Want to improve your injection mold design skills? I have experienced that too. It can feel like too much at once. Let’s understand it step by step together!
When designing an injection mold, consider product shape, size, wall thickness, precision, functional requirements, and cooling system to ensure efficient production, high quality, and cost-effectiveness.
When I began designing injection molds, I understood the importance of focusing on key factors. Product shape, wall thickness and cooling systems are essential. I recall the stress of working on a complex car shell mold. Recognizing these elements changed everything. We achieved fast production and top-quality results. Each mold design presents its own challenges. Useful knowledge helps us face them without fear!
Product shape significantly impacts injection mold design.True
The shape of the product determines the mold's complexity and functionality, influencing production efficiency and quality.
Cooling system design is irrelevant in injection molding.False
A well-designed cooling system is essential for controlling cycle times and ensuring product quality during injection molding.
- 1. How Do Product Shape and Size Influence Mold Design?
- 2. Understanding How Product Shape and Size Affect Mold Design
- 3. How Does Wall Thickness Affect Injection Molding Processes?
- 4. Why Are Precision Requirements Critical for Mold Creation?
- 5. What Are the Best Practices for Cooling System Design in Molds?
- 6. How Can Material Selection Impact Mold Performance and Cost?
- 7. Conclusion
How Do Product Shape and Size Influence Mold Design?
Have you thought about the complex relationship between product shape and size in mold design? This is a very interesting journey. It is essential for successful manufacturing. I really want to share my insights with you.
Product shape and size significantly impact mold design by influencing geometry, cooling requirements, precision, and demolding methods, ensuring high-quality outputs and optimized manufacturing efficiency.
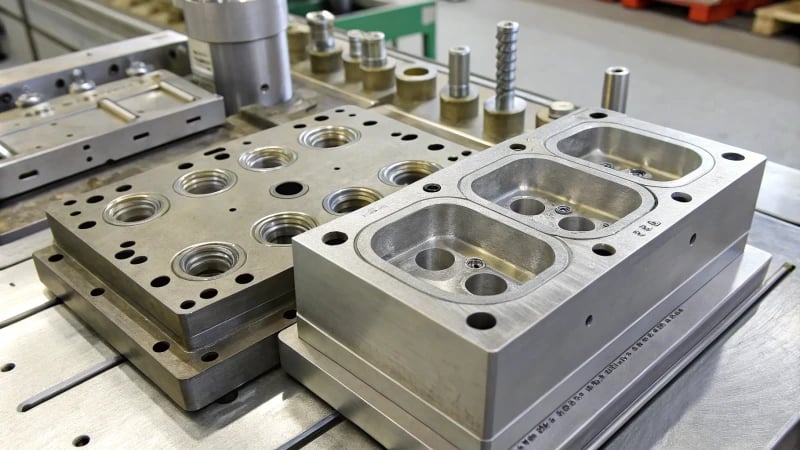
Understanding How Product Shape and Size Affect Mold Design
Understanding how product shape and size affect mold design is more than a technical task. It really involves creativity and innovation. These features guide how we design molds. Choices are influenced by shape and size. They steer us toward solutions that fit both specifications and the needs of users.
The Impact of Product Shape on Mold Geometry
Product shape greatly influences mold geometry. Imagine a project where you’re designing a complex car part. Seeing complex geometry signals the need for special mold features like slides or inclined tops for smooth demolding. A classic example is an automotive part, where a large shell requires an intricate cooling channel layout to ensure uniform cooling and prevent defects.
Size Considerations in Mold Design
Size also plays a critical role. For larger products, such as appliance covers, the mold must be very sturdy. I remember working on a massive appliance mold. Keeping it strong without losing cooling effectiveness was tough! Bigger molds often need advanced cooling systems, which greatly influence the final product’s quality.
Size Consideration | Effects on Molding | Solutions |
---|---|---|
Large | Sturdy structure needed | Advanced cooling systems |
Small | Faster production speed | Simplified designs |
Wall Thickness Variability
Wall thickness is a critical element. Uneven thickness can disrupt the injection molding process. Dealing with thick-walled parts led to cooling challenges for me, increasing production time and causing defects like shrinkage marks. My fix involved adjusting gate positions and optimizing cooling channels.
Wall Thickness | Effects on Molding | Solutions |
---|---|---|
Thick | Longer cooling times | Dense cooling channels |
Thin | Risk of defects | Multi-point gates for filling |
Precision Requirements in Mold Design
High-precision products demand extra care. Crafting molds for delicate lenses or electronic housings brings high stakes; tolerances become very crucial. Dimensional accuracy depends on top-quality materials and precise equipment.
Functional Requirements Influence Mold Structure
Functional needs can intricately shape mold design. For instance, waterproof products need smooth, pore-free surfaces to maintain integrity.
Aligning Mold with Injection Molding Machine Parameters
Mold design needs to match injection molding machine parameters; knowing clamping force, mold stroke, and injection volume is essential to avoid equipment problems caused by size mismatches.
Pressure and Speed Considerations in Injection Molding
Choosing the right injection pressure and speed adds complexity; high-viscosity plastics require precise adjustments to maintain product quality while optimizing efficiency.
Cooling Time and Temperature Management
Cooling systems have a huge impact on mold design as they affect cycle times significantly; effective cooling channels boost production efficiency while ensuring product integrity.
Choosing the Right Mold Materials
Material selection in mold design depends on product needs; high-output molds need strong materials like P20 or H13 steel known for their durability while balancing budget considerations is crucial.
Cost Control Strategies in Mold Design
Managing production costs while ensuring quality is a constant challenge; streamlining structures helps reduce costs while meeting performance standards feels rewarding.
Demolding Techniques Customized for Product Shape
Now, let’s discuss demolding methods tailored to product shapes; picking the right technique is crucial as I have encountered situations where using an ejector method for standard shapes saved me from problems.
Complex product shapes require specialized mold features.True
Specialized mold features like slides are essential for demolding complex geometries, ensuring effective production without defects.
Larger products necessitate simpler mold designs.False
Larger products actually require more robust and sophisticated mold structures to maintain integrity and efficiency in manufacturing processes.
How Does Wall Thickness Affect Injection Molding Processes?
Do you ever think about how wall thickness might transform everything in injection molding? It’s really fascinating and very important. Wall thickness truly matters. Let’s explore why knowing this aspect improves your designs and production efficiency.
Wall thickness significantly impacts injection molding by influencing filling patterns, cooling times, and potential defects. Proper management ensures high-quality results and efficient production.
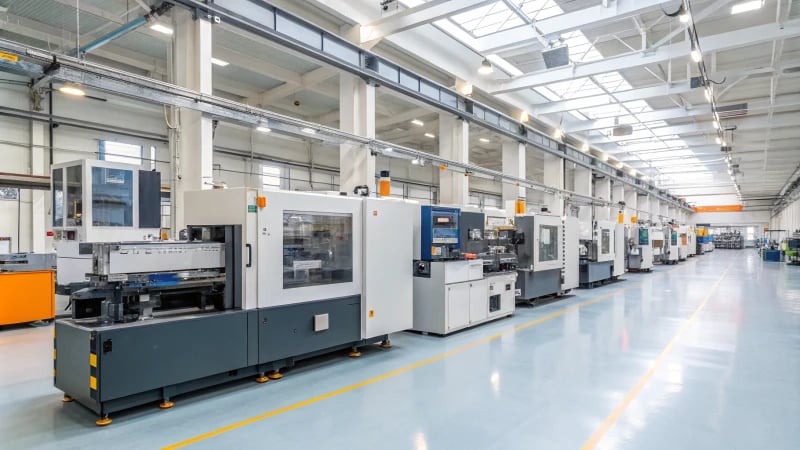
Understanding the Impact of Wall Thickness on Filling and Cooling
Wall thickness is a critical factor in the injection molding process. It directly influences how a molded part fills and cools within the mold. For instance, thick-walled parts take considerably longer to cool compared to thin-walled parts. This prolonged cooling time can lead to defects like shrinkage marks and porosity.
To effectively manage these issues, designers must consider various strategies:
- Gate Positioning: Adjusting the gate location can help ensure that the molten plastic fills the mold evenly, reducing the risk of defects.
- Cooling Channel Design: Implementing denser cooling channels in areas with thicker walls can significantly improve cooling efficiency.
For example, consider a product with varying wall thicknesses:
Wall Thickness (mm) | Cooling Time (s) | Potential Defects |
---|---|---|
2 | 5 | Minimal |
5 | 10 | Shrinkage |
10 | 15 | Pores |
The Role of Precision in Mold Design
High-precision products, such as optical lenses or electronic component housings, demand strict control over mold precision. Wall thickness plays a vital role here; deviations can lead to functional issues in the final product. Designers must account for:
- Dimensional Tolerances: Ensuring the mold can produce parts within specified tolerances, which may vary based on wall thickness.
- Surface Roughness: Thicker walls may require additional finishing processes to achieve the desired surface quality.
When designing molds for high-precision applications, it is essential to incorporate features that minimize deformation due to varying wall thickness, such as support structures1.
Cooling System Considerations
The cooling system’s layout must align with the thermal properties of the materials being used and the product’s wall thickness. Different plastics have unique cooling requirements:
- Crystalline Plastics: These materials often require careful consideration of the crystallization temperature range during cooling.
- Non-Crystalline Plastics: They may cool uniformly, but variations in wall thickness can still affect cooling rates.
A well-designed cooling system will optimize cycle times and improve production efficiency. Here’s a comparison of cooling strategies:
Plastic Type | Ideal Cooling Method | Cooling Time Reduction |
---|---|---|
Crystalline | Controlled temperature cooling | 20% |
Non-Crystalline | Standard cooling channels | 15% |
Manufacturing Cost Implications
Selecting the appropriate wall thickness impacts not only product quality but also production costs. Thicker walls may necessitate higher-quality materials, which can increase overall costs. Key considerations include:
- Material Selection: High-quality mold steels may be required for thick-walled molds to withstand stress.
- Processing Costs: Thicker molds may require more complex processing techniques that add to labor costs.
It’s essential to balance quality requirements with cost considerations by:
- Simplifying mold structures when possible.
- Evaluating processing methods for efficiency.
Demolding and Ejection Factors
The wall thickness also affects how a part is demolded. Thicker areas may require specialized demolding techniques to prevent damage during ejection. Key points include:
- Ejection Positioning: Avoiding weak spots in the design helps maintain product integrity during ejection.
- Ejection Force Calculation: Proper calculation based on wall thickness is necessary to avoid defects like top whitening.
Utilizing suitable demolding methods can significantly enhance the success rate of ejection processes:
Demolding Method | Ideal Application |
---|---|
Ejector Ejection | General parts without undercuts |
Slider Demolding | Parts with undercut structures |
Inclined Ejector | Products needing careful handling |
and by considering these aspects related to wall thickness, designers and manufacturers can optimize their injection molding processes effectively.
Thicker walls increase cooling time in injection molding.True
Thicker-walled parts take longer to cool, leading to potential defects like shrinkage and porosity.
Wall thickness has no impact on mold precision.False
Variations in wall thickness can cause functional issues, making precision control essential in mold design.
Why Are Precision Requirements Critical for Mold Creation?
Have you ever wondered why accuracy is very important in creating molds? Precision is more than just helping things fit properly. Each product needs to be excellent. This detail is essential. Let’s explore why precision is a must in this work!
Precision in mold creation is vital as it impacts product quality, performance, and cost. Key factors like shape, wall thickness, and injection parameters must be meticulously managed to ensure optimal results.
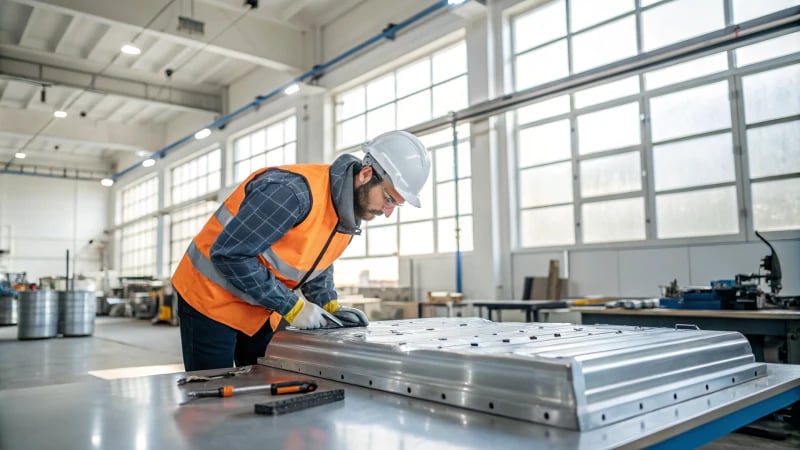
Understanding Precision in Mold Creation
Precision requirements are vital for mold creation, as they directly affect product quality, performance, and cost. High-precision molds ensure that products meet stringent dimensional tolerances, which is crucial for applications in various industries, including automotive and consumer electronics.
For instance, consider optical lenses where even a slight deviation can lead to significant functional defects. The precision requirements for such components necessitate advanced mold design and machining techniques.
Product Factors Affecting Precision
-
Shape and Size: The shape of a product decides the mold cavity’s geometry. Complex designs often need special features for easy removal.
- Larger products require molds with increased strength and more sophisticated cooling designs to ensure uniform temperature distribution during production. An example can be seen in the production of a large automobile shell, which demands careful consideration of mold structure and cooling channels to avoid defects.
-
Wall Thickness: Variations in wall thickness can greatly impact molding. Thick sections cool slower, risking defects like shrink marks.
- To avoid these issues, designers often change gate positions or add dense cooling channels in thick parts. Balancing this is key.
Wall Thickness | Impact on Cooling | Design Adjustments |
---|---|---|
Thick | Longer cooling | Adjust gate position |
Thin | Faster cooling | Increase cooling channels |
- Functional Requirements: Special functions like waterproofing must be reflected in the mold design.
- For example, waterproof parts require meticulous mold structures to ensure surface integrity, preventing cracks that could lead to failure.
Injection Molding Process Factors
-
Machine Parameters: The mold must match the injection machine’s settings, like clamping force and injection volume.
- Mismatches can cause incomplete injections or damage equipment; precise alignment is vital between mold and machinery.
-
Injection Pressure and Speed: Different materials need specific pressure and speed.
- For thick plastics, high pressure and low speed are often necessary. A well-designed mold helps by optimizing runner and gate sizes.
Material and Cost Factors
- Material Selection: Right materials are crucial for durability and precision.
- High-quality steels or alloys may be needed for molds requiring good performance; choosing the right material is truly important for longevity.
Mold Material | Application | Benefits |
---|---|---|
P20 Steel | General production | Good wear resistance |
H13 Steel | High-precision needs | Excellent toughness |
- Production Cost Control: Balancing quality with cost is key; good design avoids unnecessary details while maintaining precision.
Demolding and Ejection Factors
- Demolding Methods: The chosen demolding method greatly affects product quality; options include ejector ejection or slider demolding for products with undercuts.
- Ejection Forces: Calculating ejection forces correctly prevents damage during demolding.
- Too much force can cause defects; too little can make ejection difficult; careful planning ensures smooth operation.
Achieving precision in mold creation requires understanding various factors that affect the final product’s quality, efficiency, and cost. Every part—from mold shape to how products are removed—holds a very important role in the proper function of molds in factories. For more details on top practices in precise molding, visit mold design standards2.
Precision molds enhance product quality in manufacturing processes.True
High-precision molds ensure products meet dimensional tolerances, crucial for quality and performance across industries.
Complex shapes require simpler mold designs for efficiency.False
In fact, intricate designs necessitate advanced mold features to ensure proper demolding and quality outcomes.
What Are the Best Practices for Cooling System Design in Molds?
Let’s explore the world of cooling system design in molds. This area really influences the efficiency and quality of your product. It’s very important to get it right. This involves more than just technical skills. It’s about creating solutions based on our experiences in manufacturing.
Design an effective mold cooling system by meticulously planning channel layouts, selecting appropriate cooling mediums, and considering material thermal properties. These steps ensure even cooling and reduce cycle times.
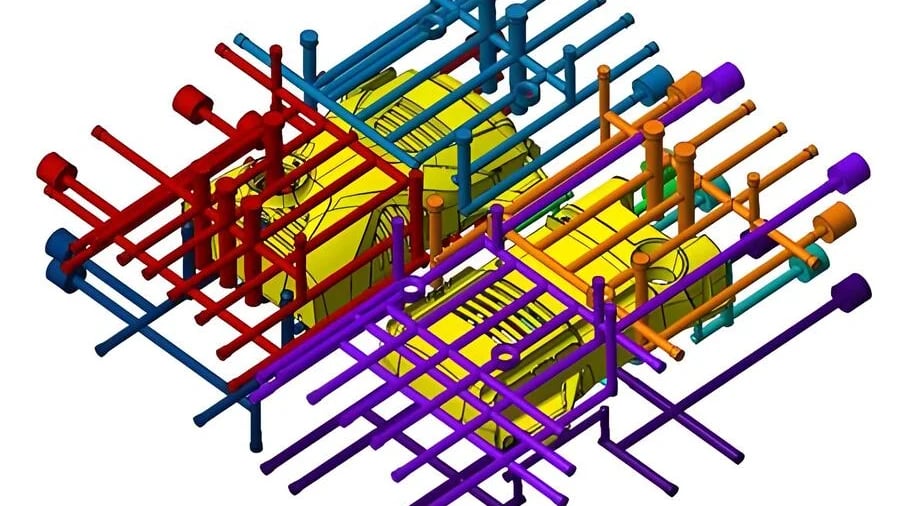
Understanding Cooling System Importance
Cooling systems in molds play a crucial role in the injection molding process. Proper cooling ensures uniform temperature distribution throughout the mold, which in turn affects the quality of the final product. An effective cooling system minimizes cycle times, reduces defects, and enhances overall productivity.
Key Factors in Cooling System Design
- Cooling Channel Layout
Designing the layout of the cooling channels is critical. The channels should be positioned to allow for optimal heat transfer from the mold to the cooling medium.
For instance, a well-designed layout might resemble this:
Channel Type | Description |
---|---|
Straight Channels | Direct pathways for coolant flow, easy to manufacture. |
Curved Channels | Allows for better coverage around complex geometries. |
Baffle Channels | Improves flow distribution and cooling efficiency. |
- Thermal Properties Consideration
Each plastic reacts differently to heat. I always consider these properties when designing. Crystalline plastics usually need longer cooling than non-crystalline ones.
- Example: With crystalline materials, cooling channels should keep temperatures above their crystallization point during filling but must drop below it during cooling.
- Integration with Injection Parameters
Designing cooling systems with injection parameters is important. Once, a mismatch caused incomplete filling. That was frustrating!
- Faster injection speeds sometimes need quicker cooling to prevent overheating.
- Monitoring and Adjustment Systems
Technology helps in checking temperature and coolant flow with sensors. Real-time data allows for quick changes during production, greatly improving quality control.
For anyone wanting to learn more about cooling systems, look into advanced cooling techniques3 or cooling system designs4. Refining large automobile shells or making precise electronic parts may benefit from these insights; they can truly change your mold design approach.
Cooling systems significantly impact injection molding quality.True
Effective cooling ensures uniform temperatures, reducing defects and enhancing product quality in the injection molding process.
Water is the only suitable cooling medium for molds.False
While water is common, alternatives like oil and glycol may be better for specific applications due to their unique properties.
How Can Material Selection Impact Mold Performance and Cost?
Have you ever thought about how picking the right material affects your injection molding process? This decision is really important! It changes how well the mold works and influences costs greatly.
Selecting appropriate materials in injection molding enhances performance and controls costs. Key considerations include product shape, size, precision needs, and cooling systems, all of which significantly influence material choices.
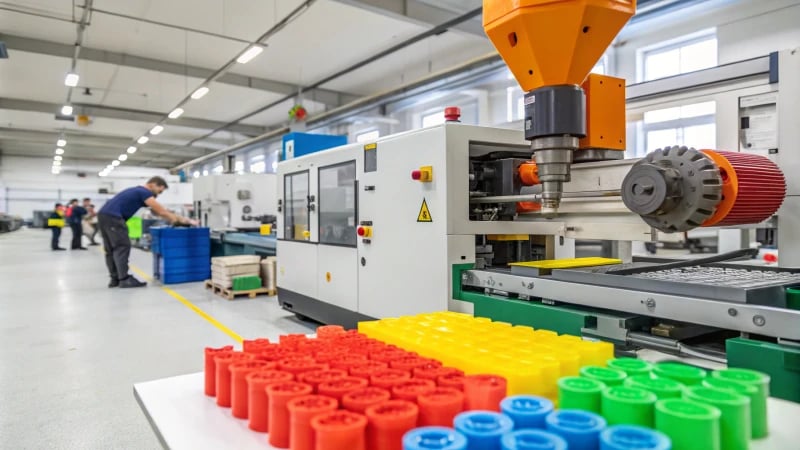
Understanding the Role of Material Selection
Material selection is pivotal in injection molding as it directly impacts both mold performance and overall costs. The choice of material can dictate the longevity and effectiveness of the mold, as well as the quality of the final product.
For instance, using high-quality steel such as P20 or H13 can enhance the mold’s durability and precision, which is especially important for products with intricate designs or high-volume production needs. However, these materials come at a higher price point, leading to increased initial costs. Balancing cost with performance is crucial for manufacturers aiming to optimize production efficiency while maintaining product integrity.
Product Factors Affecting Material Choice
Several product factors play a role in determining the appropriate material for molds:
- Shape and Size: Complex shapes require robust materials to withstand the stresses during demolding. For example, large molds for automobile components necessitate materials that can support intricate cooling systems and maintain structural integrity under pressure.
- Wall Thickness: Variations in wall thickness can complicate material selection. Thicker sections may require materials with better thermal conductivity to ensure uniform cooling and avoid defects like shrinkage marks. The design of cooling channels must also consider these variations, making material choice critical in achieving optimal cooling performance.
- Precision Requirements: High-precision molds necessitate the use of materials that can be machined to tight tolerances without deforming. Using high-quality alloys can help meet these demands but increases production costs.
Injection Molding Process Factors
The selection of material also needs to align with the parameters of the injection molding process:
- Injection Molding Machine Compatibility: The mold material must be compatible with the specific machine’s clamping force and injection volume. If the selected material cannot withstand operational pressures, it could lead to costly damages or production delays.
- Pressure and Speed Considerations: Different materials respond uniquely to varying pressures and speeds. For instance, high-viscosity plastics may require materials that can endure higher injection pressures without failing.
Material Type | Strength | Cost | Best Use Case |
---|---|---|---|
P20 Steel | High | $5 | High-volume production with complex shapes |
H13 Steel | Very High | $10 | High precision molds for intricate designs |
Aluminum | Moderate | $2 | Low-volume production or prototypes |
Cost Implications of Material Selection
Choosing the right mold material involves careful consideration of both performance and cost implications:
- Production Cost Control: Selecting lower-cost materials may reduce upfront expenses but could lead to higher long-term costs due to increased wear and tear or lower product quality. Manufacturers must analyze whether short-term savings outweigh potential long-term losses in production efficiency.
- Service Life and Maintenance Costs: Investing in durable materials often leads to a longer service life for molds, reducing maintenance needs and downtime. For example, a mold made from high-quality steel may incur higher initial costs but result in fewer repairs and replacements over time.
Demolding Factors Linked to Material Choice
Finally, the method of demolding is influenced by the chosen material:
- Demolding Method: Some materials facilitate easier demolding processes, reducing the risk of damage during ejection. For instance, softer materials may allow for smoother ejection but could wear down faster.
- Ejection Force Considerations: The appropriate ejection force is crucial to avoid product defects. Choosing a material that can withstand these forces without deformation is essential for maintaining product quality.
For more insights on optimizing your mold design5 based on material selection, consider exploring advanced resources that detail the latest techniques in manufacturing.
Understanding how material selection impacts mold performance and cost is vital for engineers and designers like Jacky to make informed decisions that balance quality with economic viability.
High-quality steel molds enhance durability and precision.True
Using materials like P20 or H13 improves mold longevity and product quality, essential for intricate designs and high-volume production.
Lower-cost materials always reduce overall production costs.False
While cheaper materials may lower initial costs, they can lead to higher long-term expenses due to increased wear and maintenance needs.
Conclusion
Key factors in injection mold design include product shape, size, wall thickness, precision requirements, cooling systems, and cost control for optimal manufacturing efficiency.
-
Exploring this link will provide insights into best practices for managing wall thickness in injection molding, helping you enhance your designs. ↩
-
Discover best practices for achieving precision in mold design and production processes that enhance your manufacturing outcomes. ↩
-
Learn about effective strategies for optimizing cooling systems in mold design, improving efficiency and product quality. ↩
-
Explore advanced techniques for cooling channel layouts and materials selection that enhance mold performance. ↩
-
Discover how proper material selection can enhance your mold designs and reduce overall production costs. ↩