I remember the first time I saw an injection molding machine. It felt like watching magic! But behind this magic hides a very precise science.
Incorrectly setting injection pressure during molding often results in problems such as flash, spray marks, silver streaks, size errors and bubbles. These defects reduce the finished products’ looks, usefulness and strength. Quality and strength drop significantly.
When I recall problems with injection molding, memories of my early years in manufacturing come to mind. I struggled with strange issues back then. Every defect revealed something important about the process. Understanding the causes of these defects is like finding hidden truths. These secrets really help improve production quality. Let’s explore each defect and learn how to stop them. Our work should not only succeed but also show our skill.
Improper pressure causes flash in injection molding.True
Flash occurs when excess material escapes the mold, often due to high pressure.
Silver streaks enhance product appearance in molding.False
Silver streaks are defects that negatively affect the visual quality of products.
- 1. How does high injection pressure lead to flash and its consequences?
- 2. Why Do Silver Streaks Appear on Molded Products and How Can I Prevent Them?
- 3. How Do Pressure Variations Cause Dimensional Deviations?
- 4. Why Do Welding Marks Form in Injection Molding and What Are Their Impacts?
- 5. Conclusion
How does high injection pressure lead to flash and its consequences?
Have you ever thought about how the smallest detail in injection molding might cause big problems for your final product?
High injection pressure forces plastic melt past the mold’s parting lines. This happens when the pressure overcomes the mold’s clamping force. Uneven edges result from this process. Trimming costs really increase.
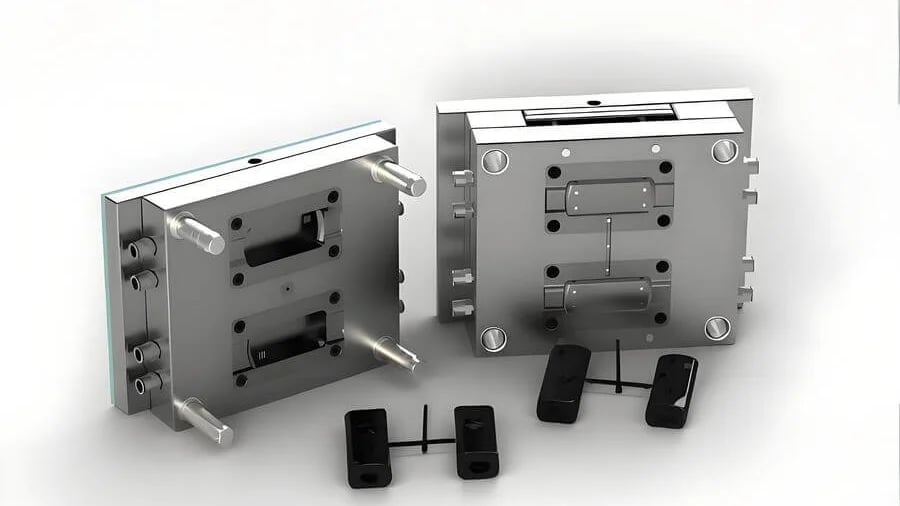
How Flash Forms
Flash appeared like an unwelcome surprise during my early industry days. It sneaked in when injection pressure overwhelmed the clamping force in the mold. This pressure pushed plastic through small gaps. Imagine trying to cover a steaming pot without a tight lid – steam escapes anywhere it can.
Visual Defects and Their Effects
Defect | Cause | Impact |
---|---|---|
Flash | High injection pressure forces melt past mold edges. | Uneven edges, increased post-processing costs. |
Size Accuracy | High injection pressure causes products to swell beyond intended dimensions, similar to putting too much dough on a baking tray. | Misfit with other components, affecting functionality. |
Issues with Size Accuracy
High injection pressure not only affects appearance; it influences size. Too much pressure makes products swell beyond their intended dimensions, similar to putting too much dough on a baking tray. Low pressure has the opposite effect, leaving the product underfilled.
- Dimensional Deviation: Flash or short shots alter product size beyond design specifications.
- Uneven Shrinkage: Incorrect pressure affects melt shrinkage during cooling, leading to uneven dimensions.
Problems Inside the Product
Internal flaws cause significant problems. I often dealt with shrinkage marks and bubbles. Filling a balloon without causing wrinkles or air pockets feels familiar.
- Shrinkage Marks: These arise when thick parts don’t receive enough melted material.
- Welding Marks: Occur when two molten streams don’t merge correctly due to insufficient pressure.
- Bubbles: Appear from trapped air during fast or slow melt flow.
Grasping these defects was crucial. This understanding has transformed my method. Each change brings better quality and reduces costs, which is essential in optimizing injection molding1 processes for better quality control and reduced production costs.
Flash occurs when injection pressure exceeds clamping force.True
High pressure forces plastic melt past mold edges, causing flash.
Low injection pressure leads to flash defects.False
Flash results from excessive, not low, injection pressure.
Why Do Silver Streaks Appear on Molded Products and How Can I Prevent Them?
Ever thought about why those annoying silver lines appear on your otherwise flawless molded items? These streaks surprise many. They leave marks where everything else looks perfect. They really stand out, don’t they? This issue puzzles even the most skilled craftsmen.
Silver lines in molded items happen because of wrong pressure during injection. This traps air or evaporates moisture in the melted plastic. Adjusting injection speed, pressure and mold temperature really stops these lines.
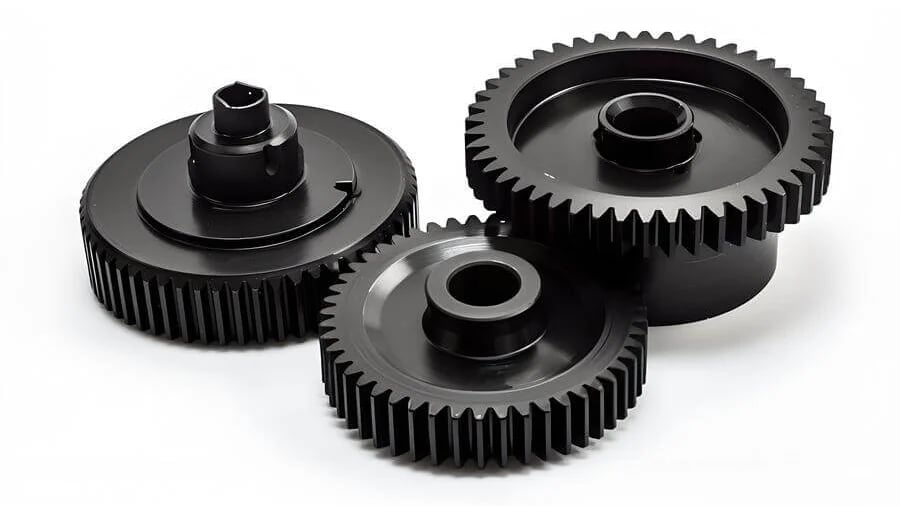
Understanding How Silver Streaks Form
I remember my first encounter with silver streaks on molded products. It was really frustrating! These splash marks appear when air or moisture2 gets trapped in the plastic during injection. As the product cools, these trapped elements leave behind visible streaks or spots.
Causes of Silver Streaks
- High Injection Pressure: Moving the melt too quickly traps air, similar to how excessive pressure causes flash formation3.
- Low Injection Pressure: Not enough pressure leads to overheating in parts of the mold, making moisture evaporate and leaving streaks.
Cause | Description |
---|---|
High Injection Speed | Traps air due to rapid flow |
Low Injection Speed | Causes moisture evaporation |
Mold Temperature | Inconsistent temperature leads to air/moisture entrapment |
Prevention Techniques
- Optimize Injection Pressure and Speed: Balancing these reduces defects like tricky spray patterns4.
- Control Mold Temperature: Keeping the temperature even prevents localized issues.
- Proper Mold Design: Features for air venting really help reduce defect formation.
Impact on Product Quality
Silver streaks spoil the look of products, making them seem less valuable. In industries where appearance is key, like consumer electronics, removing these streaks is critical. By understanding their causes and making changes, I’ve seen product quality really improve.
For those who want to learn more about dealing with appearance defects, explore dimensional accuracy strategies5. A complete approach, including design, processing conditions, and material choice is necessary. Doing this reduces defects and improves both reliability and market acceptance. It is essential for smooth production and staying competitive in our industry.
High injection speed causes silver streaks.True
Rapid flow traps air, forming silver streaks during cooling.
Proper mold design eliminates all silver streaks.False
Mold design reduces but doesn't completely eliminate streaks.
How Do Pressure Variations Cause Dimensional Deviations?
Ever thought about why some products don’t work well together or appear as nice as you expected? Pressure changes often cause this problem.
Pressure changes really change a material’s size or shape from its original design. This messes up assembly. Appearance suffers too. Performance decreases, especially in molded items.
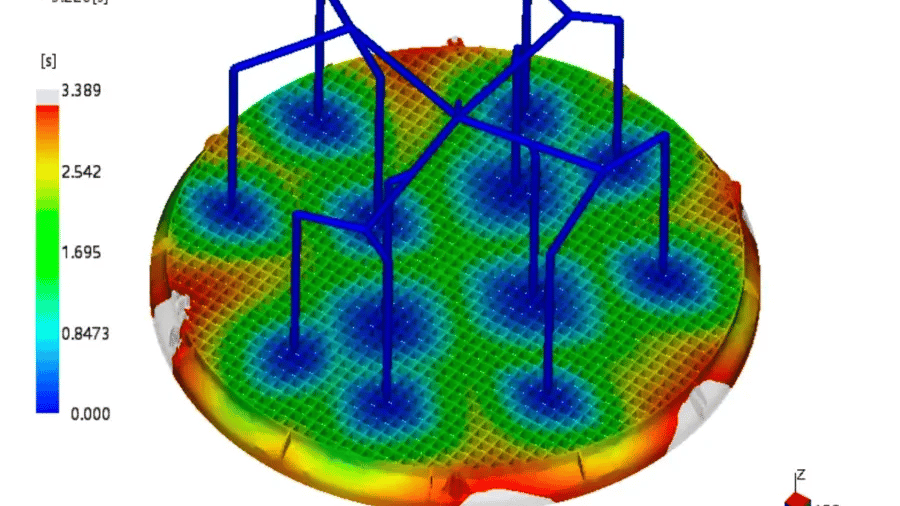
Causes of Dimensional Deviations
Dimensional deviations often arise from pressure variations6 during processes like injection molding. High pressure can lead to flash, where excess material overflows from the mold, creating unwanted extensions beyond the desired shape. Conversely, low pressure may result in short shots, where insufficient material fills the mold, leading to smaller product dimensions.
Appearance Defects
Defect Type | Cause | Impact |
---|---|---|
Flash (Overflow) | Excess pressure causing material to overflow | Uneven edges, increased trimming costs |
Silver Streaks | Air mixed into melt due to fast flow | Diminishes product appearance quality |
These flaws showed up clearly during a project when silver streaks appeared on electronic casings. They looked like scars on what should have been perfect surfaces.
Dimensional Accuracy Defects
High injection pressure can cause flash that might break design limits, while low pressure leads to underfilled parts. Both scenarios result in dimensional deviations that hinder product assembly7 and functionality.
Uneven Shrinkage
Improper pressure affects shrinkage. High pressure alters shrinkage rates across the product, while low pressure may cause shrinkage marks in thick areas. This deformation impacts both fit and visual quality.
Internal Quality Concerns
Pressure variations not only affect external appearance but also internal quality:
- Shrinkage Marks: Insufficient pressure leads to uneven surfaces and reduced strength.
- Welding Marks: Low pressure causes poor fusion where multiple melts meet, weakening structure.
- Bubbles: Both low and high pressures can trap air within the material, compromising density and integrity.
Understanding these factors helps improve design and manufacturing processes, ensuring high-quality plastic products8. Every project teaches valuable lessons about predicting and combating these unseen forces that could ruin designs.
High pressure causes flash in molded products.True
Excess pressure leads to material overflow, creating flash.
Low pressure results in larger product dimensions.False
Low pressure causes underfilling, resulting in smaller dimensions.
Why Do Welding Marks Form in Injection Molding and What Are Their Impacts?
Curious about why those annoying lines show up on plastic items? These lines are not merely a surface problem!
Welding marks appear in injection molding. Different flow fronts of molten plastic meet in the mold cavity. The plastic does not fully bond. This results in visible lines that weaken and spoil the look of the final product.
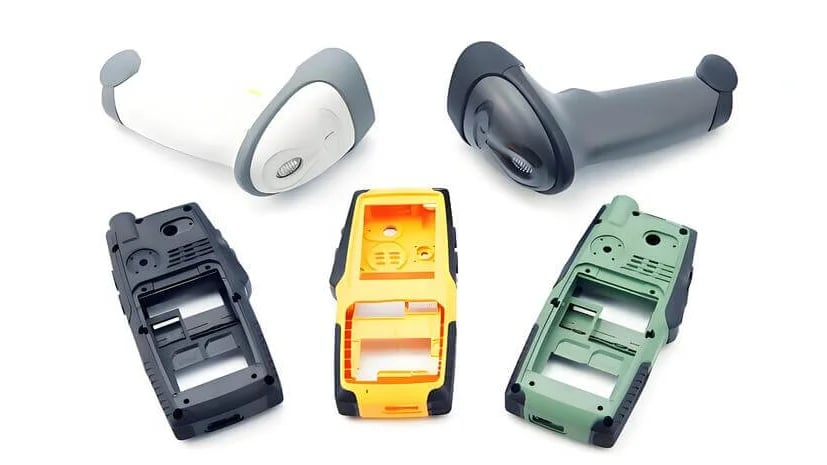
Formation of Welding Marks
Oh, welding marks! Anyone who works with injection molding knows these are unwanted like a bad haircut before an important event. These marks appear when the flowing plastic doesn’t fully join. This usually happens when the temperature or pressure isn’t correct. Imagine mixing oil and water; without perfect conditions, they won’t fully join. I’ve witnessed this occur when the injection speed isn’t set correctly or when the mold temperature is slightly too low.
In injection molding, welding marks9 occur when different flows of molten plastic meet within the cavity. If the temperature and pressure conditions are not optimal, these flows may not fuse correctly, leaving a visible line.
Factor | Impact on Weld Marks |
---|---|
Injection Speed | Slow speeds can cause insufficient fusion. |
Mold Temperature | Lower temperatures prevent proper fusion. |
Impact on Product Quality
Weld marks can ruin a successful production run. They create weak spots, making parts likely to break. This is not something you want, especially in critical parts like car components. Picture driving on the highway and feeling the steering wheel move more than it should. That’s really not good.
- Reduced Strength: As weak points, weld marks can decrease the structural integrity of molded parts. For components such as automotive parts, this weakness can lead to premature failure under stress.
- Aesthetic Concerns: Products like consumer electronics housings require flawless finishes. Weld marks compromise the appearance, making them unacceptable for high-end applications.
- Increased Production Costs: Correcting these issues means more adjustments, longer production times and more resources used.
Addressing weld mark issues may involve process adjustments10, leading to increased cycle times and resource use.
Addressing Welding Marks
So, how do we remove these annoying weld marks? It involves optimization:
- Optimize Injection Parameters: Adjusting speed and pressure ensures better fusion of molten flows.
- Control Mold Temperature: Maintaining an appropriate mold temperature promotes better bonding between flow fronts.
- Modify Part Design: Redesigning areas to avoid multiple flow fronts cuts down on weld lines a lot.
Adjusting where you place gates or adding flow channels is very effective.
For those curious about this topic, many detailed guides exist that provide more insight into refining the injection molding process and avoiding weld marks effectively. Checking in-depth guides11 on injection molding process optimization can provide further insights.
Weld marks form due to high injection speed.False
Weld marks form from low injection speeds causing insufficient fusion.
Mold temperature affects weld mark formation.True
Lower mold temperatures prevent proper fusion, causing weld marks.
Conclusion
Improper injection pressure in molding can lead to defects like flash, silver streaks, and size inaccuracies, affecting product quality and increasing production costs.
-
Learn about methods to enhance molding efficiency and product quality by managing pressure effectively. ↩
-
Explore detailed causes of air entrapment in plastic injection molding, vital for understanding defect prevention. ↩
-
Learn how excessive injection pressure leads to flash, a common molding defect affecting product quality. ↩
-
Discover techniques to prevent spray patterns, ensuring superior surface quality in molded products. ↩
-
Understand solutions for dimensional accuracy defects, enhancing precision and fit of molded parts. ↩
-
Explore detailed insights into how different pressure levels impact dimensional accuracy and product quality. ↩
-
Learn about the challenges dimensional deviations pose during assembly and how they can disrupt product functionality. ↩
-
Gain practical tips on enhancing plastic product quality by addressing pressure-related defects. ↩
-
Understand the technical details of how weld marks form during the injection molding process. ↩
-
Learn about specific parameter adjustments that can minimize weld line formation. ↩
-
Explore comprehensive strategies for improving injection molding processes to reduce defects. ↩