Ever wonder how those sleek plastic products are made? At the core of this process lies a remarkable technology: hydraulic systems. They power injection molding machines with precision and strength.
In injection molding machines, hydraulic systems convert mechanical energy into hydraulic energy, enabling the movement of clamping, injection, and ejector mechanisms. They provide necessary clamping force, control the speed and position of machine parts, and adjust pressure to meet specific molding requirements.
While this offers a glimpse into hydraulic systems’ vital functions, there’s so much more beneath the surface. Let’s delve deeper to uncover the intricate roles these systems play in enhancing efficiency and product quality.
Hydraulic systems in injection machines provide power for clamping.True
Hydraulic systems generate clamping force to keep molds closed, preventing leaks.
What are the Components of a Hydraulic System in Injection Molding Machines?
Understanding the components of a hydraulic system is crucial to mastering injection molding machines’ functionality.
The key components of a hydraulic system in injection molding machines include the hydraulic pump, valves, actuators, reservoir, and hydraulic fluid. These components work together to convert mechanical power into hydraulic energy, manage fluid flow, and ensure precise operation and control of the molding machine.
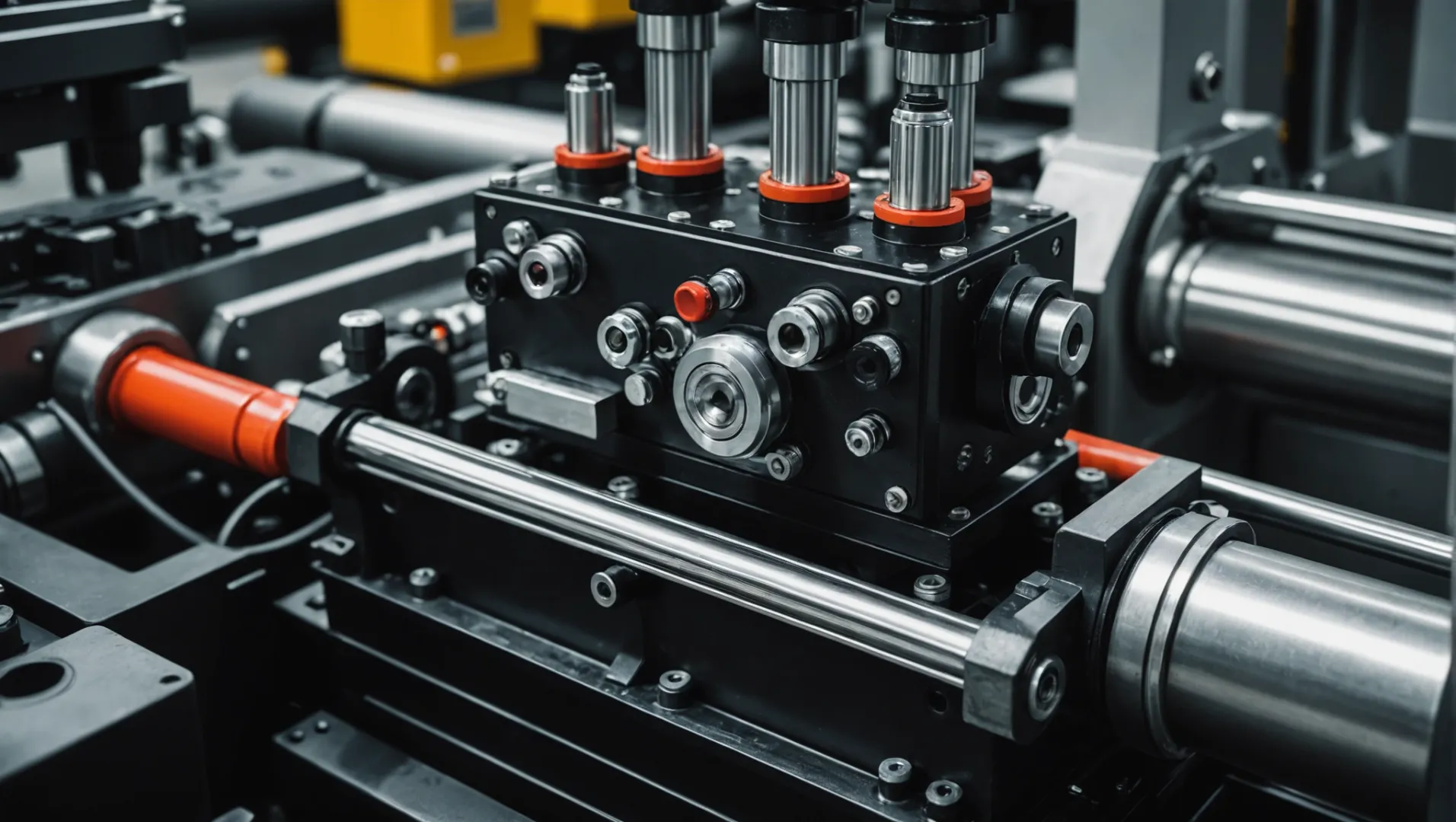
Hydraulic Pump
The hydraulic pump1 is the heart of the system, converting mechanical energy into hydraulic energy. It’s responsible for moving the hydraulic fluid through the system and creating the pressure needed to operate various machine components.
Types of Pumps
- Gear Pumps: Commonly used for their simplicity and cost-effectiveness, they provide a steady flow but are less efficient at high pressures.
- Vane Pumps: Offer higher efficiency and can handle moderate pressures, making them suitable for many injection molding applications.
- Piston Pumps: Known for high pressure and efficiency, they’re ideal for large machines requiring significant power.
Valves
Valves control the direction, pressure, and flow rate of the hydraulic fluid. They are essential for precise control over the machine’s movements.
- Directional Control Valves: Direct fluid flow to different parts of the system to control the movement of actuators.
- Pressure Control Valves: Maintain desired pressure levels, protecting the system from overload and ensuring consistent operation.
- Flow Control Valves: Regulate the speed of actuators by controlling fluid flow rate.
Actuators
Actuators convert hydraulic energy back into mechanical energy to perform work. In injection molding machines, these include:
- Cylinders: Used for linear movements such as clamping and ejection.
- Hydraulic Motors: Provide rotational motion, often driving screws in the injection process.
Reservoir
The reservoir2 holds the hydraulic fluid, providing a cooling effect and settling out contaminants. It also compensates for fluid volume changes during operation.
Hydraulic Fluid
Hydraulic fluid is crucial for transmitting power, lubricating components, sealing clearances, and dissipating heat. Selecting the right fluid involves considering viscosity, temperature stability, and contamination resistance.
Sensors and Feedback Devices
Sensors, including pressure sensors and position sensors, provide real-time feedback to ensure precision and safety. They enable automated systems to adjust operations dynamically, enhancing efficiency and product quality.
Each component plays a pivotal role in ensuring that an injection molding machine operates efficiently and effectively. Understanding these components helps in troubleshooting issues and optimizing machine performance.
Hydraulic pumps in molding machines create fluid pressure.True
Pumps convert mechanical energy into hydraulic energy, creating pressure.
Valves in hydraulic systems are only for fluid storage.False
Valves control fluid direction, pressure, and flow rate, not storage.
How Does Clamping Force Affect Injection Molding Quality?
Clamping force is a critical factor in injection molding, directly impacting product quality and dimensional accuracy.
Clamping force in injection molding ensures the mold remains securely closed during the injection process, preventing plastic leakage and ensuring precise product dimensions. Adequate clamping force contributes to the structural integrity and surface finish of the molded part, significantly affecting overall product quality.

Understanding Clamping Force in Injection Molding
In the realm of injection molding, clamping force is crucial for maintaining the mold’s integrity during the injection phase. The clamping unit of an injection molding machine is responsible for holding the two halves of the mold together with enough force to counteract the pressure exerted by the injected plastic melt. This ensures that the mold remains tightly closed, preventing any leakage of material and preserving the shape and dimensions of the final product.
Importance of Accurate Clamping Force
The accuracy of clamping force is paramount. Insufficient clamping force can lead to issues such as flash, where excess material seeps out at the parting line, compromising the aesthetics and functional aspects of the product. On the other hand, excessive clamping force can damage the mold or even the machine itself, leading to increased maintenance costs and downtime. Therefore, determining the right amount of clamping force is essential for achieving optimal product quality.
For instance, a hydraulic system can generate clamping forces ranging from a few tons to several thousand tons, depending on the size and complexity of the machine and mold. This range enables manufacturers to adjust the clamping force based on specific product requirements, ensuring precision and quality.
Mold Type | Recommended Clamping Force (tons) |
---|---|
Small Parts | 10-50 |
Medium Parts | 50-200 |
Large Parts | 200-500+ |
Factors Affecting Clamping Force
Several factors influence the determination of appropriate clamping force:
- Material Viscosity: Different plastic materials have varying viscosities. High-viscosity materials require higher clamping forces to prevent mold separation.
- Part Geometry: Complex geometries with intricate details might demand adjustments in clamping force to ensure proper filling without defects.
- Mold Material: The strength and durability of mold materials can affect how much clamping force they can withstand without deformation.
The Role of Hydraulic Systems in Managing Clamping Force
Hydraulic systems play a pivotal role in managing and delivering precise clamping forces. By controlling hydraulic pressure and flow, these systems ensure that the force applied is consistent and adjustable according to specific production needs3. The integration of feedback mechanisms like sensors allows for real-time monitoring and adjustments, enhancing both safety and quality.
By understanding and optimizing clamping force, manufacturers can improve production efficiency, reduce waste, and enhance product consistency, ultimately leading to superior outcomes in injection molding processes.
Excessive clamping force can damage the mold.True
Too much force may harm the mold, increasing maintenance costs.
Hydraulic systems can't adjust clamping force.False
Hydraulic systems can adjust force through pressure and flow control.
Why is Pressure Control Crucial in Hydraulic Systems?
Effective pressure control is vital in hydraulic systems, ensuring safe, efficient operations and high-quality outcomes in injection molding.
Pressure control in hydraulic systems prevents system overload, ensures consistent product quality, and adapts to various process demands.
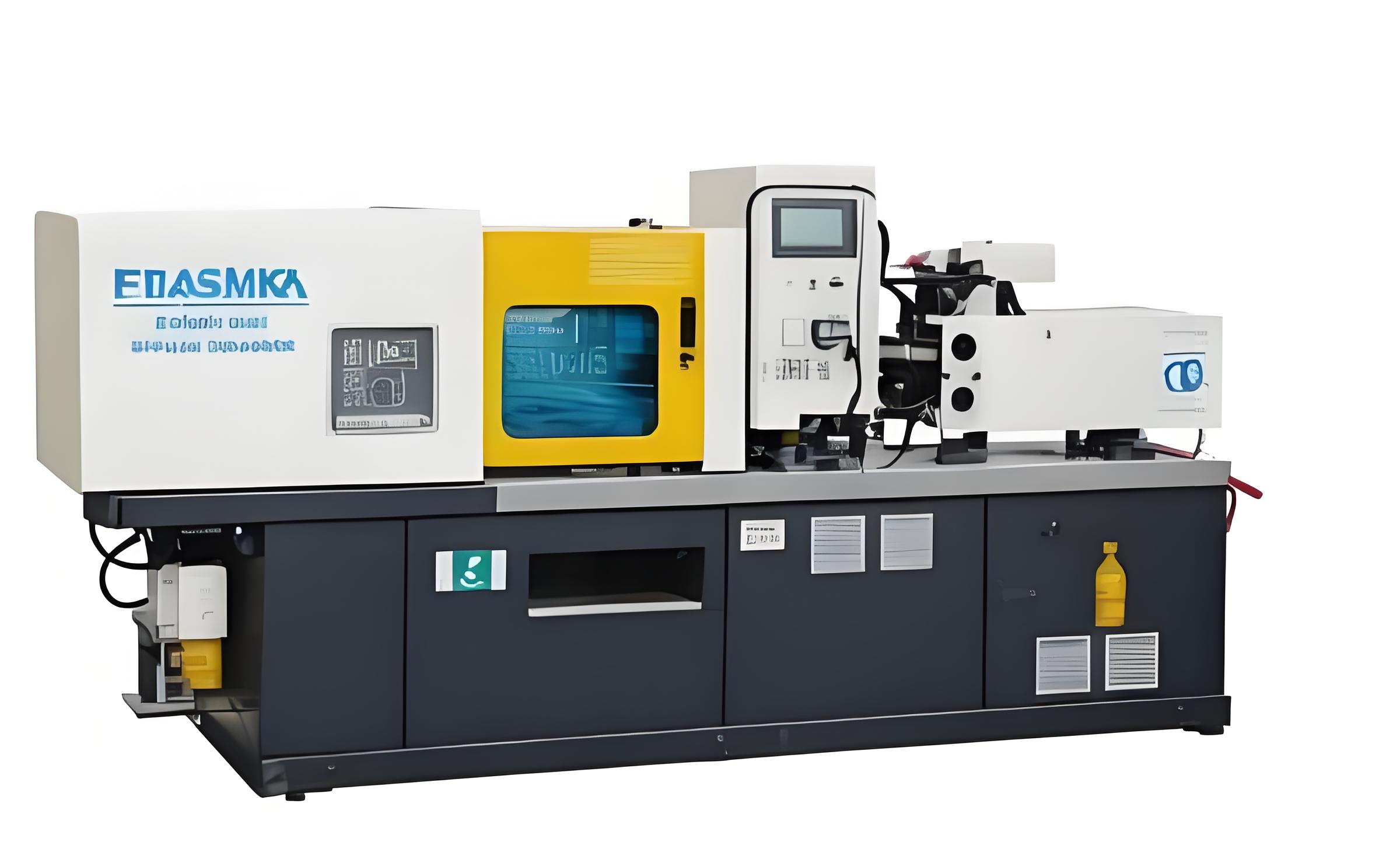
Ensuring System Safety and Stability
Pressure control is a critical aspect of hydraulic systems as it safeguards the machinery against potential damage. For instance, when system pressure exceeds safe limits, a pressure control valve can automatically relieve the excess pressure, thereby preventing system overload damage4. This mechanism is crucial for maintaining the long-term integrity of the hydraulic system and avoiding costly repairs.
Real-time monitoring of pressure levels through sensors further enhances safety by allowing operators to keep the system within its designated safe range. This is particularly important in high-pressure environments like injection molding, where the risk of sudden pressure spikes could be detrimental to both the machine and the final product.
Achieving Consistent Product Quality
In the context of injection molding, precise pressure control directly impacts the quality of the molded products. By adjusting the injection pressure to suit different materials and product designs, manufacturers can ensure that each mold is filled adequately. For example, higher pressures may be required for thin-walled products to guarantee complete cavity filling, whereas lower pressures might be more appropriate for thicker designs to reduce internal stress and deformation.
A failure in pressure control can lead to defects such as incomplete filling or excessive flashing, which compromises the overall product quality. Thus, maintaining optimal pressure levels is essential for achieving consistent and reliable manufacturing outcomes.
Adapting to Diverse Process Requirements
The ability to adjust pressure in hydraulic systems allows for flexibility in meeting various process demands5. This adaptability is crucial in industries where different plastic materials or product specifications necessitate specific pressure settings. For instance, altering the pressure can help in optimizing cycle times, improving efficiency, and reducing material wastage.
Moreover, hydraulic systems equipped with advanced pressure control capabilities can switch seamlessly between manual, semi-automatic, and fully automatic modes. This versatility supports diverse production needs and enhances overall productivity by allowing operations to adapt quickly to changing requirements without sacrificing quality or safety.
Pressure control prevents system overload in hydraulics.True
Pressure control valves relieve excess pressure, preventing overload damage.
Inconsistent pressure in injection molding affects product quality.True
Proper pressure ensures molds fill correctly, avoiding defects like flashing.
How Do Hydraulic Systems Enhance Automation in Injection Molding?
Automation in injection molding has reached new heights, thanks to advanced hydraulic systems that streamline operations.
Hydraulic systems enhance automation in injection molding by providing precise control over movement, enabling multiple operational modes, and facilitating efficient pressure adjustments. These systems improve production efficiency, ensure high-quality outputs, and adapt to varied manufacturing needs, making them essential in modern injection molding processes.
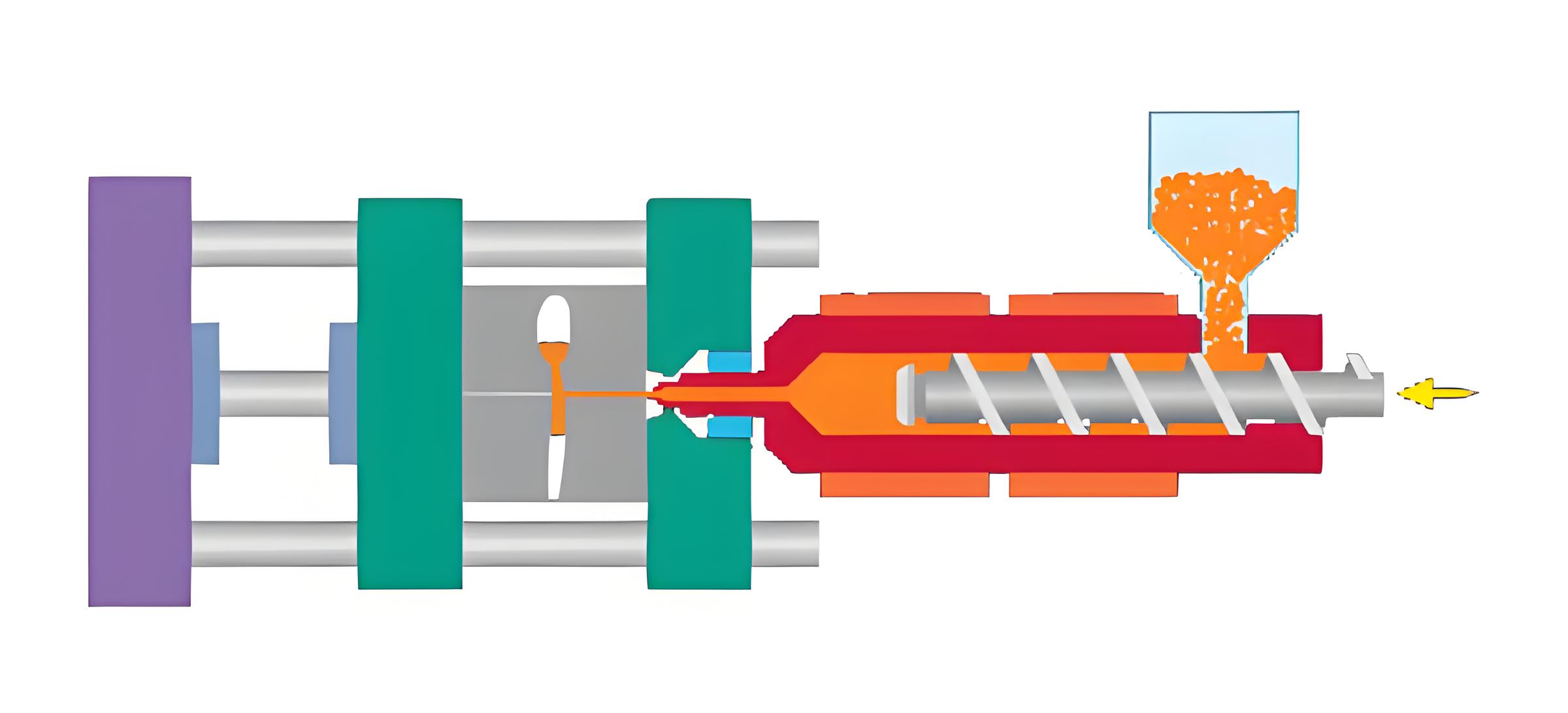
Precision Control in Hydraulic Systems
Hydraulic systems play a crucial role in providing power and precision6 to injection molding machines. By regulating hydraulic flow and pressure, these systems can accurately control the speed and position of machine movements. For example, the injection speed can be adjusted according to the type of plastic used, ensuring optimal molding quality. Position sensors further enhance this precision by maintaining the correct mold alignment, which is vital for achieving dimensional accuracy in products.
Multiple Operational Modes
One of the standout features of hydraulic systems is their ability to support various operational modes, such as manual, semi-automatic, and fully automatic. This versatility allows manufacturers to tailor operations to their specific needs and production requirements. In automatic modes, the hydraulic system can programmatically manage the sequence and timing of each action, significantly boosting production efficiency and reducing the need for manual oversight.
Efficient Pressure Adjustments
Hydraulic systems also facilitate precise pressure control7 during the injection process. By adjusting the hydraulic pump’s output pressure or utilizing pressure control valves, these systems can cater to different material properties and product specifications. For instance, thin-walled products may require higher injection pressures to ensure complete mold filling, whereas thick-walled products might benefit from reduced pressure to prevent stress-related deformities.
Functionality | Manual Mode | Semi-Automatic Mode | Fully Automatic Mode |
---|---|---|---|
Action Sequencing | Manual | Partial | Automated |
Pressure Adjustment | Manual | Manual/Automated | Automated |
Speed Control | Manual | Manual/Automated | Automated |
These adaptations enable hydraulic systems to seamlessly integrate with automated processes, ensuring consistent quality and reliability in injection molding operations. Moreover, real-time monitoring of system pressure through sensors safeguards against overloads and maintains system integrity, contributing to safe and stable machine operation.
Hydraulic systems allow only manual operation in injection molding.False
Hydraulic systems support manual, semi-automatic, and automatic modes.
Precision control in hydraulics ensures mold alignment accuracy.True
Position sensors in hydraulic systems maintain correct mold alignment.
Conclusion
Hydraulic systems are essential for efficient injection molding. They ensure precise movements and adaptable pressures while optimizing operations for higher quality products.
-
Explore various pump types to optimize machine efficiency.: The pump pushes the fluid through the lines. The pumps most commonly used on injection-molding machines are the balanced-vane type. ↩
-
Learn how reservoirs support fluid management and system stability.: A reservoir: The reservoir stores the hydraulic fluid. Valves: The … The three basic functions of a hydraulic system in an injection molding machine are:. ↩
-
Explore how hydraulic systems ensure precise clamping force management.: Clamping devices maintain the mold closed against pressures created when injection pressure pulls plastic into the closed mold. ↩
-
Learn how pressure control valves protect systems from dangerous overloads.: A relief valve opens and bypasses fluid when pressure exceeds its setting. The valve then closes again when pressure falls. ↩
-
Discover the impact of hydraulic pressure adjustments on manufacturing efficiency.: Hydraulically, pressure compensation reduces the volumetric efficiency of a pump by redirecting pump outlet flow to the compensator control … ↩
-
Explore how precision control enhances injection molding accuracy.: Hydraulic machines are often considered to be more effective where greater clamp forces or high linear speeds are required, where plastic nozzle pressures are … ↩
-
Understand why precise pressure control is vital for quality products.: Pressure control valves are used in hydraulic systems for obtaining pressure-related regulation and control tasks. The control tasks include … ↩