Injection molding is more than just a manufacturing process; it’s a dance of precision and creativity. So, what truly makes this intricate process tick?
The key factors in the injection molding process include mold design, raw material selection, precise parameter settings, equipment maintenance, and rigorous quality control. Understanding these aspects is crucial for enhancing efficiency and product quality.
While this overview provides a snapshot of critical elements, delving into each factor reveals how they individually and collectively contribute to optimizing the injection molding process. Let’s explore how understanding these can lead to superior outcomes.
Mold design affects the flow of plastic melt.True
Mold design influences how plastic melt flows, impacting quality.
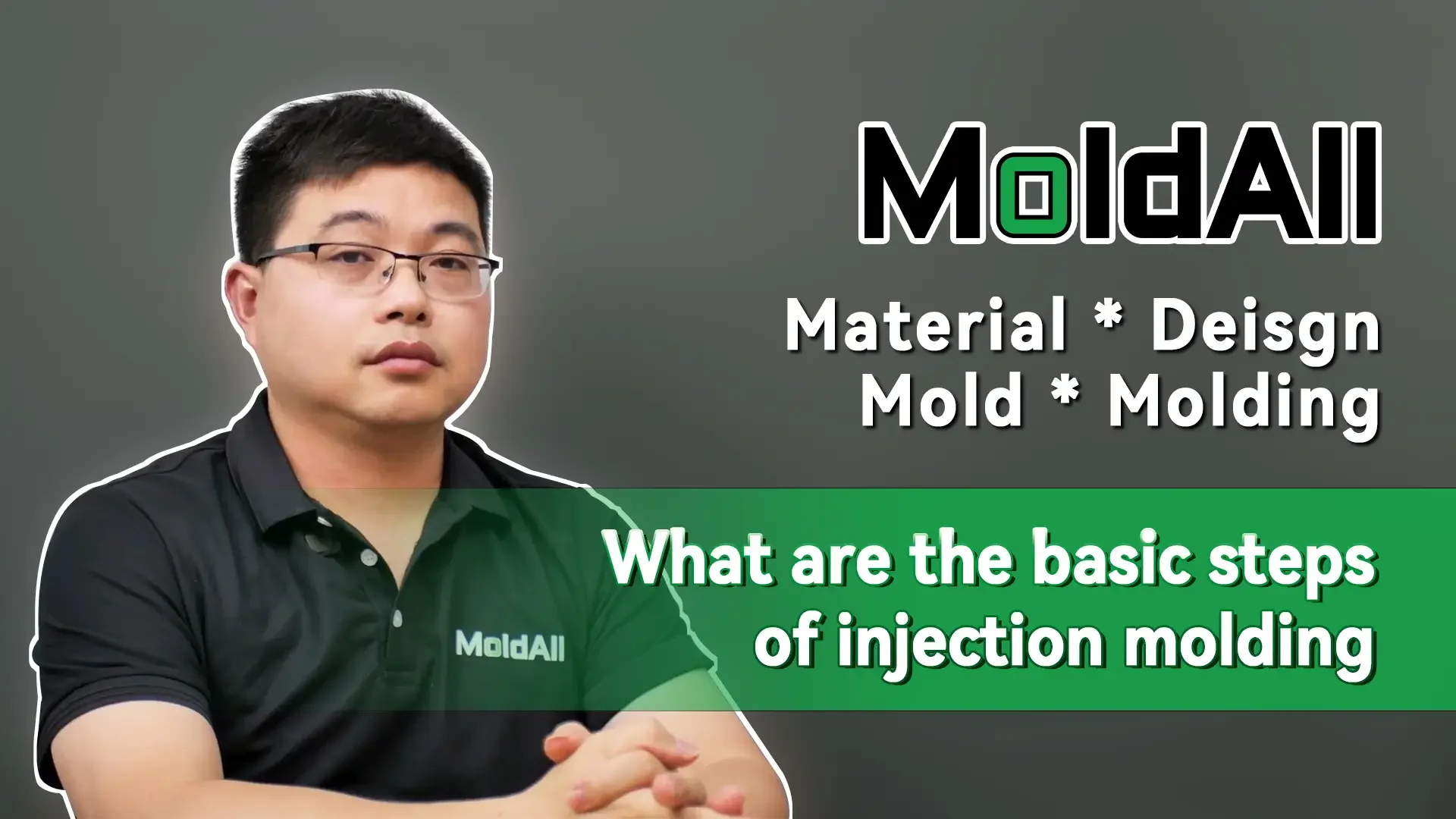
How Does Mold Design Impact Injection Molding?
Mold design is a cornerstone of the injection molding process, influencing both efficiency and product quality.
Mold design impacts injection molding by determining the flow of plastic melt, cooling efficiency, and precision of the final product. A well-designed mold ensures uniform melt flow, effective cooling, and high dimensional accuracy, reducing defects and improving production efficiency.
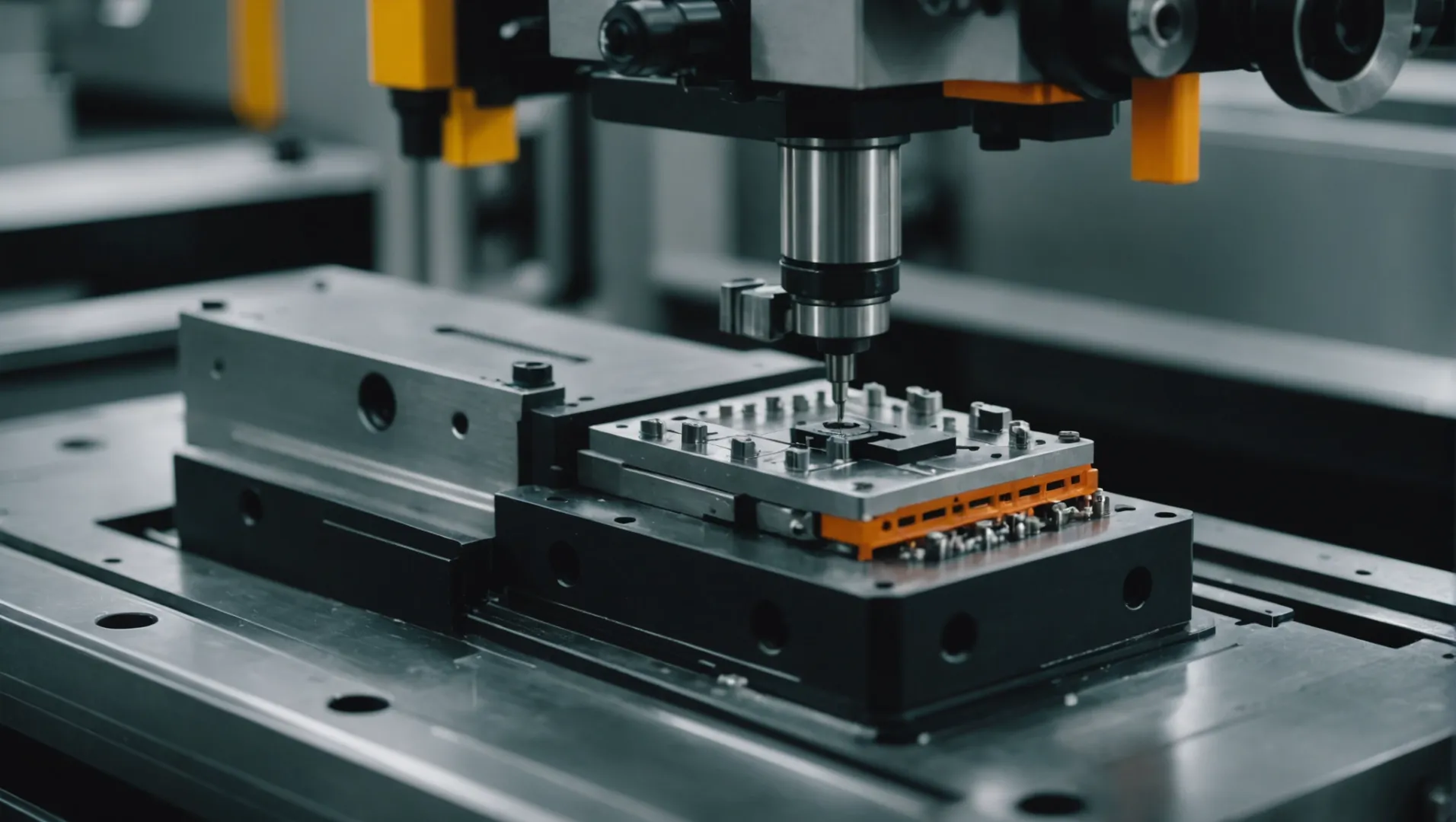
Structural Rationality in Mold Design
Structural rationality is critical in mold design, as it dictates how the plastic melt flows into the mold cavity. By strategically positioning gates in thicker sections of the plastic part, designers can ensure smooth filling with minimal flow resistance. This strategic placement also helps in minimizing defects such as short shots and weld marks.
Moreover, the mold cooling system plays a pivotal role in structural rationality. An efficient cooling system decreases the molding cycle time and enhances production efficiency. Ideally, cooling channels should be evenly distributed to maintain a consistent temperature throughout the plastic part, thereby reducing warping and deformation risks.
Precision Control for Quality
Precision control in mold design is essential for achieving high dimensional accuracy and surface quality. High-precision molds are necessary for producing components with tight tolerances and superior finishes. Using advanced processing techniques and equipment can ensure that molds meet stringent design specifications for dimensional accuracy and surface roughness.
Regular maintenance and timely repair of molds can further extend their service life and maintain consistent quality in the injection molded parts. This proactive approach not only ensures longevity but also keeps production disruptions at bay.
Importance of Gate Design
The gate design is another crucial element in mold design. It determines how the molten plastic enters the mold cavity, affecting fill time and pressure distribution. Proper gate size and location help in achieving optimal fill patterns, reducing residual stress, and enhancing part strength.
Designers must also consider gate removal post-molding to ensure ease of part separation without affecting surface aesthetics or functionality.
Cooling System Design
An effective cooling system is integral to mold design, significantly impacting cycle times and product consistency. Efficient cooling involves optimizing channel layouts to ensure uniform temperature distribution during the cooling phase. This uniformity helps in reducing internal stresses and dimensional variations in the final product.
Incorporating technologies such as conformal cooling can enhance traditional methods by using 3D printing to create more efficient cooling paths tailored to complex geometries.
For further insights on mold cooling system advancements1 and their effects on efficiency, explore cutting-edge technologies shaping the industry.
Ultimately, a well-thought-out mold design not only streamlines the injection molding process but also results in high-quality products with fewer defects.
Mold design affects product quality in injection molding.True
Mold design determines flow, cooling, and precision, impacting quality.
Gate design has no impact on injection molding efficiency.False
Gate design affects fill time and pressure, influencing efficiency.
Why Is Material Selection Crucial in Injection Molding?
Choosing the right material is fundamental to successful injection molding, impacting performance and cost.
Material selection in injection molding is vital because it determines the product’s performance, durability, and cost-effectiveness. Factors such as plastic performance, quality, and environmental impact must be considered to meet specific application requirements and ensure product excellence.
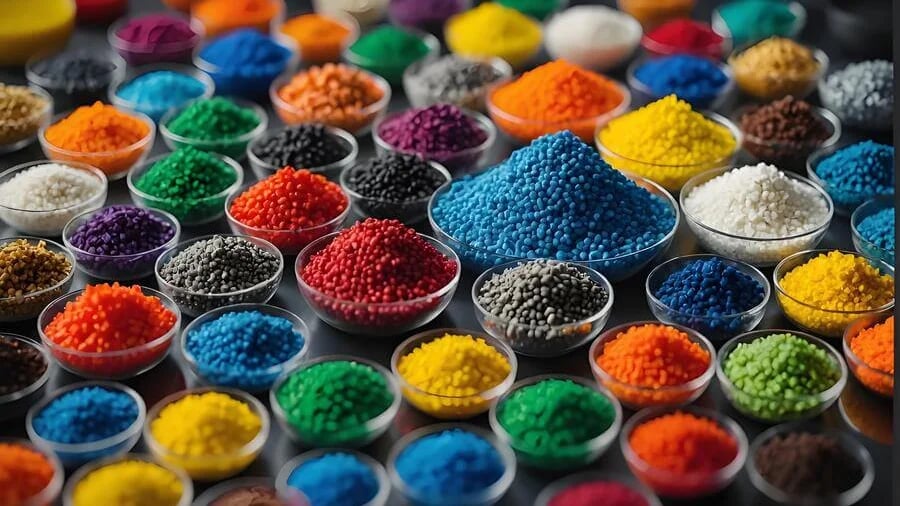
Understanding Plastic Performance
The performance characteristics2 of plastic materials are diverse, influencing the properties of the final product significantly. Each type of plastic, from ABS to polycarbonate, has unique strengths and limitations. For example, if high strength and heat resistance are essential for your product, polycarbonate might be ideal.
Fluidity is another key factor. Plastics with good fluidity fill molds more easily, reducing defects like short shots or weld lines. This results in a smoother manufacturing process and higher quality products. Moreover, controlling the shrinkage rate is crucial for maintaining dimensional accuracy, which varies among different plastics.
Ensuring Material Quality
Reliable material quality can make or break the injection molding process. Regular suppliers who meet stringent inspection standards should be prioritized. Inspections focus on aspects such as appearance, particle size, and moisture content. Poor-quality materials can introduce defects like bubbles or impurities.
For applications like food packaging or medical devices, choosing environmentally friendly materials3 is essential to meet health and safety standards. These materials should be non-toxic and comply with relevant regulations to ensure consumer safety.
Economic and Environmental Considerations
Material costs directly influence the overall manufacturing expense. Therefore, balancing performance needs with cost-effectiveness is necessary. Recycled or composite materials can offer a cost-efficient alternative without compromising quality.
Additionally, considering the environmental impact of materials is increasingly important. Opting for sustainable options not only aligns with global eco-friendly initiatives but can also enhance brand reputation.
The Impact of Material Selection on Product Development
Selecting the right material is not just about immediate production benefits; it also affects long-term product success. High-quality materials reduce maintenance needs and extend product life, ensuring customer satisfaction and reducing warranty claims.
By strategically choosing materials during the design phase, manufacturers can optimize production efficiency4 and product quality, ultimately boosting competitiveness in the market.
Polycarbonate is ideal for high-strength products.True
Polycarbonate offers high strength and heat resistance, suitable for durable products.
Poor-quality materials reduce injection molding defects.False
Poor-quality materials increase defects like bubbles and impurities, affecting product quality.
What Role Do Parameter Settings Play in the Injection Molding Process?
Parameter settings in injection molding are crucial for ensuring product quality, efficiency, and consistency. But what specific roles do they play in this intricate process?
Parameter settings in injection molding dictate the temperature, pressure, and speed of the process, crucially affecting the quality and efficiency of the final product. Proper adjustment is essential to avoid defects and ensure precision.

Temperature Control: A Key to Quality
Temperature settings in injection molding involve controlling the barrel, nozzle, and mold temperatures. The barrel temperature must be tailored to the plastic’s characteristics to guarantee complete melting without decomposition. Nozzle temperature slightly lower than the barrel prevents drooling.
For instance, a higher mold temperature can enhance surface gloss and flatness for parts with stringent aesthetic requirements. Conversely, crystalline plastics might benefit from lower mold temperatures to quicken crystallization and boost productivity.
Pressure Settings: Balancing Force and Precision
Pressure in injection molding is bifurcated into injection and holding pressures. Injection pressure influences how swiftly and fully the plastic melt fills the mold. To optimize fluidity and avoid short shots, it’s important to calibrate this pressure precisely.
Holding pressure compensates for shrinkage during cooling, maintaining dimensional accuracy and density. Adjustments should reflect both the plastic properties and part structure. Explore more about pressure control techniques5 to master this balancing act.
Speed Control: Synchronizing Movement
Injection speed and screw speed are pivotal parameters in this process. An overly rapid injection can lead to defects like weld marks, while a sluggish pace may drag out cycle times.
Selecting the correct screw speed is crucial for consistent melting and transportation of the plastic. Learn more about optimal speed settings6 for various materials and machines.
Ensuring Consistency through Parameter Settings
Consistent parameter settings underpin the repeatability of the injection molding process. Regular monitoring and adjustments ensure that each cycle remains within defined tolerances, essential for high-quality output.
To deepen your understanding, consider exploring how parameter adjustments impact cycle time7. This knowledge can lead to more efficient production cycles, reducing waste and enhancing throughput.
Parameter settings in injection molding are a delicate balance of heat, pressure, and speed. Mastery of these factors ensures not only the quality of the finished product but also the efficiency and cost-effectiveness of the production process.
Temperature affects surface gloss in injection molding.True
Higher mold temperatures can enhance surface gloss and flatness.
Injection speed doesn't affect cycle time in molding.False
Sluggish injection speeds can prolong cycle times, affecting efficiency.
How Can Equipment Maintenance Improve Injection Molding Efficiency?
Proper equipment maintenance is crucial in injection molding, enhancing efficiency and product quality. But how exactly does it impact the process?
Equipment maintenance improves injection molding efficiency by ensuring machine reliability, reducing downtime, and maintaining optimal production conditions. Regular servicing of machinery and auxiliary equipment prevents defects, ensures consistency, and extends equipment lifespan.
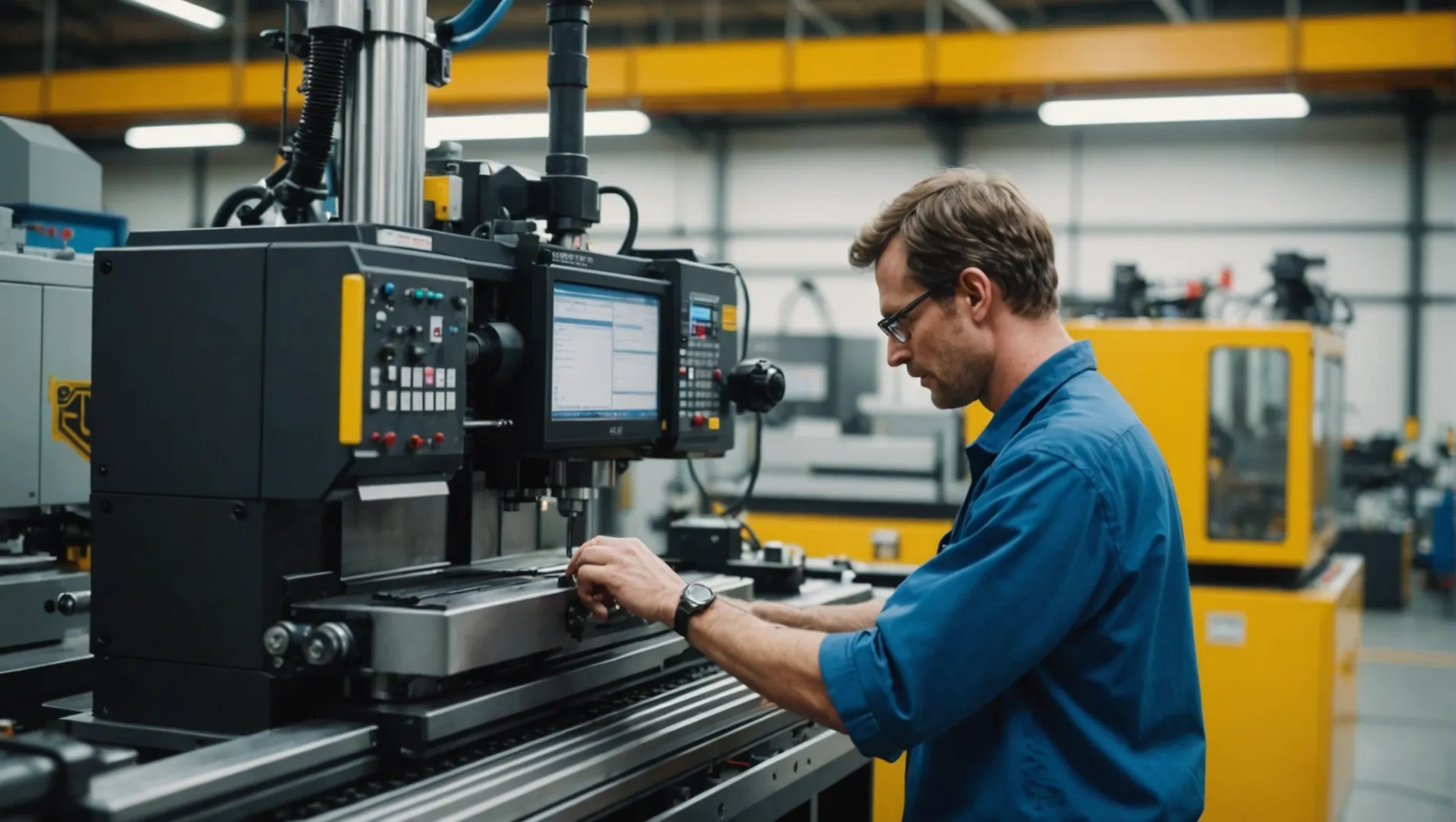
The Importance of Machine Reliability
Maintaining the injection molding machines is essential for their reliability. Regular checks and servicing ensure that components such as the hydraulic system and mechanical transmission are functioning correctly. This reliability minimizes unexpected breakdowns that can halt production and lead to costly delays.
A well-maintained machine operates smoothly, reducing the risk of producing defective parts. For example, monitoring and replacing worn parts in the hydraulic system8 can prevent issues that might affect clamping force consistency or injection pressure.
Minimizing Downtime with Preventative Maintenance
Downtime in manufacturing can lead to significant financial losses and production backlogs. Implementing a preventative maintenance schedule helps in anticipating potential failures before they occur. This involves routine inspections and timely replacement of parts that are prone to wear and tear.
Auxiliary equipment like dryers and mold temperature controllers also require regular maintenance to avoid moisture-related defects and to maintain precise temperature settings, respectively. When all components work seamlessly, production efficiency increases considerably.
Ensuring Consistency and Quality
Consistent product quality is a hallmark of efficient injection molding. By maintaining equipment properly, manufacturers can sustain the required settings for temperature, pressure, and speed, ensuring each product meets the design specifications.
For instance, a malfunctioning screw in an injection molding machine could lead to improper melting of plastic, causing variations in the final product. Regular cleaning and calibration of these parts are necessary for maintaining high standards of production.
Extending Equipment Lifespan
Regular maintenance not only improves efficiency but also extends the lifespan of equipment. By addressing minor issues promptly, manufacturers can avoid major breakdowns that might necessitate costly repairs or replacements.
Investing time and resources into maintenance can lead to long-term savings and a more sustainable operation. This approach fosters a culture of continuous improvement9 within the manufacturing process, where efficiency and quality are continually enhanced.
Regular maintenance reduces injection molding downtime.True
Routine checks prevent breakdowns, minimizing production halts.
Neglecting equipment maintenance boosts injection molding quality.False
Lack of maintenance leads to defects and inconsistency in products.
Conclusion
Mastering these key factors ensures improved efficiency and high-quality products. Reflect on your processes and consider fine-tuning these aspects for better results in injection molding.
-
Discover new technologies enhancing efficiency in injection molding cooling systems.: There are many instances in which the injection mold process has evolved due to newer technologies, most notably the cooling systems. ↩
-
Explore how different plastics influence injection molding outcomes.: The Primary Characteristics of Plastics · Usually lightweight with a high strength-to-weight ratio. · Very versatile. · Moldable into different … ↩
-
Discover sustainable material options for eco-conscious manufacturing.: Sulapac Universal Flex 35 is a sustainable, beautiful, and functional injection molding material which contains 87% USDA certified bio-based content. The … ↩
-
Learn how strategic material choices enhance manufacturing processes.: Some materials may be harder to mold than others, and this can impact the overall cost and efficiency of the production process. Availability: The material … ↩
-
Discover effective methods to adjust holding pressure for optimal results.: Pressures determine finished part quality, cycle times, and ultimately, your cost per piece. Understanding injection pressure. Product … ↩
-
Find expert advice on setting optimal speeds for diverse materials.: Adjusting the injection speed helps prevent issues like flow lines or air traps. 3. Cooling Time: The cooling time is the duration the part … ↩
-
Learn how tweaking parameters can optimize production efficiency.: Adjusting the injection speed helps prevent issues like flow lines or air traps. 3. Cooling Time: The cooling time is the duration the part … ↩
-
Explore how hydraulic system maintenance prevents breakdowns and ensures smooth operations.: In addition to improper maintenance, contaminated hydraulic oil is one of the principal causes of faults in injection molding machines. ↩
-
Learn about strategies to enhance efficiency and quality in manufacturing.: The primary goals of continuous improvement in manufacturing include increasing productivity and efficiency, eradicating waste and improving both employee … ↩