Understanding the costs of injection molding machines is like solving a puzzle. Every part is essential for financial success. Financial success is the goal. Each component plays a vital role.
Focus on machine acquisition costs, operational expenses, maintenance, labor costs, and material wastage to optimize budgeting and enhance efficiency in injection molding machine cost accounting.
When I started to learn about injection molding cost accounting, I found out that knowing each cost part is central for a good profit. Watching raw material prices is like trying to predict rain – hard to foresee but manageable with smart tactics.
Labor costs reminded me of my first job. Every hour mattered and needed careful tracking. Workers’ time needs to fit perfectly with the products they create.
Equipment depreciation comes next. It is a part often ignored, but crucial for the budget. Choosing how to calculate depreciation is like picking the best tool for a home project. It needs thought and preparation.
Material loss rate in molding is 10%.True
Material loss during injection molding is typically around 10%.
Straight-line depreciation affects product costs.True
Different depreciation methods, like straight-line, impact annual costs.
How Do Raw Material Fluctuations Impact Cost Calculations?
Have your budget plans ever gone off track because of surprising changes in raw material costs? You’re probably not the only one! These price shifts affect how we calculate costs and plan to stay very profitable.
Fluctuations in raw material costs really affect production expenses. These changes alter the cost base, influence pricing plans and impact profits. Manufacturers maybe should use methods like weighted averages to keep costs steady over time.
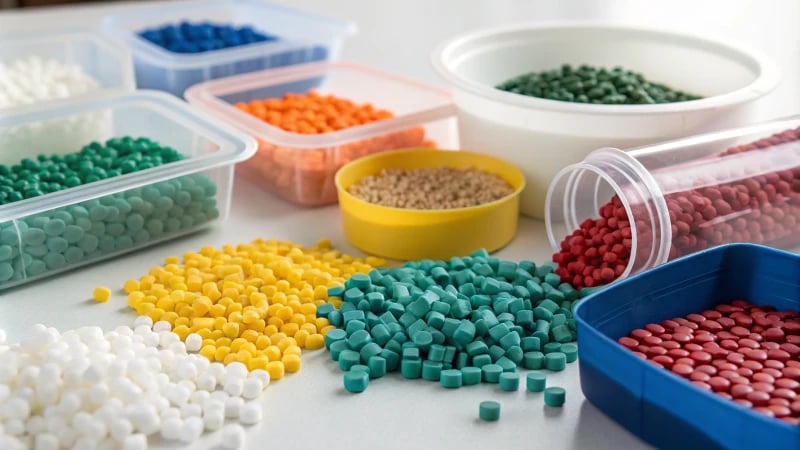
Understanding Raw Material Changes
I remember a time when I was busy with a project and suddenly, raw material prices rose sharply. It felt like being caught by a big wave while peacefully surfing. Market demand changes, world events, and oil price shifts often cause such changes. These numbers aren’t just statistics; they directly impact the cost of the products we work hard to produce.
Material Loss Awareness
In my early days, I learned about material loss the hard way. Imagine buying 100 kg of material and discovering 10% vanishes into air due to residues and waste during production. That feels like starting a road trip and realizing the handbrake is on.
Purchased Material | Used Material | Loss Rate |
---|---|---|
100 kg | 90 kg | 10% |
Calculating these losses precisely helps avoid surprises when figuring out true product costs.
Adjusting to Price Changes
Adjusting to price changes is challenging. In the past, I changed cost estimates based on instinct – big error! Now, I trust more structured methods like the weighted average1, which helps ease the sudden jolts over time.
Labor and Equipment Costing
Correct Labor Cost Tracking
Monitoring labor costs can be like herding cats. There was a project needing a special mold debugging process, but I forgot to add those hours to the final cost. Rookie mistake! Now, I carefully record every hour, including any overtime2, which often costs more.
Equipment Depreciation Choices
Choosing depreciation methods for equipment isn’t just for accountants. It’s essential for us too. For example, an injection molding machine costing 500,000 yuan depreciates by 45,000 yuan each year with the straight-line method. It took some time to see how this affects our yearly budgets.
Mold and Energy Cost Tracking
Molds are tricky. A mold expected to produce 100,000 products needed fixes halfway, so I adjusted its cost – a real puzzle at first. Accurately measuring energy use is also key, especially when machines have different efficiency levels.
Managing Cost Changes
These are my lessons for managing raw material price changes:
- Use flexible pricing methods.
- Secure long-term deals with suppliers.
- Have multiple suppliers to avoid reliance on one.
- Use forward contracts to keep prices steady.
These ideas aren’t just theory. They helped me stabilize costs even in a roller-coaster market. Understanding and using these tips keep manufacturing smooth and profitable despite market changes.
Material loss rate affects product cost calculations.True
Material loss, like residues and waste, impacts the actual material used.
Energy consumption is irrelevant in manufacturing cost accounting.False
Accurate energy measurement is crucial for determining manufacturing costs.
Why is Accurate Labor Cost Allocation Critical in Injection Molding?
Have you ever thought about why understanding labor costs is so important in injection molding? It’s not only about numbers. It’s about staying competitive. Each product needs to succeed financially. It’s really essential.
Accurate distribution of labor costs in injection molding is very important. Labor cost distribution directly affects how efficiently things get produced. It influences pricing strategies and profitability. Each product carrying its true cost increases competitiveness. It’s really important.
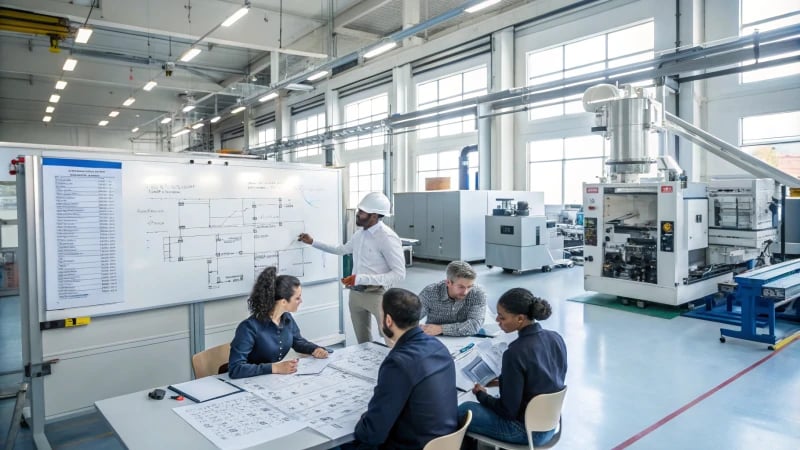
Understanding Labor Cost Parts
Exploring labor costs in injection molding feels like solving a tricky puzzle. Imagine the care needed to track each operation hour, machine setup, mold change, or any special tasks like fixing problems. I often struggle with this task, trying to capture every detail in work time statistics3 correctly. Every minute spent on a task should fairly contribute to the product’s final price.
The Effect of Mistakes
Once, a small mistake in labor cost allocation led to a product being too cheap. That was a real surprise. Misallocating labor costs can mess up product pricing. Overpricing might scare off customers, while underpricing can cause losses. For example, forgetting to include costs for special mold setups can greatly hurt profit checks.
Ways for Correct Allocation
To avoid these errors, several ways prove helpful:
- Time Tracking Systems: Digital tools help me capture working hours accurately.
- Proportionate Allocation: Sharing costs based on each product’s share of production hours makes it fair.
Here’s a basic example:
Product | Production Hours | Labor Cost Allocation |
---|---|---|
A | 50 | $500 |
B | 30 | $300 |
C | 20 | $200 |
Effect of Outside Factors
External factors like material price changes4 can disrupt everything. I learned harshly how such changes could switch up production schedules and affect labor needs. This can impact cost allocations. By mastering these aspects, I have managed to keep cost structures right and improve overall efficiency. Grasping these details means every product stays competitive and profitable.
Material loss rate in injection molding is 5%.False
The context specifies a 10% material loss rate, not 5%.
Straight-line method impacts annual depreciation cost.True
Different depreciation methods affect the annual depreciation amount.
How Does Equipment Depreciation Affect Cost Accounting?
Do you ever think about how the secret expenses of your machines might affect your profits?
Equipment depreciation is important in cost accounting. It shows how asset value goes down over time. This decline affects product costs and financial reports directly. Methods like straight-line or double declining balance calculate yearly depreciation. These methods are crucial for accurate finances. Financial accuracy is vital.
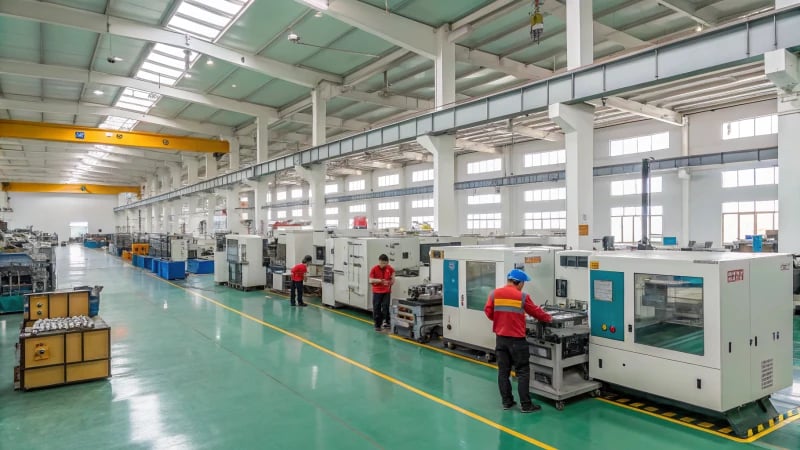
Understanding Equipment Depreciation
When I first entered the manufacturing world, depreciation seemed like a far-off accounting concept. Only accountants appeared to care. However, as I explored cost accounting, I realized that equipment depreciation is truly important for matching costs with the income from our assets. Spreading an asset’s cost over its lifespan helps us accurately assign costs. We don’t just assign costs randomly; costs line up with our production and sales periods.
Methods of Depreciation
Choosing a depreciation method feels like picking your pace for a marathon:
- Straight-Line Method: Provides a steady, even pace, spreading costs evenly over time. For example, if a machine is valued at $500,000 with a $50,000 residual value over ten years, it depreciates by $45,000 each year.
- Double Declining Balance Method: Places more expenses at the start and can be beneficial for tax purposes5.
Impact on Product Costing
Depreciation is more than an accounting task—it impacts each item made. Early in my career, I discovered that the $45,000 of annual depreciation for our molding machine added a $3 cost for each unit when creating 15,000 pieces every year. Every asset’s use impacts costs and earnings; this fact is very crucial.
Depreciation and Financial Statements
Depreciation acts quietly but importantly on financial statements:
- Balance Sheet: It slowly decreases asset book values, offering a clearer view of their worth now.
- Income Statement: As a non-cash expense that lowers taxable income, it can be beneficial for any business owner wanting to see better profit margins.
Influence on Asset Management Decisions
Depreciation knowledge helps with smart decisions about repairing or replacing machines. When equipment nears the end of its depreciable life, it’s time to decide whether repairs suffice or new machines are needed. This foresight is necessary for keeping efficiency high and staying competitive.
Practical Example of Depreciation Calculation
Asset | Purchase Price | Residual Value | Useful Life | Annual Depreciation |
---|---|---|---|---|
Machine | $500,000 | $50,000 | 10 Years | $45,000 |
Knowing these calculations allows for exact cost allocation6 and improves financial understanding. For any professional in our field, mastering this information means developing strategies for growth and sustainability—more than just crunching numbers.
Material loss rate affects product cost calculation.True
Material loss rate impacts the effective material used, altering costs.
Straight-line depreciation increases annual equipment costs.False
Straight-line depreciation distributes costs evenly over time, not increasing them.
How does mold cost allocation affect your budget?
Ever think about how something like mold cost allocation changes your budget? It’s a big shift in manufacturing finances. Let’s explore this topic.
Mold cost allocation affects your whole budget by spreading out costs such as materials, labor and equipment among products. Accurate pricing results from this. Financial efficiency follows from this.
Raw Material Calculations
The journey starts by understanding raw material costs. This part was quite an adventure by itself. I once had to include the material loss rate in my calculations. Surprisingly, it was higher than I imagined. For example, out of 100 kg of materials bought, only 90 kg turned useful, implying a 10% loss rate. That 10% loss was more than just a number; it was a real impact on the budget, affecting the product cost7. Market demand or oil prices often changed material prices too, constantly keeping us alert. Using methods like the weighted average helped bring order to the chaos.
Labor Cost Allocation
Accurately tracking operation, debugging, and mold change hours mattered a lot. I learned how easily costs went out of control if overtime wasn’t separated. Sharing labor costs fairly among products felt like walking on a tightrope.
Labor Cost Considerations | Description |
---|---|
Working Time Accuracy | Include operation, debugging, and mold change hours. |
Overtime Differentiation | Overtime wages are higher and should be tracked separately. |
It was really important to keep peace and fairness in the workplace.
Manufacturing Cost Accounting
Calculating depreciation added another level of difficulty. I remember figuring out the yearly depreciation for a machine costing 500,000 yuan with a 10-year life and 50,000 yuan residual value using straight-line depreciation method resulted in an annual amount of 45,000 yuan.
Energy consumption measurement is another key factor. Watching energy use closely was essential too; we had to check that our machines’ energy-saving features weren’t being wasted.
Mold Cost Allocation
Finally, dividing mold costs was like adding the final piece to a jigsaw puzzle. We considered everything from service life expectations to production quantities.
For instance:
- Initial Cost: 200,000 yuan
- Repair Cost: 50,000 yuan
- Total Products: Initially expected for 100,000 units
- New Cost per Product after repair: Recalculated to 2.5 yuan per unit for remaining products.
Ensuring accurate mold cost allocation can lead to better budget management and pricing strategies in manufacturing operations.
Material loss rate affects product cost.True
Material loss during production increases the actual cost of materials.
Energy-saving devices increase equipment energy consumption.False
Energy-saving devices reduce, not increase, energy consumption.
Conclusion
This article outlines essential factors in injection molding cost accounting, focusing on raw material pricing, labor costs, equipment depreciation, and mold cost allocation for financial efficiency.
-
Learning weighted average calculations aids in stabilizing raw material cost fluctuations. ↩
-
Knowing how overtime impacts labor costs ensures accurate financial assessments. ↩
-
Discover methods and tools for maintaining accurate working time statistics to improve cost allocation efficiency. ↩
-
Explore how material price fluctuations can impact labor cost allocation and overall injection molding expenses. ↩
-
Discover how using double declining balance can reduce tax liabilities by accelerating depreciation expenses. ↩
-
Understand methods for distributing equipment depreciation costs across products to ensure accurate pricing. ↩
-
Understanding material loss rates helps in precise cost calculations, crucial for financial efficiency and accurate pricing. ↩