Did you ever think about how the smallest parts in injection molding might ruin or improve a project?
The strength of an ejector pin depends on many things. Size and shape of the product matter. So do wall thickness and mold design. Material properties are important too. The size and strength of the pins themselves also play a role. Knowing these factors helps remove parts from molds quickly. This prevents damage.
When I first started exploring injection molding, I was really surprised. Little things like an ejector pin could change everything. Once, I worked on a challenging project. The product had a large size and shape. Bigger surfaces meant stronger holding forces. Releasing needed more strength.
Another time, I faced a complicated design. It had deep holes. It felt like pulling a stuck cork out of a bottle! I understood then how crucial it is to know each factor. Material and ejector design are important. Each part matters. Surface roughness or pin strength impacts the process. Learning these details is like having a secret tool. It’s key to mastering mold design.
Product size affects the ejection force of an ejector pin.True
Larger products generally require more force to be ejected from molds.
Ejector pin material does not influence ejection force.False
The material's strength and durability affect how much force it can exert.
- 1. How Does Product Size and Shape Affect Ejection Force?
- 2. Why is Product Wall Thickness Important for Ejection Force?
- 3. How does mold structure affect ejection force?
- 4. How Do Plastic Material Characteristics Influence Ejection Force?
- 5. Why are ejector pin dimensions and material strength so important?
- 6. Conclusion
How Does Product Size and Shape Affect Ejection Force?
Do you ever think about why some products smoothly slip out of molds, while others stubbornly stick?
Product size and shape really hold great importance in deciding ejection force. They affect how much contact and friction there is with mold surfaces. Big or complex-shaped products usually need more force to get them out. This happens because of the extra holding forces.
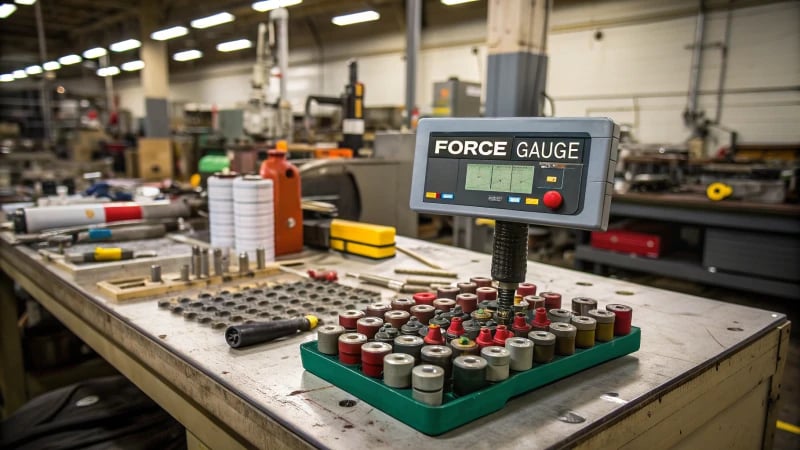
The Influence of Product Size
I remember the first time I noticed how much the size of a product impacts the ejection process. In manufacturing, larger products have more contact with the mold, resulting in higher holding forces. For example, a big plastic shell may need a larger ejector pin1 to overcome friction during demolding.
Product Size | Ejection Force Required |
---|---|
Small | Low |
Medium | Moderate |
Large | High |
The Role of Product Shape
Shapes are tricky too. Complex shapes, such as those with deep holes and undercuts, increase the difficulty of demolding. It was like trying to open a stubborn jar lid. These intricate contours can cause uneven stress distribution, necessitating a higher ejection force2 to prevent damage.
Wall Thickness Considerations
Wall thickness matters as well. Thicker walls shrink more during cooling, making the holding force against the mold stronger. For instance, I worked on a project with a product having a 5mm wall thickness that required a stronger ejection mechanism to release everything properly.
Material Characteristics Impact
Material choice plays a big role. Different plastics shrink and create friction differently. For example, using polycarbonate (PC) for a project resulted in high shrinkage rates and tighter fits within the mold, thus requiring greater ejection forces3.
Ejector Mechanism Design
Let’s talk about the ejector mechanism. A good design really matters; it significantly influences force transmission efficiency. I explored various designs and found that a well-guided ejector pin distributes force evenly, reducing deformation risk during ejection—like finding the perfect tool that makes everything easier.
Ejector Type | Force Efficiency |
---|---|
Pin | Moderate |
Sleeve | High |
Push Plate | Very High |
Larger products require more ejection force.True
Larger products have more contact area, increasing holding forces.
Complex shapes decrease ejection force needed.False
Complex shapes increase stress distribution, requiring higher forces.
Why is Product Wall Thickness Important for Ejection Force?
Do you ever think about why the walls of your product matter so much when they come out?
Thicker product walls hold more tightly because they shrink more when they cool down. Stronger ejection forces are necessary to easily remove the product from the mold cavity.
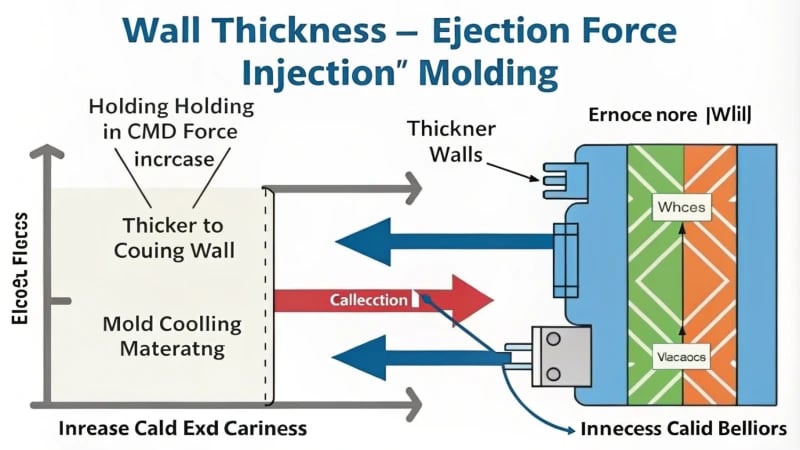
Impact of Product Structure on Ejection Force
Size and Shape Considerations
Long ago, during my initial design days, I didn’t grasp how size and shape change the ejection force. A big plastic piece with lots of area felt like peeling a tough sticker. Great force was necessary to release it. Complex shapes, with hidden corners, are like puzzles. They demand special care and sometimes extra effort.
Factor | Description | Impact on Ejection Force |
---|---|---|
Large Surface Area | Increases contact | Requires higher force |
Complex Shapes | Harder to demold | Increases difficulty |
Wall Thickness Influence
Thicker walls feel like walking a tightrope. They hold tight to the mold as they cool and shrink. Imagine trying to remove a snug glove – it isn’t simple. Adjusting ejection techniques is necessary for items with thicker walls versus thinner ones. Thick walls really need different strategies.
Mold Structure’s Role in Ejection
Ejector Mechanism Design
The ejector mechanism is like an unsung hero here. A straight ejector gives direct force but needs cautious handling to prevent uneven results. Push plates are more complex but offer balanced force. Strong mechanisms are crucial; it’s like trying to open a heavy door with a weak stick.
- Surface Roughness and Demolding Angle
Smooth mold surfaces really reduce friction, easing the process. It’s like sliding on ice instead of trudging through mud. Getting the demolding angle right is critical. If it’s too shallow, it’s back to struggling with that stubborn sticker again.
Material Characteristics Affecting Ejection Force
Different plastics bring unique challenges. High-shrinkage materials like polycarbonate hold tight after cooling, while high-friction plastics like polyoxymethylene feel like pulling gum off a shoe. Material behavior varies.
- Elastic Modulus Considerations
Low elastic modulus materials are trickier to handle. They may deform easily if not managed with care during ejection. Gently applying force preserves their form.
Ejector and Sleeve Pin Factors
Ejector pin size matters a lot. Larger diameters handle bigger forces; it’s like having the right tool, such as a thick hammer instead of a thin nail. Short pins lower bending risks, allowing effective force application.
For more information on these topics, visit ejector mechanism design4 and check plastic material characteristics5.
Thicker walls require more ejection force.True
Increased shrinkage with thicker walls heightens mold grip.
Smooth mold surfaces increase ejection force.False
Smooth surfaces reduce friction, lowering the needed ejection force.
How does mold structure affect ejection force?
Have you ever thought about why some molds hold onto your product so tightly? Mold design greatly affects the ejection force. This can really improve production flow. Good molds lead to smoother manufacturing. Your products become exceptional.
Mold structure greatly affects ejection force. Key parts include how the ejector mechanism works, the mold’s surface smoothness and the angle for removing parts. These aspects change friction, holding strength and the simplicity of demolding.
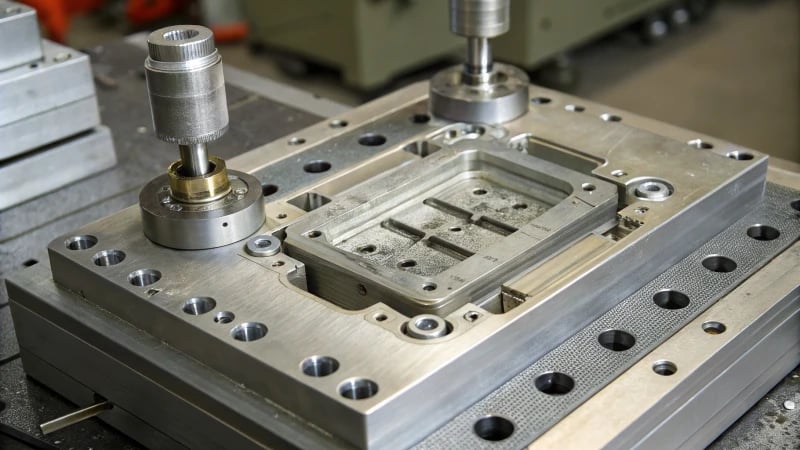
Understanding Ejector Mechanism Design
In mold design, the ejector mechanism6 plays a key role in the molding process. A direct ejector pin works efficiently like a reliable friend but might be a bit harsh without proper control. Push plate mechanisms act like a well-organized team. They share force evenly, though they are slightly more complex to handle.
Mechanism Type | Force Transmission | Complexity |
---|---|---|
Direct Ejector Pin | Direct | Simple |
Push Plate | Uniform | Complex |
Impact of Mold Surface Roughness
I once worked on a project with a mold surface as smooth as a calm morning lake. This smoothness made a huge difference. Less friction happened, making ejection much easier. Rough surfaces, like sliding down an old wooden banister, usually make things challenging. Friction increases, needing more force for ejection.
Demolding Angle Considerations
Finding the right demolding angle7 takes balance, just like flipping a pancake perfectly. A proper angle eases the process, reducing the need for extra force. Wrong angles require more effort to remove the product.
Product Structure and Its Influence
- Product Size and Shape: Large products deceive with their vast contact area, needing more force to eject. Complex shapes challenge, but solving them feels rewarding.
- Product Wall Thickness: Thick walls cling after cooling, requiring more force for removal, similar to a sweater that fits tightly after washing.
Material Factors in Ejection Force
Materials like polycarbonate often increase holding forces due to high shrinkage rates. Different plastics behave differently. Understanding these traits really helps avoid problems.
Ejector and Sleeve Pin Characteristics
The diameter and length8 of ejector pins are very important. Larger diameters endure more force and shorter ones limit bending risks during ejection. Balance is crucial for best results.
Feature | Effect on Force |
---|---|
Larger Diameter | Greater Capacity |
Shorter Length | Less Bending |
Studying these factors provides a clear path to improve mold designs for efficiency and quality. Adjusting these elements improves the manufacturing process and product results.
Direct ejector pins provide uniform ejection force.False
Direct ejector pins transmit force directly, not uniformly, unlike push plates.
Larger ejector pin diameters support greater forces.True
Larger diameters offer more strength to withstand and transmit greater forces.
How Do Plastic Material Characteristics Influence Ejection Force?
Sometimes, plastics stick tightly to their molds while others glide out smoothly. This difference occurs due to the material’s unique properties. Some plastics are really sticky, holding onto the mold. Others are slippery. The way they behave probably depends on their surface texture and temperature. So, next time you notice this, remember꞉ the plastic’s nature makes the difference.
Plastic material traits such as shrinkage, elastic modulus and friction coefficient are very important. They decide the ejection force needed during injection molding. High-shrinkage plastics like polycarbonate need greater ejection force. Strong clamping force forms after cooling with these plastics.
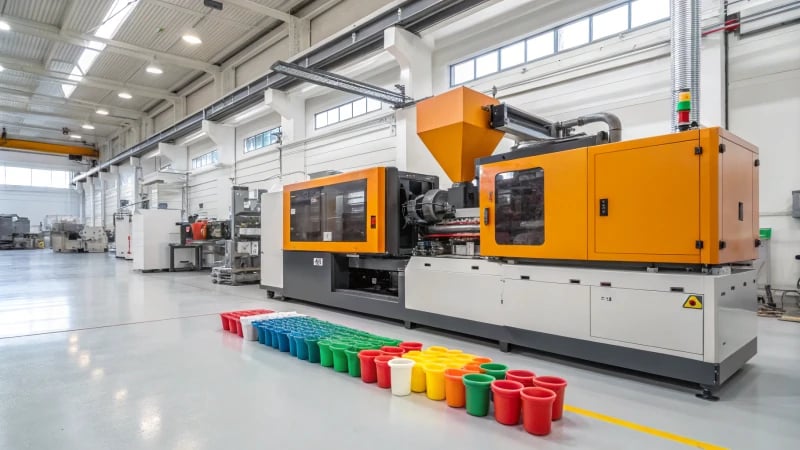
Understanding Material Characteristics
Injection molding depends greatly on plastic type9. The choice of plastic is crucial. Properties like shrinkage, elastic modulus, and friction coefficient impact how hard it is to eject a product. It’s like a jar lid that doesn’t want to open!
Shrinkage
Polycarbonate presents a real test. This plastic shrinks a lot. It fits so tightly in the mold when it cools. You might feel like you need superhero strength to remove it.
Material | Shrinkage (%) | Example Application |
---|---|---|
Polycarbonate | 0.5 – 0.7 | Optical lenses |
Polyethylene | 1.5 – 2.5 | Plastic bags |
Elastic Modulus
Elastic modulus measures how much a material changes shape under pressure. With low elastic modulus, material bends easily. Adjusting ejection force10 carefully prevents cracking or bending the piece.
Friction Coefficient
Friction coefficient throws its challenges too. Some plastics stick tightly. Polyoxymethylene (POM), for instance, grips so much it takes extra strength to slide from the mold. Learning the right force was tricky for me.
Product Structure Factors
Size impacts the force needed. Larger items demand more strength. Thicker walls also mean more material, more shrinkage, and more mold grip.
Grasping these details taught me the importance of choosing the right mold and material for smooth production and high-quality parts.
Mold Structure and Ejector System
Mold design holds significance as well. Different ejector types, like push plates, spread force in diverse ways. These designs are often complex.
Studying these aspects allows manufacturers to produce high-quality goods while reducing issues like deformation or weak ejection forces.
Understand how various mold design techniques11 solve these problems effectively.
Polycarbonate requires less ejection force than polyethylene.False
Polycarbonate has a higher shrinkage rate, requiring more ejection force.
High friction coefficient increases ejection force in molding.True
Higher friction increases resistance, thus requiring more force for ejection.
Why are ejector pin dimensions and material strength so important?
Have you ever tried baking a cake without a non-stick pan? Ejector pins in injection molding do something similar. They push the product out smoothly. The product doesn’t stick.
Ejector pin dimensions and material strength are very important. They decide the force needed for ejection. They also influence the product’s surface quality and mold lifespan. Correctly sized and strong pins stop flaws. They also help in easy demolding.
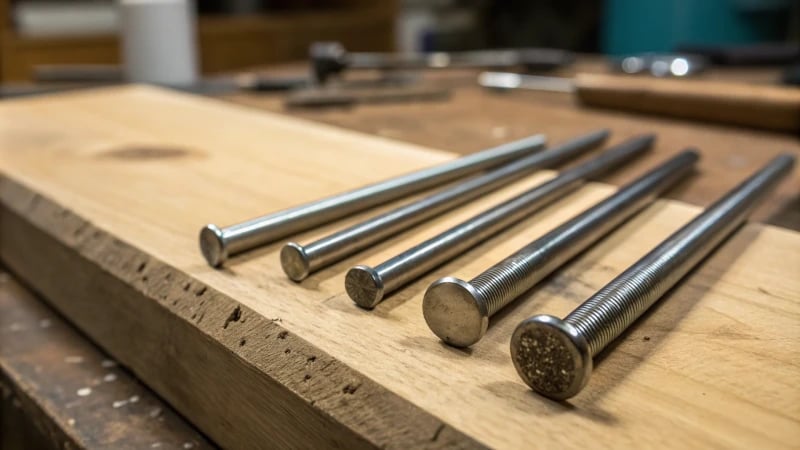
Understanding Ejection Force Needs
I remember my first big project – designing a large plastic cover for a gadget. Watching it form was thrilling, but getting it out of the mold was tough. Bigger products stick more to molds because of their large surface area. Thick walls also cause problems! Thicker walls shrink more when they cool, making them grip the mold harder. It feels like trying to pull apart Velcro. You need strength.
Mold Design Factors
The ejector mechanism plays a key role in getting parts out of molds successfully. Early in my career, I used a simple pin mechanism, thinking it was the best choice. But uneven ejections proved me wrong. A push plate might have spread the force better.
Smooth mold surfaces are important too – they lessen friction, making it easier to remove the product. It feels like driving on a smooth road compared to a bumpy one.
Mold Factors | Impact on Ejection |
---|---|
Surface Roughness | Lowers Friction |
Demolding Angle | Reduces Clamping Force |
Effect of Material Properties
The type of plastic changes things a lot. Polycarbonate, for example, shrinks a lot, like trying to remove chewing gum from a shoe. More force is needed.
Don’t ignore the elastic modulus; it’s like the material’s flexibility rating. A lower modulus means it bends more during ejection, so you have to be careful with the force to avoid bending it too much.
Ejector Pin Size and Toughness
Size of the pins really matters. I like to use pins that are thicker and shorter because they handle pressure without bending.
Materials like SKD61 are top choices for me. They are strong and perform well under pressure, like good hiking boots on rough trails.
Ejector Pin Features | Benefits |
---|---|
Large Diameter | Greater Force Resistance |
Shorter Length | Reduced Bending Risk |
High-Strength Material | Enhanced Durability |
Learning these details helped me improve mold designs. It’s about finding the right balance between being efficient and keeping quality.
If you’re interested, dive into ejector pin materials12 to see how they fit into modern manufacturing plans.
With this understanding, smoother production and fewer downtimes are likely.
Larger ejector pins reduce bending risk.False
Shorter lengths, not larger diameters, reduce bending risks.
Polycarbonate requires high ejection forces due to shrinkage.True
Polycarbonate's high shrinkage increases the necessary ejection force.
Conclusion
Ejection force in injection molding is influenced by product size, shape, wall thickness, material properties, and ejector mechanism design, impacting demolding efficiency and product quality.
-
Explore how larger ejector pins help in effectively managing increased holding forces during demolding. ↩
-
Learn about strategies to manage high ejection forces needed for products with complex shapes. ↩
-
Understand why materials with high shrinkage require greater ejection forces. ↩
-
Discover how different designs impact force distribution and efficiency. ↩
-
Learn about material properties that influence ejection force requirements. ↩
-
Learn about different ejector mechanisms and how they affect force distribution. ↩
-
Explore how proper demolding angles reduce ejection force. ↩
-
Understand how ejector pin dimensions influence ejection force capacity. ↩
-
Click to explore how different plastic properties impact the necessary ejection force in molding. ↩
-
Learn why adjusting the ejection force based on elastic modulus is crucial to prevent deformation. ↩
-
Find out how mold design strategies can help minimize required ejection forces effectively. ↩
-
Provides insights into durable materials for ejector pins ensuring longevity. ↩