Have you ever thought about how injection molding speed affects the strength of plastic products?
Reduce injection speed’s bad effects on plastic’s pulling strength by fine-tuning speed settings. Change mold design. Use correct material steps before and after treatment. These actions give better results. These steps keep production efficient.
I spent many hours in front of a CAD screen, changing designs for plastic parts that need to look good and stay strong. It’s a careful process. Injection speed plays a really big role in keeping everything balanced. Precisely controlling it with multiple stages helps even difficult shapes fill smoothly without stress.
Speed isn’t the only focus. Mold structures, like exhaust designs and gate sizes, need adjustments to avoid issues like internal stress or holes. Drying materials first is very important – nylon, for example, needs some time in the oven to stop bubbles from forming.
One time, I watched a design fall apart because I ignored these small things. It taught me a crucial lesson. Proper post-processing, like annealing, really matters for maintaining strength. These strategies are essential for my work in delivering strong and reliable products.
Optimizing injection speed improves tensile strength.True
Adjusting injection speed parameters ensures better material bonding.
Ignoring mold structure has no effect on tensile strength.False
Proper mold design is crucial for maintaining tensile strength.
What Are the Key Factors Affecting Injection Speed?
Ever thought about what drives injection molding? It relies on quickness and accuracy.
Key factors impacting injection speed include material properties, mold design and certain process details. Understanding these aspects greatly improves product quality and reduces flaws. Really, product quality depends on this mastery.
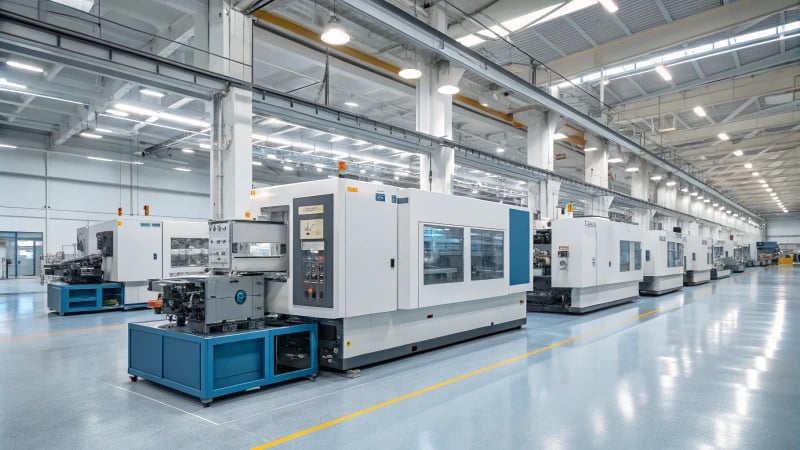
Material Properties
Different plastics have varying fluidity, which directly influences injection speed. For instance, materials like polyethylene (PE) with good flow properties can handle higher speeds, typically between 100-200mm/s. In contrast, polycarbonate (PC) with lower fluidity requires moderate speeds ranging from 50-100mm/s.
- Material Drying Treatment: Some plastics are hygroscopic, like nylon (PA), requiring pre-drying to prevent moisture-induced defects during molding. Proper drying (e.g., at 80-100℃ for 4-8 hours) ensures better melt flow characteristics1.
Mold Design Considerations
The design of the mold significantly impacts injection speed. A well-designed mold with proper exhaust systems and gate sizing reduces resistance and enables efficient filling.
Mold Feature | Impact on Injection Speed |
---|---|
Exhaust Design | Improves gas evacuation, reducing defects. |
Gate Size | Larger gates handle higher speeds without jetting issues. |
- Optimize Gate and Runner Design: A well-planned runner system with smooth surfaces minimizes flow resistance, ensuring that even lower speeds can fill the cavity efficiently.
Process Parameters
Adjusting process parameters like holding pressure and multi-stage injection speeds helps manage injection speed more effectively.
-
Multi-Stage Injection: This technique employs different speeds at various stages of cavity filling. For example, starting at 30-50mm/s allows smooth entry, then increasing to 80mm/s mid-filling, and finally slowing down to 30mm/s towards completion reduces residual stress.
-
Holding Pressure Settings: Adequate holding pressure compensates for shrinkage and minimizes underfilling risks, crucial for maintaining tensile strength when adjusting injection speeds2.
Product Post-Processing
Post-treatment like annealing can alleviate residual stresses caused by inappropriate injection speeds. For example, heating PC products to 120-140℃ for 30-60 minutes can improve tensile strength by relaxing internal stresses. More insights into post-processing techniques3 offer further optimization strategies.
These factors underscore the intricate balance required in controlling injection speed for optimal production quality.
Polycarbonate requires higher injection speeds than polyethylene.False
Polycarbonate needs moderate speeds due to lower fluidity.
Larger gate sizes can handle higher injection speeds.True
Larger gates reduce jetting issues, allowing higher speeds.
How Can I Optimize Multi-Stage Injection Speed Settings?
Did you ever think about how controlling different stages of injection speed might change your molding process? Let me guide you through it!
To set the best speeds for different stages of injection, I begin by changing speeds according to how the plastic flows. Lower speeds at the start help stop problems. Speeds go up during filling. Speeds drop near the end to handle stress. Stress control is very important.
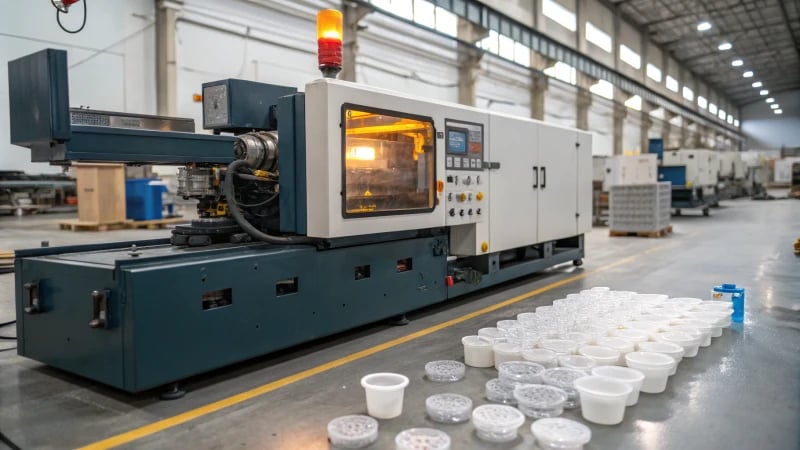
Understanding Injection Speed Parameters
I remember discovering how vital injection speed is – it was like finding a key ingredient in grandma’s famous dish. The difference in molded product quality is unbelievable. Controlling injection speed4 based on the specific plastic material and product needs is essential. Materials like polyethylene (PE) do well with faster speeds (100-200mm/s). Very fast. In contrast, polycarbonate (PC), with moderate fluidity, usually needs speeds of around 50-100mm/s.
Utilizing Multi-Stage Injection
Magic happens with multi-stage injection. First, gentle speeds (30-50mm/s) allow the melt to fill the cavity smoothly, keeping things neat. As temperatures rise, gradually increasing the speed efficiently fills the cavity without losing control. Almost finished, slowing down reduces stress. I learned this after a mistake with complex products.
Stage | Speed Range | Purpose |
---|---|---|
Initial | 30-50 mm/s | Smooth entry, avoid spraying |
Mid-Filling | 50-80 mm/s | Efficient cavity filling |
Completion | 30 mm/s | Reduce residual stress |
Adjusting Mold Structure and Process Parameters
Tweaking the mold structure can change outcomes dramatically. I tackled poor exhaust by adding grooves and using breathable steel. Huge impact. Improving mold design really helps minimize defects like pores, even at lower speeds.
Gate and Runner Design: Choosing the right gate size and type based on product size was eye-opening. Large gates often use side gates to handle high speeds without issues. Smooth and sufficient runner diameter lowers melt flow resistance.
Holding Pressure Settings: Adjusting holding pressure after injection is crucial. I set it between 50%-80% of the injection pressure for 5-15 seconds, depending on wall thickness.
Material Pretreatment and Post-Treatment
Material Drying: Drying is key for materials like nylon (PA). I dry them at 80-100°C for 4-8 hours to stop bubbles during injection.
Post-Processing Techniques: Techniques like annealing are wonderful for reducing internal stresses from high injection speeds. Heating PC products at 120-140°C for 30-60 minutes really increases tensile strength.
For tips on optimizing parameters, explore technical resources5 that give best practices in injection molding settings.
Polyethylene requires 100-200mm/s injection speed.True
Polyethylene's good fluidity allows for faster injection speeds.
Poor exhaust design reduces tensile strength at low speeds.True
Inadequate exhaust can cause defects like pores, affecting strength.
Why Is Mold Design Crucial for Managing Injection Speed?
Curious about the importance of mold design in controlling how fast injection molding happens? I will explain its importance, based on my own experiences in mold design.
Mold design is very important for injection speed control. It decides how molten plastic moves through the flow path. This movement affects flow resistance and speed management for different materials. Mold design is crucial.
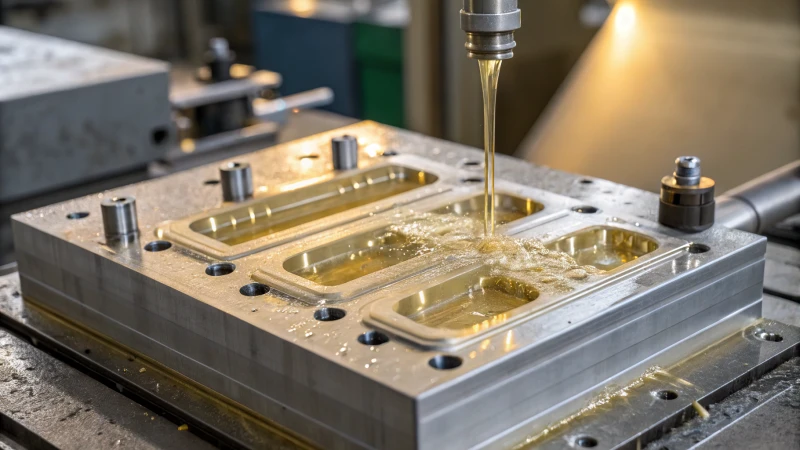
Understanding the Role of Mold Design
Years ago, as I began in mold design, I discovered how important mold design is for controlling speed in injection. I remember one project where a small mistake in gate placement caused big delays. Mold shape, including the gate and runner layout, controls how liquid plastic moves through spaces. A well-planned runner system6 lowers flow resistance. This control helps manage speed better.
Optimizing Injection Speed Parameters
I’ve worked with many materials and trust me, fluidity affects injection speed a lot. For example, polyethylene works best at faster speeds (100-200mm/s). In contrast, polycarbonate needs slower speeds (50-100mm/s). Knowing how materials behave lets you adjust mold details to enhance performance7.
Multi-Stage Injection Speed
A favorite method is using stages of speed for smooth filling. Begin with a lower speed (30-50mm/s) to avoid issues like spraying. Then, raise the speed in the middle and slow down at the end. This gradual style cuts down on stress and improves product quality8. It really helps.
Adjusting Mold Structure for Optimal Results
Improving Mold Exhaust Design
I remember a key moment when adding exhaust grooves improved mold design. Such a small change reduced defects like pores. Using breathable steel helps fill cavities evenly, especially at lower speeds.
Optimizing Gate and Runner Design
Picking the right gate size is critical. Trust me on this. A bigger side gate can handle higher speeds without trouble. Along with picking the right runner size and keeping it smooth, this is essential for efficient flow9.
Material Pretreatment and Post-Treatment
Drying hygroscopic materials like nylon before molding changed everything. I learned early on that bubbles can ruin a batch. Post-treatments like annealing remove stress from fast injection, making things stronger.
Importance of Accurate Process Parameters
Setting the right holding pressure was a lesson from a mentor. We adjusted holding pressure to be 50%-80% of injection pressure and timed it between 5-15 seconds. This greatly improved product density and cut down on flaws—these changes are crucial for ensuring quality10. Quality matters.
Larger side gates reduce stress in injection molding.True
Larger side gates accommodate higher speeds, reducing jetting and stress.
Polycarbonate requires the fastest injection speed.False
Polyethylene needs higher speeds (100-200mm/s) than polycarbonate (50-100mm/s).
Why Is Material Treatment Essential in Injection Molding?
Exploring injection molding, I found that treating materials is the secret to creating strong and high-quality items. Precision with moisture control is crucial. Thermal properties are very important. Managing both helps prevent defects. It truly is the key.
Material treatment in injection molding plays a key role in improving plastic performance by controlling moisture levels and thermal properties. Proper drying and post-processing steps lower defects. These steps boost product quality and extend the lifespan of items. Quality and durability increase.
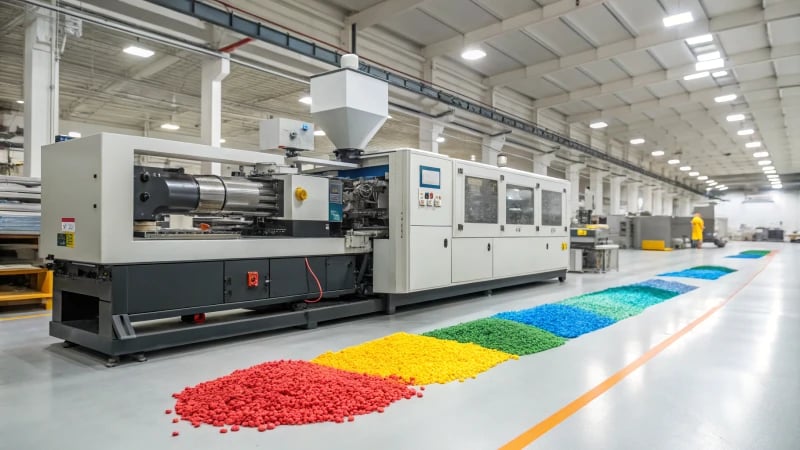
Understanding Material Treatment in Injection Molding
Once I discovered the complex steps of treating materials, I found a treasure of ideas that changed how I approached injection molding. The real challenge is in the drying stage. Many forget this crucial step. Think about using nylon; if it isn’t dried well, bubbles might appear. These bubbles are bad. They spoil the product’s internal quality11 and strength.
Drying Techniques
Let me share some advice from my journey. Here are the best drying conditions for common materials:
Material | Temperature (°C) | Time (Hours) |
---|---|---|
Nylon | 80-100 | 4-8 |
PC | 120-140 | 2-4 |
After perfect drying, materials move to the molding phase. Here, injection speed becomes crucial. Polyethylene needs fast injection due to its liquid form, while polycarbonate requires a slower speed of 50-100mm/s.
Optimizing Injection Speed
I learned about using multiple speeds during injection. Beginning slowly at 30-50mm/s stops problems like spraying. Speeding up later ensures filling. For tricky shapes, I begin at 40mm/s, push to 80mm/s, then slow down to 30mm/s at the end. This process lowers stress and strengthens tensile strength12.
Mold Design Considerations
Mold designs are vital. Better exhaust designs with grooves or breathable steel calm down the speed’s stressful effects on strength.
Gate and Runner Design
- Gate Selection: Use bigger gates for fast speeds and avoid jetting.
- Runner System: Keep smooth surfaces and wide paths to cut resistance.
This setup allows slower speeds but keeps good cavity filling, strengthening the result.
Post-Treatment Processes
Annealing stands out in post-processing. It lessens leftover stress by keeping PC products at 120-140°C for 30-60 minutes really helps to ease stress from quick speeds.
Thinking about material treatment in this complete way improves the product’s performance13. It also stretches mold life by lowering wear. Careful processes like these trimmed production costs and lifted product quality in my experience.
Nylon requires drying at 80-100°C for 4-8 hours.True
Nylon needs drying to remove moisture, preventing defects and ensuring quality.
High injection speed is ideal for polycarbonate.False
Polycarbonate requires moderate speed to avoid defects and ensure quality.
Conclusion
Optimize injection speed and mold design to enhance the tensile strength of plastic products, ensuring efficient production while minimizing defects through proper material treatment and post-processing techniques.
-
Understanding melt flow characteristics helps optimize injection speed settings for different plastics. ↩
-
This link provides strategies for effective multi-stage injection processes, enhancing product quality. ↩
-
Learn about post-processing methods that reduce internal stresses and improve product durability. ↩
-
Explore detailed guidance on managing injection speed settings tailored for different plastic materials. ↩
-
Delve into expert-recommended strategies for optimizing multi-stage injection molding processes. ↩
-
Understanding how runner systems affect flow can help optimize mold design for better control of injection speed. ↩
-
Exploring material-specific mold designs offers insights into achieving optimal injection speeds for different plastics. ↩
-
Learn about how multi-stage speeds can improve quality by managing stress distribution during the molding process. ↩
-
Discover why gate and runner design is crucial for reducing resistance and achieving smooth plastic flow. ↩
-
Understand how proper holding pressure settings enhance product density and reduce defects. ↩
-
Explore detailed guidelines on drying nylon to prevent quality issues like bubbles during molding. ↩
-
Learn how multi-stage injection techniques improve tensile strength and manage stress in complex shapes. ↩
-
Discover how annealing reduces internal stress, enhancing product performance and durability. ↩