Navigating the world of injection molding can feel like walking a tightrope—one small misstep in dimensional accuracy can lead to a tumble into costly errors.
Dimensional deviation in injection molded products can stem from unstable machine parameters, improper mold design, variable plastic shrinkage rates, process parameter errors, and environmental factors. Addressing these issues requires a comprehensive approach across equipment, materials, and environmental controls.
While these insights provide a foundational understanding, the complexity of injection molding means there’s more to explore. Delve deeper into each cause and solution to ensure your production process achieves the highest precision possible.
Unstable machine parameters cause dimensional deviation.True
Machine parameters like pressure and speed affect product dimensions.
How Does Machine Maintenance Impact Dimensional Accuracy?
In the manufacturing sector, machine maintenance is crucial for ensuring product precision, especially in injection molding processes.
Machine maintenance significantly impacts dimensional accuracy by stabilizing injection parameters, reducing wear, and preventing equipment failures that lead to deviations.
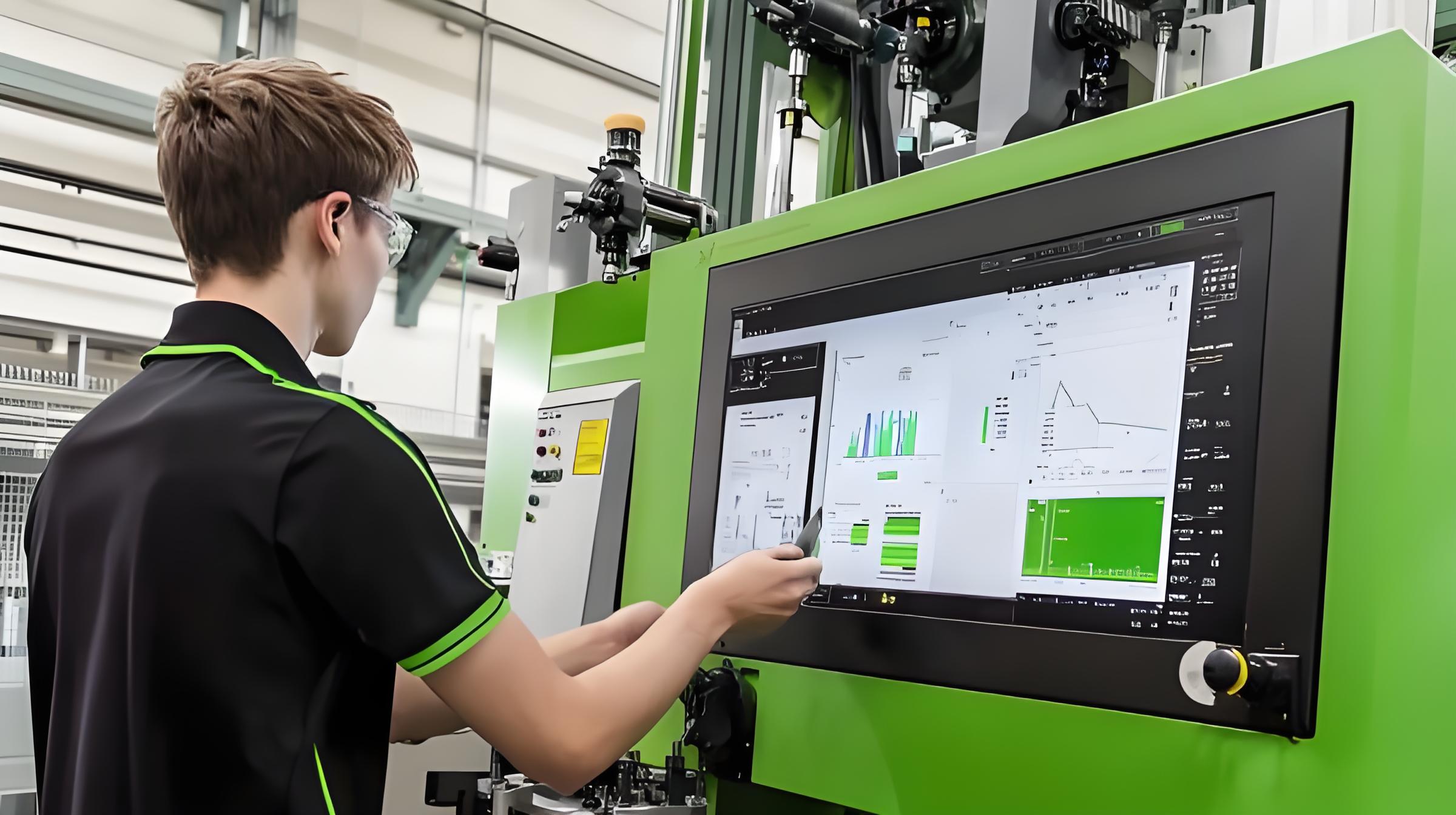
Understanding the Connection Between Machine Maintenance and Precision
Regular maintenance of injection molding machines1 is vital for maintaining consistent product quality. Variability in machine performance can result in significant deviations in product dimensions, leading to costly errors and rework. By adhering to a strict maintenance schedule, manufacturers can ensure their equipment operates within optimal parameters.
Key Areas of Maintenance
-
Injection Pressure Stability
One primary focus of machine maintenance is ensuring stable injection pressure. Unstable pressure can lead to inconsistent filling of the mold, resulting in dimensional deviations. Regular checks and adjustments help maintain the desired pressure levels.
-
Injection Speed and Plasticizing Capacity
Properly maintained machines allow for precise control over injection speed, crucial for reducing internal stress and achieving uniform product dimensions. Enhancing the plasticizing capacity through regular cleaning and component checks also ensures even melting of materials.
Maintenance Task | Impact on Dimensional Accuracy |
---|---|
Checking Injection Pressure | Ensures consistent mold filling |
Regulating Injection Speed | Reduces internal stress and variation |
Enhancing Plasticizing Capacity | Promotes uniform melting and flow |
-
Component Wear and Replacement
Over time, components such as screws and barrels may wear, impacting dimensional accuracy. Timely replacement of worn parts ensures that the machine functions effectively, maintaining precise product dimensions.
Benefits of Routine Maintenance
- Cost Efficiency: By preventing machine failures, routine maintenance reduces unexpected downtime and costly repairs.
- Product Quality: Maintained machines ensure stable parameters, leading to high-quality products with minimal dimensional deviations.
- Operational Consistency: Regular maintenance schedules lead to predictable machine behavior, aiding in precise production planning.
Overall, integrating a comprehensive maintenance program is essential for any manufacturer aiming to achieve top-tier precision in injection molding processes.
Regular maintenance stabilizes injection pressure.True
Stabilizing injection pressure prevents dimensional deviations in products.
Component wear has no effect on dimensional accuracy.False
Worn components can lead to inaccurate product dimensions.
What Role Does Mold Design Play in Product Precision?
Mold design is a critical factor in ensuring the precision of injection-molded products. Poor design can lead to significant dimensional deviations.
Effective mold design is crucial for maintaining product precision in injection molding. It involves careful consideration of gate position, runner size, and manufacturing accuracy to ensure consistent melt flow and prevent size deviations.
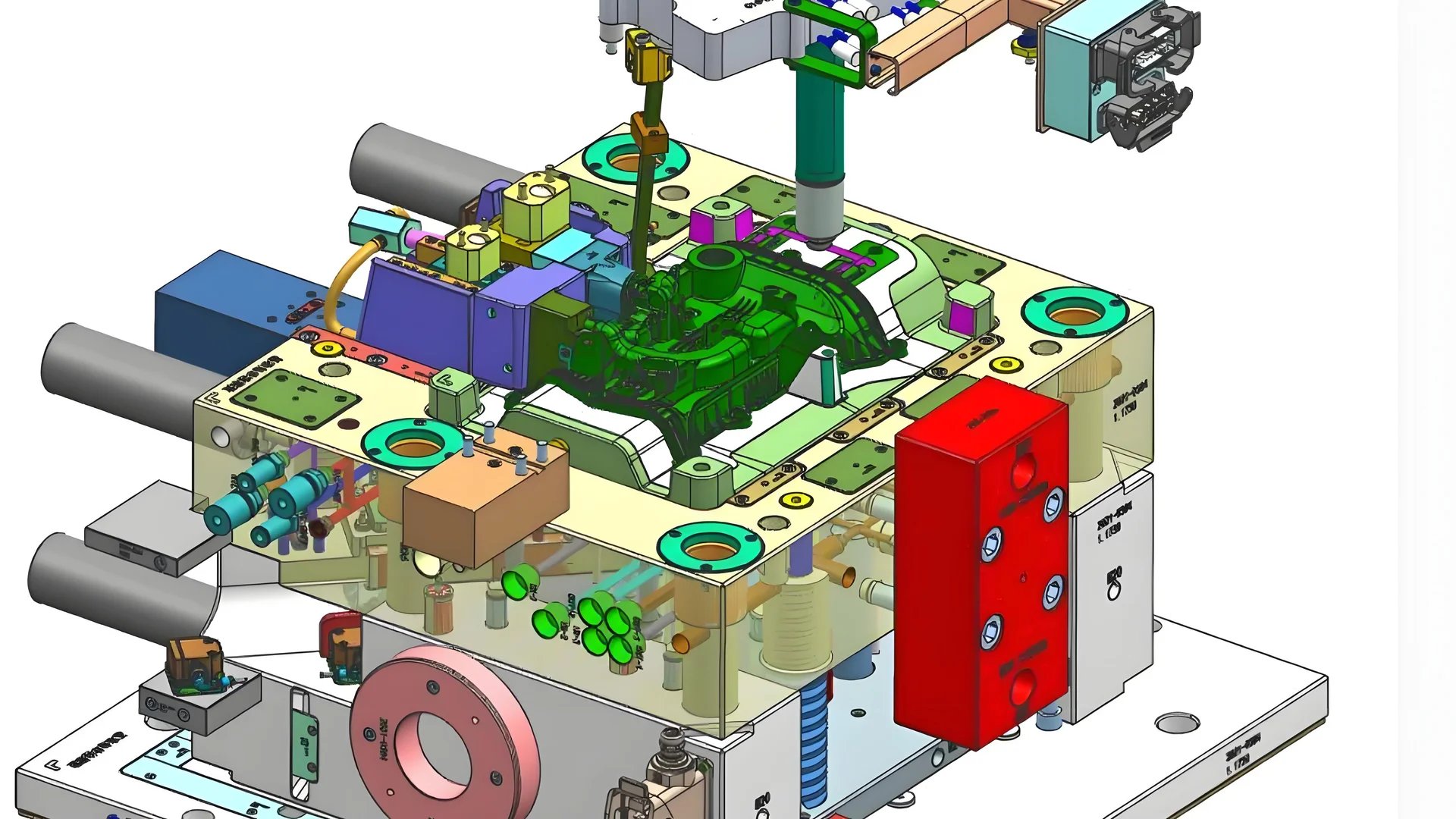
Understanding Mold Design
Mold design is more than just the blueprint of the product; it’s the science behind ensuring that every injection-molded piece meets its dimensional specifications. A well-designed mold accounts for potential issues that could cause variations, such as inconsistent melt flow or improper cooling.
Importance of Gate Position
The placement of the gate, where molten plastic enters the mold, is vital. A strategically positioned gate ensures uniform pressure and temperature distribution, reducing stress and preventing warpage or shrinkage. Poor gate positioning can lead to uneven filling and ultimately affect the dimensional precision2 of the final product.
The Role of Runner Size
Runners are channels that guide the molten material from the injection point to the cavity. Their size and shape must be optimized for efficient material flow. Oversized runners can waste material and increase cycle time, while undersized runners may cause incomplete filling or increased pressure, both affecting product dimensions.
Runner Size | Impact on Precision |
---|---|
Too Large | Wastes material, prolongs cycles |
Too Small | Causes incomplete filling |
Precision in Mold Manufacturing
The accuracy with which molds are manufactured directly impacts product precision. Any errors during this phase can translate to dimensional deviations in the final product. Modern techniques such as CNC machining and 3D printing help achieve high levels of precision in mold production.
Addressing Mold Wear and Tear
Over time, molds can wear out, especially when used frequently for high-volume production. Regular maintenance and timely replacement of worn parts are essential to prevent gradual deviations in product size. Implementing a predictive maintenance3 schedule can mitigate these issues.
Conclusion: A Comprehensive Approach
While mold design plays a pivotal role in ensuring precision, it must be considered alongside other factors like machine settings and material choice for optimal results. Collaborating with experienced designers and manufacturers can further enhance the precision of injection-molded products.
Poor mold design leads to dimensional deviations.True
Poor design affects melt flow, causing size variations in products.
Gate position does not affect product precision.False
Incorrect gate placement leads to uneven filling and warping.
How Can Material Selection Influence Shrinkage Rates?
Choosing the right material is crucial in minimizing shrinkage rates in injection molded products. This decision impacts dimensional accuracy significantly.
Material selection affects shrinkage rates in injection molding by influencing thermal expansion, crystallinity, and viscosity. Opting for materials with consistent shrinkage properties and appropriate processing conditions ensures uniform product dimensions.
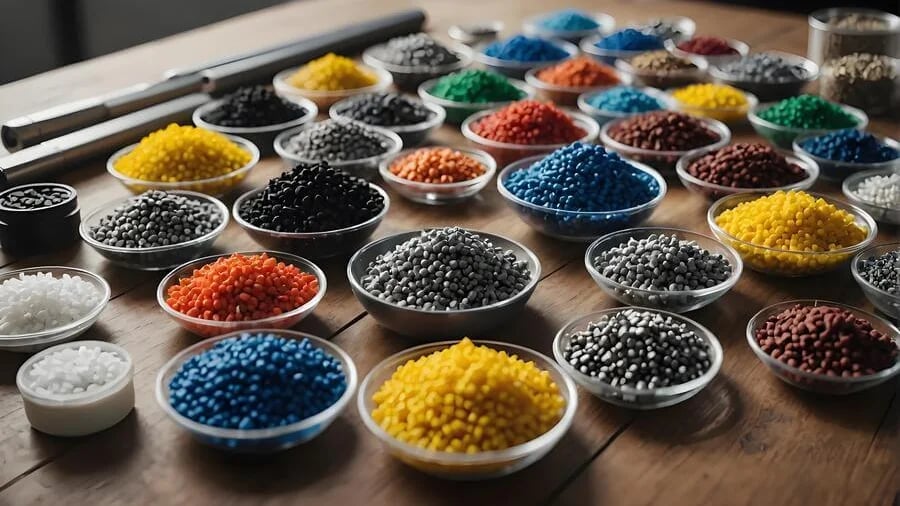
Understanding Material Properties and Their Impact on Shrinkage
Materials used in injection molding4 possess distinct properties that determine their behavior during the molding process. Key factors include thermal expansion, crystallinity, and viscosity.
-
Thermal Expansion: Materials with high thermal expansion rates tend to contract more as they cool, leading to increased shrinkage. For example, amorphous polymers like polystyrene typically exhibit lower shrinkage than crystalline polymers such as polypropylene.
-
Crystallinity: The level of crystallinity in a material can affect its shrinkage rate. Highly crystalline materials often show more uniform shrinkage due to their structured molecular arrangement, while semi-crystalline materials might exhibit variable shrinkage.
-
Viscosity: A material’s viscosity affects how well it flows into a mold, impacting the final product’s dimensions. Materials with high viscosity may not fill the mold completely, leading to uneven shrinkage.
Selecting Stable Material Properties
To minimize dimensional deviation, choosing materials with stable shrinkage properties is essential. Consistency across different batches can be achieved by selecting materials from reputable suppliers known for quality control.
Practical Considerations in Material Selection
-
Batch Consistency: Using the same batch of material reduces variability in shrinkage rates. Fluctuations between batches can cause significant dimensional deviations.
-
Material Testing: Conducting pre-production tests on new materials can help predict potential shrinkage issues and allow for adjustments before full-scale production.
The Role of Additives and Fillers
Incorporating additives and fillers can modify the base material’s properties, influencing shrinkage rates. For example, adding glass fibers to a polymer matrix reduces overall shrinkage due to the fibers’ resistance to thermal expansion.
Here’s a simple table summarizing material types and their typical shrinkage behavior:
Material Type | Typical Shrinkage Behavior |
---|---|
Amorphous Polymers | Lower shrinkage, more predictable |
Semi-crystalline | Higher shrinkage, requires precise control |
Filled Polymers | Reduced shrinkage due to filler stability |
By understanding these aspects of material selection, manufacturers can better control shrinkage rates, ensuring the final product meets dimensional specifications and maintains quality standards.
Amorphous polymers have lower shrinkage than crystalline polymers.True
Amorphous polymers like polystyrene shrink less due to lower thermal expansion.
High viscosity materials lead to more uniform shrinkage.False
High viscosity can cause incomplete mold filling, leading to uneven shrinkage.
Why Are Process Parameters Critical in Injection Molding?
The success of injection molding hinges on mastering process parameters. These factors can make or break product quality.
Process parameters in injection molding, such as temperature control, injection speed, and pressure, are crucial for ensuring dimensional accuracy and reducing defects in the final product.
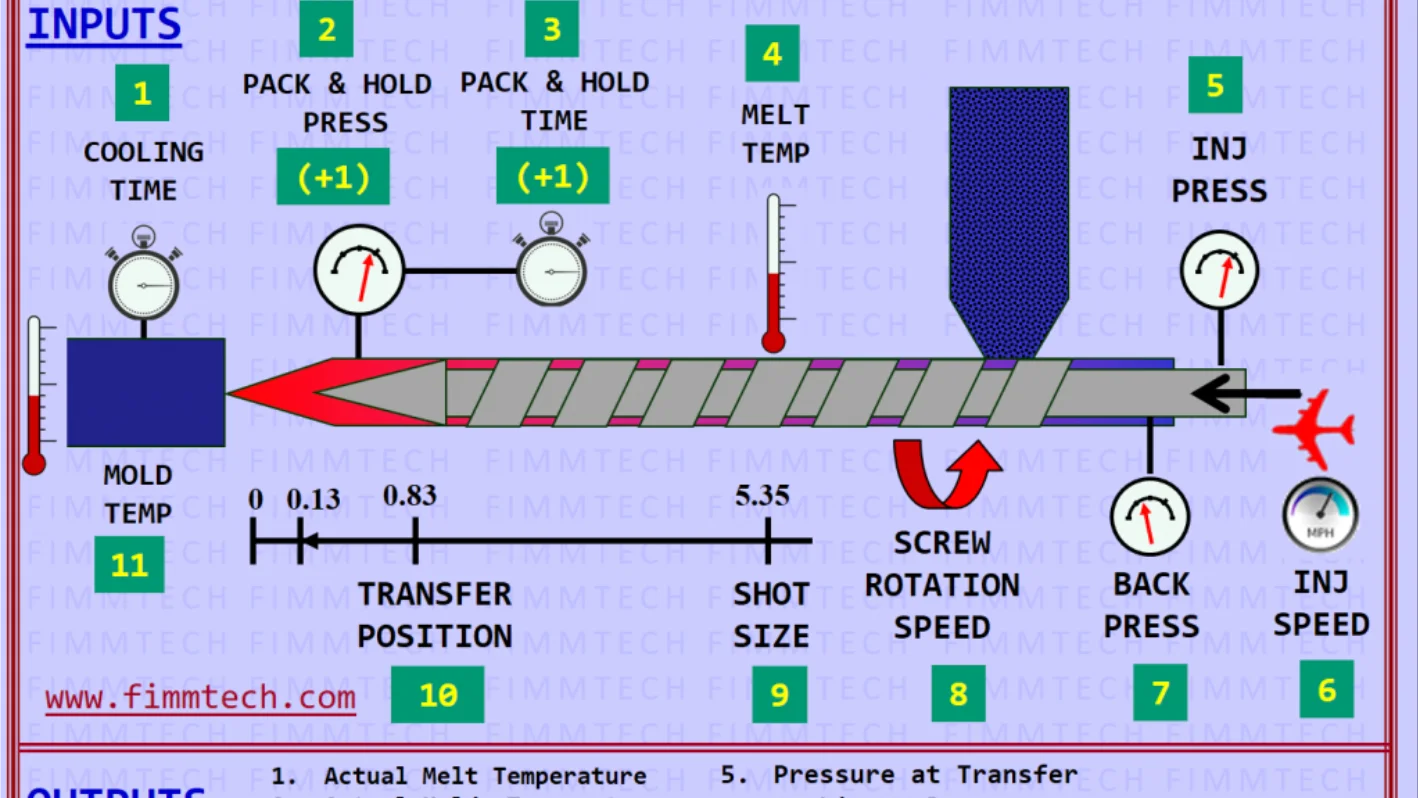
Understanding Process Parameters
Process parameters in injection molding encompass a variety of settings that influence how plastic is transformed into a finished product. The most critical parameters include temperature control, injection speed, and holding pressure. Each plays a pivotal role in maintaining the desired dimensional accuracy5 and minimizing product defects.
Temperature Control: Proper regulation of barrel, nozzle, and mold temperatures ensures optimal plastic flow and shrinkage rates. If temperatures are too high, plastics may degrade, while too low temperatures can cause incomplete filling of the mold.
Injection Speed: The rate at which molten plastic is injected affects the internal stresses and potential turbulence within the mold. A balanced speed prevents warping and ensures uniformity across the product.
Holding Pressure and Time: These factors determine how much material is packed into the mold during cooling. Insufficient pressure or time can lead to shrinkage, while excess can create stress marks.
The Impact of Process Parameters
Dimensional Deviation: Inconsistent parameters can lead to variations in product size and shape. For instance, an unstable injection speed may cause turbulence, resulting in uneven cooling and size discrepancies.
Defect Prevention: By meticulously adjusting these parameters, manufacturers can significantly reduce common defects like warping or sink marks.
Parameter | Potential Issue | Solution Strategy |
---|---|---|
Temperature | Incomplete filling | Adjust barrel/nozzle/mold temperatures |
Injection Speed | Turbulence | Optimize speed to prevent internal stresses |
Holding Pressure | Excess shrinkage | Calibrate pressure and time accurately |
Optimizing Process Parameters
To achieve precision in injection molding, continuous monitoring and adjustment of parameters6 are essential. Implementing robust quality control measures helps identify deviations early, allowing for quick corrections.
Process parameter optimization not only ensures product quality but also enhances production efficiency, reducing material waste and downtime. Regular experimentation with these settings can uncover ideal conditions for different materials and product designs.
Understanding the critical nature of process parameters is essential for anyone involved in injection molding. By leveraging these insights, manufacturers can enhance their production processes, leading to superior products and satisfied customers.
Temperature control affects plastic flow in molding.True
Proper temperature regulation ensures optimal plastic flow and shrinkage.
Injection speed has no impact on product uniformity.False
Balanced injection speed is crucial to prevent warping and ensure uniformity.
Conclusion
Addressing dimensional deviation requires a systematic approach focusing on machine settings, mold precision, material consistency, and environmental stability.
-
Learn how regular machine checks ensure stable production quality.: However, like any machinery, injection molding equipment requires regular maintenance to ensure optimal performance, longevity, and safety. ↩
-
Discover how gate position influences melt flow and product accuracy.: The gate location should consider the product’s functional requirements, such as ensuring proper filling, packing, and part performance. The … ↩
-
Learn about strategies to prevent mold wear-related dimensional issues.: Sensors placed intelligently in the mold can be used to monitor the operational status of the tool (mold monitoring). ↩
-
Explore the basics of injection molding processes and techniques.: injectionmolding Learn everything you need to know about injection molding in this video. We … ↩
-
Dimensional accuracy is vital for maintaining consistent product quality.: Manufacturing Precision of Mold Dimensions: The precision with which the mold is manufactured is a key factor in determining the dimensional accuracy of the … ↩
-
Learn techniques to fine-tune settings for optimal results.: 1. Temperature Control: · 2. Injection Speed: · 3. Cooling Time: · 4. Plastic Material Selection: · 5. Screw Speed and Back Pressure: · 6. Injection … ↩