Ever thought about how a small design change might completely change your injection molding process?
The design of the main channel in injection molds is very important for efficiency. A cone shape reduces resistance to the melt flow. The correct size keeps the flow rate perfect. Short runners lower pressure loss. The position of the main channel allows for even distribution. This improves injection efficiency. Efficiency indeed improves.
When I first explored mold design, I felt surprised by how a small part, like the main channel, affected everything. The main channel serves as a highway for melted plastic. Its shape and path decide how easily it all moves. In one of my early projects, I struggled with a badly shaped channel. It led to many flow problems, like traffic jams during rush hour! Changing to a cone-shaped design fixed everything. This increased efficiency a lot.
Shape is important, but size is crucial, too. Think of squeezing people through a tiny gate. If it’s too narrow, it blocks or else it gets wild. The runner’s length and place also matter. I discovered this harsh lesson on a tight schedule when a too-long runner led to big pressure drops and longer injection times.
Next time you’re designing or adjusting a mold, focus on that main channel. It might really change your project!
Conical channel shape reduces melt flow resistance.True
A conical shape in the main channel design reduces resistance, improving flow.
Longer runners increase pressure loss in molds.True
Long runners create more friction, leading to higher pressure loss.
- 1. How Do the Shape and Size of the Main Channel Impact Functionality?
- 2. Why Is Main Runner Length Critical for Efficiency?
- 3. How does runner position and layout influence mold performance?
- 4. How does the main runner connect with nozzle design?
- 5. How can these design principles be applied in real-world scenarios?
- 6. Conclusion
How Do the Shape and Size of the Main Channel Impact Functionality?
Do you ever think about why the shape and size of a channel are important? Let me guide you through this interesting subject!
The shape and size of the main channel really matter for better flow dynamics. A cone-like design with exact measurements cuts down on resistance. This design helps the flow move smoothly, especially in processes such as injection molding. A conical shape means you probably get better flow. Precise sizing means smoother transitions. Really smooth.
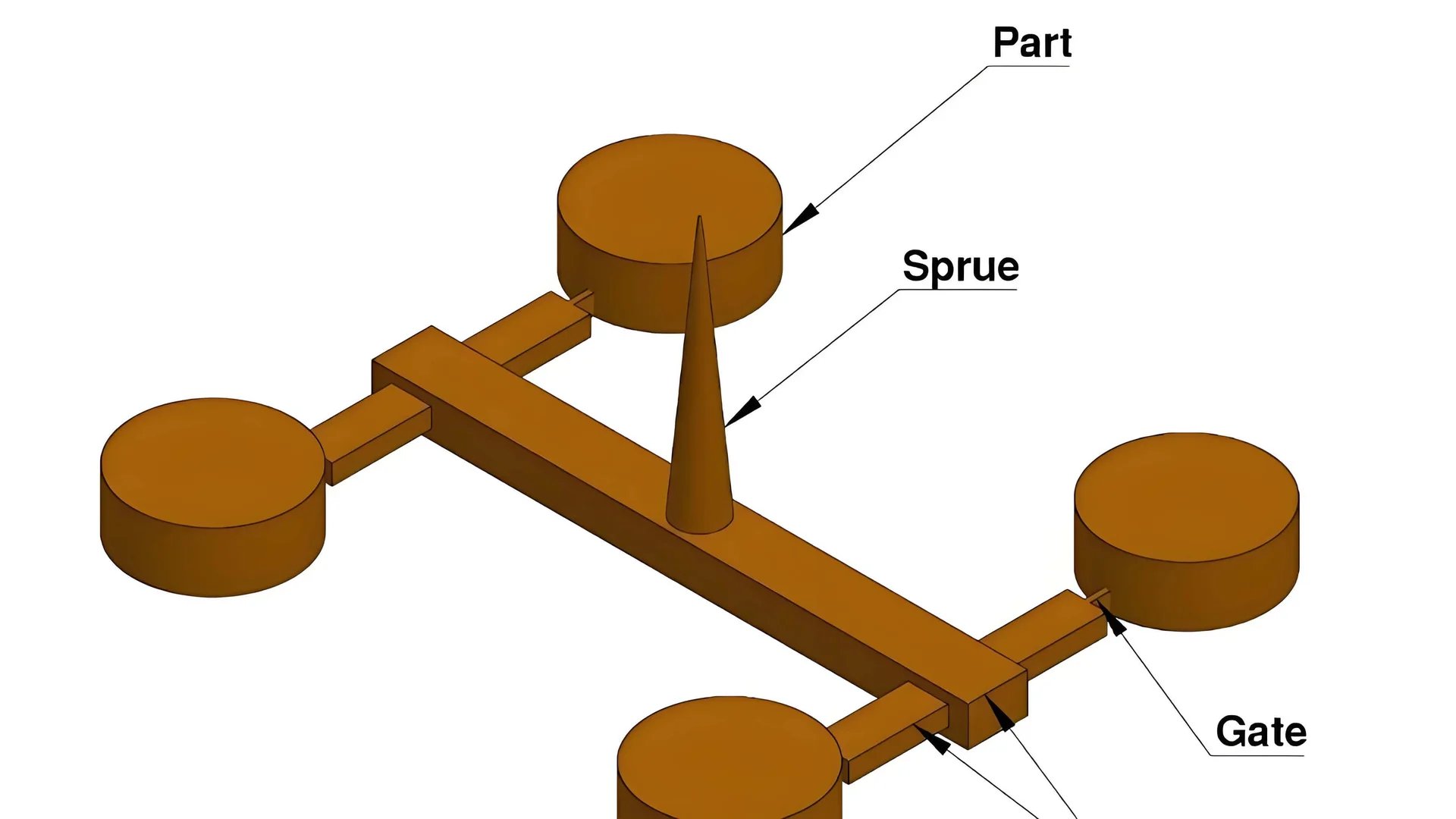
Shape’s Influence on Flow
Picture being on a long drive, gliding along a smooth highway. The ride is pleasant. Now think about a rough, twisty back road. That’s like what a cone-shaped main channel does for flow. It makes the journey easy for things like plastic melts. I learned this early in my mold factory days. A conical shape lowers resistance and stops those annoying whirlwinds that slow things down. Irregular shapes cause trouble, like hitting a pothole. Nobody wants that!
Table: Shape’s Effect on Flow
Shape | Impact |
---|---|
Conical | Smooth transition, reduced resistance |
Irregular | Increased resistance, potential stagnation |
Size is Important
I recall a project where I adjusted the main channel’s diameter. It was crucial. A tiny mistake leads to problems. The small end should be 0.5-1mm larger than the nozzle for a good flow, much like choosing the right straw1 for your drink – not too small, not too big.
- Small End Diameter: 0.5-1mm larger than the nozzle.
- Chamfer Design: Assists smooth material movement.
Position and Layout Considerations
I’ve seen designs with incorrectly placed channels causing uneven flow. Imagine pouring juice from one pitcher to many glasses – if your aim is off, some glasses get more juice than others. Channels must align with the mold’s center for smooth, even flow.
The layout should effectively distribute materials across multiple cavities to prevent blockages or uneven distribution.
Once, my team faced an uneven flow problem; better planning avoided it.
Length and Pressure Impact on Heat Loss
I always go for shorter channels as they save pressure and reduce heat loss—like inflating a tough balloon; longer channels require much pressure and are less efficient.
Channel and Nozzle Interface Matching
Matching the main channel with the nozzle is akin to fitting puzzle pieces together—it must fit well to prevent leaks or uneven flow.
Correct depth and radius measurements enhance efficiency:
- Contact Depth: Usually 3-5mm.
- Gate Sleeve Radius: 1-2mm larger than the nozzle’s radius.
Precision matters in channel design2, impacting both flow efficiency and overall performance across various applications in manufacturing or biological systems.
Curious minds might explore how these principles apply3 across different fields.
Conical channels reduce flow resistance.True
Conical designs guide materials smoothly, minimizing resistance and preventing vortices.
Irregular channel shapes enhance flow efficiency.False
Irregular shapes increase resistance and can lead to stagnation, hindering flow efficiency.
Why Is Main Runner Length Critical for Efficiency?
Ever wondered why the length of the main runner in mold design matters so much? I really did when I first entered the world of injection molding.
The primary runner length is crucial for efficiency. It affects pressure loss, heat retention and flow distribution. Shorter runners decrease resistance and cut heat loss. This really improves injection efficiency.
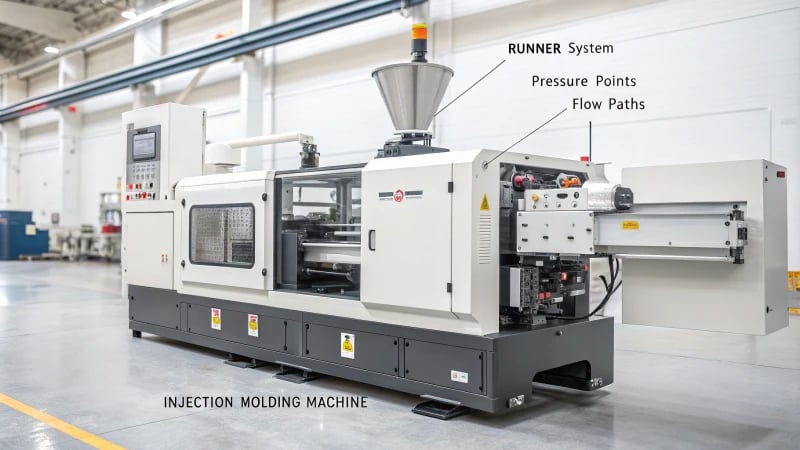
The Role of Main Runner Length
I remember the first time entering a mold design meeting. It felt like joining a secret club. People talked about runner lengths and efficiency, while I tried to catch up. Soon, I realized the main runner is like a highway for molten material. It guides it from the nozzle to the mold cavity. Length involves more than distance; it affects how smoothly material moves. Less resistance and pressure loss occur with a shorter runner. Shorter runners consume less energy, boosting overall efficiency4.
Heat Retention and Flow Dynamics
Chilly mornings in the shop taught me not to lose heat with molten material. Longer runners remove heat, cooling the material, which affects its fluidity5. Fluidity is vital as it allows every mold corner to fill without defects.
Influence on Injection Efficiency
Efficiency means everything in mold design. I’ve watched shorter runners transform operations by reducing melt resistance and heat loss. The process resembles a well-oiled machine: less energy consumption, faster fill times, and reduced equipment wear.
Shape and Size Considerations
Shape and size matter for efficiency. The main runner needs the right fit—not too loose or too tight. Conical shapes are often used as they let molten material flow smoothly, avoiding troublesome vortices that disrupt efficiency6.
Positional Layout Impacts
Placement means all—my mentor always said this. The runner must sit right; symmetrical placement helps distribute material evenly across the mold. An off-center runner disrupts everything, causing uneven fills and reducing product quality.
Contact Point Design
I once spent hours tweaking the contact point between the main runner and injection machine nozzle. A perfect fit prevents leaks and ensures smooth transition into the runner through precise matching of contact dimensions7. This minor detail is crucial for maintaining operational efficiency.
Factor | Impact on Efficiency |
---|---|
Runner Length | Affects pressure loss and heat |
Runner Shape & Size | Influences flow resistance |
Positional Layout | Ensures even melt distribution |
Contact Point Design | Prevents leaks and uneven flows |
Understanding these details has been key in optimizing our runner designs for enhanced efficiency without losing quality or production speed.
Shorter main runners reduce pressure loss.True
Shorter runners decrease the distance for melt travel, minimizing pressure loss.
Longer main runners enhance heat retention.False
Longer runners increase heat loss, lowering melt temperature and fluidity.
How does runner position and layout influence mold performance?
Ever thought about why some plastic pieces turn out perfect while others don’t? It probably depends on how the runner system works in injection molding.
Runner position and layout deeply influence how a mold performs. These aspects affect where and how melt flows, how long it takes to fill and how much pressure is lost. A perfect setup leads to even filling. It shortens cycles. It also results in better quality products. Better products!
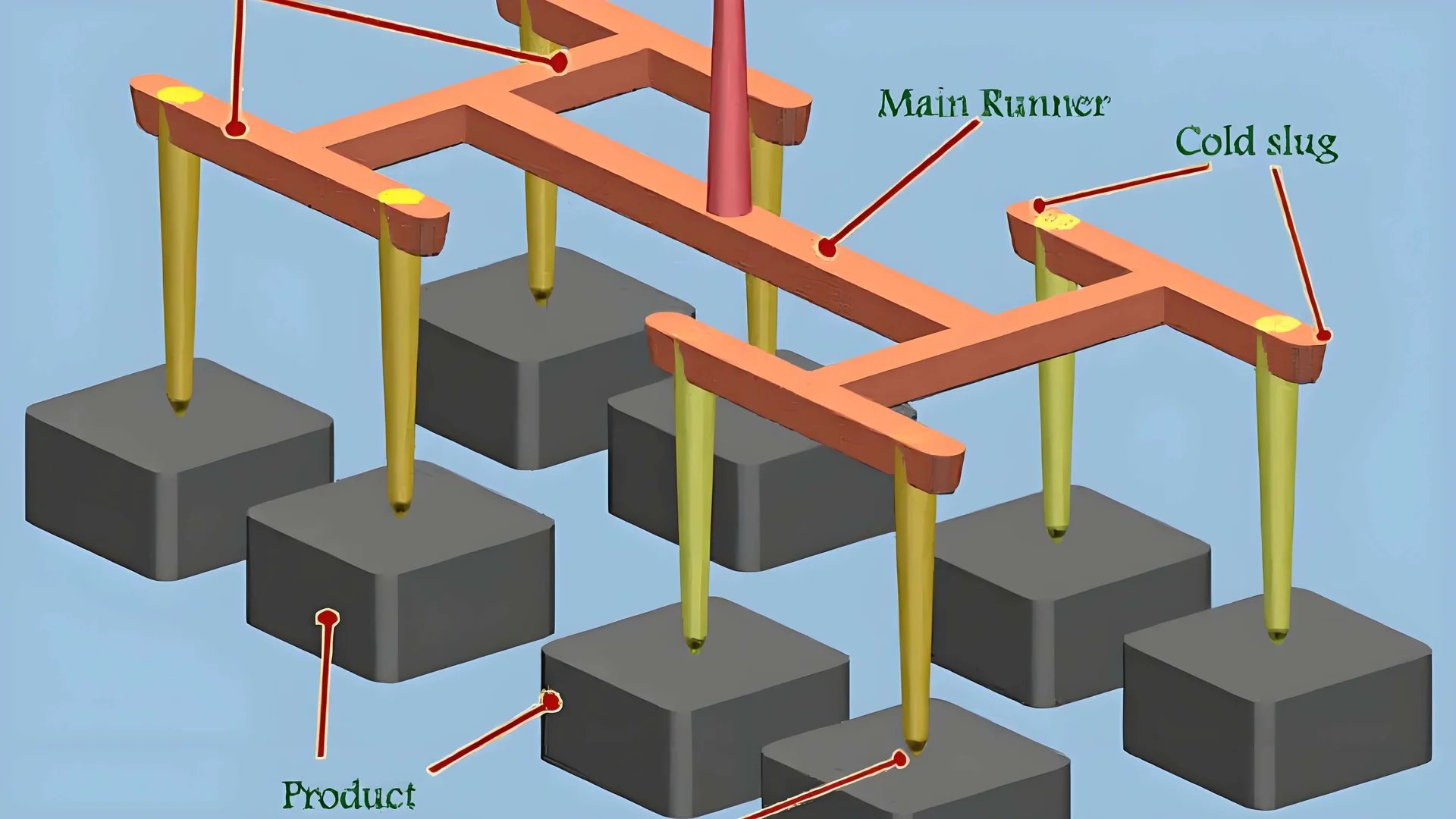
The Importance of Runner Position
The runner’s position is very important, like setting the stage for a great show. The main runner should be at a straight angle to the mold’s parting surface. This way, the melt spreads evenly and does not hit small cores or inserts directly. In a past project, I positioned the runner a bit off-center. The result was uneven filling in cavities, which was a costly mistake. Very costly.
Incorrect positioning may cause uneven filling of cavities, impacting the mold’s overall performance8. If the runner deviates from the center line, certain cavities may fill faster than others, leading to inconsistencies.
Runner Layout Design
The runner layout design is similar to planning a road trip. The journey should be smooth, with little resistance, to reach each cavity. In molds with many cavities, when the design is wrong, blockages occur, causing the melt to spread inefficiently. Adjusting this feels like untangling holiday lights, but the joy comes when everything works correctly!
Consider a layout that minimizes resistance while ensuring each cavity receives an equal amount of melt. This involves smooth transitions between the main and branch runners to prevent blockages.
Influence of Runner Shape and Size
Runner shape and size are as crucial as choosing the right hiking gear. A conical runner shape gently guides the melt, lowering resistance.
Shape Influence | Size Influence |
---|---|
Conical shapes reduce resistance. | Diameter affects flow rate. |
Irregular shapes disrupt flow – like potholes on a highway. | Too small diameter limits flow rate. |
Reflecting on this, we see that a slightly larger diameter than the nozzle helps smooth flow, like widening a path for easier passage.
Managing Runner Length
Main runner length is like measuring a sprint distance: shorter is usually better. A longer runner feels like running uphill with more resistance and pressure loss.
Long runners increase heat loss and require higher injection pressure and longer cycle times. Design runners to be as short as feasible without compromising layout efficiency.
Integration with Injection Machine Nozzle
The main runner and nozzle connection is vital—like fitting a jar lid tightly.
Good Fit | Poor Fit |
---|---|
No leaks or uneven spray during melt entry. | Melt overflow or entry issues requiring adjustments. |
Smooth transition from nozzle to runner. | Requires parameter adjustments or redesign. |
A snug fit stops leaks and uneven spray when the melt enters.
I faced a situation with a poor fit that needed many adjustments; it felt like finding that elusive puzzle piece.
A well-planned runner design greatly impacts smooth operation and high-quality output in plastic production processes.
Consideration for Multi-Cavity Molds
In multi-cavity molds, equal distribution is essential—like making sure each guest at a party gets a piece of cake.
An effective layout ensures even filling and avoids problems like different shrinkage or warping.
Those exploring mold design should really grasp these runner parameters9. Understanding them helps optimize mold performance in many production settings.
Runner position impacts mold cavity filling.True
Incorrect runner positioning leads to uneven cavity filling, affecting performance.
A smaller runner diameter increases flow rate.False
A smaller diameter limits flow rate, requiring higher pressure for efficiency.
How does the main runner connect with nozzle design?
Have you ever thought about how a small change in design transforms your injection molding process? The bond between the main runner and nozzle design reveals incredible efficiency.
The main runner and nozzle design matter a lot in injection molding. The shape and size of the runner affect how the plastic melts flow. The fit of the nozzle impacts how well the injection works. Good designs help plastic flow smoothly. This smooth flow reduces defects. Fewer defects mean better products.
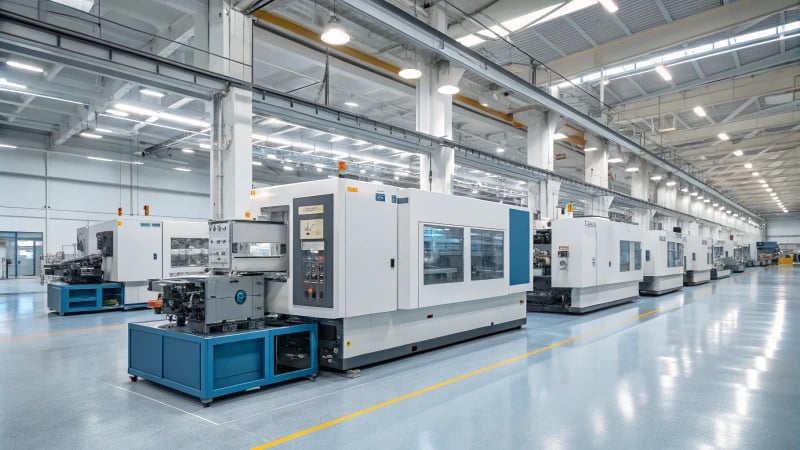
How Shape and Size Influence Melt Flow
I remember working on a project where a small change in the main runner’s shape changed everything. The shape truly matters. A cone shape, for example, smoothly guides melted plastic from the nozzle into the mold. It’s like pouring water through a funnel. When the shape is too irregular, you get spirals and stuck flows.
- Size Considerations: I learned this the hard way. If the small end diameter isn’t correct, the flow gets blocked or space gets wasted. It should ideally be 0.5-1mm larger than the nozzle.
Parameter | Recommended Size | Impact |
---|---|---|
Small End Diameter | 0.5-1mm larger than nozzle | Ensures adequate flow |
Impact of Main Runner Length
Length matters. A shorter main runner lowers resistance and pressure loss. Imagine trying to push a thick milkshake through a straw. Longer runners steal heat and fluidity, affecting performance.
- Runner Positioning: Keeping it perpendicular to the mold’s parting surface ensures even distribution. Slight deviations cause uneven fills, leading to problems with consistency.
Nozzle Fit and Injection Efficiency
The nozzle’s meeting point with the main runner is like a handshake. It needs to be just right to stop leaks. Consider depth and radius; getting them wrong creates a mess.
- Contact Point Design:
- Hemispherical pit depth should be 3-5mm.
- Gate sleeve radius needs to be 1-2mm larger than nozzle radius.
For more details on contact point design, explore this detailed guide10. Understanding these parts is crucial for better injection efficiency.
Exploring these elements of main runner and nozzle design really helps improve plastic injection processes, reducing defects and increasing production efficiency. Every detail matters—really! Trust me, I’ve been there, dealing with small tweaks that significantly change manufacturing outcomes.
A conical runner shape reduces melt flow vortices.True
A conical design guides plastic smoothly, minimizing flow disturbances.
Long runners decrease injection time efficiency.False
Long runners increase heat loss, impacting fluidity and time.
How can these design principles be applied in real-world scenarios?
Design principles are not just abstract ideas. They add a special touch to projects. These principles help projects come alive. They really connect with people. Truly connect.
To use design rules well in real situations, begin by matching them with your project’s main goals. Each part of the design should serve a purpose and look nice. Feedback and repeated testing help improve the work. Focus on both function and look to optimize it.
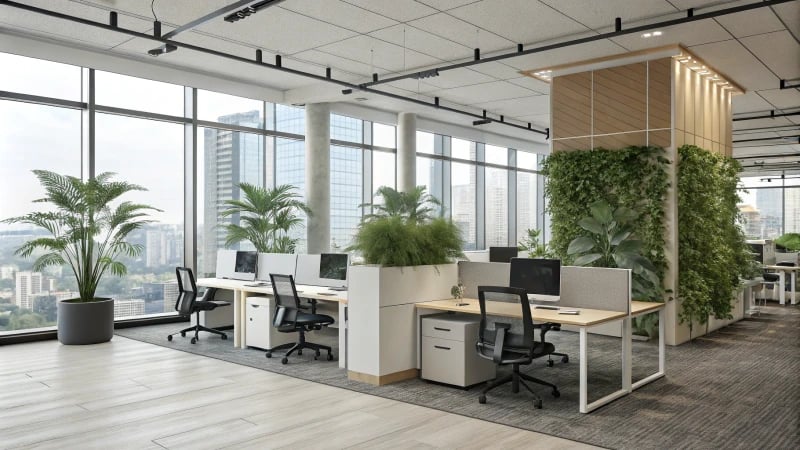
Understanding the Main Goals
Every project I work on starts with knowing the main goals. Whether creating a smooth product mold11 or improving a digital interface, matching these goals with design rules is very important. For example, when I designed a new phone case, knowing the trade-off between strength and looks was crucial.
Shape and Size Importance
I learned that shape and size are very important in design. The shape of a mold’s channel really matters. It is conical to guide material smoothly, reducing resistance. Once, I changed the end diameter by just a millimeter and saw flow efficiency rise significantly. Consider using a table to map out ideal dimensions:
Component | Ideal Shape | Benefits |
---|---|---|
Main Channel | Conical | Smooth flow |
End Diameter | Slightly larger than nozzle | Efficient flow |
Position and Layout Setting
Setting elements in the right position is like arranging a stage perfectly. Everything has to be just right. In multi-cavity molds, symmetry and correct layout really improve material delivery. There was a time I had to adjust the layout many times to get the best results.
Practical Feedback Loops
Feedback is crucial for fixing designs. I usually use tests repeatedly to get feedback12 on a design’s performance in real-life settings. It’s like tuning an instrument until it plays the right note.
Real-World Use in Product Design
In product design, usability and access are more than just words – they are basic ideas. A simple navigation system in a digital product really changes user experience. A mold’s good efficiency increases speed in production.
Industry-Specific Changes
Various industries need special changes in these ideas. In architecture, the environment is a big focus, making us search for sustainable materials and technologies. These thoughts keep designs not just useful but likely ready for the future.
Using design ideas in different areas shows their strength and adaptability. By always testing and getting feedback, we create solutions that work well and look nice.
For more info on using design thinking in different fields, look at resources on design thinking methodologies13.
Conical shapes reduce flow resistance in molds.True
Conical shapes guide material smoothly, reducing flow resistance effectively.
Symmetrical layouts hinder material distribution.False
Symmetrical layouts enhance efficient distribution of materials in designs.
Conclusion
The design of the main channel in injection molds significantly impacts efficiency, with shape, size, length, and layout affecting melt flow and overall production quality.
-
Explore why conical shapes enhance flow efficiency in injection processes. ↩
-
Learn why precise design is critical for channel functionality. ↩
-
Discover how these design principles apply across different domains. ↩
-
Understanding how runner length impacts melt resistance helps in designing more efficient molds. ↩
-
Fluidity is key to ensuring that molds are filled correctly without defects. ↩
-
Exploring how irregular shapes affect flow can help avoid common pitfalls in mold design. ↩
-
Effective contact points prevent leaks and maintain efficient material flow into molds. ↩
-
Explore how precise runner positioning improves even melt distribution and prevents defects. ↩
-
Discover detailed methods to enhance mold design efficiency through optimal runner layout. ↩
-
Discover best practices in designing contact points for nozzles to improve efficiency. ↩
-
Discover detailed specifications for main channel designs that enhance material flow efficiency. ↩
-
Learn how iterative testing can lead to more efficient and effective design solutions. ↩
-
Explore methodologies that integrate design principles into real-world problem-solving scenarios. ↩