Injection molding requires precision, especially when determining the right draft angle for molds.
The ideal draft angle in injection molding is influenced by plastic material properties, product shape and size, and mold structure. Adjusting these variables ensures smooth demolding and high-quality production.
While understanding these primary factors is essential, applying them effectively to your specific mold designs can be complex. Read on to discover detailed guidelines and expert tips to ensure optimal injection molding processes.
Polypropylene shrinkage rate is 0.4 - 0.7%.False
Polypropylene shrinkage is generally 1.0 - 2.5%, not 0.4 - 0.7%.
Higher product height increases demolding difficulty.True
Taller products increase friction with the mold, complicating demolding.
How Does Plastic Material Affect Draft Angle?
Understanding how plastic material properties influence draft angle is crucial for optimal mold design in manufacturing.
Plastic material affects draft angle through its shrinkage rates, elasticity, and the complexity of the product’s shape. Materials with higher shrinkage require a larger draft angle to ensure smooth demolding, while soft materials with low elasticity need increased slope to prevent deformation. Complex shapes also demand draft angles.
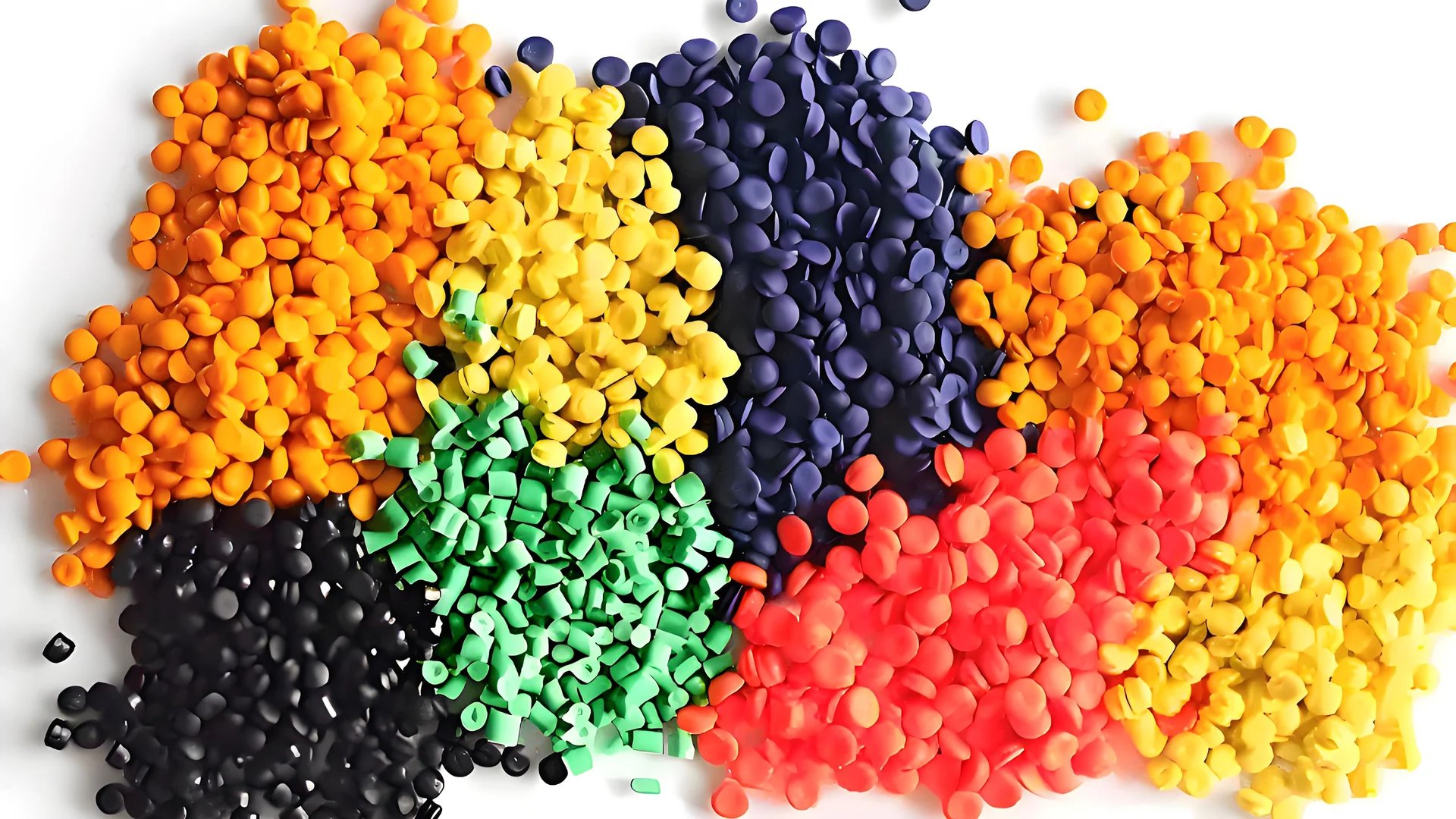
The Role of Shrinkage in Draft Angle
Shrinkage is a critical factor in determining draft angle. For example, materials like polypropylene (PP) with a shrinkage rate of 1.0 – 2.5% need a larger slope compared to polystyrene (PS), which has a shrinkage rate of about 0.4 – 0.7%. This is because high shrinkage can cause the product to cling tightly to the mold core during demolding1. A draft slope of 1° – 3° is often necessary for high-shrinkage plastics, whereas materials with lower shrinkage might only require 0.5° – 1.5°.
Modulus of Elasticity and Its Influence
Plastics with a low modulus of elasticity, such as soft PVC, are more prone to deformation and stretching when demolded. This necessitates a larger draw slope to facilitate smooth removal without damaging the product. In contrast, harder plastics can tolerate smaller slopes. This flexibility helps manufacturers determine the best angle for different material types2.
Impact of Product Shape and Size
The shape complexity and size of the product significantly affect the required draw slope. Products with intricate designs, like those featuring inverted buckles or reinforcements, need a larger slope—up to 3° – 5°—to ensure seamless demolding. For simpler items, such as flat surfaces or cylinders, a slope of 0.5° – 1° suffices. Additionally, taller products generate more friction during demolding, thus requiring greater slope angles for successful ejection from the mold cavity3.
Considering Mold Structure and Surface Roughness
In multi-cavity molds, the spatial relationship between cavities can influence draft angle decisions. A well-thought-out design prevents issues that arise from overly compact structures. Smooth mold surfaces aid in easy demolding, allowing for reduced slope angles. However, rough surfaces necessitate increased slopes to mitigate resistance during the ejection process4. Proper surface treatment can thus enhance efficiency in mold design.
Polypropylene has a shrinkage rate of 1.0 - 2.5%.True
Polypropylene's shrinkage rate ranges from 1.0% to 2.5%.
Higher product height requires smaller mold pulling tilt.False
Higher product height increases friction, needing larger tilt.
Why Is Product Shape Crucial in Mold Design?
Understanding product shape is vital in mold design as it affects manufacturing efficiency, quality, and cost.
Product shape in mold design dictates the ease of production, material usage, and end-product quality. Complex shapes may require advanced mold structures and affect demolding processes, while simple shapes streamline production and reduce costs. Understanding these dynamics is essential for efficient and high-quality manufacturing outcomes.
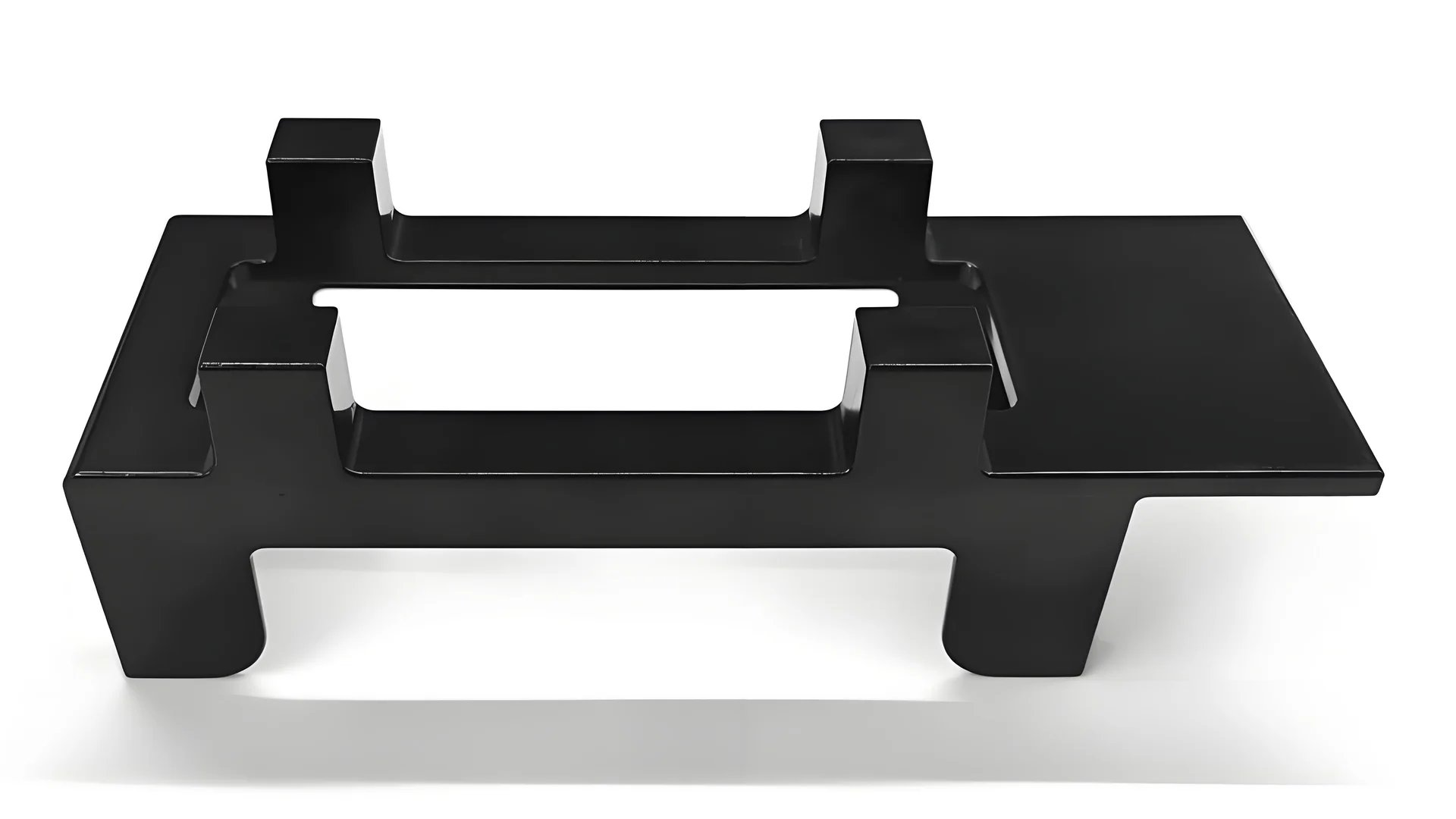
The Role of Plastic Material Properties
The properties of plastic materials are pivotal in determining mold design. For instance, plastics with high shrinkage rates, like polypropylene, require a larger draft angle to prevent issues during demolding. If shrinkage is significant, the mold pulling slope should be increased to accommodate these properties. In contrast, materials such as polystyrene have lower shrinkage, which allows for a smaller draft angle.
Similarly, the modulus of elasticity5 plays a critical role. Soft plastics with low elasticity may deform easily and necessitate a larger mold pulling slope for smooth demolding. This ensures that the final product maintains its intended shape without distortion.
Impact of Product Shape and Size
The complexity of a product’s shape significantly influences mold design. Products with intricate structures, such as inverted buckles or reinforcements, require a more substantial draft angle. For example, a plastic box with an internal invert might need a slope of 3° – 5° to ensure proper release from the mold.
Product height also affects mold design. Taller products increase friction during demolding and may require steeper draft angles to ensure they are released without damage. When designing molds for taller products, engineers must carefully balance the slope to optimize the manufacturing process.
Considerations for Mold Structure and Surface Roughness
The structural design of the mold itself is crucial when accommodating different product shapes. In multi-cavity molds, adequate spacing must be considered to avoid compactness that impedes demolding. This becomes even more complex in designs like hot runner multi-cavity injection molds, where spatial relationships between cavities are critical.
Surface roughness is another key factor. A smoother mold surface reduces friction during demolding, allowing for a smaller draft angle. Conversely, rougher surfaces may necessitate a greater slope to ensure that products do not stick to the mold, affecting the efficiency of the production line.
By considering these factors, engineers can create effective mold designs that not only facilitate production but also enhance product quality. Understanding these aspects helps in optimizing the mold design process6 and ultimately contributes to successful manufacturing outcomes.
Polypropylene shrinkage is 1.0-2.5%.True
Polypropylene typically has a shrinkage rate of 1.0-2.5%.
Smooth mold surfaces require larger draft angles.False
Smooth mold surfaces allow for smaller draft angles due to easier demolding.
What Role Does Mold Structure Play in Demolding?
Mold structure significantly influences the demolding process in manufacturing, impacting efficiency and product quality. Understanding its role can help optimize design.
Mold structure is crucial in demolding as it dictates the ease of part removal without damage. Considerations include the mold’s geometry, surface roughness, and the spatial arrangement of cavities, especially in multi-cavity molds. Proper design minimizes friction and reduces the risk of defects during demolding.
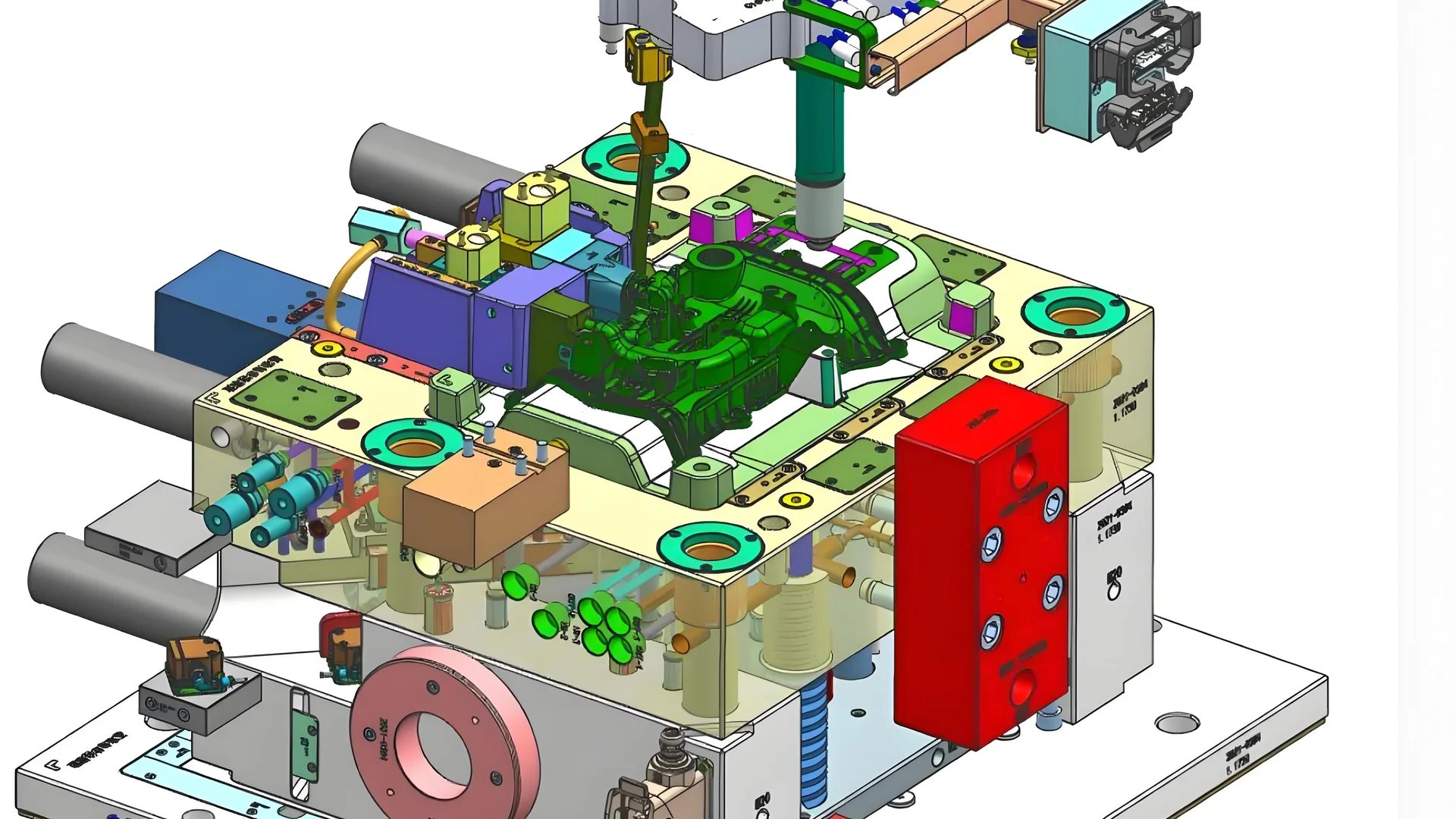
The Impact of Plastic Material Properties
Understanding how different plastic materials react during demolding is vital. For instance, shrinkage rates vary between materials. Polypropylene (PP) and polystyrene (PS)7 demonstrate different shrinkage behaviors. High shrinkage materials might require larger draft angles to prevent the product from clinging to the core. Materials with a low modulus of elasticity, such as soft PVC, are prone to deformation, necessitating a steeper mold pull slope.
Shape and Size Considerations
The product’s shape complexity and height can significantly affect demolding. Complex structures, like inverted buckles or reinforcements, demand larger mold pull tapers to facilitate smooth removal. In contrast, simpler shapes like cylindrical products can have smaller draft angles. Additionally, taller products experience greater friction during demolding, requiring adjustments in tilt angles.
Mold Structure and Surface Roughness
The spatial arrangement within a mold, particularly in multi-cavity designs, is crucial. An efficient design avoids compactness that hinders proper demolding. For example, in hot runner multi-cavity molds, ensuring enough space for each cavity extraction is essential. Moreover, surface roughness8 plays a pivotal role; smoother surfaces aid in easier demolding, allowing for reduced draft angles compared to rougher surfaces.
Geometry and Design of Mold Components
The geometry of mold components should consider factors like the draft angle, which affects how easily a part releases from the mold. Draft angles might vary significantly based on the material properties and the desired product features. A precise understanding of these geometrical considerations9 can lead to optimized mold designs that enhance the efficiency of the production process without compromising on quality.
By examining these aspects, manufacturers can address potential issues related to demolding defects and ensure high-quality output with fewer interruptions in the production line.
PP has a shrinkage rate of 0.4 - 0.7%.False
PP shrinkage is 1.0 - 2.5%, not 0.4 - 0.7%.
A rough mold surface requires a larger draft angle.True
Rough surfaces need a larger angle to ensure smooth demolding.
How to Optimize Mold Surface Roughness for Better Results?
Unlock the secret to flawless mold finishes with effective surface roughness optimization techniques. Discover how to enhance your product’s quality and performance.
To optimize mold surface roughness, consider the plastic material properties, product shape, and mold structure. Adjust the draft angle based on shrinkage rates and surface finish. Use polishing techniques to achieve smoother surfaces for easier demolding and superior results.
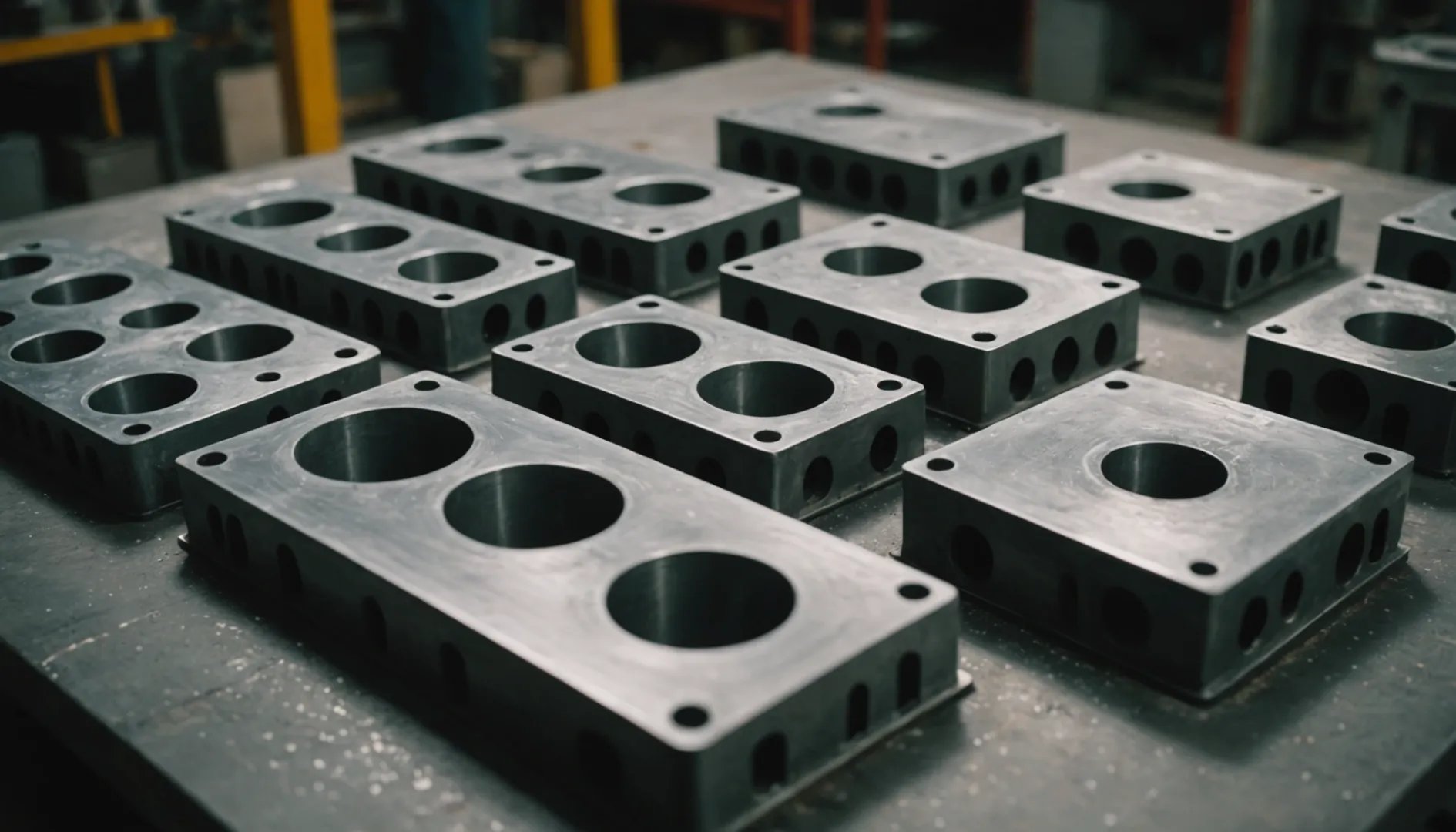
Understanding Material Properties
The optimization of mold surface roughness begins with a deep understanding of the plastic material properties10. For instance, materials with higher shrinkage rates, like polypropylene (PP), require specific adjustments in mold design to prevent issues during demolding. A key strategy is adjusting the draft angle according to the material’s shrinkage characteristics.
For plastics with a low modulus of elasticity, a slightly larger draft angle is necessary to avoid deformation during demolding. Materials such as soft PVC are more prone to stretching, requiring thoughtful consideration of demolding angles.
Evaluating Product Shape and Size
The shape and size of the product directly influence mold design. Complex structures, including inverted buckles or reinforcements, demand a larger mold pulling taper for efficient demolding. In contrast, simpler shapes like cylindrical or flat products can function with a smaller draft slope.
Additionally, product height11 plays a role in friction levels during demolding. Taller products increase friction, necessitating a steeper draft angle for smooth release. Lower products can often manage with reduced angles, offering greater flexibility in design.
Mold Structure and Surface Considerations
Mold structure intricacies, especially in multi-cavity molds, require careful planning. The spatial relationship between cavities is crucial to avoid compact designs that hinder proper demolding. For hot runner multi-cavity injection molds, it’s essential to allocate enough space for each cavity extraction.
Surface roughness impacts the ease of demolding significantly. A polished surface allows for a reduced mold pulling slope, while rough surfaces require a steeper slope. Techniques such as fine polishing12 can transform a rough surface into a smooth one, facilitating easier product release and enhancing surface quality.
Techniques for Surface Optimization
Advanced polishing techniques are critical for achieving an optimal mold finish. Methods like diamond polishing or chemical etching can significantly improve surface smoothness. Furthermore, maintaining consistent injection speed and temperature13 throughout the process is vital as fluctuations can affect surface quality.
By balancing these factors—material properties, product design, and mold structure—manufacturers can effectively optimize mold surface roughness for superior results. This not only enhances product quality but also improves efficiency in the manufacturing process.
Polypropylene has a shrinkage rate of 0.4% to 0.7%.False
Polypropylene has a shrinkage rate of 1.0% to 2.5%, not 0.4% to 0.7%.
High product height increases demolding difficulty.True
Higher product height increases friction during demolding, complicating the process.
Conclusion
The ideal draw slope in injection molding is determined by plastic properties, product shape, size, and mold structure, ensuring effective demolding and high-quality production.
-
Learn why shrinkage rates dictate draft angles in molds. ↩
-
Discover how elasticity influences plastic moldability. ↩
-
Understand how complex shapes impact draw slopes. ↩
-
Explore how surface texture affects mold ejection. ↩
-
Discover how elasticity affects plastic deformation in molding. ↩
-
Learn how effective mold design enhances production quality. ↩
-
Learn about varying shrinkage rates affecting mold design choices. ↩
-
Explore how surface smoothness facilitates easier demolding. ↩
-
Understand how draft angles influence the release of molded parts. ↩
-
Discover how different materials impact mold design choices. ↩
-
Learn why taller products need careful draft angle adjustments. ↩
-
Explore effective methods to achieve smoother mold surfaces. ↩
-
Understand how consistent conditions ensure better surface finishes. ↩