Have you ever wondered how to make those plastic parts sound just right?
Optimize acoustic properties in injection molding by selecting sound-dampening materials, refining mold design to reduce vibration, and precisely adjusting temperature and pressure settings to enhance sound quality.
I remember working on a project where the client needed a sleek yet quiet casing for their new line of speakers. The challenge was real, but by experimenting with different materials and tweaking the mold design to minimize unwanted vibrations, we achieved the perfect harmony. It’s fascinating how a small adjustment in temperature or pressure can turn a noisy rattle into a pleasant hum. These tweaks might seem minor, but they can make all the difference in creating products that not only look great but sound even better.
Material selection impacts acoustic properties in molding.True
Choosing materials with sound-dampening qualities enhances acoustic performance.
Mold design does not affect acoustic outcomes.False
Mold design influences vibration and resonance, affecting acoustics.
Which materials excel in acoustic optimization for injection molding?
Ever wondered how to make your molded products sound just right? Picking the right materials for acoustic optimization can be the secret sauce.
Polypropylene, ABS, and nylon are ideal for acoustic optimization in injection molding, effectively minimizing noise and vibrations for sound-sensitive applications.
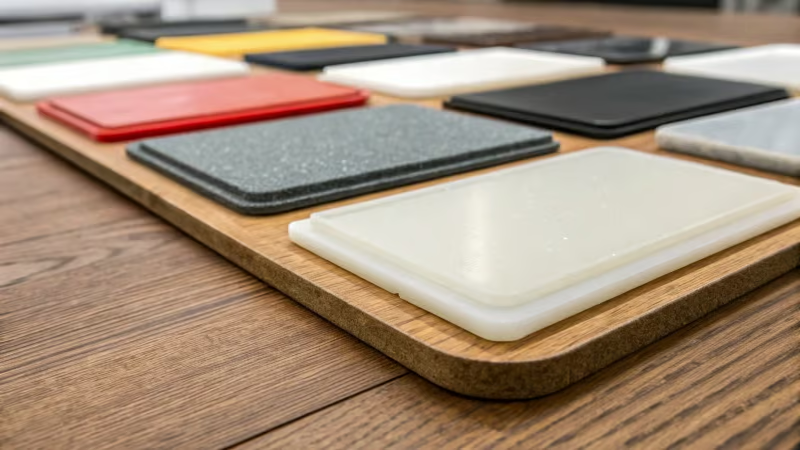
Understanding Acoustic Properties
As someone who’s spent countless hours designing products that need to sound as good as they look, I know firsthand how crucial it is to choose the right materials for acoustic optimization. Whether it was trying to reduce that annoying road noise in car interiors or ensuring that a speaker housing doesn’t vibrate like a tambourine, I’ve learned that density, stiffness, and damping are the holy trinity of acoustics. These factors aren’t just numbers on a spec sheet—they’re the key to ensuring your design sings.
Key Material Attributes:
Attribute | Importance |
---|---|
Density | Affects sound absorption capability |
Stiffness | Influences vibration transmission |
Damping | Reduces noise by dissipating energy |
Material Options for Acoustic Optimization
- Polypropylene (PP): I remember my first automotive project where we used PP to dampen road noise. Its lightweight and flexible nature made it perfect for reducing those pesky vibrations.
- ABS (Acrylonitrile Butadiene Styrene): This material is like the unsung hero in consumer electronics. It combines toughness with excellent acoustic properties, ideal for creating housing that doesn’t buzz.
- Nylon (Polyamide): Nylon has always been my go-to for precision components that demand strict acoustic control. It’s rigid enough to absorb vibrations effectively.
- Thermoplastic Elastomers (TPE): With TPEs, I could finally add that soft touch to my designs without compromising on vibration damping—a win-win for grips or mounts.
Exploring Advanced Composites
Diving into composites opened a whole new world of possibilities. By mixing polymers with fillers or fibers, like adding glass fibers to polypropylene, you can significantly enhance acoustic properties without adding much weight. I learned that picking the right filler and ensuring it blends well with your polymer matrix can turn a good design into a great one.
Consideration of composites should involve:
- Type of filler: Glass, carbon, or other fibers.
- Volume fraction: The proportion of filler impacts acoustic performance.
- Compatibility: Ensuring that the composite works harmoniously with the chosen polymer matrix.
Learn more about composite material properties1 and their applications in acoustics.
Best Practices for Material Selection
Selecting materials is not just about ticking boxes; it’s about understanding where and how your product will be used. From handling temperature variations that might affect performance to ensuring the final product looks as good as it sounds, every detail counts. Balancing aesthetic requirements with manufacturing constraints is an art form that I’ve come to appreciate over the years.
Explore the impact of environment on materials2 and how to optimize your selection process accordingly.
By weaving these considerations into your design process, you can achieve remarkable acoustic performance in your molded products. It’s a journey of discovery but one that’s immensely rewarding when you hear the results.
Polypropylene offers good damping properties.True
Polypropylene is lightweight and flexible, enhancing its damping ability.
Nylon is unsuitable for precise acoustic control.False
Nylon's rigidity and vibration absorption make it ideal for acoustic control.
How Does Mold Design Affect Acoustic Properties?
Ever wondered how the design of a mold could shape the way we hear sound? Dive in to explore this fascinating connection!
Mold design impacts acoustic properties by altering surface texture and density, thus affecting sound absorption and transmission. Careful design adjustments can enhance or reduce acoustic performance based on specific application requirements.
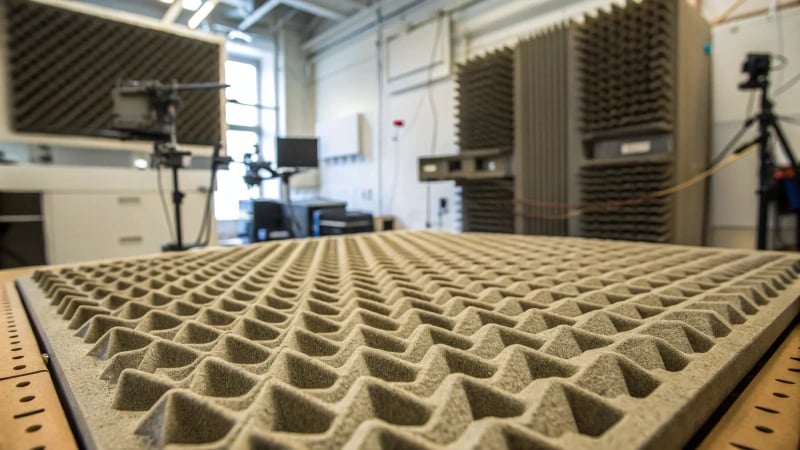
The Role of Surface Texture
I remember the first time I encountered the impact of mold texture on sound. It was during a project where we were designing speaker casings. We had this moment of realization: a textured mold could break up sound waves, reducing echoes and enhancing clarity. The feeling was like discovering a hidden treasure. Consider the textured molds3 used in speaker casings, which are crucial in shaping how sound behaves.
Material Density and Its Impact
Choosing the right material feels like balancing on a tightrope. In one of my early projects, I opted for a denser material, thinking it would offer better durability. Little did I know, it reflected sound, creating an unwanted echo. That’s when I learned that lighter materials, like foam, are champions at absorbing sound.
Material Type | Acoustic Effect |
---|---|
Dense (e.g., metal) | Sound reflection |
Light (e.g., foam) | Sound absorption |
It’s about finding that sweet spot in mold design to achieve desired acoustic outcomes4.
Innovative Techniques in Mold Design
The world of mold design is ever-evolving, much like our favorite gadgets. I recall experimenting with 3D-printed molds5 that allowed us to incorporate complex geometries into our designs. This innovation opened up a whole new world for us, enabling intricate patterns that optimize sound dispersion like never before.
These advancements open up new possibilities for designing acoustically optimized products across various industries.
Applications in Consumer Electronics
In consumer electronics, achieving optimal acoustic performance is like hitting a high note. I’ve worked on smartphones and laptops where precision in mold design directly impacted audio quality. The goal was to ensure that these devices delivered clear sound without compromising on compactness.
Designers must consider6 this delicate interplay between form and function to ensure high-quality sound in compact devices.
Through understanding these principles, I’ve seen firsthand how well-crafted molds can lead to superior acoustic performance, setting products apart from the competition. It’s a journey that continues to inspire and challenge me every day.
Textured molds improve sound clarity in speaker casings.True
Textured surfaces disperse sound waves, reducing echoes and enhancing clarity.
Denser materials in mold design absorb more sound.False
Denser materials reflect sound waves, while lighter ones absorb them.
What process parameters influence sound quality?
Ever wondered why some products sound like a dream while others fall flat? As a designer, I know firsthand how critical sound quality is and which parameters make all the difference.
Material properties, manufacturing precision, and environmental conditions are key process parameters that influence sound quality by shaping the overall audio experience essential for superior design.
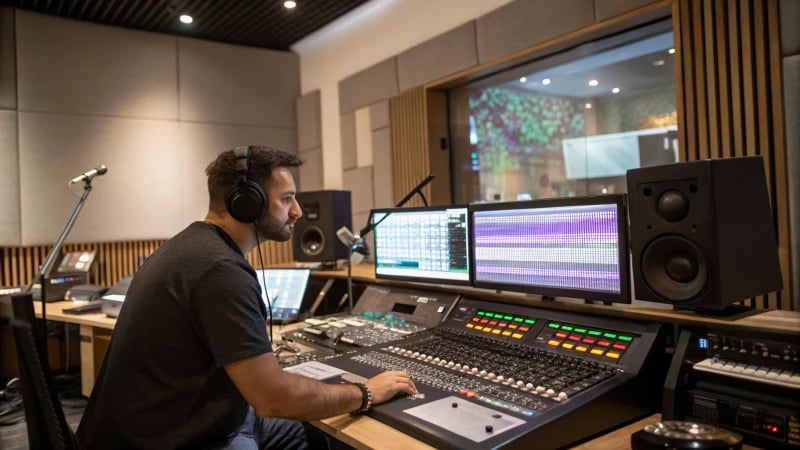
Material Properties
Choosing the right material feels like picking the perfect guitar for a gig. The density and elasticity of materials used in speaker housings7 or enclosures can make or break the resonance and vibrational damping. I’ve found that denser materials typically offer better sound insulation, cutting down on those pesky unwanted reverberations. It’s a bit like finding that sweet spot where your voice echoes just right in an empty room.
Material | Density (kg/m³) | Impact on Sound Quality |
---|---|---|
Plastic | 900-2200 | Moderate vibration control |
Aluminum | 2700 | Good resonance reduction |
Wood | 600-1000 | Excellent acoustic warmth |
Manufacturing Precision
Manufacturing precision is like ensuring every note in a symphony is perfectly in tune. Processes such as CNC machining or injection molding have taught me that even minor tolerances can lead to air leaks or misalignments in acoustic systems8. It’s akin to having an instrument slightly out of tune—everything sounds just a bit off.
- Tolerances: Keeping strict tolerances ensures parts fit together seamlessly, enhancing sound quality.
- Surface Finish: A smoother finish can improve the flow of sound waves, reducing distortion.
Environmental Conditions
Environmental factors are the wild cards in our deck. I’ve noticed that temperature and humidity can dramatically affect materials, causing them to expand or contract. This is particularly true with wooden enclosures, which can warp under high humidity, much like how my hair reacts to a rainy day! Understanding these interactions allows me to design products that perform consistently, no matter what Mother Nature throws at us.
Utilizing advanced CAD software has been my go-to for simulating these conditions and tweaking designs before jumping into physical prototyping. Simulations9 provide valuable insights into how changes in parameters might affect sound quality, allowing for preemptive adjustments.
When designing for high-quality audio outputs, it’s crucial to consider these factors, keeping in mind the audience’s expectations10 and the specific use case of the product. Each parameter is like a volume knob that can be adjusted for enhanced audio performance.
Denser materials improve sound insulation.True
Denser materials reduce unwanted reverberations, enhancing sound quality.
Humidity has no effect on sound quality.False
High humidity can warp wooden enclosures, affecting audio performance.
How Can Post-Processing Transform Your Audio?
Have you ever felt like your audio could use a little magic to make it truly stand out?
Post-processing enhances audio by adjusting frequencies with equalization, reducing noise, and adding reverb, resulting in clearer, more professional sound quality.
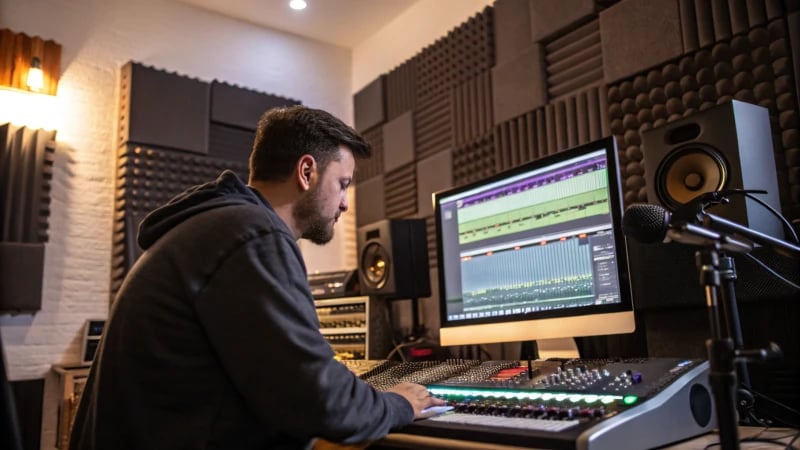
Understanding Post-Processing in Audio
When I first dipped my toes into audio production, I was fascinated by how post-processing could turn a simple recording into something mesmerizing. It’s like giving your audio a makeover, refining it after the initial recording phase. This involves enhancing clarity and richness through several techniques. For instance, equalization (EQ) is one such tool that lets me adjust the balance of frequency components, allowing me to fine-tune specific sounds11 within my audio mix. It’s like painting with sound—each adjustment adds a layer of depth and emotion.
Techniques for Enhanced Acoustic Characteristics
-
Equalization (EQ):
I remember the first time I played around with EQ; it felt like sculpting sound waves. By boosting or cutting specific frequency ranges, I could create a balanced harmony where no single frequency overwhelmed the others. Picture boosting the bass to give it that warm, enveloping feel, or reducing the high frequencies to tame the harshness. It’s akin to seasoning a dish just right. -
Noise Reduction:
Unwanted noise can be as annoying as a mosquito buzz at night. I’ve learned to appreciate the beauty of silence, especially when advanced noise reduction tools can identify and eliminate noise12 without touching the main content. It’s like cleaning up clutter from a beautiful room. -
Reverb and Echo:
Adding reverb is one of my favorite techniques—it creates an illusion of space, making audio feel grand and immersive. Whether I’m aiming for the acoustics of a grand hall or a cozy room, reverb adds that necessary ambience. In music production, it’s the secret ingredient that can transport listeners to another world. -
Compression:
Compression is like having a conversation where everyone gets to speak clearly. It balances the dynamic range of your audio, ensuring softer parts are audible while preventing louder sections from distorting. This results in a more consistent listening experience.
Technique | Purpose |
---|---|
Equalization (EQ) | Balances frequencies |
Noise Reduction | Removes unwanted sounds |
Reverb | Adds depth and ambience |
Compression | Controls dynamic range |
Practical Applications of Post-Processing
In music production, I’ve seen how post-processing can transform raw recordings into polished tracks that are ready for distribution—it’s like turning rough sketches into masterpiece paintings. In fields like podcasting or broadcasting, these techniques ensure that voice clarity remains at its peak, engaging the audience throughout the session.
Moreover, immersive audio experiences13 benefit greatly from post-processing, providing listeners with an auditory environment that’s not just heard but felt. The first time I listened to a track with expertly applied post-processing, I realized how deeply sound can affect us emotionally—making every note more vibrant and every pause more poignant.
Equalization boosts bass for a fuller sound.True
EQ can enhance audio by increasing bass, enriching the sound.
Noise reduction increases unwanted sounds in audio.False
Noise reduction decreases unwanted sounds, improving audio quality.
How are acoustic innovations changing molded parts?
When I first heard about acoustic enhancements in molded parts, I was intrigued by how these innovations could transform my designs.
Acoustic innovations, including thermoacoustic composites and micro-perforated surfaces, are revolutionizing molded parts by improving sound absorption and insulation, benefiting industries like automotive and consumer electronics with enhanced acoustic performance.
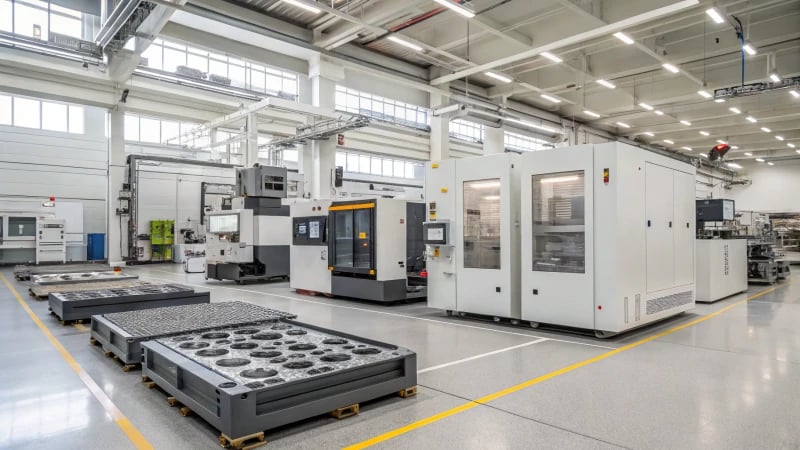
Advanced Material Technologies
I remember the first time I worked with thermoacoustic composites14. It was like discovering a secret weapon against noise! These materials magically turn sound into heat, dramatically cutting down unwanted noise. For someone like me, who’s always on the lookout for lightweight yet robust solutions in automotive design, they were a game-changer.
Material | Benefits |
---|---|
Thermoacoustic | Lightweight, efficient |
composites | sound absorption |
Micro-Perforated Surfaces
Then there’s the innovation of micro-perforated panels. Imagine tiny, perfectly crafted holes capturing sound waves like a spider’s web. It’s fascinating how these can significantly dampen noise. In my work with consumer electronics, where every millimeter counts, these panels have become indispensable for optimizing space without sacrificing sound control.
Sustainability in Acoustic Design
Incorporating sustainable materials15 into my projects has always been a priority. Not only does it feel great to use recycled or eco-friendly components, but these materials also boost acoustic properties. I’ve found natural fibers particularly effective—they absorb sound beautifully while meeting all the regulatory standards we strive for.
Integration of Acoustic Layers
Layering acoustic materials within molded parts16 allows me to tailor sound profiles to perfection. By playing with different material densities, I can create specific acoustic responses that are crucial for high-quality custom audio equipment. It’s like having an artist’s palette for sound!
Emerging Applications
These innovations aren’t just for traditional uses; they’re expanding into exciting new areas like smart home devices17. It’s incredible how acoustic enhancements are improving user experiences by ensuring clear communication and minimal interference in smart ecosystems.
These breakthroughs highlight a shift towards designs that are not only functional but also aesthetically pleasing and sustainable. It’s thrilling to be part of this evolution in molded components, where everything comes together seamlessly.
If you’re curious about these technologies in action, check out recent case studies showcasing their application across various industries. They’ve been an endless source of inspiration for me, pushing me to innovate further in my own projects.
For more insights, dive into resources focused on material science and its impact on product acoustics. Trust me; understanding these principles can significantly enhance your design capabilities and outcomes.
Thermoacoustic composites are lightweight and efficient.True
Thermoacoustic composites convert sound into heat, reducing noise efficiently.
Micro-perforated panels decrease acoustic performance.False
Micro-perforated panels enhance acoustic performance by trapping sound waves.
Conclusion
Optimize acoustic properties in injection molding by selecting sound-dampening materials, refining mold designs, and adjusting processing parameters to enhance product sound quality and performance.
-
Understand how composites enhance acoustic properties through fillers and fibers. ↩
-
Learn how environmental factors affect material performance in injection molding. ↩
-
Explore how textured molds enhance sound clarity in speaker designs by dispersing sound waves effectively. ↩
-
Learn how different material densities affect sound absorption and reflection, crucial for optimizing acoustic performance. ↩
-
Discover how 3D printing technologies enable intricate mold designs that improve acoustic properties through innovative geometries. ↩
-
Understand the balance of form and function in designing consumer electronics for optimal sound quality. ↩
-
Explore how different materials in speaker housings affect acoustic performance. ↩
-
Learn why precise manufacturing is vital for maintaining sound clarity in audio products. ↩
-
Discover how simulations help predict and enhance audio design outcomes. ↩
-
Find out what consumers expect from audio quality in electronic devices. ↩
-
Discover methods to fine-tune specific sounds within your audio mix for optimal balance. ↩
-
Explore advanced algorithms that identify and eliminate noise without affecting main content. ↩
-
Learn how post-processing enhances immersive audio, creating engaging auditory environments. ↩
-
Learn how thermoacoustic composites are revolutionizing noise reduction in automotive applications. ↩
-
Discover how sustainable materials are enhancing acoustic properties in modern design. ↩
-
Explore how layering different materials can tailor acoustic properties in molded designs. ↩
-
Understand the role of acoustic enhancements in improving smart home device performance. ↩