Have you ever marveled at the sleek design of a modern electronic device? That’s the magic of thin-wall injection molding at work!
Key process points in thin-wall injection molding include selecting high-fluidity materials, optimizing mold design with efficient cooling systems, setting precise injection parameters, and using high-speed machines to ensure quality and efficiency.
While the basics are straightforward, each step involves nuanced decisions that can greatly impact the final product. Let’s delve deeper into these critical areas to unlock the potential for superior thin-wall molded products.
High-fluidity materials are essential in thin-wall injection molding.True
High-fluidity materials ensure rapid mold filling, reducing defects.
How Does Material Selection Affect Thin-Wall Injection Molding?
In thin-wall injection molding, selecting the right material is critical to achieving precise and efficient production outcomes. It’s not just about choosing a plastic but selecting one with the right fluidity and thermal stability.
Material selection in thin-wall injection molding impacts mold filling efficiency and part quality. High-fluidity materials like modified polypropylene (PP) and polystyrene (PS) ensure rapid mold filling, while thermal stability prevents degradation during processing, crucial for high-quality results.
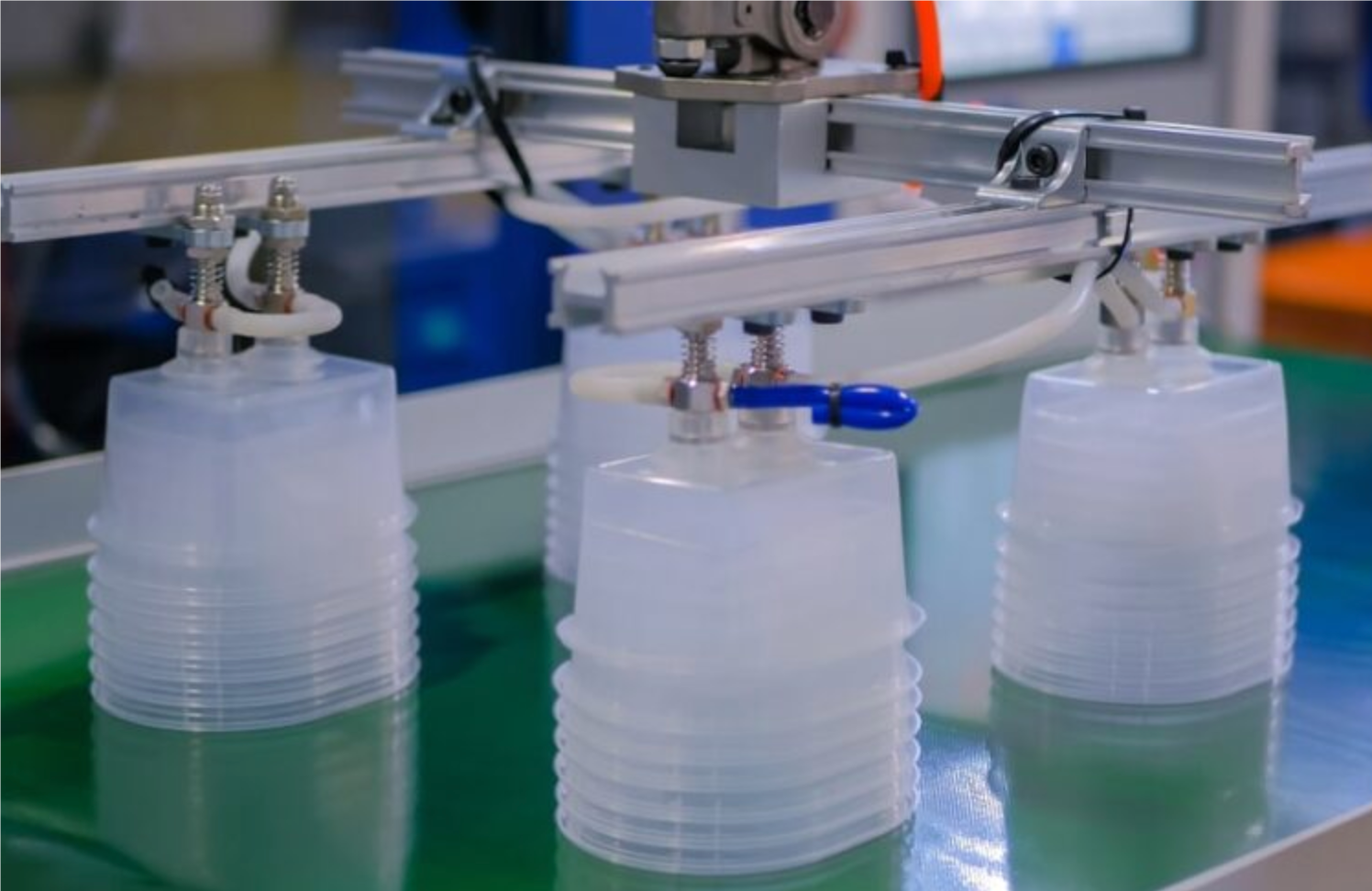
The Importance of High Fluidity
Thin-wall injection molding demands materials with exceptional fluidity to fill intricate mold cavities rapidly. Plastics like high-flow grades of polypropylene (PP) and polystyrene (PS) are often chosen due to their ability to flow swiftly into thin-walled sections. This capability minimizes the risk of incomplete filling or defects such as voids and surface blemishes.
In practice, high-fluidity materials reduce cycle times, which is advantageous for high-volume production. The rapid filling also allows for more complex geometries to be molded effectively without compromising structural integrity.
Ensuring Thermal Stability
Thermal stability is another critical aspect of material selection. During thin-wall injection molding, the plastic melt must maintain its integrity as it cools rapidly within the mold. Materials lacking thermal stability are prone to degradation, leading to weakened or defective parts.
To combat this, engineering plastics often incorporate heat stabilizers, allowing them to perform consistently at elevated injection temperatures. This ensures that parts exhibit consistent mechanical properties and surface quality, even under demanding conditions.
Balancing Cost and Performance
While high-fluidity and thermally stable materials are essential, cost considerations cannot be ignored. The chosen material should align with the product’s functional requirements without unnecessarily inflating costs. Thus, a balance between performance and budget is vital.
For instance, while some high-performance materials offer outstanding features, they might be overkill for applications that don’t require such properties. Therefore, evaluating the specific application needs and matching them with the right material properties is crucial.
Case Study: Material Selection in Action
Consider a scenario involving the production of thin-wall electronic housings. Here, high-flow PP grades1 might be selected for their excellent fluidity and good electrical insulation properties. In contrast, engineering plastics with added stabilizers2 could be used for parts requiring higher thermal stability.
By analyzing specific applications, manufacturers can choose materials that optimize both performance and cost-effectiveness.
In summary, material selection is a pivotal factor that influences the efficiency and quality of thin-wall injection molding. By prioritizing high fluidity and thermal stability, manufacturers can achieve superior product outcomes while maintaining cost efficiency.
High-fluidity materials reduce cycle times in molding.True
High fluidity allows rapid mold filling, reducing production cycle time.
Thermal stability is irrelevant in thin-wall injection molding.False
Thermal stability prevents material degradation, ensuring quality parts.
What Are the Best Practices for Mold Design in Thin-Wall Molding?
Optimizing mold design is crucial for achieving efficiency and quality in thin-wall molding processes. Let’s explore the best practices.
To excel in thin-wall molding, ensure large-size gates for rapid material flow and a well-designed cooling system for uniform temperature control.
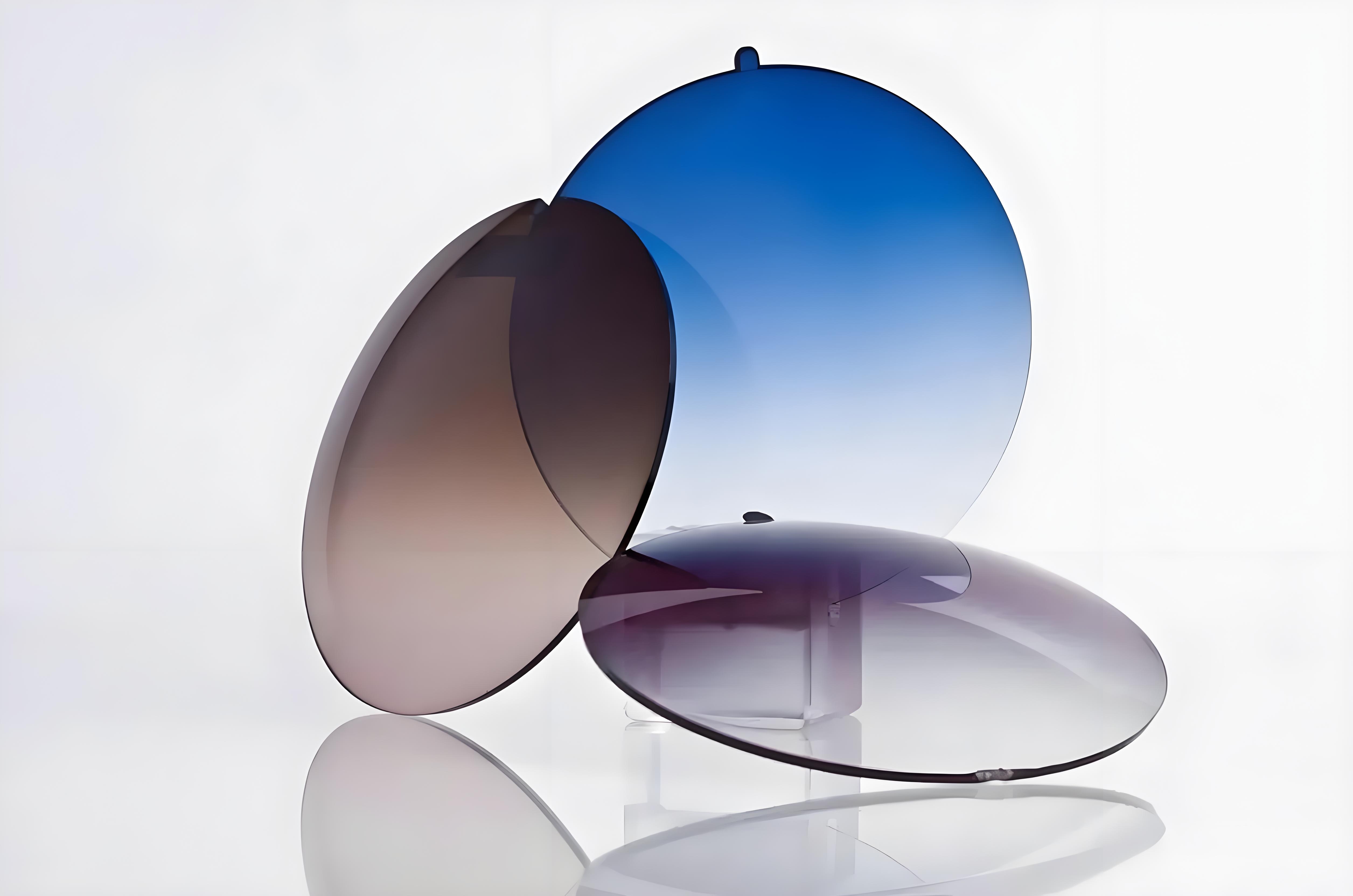
Gate Design: Optimizing Flow and Reducing Stress
In thin-wall molding, gates act as the crucial entry points for molten plastic into the mold cavity. The design of these gates can significantly impact the efficiency and quality of the molding process.
-
Utilize Large-Size Gates: Increasing gate size allows for quicker entry of plastic melt, crucial for reducing cycle time in thin-wall applications. Consider using fan-shaped or thin-sheet gates to enhance the flow rate.
-
Strategic Gate Positioning: Position gates close to thin-walled areas to minimize the flow distance. This not only improves material distribution but also helps prevent stress concentration that could lead to defects.
Cooling System: Ensuring Uniformity and Efficiency
Effective cooling systems are vital in thin-wall molding to maintain product integrity and reduce cycle times. Here are key strategies:
-
Increase Cooling Channels: Implement multiple cooling water channels around critical areas, such as near thin-walled sections, to promote uniform cooling and improve efficiency.
-
Optimize Channel Layout: Employ conformal cooling channels that mirror the shape of the mold cavity. This strategy enhances cooling efficiency by ensuring consistent heat removal throughout the mold.
Design Considerations: Balancing Rigidity and Flexibility
Mold design for thin-wall parts requires a delicate balance between rigidity to support high pressures and flexibility to accommodate complex geometries.
-
Material Choice for Molds: Select materials that can withstand high thermal and mechanical stresses without deforming over time.
-
Use of Inserts and Advanced Structures: Incorporate inserts or ribs where necessary to provide additional support without increasing thickness. This approach helps maintain structural integrity while minimizing material use.
Implementing these best practices in mold design3 can significantly enhance the efficiency and quality of thin-wall injection molding processes, ensuring products meet both performance and aesthetic standards.
Large gates improve cycle time in thin-wall molding.True
Large gates allow faster material flow, reducing cycle time.
Conformal cooling channels are inefficient for thin walls.False
Conformal channels enhance cooling efficiency by matching mold shapes.
How to Optimize Injection Molding Process Parameters?
Optimizing process parameters in injection molding ensures the production of high-quality, precision parts while minimizing defects.
Optimize injection molding by adjusting injection speed and pressure, mold temperature, and holding time to enhance quality and efficiency.
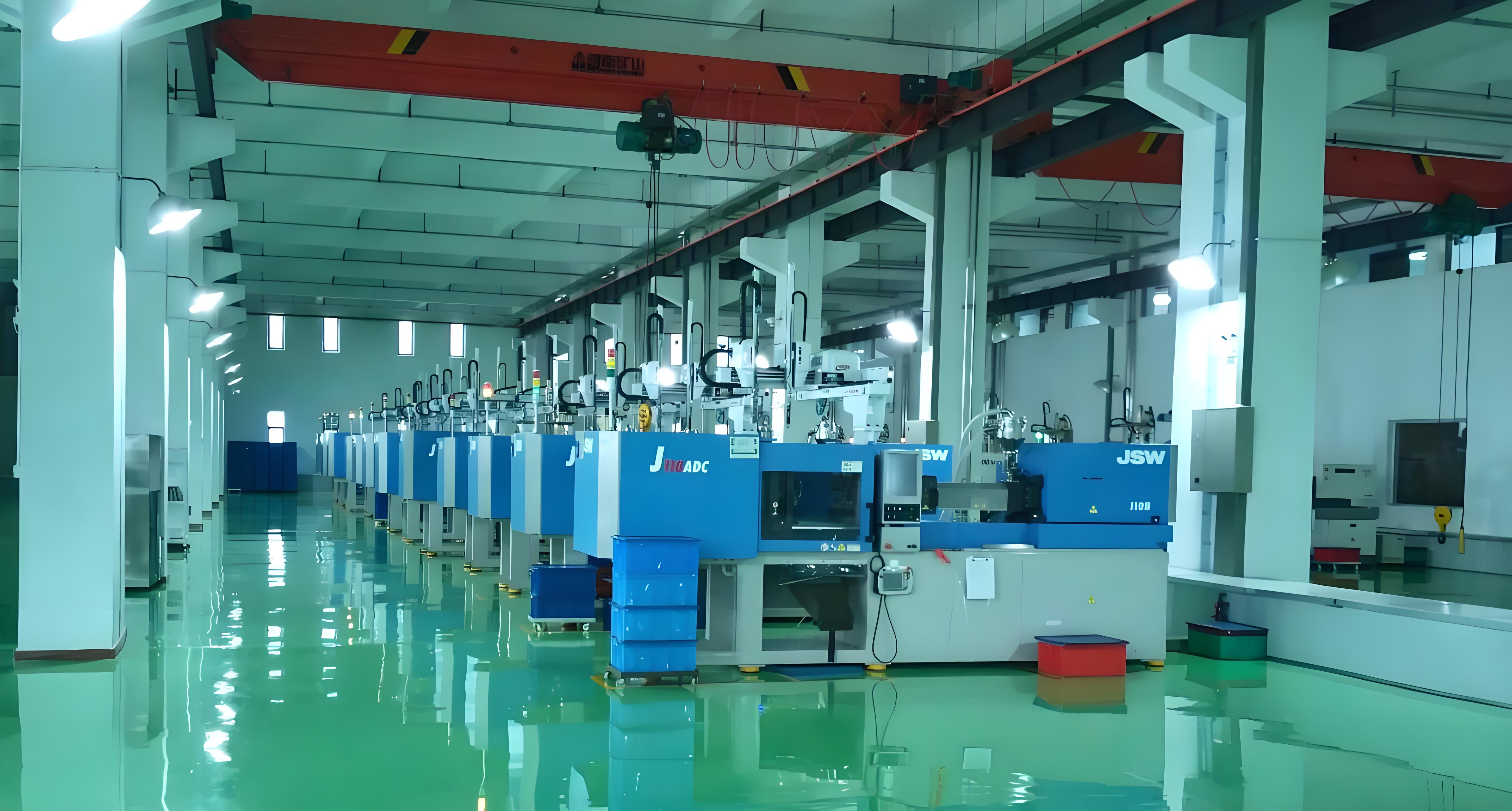
Injection Speed and Pressure
In thin-wall injection molding, achieving the right balance of injection speed and pressure is crucial. A high injection speed4 ensures rapid filling of the mold cavity, minimizing the potential for defects such as short shots or incomplete filling. However, excessive speed can lead to issues like melt fracture or burn marks. It is essential to find a speed that optimizes flow without compromising the material’s integrity.
Simultaneously, injection pressure must be carefully managed to overcome the resistance presented by thin-walled sections. Higher pressure can ensure complete filling but might also risk mold damage or flash formation. Adjusting pressure settings based on part geometry and material characteristics is pivotal.
Mold Temperature Settings
The temperature of the mold directly impacts the cooling rate of the molten plastic. Lowering mold temperature can expedite cooling, thus enhancing production efficiency. However, it requires precise control to prevent warping or shrinkage in the final product. Each material has an optimal temperature range that should be adhered to for best results.
Material Type | Recommended Mold Temperature Range |
---|---|
Polypropylene | 40°C – 80°C |
Polystyrene | 50°C – 70°C |
Holding Time and Pressure Optimization
Holding time and pressure are critical for ensuring dimensional stability and surface quality. During the holding phase, additional material is injected to compensate for shrinkage as the part cools. Longer holding times can improve surface finish and reduce voids but may introduce internal stresses if overextended. Likewise, holding pressure should be sufficient to maintain part integrity without causing excessive stress or distortion.
Understanding the interplay between these parameters allows for fine-tuning that leads to superior product quality and reduced cycle times. Each adjustment should be made with careful consideration of material properties and design requirements, ensuring that every parameter supports the overall production goals.
High injection speed prevents short shots.True
Rapid mold filling minimizes defects like short shots.
Lower mold temperature always prevents warping.False
Precise control is needed; too low can cause shrinkage.
Why Is Equipment Choice Crucial for Thin-Wall Injection Molding?
Selecting the right equipment is vital in thin-wall injection molding to achieve precision and efficiency.
Choosing the right equipment ensures stability, precision, and speed, which are crucial for the demanding process of thin-wall injection molding. High-speed and accurate machines are necessary to meet the stringent requirements of this advanced manufacturing technique.
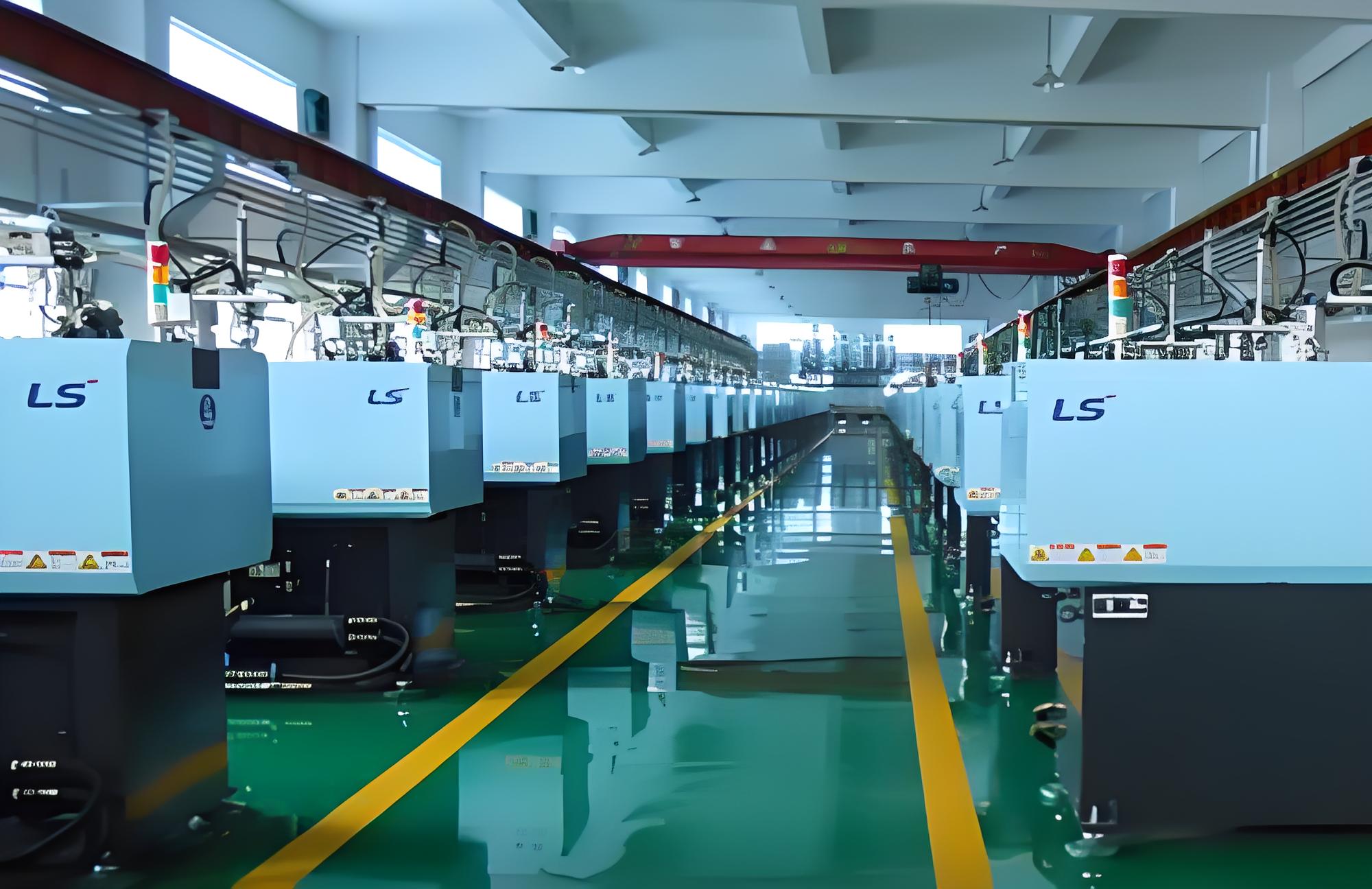
The Role of High-Speed Injection Molding Machines
Thin-wall injection molding demands high-speed injection molding machines due to their ability to deliver rapid shooting speeds and pressure responses. This capability is essential to ensure that the plastic melt fills the cavity quickly enough to prevent premature cooling and incomplete filling.
-
Speed and Pressure: High-speed machines can offer both the speed and pressure needed to overcome the high resistance in thin-walled cavities, ensuring that the molten material reaches every corner before solidifying.
-
Example Machines: Machines such as all-electric injection molding machines or high-speed hydraulic injection machines exemplify the precision and response time needed in thin-wall applications. They provide consistent performance, which is crucial for maintaining product quality over extended production runs.
Importance of Stability and Accuracy
In addition to speed, the stability and accuracy of the equipment play a pivotal role in thin-wall injection molding. These characteristics ensure that the dimensional integrity of the molded parts is maintained, reducing defects such as warping or shrinkage.
-
Mechanical Structure: A robust mechanical structure in the injection molding machine helps maintain consistent performance even under high-speed operations. This consistency is vital for producing parts with precise dimensions.
-
Control Systems: Advanced control systems enable precise regulation of injection parameters, which helps in maintaining uniformity across batches. Such systems also reduce cycle times, boosting production efficiency.
Balancing Cost with Performance
While high-performance machines come with higher upfront costs, their ability to enhance production quality and reduce defect rates often justifies the investment.
-
Efficiency Gains: Over time, the efficiency gains from reduced cycle times and lower rejection rates can lead to significant cost savings.
-
Long-Term Value: Investing in superior equipment ensures long-term reliability and adaptability to evolving production demands, making it a crucial consideration for manufacturers focusing on thin-wall products.
To understand more about selecting optimal equipment, consider exploring industry reviews and guides like those available in high-speed injection machine reviews5. These resources can offer insights into machine performance and user experiences, aiding informed decision-making.
High-speed machines prevent cooling in thin-wall molding.True
High-speed machines ensure rapid filling, preventing premature cooling.
All-electric machines lack precision for thin-wall molding.False
All-electric machines provide high precision, crucial for thin-wall molding.
Conclusion
By mastering these key process points, you can enhance product quality and operational efficiency in thin-wall injection molding.
-
Learn why high-flow PP grades are ideal for thin-wall applications.: The high fluidity and high gloss of Moplen RP5007 enable processing temperatures to be reduced by 10 to 20°C, injection speeds to be increased, … ↩
-
Explore engineering plastics enhanced with stabilizers for thermal resilience.: Heat stabilizers are used to prevent degradation of plastics by heat, especially during processing, but also in applications. ↩
-
Discover detailed mold design strategies for superior thin-wall molding outcomes.: In general, ensuring your design has uniform wall thickness between 0.060 and 0.120 in. ↩
-
Explore how injection speed affects product quality in molding.: Principles of Injection Speed Setting · 1. The surface velocity of the fluid should be constant. · 2. Use rapid injection to prevent the melt from … ↩
-
Gain insights on top-performing machines and user experiences.: Thin wall injection molding with e-speed ✓ Ideal for thin-wall plastic parts & high-speed applications ✓ Cycle times <2 sec. ✓ Clamping force <6500 kN … ↩