Ever stared at a product and wondered how something so seemingly simple could be so complex? Let’s dive into the fascinating world of injection molding!
Uneven wall thickness in injection molded products is often caused by factors such as unreasonable mold design, inaccurate mold manufacturing, unstable injection pressure, and improper material selection. To optimize this, manufacturers must refine mold design, stabilize process parameters, and select suitable materials.
While this overview provides a snapshot of the causes and solutions for uneven wall thickness, a deeper understanding is essential for effectively troubleshooting and optimizing your manufacturing processes. Read on to explore detailed strategies for improving your injection molding outcomes.
Mold design impacts wall thickness uniformity.True
Mold design affects wall thickness through cavity design and gate positioning.
How Does Mold Design Affect Wall Thickness?
Mold design is pivotal in determining the uniformity of wall thickness in injection molded products. It requires precision and optimization.
Mold design impacts wall thickness through factors like cavity design, gate positioning, and manufacturing accuracy. Unoptimized molds can cause thickness variations, affecting product quality.
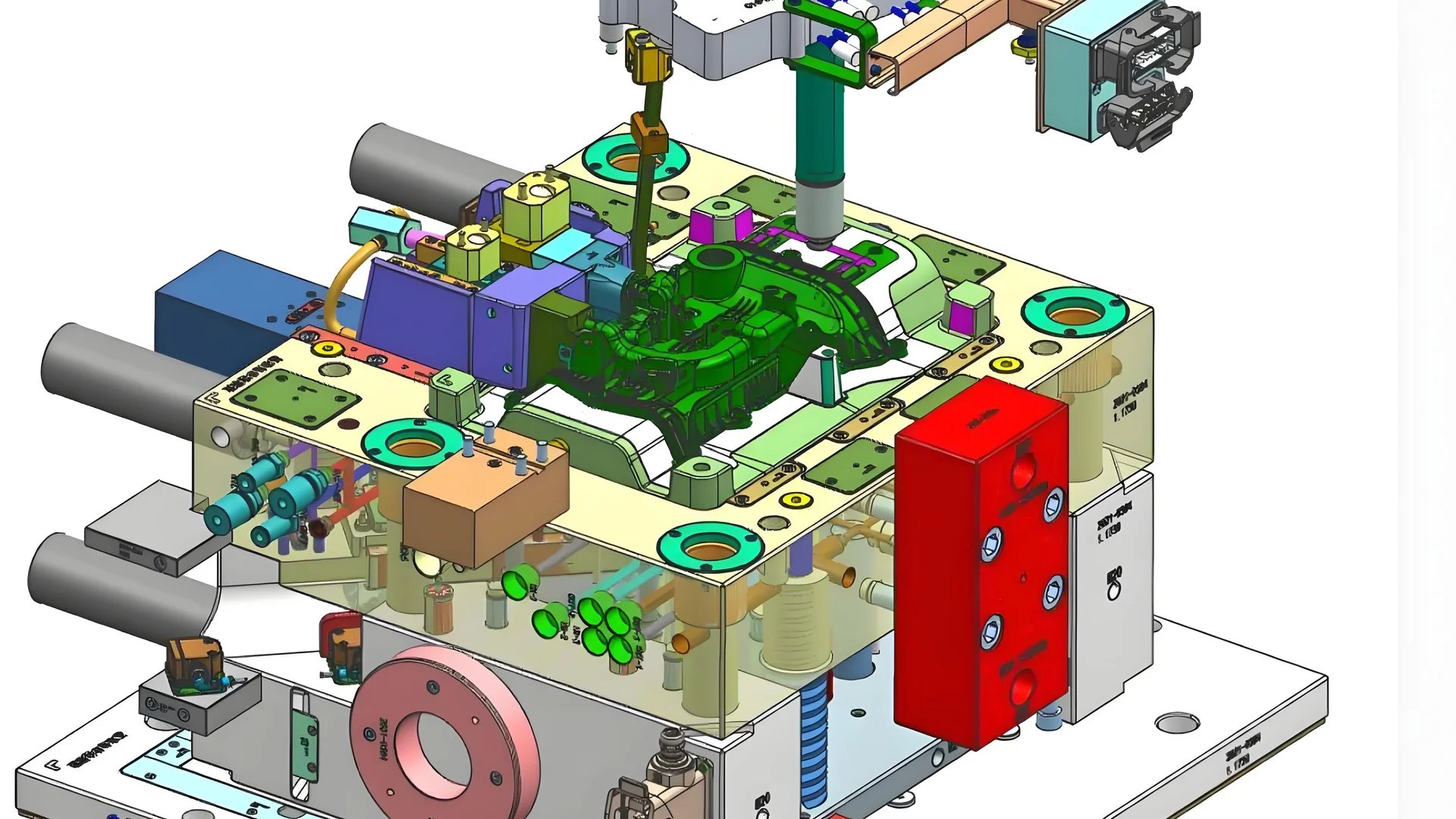
The Influence of Cavity Design
The cavity design is fundamental to mold design and directly influences the wall thickness of the final product. If the cavity is designed with uneven wall thickness, it can lead to parts of the product being too thick or too thin. This often happens in complex-shaped products where certain areas are inadvertently designed with more material than necessary.
To address this, engineers should utilize flow simulation software to optimize the mold design1 before manufacturing. This ensures that wall thickness is evenly distributed throughout the product, reducing the likelihood of defects.
Importance of Gate Positioning
The position of the gate, through which molten plastic enters the mold cavity, is another critical aspect. Improper gate placement can lead to uneven distribution of material. For instance, if the gate is positioned too close to a specific section, that area may become thicker as it fills first.
Using multiple gates or latent gates can help achieve a more uniform distribution by balancing the flow of plastic across the cavity. This approach minimizes areas of excess or insufficient material.
Manufacturing Accuracy Matters
Accurate manufacturing is essential to maintain consistent wall thickness. During the mold creation process, any errors—whether from tool wear or assembly inaccuracies—can lead to deviations in cavity dimensions. These small errors can accumulate, resulting in uneven wall thickness in the final product.
Employing high-precision CNC machines and regularly checking tool integrity can mitigate these issues. Moreover, ensuring tight tolerances during mold assembly will also contribute to consistent product quality.
Conclusion
In summary, mold design intricately affects wall thickness through various factors such as cavity design, gate positioning, and manufacturing precision. Each component must be meticulously designed and executed to achieve a high-quality product. By focusing on these areas, manufacturers can significantly improve their injection molding outcomes.
Cavity design affects wall thickness uniformity.True
Cavity design directly influences wall thickness by determining material flow.
Gate positioning has no impact on wall thickness.False
Improper gate placement can lead to uneven material distribution.
What Role Does Injection Pressure Play in Wall Uniformity?
Injection pressure is a pivotal factor in determining the uniformity of wall thickness in molded products.
Injection pressure affects wall uniformity by influencing plastic flow in the mold cavity. High pressure can cause overfilling and thick walls, while low pressure risks underfilling and thin walls. Consistent pressure ensures even distribution of material.
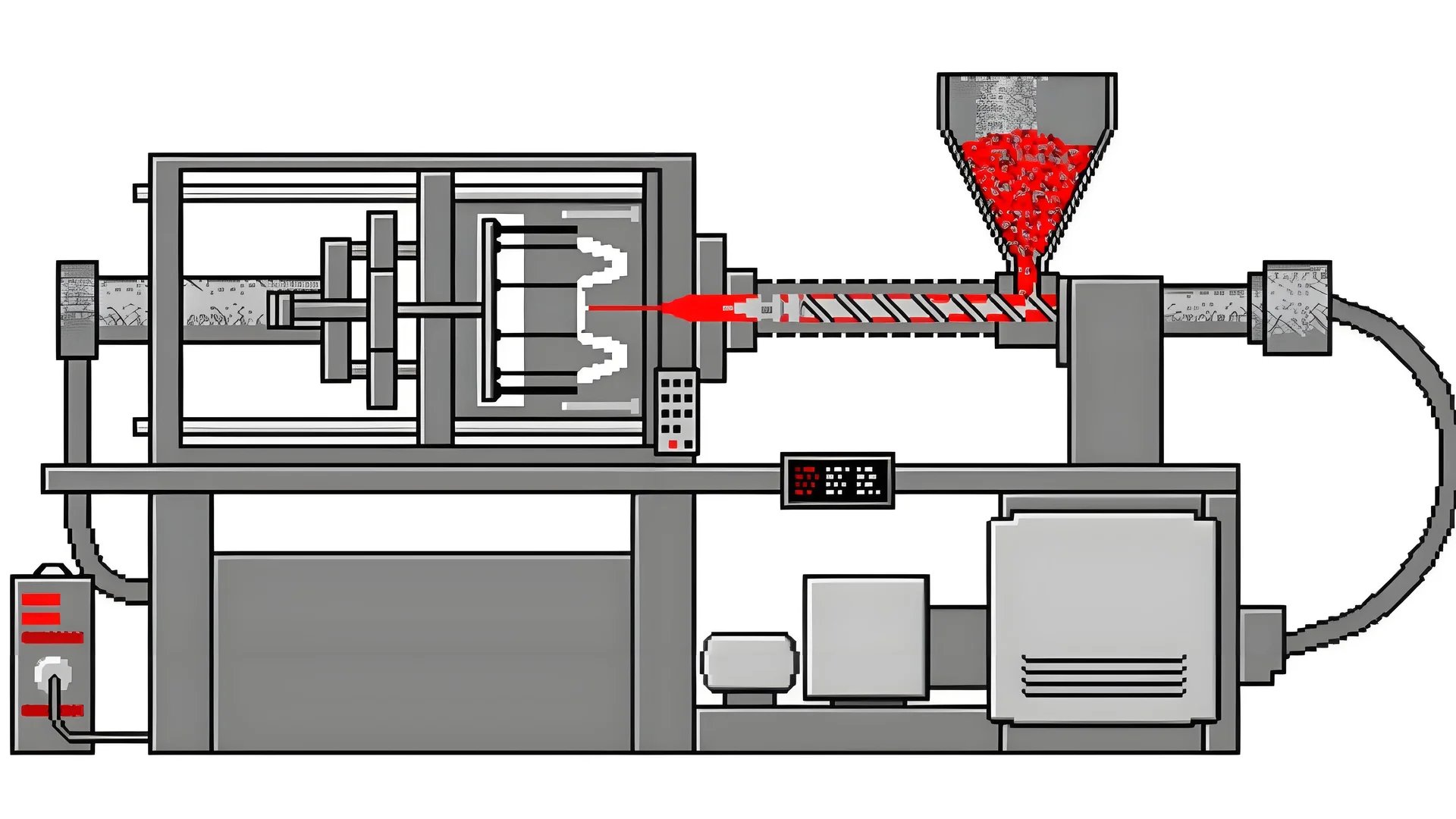
Understanding Injection Pressure
Injection pressure is the force exerted by the injection molding machine to push molten plastic into the mold cavity. The consistency of this pressure is vital for achieving uniform wall thickness.
How Pressure Affects Wall Thickness
-
High Injection Pressure: When the pressure is excessively high, the plastic flows too rapidly, potentially leading to overfilling. This can increase wall thickness in areas close to the gate where material enters. Over time, this may cause defects like warping or stress marks.
-
Low Injection Pressure: Conversely, insufficient pressure might not fully fill the cavity, resulting in thinner walls and even incomplete parts. This can compromise the structural integrity of the final product.
Stabilizing Injection Pressure
-
Monitoring Systems: Incorporating real-time monitoring systems, such as pressure sensors, helps maintain consistent pressure throughout the injection process. These systems can detect fluctuations and allow for immediate adjustments.
-
Hydraulic System Maintenance: Regular maintenance of the machine’s hydraulic system ensures it functions correctly, minimizing the risk of pressure drops or spikes.
Practical Example: Injection Pressure Calibration
Consider a scenario where you’re producing a plastic casing with a target wall thickness of 2mm:
Step | Action | Expected Outcome |
---|---|---|
1 | Set initial pressure based on material specifications. | Initial filling of cavity. |
2 | Monitor using sensors for consistent pressure. | Detect and adjust for fluctuations. |
3 | Adjust pressure incrementally based on wall thickness measurements. | Achieve target uniformity across the part. |
Further Exploration of Injection Pressure2
Delving deeper into how injection pressure interacts with other variables, like temperature and mold design, can provide additional insights for fine-tuning the injection molding process.
By understanding and controlling injection pressure, manufacturers can significantly enhance product quality, ensuring that every product meets exact specifications and performs reliably.
High injection pressure causes overfilling.True
Excessive pressure pushes plastic too rapidly, leading to overfilling.
Low injection pressure ensures thick walls.False
Insufficient pressure results in underfilling, causing thinner walls.
Why Is Material Selection Crucial for Consistent Wall Thickness?
Choosing the right material is pivotal in achieving consistent wall thickness in injection molding, directly impacting product reliability and performance.
Material selection is crucial for consistent wall thickness because different materials exhibit varying fluidity and shrinkage rates during the injection molding process. Selecting a material with suitable properties ensures uniform flow and cooling, minimizing thickness variations.
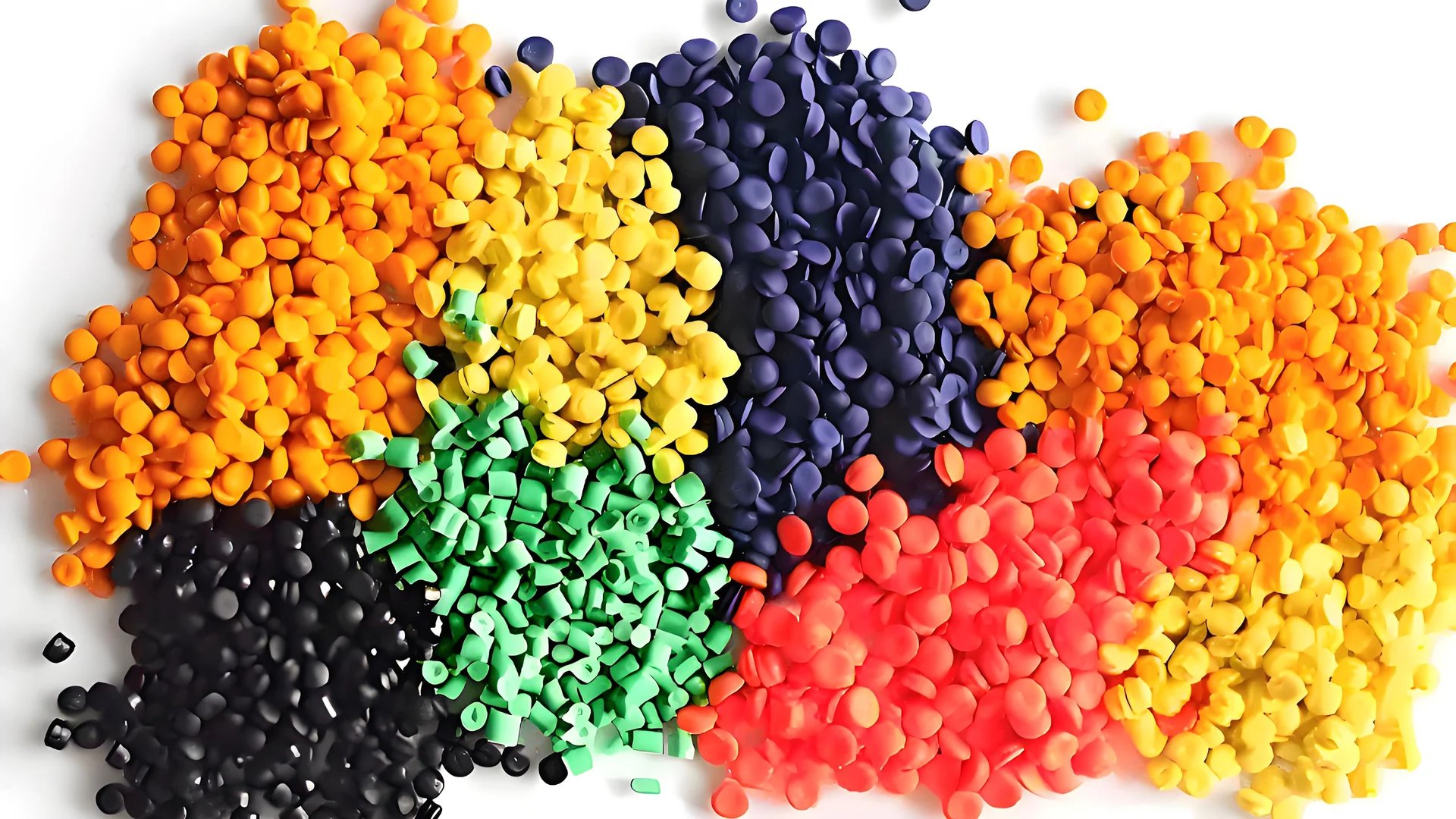
Understanding Material Fluidity
The fluidity of a material determines how easily it can fill a mold cavity. Materials with higher fluidity ensure even distribution throughout complex geometries, reducing the risk of uneven wall thickness3. Conversely, materials with low fluidity may struggle to reach all areas of the mold, leading to inconsistent thickness.
For instance, amorphous plastics like ABS (Acrylonitrile Butadiene Styrene) typically possess higher fluidity compared to semi-crystalline plastics such as PP (Polypropylene). Choosing a plastic with optimal fluidity for the product’s design ensures a smoother flow and uniform wall distribution.
The Role of Material Shrinkage
Different materials shrink at different rates as they cool. This characteristic can significantly influence wall thickness if not accounted for in the mold design and material choice. Selecting materials with minimal shrinkage can prevent post-molding deformities, ensuring a consistent thickness across the product.
For example, materials like nylon have higher shrinkage rates than polystyrene. Therefore, understanding the shrinkage properties of potential materials is essential for maintaining uniform wall thickness.
Moisture Content and Its Impact
Moisture within plastic materials can vaporize during molding, leading to defects such as bubbles or voids that compromise wall thickness consistency. Proper drying of materials like polycarbonate and nylon is crucial before injection molding to maintain the integrity and uniformity of the finished product.
Leveraging Modified Plastics
Using modified plastics can be beneficial when standard plastics do not meet the specific requirements for wall thickness consistency. Reinforced or flame-retardant plastics can offer enhanced performance and stability. For products requiring special attributes, these modifications can provide the necessary properties without sacrificing wall thickness uniformity.
Selecting the right material involves considering factors such as fluidity, shrinkage, moisture sensitivity, and any specific performance requirements. A thorough analysis of these properties, possibly in consultation with suppliers or through material testing, is essential for achieving consistent wall thickness in injection molding processes.
Amorphous plastics have higher fluidity than semi-crystalline plastics.True
Amorphous plastics like ABS flow better in molds compared to PP.
Material shrinkage does not affect wall thickness consistency.False
Different shrinkage rates can lead to uneven wall thickness post-molding.
How Can Process Adjustments Improve Wall Thickness Consistency?
Achieving consistent wall thickness in injection molding is key to maintaining product quality and reliability.
Process adjustments such as stabilizing injection pressure, optimizing injection speed, and adjusting holding time and pressure are crucial for improving wall thickness consistency in injection molded products. These adjustments help control the flow and cooling of materials, ensuring uniformity throughout the product.
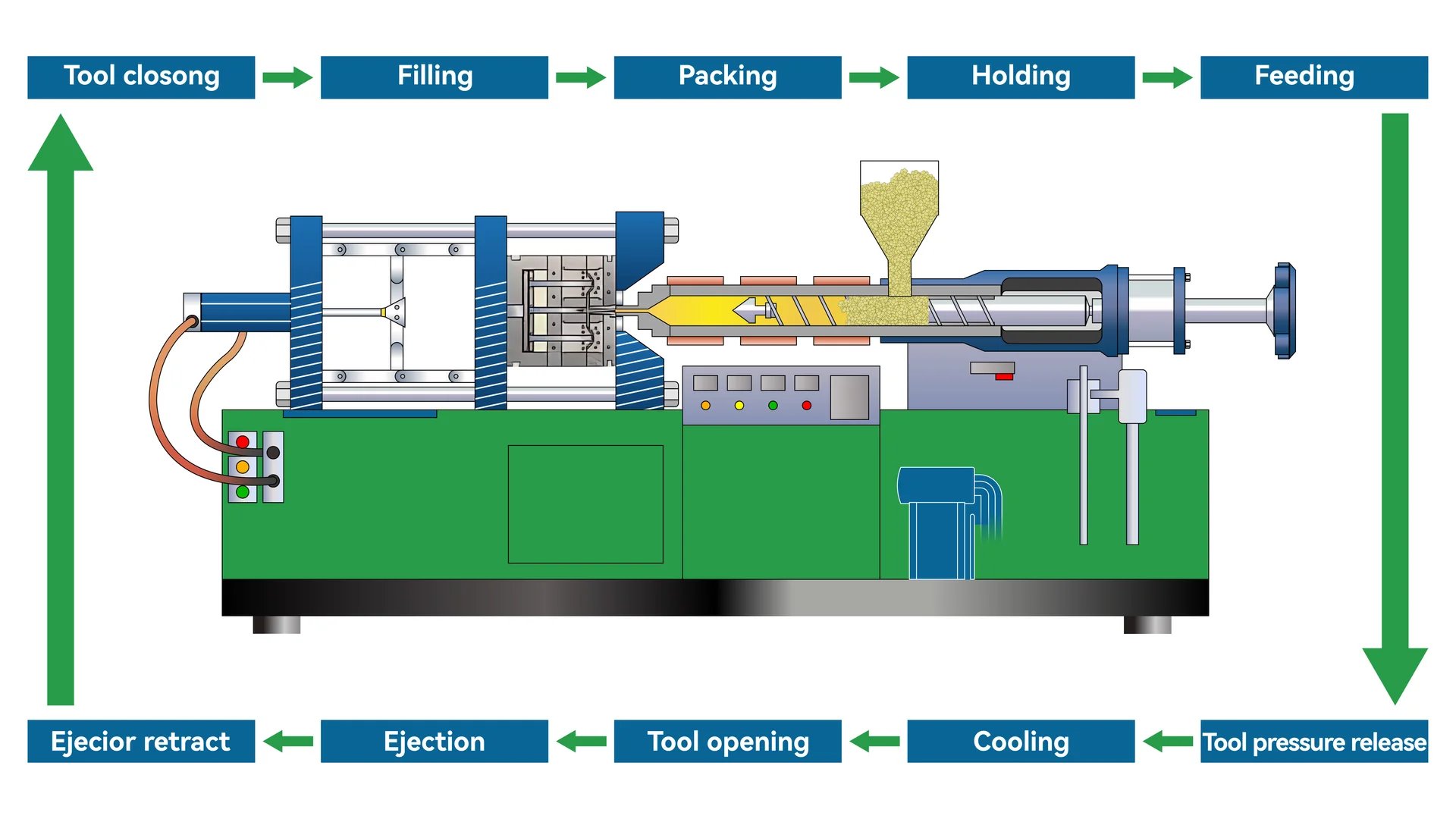
The Impact of Injection Pressure
Stabilizing injection pressure is paramount in achieving uniform wall thickness. Fluctuations in pressure can lead to uneven material flow, causing variations in wall thickness. Regular checks of the hydraulic system can ensure stability. Employing pressure sensors aids in real-time monitoring, allowing for timely adjustments to maintain consistent filling across the mold.
- For thin-walled sections, a moderate reduction in pressure can prevent overfilling.
- In thicker areas, increased pressure might be necessary to ensure adequate filling.
Optimizing Injection Speed
The speed at which material is injected into the mold significantly influences its distribution and cooling. An optimized speed ensures the plastic flows evenly, minimizing risks of defects like spraying or voids.
- Fast speeds enhance fluidity for thin-walled products, while slower speeds are preferable for thicker sections to prevent issues like spraying.
- Implementing multi-stage speed control allows for tailored flow dynamics at different stages of the molding process.
Holding Time and Pressure Adjustments
The settings for holding time and pressure are crucial in the cooling phase of molding. Proper adjustments can prevent defects caused by shrinkage or overfilling.
- Conduct experiments to determine optimal holding times based on product dimensions and material shrinkage rates.
- Gradually reducing holding pressure during cooling helps avoid overfilling, ensuring precise wall thickness.
Benefits of Material Selection and Processing
While primarily focused on process adjustments, the choice of materials plays a supporting role in achieving uniformity. Selecting materials with excellent flow characteristics and ensuring they are properly dried pre-molding is essential.
- Refer to technical data sheets4 from material suppliers to choose the best fit for your product’s requirements.
- Use dryers or ovens to eliminate moisture from hygroscopic materials like nylon, as moisture can lead to irregularities in wall thickness.
Stabilizing injection pressure ensures uniform wall thickness.True
Consistent pressure prevents uneven flow, achieving uniform thickness.
Faster injection speeds are ideal for thicker sections.False
Slower speeds are better for thicker sections to avoid defects.
Conclusion
In summary, mold design intricately affects wall thickness through various factors such as cavity design, gate positioning, and manufacturing precision. By focusing on these areas, manufacturers can significantly improve their injection molding outcomes.
-
Discover tools and techniques for achieving even wall thickness.: It is better to modify the geometry of a part to eliminate thick sections rather than design special cooling for the thick sections to prevent … ↩
-
Understand how pressure interacts with material flow for better mold design.: Three, high injection pressure can force the mold open at the parting line. This creates flashing on the part, but more importantly, it can … ↩
-
Learn how material fluidity affects product consistency in injection molding.: The fluidity of plastic molding material refers to the ability of plastic materials to flow within the injection mold in the manufacturing of plastic products. ↩
-
Access detailed specifications to select materials that suit your product’s needs.: The standard material data sheet consists almost entirely of performance characteristics measured at room temperature. In addition, the performance … ↩