness on material flow during the injection molding process. Thinner walls allowed the material to race through the mold, which was great for reducing cycle times but resulted in incomplete fills that turned out to be a nightmare. On the flip side, thicker walls meant the material took its sweet time, leading to longer cooling times1. It’s all about finding that sweet spot for both efficiency and quality.
Considerations for Optimizing Screw Boss Design
- Material Selection: I’ve learned that different materials have their quirks when it comes to wall thickness. Take ABS2, for example—its needs are worlds apart from something like polycarbonate.
- Design Guidelines: Keeping the wall thickness uniform is key, and I’ve found that using ribs or gussets can be a clever way to boost strength without just piling on more material.
- Simulation and Testing: Tools like CAD software have been lifesavers for me. Running simulations helps pinpoint potential issues before they snowball into bigger problems during production.
By weighing these factors carefully, designers like me can create screw bosses that don’t just meet the mark for functionality but also stand up to the rigors of manufacturing. The trick is balancing wall thickness with other design aspects to nail down those optimal results in plastic component manufacturing.
Further Reading
For those of us keen on honing our craft, diving into case studies3 on plastic component design or chatting with material experts can offer some solid insights. These resources have been invaluable in fine-tuning my design practices.
Thicker walls increase screw boss structural integrity.True
Thicker walls provide more material to distribute stress, enhancing strength.
Thin walls reduce cooling times in molding processes.False
Thin walls allow faster material flow, not necessarily reducing cooling time.
What Are the Best Materials for Screw Bosses?
Deciding on the right material for screw bosses feels like piecing together a puzzle. Each material has its own strengths and quirks, just like each piece has its own shape.
Top materials for screw bosses are ABS, polycarbonate, and nylon, offering strength, durability, and moldability, ideal for plastic components with screw bosses.
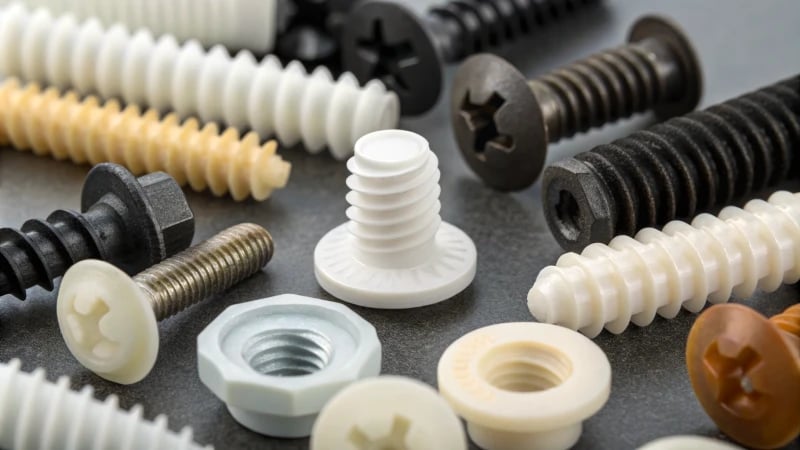
Key Characteristics of Ideal Materials
When selecting materials for screw bosses, consider factors like tensile strength, flexibility, and thermal resistance4. Thermoplastics are often preferred due to their versatility and ability to withstand repeated stress without cracking or deforming.
Material | Tensile Strength | Flexibility | Thermal Resistance |
---|---|---|---|
ABS | Moderate | High | Moderate |
Polycarbonate | High | Moderate | High |
Nylon | High | High | Moderate |
Thermoplastics stood out to me because they can handle repeated stress without cracking, which is crucial in ensuring the longevity of a product.
Advantages of Thermoplastics
In my journey through the world of mold design, thermoplastics like ABS and polycarbonate became my go-to. They are akin to having a trusty Swiss army knife—they’re versatile and reliable. ABS, with its impact resistance and ease of machining, is a lifesaver in high-stress situations. It reminds me of the time I worked on a project with stringent impact resistance requirements; ABS was the hero of that story. On the flip side, polycarbonate offers excellent transparency and high thermal stability, making it perfect for applications where these features are paramount.
Thermoplastics such as ABS (Acrylonitrile Butadiene Styrene) and polycarbonate are popular choices for screw bosses because they combine mechanical strength with easy processing5.
Considerations for Design
Selecting the right material is just the first step. The design of screw bosses can greatly influence performance, much like how a recipe’s method can affect the final dish. Ensuring proper wall thickness and avoiding undercuts during molding are lessons I learned the hard way.
Nylon6 is another excellent choice I often consider, especially when dealing with applications involving moving parts due to its exceptional wear resistance and low friction.
Through understanding these materials’ properties, I’ve learned to optimize screw boss designs not just for performance but also for cost-effectiveness. Every project has its unique set of requirements, and evaluating these needs is key to selecting the most suitable material.
Thermoplastics are preferred for screw bosses due to flexibility.True
Thermoplastics offer high flexibility, essential for withstanding stress.
Nylon has low thermal resistance compared to polycarbonate.True
Polycarbonate has high thermal resistance, while nylon's is moderate.
How Do Draft Angles Influence Molded Part Performance?
Ever wondered how something as tiny as a draft angle can make or break your design? Turns out, these little angles hold the key to a seamless molding process and flawless product outcomes.
Draft angles reduce friction during part release from molds, protecting both parts and molds from damage, thus enhancing quality and durability of molded components.
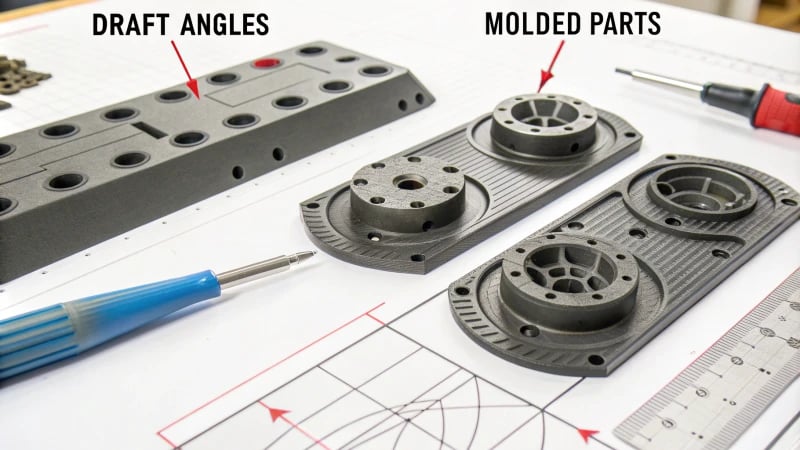
The Role of Draft Angles in Ejection
Have you ever tried to get a cake out of a pan without greasing it first? That’s kind of what happens when a molded part doesn’t have the right draft angle. As the part cools, it shrinks and clings to the mold. This can turn what should be a smooth ejection process into an uphill battle. I’ve seen this happen firsthand, back when I was learning the ropes in my early design days. A well-thought-out draft angle7 adds that extra flair, allowing parts to slide out effortlessly, almost like magic.
Table: Impact of Draft Angle on Ejection Ease
Draft Angle | Ejection Ease | Surface Finish |
---|---|---|
0 degrees | Difficult | Poor |
1-3 degrees | Moderate | Good |
4+ degrees | Easy | Excellent |
Minimizing Defects with Proper Draft
It’s fascinating how something invisible to the naked eye can have such a profound impact. Without those crucial draft angles, parts can warp or scratch as they’re pried from molds, which is like trying to peel off a stubborn sticker without leaving any residue. This is especially critical when creating intricate electronic components where every millimeter counts. I remember a project where even a minor surface defect led to major assembly issues, underscoring how precision is everything in this field.
Material Considerations and Design Flexibility
Different materials behave like different personalities at a party. Thermoplastics, for instance, are more like the life of the party—they shrink more and need bigger draft angles compared to their more reserved counterparts, thermosets. When I’m designing molds, I always keep this in mind, ensuring that each material’s unique behavior is accounted for to maintain consistency across the board. Thoughtful drafting isn’t just about avoiding defects; it’s about boosting production efficiency8, too.
By weaving in just the right draft angles, we can elevate both the form and function of our molded parts. It’s like hitting all the right notes in a song, ensuring our products not only look great but also meet rigorous industry standards without a hitch.
Draft angles reduce friction during part ejection.True
Draft angles create a taper that minimizes friction between the part and mold.
Thermosets require larger draft angles than thermoplastics.False
Thermoplastics require larger draft angles due to higher shrinkage rates.
How Does Diameter Influence Screw Boss Effectiveness?
I remember the first time I realized how crucial screw boss diameter is in ensuring product durability—it was a game-changer in my design career.
The diameter of a screw boss is vital for strength and stability, impacting load distribution. An optimal size ensures secure fastening, preventing material failure or stripping.
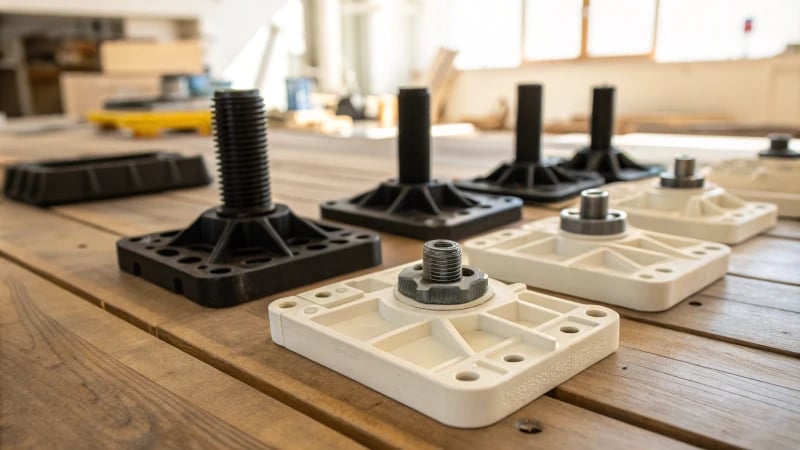
Understanding Screw Boss Dynamics
In my journey through the world of plastic component designs9, screw bosses have always stood out as unsung heroes, especially when it comes to fastening parts securely. I recall working on a project where the difference between success and disaster hinged on getting the screw boss diameter just right. It taught me that the diameter plays a pivotal role in how much load a boss can bear and how well it resists stripping. A well-thought-out screw boss must not only fit the screw but also boast enough wall thickness to ward off deformation—a lesson I learned from a near-miss experience.
Optimal Diameter for Strength
I’ve found that aiming for a screw boss diameter that’s about 2.5 times the major diameter of the screw is a sweet spot. This ratio allows the boss to handle stress without compromising the integrity of the material. For example, if you’re dealing with a screw that’s 4 mm in diameter, you’d want a boss that’s around 10 mm to efficiently distribute the load. I’ve always kept this rule of thumb handy:
Screw Size | Recommended Boss Diameter |
---|---|
M3 | 7.5 mm |
M4 | 10 mm |
M5 | 12.5 mm |
Factors Influencing Diameter Selection
Of course, rules are made to be adapted. I’ve learned that materials react differently under stress, which means adjusting diameters is often necessary. For instance, I once had to tweak designs because polycarbonate parts required different diameters compared to polypropylene due to their higher flexural modulus10. Also, environmental conditions like temperature fluctuations can throw a wrench in the works, making it crucial to consider these factors during design.
Practical Considerations in Design
Incorporating practical aspects like draft angles and parting lines has saved me more than once from embarrassing design flaws. Ensuring that a boss isn’t too close to the edge of a part is something I wish I’d been told earlier—it can prevent cracking during installation. These days, I rely heavily on computer-aided design11 tools to visualize potential pitfalls before they become costly mistakes. Every design is a lesson learned, and each project adds another tool to my kit.
The optimal boss diameter is 2.5 times the screw's major diameter.True
This ratio allows for effective load distribution without material compromise.
Polycarbonate and polypropylene require the same boss diameter.False
Different materials have varying flexural moduli, affecting boss diameter needs.
How Can I Ensure Screw Bosses Meet Industry Standards?
Remember the first time you tried to assemble a flat-pack desk and realized a crucial screw was missing? Designing screw bosses is like ensuring every piece fits perfectly.
Ensure screw bosses meet industry standards by selecting appropriate materials, maintaining precise dimensions, and following design guidelines with CAD and industry references for optimized functionality and compliance.
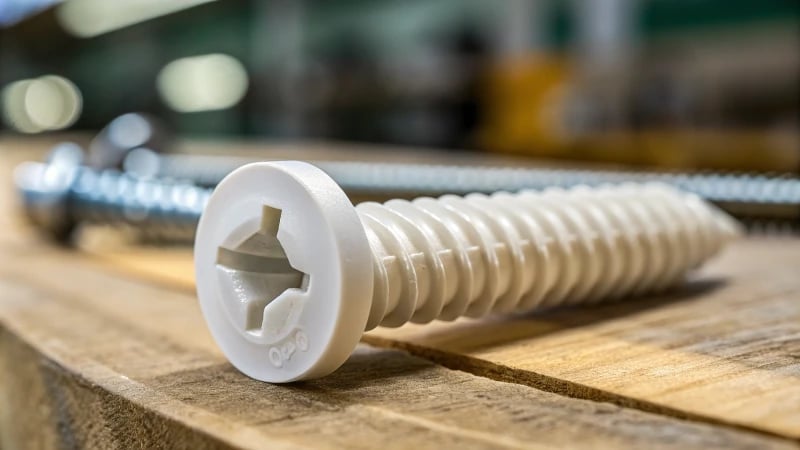
Material Selection for Screw Bosses
I once found myself in a bind when a batch of prototypes failed because I underestimated the importance of material choice. Now, I understand that selecting the right material, like ABS, polycarbonate, or nylon, can make all the difference. These materials offer unique properties such as strength and flexibility, which are crucial for the performance of the final product. Understanding material properties12 has become a key step in my design process.
Dimensional Accuracy and Tolerances
Precision in dimensions is not just a technical requirement; it’s an art form I’ve come to appreciate deeply. Early in my career, I learned the hard way when a slight miscalculation led to an entire redesign. Now, using CAD software is second nature to me. It ensures that measurements and tolerances are spot on, avoiding costly errors. Guidelines from trusted engineering standards13 are my go-to resources for maintaining accuracy.
Dimension | Tolerance (mm) |
---|---|
Diameter | ±0.05 |
Height | ±0.10 |
Wall Thickness | ±0.02 |
Design Guidelines for Optimal Performance
There’s a certain satisfaction in following design guidelines that promise optimal performance. Like the time I discovered the perfect boss height-to-diameter ratio—typically between 2:1 to 4:1—this ratio has become a cornerstone in my designs for structural integrity. Adding ribs for support is another trick I picked up from various industry case studies14.
Implementing CAD Tools for Precision
Working with CAD tools has been a game-changer in how I approach screw boss design. These tools allow me to model with precision and even simulate stress tests to ensure compliance before production starts. Discovering advanced CAD techniques15 has enhanced my design accuracy significantly.
Consulting Industry References
In an industry that’s constantly evolving, staying updated with the latest standards is essential. ISO guidelines and manufacturer specifications provide me with critical insights into emerging trends and regulatory requirements. Review comprehensive guides16 to stay ahead.
By concentrating on these aspects, I can ensure that my screw bosses not only meet but often exceed industry standards, setting the stage for durable and compliant product designs.
ABS is a common material for screw bosses.True
ABS is frequently used for screw bosses due to its strength.
Screw boss height should always be twice its diameter.False
Height-to-diameter ratio varies; it ranges from 2:1 to 4:1.
What Are Common Mistakes in Screw Boss Design and How to Avoid Them?
Ah, the world of screw boss design—it’s a maze where even the tiniest misstep can lead to big headaches. I’ve been there, scratching my head over why that seemingly perfect design just won’t hold up. Let’s dive into those common pitfalls and how to steer clear of them.
Common mistakes in screw boss design include incorrect diameter, wall thickness, and draft angles. Avoid these by adhering to design guidelines on dimensions and materials for optimal product performance.
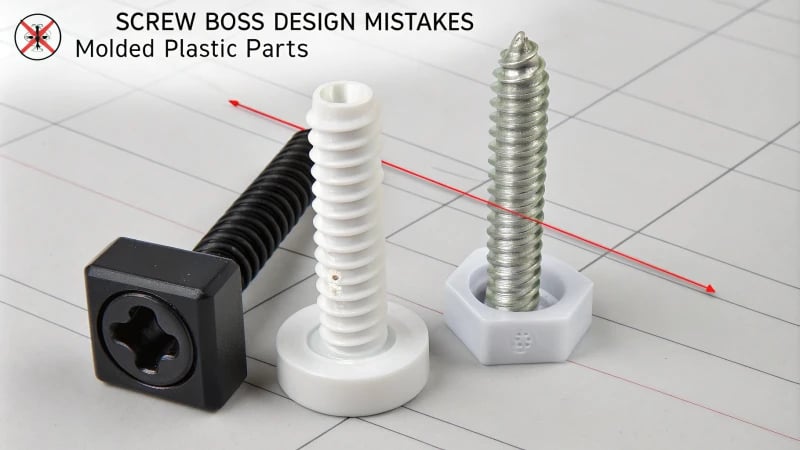
Incorrect Diameter Sizing
Oh boy, I remember the first time I underestimated the importance of getting the diameter just right. I ended up with screws that either wobbled like they were auditioning for a dance show or wouldn’t fit at all. Imagine the embarrassment in front of my team! A diameter too small can cause assembly nightmares17, while too large leaves your material weak and prone to failure.
How to Avoid: Stick to standard tables for screw sizes; they’re your best friend here. Make sure the boss diameter is snug but not suffocating. Keep an eye on the material’s shrinkage rate—you don’t want any surprises.
Screw Size | Recommended Boss Diameter | Material Shrinkage |
---|---|---|
#4 | 3.6mm | 0.5% |
#6 | 4.8mm | 0.6% |
Improper Wall Thickness
Then there’s the wall thickness saga. I learned this lesson the hard way when I designed a part that resembled a pumpkin during Halloween because of those awful sink marks18. On the flip side, go too thin and you risk compromising strength.
How to Avoid: Aim for a wall thickness that’s in harmony with its surroundings. Generally, keeping it between 40-60% of the nominal wall thickness of the part works well.
Inadequate Draft Angles
Draft angles were another hurdle I stumbled over. It’s like trying to unstick gum from under your shoe if you don’t get this right. Without enough draft angle, removing your piece from the mold is a risky business that can lead to damage.
How to Avoid: A minimum draft angle of 0.5 degrees can be a lifesaver, making it easier to release from molds and giving your surface finish a nice touch.
Material Selection Concerns
Choosing the wrong material is like picking a pair of shoes that look fantastic but give you blisters after an hour. A brittle or excessively worn-out boss is no fun.
How to Avoid: Select materials based on what your part needs to do. Consider factors like temperature resistance, mechanical strength, and chemical compatibility19.
Lack of Rib Reinforcements
Lastly, don’t underestimate rib reinforcements. I skipped them once, thinking my boss was strong enough on its own, only to see it collapse under pressure like a house of cards.
How to Avoid: Design ribs around the base of the boss strategically. They should support without getting in the way of screw insertion, handling stress like a pro.
In our ever-evolving industry, staying updated with best practices is crucial. It’s worth investing time in continuous learning to refine designs and processes. For more advanced insights into screw boss designs, check out resources tailored for product designers20. Let’s keep pushing those design boundaries together!
Incorrect diameter sizing weakens screw boss support.True
A wrong diameter can lead to improper screw fit or weak material support.
Using thick walls prevents sink marks in screw bosses.False
Thick walls can actually cause sink marks due to uneven cooling.
Conclusion
Designing an effective screw boss involves optimizing wall thickness, diameter, draft angles, and material selection to ensure structural integrity and manufacturability in plastic components.
-
Understand how wall thickness influences cooling times, affecting production efficiency and quality. ↩
-
Compare how different materials like ABS and polycarbonate respond to changes in wall thickness. ↩
-
Gain practical insights from case studies on optimizing wall thickness in plastic designs. ↩
-
Explore how thermal resistance in thermoplastics affects durability in high-temperature environments, ensuring screw bosses maintain integrity under stress. ↩
-
Learn why ABS is favored for its balance of strength, impact resistance, and ease of processing in manufacturing screw bosses. ↩
-
Discover how nylon’s wear resistance and low friction make it an excellent material choice for applications with moving parts. ↩
-
Understand the fundamental concept of draft angles to grasp their importance in injection molding. ↩
-
Discover how proper draft angles contribute to enhanced production efficiency. ↩
-
Explore why screw bosses are vital in securing components within plastic designs, enhancing overall assembly integrity. ↩
-
Discover how flexural modulus impacts plastic material performance, influencing design choices in engineering applications. ↩
-
Learn about the advantages of CAD in mold design, improving precision and reducing error rates in manufacturing. ↩
-
Exploring material properties helps in selecting suitable materials for durability and strength in screw boss design. ↩
-
Reviewing engineering standards ensures adherence to precise dimensional tolerances, crucial for reliable screw boss designs. ↩
-
Examining case studies provides practical insights into successful design strategies for screw bosses. ↩
-
Learning advanced CAD techniques enhances precision in modeling and verifying screw boss designs. ↩
-
Reviewing ISO guidelines helps in aligning designs with international standards, ensuring compliance and quality. ↩
-
Learn how incorrect sizing affects assembly efficiency and explore guidelines to improve fit. ↩
-
Understand how improper wall thickness causes defects and discover techniques to mitigate them. ↩
-
Find out how choosing the right material enhances durability and performance. ↩
-
Access expert insights on optimizing designs for durability and efficiency. ↩