As I navigated the world of injection molding, one thing became clear: not all PVC is created equal.
Choosing the right type of PVC for injection molding can significantly impact the performance and durability of your products. Rigid PVC is known for its high hardness and stability, making it ideal for durable products like pipes and window frames. In contrast, plasticized PVC offers flexibility due to added plasticizers, suitable for items requiring bendability such as cable sheaths.
While the core differences might seem straightforward, the implications on manufacturing processes and end-use applications are profound. Let’s dive deeper into how these variations can influence your injection molding projects.
Rigid PVC has higher hardness than plasticized PVC.True
Rigid PVC is known for its high hardness and stability, unlike plasticized PVC.
- 1. How Do Physical Properties Affect PVC Selection in Injection Molding?
- 2. What Are the Processing Performance Differences Between Rigid and Plasticized PVC?
- 3. How Do Chemical Properties Influence PVC Material Choice?
- 4. What Are the Common Applications for Rigid and Plasticized PVC?
- 5. Conclusion
How Do Physical Properties Affect PVC Selection in Injection Molding?
Understanding the physical properties of PVC is crucial in selecting the right type for your injection molding needs.
Rigid PVC is chosen for its high hardness and density, ideal for strong and durable products. Meanwhile, plasticized PVC is softer and more flexible due to added plasticizers, making it suitable for flexible items.
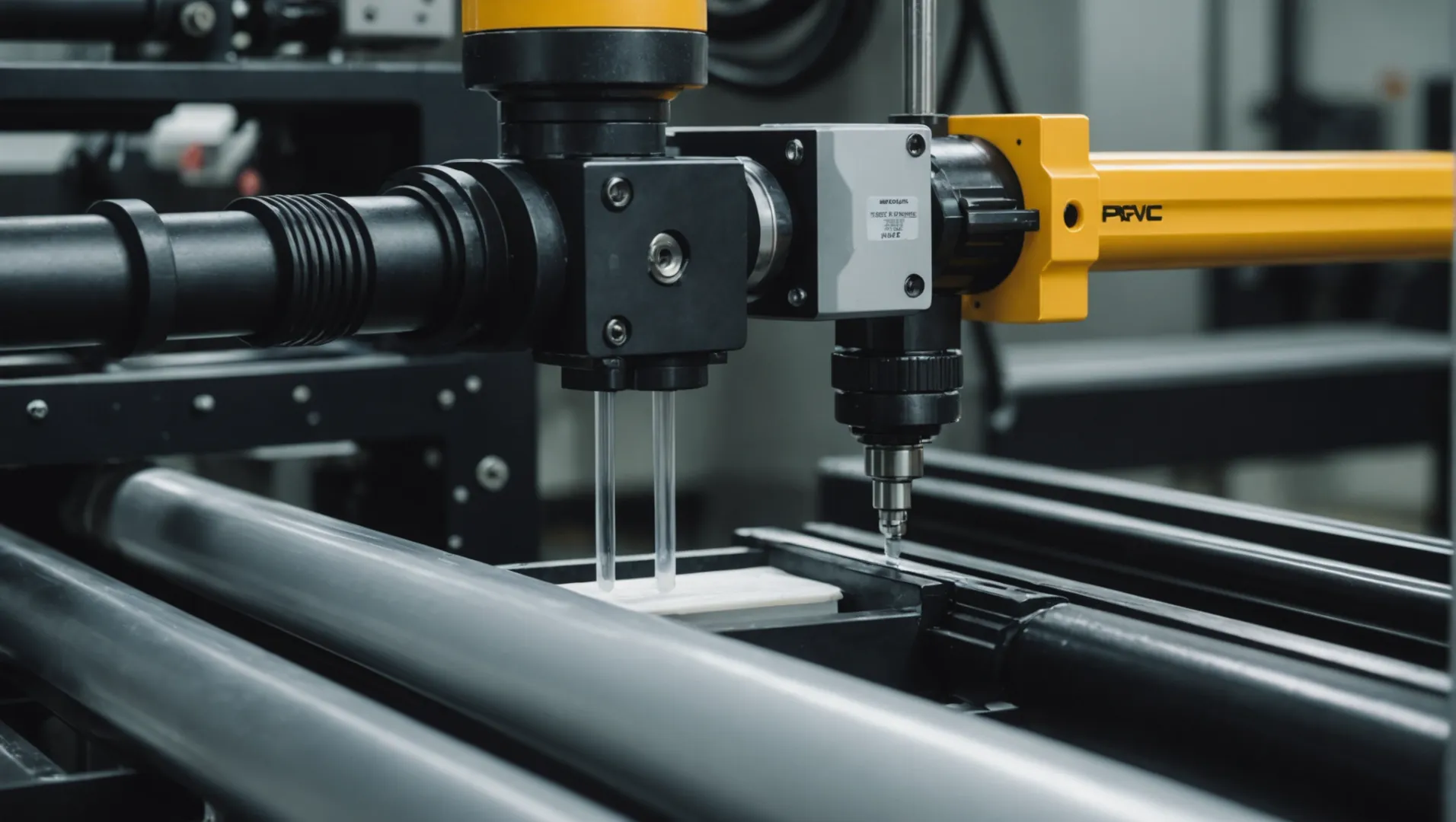
Hardness and Rigidity
When selecting PVC for injection molding, understanding the hardness and rigidity is pivotal. Rigid PVC is renowned for its high hardness and rigidity. This makes it perfect for products that demand a stable shape and significant strength, such as pipes and window frames. Its robust nature ensures longevity and resistance to deformation.
Conversely, Plasticized PVC includes plasticizers that make it softer and more bendable. This property is beneficial for applications requiring flexibility, such as cable sheaths and soft toys. The enhanced pliability allows for innovative design possibilities in products where softness is key.
Density Considerations
The density of PVC can influence material choice in injection molding. The density of Rigid PVC typically ranges from 1.38 to 1.43g/cm³, which contributes to its sturdiness and rigidity. In contrast, Plasticized PVC often exhibits a slightly lower density. This reduction is due to the presence of plasticizers that increase molecular gaps, making the material less dense.
Property | Rigid PVC | Plasticized PVC |
---|---|---|
Hardness | High | Low |
Density | 1.38-1.43 g/cm³ | Lower than rigid |
Implications on Product Design
The implications of these physical properties on product design are significant. For instance, choosing rigid PVC1 for products in environments with high mechanical stress ensures durability and minimal deformation over time.
Meanwhile, opting for plasticized PVC2 can enhance the functionality of products requiring frequent manipulation or flexibility, such as medical tubes or electrical cable coverings.
Ultimately, the selection between rigid and plasticized PVC should align with the specific requirements of your project, factoring in the desired balance between strength and flexibility.
Rigid PVC has higher density than plasticized PVC.True
Rigid PVC's density ranges from 1.38 to 1.43 g/cm³, higher than plasticized.
Plasticized PVC is ideal for products needing high rigidity.False
Plasticized PVC is softer and more flexible, not suited for rigid products.
What Are the Processing Performance Differences Between Rigid and Plasticized PVC?
Understanding the processing performance of PVC types is crucial for efficient manufacturing.
Rigid PVC requires higher temperatures and pressures in injection molding due to poor fluidity, while plasticized PVC benefits from added plasticizers, allowing for easier processing at lower temperatures.
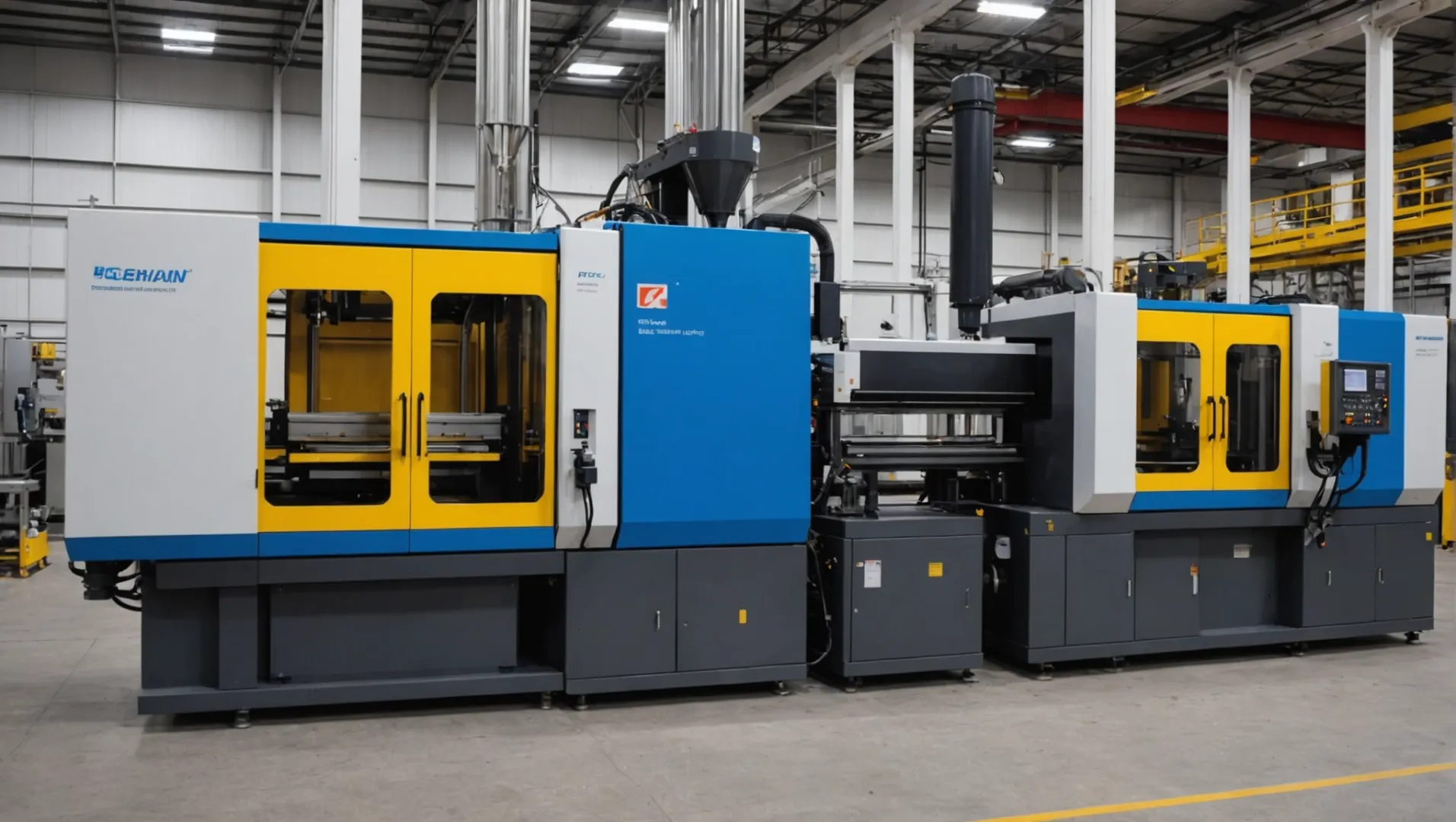
Fluidity in Injection Molding
One of the key differences between rigid and plasticized PVC lies in their fluidity during the injection molding process3. Rigid PVC has relatively poor fluidity, necessitating higher temperatures and pressures to ensure that the melt flows adequately to fill the mold cavity. This requirement not only increases the complexity of the molding process but also places higher demands on the injection molding equipment.
In contrast, plasticized PVC, thanks to the inclusion of plasticizers, exhibits improved fluidity. It can be processed at lower temperatures and pressures, which simplifies the molding process and reduces energy consumption. This characteristic makes it particularly appealing for applications where ease of manufacturing is a priority.
Molding Temperature Variations
The difference in molding temperature between these two types of PVC is another significant factor. Rigid PVC typically requires a higher molding temperature, ranging between 160℃ and 210℃. This high temperature range is critical to ensure proper flow and molding but must be carefully controlled to prevent decomposition or poor product quality.
Plasticized PVC, on the other hand, can be molded at lower temperatures, usually between 120℃ and 180℃. The presence of plasticizers reduces both the softening and melting temperatures of PVC, making it easier to manage during processing and reducing the risk of thermal degradation.
Equipment and Cost Implications
The differences in processing requirements have direct implications on equipment choice and operational costs. Rigid PVC’s need for higher processing temperatures and pressures can lead to increased wear on machinery and higher energy costs. Manufacturers might need to invest in more robust equipment capable of handling these conditions, impacting overall production budgets.
Conversely, plasticized PVC allows for more flexible equipment options, potentially reducing initial machinery investments and ongoing maintenance costs. Its lower processing temperatures also contribute to reduced energy consumption, offering a cost-effective solution for manufacturers focusing on efficiency.
Material Handling Considerations
Handling these materials also differs significantly. Rigid PVC’s lack of flexibility means it must be handled with care to avoid cracking or breaking, especially during post-processing stages like trimming or finishing.
Plasticized PVC, with its enhanced flexibility, offers greater resilience during handling. This characteristic can lead to reduced waste and improved throughput in production lines that involve multiple handling stages or complex shapes.
By understanding these key differences, manufacturers can make informed decisions that optimize production efficiency and product quality based on their specific needs and constraints.
Rigid PVC requires higher molding temperatures than plasticized PVC.True
Rigid PVC needs 160℃ to 210℃, while plasticized PVC needs 120℃ to 180℃.
Plasticized PVC increases equipment wear more than rigid PVC.False
Rigid PVC's high processing demands increase machinery wear more than plasticized.
How Do Chemical Properties Influence PVC Material Choice?
The choice between rigid and plasticized PVC often hinges on their chemical properties, impacting durability and application scope.
Chemical resistance and stability are crucial in selecting PVC types for specific applications. Rigid PVC offers superior chemical corrosion resistance, ideal for harsh environments, while plasticized PVC provides flexibility but may compromise chemical stability due to plasticizers.
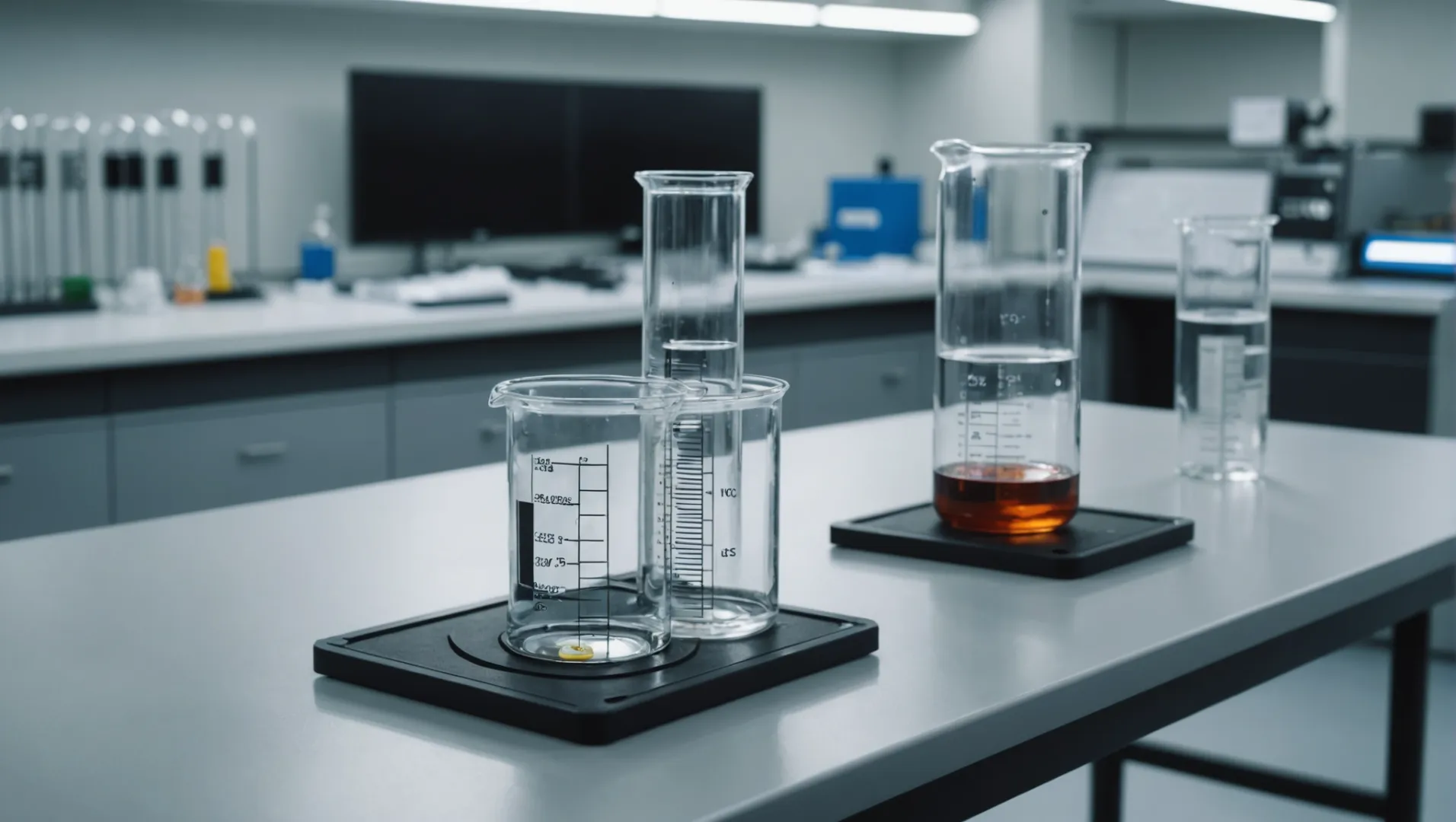
Understanding Chemical Corrosion Resistance
Chemical corrosion resistance is a key factor when selecting PVC materials for environments exposed to chemicals. Rigid PVC4 is renowned for its robust resistance to acids, alkalis, and salts, making it suitable for industries that deal with aggressive chemical substances. This property ensures that products like pipes and storage tanks maintain their integrity over time, reducing maintenance costs.
On the other hand, plasticized PVC incorporates plasticizers that can make it more susceptible to chemical attacks. In environments with highly corrosive substances, these plasticizers might leach out, diminishing the material’s integrity and potentially leading to premature failure.
Evaluating Thermal Stability
Thermal stability is another critical consideration. Rigid PVC maintains good thermal stability within a defined temperature range but can decompose at high temperatures, releasing hydrogen chloride gas. This necessitates strict temperature control during processing and application.
Conversely, plasticized PVC5 tends to have reduced thermal stability due to its composition. Plasticizers, over time, can evaporate or migrate, altering the material’s physical properties and leading to issues like brittleness or deformation.
Comparing Chemical Properties: A Table View
Property | Rigid PVC | Plasticized PVC |
---|---|---|
Chemical Resistance | High resistance to acids, alkalis, and salts | Lower resistance; potential leaching |
Thermal Stability | Good up to a certain temperature | Reduced; affected by plasticizer presence |
Suitability | Harsh chemical environments | Flexible applications with moderate exposure |
Implications for Application Areas
The differences in chemical properties significantly influence where each type of PVC is most effectively utilized. For instance, the robust chemical resistance of rigid PVC makes it a prime candidate for construction and industrial applications where exposure to harsh chemicals is expected.
Plasticized PVC, while not as chemically resistant, excels in applications requiring flexibility and a softer touch. This includes medical supplies such as infusion tubes and blood bags, where a balance between flexibility and moderate chemical exposure is essential.
Choosing the appropriate type of PVC hinges not only on the immediate needs but also on the long-term environmental conditions the material will face. By understanding these chemical properties thoroughly, manufacturers can make informed decisions that enhance product longevity and performance.
Rigid PVC resists chemical corrosion better than plasticized PVC.True
Rigid PVC is known for its high resistance to acids, alkalis, and salts.
Plasticized PVC has superior thermal stability compared to rigid PVC.False
Plasticized PVC has reduced thermal stability due to plasticizer migration.
What Are the Common Applications for Rigid and Plasticized PVC?
The versatility of PVC makes it a staple across numerous industries, offering solutions from construction to medical fields.
Rigid PVC is commonly used in construction for pipes and windows due to its durability, while plasticized PVC finds applications in flexible products like cable sheaths and medical supplies.
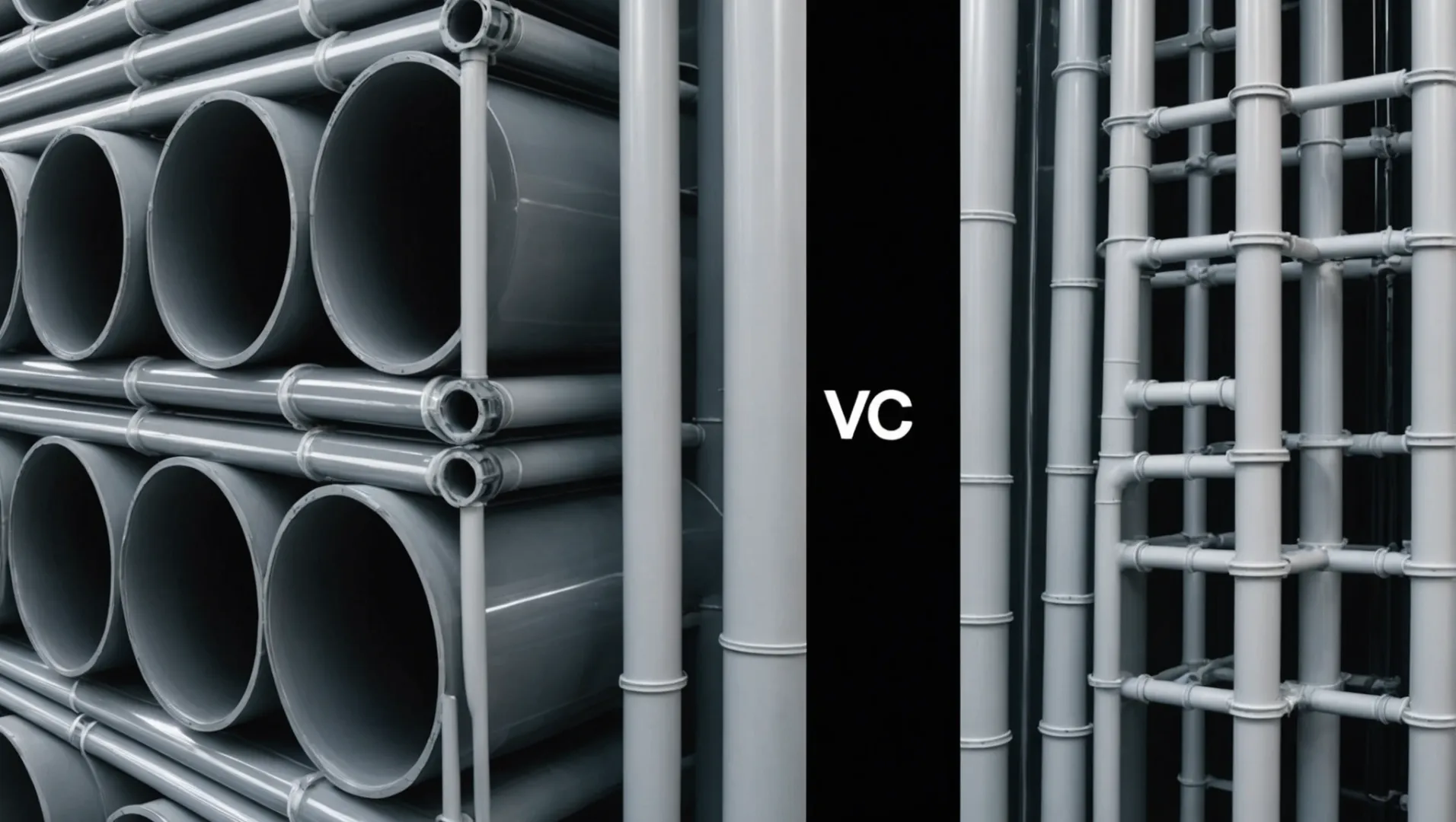
Construction and Industrial Applications of Rigid PVC
Rigid PVC is a favorite in the construction industry due to its high durability and excellent corrosion resistance. It is extensively used in making pipes6, which are integral to plumbing systems, as well as window frames that demand strength and longevity.
In industrial settings, rigid PVC’s chemical resistance makes it suitable for manufacturing chemical equipment and storage tanks. Its stability under electrical conditions also makes it an ideal choice for electrical housings and components like plugs and sockets.
Versatile Uses of Plasticized PVC
Plasticized PVC, enhanced with plasticizers for flexibility, is widely used where bendability is essential. One of its primary applications is in the electrical industry, where it serves as a protective sheath for cables, providing both insulation and durability.
Moreover, plasticized PVC is popular in the production of soft consumer goods such as toys, where a soft touch and flexibility are crucial. The medical industry also benefits from its versatility, utilizing it in the production of disposable items like infusion tubes and blood bags.
Comparing Applications: Rigid vs. Plasticized PVC
Feature | Rigid PVC Applications | Plasticized PVC Applications |
---|---|---|
Durability | Construction materials, industrial tanks | Cable sheaths, toys |
Flexibility | Limited | High – suits medical disposables |
Chemical Resistance | High | Moderate |
While rigid PVC dominates applications requiring structural integrity and chemical resistance, plasticized PVC excels where flexibility and ease of processing are paramount. Explore more7 to discover how these distinct properties are harnessed across various fields.
Understanding the specific needs of your project will guide you in selecting the most suitable form of PVC, ensuring both performance efficiency and cost-effectiveness.
Rigid PVC is used for electrical housings.True
Its stability under electrical conditions makes it ideal for housings.
Plasticized PVC is unsuitable for medical supplies.False
It is widely used in medical disposables like infusion tubes.
Conclusion
Selecting between rigid and plasticized PVC is crucial for project success, impacting performance, flexibility, and costs.
-
Discover how rigid PVC enhances durability and structural integrity.: PVC exhibits excellent durability and resistance to chemicals, fire, and abrasion. PVC also has great dimensional stability and is highly … ↩
-
Explore how flexible PVC improves product adaptability and usage.: What are the pros and cons of rigid & flexible PVC? · Low cost, flexible & high impact strength · Good resistance to UV, acids, alkalis, oils and many corrosive … ↩
-
Explains how PVC behaves during injection molding.: PVC Injection Molding Processing Guide Step-by-Step. PVC material comes in pellet or powder form. The pellets or powder is fed down a barrel and … ↩
-
Discover why rigid PVC excels in resisting harsh chemicals.: Rigid PVC is chemically resistant to many acids, salts, corrosives, bases, fats, and alcohols · The melting point of PVC is low, around 100°C / 212°F) · Maximum … ↩
-
Learn how plasticizers impact PVC’s thermal properties.: The effect of the type of plasticizer and resin on the thermal decomposition of PVC plastisols has been studied by thermogravimetric analysis. ↩
-
Learn how rigid PVC is revolutionizing construction with its durable applications.: PVC is the most used plastic material for building and construction products such as pipes, cables, window profiles, flooring and roofing. ↩
-
Discover detailed comparisons of PVC applications across industries.: Rigid vinyl and Flexible vinyl are both affordable and cost-effective. FPVC is suited for required flexibility and RPVC is best for more rigid applications. ↩