Imagine transforming a simple product into something extraordinary with just a touch of creativity and technique. That’s what overmolding does!
When designing molds for overmolding, prioritize material compatibility, mold precision, and process parameters to ensure the final product’s functionality and aesthetics, essential for project success.
Once I got the hang of these fundamental aspects, I realized how they formed the backbone of successful designs. But let me tell you, diving deeper into each factor was a game-changer for me. In this post, I’ll share insights and practical tips that have helped me master the art of overmolding.
Material compatibility is crucial in overmolding.True
Using compatible materials ensures proper bonding and product durability.
Mold design precision is not important in overmolding.False
Precision in mold design ensures accurate product dimensions and fit.

- 1. Why Is Material Compatibility Crucial in Overmolding?
- 2. How Does Mold Design Affect Overmolding Success?
- 3. How Can You Optimize Overmolding Parameters?
- 4. How can I address common challenges in overmolding applications?
- 5. How Do I Design Durable Overmolds?
- 6. How Can Overmolding Enhance Product Aesthetics and Functionality?
- 7. Conclusion
Why Is Material Compatibility Crucial in Overmolding?
I remember the first time I learned about overmolding—it’s like creating a puzzle where each piece has to fit perfectly with the next.
Material compatibility in overmolding is essential to prevent delamination and structural failure, ensuring proper bonding, desired mechanical properties, and aesthetic appeal in multi-material products.
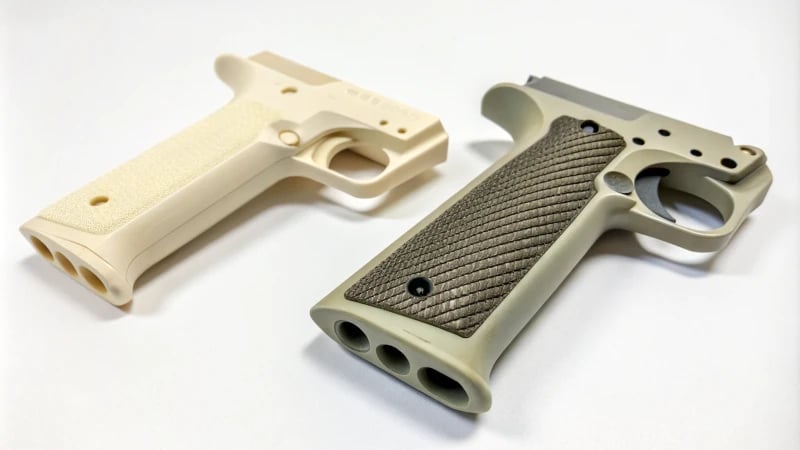
Understanding Overmolding and Its Applications
I still recall my first project that involved overmolding. It felt like a blend of art and science, layering different materials to create a single, cohesive part. Overmolding requires the precise selection of compatible materials1 to ensure everything comes together just right. This process is particularly popular in industries such as consumer electronics, automotive, and healthcare, where the stakes for quality and durability are incredibly high.
Industry | Typical Applications |
---|---|
Consumer Electronics | Smartphone covers, keypads |
Automotive | Steering wheels, dashboards |
Healthcare | Medical device handles |
Importance of Material Compatibility
I’ve learned through trial and error that material compatibility is not something you can overlook. It’s crucial for achieving optimal physical and chemical interactions between the layers. If you choose materials that don’t get along, you’ll run into problems like delamination or poor adhesion, which can be catastrophic.
Delamination Risks
There was a time when I overlooked the risk of delamination, thinking I could make incompatible materials work together. Well, nature had other plans! Incompatible materials often result in delamination, where layers separate under stress or environmental conditions, compromising the product’s structural integrity2.
Adhesion Challenges
Achieving proper adhesion is a delicate dance of evaluating material properties such as surface tension and chemical composition. I’ve learned that designers must carefully evaluate these factors to ensure that the overmolded product3 performs as expected.
Factors Influencing Compatibility
- Thermal Expansion: Different materials expand at different rates when heated. I remember one project where this led to unexpected warping; it was a valuable lesson in managing these differences.
- Chemical Resistance: Some materials may react negatively when combined, leading to degradation over time.
- Mechanical Properties: Factors like hardness, flexibility, and tensile strength must be compatible to maintain product durability.
Material compatibility goes beyond just matching colors or textures; it’s about ensuring longevity and performance in overmolded products. By understanding these nuances, designers can make informed decisions that enhance product quality and reliability.
Material Selection Tools
There are several tools available to assist in selecting compatible materials for overmolding:
- Material Databases: These comprehensive libraries with material properties have saved me countless hours of research.
- Simulation Software: Helps predict how different materials will interact under specific conditions.
- Industry Standards: Provide baseline compatibility data.
These resources can guide designers in navigating the complexities of material selection4, helping them create successful overmolded components. I’ve found that using these tools not only streamlines the design process but also boosts confidence that the final product will stand the test of time.
Incompatible materials in overmolding cause delamination.True
Delamination occurs when layers separate due to incompatible materials.
Material databases are irrelevant for overmolding.False
Material databases provide crucial data on material properties for compatibility.
How Does Mold Design Affect Overmolding Success?
Ever wondered why some overmolded products last longer and look better? The secret often lies in the mold design!
Successful overmolding requires precise mold design, emphasizing alignment, venting, and material compatibility to ensure strong bonding, minimize imperfections, and enhance product durability and appearance.
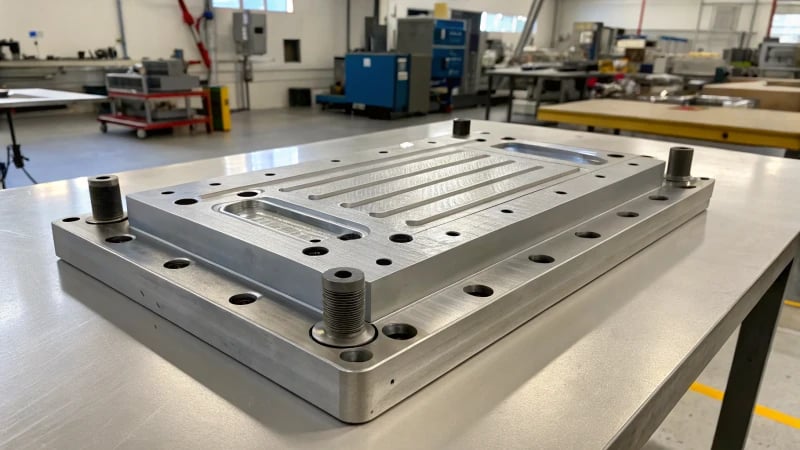
The Importance of Precise Alignment
I remember the first time I worked on an overmolding project. It felt like piecing together a complex puzzle, where every component had to fit just right. Achieving precise alignment5 between material layers was crucial. Misalignment can cause gaps or weak bonds, leading to product failures. It was a lesson learned early on—each mold part must be crafted with meticulous care to maintain its position during injection.
Optimal Venting for Quality
I once faced a challenge with voids in a batch of overmolded electronics cases. It turned out that improper venting was trapping air inside, causing defects. Venting allows gases to escape during molding, preventing such issues. By placing vents strategically, like along edges or near joint interfaces, we significantly improved product quality.
A table illustrating typical vent placement for common overmolding applications can be beneficial:
Application | Vent Placement |
---|---|
Electronics Cases | Along edges and corners |
Handles | Near joint interfaces |
Gaskets | Throughout surface |
Material Compatibility Considerations
Choosing the right materials can feel like matchmaking in the overmolding process. The primary and secondary materials must adhere well, akin to finding two puzzle pieces that fit perfectly. Ensuring matching thermal expansion coefficients and chemical compatibility is key to avoiding peeling or cracking. Understanding material properties6 guided me in selecting combinations that enhanced longevity and performance.
Utilizing Advanced CAD for Mold Design
Modern CAD tools have become my go-to for simulating overmolding processes before production. These tools help visualize potential issues like shrinkage or stress points, allowing for adjustments early in the design stage. Incorporating these advanced techniques7 has not only saved costs but also improved product outcomes significantly.
Reflecting on my journey, it’s clear that mold design isn’t just about technical specifications—it’s about crafting each element with care to ensure every product emerges as a success story.
Precise alignment prevents overmolding defects.True
Misalignment can cause gaps and weak bonds, leading to product failures.
Venting is unnecessary for high-quality overmolding.False
Venting allows air to escape, preventing defects like voids or incomplete filling.
How Can You Optimize Overmolding Parameters?
Ever felt like you’re juggling a dozen spinning plates, trying to perfect an overmolding process? Trust me, I’ve been there, and it’s all about nailing those parameters to keep everything in balance.
Optimize overmolding by adjusting mold temperature, injection pressure, and cycle time to ensure strong material bonding and high-quality products, crucial for successful manufacturing.
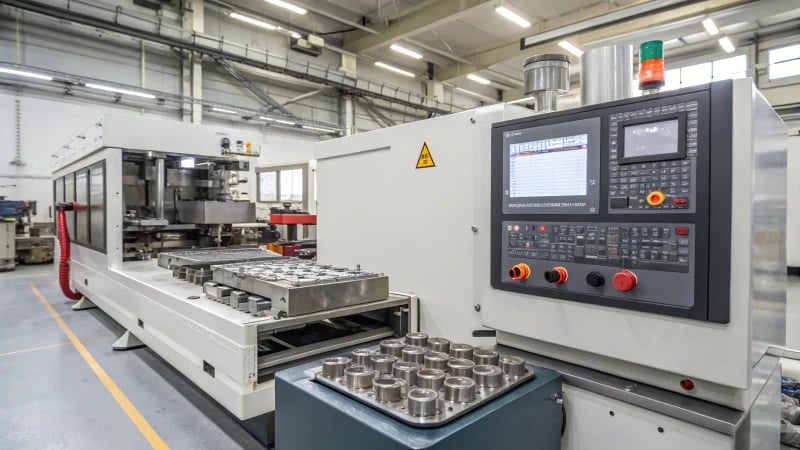
Understanding Key Overmolding Parameters
I remember the first time I got my hands on an overmolding project—it felt like solving a complex puzzle. Every piece had to fit perfectly, or the whole thing would fall apart. Overmolding is a bit like that; it’s a complex dance where every move—every parameter—needs to be just right to ensure the final product is both durable and high-quality.
Mold Temperature
Mold temperature is where it all begins. It’s like setting the oven to the perfect temperature for baking bread. Too low, and you’re left with a loaf that’s raw in the middle. Too high, and you end up with a burnt crust. Similarly, the right mold temperature8 ensures your materials flow and bond just right.
Parameter | Optimal Range |
---|---|
Mold Temperature | 80°C – 120°C |
I’ve found that staying within this range works wonders for adhesion without risking degradation.
Injection Pressure
The first time I adjusted injection pressure felt like tuning a guitar—you just know when you hit the right note. Injection pressure controls how well the material fills the mold. It’s about finding that sweet spot: enough pressure for details but not so much that it blows everything out of proportion.
Cycle Time
Cycle time is like the rhythm of production. Too fast, and you’re rushing through things, risking mistakes. Too slow, and you’re wasting precious time. Balancing cycle time is crucial for productivity and energy efficiency. It’s a delicate dance, but once you get into the groove, it feels incredibly rewarding.
Material Selection
Choosing materials for overmolding is like selecting the right ingredients for a recipe—each one can drastically affect the outcome. Thermoplastic elastomers (TPEs) have become my go-to because they offer flexibility and excellent adhesion properties. Each material behaves differently under various conditions, so understanding these nuances is key.
Best Practices in Overmolding
- Preheat Inserts: Think of it like warming up before a run; preheating reduces thermal shock and improves bonding.
- Optimize Cooling Rates: Just as cooling cookies prevents them from crumbling, proper cooling in overmolding reduces warping and improves accuracy.
- Test Iteratively: Before diving headfirst into full-scale production, I always run small-scale tests to iron out any kinks in settings.
Embracing these best practices9 has transformed my workflow. It’s about creating harmony between all these factors, ensuring each one supports the other for optimal results. Whether you’re troubleshooting a persistent issue or just looking to sharpen your skills, a holistic approach to parameter optimization can make all the difference.
Mold temperature should be between 80°C and 120°C for overmolding.True
This range ensures proper material flow and bonding without degradation.
Higher injection pressure is always better for overmolding details.False
While higher pressure aids detail, it may not suit all designs or materials.
How can I address common challenges in overmolding applications?
I remember the first time I tackled an overmolding project, and I was amazed by the combination of aesthetics and functionality it promised. But boy, did it come with its own set of challenges!
Addressing overmolding challenges involves ensuring material compatibility, precise mold design, and process optimization to improve product quality and reduce manufacturing issues.
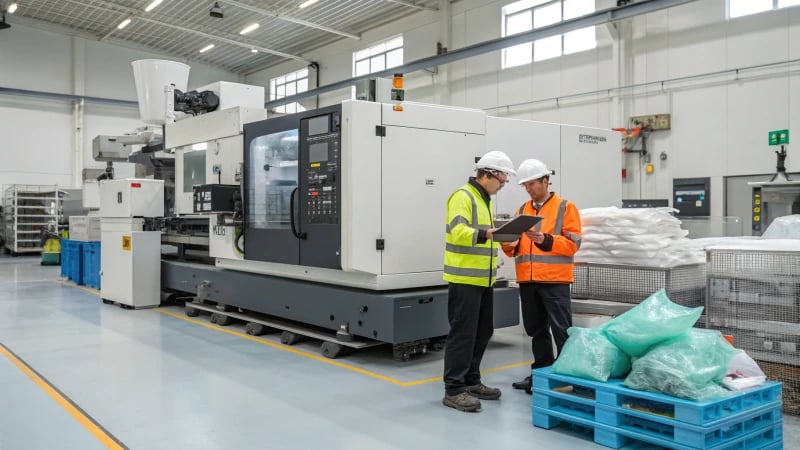
Material Compatibility
One of my early experiences with overmolding10 involved a project where the materials simply didn’t play nice together. I learned the hard way that choosing compatible materials is crucial. Imagine pairing a peanut butter base with a jelly overmold—it sounds delicious, but not every combination is as complementary in manufacturing. Using a compatibility chart has become a staple in my process, and here’s a quick reference:
Base Material | Overmold Material | Compatibility |
---|---|---|
ABS | TPE | High |
PC | Silicone | Medium |
Nylon | PVC | Low |
Diving into these details can be the difference between a seamless integration and a sticky mess.
Precision Mold Design
When it comes to precision mold design, I remember a project where we had an unexpected air trap issue. It taught me the importance of designing molds that accommodate both base and overmold materials perfectly. Proper venting, gating, and wall thickness are non-negotiables to prevent defects like air traps or weak bonding. These days, I swear by advanced CAD software to refine these designs efficiently. If you’re curious about more CAD techniques11 for intricate designs, it’s worth exploring.
Process Optimization
Optimizing the overmolding process is a bit like fine-tuning a recipe—everything from temperature to pressure has to be just right. Early on, I faced issues with inconsistent quality due to improper settings. Conducting thorough testing and simulations became my go-to strategy to achieve the best results. Regular maintenance of machinery also proved essential in avoiding unexpected downtimes. For tips on keeping your machinery in top shape, check out these machinery maintenance tips12.
Moreover, implementing robust quality control measures ensures that each product meets the desired standards. Adopting automated inspection systems can be a game changer, catching defects before they spiral into bigger problems.
By honing in on these areas, I’ve found that many of the common hurdles in overmolding become much more manageable. The result? Smoother production cycles and products that meet the highest quality standards every time.
ABS and TPE have high compatibility in overmolding.True
ABS and TPE are listed as having high compatibility in the chart.
Precision mold design is not crucial for overmolding.False
Proper mold design is vital to prevent defects like air traps.
How Do I Design Durable Overmolds?
Ever wondered how to make overmolds that withstand the test of time?
Design durable overmolds by choosing compatible materials, designing stress-distributing molds, and ensuring strong layer adhesion to enhance product longevity and performance.
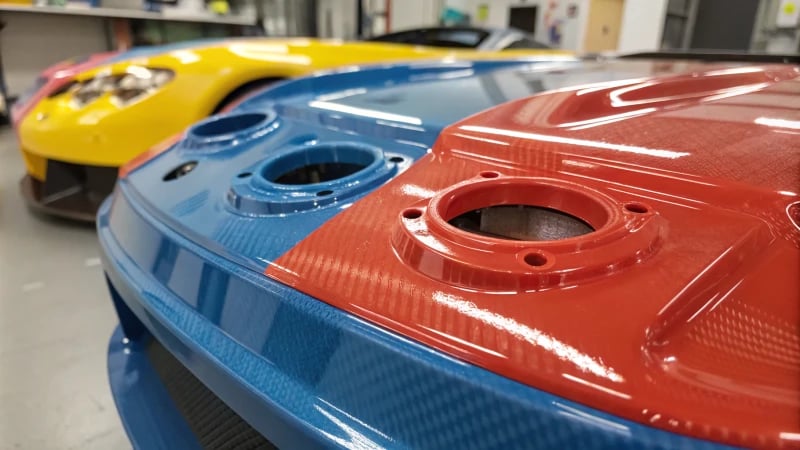
Material Selection
When it comes to material selection, I always start by considering the compatibility between the substrate and the overmold materials. It’s like finding the perfect dance partner—they need to move together without stepping on each other’s toes. A classic combo I often use is thermoplastic elastomers (TPE) over rigid plastics like ABS or polycarbonate. These pairings not only ensure good adhesion13 but also align their thermal expansion coefficients to avoid issues like delamination under stress.
Design Considerations
In my experience, optimizing mold design is crucial. I learned early on that sharp corners are the enemy—they can be stress concentration points waiting to cause trouble. Instead, I use fillets and ribs to spread out the stress, adding strength where it’s needed most. Once, I used finite element analysis (FEA)14 to simulate stress on a project before manufacturing, and it was a game-changer for enhancing durability.
Feature | Impact on Durability |
---|---|
Rounded edges | Reduces stress points |
Fillets | Increases strength |
Ribs | Adds support |
Adhesion Techniques
Strong adhesion is like the glue in a strong relationship—it holds everything together. I’ve found that techniques such as plasma treatment or priming can significantly improve surface energy and bonding. Before starting the molding process, I always ensure both surfaces are clean. Once, after a frustrating day of weak bonds, I started incorporating co-injection or insert molding processes, which improved adhesion properties15 considerably.
Process Control
Process control is where precision meets patience. Monitoring temperature, pressure, and curing times meticulously has saved me from many a headache. Using advanced sensors and IoT solutions for real-time monitoring can feel like having a personal assistant ensuring quality control throughout manufacturing. This diligence helps minimize defects like voids or weak bonds, leading to more durable products.
Designing overmolds isn’t just about following steps—it’s about anticipating challenges and adapting solutions. Each project offers a new chance to learn and improve, reminding me why I love what I do.
TPE is compatible with ABS for overmolding.True
Thermoplastic elastomers (TPE) are often used over ABS due to good adhesion.
Sharp corners improve overmold durability.False
Sharp corners create stress points, reducing the structural integrity of overmolds.
How Can Overmolding Enhance Product Aesthetics and Functionality?
Imagine holding a sleek gadget that feels like it was tailor-made for your hands. That’s the magic of overmolding!
Overmolding combines multiple materials in one part, enhancing product aesthetics, grip, durability, and design flexibility.
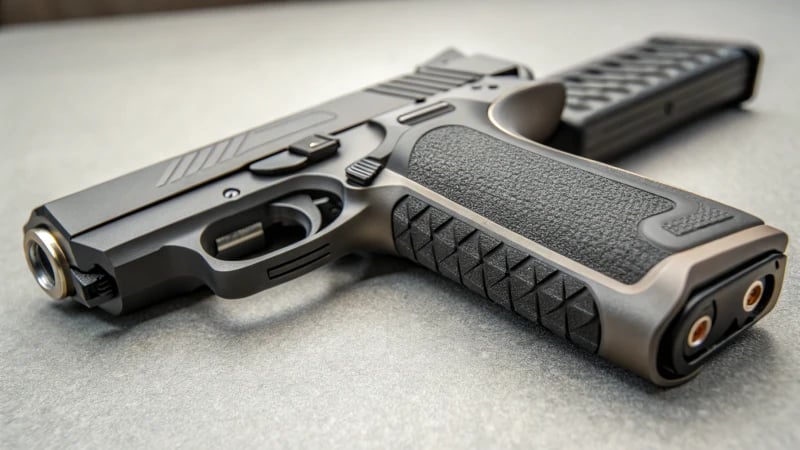
Understanding Overmolding
Overmolding is a fascinating process that allows for the combination of different materials to create something entirely new. Imagine molding a soft-touch material over a sturdy base—it’s like giving your product an upgrade in comfort and usability. It’s all about blending the best of both worlds to create something that’s as functional as it is beautiful.
For instance, using a soft-touch material over a rigid base can improve the user experience16 by providing better grip and comfort.
Enhancing Aesthetics
When it comes to aesthetics, overmolding is like having a painter’s palette in your toolbox. I once worked on a project where we used this technique to add unique textures and colors to our designs. It was incredible to see how these changes made our products stand out in the market.
Material | Finish | Benefit |
---|---|---|
Silicone | Matte | Soft touch |
TPU | Glossy | Flexible and durable |
The seamless transitions between materials not only improved the look but also eliminated extra assembly steps, making the process smoother and more efficient.
Boosting Functionality
Overmolding isn’t just about looks; it’s also about practicality. I remember designing a product with rubberized grips that made holding it for extended periods so much more comfortable. This simple addition significantly improved ergonomics17, making it safer and more user-friendly.
Functionality is another critical aspect where overmolding shines. It enables the integration of features such as seals, grips, or anti-slip surfaces directly into the product design.
Real-World Applications
In consumer electronics, overmolding has been a game-changer. I’ve seen it used to create protective casings that are both eye-catching and durable by combining hard plastics with softer elastomers. It’s a win-win for durability and aesthetics.
Additionally, in the automotive industry, overmolded parts are utilized for their ability to provide vibration damping18 and noise reduction, contributing to a more comfortable driving experience.
By understanding and applying overmolding, designers can transform their products, adding both visual appeal and practical functionality, making it an indispensable tool in modern manufacturing.
Overmolding improves product grip and comfort.True
Overmolding uses soft-touch materials over rigid bases, enhancing grip.
Overmolding requires additional assembly processes.False
Overmolding eliminates extra assembly, allowing smoother transitions.
Conclusion
Key factors in designing molds for overmolding include material compatibility, precise mold design, and process optimization to enhance product durability, aesthetics, and functionality.
-
Explore a list of materials known for their compatibility in overmolding applications, essential for successful product design. ↩
-
Understand the common causes of delamination to prevent structural failures in your designs. ↩
-
Learn tips and techniques for achieving strong adhesion between layers in overmolded products. ↩
-
Discover tools that assist in choosing the right materials for effective overmolding processes. ↩
-
Discover how precise alignment in mold design eliminates gaps and enhances bonding in overmolded products. ↩
-
Learn about essential material properties that ensure successful bonding and longevity in overmolded parts. ↩
-
Explore modern CAD techniques to enhance mold design efficiency and reduce production costs. ↩
-
Explore detailed guidelines on setting mold temperature to improve material flow and bonding during overmolding. ↩
-
Discover industry best practices for enhancing overmolding processes to ensure high-quality outcomes. ↩
-
Discover which materials work best together in overmolding applications to avoid common compatibility issues. ↩
-
Learn how advanced CAD techniques can improve mold design precision and efficiency. ↩
-
Find out effective maintenance tips to keep injection molding machinery running smoothly and prevent downtimes. ↩
-
Exploring adhesion techniques can help you enhance the bonding between different materials, leading to more durable overmolded parts. ↩
-
Understanding FEA can aid in predicting how your design will behave under various stresses, optimizing durability. ↩
-
Learning about advanced adhesion methods will ensure stronger bonds in your overmolded products. ↩
-
Learn how soft-touch materials improve user experience by enhancing grip and comfort. ↩
-
Explore why ergonomic design is crucial for reducing user fatigue and improving functionality. ↩
-
Discover how vibration damping enhances comfort and safety in vehicles. ↩