Injection molding might seem straightforward at first glance, but trust me, it’s a world full of intricacies.
The key control points in injection molding of small parts include material selection and processing, mold design and manufacturing, injection molding process parameter control, and quality inspection and control. Mastering these aspects ensures high-quality and consistent production.
While these foundational elements provide a starting point, delving deeper into each component reveals specific techniques and considerations essential for perfecting the injection molding of small parts. Continue reading to uncover expert insights and strategies that can significantly enhance your process.
Material drying prevents defects like bubbles in injection molding.True
Proper drying removes moisture, preventing defects such as bubbles.
How Does Material Selection Affect Injection Molding Quality?
Choosing the right material for injection molding can make or break the quality of the final product.
Material selection directly impacts injection molding quality by influencing strength, appearance, and process efficiency. Selecting materials with suitable characteristics like fluidity, strength, and heat resistance ensures the molded parts meet specific functional and aesthetic requirements, minimizing defects and maximizing performance.

Importance of Material Properties
In injection molding, the properties of the chosen material fundamentally dictate the final product’s quality1. For instance, selecting engineering plastics for parts that demand high strength and heat resistance can prevent deformation under stress. Similarly, materials with excellent gloss and transparency are ideal for parts where appearance is paramount.
Fluidity and Complex Mold Filling
Small parts often feature intricate designs requiring materials with superior fluidity to fill every nook and cranny of the mold accurately. Insufficient fluidity can lead to incomplete filling, resulting in defects such as short shots or air traps. Thus, understanding a material’s flow characteristics is crucial when choosing it for intricate designs.
The Role of Material Drying
Materials like hygroscopic plastics absorb moisture, which can lead to issues like bubbles or silver streaks during molding if not properly dried. Each material has specific drying requirements, which, when adhered to, significantly reduce defects. Ensuring that materials are dried according to supplier specifications is a critical step often overlooked in production.
Material Type | Drying Temperature (°C) | Recommended Time (hours) |
---|---|---|
ABS | 80-90 | 2-4 |
Nylon | 80-100 | 4-6 |
Polycarbonate | 110-130 | 2-3 |
Cost Considerations and Trade-offs
While high-performance materials offer benefits like increased strength and better thermal stability, they also come at a higher cost. It is essential to balance performance with budget constraints, especially in mass production scenarios. Selecting a cost-effective material without compromising on necessary qualities is an art that requires experience and market knowledge.
Environmental Impact and Sustainability
Increasingly, manufacturers are considering the environmental impact of materials. Opting for recyclable or biodegradable plastics can enhance the sustainability of production practices. Additionally, some companies look to reduce waste by selecting materials that allow for minimal scrap during production.
By understanding these aspects of material selection, manufacturers can optimize their injection molding processes to produce high-quality parts while balancing costs and environmental responsibilities.
Material fluidity affects mold filling accuracy.True
High fluidity ensures complete mold filling, reducing defects.
Nylon requires no drying before molding.False
Nylon needs drying at 80-100°C for 4-6 hours to prevent defects.
What Are the Best Practices in Mold Design for Small Parts?
Designing molds for small parts requires precision and expertise to ensure quality and efficiency.
Best practices in mold design for small parts include ensuring high mold accuracy, designing an efficient gate system, incorporating an effective cooling system, and maintaining regular mold maintenance.

Ensuring High Mold Accuracy
When it comes to small parts, dimensional accuracy is non-negotiable. This means that every aspect of the mold design must be meticulously calculated and executed. Utilizing high-precision processing equipment like EDM and wire cutting2 helps achieve the necessary tolerances. These technologies ensure that even the smallest deviation is minimized, which is crucial given that small parts often have stringent dimensional requirements.
Moreover, the choice of material for the mold itself can impact accuracy. High-grade steel or alloys can offer better resistance to wear and tear, maintaining the mold’s precision over repeated uses.
Designing an Efficient Gate System
A well-designed gate system is pivotal for small parts. Gates such as point gates or latent gates are often recommended. These not only help in achieving a smooth surface finish by minimizing gate marks but also ensure that the material fills the mold cavity evenly. This is particularly important in small parts where any inconsistency can lead to defects like voids or weak spots.
Efficient gate design should also consider the flow characteristics of the chosen material, ensuring that it can navigate through complex geometries without issues.
Incorporating an Effective Cooling System
Cooling time directly impacts cycle time and thus production efficiency. An effective cooling system ensures rapid and uniform cooling of small parts, which in turn maintains their dimensional stability and appearance quality. Thoughtful layout of cooling channels can drastically improve cooling rates, reducing cycle times without compromising on quality.
Regular Mold Maintenance
Even the best-designed molds require regular maintenance to function optimally. This includes checking for wear and tear, cleaning to prevent impurities from affecting the mold cavity, and replacing any damaged components promptly. Routine maintenance not only extends the life of the mold but also ensures consistent quality in every batch produced.
Incorporating these best practices into your mold design strategy for small parts can significantly enhance both efficiency and product quality. For further insights into advanced techniques, explore our in-depth resources on mold design3.
High mold accuracy is crucial for small parts.True
Dimensional accuracy ensures quality and efficiency in small part molds.
Regular maintenance is unnecessary for mold longevity.False
Routine checks extend mold life and ensure consistent product quality.
How to Optimize Injection Molding Parameters for Precision?
Precision in injection molding is crucial for the quality and consistency of small parts.
Optimizing injection molding parameters involves precise control of temperature, pressure, speed, and time to ensure high-quality, dimensionally accurate small parts. These adjustments minimize defects and enhance part performance.
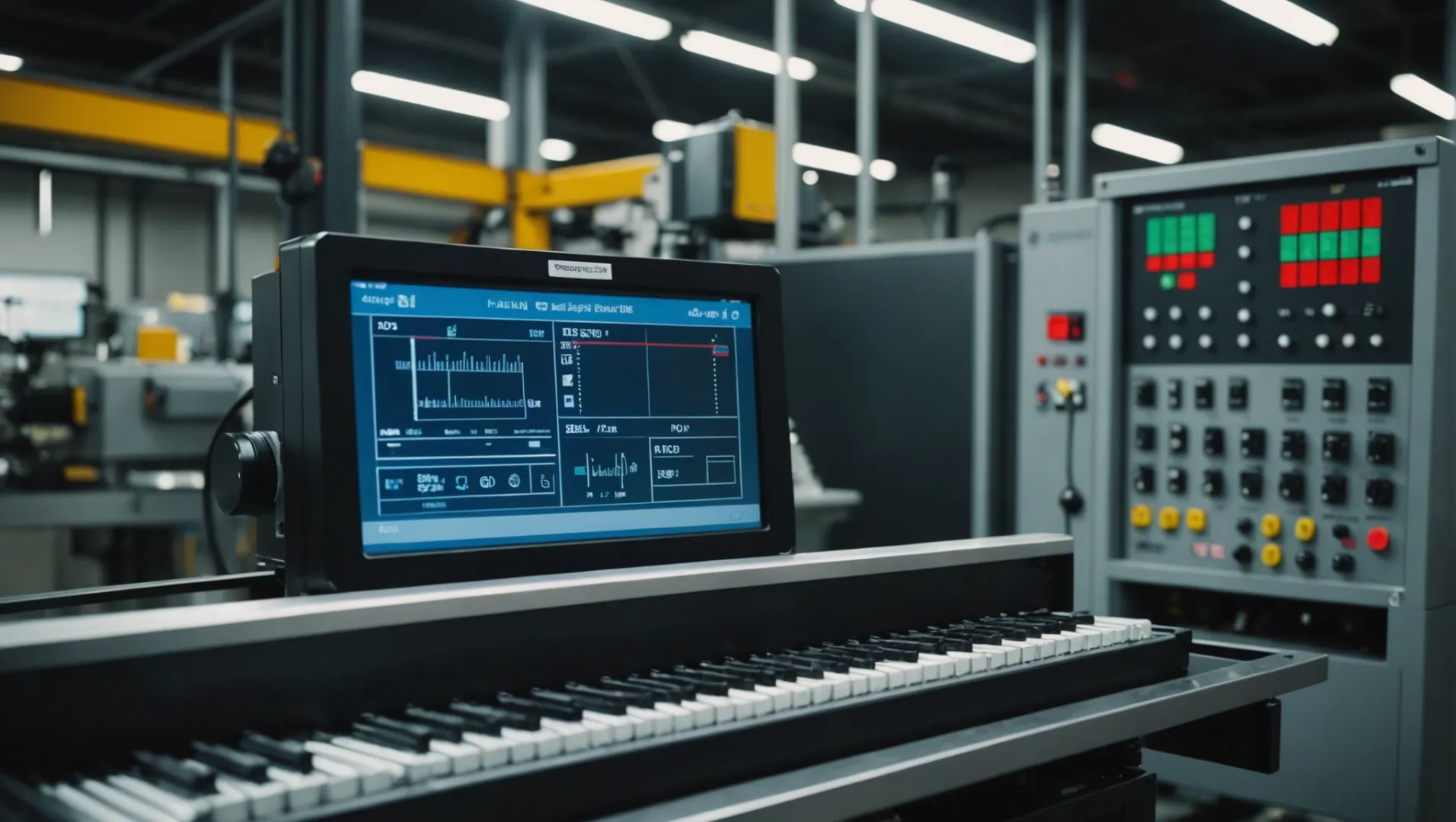
Temperature Control: A Balancing Act
Effective temperature management is a cornerstone of precision in injection molding. Two critical temperature variables are barrel and mold temperatures:
-
Barrel Temperature: Tailor this setting to the material’s characteristics. For instance, an excessively high barrel temperature can lead to material degradation, whereas a low temperature might hinder fluidity.
-
Mold Temperature: This affects both the surface finish and dimensional accuracy of the parts. High mold temperatures are beneficial for surfaces requiring a glossy finish, while consistent temperatures prevent dimensional deviations.
To delve deeper into setting these parameters accurately, consult material-specific guidelines or reach out to suppliers for tailored advice.
Mastering Pressure Parameters
Pressure is another vital factor that can drastically affect the quality of molded parts:
-
Injection Pressure: Should align with the part’s complexity and material flow characteristics. A high pressure might cause defects like flash, while low pressure risks incomplete filling.
-
Holding Pressure: Its duration and intensity influence part stability and shrinkage rates. Proper adjustment here ensures minimal size variation and optimal density.
Speed Control for Optimal Filling
The speed of injection influences both the appearance and integrity of molded parts:
-
Injection Speed: Needs to be carefully calibrated. Rapid injection can result in defects from material splashing, while slow speeds may not fill complex molds adequately.
-
Holding Speed: Should be set to achieve full material compensation during the holding phase, enhancing part density and structural integrity.
Timing It Right: Injection to Cooling
Timing controls are essential for maintaining precision:
-
Injection Time: Adjusted based on part volume and speed, ensuring full cavity filling within the specified duration.
-
Holding Time: Critical for size stability and density. This should match material properties and mold design specifics.
-
Cooling Time: Must accommodate wall thickness and mold temperature to avoid deformation from premature ejection.
For practical insights into these parameters, explore case studies or industry reports that offer data-backed examples of successful parameter optimization. Explore practical examples4.
High mold temperature improves surface gloss.True
High mold temperatures enhance the surface finish, resulting in a glossy appearance.
Low injection pressure reduces part shrinkage.False
Low injection pressure can lead to incomplete filling and increased shrinkage.
Why Is Quality Inspection Crucial in Injection Molding?
Quality inspection is pivotal in injection molding, ensuring defect-free and high-performing products.
Quality inspection in injection molding identifies defects early, ensures dimensional accuracy, and verifies performance standards. This process minimizes waste and optimizes production efficiency, leading to superior end products.

The Importance of Early Defect Detection
Quality inspection in injection molding begins with identifying defects such as flash, bubbles, or shrinkage, which can occur during material drying5 or mold temperature control6. Early detection allows for immediate corrective actions, preventing defective batches and reducing material waste.
Ensuring Dimensional Accuracy
The dimensional accuracy of small parts is critical, especially in industries requiring precision like medical devices or electronics. Inspections using high-precision tools such as three-coordinate measuring instruments ensure that the parts meet strict tolerance levels. This step is crucial given the high requirements for mold accuracy7.
Inspection Type | Tools Used | Purpose |
---|---|---|
Appearance Inspection | Optical Equipment | Detects surface defects |
Dimension Inspection | Precision Measuring Tools | Ensures size conformity |
Performance Inspection | Specialized Equipment | Verifies functionality and durability |
Verifying Performance Standards
Performance inspections assess whether parts can withstand the required stress and environmental conditions. For instance, parts that need high strength and heat resistance are tested for these characteristics to ensure they meet the necessary standards.
Process Monitoring and Control
Ongoing monitoring of process parameters such as temperature, pressure, and speed is essential for consistent quality. Regular checks and maintenance of raw materials, molds, and equipment help sustain smooth operations. These practices are vital for maintaining process stability and ensuring high-quality outcomes.
Incorporating quality inspection throughout the injection molding process not only safeguards against defects but also enhances overall efficiency, paving the way for producing reliable and top-notch products.
Early defect detection reduces material waste.True
Identifying defects early prevents defective batches, minimizing waste.
Dimensional accuracy is less critical in electronics.False
High precision is crucial in electronics for part compatibility and function.
Conclusion
Mastering these control points will not only elevate your production quality but also instill confidence in your processes.
-
Explore deeper into how different materials affect injection molding outcomes.: Learn how to select the right material for your injection molding design with this technical overview of thermoplastic resins. ↩
-
Discover how EDM and wire cutting enhance mold accuracy.: Both can be wire-cut with ease and accuracy. Inserts tapered in this manner need no shoulder, heel or mounting screws to secure them, but when … ↩
-
Explore innovative methods to optimize mold design for small parts.: Design more engaging and efficient parts, and reduce production costs, with these tips · Clips and snap fits · Living hinges · Bosses and stand offs · Text on parts … ↩
-
Gain insights from real-world examples for practical parameter adjustments.: Two case studies are illustrated in order to demonstrate the implementation of the suggested frameworks and to compare among these optimization methods. This … ↩
-
Learn how proper material drying prevents defects like bubbles and silver wires.: Drying plastic resin is used to minimize or eliminate complications that may be caused by too much moisture in a plastic material. ↩
-
Understand how mold temperature affects part appearance and dimensional accuracy.: Temperature control units are used to preheat the mold and then to keep the mold at the temperature set point by circulating coolant (water or oil) through the … ↩
-
Discover why precise mold accuracy is crucial for high-quality small parts.: Generally, the dimensional tolerance of precision injection mold should be controlled below 1/3 of the product dimensional tolerance. ↩