Have you ever wondered how those intricate plastic products are made? Injection moulding is the answer!
Key materials used in injection moulding include thermoplastics like polyethylene, polypropylene, and ABS, as well as thermosetting plastics such as phenolic and epoxy resins. These materials are chosen for their specific properties like durability, chemical resistance, and heat tolerance, making them suitable for a wide range of applications.
But there’s so much more beneath the surface! Let’s explore the unique characteristics of these materials and how they can make or break your project.
Thermoplastics are more recyclable than thermosetting plastics.True
Thermoplastics can be remelted and reshaped, unlike thermosetting plastics.
- 1. How Do Thermoplastics Compare to Thermosetting Plastics in Injection Moulding?
- 2. What Factors Should You Consider When Choosing an Injection Moulding Material?
- 3. How Do Material Properties Influence Product Design in Injection Moulding?
- 4. What Are the Environmental Impacts of Different Injection Moulding Materials?
- 5. Conclusion
How Do Thermoplastics Compare to Thermosetting Plastics in Injection Moulding?
Choosing between thermoplastics and thermosetting plastics in injection moulding can drastically influence product performance and production efficiency.
Thermoplastics, like polyethylene and polypropylene, are known for their recyclability and flexibility in design changes, while thermosetting plastics, such as phenolic and epoxy resins, offer superior heat resistance and structural integrity but cannot be remolded once set.
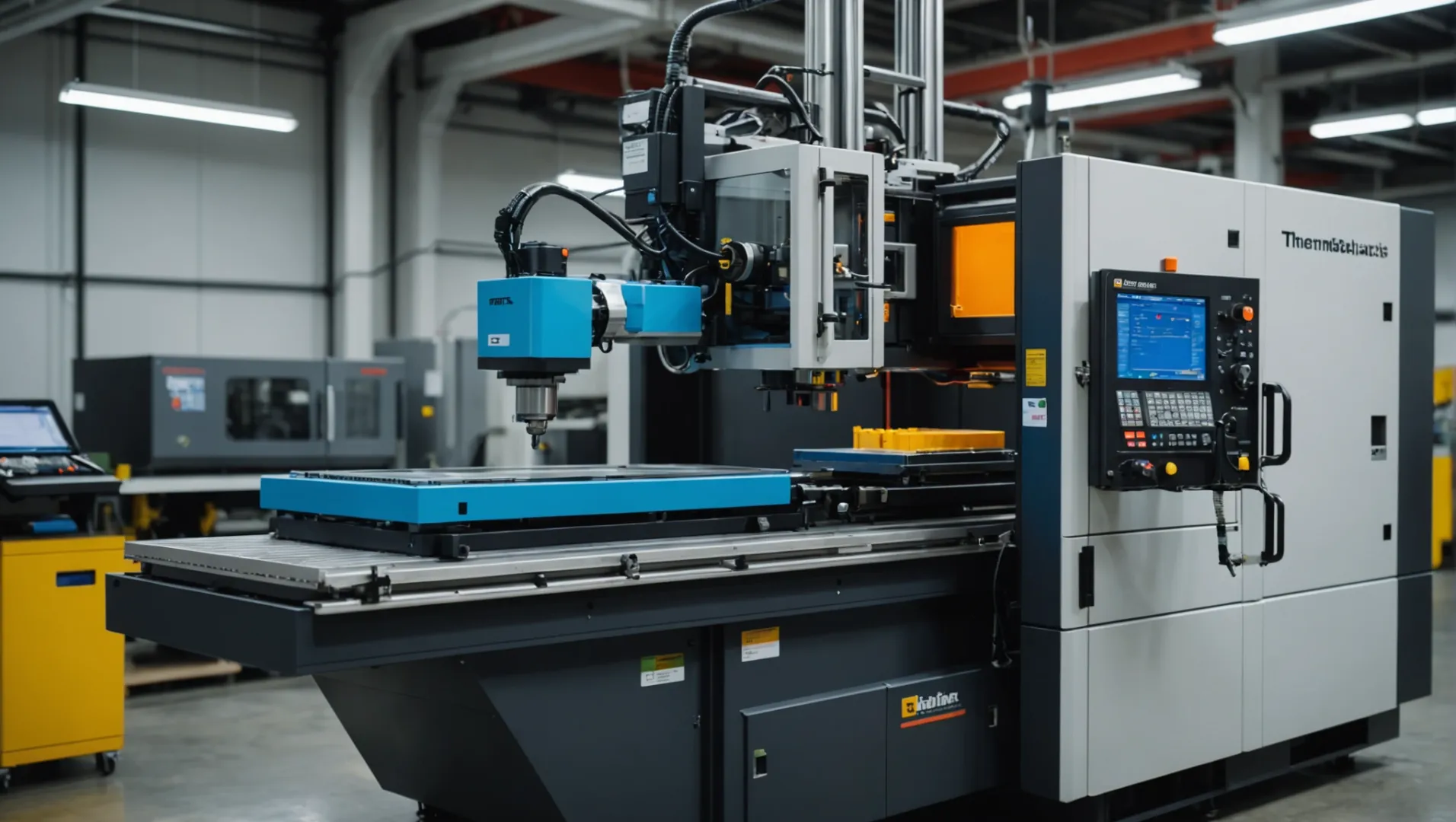
Thermoplastics: Flexibility and Recyclability
Thermoplastics dominate injection moulding due to their unique ability to be repeatedly softened and reshaped upon heating. This characteristic makes them ideal for applications where design modifications are frequent or when recycling is a priority.
-
Polyethylene (PE): Known for its chemical stability and resistance to low temperatures, PE is commonly used in consumer goods1 like plastic bags and bottles. Its versatility stems from the variety of densities available, enabling different mechanical properties.
-
Polypropylene (PP): As one of the lightest plastics with excellent heat resistance, PP finds extensive use in automotive interiors2 and food packaging. Its ability to withstand temperatures above 100°C without degrading makes it a staple in many industrial applications.
Thermoplastics also boast ease of processing, which reduces production time and costs, making them highly desirable for high-volume manufacturing scenarios.
Thermosetting Plastics: Strength and Durability
In contrast, thermosetting plastics offer unmatched strength and heat resistance. Once cured, these materials cannot be remelted, which provides a robustness that thermoplastics cannot match.
-
Phenolic Plastics: These are celebrated for their mechanical strength3 and electrical insulation properties. They are predominantly used in high-stress environments like automobile brake pads and electrical insulation parts.
-
Epoxy Resin: Offering excellent adhesion and chemical stability, epoxy resins are frequently employed in electronic packaging4 and coatings. The ability to modify their properties with fillers makes them incredibly versatile.
Thermosetting plastics typically offer longer-lasting solutions for products that require higher structural integrity or operate in harsh conditions.
Comparing Performance Characteristics
Feature | Thermoplastics | Thermosetting Plastics |
---|---|---|
Recyclability | High | Low |
Design Flexibility | High | Low |
Heat Resistance | Moderate | High |
Durability | Moderate | High |
Initial Production Cost | Lower | Higher |
When deciding between these materials, it is crucial to consider the end-use requirements of the product. For projects demanding frequent design iterations or eco-friendly solutions, thermoplastics are preferable. Conversely, for applications necessitating superior strength and thermal stability, thermosetting plastics are more suitable.
Thermoplastics can be remolded multiple times.True
Thermoplastics soften upon heating, allowing reshaping.
Thermosetting plastics are easily recyclable.False
Once set, thermosetting plastics cannot be remelted.
What Factors Should You Consider When Choosing an Injection Moulding Material?
Selecting the right injection moulding material can make or break your product’s success.
Consider factors like mechanical properties, cost, environmental impact, and application requirements when choosing an injection moulding material. Each material offers distinct characteristics that influence the final product’s performance and suitability for specific uses.
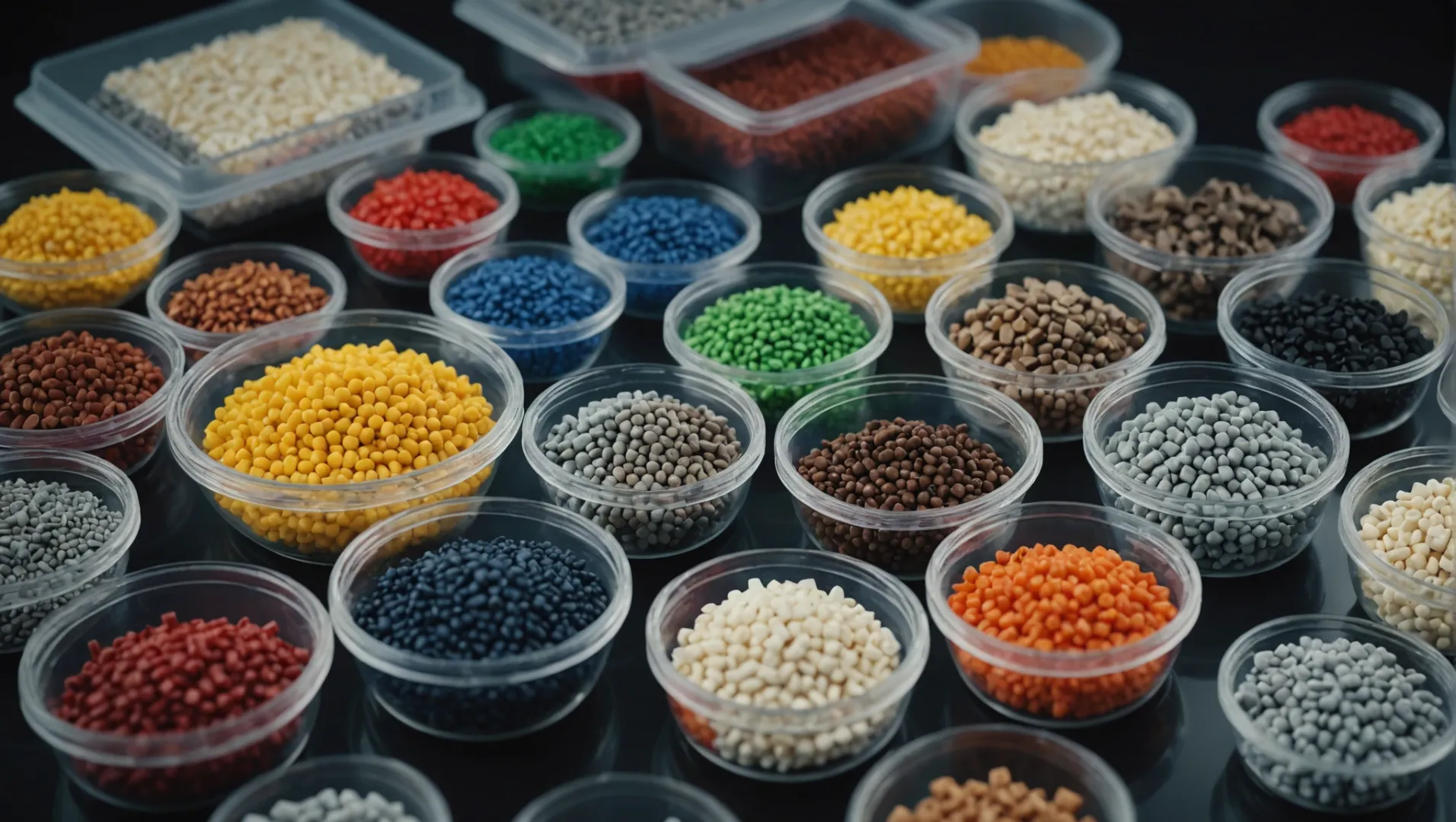
Mechanical Properties
Understanding the mechanical properties5 of materials is crucial. For instance, if you’re designing a product that requires flexibility, thermoplastics like polyethylene (PE) might be ideal due to their good low temperature resistance and softness. However, if strength and rigidity are more critical, consider high-density polyethylene or acrylonitrile-butadiene-styrene (ABS), known for its toughness and high surface hardness.
Cost Considerations
Budget constraints often guide material selection. While polyethylene is generally cost-effective, materials like polycarbonate (PC) might incur higher costs due to their enhanced properties such as high transparency and impact resistance. Balancing cost with performance needs can help optimize your design without overspending.
Material | Average Cost per kg | Key Properties |
---|---|---|
Polyethylene | $1 – $2 | Flexibility, chemical stability |
Polycarbonate | $3 – $5 | High strength, transparency |
ABS | $2 – $3 | Toughness, heat resistance |
Application Requirements
The intended application dictates the choice of material. For automotive parts requiring high heat resistance, polypropylene (PP) is suitable due to its ability to withstand temperatures above 100°C. Conversely, for electrical components necessitating excellent insulation, phenolic plastics offer high mechanical strength and electrical insulation.
Environmental Impact
Sustainability is increasingly vital in material selection. Evaluate the environmental impact6 of your choice by considering factors such as recyclability and biodegradability. Thermoplastics are often recyclable, making them a preferred choice for eco-conscious projects. Moreover, advances in biodegradable plastics offer alternatives that reduce environmental footprints.
Regulatory Compliance
Ensure materials meet industry regulations and standards. For instance, food packaging applications require materials with FDA approval, such as certain grades of polypropylene. Thoroughly review regulatory guidelines relevant to your industry to avoid legal complications.
By weighing these factors, you can make informed decisions that align with both your project requirements and broader business goals.
Polyethylene is ideal for products needing flexibility.True
PE offers good low temperature resistance and softness, ideal for flexibility.
Polycarbonate is the cheapest injection moulding material.False
Polycarbonate costs $3-$5 per kg, more expensive than polyethylene.
How Do Material Properties Influence Product Design in Injection Moulding?
Material properties dictate how injection moulded products perform, influencing design decisions profoundly.
Material properties such as strength, flexibility, and thermal resistance play a crucial role in product design during injection moulding. Selecting the right material ensures the final product meets functional requirements while remaining cost-effective. This selection impacts durability, appearance, and overall performance.
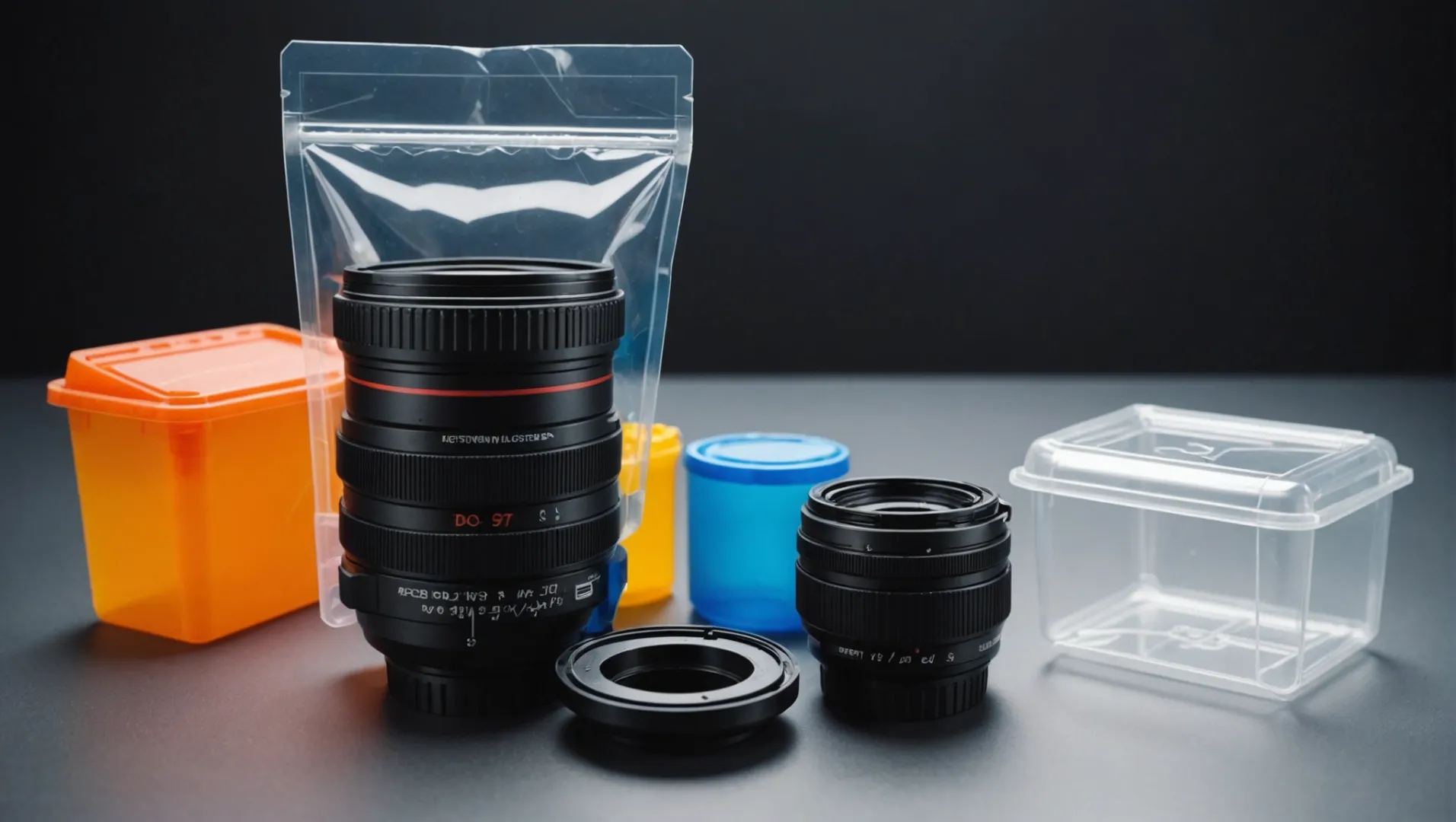
The Role of Material Strength and Durability
When designing products through injection moulding, understanding the material’s strength7 is crucial. High-strength materials like Polycarbonate (PC) are preferred for applications requiring impact resistance, such as automotive parts and electronic housings. Conversely, materials with moderate strength but high flexibility, like Polyethylene (PE), are suitable for everyday items like plastic bags or films.
Table 1: Strength Comparison of Common Injection Moulding Materials
Material | Tensile Strength (MPa) | Application Example |
---|---|---|
Polycarbonate | 60-70 | Optical lenses, lampshades |
Polyethylene | 20-30 | Plastic bags, containers |
ABS | 40-50 | Automotive parts, toys |
Flexibility and Thermal Resistance in Design
Flexibility is another critical factor. Polypropylene (PP), known for its low density and high heat resistance, is frequently used in food packaging and automotive interiors due to its ability to withstand temperatures over 100°C without deforming. In contrast, Polyvinyl Chloride (PVC) offers flexibility in its soft form and rigidity in its hard form, making it versatile for various designs from cables to pipes.
The thermal properties of materials also dictate their suitability for certain environments. For instance, phenolic plastics used in electrical insulation must endure high heat levels without degrading.
Aesthetic and Surface Finish Considerations
Surface finish and aesthetic appeal often influence material choice. Acrylonitrile-butadiene-styrene (ABS) is favored for its excellent surface hardness and ease of painting, making it ideal for consumer electronics with glossy finishes.
Furthermore, material transparency is a design consideration; materials like Polystyrene (PS) and PC offer high transparency, making them suitable for products like clear packaging and lenses.
In summary, selecting the right material based on its properties is paramount in ensuring the product not only meets functional requirements but also aligns with aesthetic goals and cost considerations. By analyzing factors like strength, flexibility, thermal resistance, and surface finish, designers can optimize their injection moulding projects for success.
Polycarbonate is used for optical lenses.True
Polycarbonate's high strength makes it ideal for optical lenses.
Polyethylene is preferred for high-impact applications.False
Polyethylene is used for flexible items, not high-impact needs.
What Are the Environmental Impacts of Different Injection Moulding Materials?
Injection moulding materials vary in their environmental impact, affecting sustainability and carbon footprint.
The environmental impact of injection moulding materials hinges on factors like recyclability, biodegradability, and energy consumption during production. Thermoplastics generally offer better recyclability, while thermosetting plastics often require more energy and resources, leading to a higher environmental footprint. Understanding these impacts aids in making eco-friendly material choices.
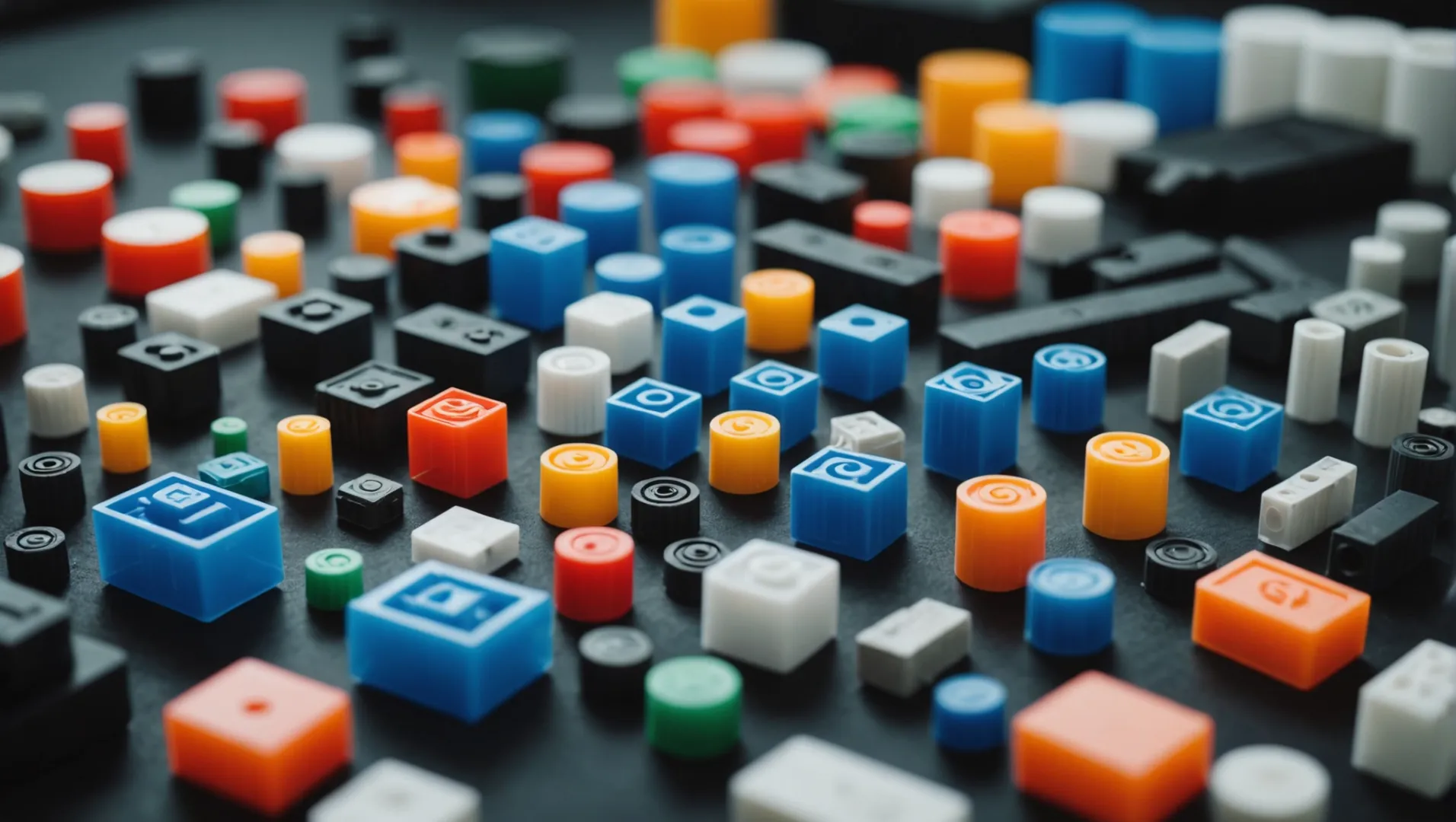
Thermoplastics: A Recyclable Option?
Thermoplastics such as polyethylene8 (PE) and polypropylene (PP) are often praised for their recyclability. These materials can be melted down and reshaped multiple times, reducing waste in manufacturing processes. For instance, polyethylene’s wide usage in daily necessities like plastic bags and bottles makes its recyclability crucial for minimizing plastic waste.
However, despite their recyclability, thermoplastics have challenges. The recycling process can degrade the quality of the material over time, limiting its reuse potential. Moreover, the actual recycling rates depend significantly on local recycling facilities and consumer participation.
Thermosetting Plastics: Environmental Challenges
Unlike thermoplastics, thermosetting plastics such as phenolic plastics and epoxy resin are not recyclable. Once cured, they cannot be remelted or reshaped, which poses a significant environmental challenge. The production and disposal of thermosetting plastics require careful consideration due to their permanence.
The environmental impact is further amplified by the energy-intensive processes involved in producing thermosetting plastics. This results in higher carbon emissions compared to their thermoplastic counterparts.
Biodegradability and Alternatives
As industries strive for sustainability, biodegradable alternatives to conventional injection moulding materials are gaining traction. Bioplastics, made from renewable resources like cornstarch, offer a promising solution to reduce the environmental footprint. However, these materials are not without drawbacks. Their performance may not match traditional plastics in terms of durability and heat resistance.
Energy Consumption and Lifecycle Analysis
An important aspect to consider is the energy consumption involved in the lifecycle of injection moulding materials—from raw material extraction to production, usage, and disposal. Lifecycle analysis helps identify the most sustainable options by assessing the total environmental impact over a product’s life.
Conclusion
Understanding the environmental impacts of different injection moulding materials is crucial for making informed decisions that balance performance with sustainability. As technology evolves, the industry may see more efficient recycling methods and biodegradable alternatives that could revolutionize sustainable manufacturing practices.
Thermoplastics are always more sustainable than thermosetting plastics.False
While often more recyclable, thermoplastics' sustainability depends on various factors.
Bioplastics offer a completely sustainable alternative to conventional plastics.False
Bioplastics have limitations in durability and heat resistance, affecting sustainability.
Conclusion
Choosing the right injection moulding material is essential for success. Reflect on your project’s needs to select materials that balance performance and cost.
-
Discover the versatility of polyethylene in everyday products.: Its resistance to contamination and precise engineering capabilities make it perfect for items such as medicinal containers, syringes, and … ↩
-
Learn why polypropylene is favored in car interiors.: In the automotive industry, PP’s commonly used for bumpers, chemical tanks, cable insulation, and gas cans. Polypropylene is also often utilized … ↩
-
Explore the robust applications of phenolic plastics.: Suited for support components in a wide range of mechanical and electrical applications because they resist corrosion and provide electrical insulation. … ↩
-
Uncover how epoxy resin protects electronic components.: Epoxy resins are the main component of durable epoxy compounds used in semiconductor packaging assemblies. Therefore, the properties of the … ↩
-
Explore detailed mechanical properties to enhance product design.: Tough, stiff, hard, and strong. Good lubricity and resistance to hydrocarbons and organic solvents. Good elasticity, slippery. Low creep. Great fatigue … ↩
-
Understand the sustainability and recyclability of various materials.: The most common type of material used in injection moulding is plastic, and plastic production is a major source of air pollution. ↩
-
Explore material strength differences to make informed design choices.: Comparing Injection Molding Materials. Tough, stiff, hard, and strong. Good lubricity and resistance to hydrocarbons and organic solvents. ↩
-
Explore how polyethylene’s recyclability impacts sustainability efforts.: When PE products are recycled, they can have a positive environmental impact. Instead of turning into plastic waste that fills up landfills, … ↩