Ever wonder how much it truly costs to make each piece in injection molding?
Calculate injection molding cost per part by summing material, mold, processing, packaging, and transportation costs, using precise data for accuracy.
I remember when I first dived into injection molding; it was like solving a complex puzzle. Each piece of the cost calculation has its own story—like material costs, where understanding how much plastic you need can feel like a chemistry experiment. Let’s take a deeper look at each component to make sense of it all and improve your cost estimation skills.
Material cost is the largest expense in injection molding.False
While significant, material cost isn't always the largest expense; mold and processing costs can be higher.
Accurate data is essential for precise cost estimation.True
Using precise data ensures each component's cost is correctly calculated, affecting overall estimation accuracy.
- 1. What Factors Affect Material Costing in Injection Molding?
- 2. How is mold cost sharing calculated for each product?
- 3. What Are the Key Components of Injection Molding Processing Costs?
- 4. How Do Packaging and Transportation Costs Impact Overall Production Costs?
- 5. What Tools Can Help Accurately Estimate Injection Molding Costs?
- 6. Conclusion
What Factors Affect Material Costing in Injection Molding?
Ever wondered why injection molding costs can feel like a tangled web? Let’s untangle it together.
Material costing in injection molding is influenced by material usage, unit costs, mold investments, processing, packaging, and shipping expenses, all contributing to the overall cost.
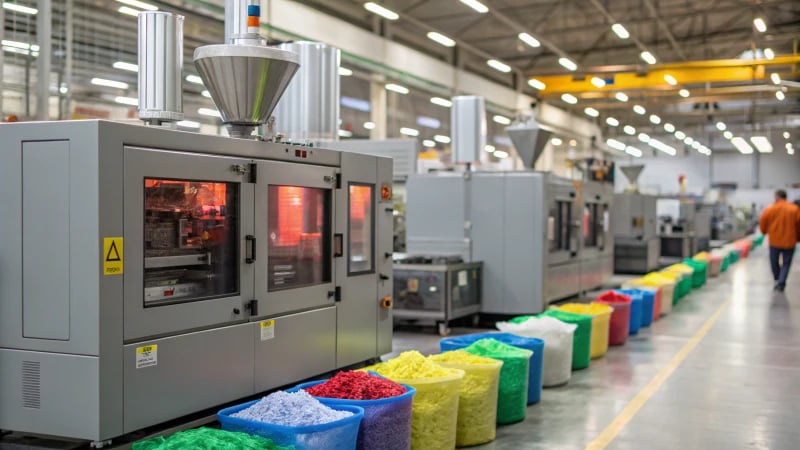
Determining Material Usage and Costs
Understanding how much material goes into injection molding is like baking your favorite cake—you’ve got to know your ingredients! It all begins with the product’s volume and material density. I remember the first time I used 3D modeling software1 to estimate the volume of a tricky, irregular shape. It felt like solving a puzzle! You just multiply the volume by the density and unit price to get your material cost.
Product Volume | Material Density | Material Used | Unit Cost | Material Cost |
---|---|---|---|---|
10 cm³ | 1.2 g/cm³ | 12 g | $0.002/unit | $0.024 |
Mold Cost Sharing
Sharing mold costs is like splitting a pizza bill with friends—everyone gets a slice! The total investment in molds includes everything from design to logistics. I learned this the hard way when budgeting for my first big project. We divided this by our expected production volume, which gave us the mold cost per product. For instance, if you spend $6,000 and expect 100,000 items, that’s just $0.06 per item.
Injection Molding Processing Costs
Energy Costs: Picture your injection molding machine like a hungry beast consuming energy. Calculate its power consumption and production time. One time, I calculated it for a machine that consumed 10 kW and took 30 seconds per item. It came out to $0.083 per unit.
Labor Costs: Don’t forget about labor. If a worker earns $6/hour and produces 60 products hourly, that’s $0.1 per item—a tidbit I learned while managing production schedules.
Equipment Depreciation: Equipment wears down just like an old pair of shoes. With a $30,000 machine and a 10-year lifespan, depreciation affects each product’s cost.
Additional Costs: Packaging and Transportation
Packaging is more than just bubble wrap—it’s about materials and labor costs too. And let’s not ignore transportation, which depends on logistics choices. I recall shipping a batch costing $1,000 for 10,000 products—simple math told me it was $0.1 per item.
Comprehensive Costing
Bringing all these elements together paints a clearer picture of injection molding costs. From mold design2 to transportation, every detail counts when optimizing budgeting and planning for production. It’s all about finding that perfect balance.
3D modeling software estimates material volume.True
3D modeling software helps accurately calculate volumes for irregular shapes.
How is mold cost sharing calculated for each product?
Navigating the maze of mold cost sharing can feel daunting, but it’s a crucial step for any manufacturer looking to keep production costs in check. Let’s break it down together.
Mold cost sharing distributes the total mold investment across its service life, allocating costs per product based on projected production units to ensure equitable cost distribution.
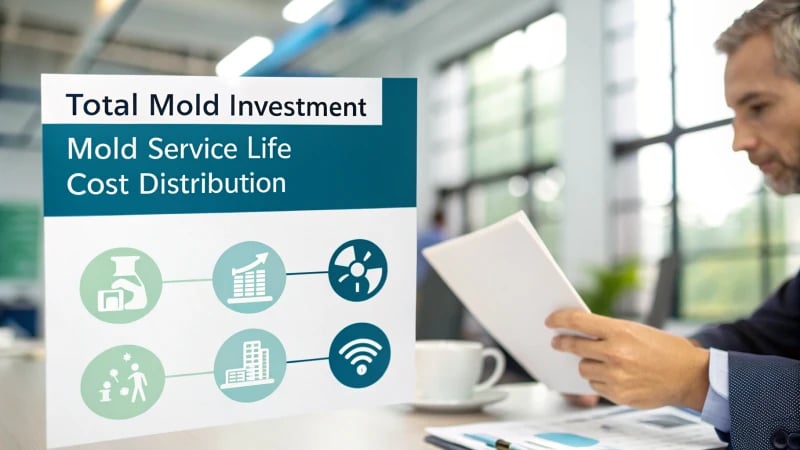
Material Costing
I remember the first time I had to figure out material costs for a project—my mind was racing with numbers! But once I got the hang of it, it was like solving a puzzle. For example, estimating the material needed starts with calculating the product’s volume3, which can be done using geometric formulas or 3D modeling. Take a product with a volume of 10 cm³ and plastic density of 1.2 g/cm³; that’s 12 grams of material. If the plastic costs $2/kg, the material cost per product comes out to $0.024.
Mold Cost Sharing
Now, let’s talk about mold investment. When I think back to my first big project, I had no idea how much went into designing and manufacturing a mold. It was a real eye-opener! Calculating total mold investment involves summing up design, manufacturing, transportation, and commissioning costs. Say these total $6,000, and your mold produces 100,000 products—each product then bears a cost of $0.06.
Injection Molding Processing Costs
Energy Costs
Energy costs are another piece of the puzzle. Imagine a machine that uses 10 kW and electricity at $1/hour—producing one item in 30 seconds costs $0.083.
Labor Costs
Then there’s labor. I once worked alongside a team where we all pitched in ideas on how to streamline labor costs. If a worker earns $6/hour and produces 60 items in that hour, each item carries a labor cost of $0.1.
Equipment Depreciation and Maintenance Costs
Depreciation and maintenance can’t be ignored either. With a $30,000 machine expected to churn out 100,000 items yearly, plus $3,000 annual maintenance, the depreciation and maintenance per product is $0.06.
Packaging and Transportation Costs
Packaging Costs
Packaging costs add up quickly too. Combine $0.2 for materials and $0.05 for labor per product; you’re looking at $0.25.
Transportation Costs
And transportation? It’s all about efficiency—shipping 1,000 products at a total cost of $1,000 means each product’s share is $1.
Understanding these aspects helps create accurate budgets and optimize injection molding4 processes by diving into these calculations; manufacturers can price their products competitively and ensure every item pulls its weight in production costs.
Cost Component | Calculation Detail | Cost per Product |
---|---|---|
Material Cost | 12 grams x ($2/kg ÷ 1000) | $0.024 |
Mold Cost | Total mold cost ÷ Lifetime output | $0.06 |
Energy Cost | Machine power x Production time | $0.083 |
Labor Cost | Worker wage ÷ Products per hour | $0.1 |
Depreciation & Maintenance | Total annual cost ÷ Expected annual output | $0.06 |
Packaging Cost | Packaging material + Labor | $0.25 |
Transportation Cost | Total shipping ÷ Batch size | $1 |
By analyzing these costs in detail, manufacturers can make informed decisions on pricing and production strategies ensuring competitiveness5.
What Are the Key Components of Injection Molding Processing Costs?
Ever wondered how injection molding costs pile up? Let’s explore the nitty-gritty details that shape your budget.
Injection molding costs are influenced by material expenses, mold fees, energy use, labor, equipment depreciation, maintenance, packaging, and transportation, all of which contribute to the final unit price.
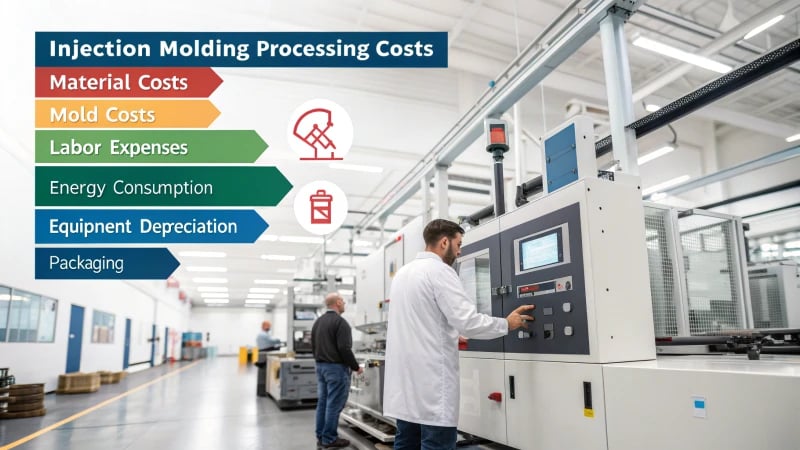
I remember the first time I dove into the world of injection molding—it felt like stepping into an entirely new universe of materials and machinery. I was overwhelmed by the sheer number of elements that could affect costs. Here’s a breakdown of what I learned and how each component plays its part in shaping those numbers.
Material Costs
Material costs hinge on two things: the weight and type of plastic used. I recall a project where I spent an entire afternoon calculating volumes using 3D modeling software, a skill that became invaluable for irregular shapes. You’d calculate the volume of your product and multiply it by the material’s density to get the required amount. Then, factor in the purchase price to find your unit cost6. It’s a bit like solving a puzzle!
Component | Calculation | Example |
---|---|---|
Weight (grams) | Volume x Density | 10 x 1.2 = 12g |
Unit Cost (USD) | Purchase Price/kg | $2/kg |
Material Cost | Weight x Unit Cost | 12 x 0.002 = $0.024 |
Mold Cost Sharing
Mold costs can be hefty, covering design, manufacturing, and commissioning expenses. I learned to spread these costs over the expected production volume—a tip from a mentor that saved me countless headaches.
- Total Investment: This includes everything from design to transportation.
- Service Life: Divides costs over expected production.
- Example: A mold costing $6,000 for 100,000 items means each unit costs $0.06.
Energy and Labor Costs
Energy expenses arise from electricity usage. I once tracked down every watt consumed during a particularly power-hungry project! Labor involves hourly wages divided by output rate—a stark reminder of how every second counts.
Cost Type | Formula | Example |
---|---|---|
Energy (per unit) | Power x (Time per unit) x Electricity | 10 kW x (1/120) x $1 = $0.083 |
Labor (per unit) | Hourly Wage / Units per hour | $6/ 60 = $0.1 |
Equipment Depreciation and Maintenance
Depreciation sneaks up on you like those sneaky maintenance surprises on my old car! Here, it’s about dividing the purchase price by total production and adding annual maintenance costs.
- Depreciation: Divided by total production.
- Maintenance: Annual costs over production.
- Example: Total $0.06 per unit from both factors.
Packaging and Transportation
Packaging and transport can be overlooked but trust me, they add up quickly! Packaging involves materials and labor; transportation varies by method and distance.
- Example Packaging: $0.2 materials + $0.05 labor = $0.25.
- Example Transport: Total $1000 for 1000 products; each $1.
With all these components, you can see how they contribute to a detailed breakdown of injection molding costs. They’re not just numbers—they’re stories of every project I’ve tackled, helping me plan financially and manage costs effectively. As designers7 will tell you, understanding these factors is key to successful manufacturing projects.
Material costs depend solely on the plastic type used.False
Material costs depend on both the weight and type of plastic used.
Mold cost is shared across the production volume.True
Mold costs are divided by the total expected production volume.
How Do Packaging and Transportation Costs Impact Overall Production Costs?
Ever wonder how those boxes and trucks affect the price of your favorite gadgets? Let’s dive into the nitty-gritty of packaging and transportation costs and see how they shape the final price tag.
Packaging and transportation costs significantly influence overall production expenses, affecting material, labor, and logistics. Efficient management is vital for competitive pricing and profit maximization.
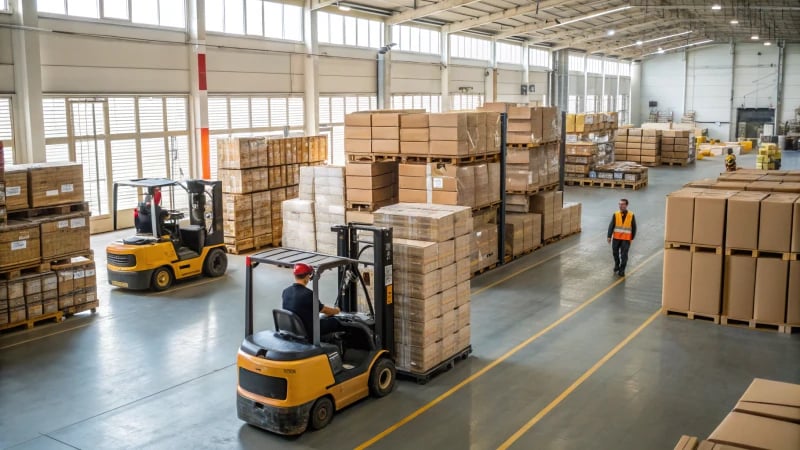
The Role of Packaging Costs
I remember my first big project like it was yesterday—designing packaging for a line of sleek gadgets. At first, I thought, "How hard can it be?" Just wrap it up, slap a logo on it, and ship it out, right? Oh, how wrong I was. Packaging isn’t just a pretty face; it’s the armor protecting our product through its journey to the customer.
Calculate the cost of materials8 and labor required to package each product. For instance, using $0.2 worth of materials and $0.05 for labor per unit might seem trivial. But when you’re talking thousands of units, those nickels and dimes add up fast.
Component | Cost per Unit |
---|---|
Materials | $0.20 |
Labor | $0.05 |
Total | $0.25 |
This illustrates how small increments can aggregate into significant expenses when scaled up.
Transportation Costs: Variables and Impacts
Transportation is another beast entirely. I once had a shipment delayed because of an unexpected snowstorm—a classic Canadian problem! It taught me how unpredictable these costs can be.
Imagine you’re shipping 1,000 units for a flat rate of $1,000—that’s $1 per unit. However, fluctuations in fuel prices or route changes can further affect this cost.
To optimize transportation costs, consider logistics strategies9 like consolidating shipments or negotiating better rates with carriers. Efficient logistics reduce overall expenses, allowing for competitive pricing.
Integrating Costs into Production
Bringing it all together—packaging and transportation are not just add-ons; they’re integral to the production cost equation. Here’s how it breaks down:
Cost Element | Cost per Unit |
---|---|
Material Cost | $0.024 |
Mold Cost Sharing | $0.06 |
Injection Molding Processing | $0.243 |
Packaging | $0.25 |
Transportation | $1.00 |
Total Production Cost | $1.577 |
By analyzing each element, manufacturers can pinpoint where we might trim some fat—maybe by exploring new packaging methods or optimizing logistics routes with insights from logistics optimization10. It’s not just about cutting costs but ensuring we stay competitive in a market that’s always looking for the next best thing.
What Tools Can Help Accurately Estimate Injection Molding Costs?
Ever tried to unravel the mystery of injection molding costs and felt a bit lost? With the right tools, you can turn that complex puzzle into a clear, manageable picture.
To accurately estimate injection molding costs, utilize 3D modeling software, cost calculators, and material estimation apps to efficiently calculate material usage, mold expenses, and processing costs.
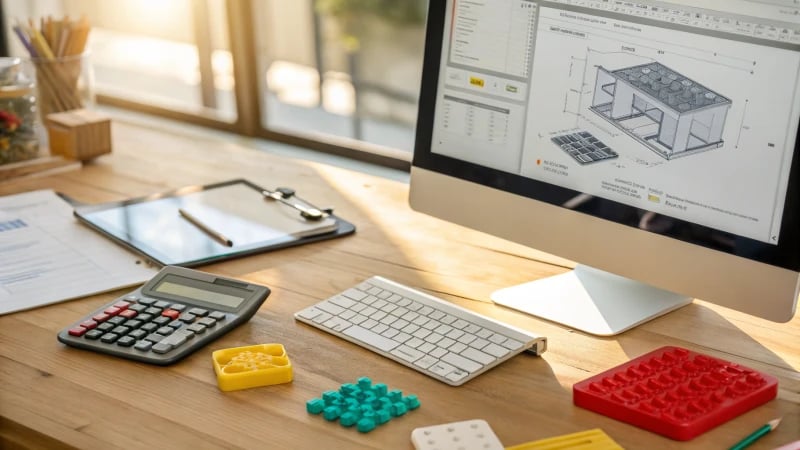
3D Modeling Software for Material Costing
I remember the first time I used 3D modeling software11 to determine the volume of an irregularly shaped product—it was a revelation. With programs like AutoCAD or SolidWorks, I could easily calculate the material needed by considering the material density. It was like having a digital sculpture in my hands, guiding me through the intricate details that once seemed overwhelming.
Online Cost Calculators
Imagine being able to input specific parameters into an online calculator like Costimator12 and getting a detailed cost analysis almost instantly. These tools let me quickly compare different scenarios, saving countless hours that I used to spend manually crunching numbers. It’s like having a personal financial advisor who specializes in injection molding.
Cost Factors | Description |
---|---|
Material Cost | Calculated based on weight and unit price. Utilizes data from 3D models13. |
Mold Cost | Includes design, manufacturing, and transportation costs. Uses historical data for better accuracy. |
Processing Cost | Covers energy and labor costs, factoring in machine specifications. |
Packaging and Transportation | Evaluated based on logistics factors such as distance and volume. |
Material Estimation Apps
Apps like Plastics Technology’s Material Cost Estimator14 have been a game-changer for me. By entering the product’s volume and the material’s density, I can get quick calculations for the amount of plastic needed. This gives me an immediate overview of material expenses, which is crucial when I’m at the initial stages of cost estimation.
Software for Mold Cost Sharing
Using dedicated software solutions such as Moldflow15, I can forecast mold investment and determine service life more accurately. It’s reassuring to know that every product’s mold cost is calculated with precision, distributing costs evenly across production runs. This ensures no surprise expenses pop up later on.
By weaving these tools into my daily workflow, I’ve been able to achieve a more accurate and comprehensive understanding of injection molding costs. Each tool serves its unique purpose, but together they make sure no aspect of costing is overlooked. It’s like assembling a team where everyone plays their part perfectly.
3D modeling software calculates material volume.True
Software like AutoCAD or SolidWorks helps determine product volume for material costing.
Online calculators ignore production volume in cost estimation.False
Tools like Costimator consider production volume when estimating injection molding costs.
Conclusion
This article explains how to calculate the cost per part in injection molding by analyzing material, mold, processing, packaging, and transportation costs for accurate budgeting.
-
Explore how 3D modeling software accurately estimates volumes for complex shapes, aiding in precise material costing. ↩
-
Learn about mold design’s critical role in determining efficiency and cost-effectiveness in injection molding processes. ↩
-
Discover methods for calculating volume for various product shapes using geometric formulas or advanced modeling. ↩
-
Learn strategies to enhance efficiency and reduce costs in the injection molding process. ↩
-
Explore ways to boost your manufacturing competitiveness through effective cost management. ↩
-
This link provides detailed steps on calculating material costs accurately. ↩
-
Explore advanced techniques for precise cost estimation in injection molding. ↩
-
Discover different methods to calculate packaging material costs, helping refine budgeting and improve cost-effectiveness. ↩
-
Explore logistics strategies to reduce transportation costs, enhancing overall production efficiency. ↩
-
Learn about techniques to optimize logistics, potentially lowering transportation costs and boosting competitiveness. ↩
-
Discover top 3D modeling software options to accurately calculate product volumes and material needs. ↩
-
Explore calculators that provide detailed injection molding cost analyses based on user inputs. ↩
-
Learn methods to calculate material costs efficiently using 3D modeling data. ↩
-
Find apps that offer quick estimates of plastic material costs for production planning. ↩
-
Examine software solutions designed to accurately estimate mold investment and sharing costs. ↩