Do you ever think about how to strengthen plastic products using injection molding?
To increase product strength in injection molding, adjust the injection pressure and speed. Optimize packaging settings to see improvements. Manage mold temperature and cooling time carefully. These changes lead to better material flow and cooling. Really sturdy products result from this approach. Reliable products are the outcome.
I remember starting with injection molding. It felt like solving a difficult puzzle. Every small change was a real victory. Each parameter interacts with others. These connections help perfect the process. Strong results come from this precision.
Higher mold temperature increases product strength.True
Increased mold temperature allows better material flow, enhancing strength.
Reducing cooling time weakens the molded product.True
Shorter cooling times may lead to incomplete solidification, weakening strength.
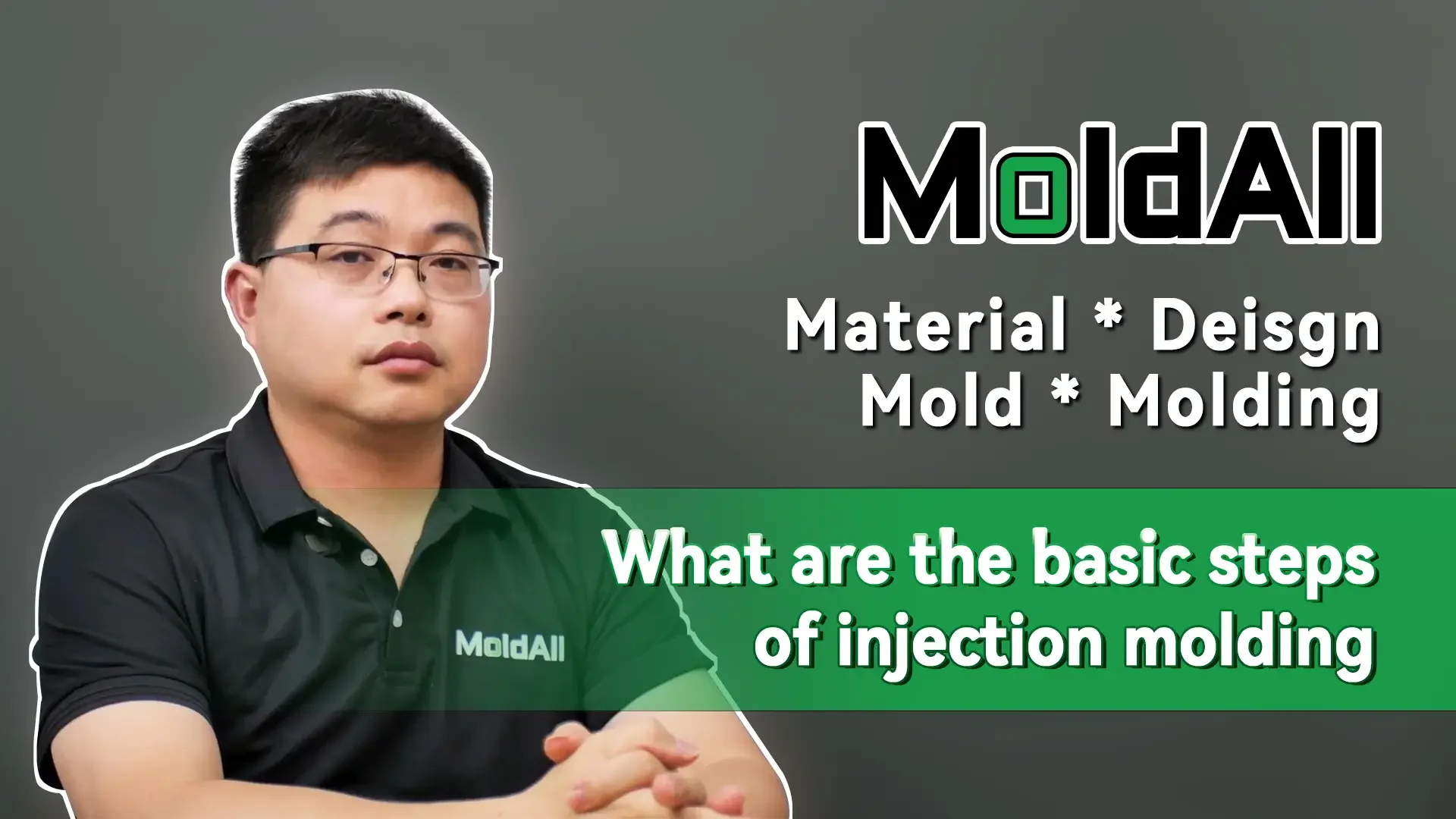
- 1. How Does Injection Pressure Influence Product Strength?
- 2. Why is Injection Speed Crucial for Uniform Filling?
- 3. How Do Packaging Parameters Affect Product Density?
- 4. How Does Mold Temperature Control Enhance Product Strength?
- 5. Why is Cooling Time Critical for Structural Stability?
- 6. Conclusion
How Does Injection Pressure Influence Product Strength?
Have you ever thought about how small changes in injection pressure totally change a product’s strength?
Injection pressure is very important in molding. It fills the cavity completely and increases material density. This directly affects how strong the product is. Changing pressure is crucial. It stops defects and strengthens materials like polyamide (PA).
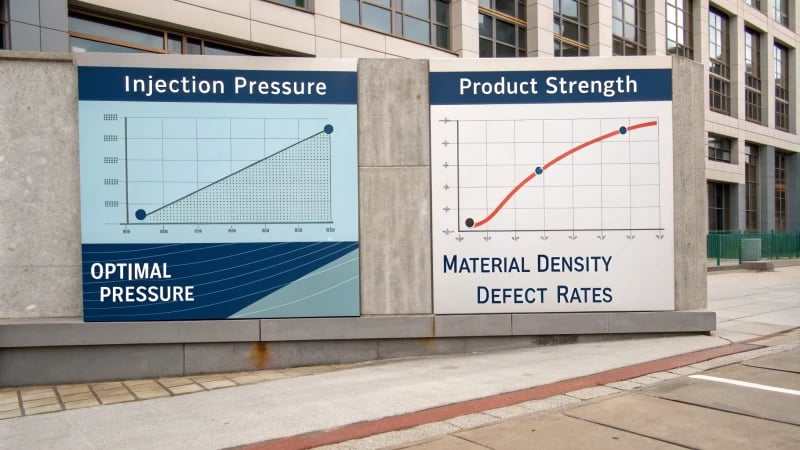
The Role of Injection Pressure
I remember realizing how important injection pressure is in plastic molding1. During one project, we faced problems with the strength of some molded parts. Adjusting the pressure helped the plastic fill every part of the mold, improving both the density and strength of the product. For example, with strong engineering plastics like polyamide (PA), using pressure from 70-80MPa to 90-100MPa made a big difference. It was very effective.
However, balance is very important. Too much pressure can cause stress and weaken the product over time. It’s like squeezing into jeans that are too small; it doesn’t work in the long run. So, we run mold trials to find the right balance.
Injection Speed Considerations
Speed plays a significant role as well. In a project with electronic casings, adjusting the speed was necessary to avoid defects and ensure even filling. By increasing the speed from 30-40mm/s to 40-50mm/s, we achieved great results for thin-walled designs. Yet, going too fast can cause spray marks, much like speeding on a highway.
Packaging Parameter Optimization
Do not ignore packaging parameters if you want stronger products. I learned this early when I saw how holding pressure affects the outcome. Raising it from 40-50MPa to 60-70MPa reduced defects by handling volume loss from shrinkage. Also, increasing holding time from 5-8 seconds to 8-12 seconds helped achieve better solidification.
Parameter | Recommended Increase | Benefit |
---|---|---|
Holding Pressure | 40-50MPa to 60-70MPa | Reduces shrinkage |
Holding Time | 5-8s to 8-12s | Improves density |
Mold Temperature and Cooling Time
Temperature control is truly vital. I recall a project involving crystalline plastics like polypropylene (PP). Adjusting mold temperature from 30-40℃ to 50-60℃ led to a more regular crystal structure and increased strength. For non-crystalline plastics, choosing the right temperature relaxed the molecular chains and improved strength.
Cooling time also demands patience. For thick-walled products, extending cooling time from 20-30 seconds to 30-40 seconds preserved shape and stability after demolding.
Focusing on these parameters allows manufacturers to significantly improve product strength and quality in injection molding processes.
Increasing injection pressure increases product density.True
Higher pressure ensures complete mold fill, enhancing density.
Excessive injection speed eliminates all defects.False
Too rapid speeds can cause defects like spray marks.
Why is Injection Speed Crucial for Uniform Filling?
Did you ever think about why your injection-molded pieces sometimes are not flawless? The speed of your injection might be the reason!
Injection speed is very important for even filling of a mold. It decides how evenly and quickly hot material spreads inside the mold. This affects the quality of the product directly. The right speed probably reduces defects such as flow lines and empty spaces. It helps to keep every piece the same. Quality and consistency are important.
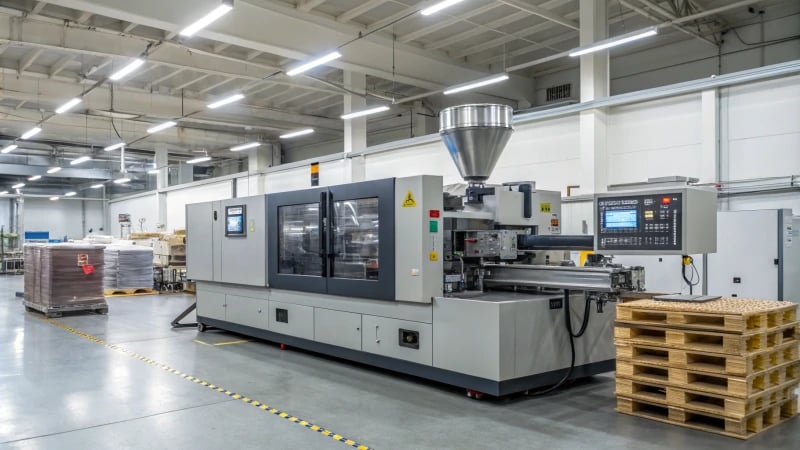
Understanding Injection Speed’s Impact
Injection speed resembles a Goldilocks situation in molding – perfect speed results in wonders. It determines how quickly the molten material settles in the mold. For complex shapes or thin-walled designs, the right speed fills every corner before cooling begins. Proper speed adjustment2 stops defects effectively. This is really important.
Balancing Injection Speed and Pressure
At first, I thought increasing speed was the ultimate solution. But it involves careful pressure management too. Both speed and pressure must work together. For materials like polyamide, adjusting pressure smoothly, from 70-80 MPa to 90-100 MPa, keeps the material stress-free and avoids problems.
Material | Original Pressure (MPa) | Optimized Pressure (MPa) |
---|---|---|
Polyamide (PA) | 70-80 | 90-100 |
The Role of Injection Speed in Preventing Defects
Higher injection speed reduces cooling time, preventing incomplete fills and air bubbles. Yet, excess speed might lead to surface marks. Adjusting speed from 30-40mm/s to 40-50mm/s for electronic casings keeps them sharp and intact. This adjustment is crucial for maintaining product integrity3.
Injection Speed and Product Density
Injection speed affects density along with filling, much like baking where rushing results in flat cakes. Right pressure and timing help shrinkage control, saving the product. Increasing holding pressure in polycarbonate helps density and strength.
Product Type | Original Holding Pressure (MPa) | Optimized Holding Pressure (MPa) |
---|---|---|
Polycarbonate | 40-50 | 60-70 |
Density is really important.
Mold Temperature and Cooling Time Considerations
Correct mold temperature avoids deformations. It’s similar to setting your oven right. For polypropylene, keeping temperature at 50-60℃ encourages crystallization, making it stronger. Proper cooling time, especially for thick items, is like letting cookies cool – no crumbling.
Balancing these parameters with injection speed is crucial for achieving uniform filling and optimal product quality in injection molding processes.
These strategies can probably change production for the better. Explore more techniques4 to master molding.
High injection speed prevents cooling before filling.True
High speed ensures molten material fills mold before cooling, preventing defects.
Increasing injection speed always improves product quality.False
Excessive speed can cause defects like spray marks, reducing quality.
How Do Packaging Parameters Affect Product Density?
Ever thought about how small changes in packaging shift product weight and quality? Join me to explore this interesting world.
Packaging elements such as injection pressure, speed and cooling time play a crucial role in shaping product density. Adjusting these factors helps the mold fill completely. This reduces flaws and strengthens the product. It is very important.
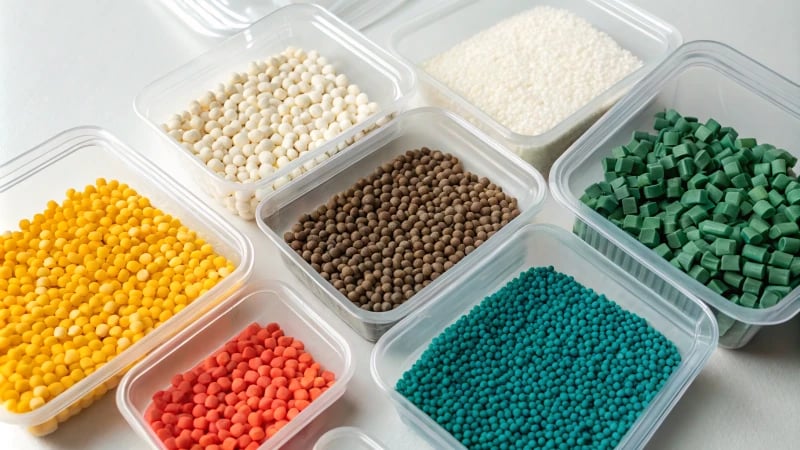
Injection Pressure and Speed Adjustment
Let’s explore the world of injection molding. I had a big "Aha!" moment once. Imagine working hard on a new polyamide part, only to see the density was wrong. The key was adjusting pressure and speed. Increasing pressure from 70-80 MPa to 90-100 MPa solved the problem. Balance is crucial – extra pressure causes stress inside.
Similarly, speed is another interesting factor. It’s like finding the right comfort level. For complex designs or thin pieces, increasing speed from 30-40 mm/s to 40-50 mm/s is important. But be careful; going too fast causes spray marks.
Optimizing Packaging Parameters
Setting Packaging Pressure and Time
Improving a polycarbonate product line was very rewarding. It felt like solving a puzzle. Increasing packaging pressure from 40-50 MPa to 60-70 MPa fixed shrinkage and improved strength. Yet, careful attention was necessary, like walking a tightrope, to avoid problems such as flashing.
Holding time matters a lot. It’s like waiting for dough to rise. Extending time from 5-8 seconds to 8-12 seconds, especially with thicker products, brought fantastic results.
Product Type | Holding Pressure (MPa) | Holding Time (seconds) |
---|---|---|
PC Products | 60-70 | 8-12 |
Thick Walls | – | 8-12 |
Controlling Mold Temperature
Temperature control in molding is a hidden key in product crystallization5. For example, working with crystalline plastics such as polypropylene involved adjusting mold temperature from 30-40℃ to 50-60℃. This shift helped crystallization and strengthened the product.
Adjusting Cooling Time
One tough project involved thick-walled products needing special cooling. Extending cooling time from 20-30 seconds to 30-40 seconds kept dimensions stable and the structure strong.
Grasping these parameters let me fine-tune production, balancing design and function in large-scale settings. It’s really about merging science with creativity.
Increasing injection pressure enhances product density.True
Higher pressure ensures complete mold filling, increasing final product density.
Lowering mold temperature increases product strength.False
Raising mold temperature enhances crystallization and structural strength.
How Does Mold Temperature Control Enhance Product Strength?
Did you ever think about how changing mold temperature increases product strength? It’s almost like magic, yet it’s science!
Controlling mold temperature is important for creating strong molded products. Factories set the correct temperature for various materials. Crystalline plastics benefit from improved crystallization. Non-crystalline plastics gain from adjusting molecular chains. This results in stronger products. It truly does.
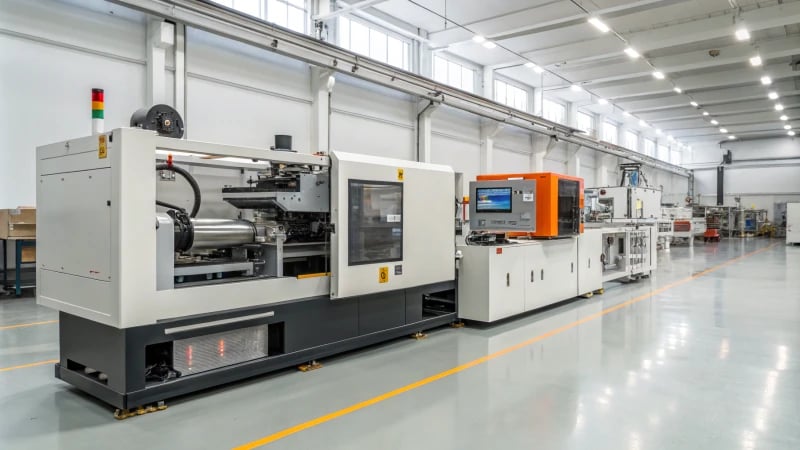
Impact on Crystalline Plastics
I remember when I started in the industry and discovered how mold temperature could change everything. Think about crystalline plastics like polypropylene (PP). Raising the mold temperature to about 50-60℃ leads to a more even crystal pattern, which increases the product’s strength. It was like finding a hidden trick in a game where suddenly all pieces fit together.
Factor | Effect on Strength |
---|---|
Higher Mold Temp | Promotes crystallization |
Lower Mold Temp | May prevent full solidification |
Influence on Non-Crystalline Plastics
Then there are non-crystalline plastics, such as polycarbonate (PC). Proper temperature control allows these materials to loosen and align their molecular chains. It’s like giving them a deep massage, making them tougher and less likely to have flaws.
Balancing Injection Pressure and Speed
During my career, pressure and speed in injection processes became very important. For example, with polyamide (PA), higher injection pressure6 fills every part of the mold well. But it’s key to find a balance – too much pressure might cause stress inside. Changing how fast you inject affects cooling rates, which then changes strength.
Factor | Effect on Strength |
---|---|
Optimized Pressure | Enhances density |
Extended Cooling | Improves structural integrity |
Packaging Parameter Optimization
Improving packaging details is another important task in this field. More holding pressure7 helps reduce shrinkage when cooling, increasing density and strength. For thick products, longer holding time is essential to prevent bending.
Cooling Time Considerations
Cooling time is crucial and often ignored. Enough cooling time allows the material to fully harden, cutting down risks of shape change after removal from the mold. For thicker items, longer cooling is vital to keep them solid. It is like letting a stew cook long enough for the best taste, bringing strength in this case.
Higher mold temperature promotes crystallization in PP.True
Higher temperatures enable regular crystal structures, enhancing strength.
Non-crystalline plastics require high temperatures for strength.True
Controlled temperatures relax molecular chains, improving material strength.
Why is Cooling Time Critical for Structural Stability?
Everyone knows that feeling when a beloved gadget functions perfectly. Nobody questions why it happens. Well, the cooling process plays a crucial role. Let me explain why it’s vital.
Cooling time is essential for materials to harden evenly. It reduces stress inside the material. This process increases material strength and stability. It also helps meet quality standards very important in manufacturing.
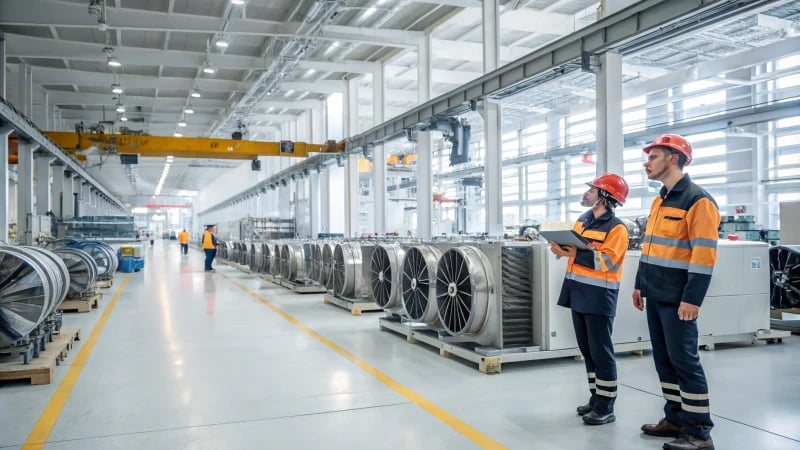
The Role of Cooling Time in Material Solidification
Cooling time determines how materials transition from liquid to solid states. An extended cooling period ensures that the material8 solidifies evenly, avoiding uneven density distribution. For instance, in plastic molding, sufficient cooling time prevents warping and dimensional inaccuracies.
Once, I worked on a big plastic molding project – so nervous about perfection. Cooling time soon became very important. It decides how materials change from liquid to solid, so they solidify evenly. Incorrect cooling causes warping and loss of shape. Try fitting a bent puzzle piece into a perfect frame – it won’t fit!
Effects on Microstructure and Stability
In metallurgy, cooling rates impact the microstructure of metals like steel. A controlled cooling rate influences the formation of crystalline structures9, enhancing hardness and tensile strength. For polymeric materials, slow cooling can enhance molecular alignment, improving mechanical properties.
While designing a steel part, I learned the importance of controlling cooling for the right microstructure. These structures affect strength and hardness a lot. With polymers, slow cooling keeps molecules in line, giving more robustness.
Injection Pressure and Speed Adjustment
Adjusting injection pressure and speed is essential for precise molding. Higher injection pressure can fill molds completely, while regulated speed ensures uniform cavity filling. These adjustments prevent defects like voids or spray marks, impacting the final product’s structural integrity.
On a project with engineering plastics, I figured out injection pressure and speed needed balance. Higher pressure filled molds completely, but too much pressure caused stress. Speed adjustment filled complex shapes more evenly, avoiding defects like spray marks – those annoying flaws that mess up look and function.
Parameter | Impact on Stability |
---|---|
Injection Pressure | Ensures mold filling and product density |
Injection Speed | Avoids defects, ensures uniform filling |
Packaging Parameter Optimization
Properly adjusting packaging pressure compensates for volume loss during cooling, reducing shrinkage holes. This step is crucial for maintaining the density10 and strength of finished products. Extending holding time further aids in achieving optimal material properties.
Once, we faced shrinkage holes in polycarbonate items. By adjusting packaging pressure, we improved their density and strength. Longer holding time allowed the melt more time to solidify perfectly – vital for thicker items.
Importance of Mold Temperature Control
Appropriate mold temperature settings enhance the structural stability of both crystalline and non-crystalline plastics. Higher temperatures promote crystallization in materials like polypropylene, leading to stronger products.
I’ve learned mold temperature is powerful. With plastics like polypropylene, changing mold temperature matters greatly. Raising it helps crystallization and strengthens the final product.
Cooling Time Adjustment Techniques
For thick-walled products, extending the cooling time is vital. Longer cooling periods allow the internal structure to stabilize, preventing post-demolding deformation. This adjustment is critical in achieving desired product specifications and maintaining consistent quality standards across production batches.
For thick products, extending cooling time became a regular step in design—like letting dough rise before baking—it guarantees stability and stops deformation after the mold.
By understanding these factors helps create stable products meeting industry standards; designers and engineers can optimize manufacturing processes to produce structurally stable products that meet industry requirements efficiently adapting to different material properties solving manufacturing issues well.
Want to know more? Learn how cooling time affects different materials uses—it’s fascinating how a simple idea holds secret solid structure many areas.
Extended cooling time prevents warping in plastic molding.True
Sufficient cooling time allows even solidification, avoiding deformation.
Faster cooling rates increase tensile strength in metals.False
Controlled cooling, not faster rates, enhances crystalline structure and strength.
Conclusion
Optimize injection molding by adjusting pressure, speed, mold temperature, and cooling time to enhance product strength and quality, ensuring better material flow and structural integrity.
-
Discover how different levels of injection pressure impact the quality and properties of molded plastic parts. ↩
-
Learn techniques for adjusting injection speed to improve mold filling and reduce defects. ↩
-
Understand strategies to prevent common defects like spray marks and air traps. ↩
-
Explore comprehensive techniques to master the complexities of injection molding. ↩
-
Explore how adjusting injection pressure impacts the density and quality of molded products. ↩
-
Learn how adjusting injection pressure can optimize plastic strength and density. ↩
-
Understand why holding pressure is crucial for preventing shrinkage and improving product strength. ↩
-
Learn how cooling time affects material transitions from liquid to solid, impacting product integrity. ↩
-
Discover how controlled cooling influences crystalline structures in metals like steel. ↩
-
Understand how packaging pressure adjustments enhance product density and strength. ↩