Are you looking to improve your understanding of the injection molding process? Let’s explore it in detail together!
Key factors influencing injection molding include material selection, mold design, process parameter control, and quality monitoring. Mastery of these aspects enhances production efficiency and ensures high-quality products.
I spent years in the mold design industry. Understanding key factors in injection molding is essential. Every detail matters, from choosing the right plastic to designing high-quality molds. I remember my first struggle with mold design. It was really challenging. I learned the importance of these elements.
This blog post explores these factors in detail. It offers insights and practical tips. These tips improve your injection molding processes. Product designers and manufacturing engineers will find valuable information. You will probably achieve better results.
Plastic raw material selection is crucial for injection molding success.True
The choice of plastic raw materials directly affects the quality and efficiency of the injection molding process.
Quality monitoring is unnecessary in the injection molding process.False
Continuous quality monitoring during production is essential to ensure high-quality products and minimize defects.
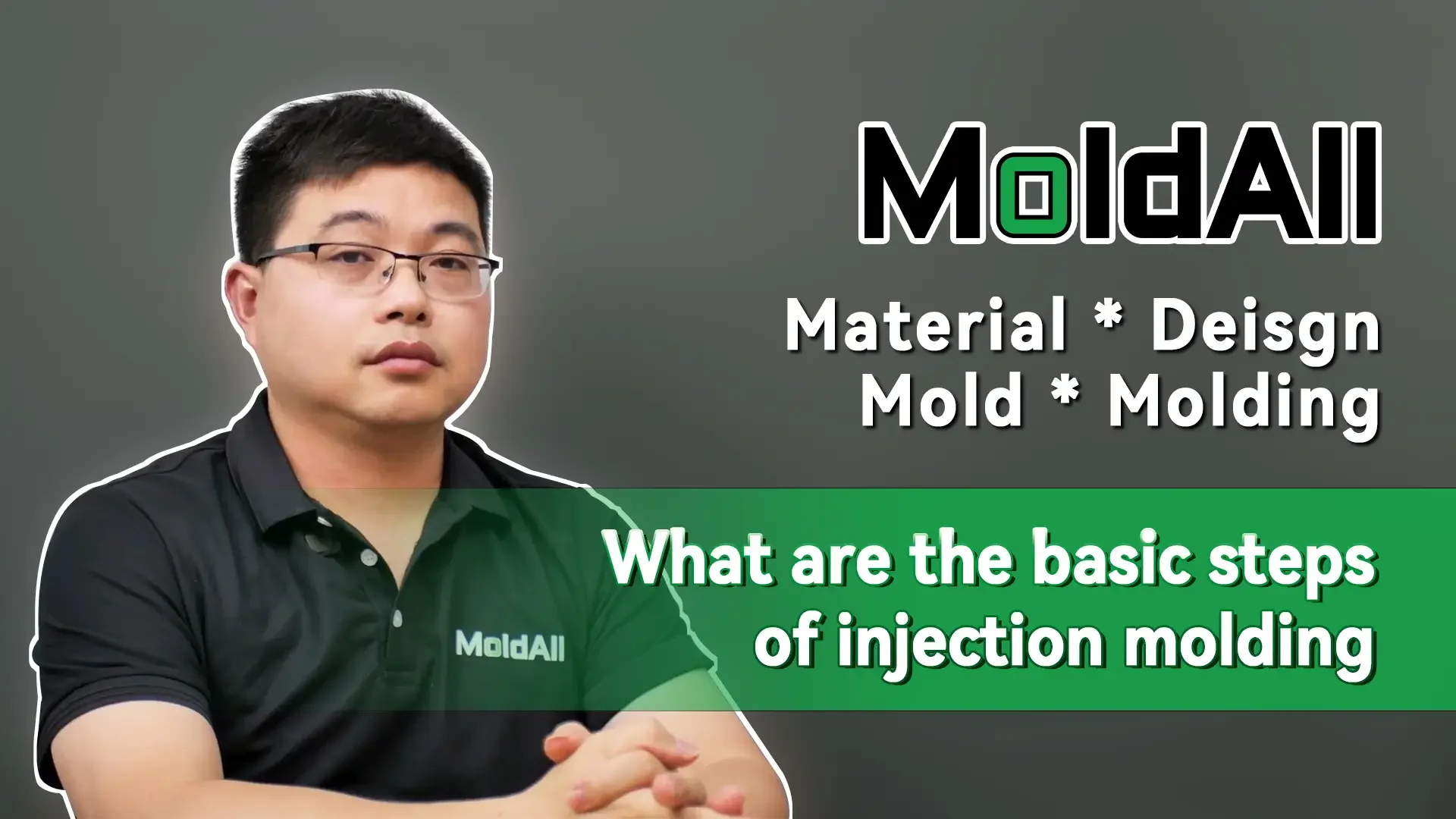
- 1. Why is raw material selection crucial in injection molding?
- 2. How does mold quality affect the final product?
- 3. Why are process parameters critical in injection molding?
- 4. What techniques can I use for effective quality monitoring during production?
- 5. How can I make adjustments during the molding process to improve product quality?
- 6. Conclusion
Why is raw material selection crucial in injection molding?
Do you ever think about how picking different materials changes the results of injection molding? Let’s look closely at this topic!
Selecting the right raw materials in injection molding is crucial for ensuring product quality, durability, functionality, cost-effectiveness, and efficient production.
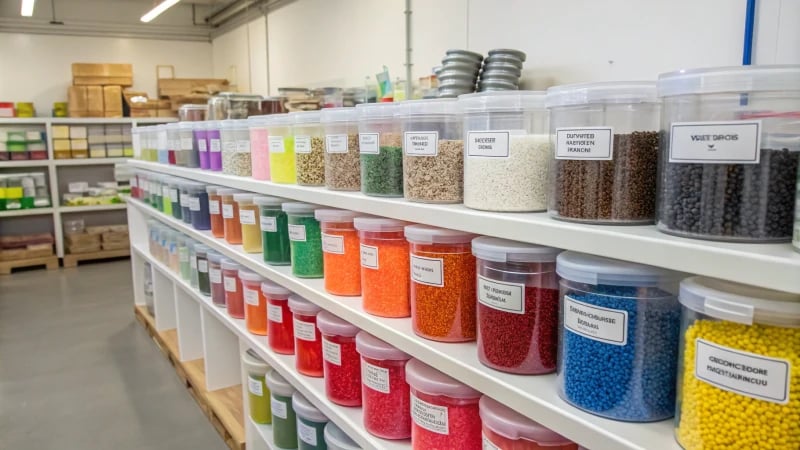
Importance of Raw Material Selection
When I entered the world of injection molding, I learned quickly that choosing raw materials is essential. It is vital for the entire process. The right choice decides how a product performs. It also affects how cost-effective and efficient production is.
Selecting the right plastic raw materials is essential based on the intended use of the product. Different types of plastics offer varied physical properties, such as strength and toughness, and chemical properties like corrosion resistance. For example, when I worked on designing a strong plastic toy, I chose polyethylene (PE) or polypropylene (PP). Their strength is perfect for handling kids’ rough play. Conversely, for items needing clear appearance – like optical lenses – I found polymethyl methacrylate (PMMA) best due to its crystal-clear transparency.
Cost Considerations
Budget is always important. When selecting raw materials, cost is a significant factor. While high-performance plastics like polyetheretherketone (PEEK) offer great qualities but are expensive, finding the point where performance and affordability meet is crucial. Here’s how I break it down:
Material Type | Cost | Typical Use Cases |
---|---|---|
Polyethylene (PE) | Low | Toys, packaging |
Polypropylene (PP) | Low | Automotive parts, household goods |
Polymethyl Methacrylate (PMMA) | Moderate | Optical lenses, signage |
Polyetheretherketone (PEEK) | High | Aerospace components, medical devices |
Processing Needs
I discovered many plastics can absorb moisture. Nylon (PA) is an example. Many plastic raw materials are hygroscopic; they absorb moisture from the air. I remember once forgetting to dry nylon before molding my product had bubbles! It was disappointing! So now, I always dry PA6 at 80-100℃ for about 8-12 hours.
Adding colorants or other additions to plastic may be necessary to give personality to the plastic! Whether it brings about certain characteristics or just the right color, these additions can greatly impact the final product.
Impacts on Mold Design and Quality
Raw material choice also affects mold design and quality. The choice of raw material also affects mold design and quality; dimensional accuracy relies on plastic properties. High-quality molds are key for keeping tight tolerances in applications like electronics.
To get the best results, I consider:
- The material’s flow during filling.
- Thermal qualities affecting cooling rates.
- Pressure and speed reaction during injection.
Understanding these elements helps me design molds for specific behaviors, improving product quality.
Conclusion Without a Conclusion
Although I can’t cover everything here, it’s evident that choosing raw materials in injection molding is a complex task. Each decision greatly impacts product performance, cost management and overall manufacturing success. If interested in learning more, I suggest looking into advanced material selection techniques1 or best practices in injection molding2.
Raw material selection affects injection molding efficiency.True
Choosing the right raw materials enhances production efficiency, impacting overall manufacturing success and product quality in injection molding processes.
High-performance plastics are always cost-effective.False
While high-performance plastics offer superior qualities, their higher costs may not always align with budget constraints, making them less cost-effective in some cases.
How does mold quality affect the final product?
Do you ever think about how the quality of a mold affects a product? It is very interesting to explore plastic injection molding. Every small detail matters and influences the final outcome.
Mold quality crucially influences injection-molded products’ size, appearance, and durability. High-quality molds ensure precise measurements, enhanced surface finish, and potentially greater longevity.
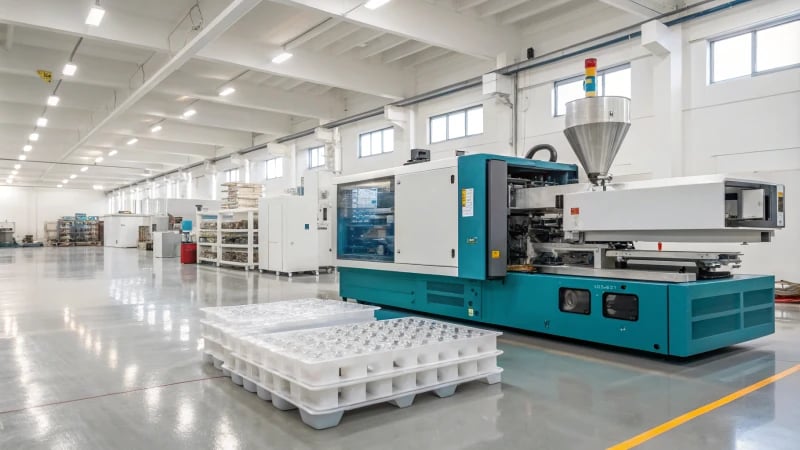
Understanding the Importance of Mold Quality
Mold quality is not just a detail; it’s the core of plastic molding. High-quality molds help products look good and work well. For example, in an automotive project, precision was crucial. Molds that keep tight tolerances, like ±0.01-±0.05mm, mean the difference between a perfect part and one that fails safety tests.
Material Selection for Molds
Picking the right mold material feels like finding the perfect recipe. I remember choosing H13 steel for high-volume production. Its durability and thermal stability suited repeated cycles perfectly. This choice greatly extended mold life and cut down maintenance.
Mold Material | Characteristics | Applications |
---|---|---|
H13 Steel | High hardness, wear-resistant, thermal stability | High-volume production |
P20 Steel | Moderate hardness, good machinability | General purpose molds |
S7 Steel | Shock-resistant | Heavy-duty applications |
Design Aspects of Molds
Mold design brings creativity and function together. I learned this when a poorly placed parting line ruined a product’s look. Design affects both manufacturing and product appearance. Cooling systems also matter; efficient cooling helps cut warping and improves surface quality. I have seen this in projects.
Injection Process Parameters
Mold quality continues into injection parameters. I recall adjusting barrel temperatures for polystyrene (PS). Getting it right at 180-220℃ ensured good melting and fluidity. This precision led to products that met expectations.
Monitoring and Adjusting Quality
Quality checks are ongoing. Once, we used automated inspection to catch defects in real-time. It was like having a sharp-eyed friend who spots errors early. Adjusting based on these insights greatly improved our product quality and reduced waste.
In summary, understanding mold quality means recognizing its key role in product durability, precision, and appearance. Exploring these elements allowed me to create products that meet and exceed market needs.
For further insights into improving mold quality, explore these resources:
High-quality molds ensure better surface finish in products.True
The surface quality of molded parts improves significantly with high-quality molds, leading to enhanced aesthetic appeal and reduced finishing work.
Mold material choice does not affect mold lifespan.False
The material selected for molds directly influences their durability and longevity, impacting production efficiency and costs.
Why are process parameters critical in injection molding?
Have you ever thought about how the smallest changes in manufacturing cause very different results? Injection molding depends a lot on knowing process parameters. These parameters are really important. They help produce high-quality products. They also help increase efficiency in production.
Controlling temperature, pressure, and speed in injection molding is crucial for ensuring product quality, reducing defects, and enhancing production efficiency.
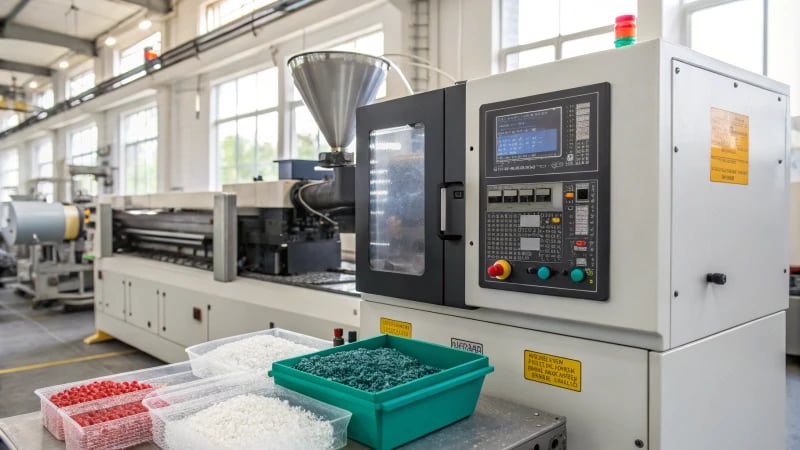
The Role of Temperature Control
Temperature is crucial in injection molding. It can truly affect your final product.
Barrel Temperature
Imagine watching plastic change before your eyes! Each plastic type has a specific melting point. Setting the right barrel temperature is essential. For instance, Polystyrene (PS) requires a front barrel temperature of 180-220°C. When we got it right, the melt flowed smoothly, creating perfect products. But if the temperature drops too low, the melt becomes sluggish, like cold syrup.
Mold Temperature
Changing mold temperature also enhances product quality. With Polycarbonate (PC), raising the mold temperature to 80-120°C reduced stresses and improved transparency. It felt satisfying to see these changes result in better products.
Importance of Pressure Control
Pressure control is like magic – it pushes molten plastic into the mold.
Injection Pressure
Setting injection pressure is tricky. Low pressure leads to incomplete fills. High pressure causes defects like flash. For thin-walled parts, high injection pressure is crucial since these molds cool fast.
Product Type | Recommended Injection Pressure |
---|---|
Thin-walled parts | High pressure required |
Complex shapes | Moderate to high pressure |
Holding Pressure
Holding pressure ensures uniform density. Adjusting holding times for product thickness really impacts quality. It’s impressive to see how much control we have!
The Significance of Speed Control
Speed greatly influences how the product turns out.
Injection Speed
Fast injection speeds suit detailed designs. They let the melt fill cavities quickly without solidifying. Seeing a perfect product without marks or bubbles is exciting – like art!
Mold Opening and Closing Speed
Mold speed matters too. Quick opening and closing can cause vibrations, affecting mold strength. Experience taught me this lesson!
Continuous Monitoring and Adjustment
Consistent monitoring during injection molding is crucial.
Quality Checks
Both manual and automated checks help maintain product quality. Finding defects early saves problems later. Automated systems are great for detecting tiny surface defects.
Process Parameter Adjustment
Observations require adjustments. For instance, if we see bubbles, increasing barrel temperature or reducing injection speed often solves the issue. Responsiveness is key.
By focusing on these process parameters and monitoring them closely, I’ve witnessed how they greatly improve product quality and manufacturing efficiency. Whether you’re starting out or refining your skills, remember each detail counts in the intricate dance of injection molding!
Temperature control is crucial for injection molding success.True
Proper temperature management prevents incomplete melting or material degradation, ensuring optimal product quality during the injection molding process.
High injection pressure is unnecessary for all product types.True
Different products require varying injection pressures; thin-walled parts need higher pressure to fill molds effectively, while others may not.
What techniques can I use for effective quality monitoring during production?
Have you ever wondered how every product that leaves the production line becomes the best it can be? Let’s explore methods that really change your quality checking process. These methods probably improve both dependability and efficiency.
Ensure effective quality monitoring in production with real-time monitoring, statistical process control, and automated
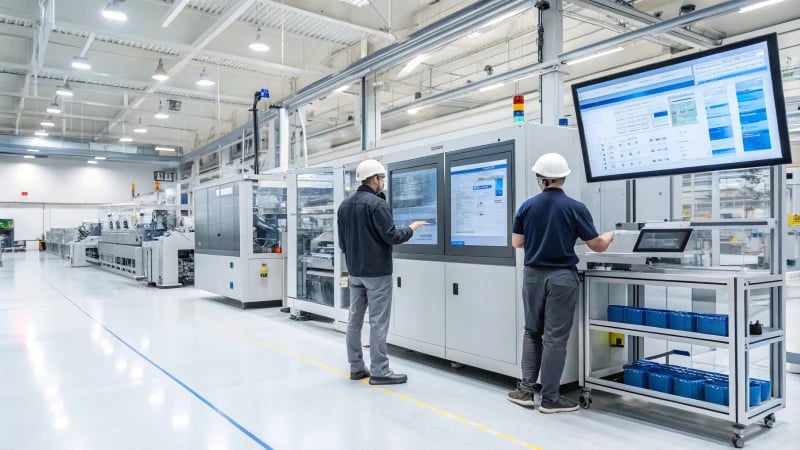
Techniques for Quality Monitoring During Production
Quality monitoring during production is essential for maintaining high standards and ensuring that the final product meets specifications. Various techniques can be employed to monitor quality effectively, ranging from manual inspections to sophisticated automated systems.
Real-Time Monitoring
Real-time monitoring involves tracking quality parameters as they happen in the production line. This can include:
- Appearance Quality Checks: Inspecting products for surface defects like bubbles or flow marks using automated optical inspection5. I recall when I first used automated optical inspections. They spotted surface problems early. This was a big change.
- Dimensional Accuracy Measurements: Utilizing precision measurement tools or robots to ensure product dimensions meet strict tolerances. For example, dimensional checks can be performed using laser measurement systems. I often used laser measurement systems which gave precise results that manual methods couldn’t reach.
Manual Inspection vs. Automated Systems
Both manual and automated inspection techniques have their advantages and limitations:
Method | Advantages | Limitations |
---|---|---|
Manual Inspection | Human judgment can detect subtle defects. | Time-consuming and prone to human error. |
Automated Systems | Fast and consistent measurements with high accuracy. | Initial setup costs can be high, and maintenance is required. |
Automated systems can leverage technology to quickly assess the quality of products in real-time. For instance, machine vision systems6 can scan products at high speeds and detect anomalies that might be missed by the human eye.
Statistical Process Control (SPC)
SPC involves using statistical methods to monitor and control production processes. Key components include:
- Control Charts: These charts help visualize data over time and identify trends or outliers. By analyzing control charts, manufacturers can make informed decisions about process adjustments before defects occur.
- Process Capability Analysis: This technique assesses how well a process can produce products within specified limits. It helps in determining whether a process is stable and capable of producing quality outputs consistently.
Feedback Loops for Continuous Improvement
Establishing feedback loops is crucial for improving production quality. This involves:
- Collecting Data: Gather data from inspections and measurements regularly.
- Analyzing Results: Use data analytics to identify patterns or recurring issues.
- Implementing Changes: Based on the analysis, adjust processes, materials, or training to address identified problems.
- For instance, if defects are traced back to raw material inconsistencies, a reassessment of raw material suppliers may be necessary.
This continuous feedback mechanism allows manufacturers to adapt and improve their quality monitoring systems over time.
Training and Standard Operating Procedures (SOPs)
The effectiveness of quality monitoring heavily relies on the knowledge and skills of the workforce. Therefore:
- Training Programs: Regular training sessions ensure that employees understand the importance of quality monitoring techniques and how to apply them effectively.
- SOPs Development: Establishing clear standard operating procedures ensures that everyone follows consistent practices during production, minimizing variability in quality.
By integrating these techniques into production practices, companies can enhance their quality monitoring efforts, leading to better product outcomes and increased customer satisfaction.
Real-time monitoring improves production quality significantly.True
Real-time monitoring allows immediate detection of defects, leading to prompt corrections and enhanced overall product quality during production.
Manual inspection is faster than automated systems for quality checks.False
Automated systems provide faster and more consistent measurements compared to manual inspections, which are time-consuming and prone to human error.
How can I make adjustments during the molding process to improve product quality?
I have explored the details of product design thoroughly. Adjustments during the molding process are crucial. They bring very important changes. These changes really improve product quality. Let’s jump into how these tweaks lead to impressive results in product quality.
To enhance product quality in molding, optimize raw materials, refine mold design, adjust injection parameters, and use real-time quality monitoring to reduce defects and ensure consistency.
Selection and Processing of Plastic Raw Materials
The choice of plastic raw materials is crucial for product quality. When I began in this field, material selection was confusing. Each type has unique properties that really affect our designs. For example, Polyethylene (PE) is great for toys because of its toughness and durability. Polymethyl methacrylate (PMMA) is perfect for optical lenses due to its excellent transparency.
Also, cost is important! Balancing performance with budget often means using economical options like PE or PP without losing quality. Do not forget about raw material processing. Once, I neglected to dry nylon properly before molding, causing bubbles and ruining an entire batch! Drying at 80-100℃ for 8-12 hours is essential for preparing raw materials for molding.
Quality and Design of Injection Molds
The quality of molds is another critical area I appreciate deeply. A well-crafted mold ensures dimensional accuracy and improves the product’s appearance. In my early design days, I learned about tolerances and tight tolerances of ±0.01-±0.05mm are very important. Choosing durable mold steel, like H13 for high-volume production, is crucial for longevity.
Small design details, like gate or cooling system placement, can have a significant impact. A point gate reduces defects in thin-walled products by allowing even filling. Evenly distributed cooling channels are my secret weapon against warping and cycle time delays.
Control of Injection Molding Process Parameters
Let’s discuss process parameters. Adjustments here often lead to big improvements. Temperature and pressure control are game-changers! Setting the barrel temperature for polystyrene (PS) between 180-220℃ allows for optimal melting and flow. Adjusting the mold temperature can improve product toughness and transparency. With polycarbonate (PC) products, a higher mold temperature (80-120℃) did wonders!
Controlling injection speed is just as important. Rapid injection helps replicate intricate details in complex shapes perfectly.
Quality Monitoring and Adjustment During Injection Molding
Quality monitoring during the injection molding process is my safety net. Watching for defects like bubbles or flow marks allows for immediate adjustments before issues escalate. If bubbles appear, increasing the barrel temperature or reducing injection speed often solves the problem quickly.
Active quality monitoring has significantly optimized production processes. If interested in learning more about material selection or industry best practices, check out plastic material selection. Together, let’s continue pushing boundaries in product design and manufacturing!
With these adjustments, our work can go from good to exceptional. Proactivity and never settling for less than excellence are key!
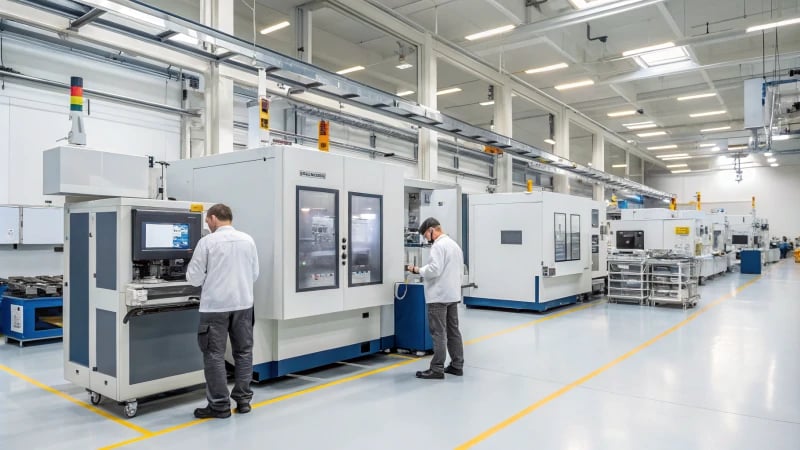
Adjustments During the Molding Process
Adjustments during the molding process resemble tuning a musical instrument. Each small change might lead to a better final product. Selecting the correct materials is crucial. Monitoring quality in real-time plays a big role. Every decision is important in reducing mistakes. Consistency is key. Precision and creativity are both needed. It’s a balancing act.
Adjustment Aspect | Importance |
---|---|
Material Selection | Critical for product performance |
Real-time Monitoring | Enables immediate corrective actions |
Decision Making | Reduces potential errors |
Additionally, cost factors should be carefully evaluated to maintain a balance between performance and budget. Using lower-cost plastics can be more economical without sacrificing quality.
Moreover, raw material processing plays a vital role in ensuring that adjustments lead to optimal outcomes.
Proper drying of nylon is essential to avoid product defects.True
Drying nylon at 80-100℃ for 8-12 hours prevents bubbles and defects, ensuring better quality in molded products.
High-quality molds ensure dimensional accuracy of final products.True
Using high-quality molds with tight tolerances improves the precision and appearance of the final molded items, enhancing overall product quality.
Conclusion
Explore key factors affecting injection molding: raw materials, mold design, process parameters, and quality monitoring for improved efficiency and product excellence.
-
Clicking this link will provide you with valuable insights into advanced material selection techniques that can enhance your understanding of injection molding processes. ↩
-
This link offers best practices in injection molding that are crucial for ensuring product quality and efficiency. ↩
-
Explore best practices in mold design that enhance product quality in injection molding. ↩
-
Learn about advanced techniques in injection molding that optimize mold performance. ↩
-
Explore various techniques that enhance quality monitoring during production, leading to improved product outcomes. ↩
-
Learn how SPC can optimize manufacturing processes and boost product quality. ↩