Picture yourself shaping a mold as detailed as a puzzle. Each piece is crucial to the complete image.
To find the best way to process complex cavity shape molds, I first look at the cavity’s surface type, internal structure and material features. High-Speed Milling helps with free-form surfaces. Electrical Discharge Machining works well for intricate structures. Accurate results need these techniques.
I remember the first time I faced a similar challenge in my design journey. Each decision seemed crucial, like deciding between HSM and EDM due to the mold’s details. These decisions directly affect how well and how good the final product turns out. Knowing these technologies really well is important for success. I will guide you through some important ideas to help us choose correctly at every step of mold creation.
High-speed milling is ideal for free-form surfaces.True
HSM efficiently processes complex surfaces, ensuring accuracy.
Deep hole processing can only be done by EDM.False
Deep holes can be processed by deep hole drilling or EDM.
- 1. How Do Cavity Surface Types Affect Mold Processing?
- 2. What Are the Challenges of Processing Complex Internal Structures?
- 3. Why Is Mold Material Choice Crucial in Manufacturing?
- 4. How can I optimize my processing sequence for efficiency?
- 5. How Do Equipment and Fixtures Enhance Mold Accuracy?
- 6. How Can Surface Treatment Enhance Mold Performance?
- 7. Conclusion
How Do Cavity Surface Types Affect Mold Processing?
Have you ever thought about how the surface of a mold influences processing? It’s similar to picking the perfect shoes for a hike – important for success!
Different cavity surfaces affect how mold processing happens. Machining methods depend on these surface types. Complicated surfaces, such as free-form shapes, frequently need high-speed milling. On the other hand, regular and simpler surfaces use standard milling.
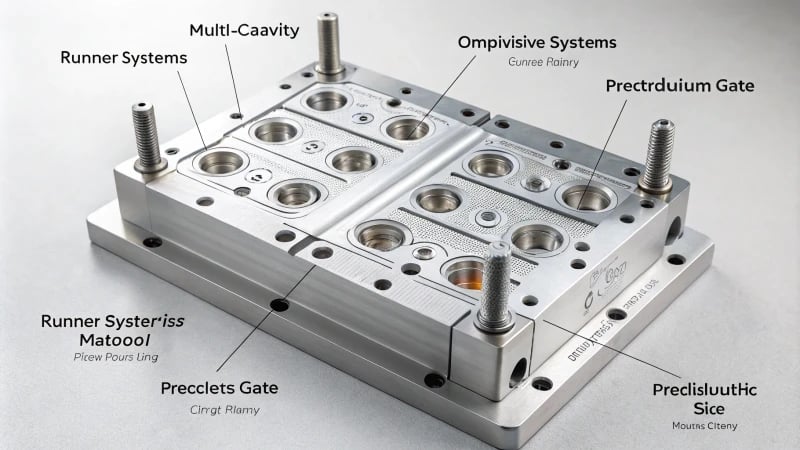
Studying Cavity Surface Types
When I started with molds, I didn’t know how much cavity surfaces changed everything. It’s amazing. These details control our choices and methods.
Free-Form and Regular Shapes
Picture shaping a car’s outer mold; the curves are very complex. For these free-form surfaces, high-speed milling (HSM) works best. It feels like using a delicate brush to capture details. But for simple shapes, like a cylinder, regular milling works fine. It’s like going back to basics – shaping, then perfecting.
Processing Techniques Based on Surface Type
Surface Type | Processing Method |
---|---|
Free-form | High-speed milling |
Regular | Ordinary & fine milling |
Internal Structures and Thin Walls
Imagine building a ship in a bottle; that’s how working with tricky internal parts feels. Tiny grooves or deep holes need careful planning, sometimes using clever tricks like tilting tops for demolding.
Thin walls are surprising. They stay strong even during rough machining. Leaving space for a gentle finish is key.
Material Choices
Picking the right material is like choosing armor. Strong materials like H13 need tough tools. It’s a balance between speed and precision for a perfect finish. For softer materials, avoiding sticky problems is very important.
Choosing Processing Sequence
Processing steps require strategy:
- Roughing: Quickly removes excess material using large diameter tools.
- Semi-Finishing: Enhances dimensional accuracy post-roughing.
- Finishing: Achieves the design’s surface quality requirements.
Using precise CNC machines treats even tough cavities with care. Setting the right fixtures1 is vital to keep things steady in this detailed process.
Surface Treatment and Equipment Choice
Getting a shiny finish is like adding the cherry on top. Advanced methods like electrochemical polishing make it shine perfectly. For durability, processes like nitriding or chrome plating add extra protection; however, be mindful of potential impacts on dimensional accuracy.
Understanding these details helps me – and others – to improve mold strategies2, making products that are both useful and beautifully crafted.
High-speed milling is suitable for free-form surfaces.True
HSM efficiently processes complex surfaces while ensuring accuracy.
Rough machining is ideal for high-gloss surface molds.False
Polishing or advanced processes are needed for high-gloss surfaces.
What Are the Challenges of Processing Complex Internal Structures?
Picture starting a project where each choice resembles solving a puzzle. Every piece gets more complicated one after the other. This is similar to handling detailed internal structures.
Dealing with complex internal structures involves handling difficult parts like complicated cavity shapes, the qualities of materials and exact machining steps. High-speed milling and custom fixtures often have crucial roles in getting past these challenges.
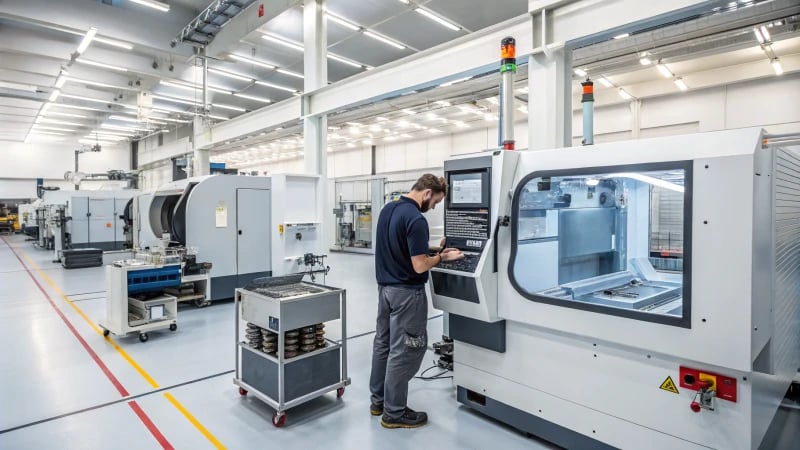
Intricate Cavity Shapes
I remember the first time I saw a mold with strange shapes. It felt like trying to carve a statue using only a simple tool and a block of marble. High-speed milling3 became my favorite method. It handled the curvy shapes with the elegance and accuracy I needed. Conventional milling worked well for regular surfaces, like an old friend. But internal undercuts and deep holes were a real challenge. They required EDM or a smart tilting mechanism to solve.
Material Characteristics
I’ve worked with many materials, from very hard ones like H13 to softer ones. Each has its own personality. Hard materials feel like a tough fight, needing strong machines and carbide tools just to scratch them. For finishing, slowing down helps achieve a perfect surface. Soft materials are tricky; they sometimes stick, but coated tools4 and plenty of cutting fluid help manage this.
Machining Sequences
Planning the machining steps feels like arranging dominoes – one mistake and everything collapses:
- Roughing: Quickly removes excess material using large tools.
- Semi-finishing: Prepares the surface for finishing by refining dimensional accuracy.
- Finishing: Achieves final design accuracy where precision is supreme.
Here’s a simplified table:
Stage | Cutting Depth (mm) | Feed Rate (mm/r) |
---|---|---|
Roughing | 1-3 | 0.2-0.5 |
Semi-finishing | 0.3-0.8 | 0.1-0.3 |
Finishing | 0.05-0.2 | 0.05-0.15 |
Equipment and Fixtures
Choosing equipment is like picking a superhero team: each tool has unique abilities. High-precision CNC centers are necessary, akin to Iron Man, while custom fixtures5 provide stability like Captain America’s shield.
Surface Treatment Considerations
Getting a shiny finish feels almost like magic; advanced polishing transforms rough surfaces into mirror-like wonders. However, processes like nitriding can change size accuracy, necessitating careful process planning to find the right balance.
Tackling these challenges needs not only technical skills but also a smart plan—like playing chess—where every move requires careful thought to optimize the manufacturing process for these complex designs.
High-speed milling is ideal for free-form surfaces.True
HSM efficiently processes complex surfaces with accuracy.
Deep hole drilling is unsuitable for narrow grooves.True
Deep hole drilling excels in deep holes, not narrow grooves.
Why Is Mold Material Choice Crucial in Manufacturing?
Do you ever think about why picking the right mold stuff matters so much in manufacturing?
Choosing the correct mold material is very important. It affects the mold’s strength, heat transfer and ease of cutting. Good materials help production run smoothly. They lower costs. They improve the quality of products by reducing defects. Good materials also help the mold last longer. Really, they extend its life. Quality is better with the right material.
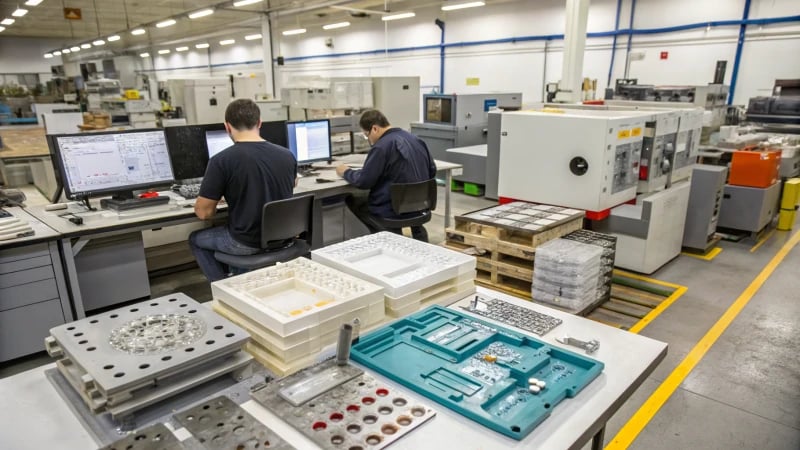
Understanding Mold Material Properties
I recall my first time selecting a mold material for a project. The pressure felt immense because the choice would influence everything from strength to how smoothly production flowed. Properties like hardness, toughness, and thermal conductivity aren’t just technical lingo – they’re vital for our manufacturing success. High-hardness materials like H13 offer great durability; however, they need special machining techniques that seem like threading a needle.
Impact of Mold Materials on Production
Different materials have shown me how they can really alter the process. Materials with high thermal conductivity help in quicker cooling, thus speeding up production. However, it’s a balancing act – excessive conductivity could lead to warping, a lesson I painfully learned once. It’s crucial to find the ideal balance to keep shape true while maintaining speed.
Property | Advantage | Consideration |
---|---|---|
Hardness | Increased durability | Difficult machining |
Toughness | Resistance to cracking | Possible machining issues |
Thermal Conductivity | Faster cycle times | Risk of warping |
Cavity Shape and Processing Methods
I faced a project where the cavity shape complexity almost drove me up the wall. Free-form surfaces needed high-speed milling (HSM)6, which offers excellent accuracy but gets tricky with complex structures, such as undercuts or deep holes. The mold material must survive these processes without wearing out – a point I never forget.
Processing Equipment and Fixtures
Choosing the correct processing equipment felt like cracking a tough riddle. I preferred high-precision CNC machines for challenging designs, maintaining stability with custom fixtures7. Though these details seem minor, they significantly affect precision.
Grasping these elements supports my choice of mold material to suit my manufacturing needs. Finding the right balance between efficiency and quality remains crucial – a lesson years of experience have taught me well.
High-speed milling is ideal for free-form surfaces.True
HSM efficiently processes complex shapes, ensuring precision.
Nitriding has no impact on dimensional accuracy.False
Nitriding can affect dimensions, requiring process adjustments.
How can I optimize my processing sequence for efficiency?
Ever think your production line is crawling? Let’s change this by exploring practical ways to speed up your processing efficiency!
To get the most out of your processing sequence, consider your materials and equipment. First, look closely at cavity shapes and mold materials. Then, select the correct tools and steps. Follow the sequence of roughing, semi-finishing and finishing to simplify your workflow. It’s important. Very important.
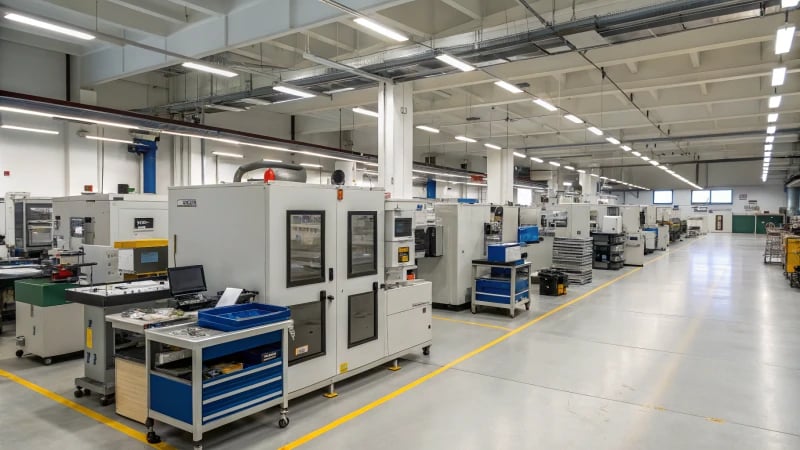
Analyzing Cavity Shape Characteristics
Understanding the cavity shape is crucial in optimizing processing. For instance, surfaces like free-form molds for car parts benefit from high-speed milling8, ensuring accuracy while processing complex shapes. Regular surfaces can undergo rough ordinary milling followed by fine milling.
Internal Structure Considerations
For cavities with internal complexities, such as undercuts or narrow grooves, it’s essential to use techniques like electrospark machining (EDM) for deep holes. Micro-diameter tools are recommended for narrow grooves. This precision prevents issues during demolding.
Considering Mold Material Characteristics
The material characteristics play a vital role in efficiency. Materials with high hardness, like H13, benefit from high-power equipment during rough machining, while softer materials require attention to avoid burrs. Tools with coatings help reduce sticking in ductile materials.
Material Type | Rough Machining | Finishing |
---|---|---|
High Hardness | High-power tools | Reduced speed |
Low Hardness | Improved efficiency | Monitor toughness |
Selecting the Right Processing Sequence
A structured sequence enhances efficiency. Start with roughing to remove excess material using large diameter tools and deeper cuts. Follow up with semi-finishing for better dimensional accuracy, adjusting the tool path as needed. Finally, finishing ensures design accuracy using minimal cutting depth.
Determining Equipment and Fixtures
Choosing the correct processing equipment is essential. High-precision CNC machines are ideal for complex cavities. Custom fixtures9 stabilize molds during processing, ensuring accuracy for irregular shapes.
Surface Treatment Process Considerations
After machining, surface treatments like polishing enhance quality. For uniformity in complex shapes, advanced techniques such as ultrasonic polishing can be used. Surface treatments improve wear resistance but may affect dimensional accuracy, requiring process adjustments.
HSM is ideal for free-form surfaces in mold design.True
High-speed milling efficiently processes complex surfaces with precision.
Deep hole drilling is unsuitable for cavity molds.False
Deep hole drilling is suitable for processing deep holes in cavity molds.
How Do Equipment and Fixtures Enhance Mold Accuracy?
Have you ever thought about how the tools and setups influence molds’ accuracy?
Equipment and fixtures hold a key place in mold accuracy. They provide stability and precision during manufacturing. These tools handle complex shapes well. They support the unique qualities of materials. These devices organize the essential steps needed for creating excellent molds. Excellent molds require meticulous care.
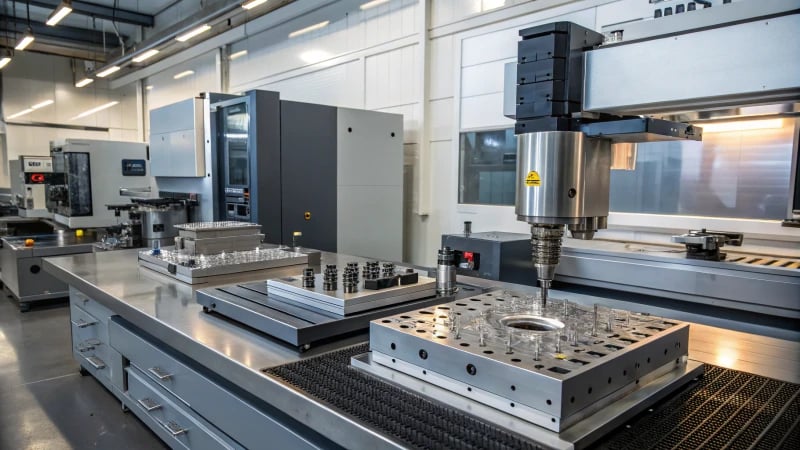
Grasping the Importance of Equipment
Finding the right processing equipment10 feels like picking the perfect tool for a project. Precision matters a lot. Those high-precision CNC machines can achieve positioning accuracy of ±0.005mm. This detail really changes the game for complex cavities that look like artworks.
For instances involving deep holes or specialized processes like EDM, having specific machinery ensures that dimensional requirements are met without compromising on accuracy.
Fixtures and Their Stability Role
Fixtures act like silent champions in mold-making. They hold mold blanks steady, especially with oddly shaped molds. Once, in a project, custom fixtures and vacuum suction fixtures helped prevent shifts during machining. Really, it felt like having extra hands.
Complex cavity shapes? Combined fixtures11 truly help with stability and precision.
Impact on Cavity Shape
While analyzing cavities, I learned the right equipment is essential. High-speed milling (HSM) handles free-form surfaces with great precision. Once, I worked on a mold with detailed internal structures. Undercuts and narrow grooves were handled well by tools like tilting tops. Processing accuracy was seamless.
Cavity Type | Recommended Process |
---|---|
Free-form surfaces | High-Speed Milling (HSM) |
Internal structures | Tilting Tops |
Thin-walled cavities | High-speed, small feed |
Considering Material Characteristics
The mold material’s hardness often guides my equipment choices. For hard materials like H13, I rely on powerful machines with carbide tools. If the material is softer, I balance efficiency and avoid burrs—it’s tricky like walking on a thin rope.
For high-ductility molds, coated tools are very valuable as they help minimize sticking during machining and process goes smoother with the lubricity of coatings12.
Sequential Processing and Equipment Teamwork
Roughing, semi-finishing, and finishing stages each demand different equipment precision:
- Roughing: Quick removal uses large tools.
- Semi-finishing: Dimensional accuracy becomes important.
- Finishing: Strategies such as equidistant cutting refine everything.
Right equipment in each phase aids smooth transitions, ensuring no loss in quality or precision. With good coordination between equipment and fixtures, achieving high mold accuracy seems really effortless.
High-speed milling suits free-form cavity surfaces.True
High-speed milling efficiently processes complex surfaces, ensuring accuracy.
Deep hole drilling is unsuitable for narrow grooves.True
Narrow groove processing requires micro-diameter tools, not deep hole drilling.
How Can Surface Treatment Enhance Mold Performance?
Ever thought about how surface treatment turns your molds from good to great?
Surface treatment increases mold performance by improving how it deals with wear, reducing friction and stopping rust. Techniques such as nitriding and chrome plating are popular because they help extend mold life and keep precision.
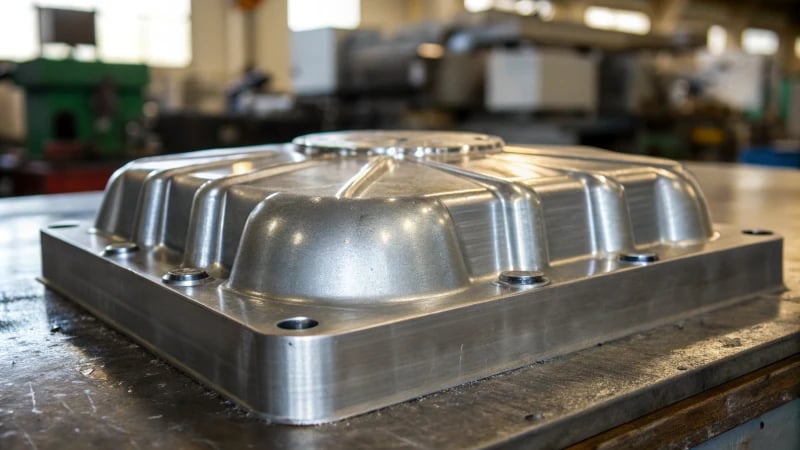
Improving Wear Resistance
Molds experience high friction often. Treatments like nitriding and chrome plating help a lot. Nitriding adds nitrogen to the steel’s surface, forming a strong, wear-resistant layer, perfect for tough conditions. Chrome plating13 puts a thin chromium layer on the mold, increasing both wear resistance and corrosion protection.
Boosting Aesthetic and Functional Quality
A product’s high-gloss finish looks very satisfying. For precise molds, polishing becomes important. Electrochemical polishing14 works great, especially in complex cavities. It smooths surfaces at a tiny level, improving both look and function.
Surface Treatment | Benefits |
---|---|
Nitriding | Wear resistance |
Chrome Plating | Corrosion protection, aesthetics |
Electrochemical Polishing | Uniform surface finish |
Managing Dimensional Accuracy
Surface treatments shift dimensional accuracy. I learned this from my early projects. Adapting processing strategies is crucial. For nitriding, consider size changes and adjust in the design stage to keep accuracy. Remember this step.
Improving Material Properties
Some molds stick during machining because they are very tough. Coated tools help a lot by reducing sticking, protecting surface quality, and keeping machining precise.
Balancing Processing and Performance
Choosing the right process sequence is an art. Begin with roughing to quickly remove extra material. Then, semi-finishing refines sizes. Finally, apply surface treatment to improve quality while maintaining efficiency.
Learn more about surface treatment methods15 to match your production goals. Whether you’re starting or have much experience like me, knowing these techniques can change the game in mold manufacturing.
High-speed milling is ideal for free-form cavity surfaces.True
HSM efficiently processes complex surfaces with accuracy, suitable for free-form.
Nitriding increases mold cavity dimensional accuracy.False
Nitriding can impact dimensional accuracy, requiring adjustments in processing.
Conclusion
This article explores effective methods for processing complex cavity shape molds, emphasizing the importance of cavity characteristics, material selection, processing sequences, equipment choice, and surface treatments.
-
Learn about different fixtures to stabilize molds during processing and enhance accuracy. ↩
-
Discover strategies to improve mold processing efficiency and product quality. ↩
-
Learn about high-speed milling, a technique crucial for efficiently processing complex surfaces while maintaining accuracy. ↩
-
Discover how coated tools reduce sticking and improve machining accuracy for ductile materials. ↩
-
Explore different fixture types to ensure stability and precision during CNC machining processes. ↩
-
Discover how high-speed milling improves processing of free-form surfaces while maintaining accuracy. ↩
-
Understand how custom fixtures enhance stability and precision during complex manufacturing processes. ↩
-
Explore how high-speed milling enhances precision and efficiency in processing complex surfaces. ↩
-
Discover how custom fixtures ensure stability and accuracy during mold processing. ↩
-
Discover how high-precision CNC machines enhance mold-making accuracy with precise positioning and complex cavity capabilities. ↩
-
Explore the benefits of using combined fixtures to stabilize irregular mold shapes during manufacturing. ↩
-
Understand how coatings reduce sticking and improve surface quality during machining. ↩
-
Discover how chrome plating enhances mold durability and corrosion resistance. ↩
-
Learn how electrochemical polishing can achieve superior surface finishes. ↩
-
Explore various techniques to find the best fit for your needs. ↩