Remember that feeling when everything fits perfectly? That’s the magic we seek with injection molding.
I first look at the material’s melt flow index and rheological curve to find the best injection pressure for an injection molding machine. Then I study the product design needs, like wall thickness and complexity. I review mold design factors, such as gate and runner systems. I also try different mold settings several times, adjusting them based on the quality of the product.
When I first played around with injection molding, I thought setting the right pressure was just about entering numbers. But then I realized it’s much like brewing a perfect cup of coffee. You need to balance the grind, water heat and brew time. Finding the right pressure mixes science with a bit of gut feeling.
Understanding the melt flow index (MFI) of the material is very important. I learned this when a batch of polyethylene needed much less pressure because of its high MFI. I also faced a project where the product design was tricky. A thin-walled part demanded higher pressure to avoid flaws. These experiences show how vital it is to analyze product design. Mold specifications matter too. Mold trials help tweak settings.
Every trial teaches something new. I have adjusted pressure by only 5-10MPa and watched how small changes really affect quality. It’s like adjusting a recipe to taste. With each try, I get closer to the moment when everything feels just right.
Optimal injection pressure is determined by melt flow index.True
The melt flow index helps assess the material's behavior under pressure.
Wall thickness has no impact on injection pressure.False
Wall thickness affects how pressure is distributed during molding.
- 1. How Does Material Performance Testing Influence Injection Pressure?
- 2. How Do Product Design Aspects Influence Injection Pressure Requirements?
- 3. Why Is Mold Design Critical in Setting Injection Pressure?
- 4. How do you conduct effective mold trials for pressure optimization?
- 5. What Are the Common Challenges in Adjusting Injection Pressure?
- 6. Conclusion
How Does Material Performance Testing Influence Injection Pressure?
Do you ever think about how material flow influences the required pressure in manufacturing? It’s crucial for both efficiency and quality. This understanding changes everything.
Testing material performance, such as checking the melt flow index (MFI) and studying rheological curves, affects injection pressure by showing how fluid and thick a material is. These tests really show if a material flows easily. They also reveal how thick it gets. This information helps set the right pressure for the best product quality. It also improves how efficiently products are made.
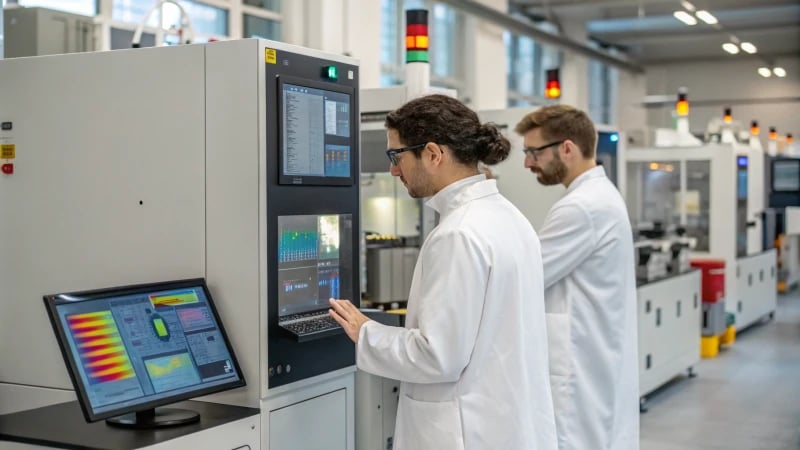
Material Performance Testing Methods
When I began learning about testing materials, I felt like I was solving a puzzle, trying to find the right balance between pressure and flow of materials. Tests such as the Melt Flow Index (MFI)1 and rheological analysis help us find clues to get that balance right.
1. Melt Flow Index (MFI) Measurement
The first time I watched an MFI test, it was like seeing a new language being broken down. The Melt Flow Index shows how easily a melted polymer flows. Higher MFI numbers mean easier flow, leading to lower pressures needed for injection. For instance, with a high MFI, polyethylene needed only 30-80 MPa for good flow.
Material | MFI Range | Injection Pressure Range |
---|---|---|
Polyethylene | High | 30-80 MPa |
2. Rheological Curve Study
Rheological analysis opened my eyes to how shear rates alter material thickness. With a rheometer, we observe how viscosity drops as shear rates rise, which affects the pressure required for injection.
Product Design Necessity Examination
1. Product Dimensions and Form
- Thicker Walls: These need less pressure because they face less resistance (40-80 MPa).
- Thin-Walled Structures: Such structures need more pressure (80-140 MPa) because they harden quickly, adding resistance.
2. Detailed Shapes and Quality Demands
For a complex design I once worked on, precise pressure tuning was needed to prevent flaws. This experience taught me the importance of adjusting pressures for superior surface quality and internal strength.
Mold Design Assessment
Mold design adds another layer to this interesting puzzle, where gate design and runner systems are key.
1. Gate Design Influence
I observed that direct gates reduce required pressure by allowing the melt to flow straight in. On the other hand, pin-point or side gates require more pressure due to their complicated paths.
Gate Type | Pressure Requirement |
---|---|
Direct Gate | Lower |
Side Gate | Higher |
2. Runner System Planning
Short and smooth runners lower resistance, thus reducing pressure. Hot runners are notably effective, keeping melt temperature stable better than cold ones, which can lower needed pressure by up to 30 MPa.
Mold Trial and Improvement Adjustment
Trial and error have always been fulfilling for me – seeing initial guesses become precisely tuned changes.
In early trials, pressures are set based on experience, like 60-100 MPa and adjusted as necessary. It’s somewhat like cooking; you begin with a recipe but adjust flavors to suit. If there’s underfilling, I increase the pressure by 5-10 MPa until perfect.
This gradual method not only suits product needs but also probably increases efficiency and quality—really worthwhile!
Higher MFI materials require lower injection pressure.True
Higher Melt Flow Index indicates better fluidity, reducing needed pressure.
Complex mold designs always use direct gates.False
Complex molds often use side gates for intricate paths, needing higher pressure.
How Do Product Design Aspects Influence Injection Pressure Requirements?
Have you ever thought about how small changes in product design really change the pressure needed for injection?
Material melt flow, product size and mold shape play important roles in affecting injection pressure. Testing how materials perform and examining product needs help find the best pressure settings.
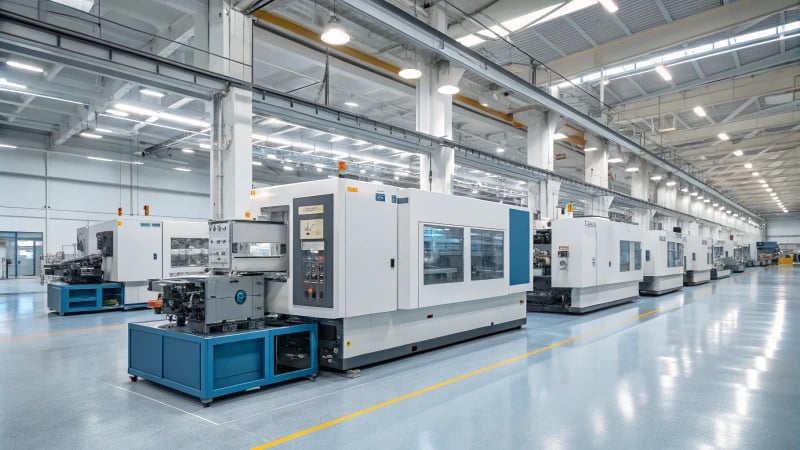
When I first entered the world of injection molding, it felt like stepping into a complex dance of science and art. Every small design detail changes the whole process. This was really fascinating but also overwhelming.
Material Performance Testing
Material characteristics significantly impact the injection pressure2 required. Melt flow index (MFI), for instance, is crucial: higher MFI implies better fluidity, reducing pressure needs.
-
Example Table: MFI vs. Injection Pressure
Material MFI Value Pressure Range (MPa) Polyethylene High 30-80 Polycarbonate Low 80-130
Drawing rheological curves felt like breaking a secret code. These curves showed viscosity changes, helping adjust pressures correctly.
Product Design Requirements Analysis
The size and shape of a product dictate the required pressure3. Thick walls reduce resistance, allowing lower pressures, while thin-walled or complex designs need higher pressures for effective filling.
- Wall Thickness vs. Pressure
- Thick (>5mm): 40-80 MPa
- Thin (<3mm): 80-140 MPa
For products with high appearance standards, gradual pressure adjustments ensure quality without defects.
Mold Design Evaluation
The mold’s gate and runner systems greatly influence pressure needs. A direct gate requires less pressure than more complex designs.
-
Gate Design Impact Table
Gate Type Pressure Impact Direct Lower Pin-point Higher
Larger gates and optimized runners act like floodgates; they decrease resistance and maintain melt temperature, reducing required pressures.
Mold Trial and Optimization Adjustment
The initial mold trial is always exciting; it is like the first brushstroke on a canvas, setting the stage for a masterpiece. Observations guide further adjustments to meet both external and internal quality standards. Each trial helps refine the pressure setting closer to the optimal level through iterative adjustments.
By evaluating these factors through trials, designers can systematically approach optimal injection pressures for any given design scenario. This methodical approach not only enhances product quality but also optimizes manufacturing efficiency. Analyzing each aspect of the design and mold process allows for precise control over injection conditions.
Higher MFI materials require lower injection pressures.True
Higher Melt Flow Index (MFI) indicates better fluidity, reducing pressure.
Thicker walls in products increase injection pressure needs.False
Thicker walls reduce resistance, allowing lower injection pressures.
Why Is Mold Design Critical in Setting Injection Pressure?
Have you ever wondered how mold design truly impacts your injection molding process? Mold design resembles a secret ingredient that determines the smoothness of the entire operation.
Mold design plays a vital role in shaping the flow path of molten material. This design decides the resistance the material meets, thus influencing the pressure required. Proper pressure is crucial to fill mold cavities well. Good mold design directly impacts product quality. High-quality products are the result of efficient mold design.
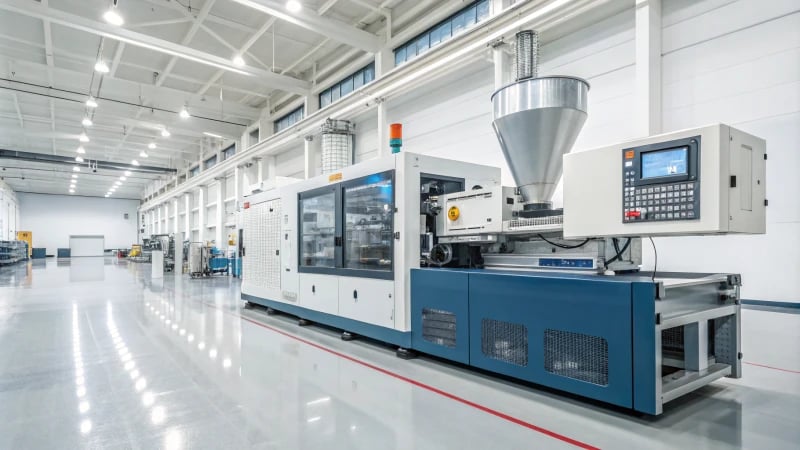
Material Performance Testing
At the start, I learned about the melt flow index (MFI)4 of materials. You can’t skip it. Think about squeezing ketchup from a bottle at a barbecue. Some materials act like old glass bottles – hard to squeeze because of low MFI, like polycarbonate. Others, such as polyethylene, flow out easily with high MFI, needing less effort.
Material | MFI | Pressure (MPa) |
---|---|---|
PE | High | 30-80 |
PC | Low | 80-130 |
Product Design Requirements Analysis
One of my first tasks involved a sleek gadget with thin walls. It looked cool but was tough to mold. It cooled fast and resisted filling. High pressure was necessary to fill every part. Picture filling an ice cube tray with thick syrup instead of water.
The product’s size and shape determine the necessary injection pressure. Thicker walls have less flow resistance, while thin-walled products need higher pressure due to rapid cooling and increased resistance.
For intricate designs, ensuring melt reaches every corner requires even more pressure. This step is critical for maintaining high product quality standards5.
Mold Design Evaluation
Gate and runner systems are crucial in mold design. On a project once, changing the gate size mattered a lot. Increasing the gate from 1mm to 2mm lowered the pressure needed. It felt like opening wide gates and watching everything fit perfectly.
The gate and runner system designs are crucial. Direct gates reduce pressure needs, whereas more complex gates like pin-point or side gates increase it. Short, thick runners with smooth surfaces lower resistance, aiding in pressure reduction.
For instance, modifying gate size6 can significantly change pressure requirements:
- Gate Diameter: Going from 1mm to 2mm can lower pressure by 10-20 MPa.
Mold Trial and Optimization Adjustment
First trials remind me of science experiments in school. You tweak until it clicks. Begin in a range, maybe 60-100 MPa and watch. If defects like flash or internal stress appear, adjust by 5-10 MPa.
Initial trials set an estimated pressure range, usually between 60-100 MPa. Observations during trials help fine-tune this setting to ensure optimal mold filling7 and product quality.
During trials, adjustments of 5-10 MPa are typical based on observed defects like flash or internal stress.
This iterative process ensures accurate settings for subsequent production batches.
Repeated optimization records these settings, providing valuable data for future molds and enhancing overall production efficiency.
High MFI materials need more injection pressure.False
High MFI materials like PE require less pressure than low MFI materials.
Thin-walled products require higher injection pressure.True
Thin walls increase flow resistance and cooling, needing higher pressure.
How do you conduct effective mold trials for pressure optimization?
Have you ever felt excitement from getting mold trials just right? Follow my personal journey. I learned how to control pressure, where every little change matters. Product quality is the top goal. Product quality is very important.
Conducting good mold trials for pressure checks involves studying material qualities, product shapes and mold styles. Evaluating these parts helps adjust injection pressure. This leads to high production quality and really good efficiency.
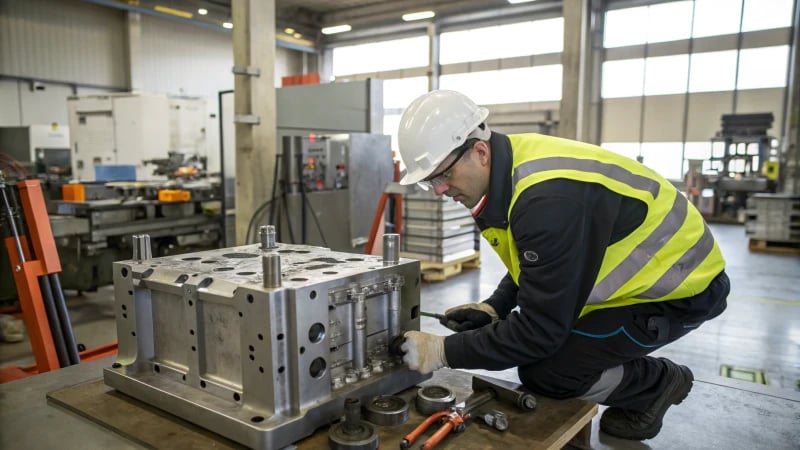
Material Performance Testing
I remember the first time I used a melt flow index (MFI) tester. It felt like I had found a secret way to understand how materials behave. When I check the MFI, I see how easily a material flows. This helps me set the right pressures for injection.
For example:
Material | MFI Range | Injection Pressure (MPa) |
---|---|---|
Polyethylene | High | 30-80 |
Using a rheometer is equally eye-opening. It shows how viscosity changes at different speeds, serving as a roadmap to guide me in choosing the right injection pressures so the product turns out just right.
Product Design Requirements
Product design blends creativity and engineering. Looking at the size and shape is like sculpting; every curve and thickness affects flow.
Consider:
- Thick walls (>5mm): Work well with lower pressures, e.g., 40-80 MPa.
- Thin walls (<3mm): Demand more pressure, needing 80-140 MPa to fill every part.
I once handled a complex shape with detailed features that needed precise pressure tweaks to prevent defects. Each try taught me something new, increasing pressures by 5-10 MPa until the product was perfect without flaws.
Mold Design Evaluation
Evaluating gate design is like playing chess; each decision affects managing pressure. Direct gates usually use less pressure, but pin-point or side gates require more to manage tricky paths.
Examine the runner system:
Runner Type | Description | Pressure Impact |
---|---|---|
Short/Thick | Less resistance, smooth surface | Lower pressure |
Hot Runner | Maintains temperature, reduces viscosity | Lower pressure by 10-30 MPa |
Mold Trial and Optimization Adjustment
Initial mold trials are always exciting. Based on earlier tests, I set an injection pressure range like 60-100 MPa and watch how well the mold fills—it’s like baking; too little pressure and it doesn’t work; too much and it fails.
Watching how the product fills helps me adjust. Small changes are vital: if I see problems like flash, I lower the pressure; if there’s a lack of filling, I increase it by 5-10 MPa until the product meets all quality standards and looks great.
Keeping records of these details is useful for future projects. It lets new challenges be met with experience-supported confidence.
For further insights on material performance testing, explore material rheological curve drawing8.
For design considerations, check product design requirements analysis9.
Higher MFI materials require lower injection pressures.True
Higher melt flow index (MFI) indicates better fluidity, reducing pressure.
Thicker walls in products need higher injection pressures.False
Thicker walls decrease flow resistance, requiring lower injection pressure.
What Are the Common Challenges in Adjusting Injection Pressure?
Adjusting injection pressure resembles walking on a tightrope. This step is very important for molding success, but it comes with many challenges.
Changing injection pressure brings challenges like different material qualities, detailed product designs and complicated mold shapes. Testing each part carefully helps find the best outcome. Small adjustments work best.
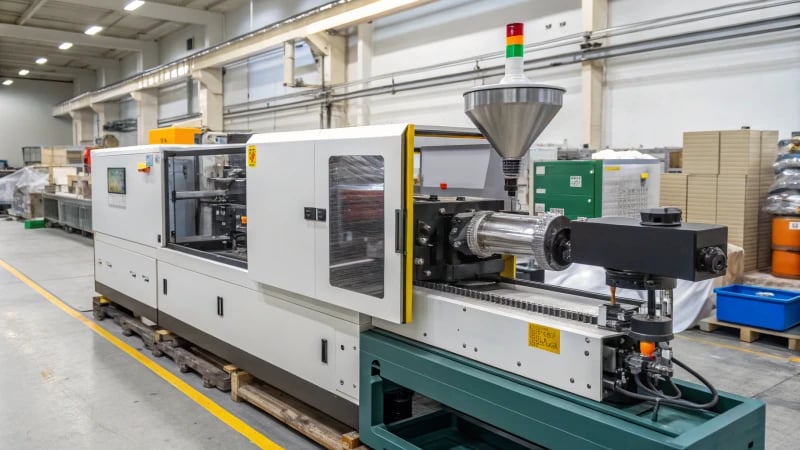
Material Characteristics and Their Impact
Each newly encountered material feels like meeting a new friend. They all have unique traits. Understanding these, especially the melt flow index (MFI), is my first move. It’s interesting how materials like polyethylene (PE) with high MFI need less injection pressure10. This makes them very fluid and easy to work with. In contrast, polycarbonate (PC) requires more pressure because of its low MFI. Pushing it through feels like getting thick syrup through a straw.
Material | Typical MFI | Injection Pressure (MPa) |
---|---|---|
PE | High | 30-80 |
PC | Low | 80-130 |
I recall my first project with PC. It felt tough, like wrestling with a bear. Then, I learned the importance of the rheological curve. By studying how viscosity shifts with shear rates, I guessed the needed pressure better. This understanding saved me from many trial-and-error attempts.
Product Design Challenges
Designing products is like solving a jigsaw puzzle. Each piece requires careful thought. A thick-walled design usually needs lower injection pressure, similar to pouring water through a wide pipe. Thin-walled items cool fast, needing higher pressures to fill completely.
- Thick wall (>5mm): 40-80 MPa
- Thin wall (<3mm): 80-140 MPa
In my early days, I learned that detailed shapes often required more pressure11. Getting the melt into every tiny space is key to keeping products strong.
Mold Design Considerations
Mold design is crucial. My favorite part is adjusting the gate and runner system designs. It’s like perfecting a musical instrument. Direct gates usually require less pressure because the flow faces less resistance compared to side gates.
I have seen larger gate sizes cut down needed pressure significantly—it’s like opening a dam for water to flow easily by reducing it by 10-20 MPa.
Hot runner systems really change the game as they keep the melt warm and cut pressure needs by 10-30 MPa.
Trial and Optimization
Starting mold trials feels like starting a brand-new adventure. I pick a pressure range—maybe between 60-100 MPa—and focus on observation and adjustment.
Small pressure tweaks often create big differences.
Every flaw during trials gives a hint: parts that aren’t filled enough might just need a bit more pressure; problems like flash suggest stepping back on pressure settings.
Constant testing and adjustments lead me to find the perfect balance for both appearance and quality.
Writing down these best settings is very useful for future tasks to ensure consistency12. Consistency matters—it really does.
Polyethylene requires higher injection pressure than polycarbonate.False
Polyethylene has a higher MFI and generally requires lower injection pressure.
Thin-walled products need higher injection pressure than thick-walled ones.True
Thin walls cool rapidly, increasing flow resistance, requiring higher pressure.
Conclusion
Determining optimal injection pressure involves analyzing material properties, product design, and mold specifications through testing methods like melt flow index and rheological curves for quality production.
-
Understanding MFI helps in determining the fluidity of polymers, guiding optimal injection pressure settings. ↩
-
Explore how the melt flow index influences material fluidity and necessary injection pressure. ↩
-
Learn how different product shapes alter resistance and impact the required injection pressure. ↩
-
Discover how MFI influences material selection and processing conditions in injection molding. ↩
-
Learn strategies to ensure your products meet rigorous quality standards. ↩
-
Explore the impact of gate size on the injection process efficiency. ↩
-
Understand the importance of proper mold filling for product integrity. ↩
-
Understand how to draw and interpret rheological curves for accurate injection pressure estimation. ↩
-
Learn how product design affects injection molding pressures and how to optimize for best results. ↩
-
Discover how MFI values influence material fluidity and required injection pressure, which is essential for efficient molding. ↩
-
Explore why intricate designs require specific injection pressures to ensure complete cavity filling. ↩
-
Learn about effective strategies for conducting mold trials to optimize product quality. ↩