OPTIMIZATION
blog & article
read our latest newsletter
Whether you’re curious about material selection, product design, mold design, mold making and injection molding, feel free to ask us anything. Our team is ready to provide the guidance and insights you need.
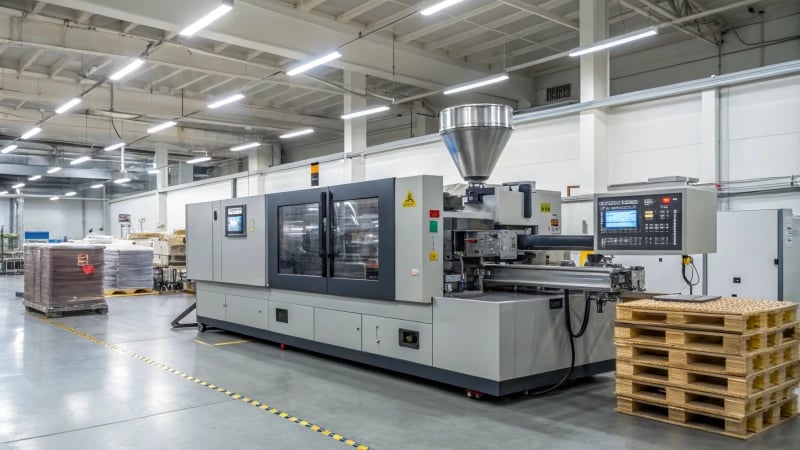
How Can You Choose the Right Injection Molding Machine to Avoid Improper Material Pretreatment?
Selecting the appropriate injection molding machine is crucial for achieving high-quality products. Key factors include an efficient dehumidification and drying system to manage moisture levels, precise temperature control for optimal plasticization, and a suitable screw design tailored to specific materials. ...
OPTIMIZATION
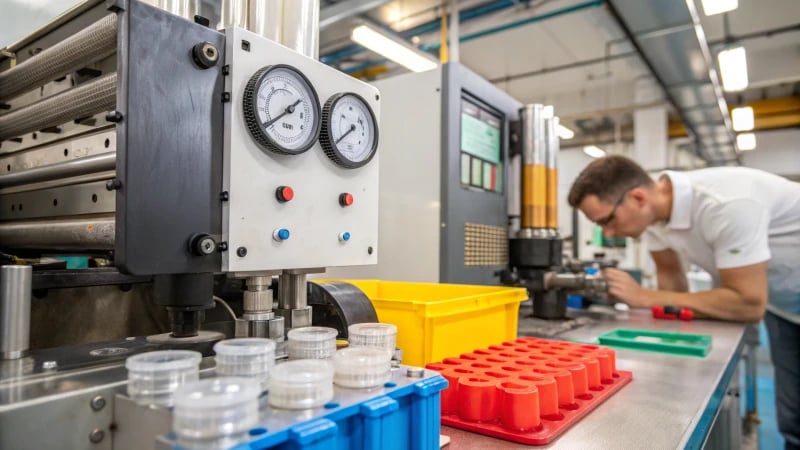
What is the Optimal Injection Pressure Range and How to Determine It?
Understanding the optimal injection pressure range is crucial in injection molding. This article explores how material characteristics like viscosity and flowability, along with product structure and mold design, influence the required pressure settings. Typically ranging between 30 to 150 MPa, ...
OPTIMIZATION
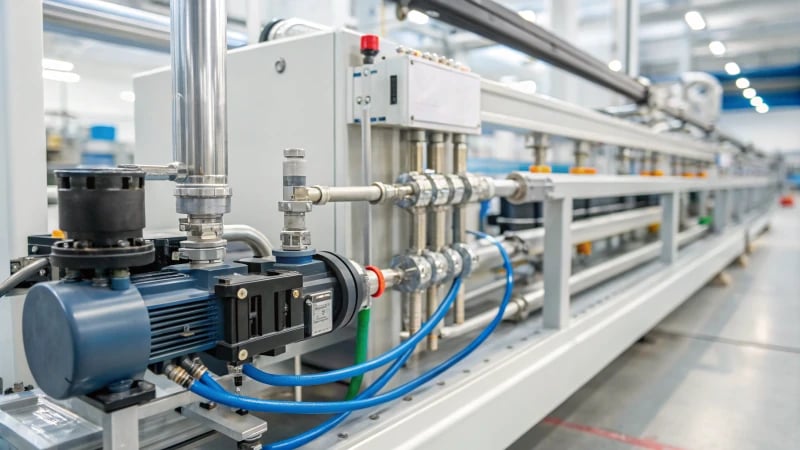
How Can You Minimize the Impact of High Mold Temperature on Injection Molded Product Strength?
High mold temperatures can significantly impact the strength and durability of injection molded products. This article explores strategies to minimize these effects by optimizing cooling systems, adjusting injection molding parameters, and selecting appropriate materials. Key techniques include redesigning cooling channels ...
OPTIMIZATION
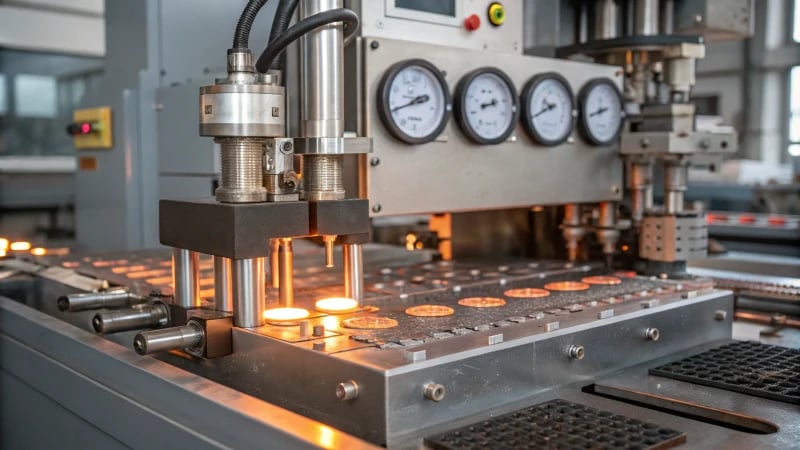
What Key Factors Should You Consider When Adjusting Injection Pressure?
This article explores the key factors influencing injection pressure adjustments in molding processes. It emphasizes the importance of product design, material viscosity, wall thickness, and mold characteristics. Understanding how these elements interact can significantly impact the quality of molded products. ...
OPTIMIZATION
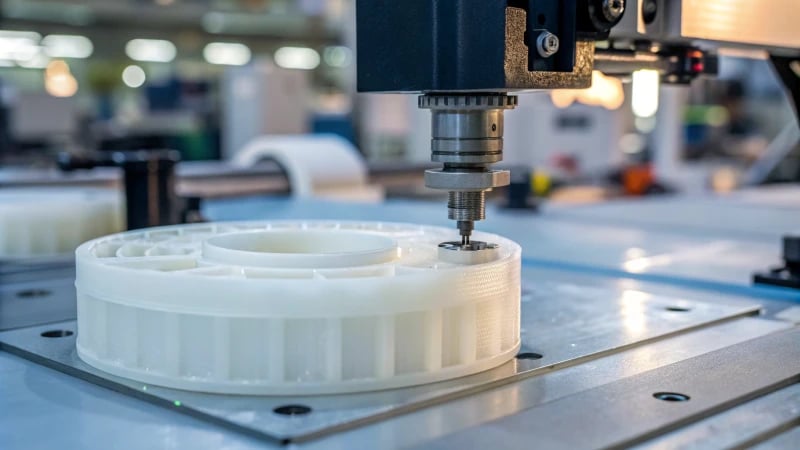
How Does Injection Pressure Affect the Properties of Molded Parts?
Injection pressure is a critical factor in injection molding that affects various properties of molded parts. It determines the appearance quality by influencing flash, surface gloss, and weld marks. Dimensional accuracy relies on proper pressure to maintain stability and uniform ...
OPTIMIZATION
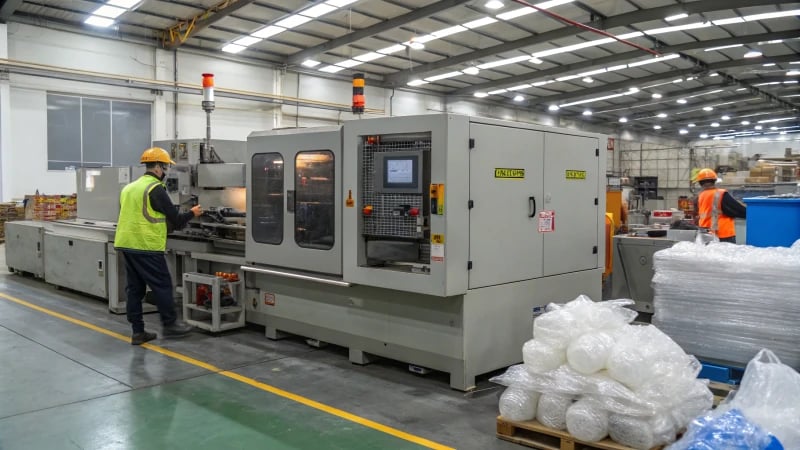
What Is the Best Way to Determine the Optimal Injection Pressure for an Injection Molding Machine?
This article explores the best practices for determining the optimal injection pressure in injection molding. It emphasizes the importance of understanding material characteristics, particularly the melt flow index (MFI), which indicates how easily a polymer flows under pressure. The relationship ...
OPTIMIZATION
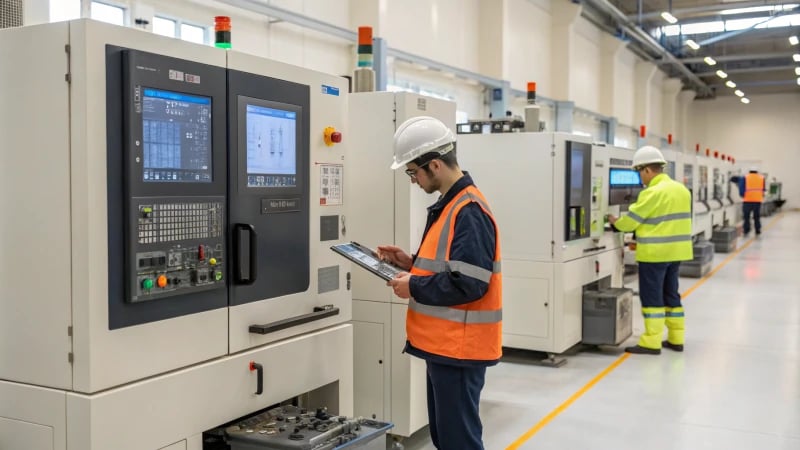
How Can You Enhance Dimensional Accuracy in Injection Molded Parts by Optimizing Injection Pressure?
This article explores how optimizing injection pressure can significantly enhance the dimensional accuracy of injection molded parts. It emphasizes the importance of understanding material properties, mold design complexities, and the implementation of advanced techniques such as segmented pressure control and ...
OPTIMIZATION
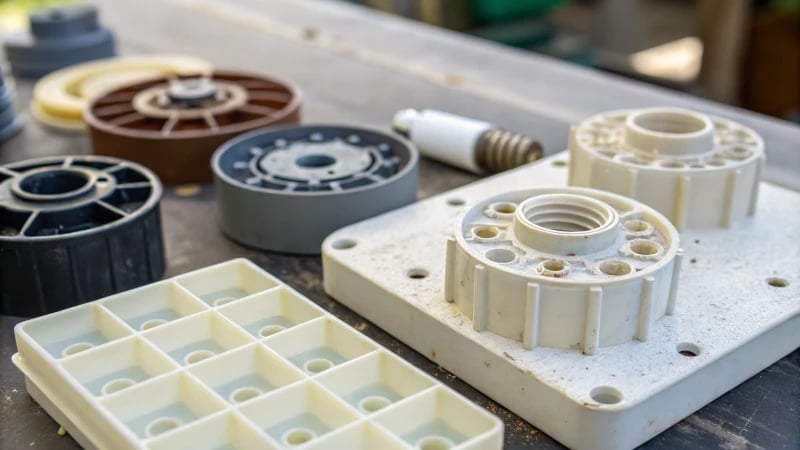
How Can You Effectively Address Flash Problems in Injection Molded Products?
Flash defects in injection molded products can be frustrating and costly. This article outlines practical steps to effectively address these issues by focusing on mold adjustments, optimizing injection molding parameters, and selecting appropriate materials. Key strategies include checking the mold ...
OPTIMIZATION
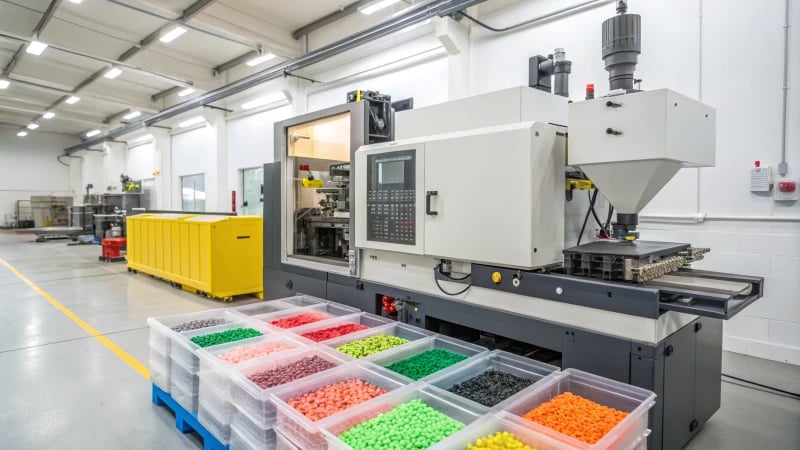
How Can You Enhance the Production Efficiency of Injection Molds?
This article explores various strategies to enhance the production efficiency of injection molds. Key methods include optimizing mold design with balanced runner systems and conformal cooling channels, selecting appropriate materials, and implementing advanced technologies such as gas-assisted and multi-color injection ...
OPTIMIZATION
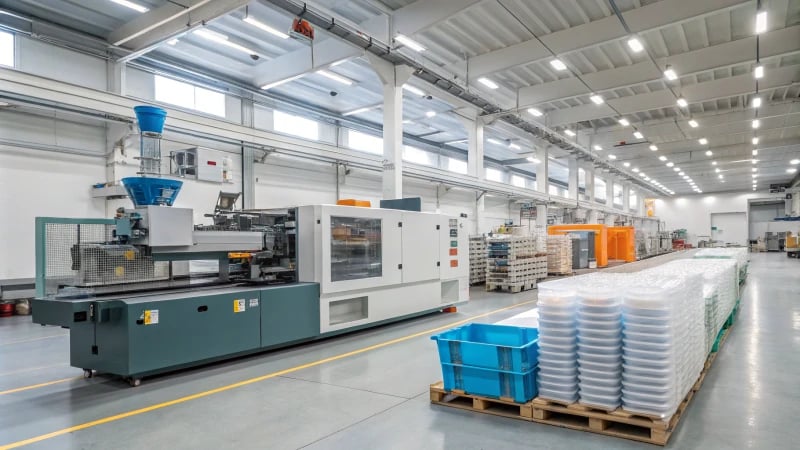
How Can You Improve Production Efficiency in Injection Molding?
Improving production efficiency in injection molding involves several strategies. Key actions include optimizing mold design with balanced runner systems and efficient cooling channels, selecting appropriate materials like P20 or H13 steel for durability, and standardizing molds to facilitate quick replacements. ...
OPTIMIZATION

How Can You Minimize the Negative Impact of Injection Speed on the Tensile Strength of Plastic Products?
This article explores how to minimize the negative impact of injection speed on the tensile strength of plastic products. Key strategies include optimizing injection speed parameters, adjusting mold structure, and implementing effective material pretreatment and post-treatment processes. By fine-tuning injection ...
OPTIMIZATION
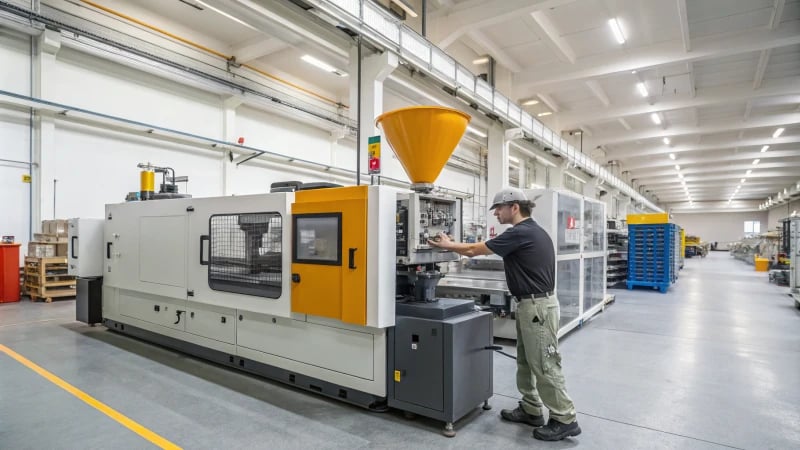
How Can You Adjust Injection Speed to Optimize Impact Strength?
This article explores how adjusting injection speed in the molding process can optimize impact strength. It emphasizes the importance of understanding material properties—differentiating between crystalline and non-crystalline plastics—and adapting speeds accordingly. For crystalline plastics like polypropylene, a controlled speed of ...
OPTIMIZATION
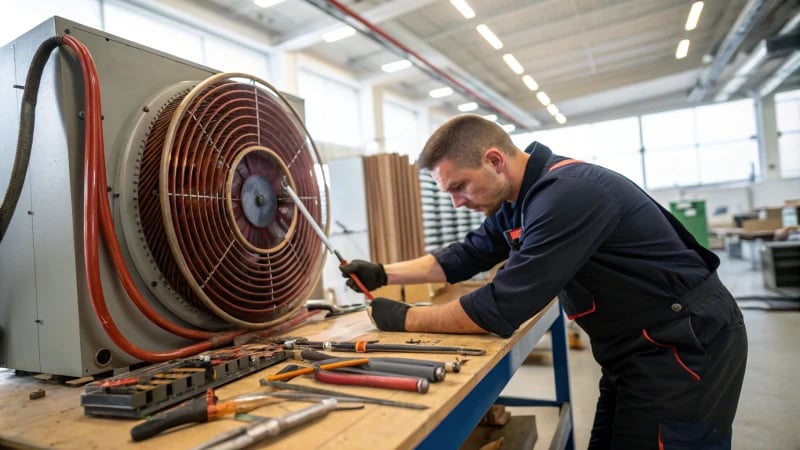
What Key Details Should You Consider When Installing a Heating Ring?
Installing a heating ring on machinery demands precision and attention to detail. Key steps include inspecting the heating coil and barrel for damage, ensuring specifications match, achieving a snug fit for optimal heat transfer, securing electrical connections properly, and conducting ...
OPTIMIZATION
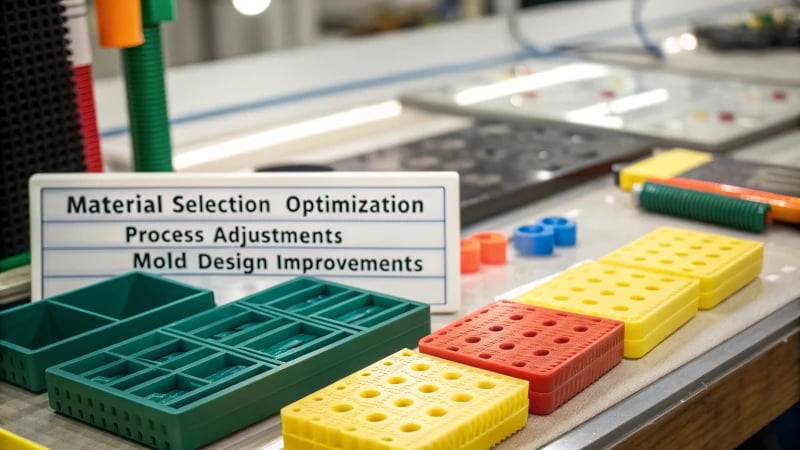
How Can Product Design Optimization Solve Warpage Defects in Injection Molded Parts?
This article explores how product design optimization can address warpage defects in injection molded parts. Key strategies include maintaining uniform wall thickness to ensure even cooling, strategically designing ribs to enhance strength without increasing thickness, and simplifying complex shapes to ...
OPTIMIZATION
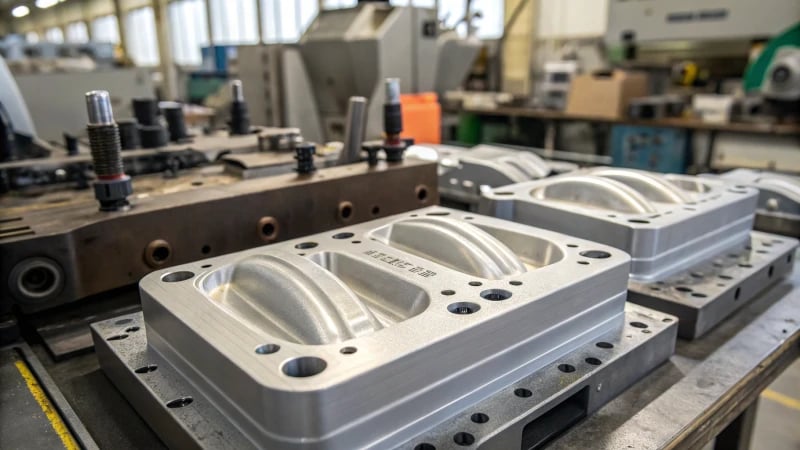
How Do Warpage Defects Affect the Performance of Injection Molded Parts?
Warpage defects significantly impact the performance of injection molded parts by altering their dimensional accuracy, mechanical properties, and appearance. These issues arise from uneven cooling, material shrinkage, and poor mold design. Warped components can lead to assembly challenges and functional ...
OPTIMIZATION
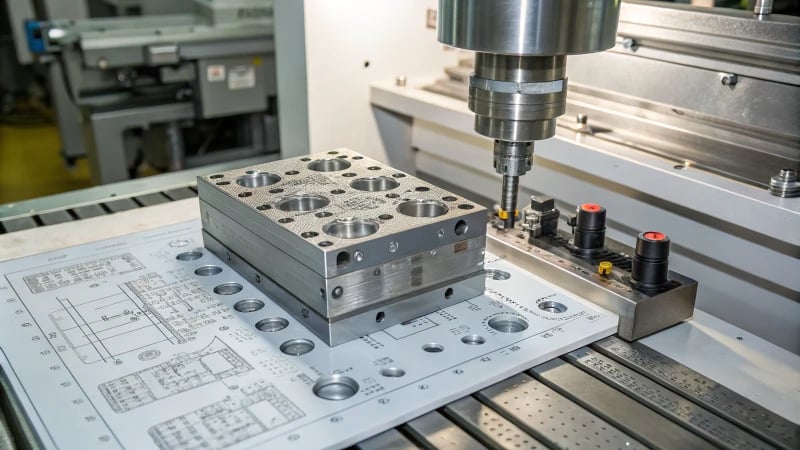
What Are the Best Methods to Determine Gate Location and Size?
This article explores the best methods for determining gate location and size in injection molding. Proper gate placement is essential for achieving optimal melt flow balance, which directly impacts product quality by preventing defects such as air pockets and uneven ...
OPTIMIZATION
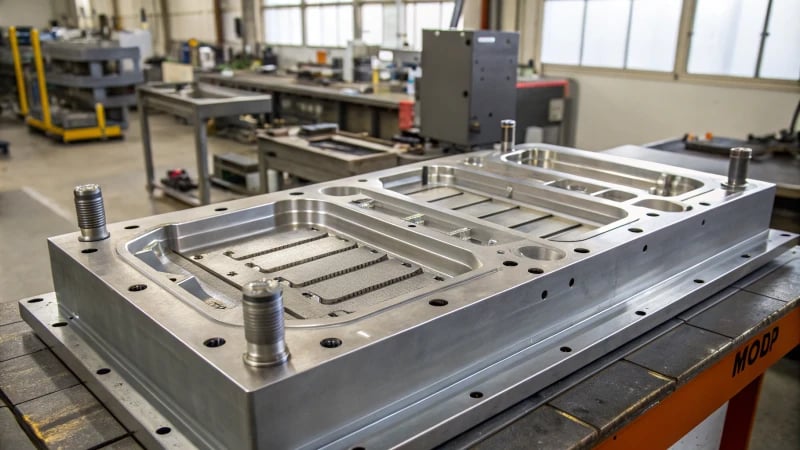
What Is the Best Gate Type for Optimizing Plastic Melt Fluidity?
Selecting the appropriate gate type in injection molding significantly influences the flow of molten plastic, impacting product quality and manufacturing efficiency. High viscosity plastics benefit from pin gates that increase shear heat, while low viscosity materials like polyethylene are better ...
OPTIMIZATION
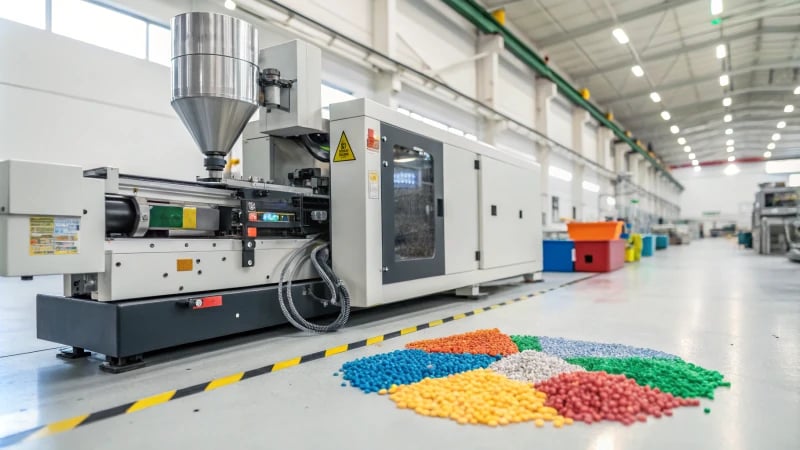
What Are the Best Methods to Improve Plastic Melt Fluidity at the Gate?
This article explores effective methods to improve plastic melt fluidity during injection molding. Key strategies include optimizing gate design, controlling molding parameters such as temperature and pressure, selecting suitable high-fluidity materials like polyethylene and polypropylene, and incorporating additives such as ...
OPTIMIZATION
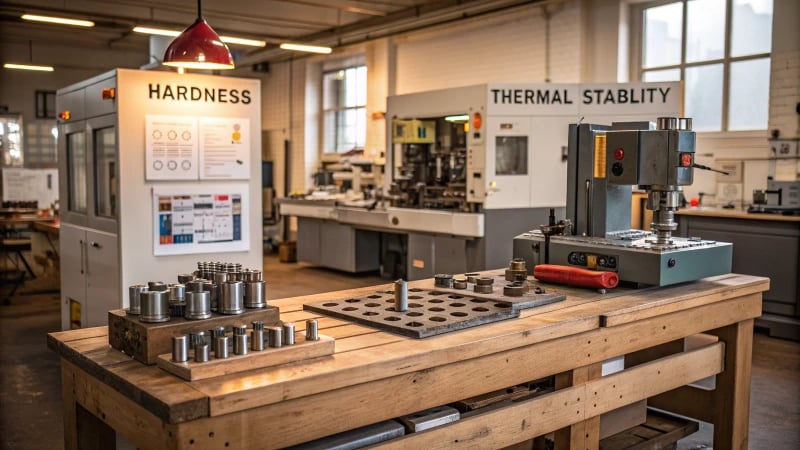
How Can You Choose the Right Processing Technology for Different Mold Material Characteristics?
Selecting appropriate processing technology for various mold materials is crucial for achieving optimal results. Factors such as material hardness, toughness, ductility, and thermal stability significantly influence tool selection and processing methods. High-hardness materials like H13 require carbide tools for effective ...
OPTIMIZATION
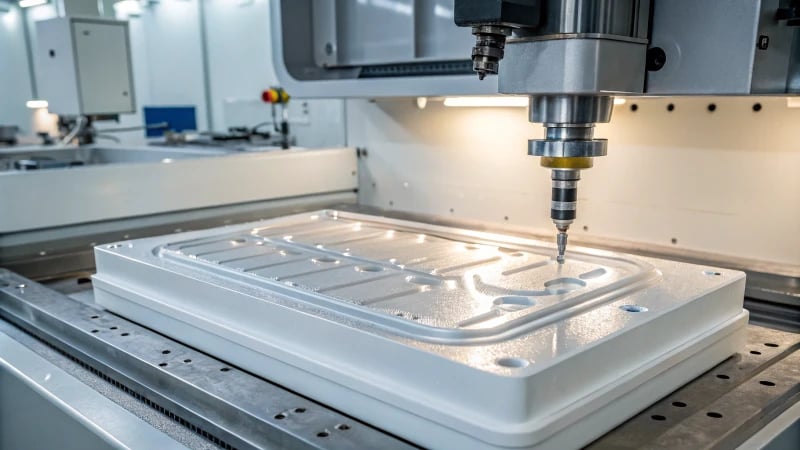
How Does Mold Processing Technology Affect Mold Service Life?
This article explores how mold processing technology affects the service life of molds. Key factors include dimensional accuracy, surface quality, and processing sequence. High precision in mold design ensures uniformity, reducing wear and preventing defects. Techniques like Electrodischarge Machining (EDM) ...
OPTIMIZATION
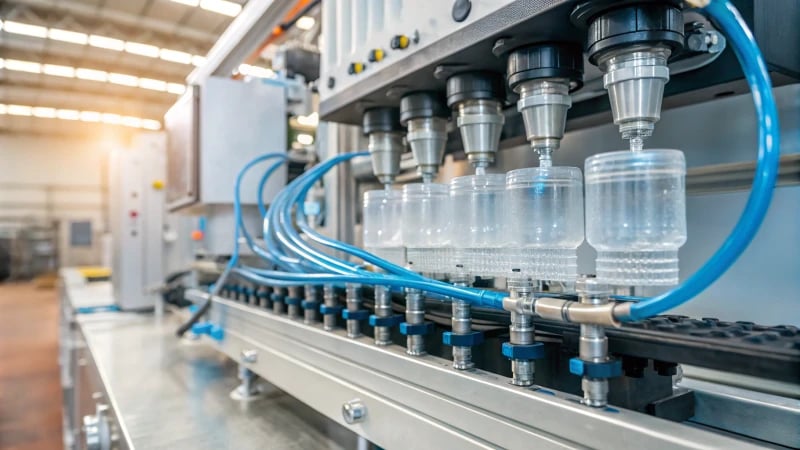
What Are the Best Practices for Optimizing Your Injection Molding Machine’s Cooling System?
This article explores best practices for optimizing the cooling system of injection molding machines. Key strategies include designing efficient water channels tailored to mold shapes, selecting appropriate coolants based on thermal properties, and implementing regular maintenance routines to ensure optimal ...
OPTIMIZATION
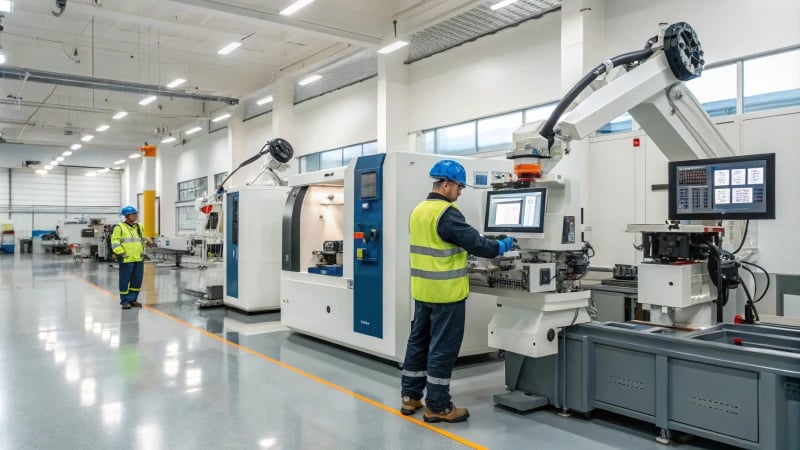
What Is the Optimal Injection Pressure Setting Range for Injection Molding Machines?
This article explores the optimal injection pressure settings for various materials in injection molding. It highlights that common plastics like polyethylene require lower pressures (40-100 MPa), while engineering plastics such as polycarbonate need higher pressures (80-160 MPa). The complexity of ...
OPTIMIZATION
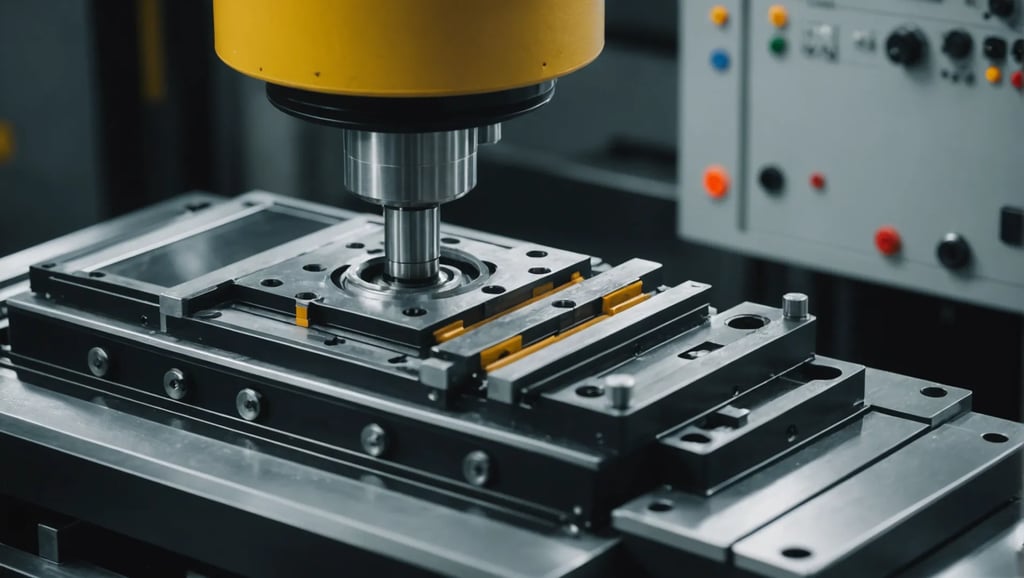
What Are the Most Effective Methods to Solve Shrinkage in Injection Molded Products?
Shrinking in injection molded products is a common challenge, but it doesn't have to be a persistent problem. By understanding the impact of material selection, mold design, and process adjustments, you can significantly enhance product quality. This guide explores effective ...
OPTIMIZATION
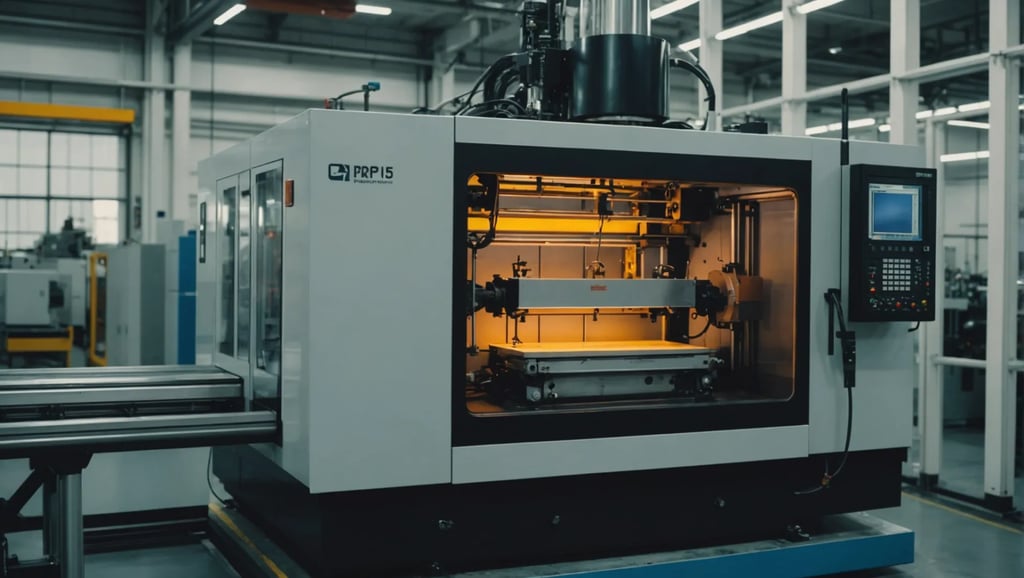
What Are the Best Techniques to Improve Dimensional Stability in Injection Molding?
Struggling with inconsistent part sizes in your injection molding process? You're not alone. This guide outlines essential techniques to enhance dimensional stability, including raw material selection, mold design, and process parameter optimization. Let's explore effective strategies that can lead to ...
OPTIMIZATION
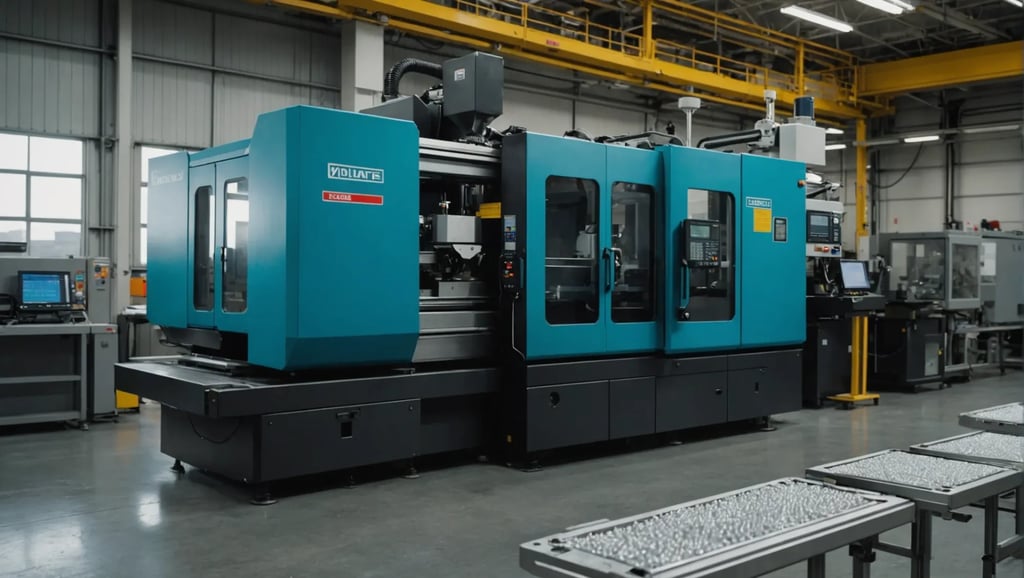
What Causes Incomplete Filling in Injection Molding and How Can You Adjust Parameters?
Injection molding is a precise manufacturing process, yet even the most controlled operations can encounter defects like incomplete filling. Known as 'short shots', this issue can compromise product integrity. This article explores the causes of incomplete filling and offers practical ...
OPTIMIZATION
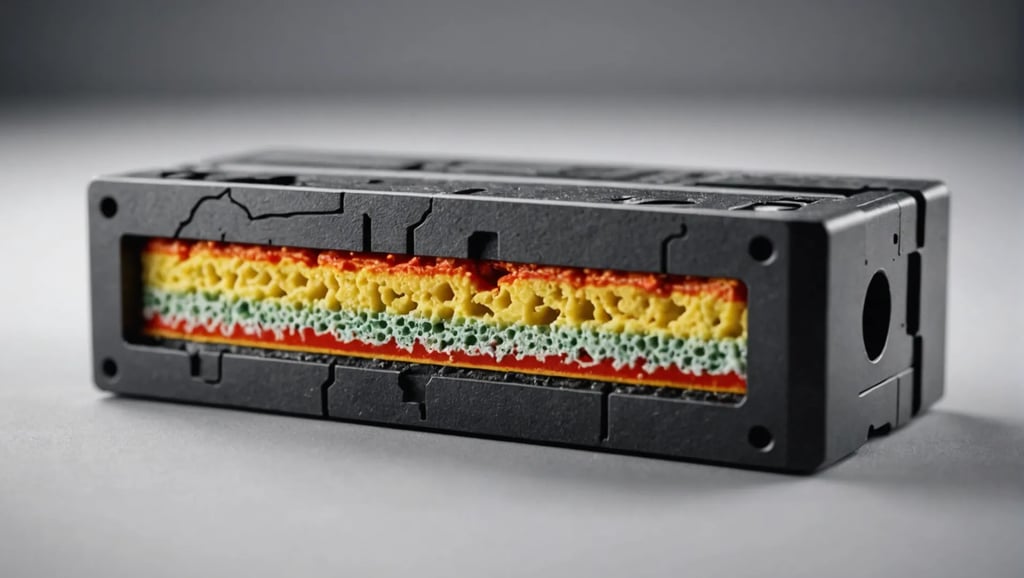
What Causes Uneven Wall Thickness in Injection Molded Products and How Can It Be Optimized?
Injection molding is a complex process, and achieving uniform wall thickness is crucial for product quality and performance. This article explores the various factors contributing to uneven wall thickness, including mold design, injection pressure, and material selection. By understanding these ...
OPTIMIZATION
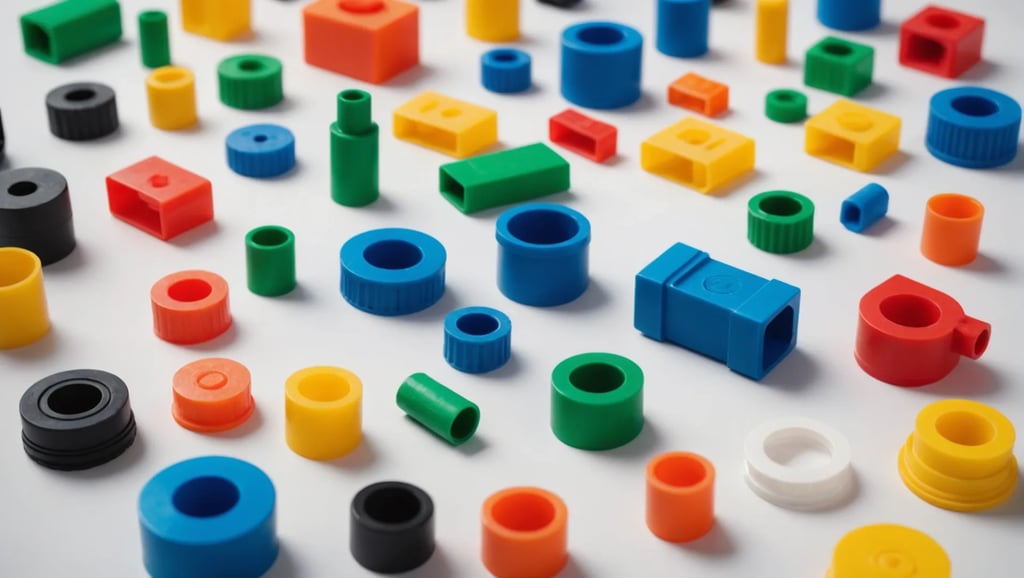
What Causes Color Variations in Injection Molded Parts?
Color consistency is crucial for the aesthetics and functionality of injection molded parts, yet achieving it can be challenging. In this post, I explore the various factors contributing to color variations in injection molding, including raw material quality, process parameters, ...
OPTIMIZATION
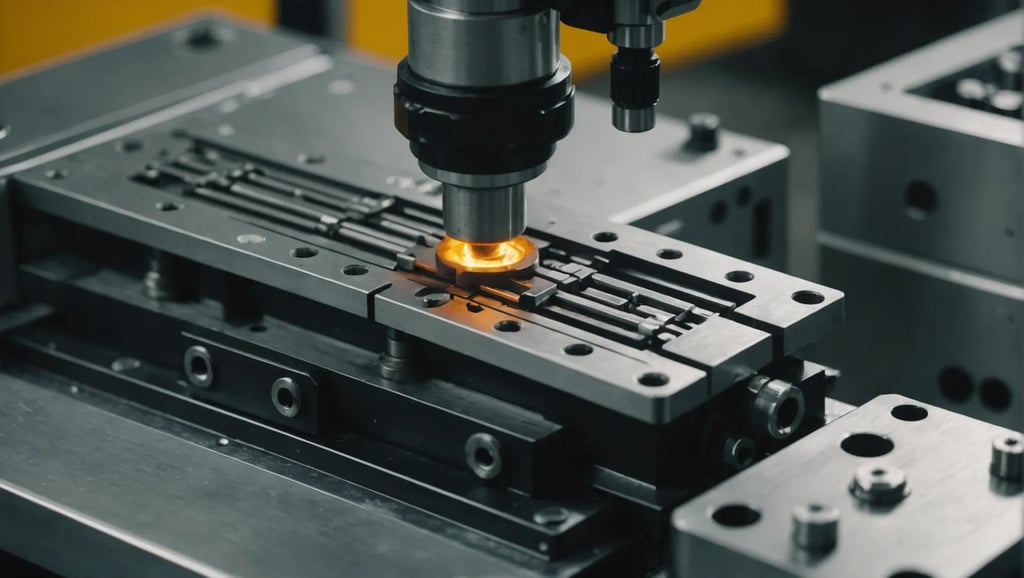
What Are the Causes and Solutions for Unsmooth Demoulding in Injection Molding?
Injection molding is a cornerstone of modern manufacturing, but unsmooth demoulding can hamper productivity and increase defect rates. This article explores common causes and practical solutions to enhance your production efficiency.
OPTIMIZATION
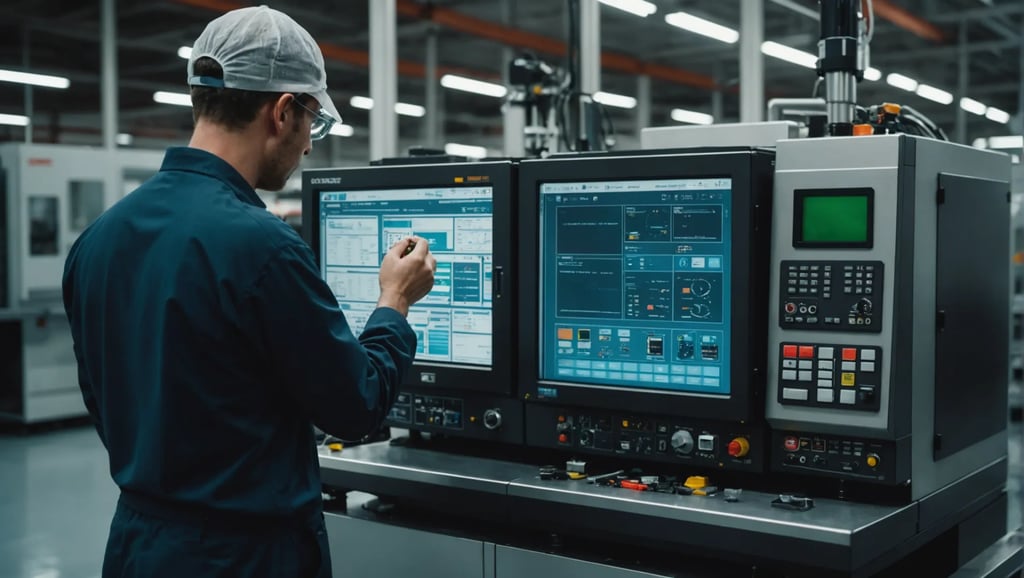
What Are the Best Strategies to Reduce Scrap Rate in Injection Molding?
Reducing scrap rates in injection molding is crucial for improving efficiency and cutting costs. This blog explores effective strategies including equipment maintenance, raw material management, process optimization, and staff training that can significantly enhance productivity while minimizing waste.
OPTIMIZATION
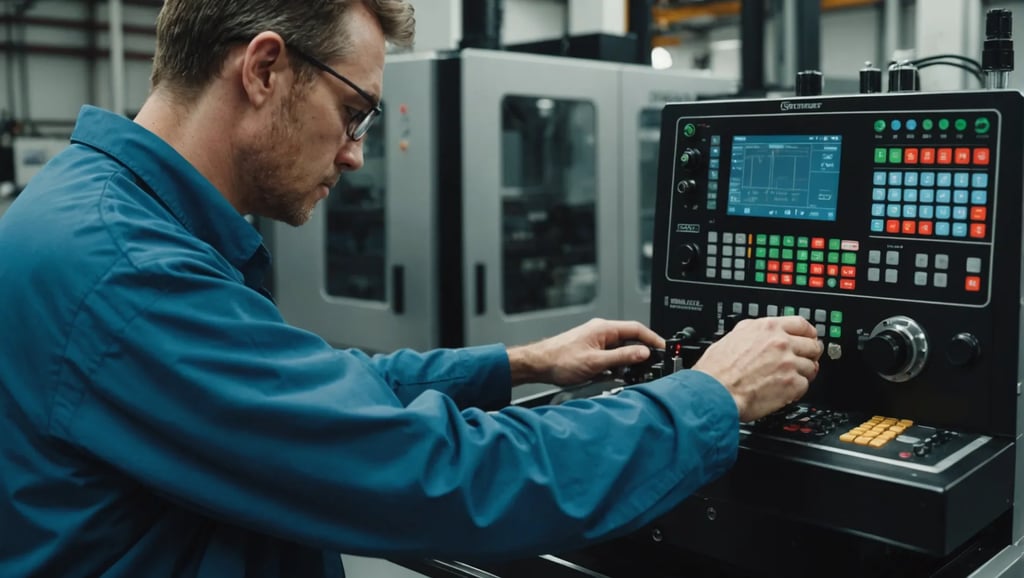
What Are Effective Solutions for Short Shot Issues in Injection Molding?
Short shot issues in injection molding can severely impact product quality and production efficiency. But what exactly causes these defects, and how can they be effectively resolved? In this article, we will explore the causes of short shots and provide ...
OPTIMIZATION