Removing gates from injection molded parts involves more than one step in the process. It is about perfecting the final product. It also involves making sure it shines. My experiences might probably interest you.
To remove gates post-injection molding, use manual tools for small gates, mechanical methods for larger parts, chemical solvents like acetone for soft materials, and ultrasonic removal for precision. Choose based on gate size, part complexity, and material.
With many years in manufacturing, I’ve discovered that choosing the correct gate removal technique affects quality and efficiency. Manual removal with simple tools like knives works wonders for smaller gates and simpler designs. Larger and more complex structures often require mechanical methods. I remember using a milling machine once – it was like a mini-adventure! Chemical solvents such as acetone have saved me when handling delicate materials. Ultrasonic removal surprises me; high-frequency vibrations are like magic! Each method has its own time and place. Knowing when to use each one really impacts my work.
Manual removal is the most common technique for gate removal.True
Manual removal is widely used due to its simplicity and effectiveness, especially for small gates on uncomplicated parts.
Ultrasonic removal is effective for all gate sizes.False
Ultrasonic removal is not suitable for all gate sizes; it works best on smaller, more delicate gates due to its precision.
What Factors Should You Consider When Choosing a Gate Removal Method?
Picking the correct way to remove gates in injection molding feels really difficult, yet it doesn’t need to be. Key factors help you decide wisely. Understanding these factors makes everything very smooth for you.
When choosing a gate removal method, consider the material, gate size and complexity, structural design, efficiency needs, and cost implications to achieve optimal results.
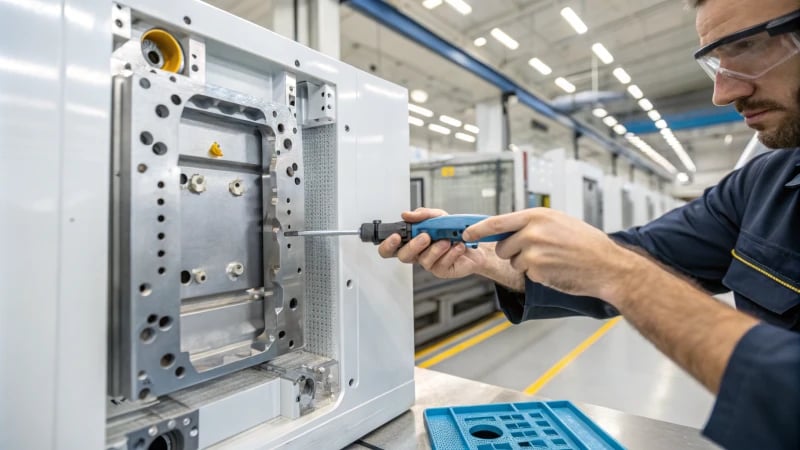
When it comes to selecting the right gate removal method, several crucial factors must be considered to ensure efficiency and quality in the final product. This decision-making process should take into account the following aspects:
Material of the Injection Molded Part
The type of material used in the injection molded part significantly influences the choice of gate removal method. For example:
- Thermoplastics: These are generally easier to work with and can often be removed manually or chemically.
- Thermosets: These may require mechanical or ultrasonic methods due to their rigidity.
Understanding the material properties can help you select a method that minimizes damage to the part while ensuring a clean removal. Learn more about material properties1.
Size and Complexity of the Gate
The size and complexity of the gate also play vital roles in determining the appropriate removal technique. Consider the following:
- Small Gates: Methods like manual, chemical, or ultrasonic removal are often effective and cost-efficient.
- Large Gates: Mechanical methods such as punching or milling may be necessary for larger gates to ensure precision and effectiveness.
Here’s a quick comparison:
Gate Size | Recommended Removal Method | Cost Estimate |
---|---|---|
Small | Manual / Chemical / Ultrasonic | Low – Moderate |
Large | Mechanical | Moderate – High |
Structural Considerations
The structural design of the molded part can dictate which method is most suitable. If the part has intricate designs or thin sections, careful consideration is needed:
- Intricate Designs: Ultrasonic or chemical removal can provide delicate handling.
- Thicker Structures: Mechanical methods might be necessary to provide sufficient force for gate removal without damaging the overall part.
Evaluate how the chosen method aligns with the design specifications to avoid any compromises in functionality.
Efficiency and Production Needs
Time and efficiency are paramount, especially in manufacturing environments. Assess how quickly each method can be executed:
- Manual Removal: Often slower, but can be applied in low-volume settings where precision is key.
- Mechanical Removal: Typically faster and better suited for high-volume production runs.
Understanding your production timeline will help determine which method balances speed and quality effectively.
Cost Implications
Finally, consider the cost associated with each removal method. This includes not just direct costs but also potential downtime and waste:
- Manual Methods: Generally lower in cost but may require more labor hours.
- Mechanical Methods: Higher initial investment but can reduce costs in mass production scenarios.
By analyzing these factors carefully, you can choose a gate removal method that aligns with both your technical requirements and your business objectives.
Thermoplastics allow for easier gate removal than thermosets.True
Thermoplastics can be removed manually or chemically, while thermosets require more complex methods due to their rigidity.
Mechanical methods are always the most cost-effective for gate removal.False
While mechanical methods can reduce costs in mass production, they involve higher initial investments compared to manual methods which are cheaper but slower.
How Does Gate Design Impact the Removal Process?
Ever thought about how a gate’s design affects the efficiency of the removal process in injection molding? Let’s explore this interesting topic together. Discover how it really impacts the process!
Gate design in injection molding influences the ease of part removal, with optimal gate size, shape, and material facilitating simpler detachment.
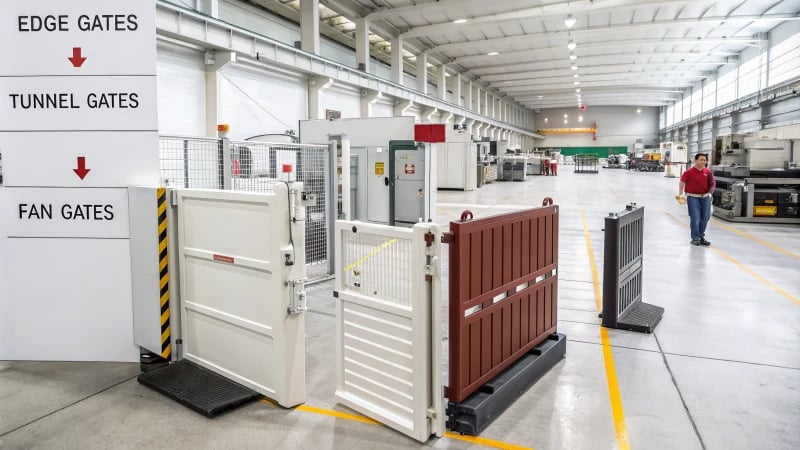
Understanding Gate Design
Gate design is more than just a technical detail. It really determines how smoothly things flow in the injection molding process. I clearly recall my first experience with gate design; it felt like solving a puzzle. The gate is where molten plastic enters the mold. Its design is the key to successful removal. Something small really makes a big difference!
There are various types of gates, including edge gates, pin gates, and submarine gates, each with its own story about removal. Edge gates might be popular for their easy access during removal but can leave marks that might need extra finishing work. Pin gates are tricky and require precision and care during extraction. It can be nerve-wracking but very rewarding when done right.
Methods of Gate Removal
After the molding process, it’s time to remove those gates. The method depends on the gate’s size and complexity:
Method | Description | Suitable For |
---|---|---|
Manual Removal | Uses tools like knives or scissors to cut the gate. | Small gates and simple structures |
Mechanical Removal | Employs machines such as punching or milling machines. | Large gates and complex structures |
Chemical Removal | Utilizes solvents like acetone to dissolve the gate. | Small gates and simple structures |
Ultrasonic Removal | Applies high-frequency ultrasound vibrations to separate the gate. | Small gates and simple structures |
Each method has its own efficiency, quality, and cost implications which should be evaluated based on specific project requirements.
Factors Influencing Gate Design
When selecting a gate design, I consider key factors:
- Material: Materials behave differently during molding, affecting removal directly.
- Structure: The molded part’s complexity shapes my choice of removal methods.
- Size: Larger gates lead me to choose more robust mechanical or chemical methods.
These factors help me adjust my gate designs for function and easy removal. It’s about finding a sweet spot where everything aligns nicely! For those interested in learning about material selection in injection molding, check out material considerations2.
Conclusion Avoidance
Gate design is not just a functional detail; it plays a big role in post-processing efficiency. By studying how different designs affect removal methods, I improve production workflows and reduce defects. If curious about defect prevention in injection molding, explore defect management3. Let’s unlock the secrets of effective gate design and improve our injection molding processes together!
Gate design influences removal efficiency in injection molding.True
The design of the gate directly affects how easily gates can be removed after molding, impacting overall efficiency.
Chemical removal is suitable for large gates in injection molding.False
Chemical removal methods are typically used for small gates, not large ones due to their robustness.
What Are the Pros and Cons of Each Gate Removal Technique?
When I started learning about injection molding, I soon understood that picking the right way to remove gates is not only a technical choice. It’s also an emotional experience. Every method has a unique character. Each has its own strengths and flaws that affect our product quality. This decision is crucial.
Gate removal techniques in injection molding—manual, mechanical, chemical, and ultrasonic—each have pros and cons affecting cost, efficiency, and product strength. Choosing the right method depends on specific production needs to achieve optimal product quality.
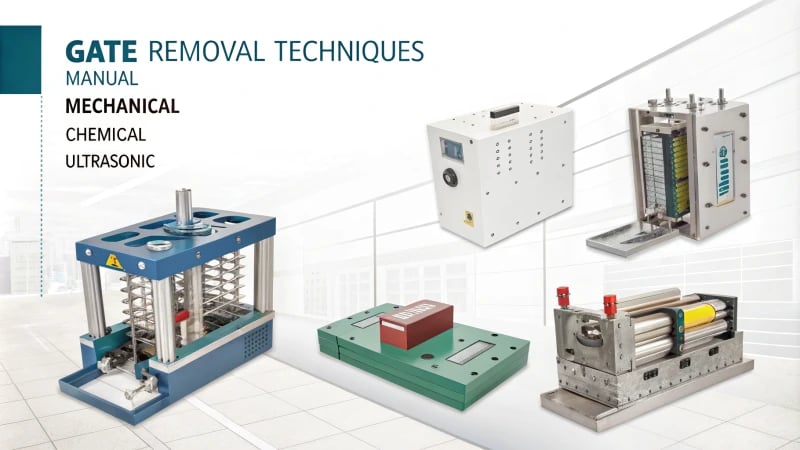
Manual Removal
My first time using manual removal felt memorable. I had only scissors and a steady hand to cut the gate from a small molded part. It was like delicate surgery.
Pros:
- Affordable: No need for expensive equipment. This method is great for small businesses like mine.
- Precision: I love having full control. It’s like being an artist shaping my creation.
Cons:
- Tiring: This method can get exhausting. My hands were sore after long sessions.
- Safety risks: Cutting has risks – accidental cuts are possible if not careful.
Mechanical Removal
Later, I switched to mechanical removal. The punching machine was loud and scary at first. But it quickly became my helper for bigger parts.
Pros:
- Fast: Efficiency changed my workflow. Large volumes were processed quickly with good quality.
- Uniformity: Consistent results were a relief; manual methods struggled with this.
Cons:
- Expensive start: Buying machinery was scary. My budget was very tight.
- Complex setups: Adjustments were often needed for different designs, which was annoying.
Chemical Removal
I felt unsure about chemical removal. Using acetone to dissolve a gate was both interesting and worrying because of the fumes.
Pros:
- Gentle: It preserved intricate designs with no damage.
- Precise for details: For delicate structures where machines might harm, chemicals were very helpful.
Cons:
- Compatibility issues: Not all materials work with chemicals; it felt risky each time.
- Environmental concerns: Safety and disposal of chemicals worried me – important for our industry.
Ultrasonic Removal
Discovering ultrasonic removal was exciting. High-frequency vibrations made separating gates easy.
Pros:
- Accurate: Reduces risk of damaging parts during removal.
- Fast: Processing delicate tasks quickly increased my productivity.
Cons:
- Costly equipment: Special machinery is expensive, a constant worry.
- Limited use: Not suitable for large gates or complex designs; felt limiting sometimes.
Comparative Summary Table
Technique | Pros | Cons |
---|---|---|
Manual Removal | Affordable, Precision | Tiring, Safety risks |
Mechanical Removal | Fast, Uniformity | Expensive start, Complex setups |
Chemical Removal | Gentle, Precise for details | Compatibility issues, Environmental concerns |
Ultrasonic Removal | Accurate, Fast | Costly equipment, Limited use |
Choosing the right gate removal method feels like navigating many options. It’s important to consider factors like material type, part structure, size, efficiency, quality and cost. Each choice impacts our projects. Knowing these pros and cons helps achieve optimal decisions for design goals. For further insights on this topic, check out gate removal techniques4.
Manual removal is the most cost-effective technique.True
Manual removal requires minimal investment in tools, making it the cheapest option for gate removal.
Ultrasonic removal is suitable for large gates.False
Ultrasonic removal is not effective for larger gates, as it works best on smaller, simpler designs.
How Can I Optimize Injection Molding Designs to Minimize Gate Issues?
Have you ever experienced frustration from problems with gates during injection molding? These issues are like obstacles in your design process. Let’s explore some smart strategies to improve gate performance and increase your manufacturing success.
Optimize injection molding designs by selecting the right gate position, size, and type. Use simulation software for design testing to minimize gate issues and enhance success.
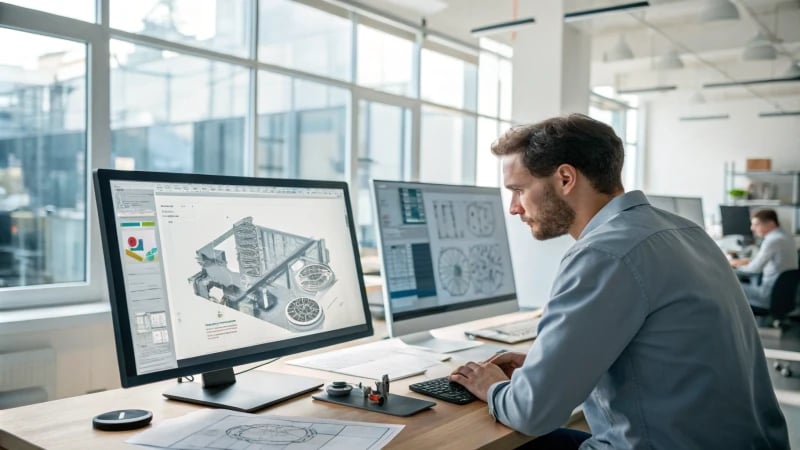
Understanding Gate Issues in Injection Molding
Gate issues can arise during the injection molding process, affecting the quality and functionality of the final product. These problems often stem from poor gate design or placement, leading to issues such as:
- Uneven material flow
- Incomplete mold filling
- Surface defects
To effectively address these challenges, designers need to consider optimizing the gate design during the initial stages of the injection molding process. By doing so, it helps in achieving a more uniform material flow and minimizes defects.
Strategies for Optimizing Gate Design
-
Gate Location and Size:
The position and size of the gate play a crucial role in material flow and mold filling.- Positioning: Gates should be located where they can facilitate even flow throughout the mold. Think of it like planning a path for water; it needs clear routes to move freely.
- Sizing: A larger gate can improve material flow but may increase the risk of sink marks. Adjusting the gate size can mitigate these issues. Finding the right gate size is essential.
-
Gate Type Selection:
Different types of gates can be employed depending on the product requirements:
Gate Type | Advantages | Disadvantages |
---|---|---|
Edge Gate | Easy to machine, cost-effective | Can leave marks on the part |
Tunnel Gate | Reduces visible gate marks | More complex to design |
Submarine Gate | Minimal impact on aesthetics | May require more engineering |
Choosing the right gate type is essential for balancing aesthetics with functional performance.
- Simulation and Testing:
Utilizing simulation software can provide insights into how different designs will behave before actual production. Here are some strategies I use:- Flow Analysis: Running simulations can help visualize flow patterns and identify potential problem areas in gate design. Learn more about flow analysis5.
- Prototype Testing: Building prototypes allows for real-world testing to assess how design changes affect performance.
Methods for Gate Removal Post-Molding
Once the molding process is complete, it’s essential to consider how to efficiently remove the gate from the molded part. Here are some common methods:
- Manual Removal: Suitable for small gates; involves tools like knives and scissors—simple but effective.
- Mechanical Removal: Ideal for large gates; uses machines like milling machines.
- Chemical Removal: Utilizes solvents like acetone for small gates on simple structures.
- Ultrasonic Removal: Employs high-frequency vibrations for effective separation.
When choosing a removal method, factors such as material type, structural complexity, and cost efficiency should be assessed for optimal results.
Optimizing gate design improves material flow in injection molding.True
Effective gate design enhances the uniformity of material flow, reducing defects in molded products.
Larger gates always eliminate all gate issues in molding processes.False
While larger gates can improve flow, they may also introduce new issues like sink marks.
Conclusion
Explore effective techniques for removing gates after injection molding, including manual, mechanical, chemical, and ultrasonic methods tailored to part complexity and material.
-
This link offers valuable insights on how material choices affect manufacturing processes, enhancing your understanding of gate removal methods. ↩
-
Clicking this link provides comprehensive guidelines on gate design choices that enhance the removal process efficiency. ↩
-
This link offers valuable insights into defect management strategies that can improve product quality post-removal. ↩
-
Discover detailed insights on each technique’s benefits and limitations to make an informed decision for your manufacturing process. ↩
-
Discover practical insights on optimizing gate designs to enhance product quality and reduce defects. ↩