Bakelite isn’t just any plastic; it’s a legend in its own right!
The Bakelite injection molding process involves preparing phenolic resin, designing and preheating molds, injecting and curing the plastic, followed by demolding and post-processing. This method ensures high-quality, precise products by adhering to detailed procedural steps.
To truly appreciate this intricate process, let’s dive deeper into each stage, from material preparation to final inspection. You might find some valuable insights that could enhance your own production experience!
Phenolic resin is a thermoplastic used in Bakelite molding.False
Phenolic resin is a thermosetting plastic, not a thermoplastic.
What Are the Key Materials Used in Bakelite Injection Molding?
Understanding the materials used in Bakelite injection molding is crucial for ensuring optimal product quality and performance.
The primary material in Bakelite injection molding is phenolic resin, a thermosetting plastic known for its high heat resistance and electrical insulating properties.
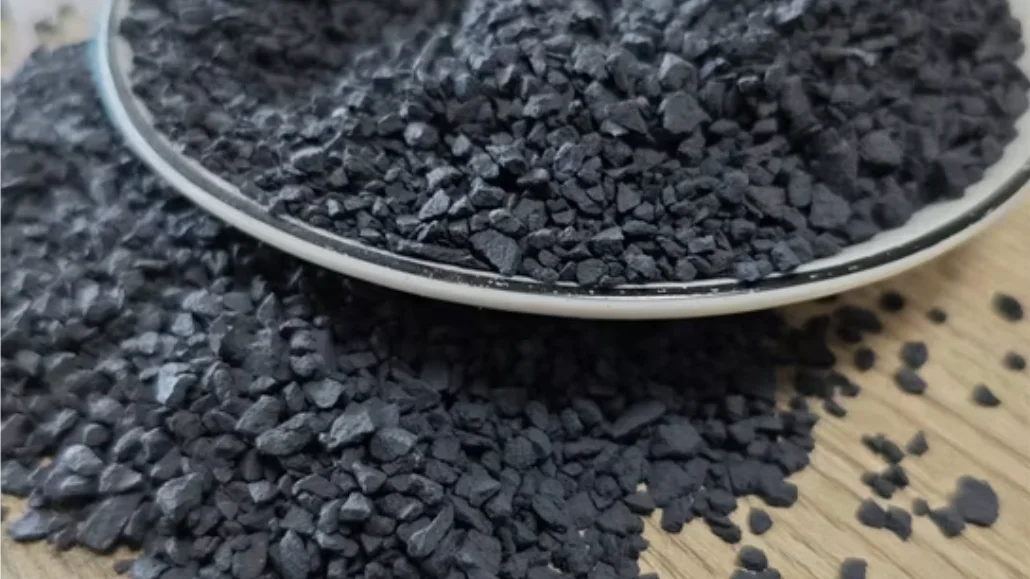
Understanding Phenolic Resin
Phenolic resin is the cornerstone of Bakelite injection molding. This thermosetting plastic is renowned for its durability, heat resistance, and excellent electrical insulating properties. Unlike thermoplastics, phenolic resin does not melt upon reheating; instead, it cures, forming a rigid structure that remains stable under high temperatures. This characteristic makes it ideal for applications requiring heat resistance and dimensional stability.
Other Essential Materials
- Fillers: To enhance specific properties of the molded product, fillers such as wood flour, cotton, or glass fibers are often added to phenolic resin. These fillers can improve mechanical strength, reduce weight, or modify electrical properties.
- Curing Agents: Phenolic resin requires curing agents to initiate the cross-linking process during molding. Common curing agents include hexamethylenetetramine (hexa) which helps in forming the final hardened structure.
- Lubricants: Lubricants like stearates are used to aid in the flow of material into the mold and ease the demolding process by reducing friction.
Additives for Enhanced Performance
- Colorants: Though Bakelite typically appears in brown or black, colorants can be introduced to achieve desired aesthetic qualities.
- Flame Retardants: Given its application in electrical components, adding flame retardants can provide extra safety by reducing flammability.
Quality and Stability Considerations
Ensuring the quality and stability of these materials is paramount. The phenolic resin must be free from impurities to avoid defects in the final product. Proper storage1 and handling protocols should be followed to maintain material integrity before use in molding.
Conclusion
Understanding the key materials used in Bakelite injection molding helps manufacturers optimize the production process and produce high-quality products. By selecting appropriate fillers, curing agents, and additives, manufacturers can tailor the properties of Bakelite to meet specific application requirements.
Phenolic resin is a thermoplastic.False
Phenolic resin is a thermosetting plastic, not thermoplastic.
Fillers enhance Bakelite's mechanical strength.True
Fillers like wood flour improve mechanical strength in Bakelite.
How Do You Design an Effective Mold for Bakelite?
Designing an effective mold for Bakelite requires precision and understanding of both material properties and product specifications.
To design an effective mold for Bakelite, consider the product’s shape, size, and precision requirements. Use high-quality phenolic resin, ensure proper preheating, and maintain precise temperature control during injection. These steps help achieve optimal results with minimal defects.
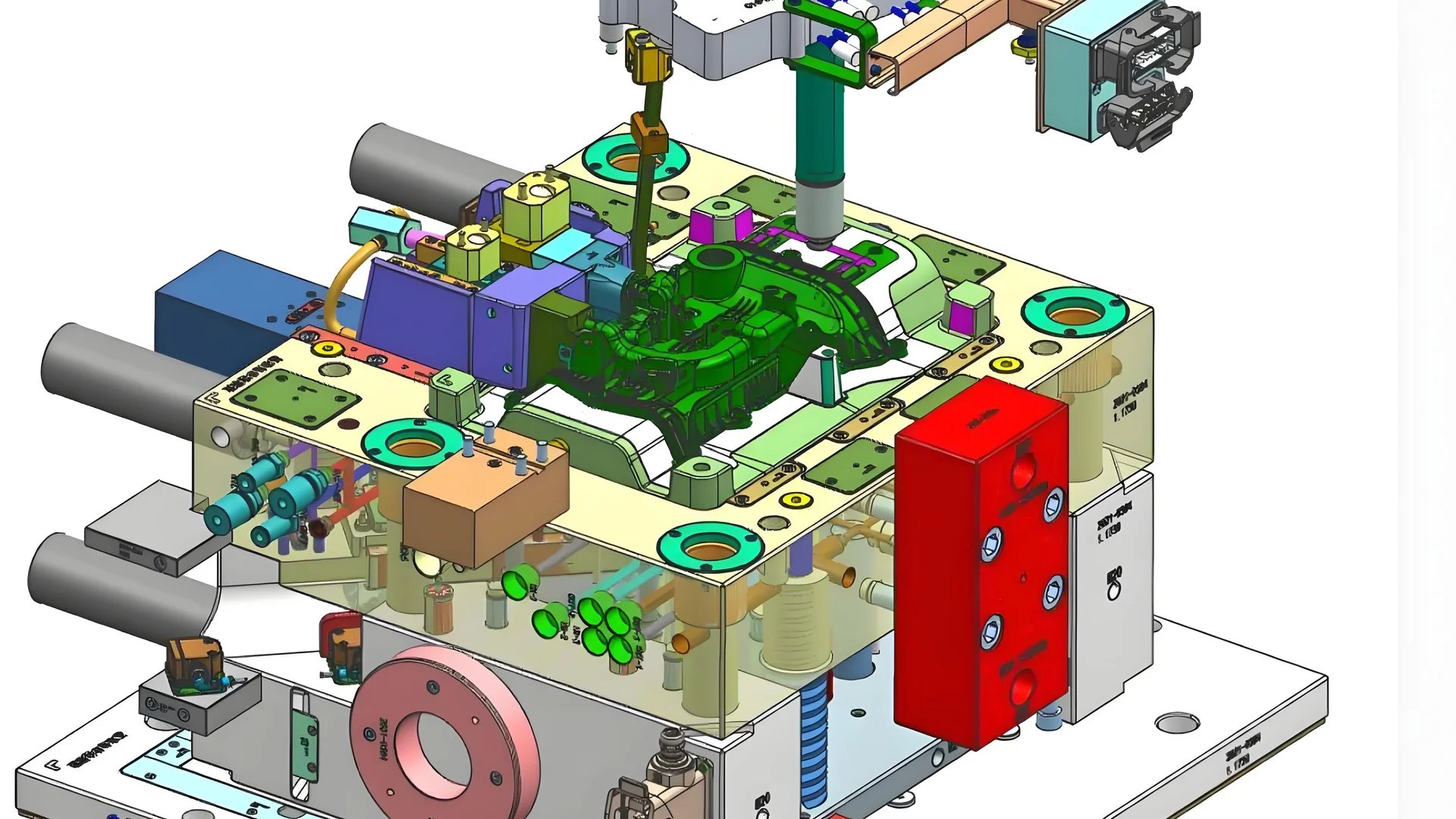
Understanding Bakelite Material Properties
Bakelite, a thermosetting plastic, is renowned for its heat resistance and electrical insulating properties. Understanding these characteristics is crucial in designing a mold that accommodates its behavior under heat and pressure.
Key Considerations in Mold Design
-
Shape and Size: The mold must accurately reflect the desired shape and dimensions of the product. This involves precise measurements and calculations to ensure uniformity across production.
-
Material Flow: Consider how the molten phenolic resin will flow through the mold. A well-designed flow channel2 minimizes air pockets and ensures even distribution of material.
-
Draft Angles: Including draft angles in the design facilitates easier removal of the product from the mold, reducing wear and tear on the mold surfaces.
The Role of Preheating
Preheating the mold to the correct temperature is essential. This step reduces curing time by ensuring that the Bakelite solidifies quickly upon injection. An effective preheating strategy enhances the mold’s lifespan by reducing thermal stress.
Temperature Control During Injection
Maintaining a stable temperature within the injection molding machine ensures the phenolic resin remains at the optimal viscosity for molding. It prevents defects such as warping or incomplete filling of the mold cavity.
Case Study: Precision Molding for Electrical Components
In manufacturing electrical components, precision is non-negotiable. A successful mold design for such applications often includes:
Feature | Importance |
---|---|
Uniform Wall Thickness | Prevents stress points and enhances structural integrity |
High-Precision Fit | Ensures compatibility with other components |
Durable Material | Withstands repeated thermal cycles |
By paying attention to these critical aspects, designers can create molds that not only produce high-quality Bakelite products but also optimize production efficiency. For further insights into improving mold longevity and efficiency, explore best practices in mold maintenance3.
Bakelite requires preheating before molding.True
Preheating reduces curing time and thermal stress on the mold.
Draft angles are unnecessary in Bakelite molds.False
Draft angles ease product removal and reduce mold wear.
What Are the Common Challenges in Bakelite Injection Molding?
Bakelite injection molding is a complex process with unique challenges that can impact product quality and efficiency.
Common challenges in Bakelite injection molding include material handling difficulties, mold design constraints, and controlling the curing process. Addressing these issues requires careful planning, precise equipment calibration, and skilled operation to ensure optimal results.

Material Handling Difficulties
Handling phenolic resin materials4 used in Bakelite injection molding presents specific challenges. These thermosetting plastics require precise temperature control during preheating to prevent premature curing, which can lead to clogs or inconsistencies in material flow. Additionally, ensuring the resin’s quality and stability is critical, as impurities or moisture can negatively impact the final product’s performance.
Mold Design Constraints
Designing an effective mold for Bakelite products involves overcoming several constraints. The mold must withstand high temperatures and pressures without deforming, which demands robust materials and intricate design features. Designing for precision while allowing for slight material shrinkage during curing is crucial. Moreover, the mold must facilitate efficient demolding, especially when dealing with complex shapes or intricate details.
Controlling the Curing Process
The curing stage in Bakelite injection molding requires stringent control of both temperature and pressure. Variations can cause uneven curing, leading to defects such as warping or surface imperfections. Operators must continuously monitor and adjust machine settings to maintain consistent conditions, ensuring the desired product quality.
Mitigating Shrinkage and Deformation
Shrinkage and deformation are common challenges due to the inherent properties of thermosetting plastics. Achieving minimal shrinkage requires maintaining consistent pressure during the pressure holding phase5, allowing the material to settle correctly within the mold cavity. Implementing precision controls and leveraging computer-aided design tools can help predict and reduce these issues.
Ensuring Quality Through Inspection
Post-production inspection plays a vital role in identifying any defects resulting from the challenges mentioned above. Automated inspection systems can aid in detecting surface anomalies or dimensional inaccuracies, facilitating corrective measures in future production cycles. Implementing a thorough inspection protocol ensures that each product meets stringent quality standards before packaging and distribution.
Bakelite molds must withstand high temperatures.True
Molds need to endure high temperatures without deforming during the process.
Moisture in phenolic resin improves Bakelite quality.False
Moisture negatively impacts the performance of the final Bakelite product.
How Can Post-Processing Enhance Bakelite Products?
Post-processing is a vital step in ensuring the quality and appeal of Bakelite products, impacting both aesthetics and functionality.
Post-processing in Bakelite production enhances product quality by refining surface finish, removing imperfections, and ensuring dimensional accuracy. Techniques such as grinding, polishing, and flash removal are employed to meet high-quality standards.
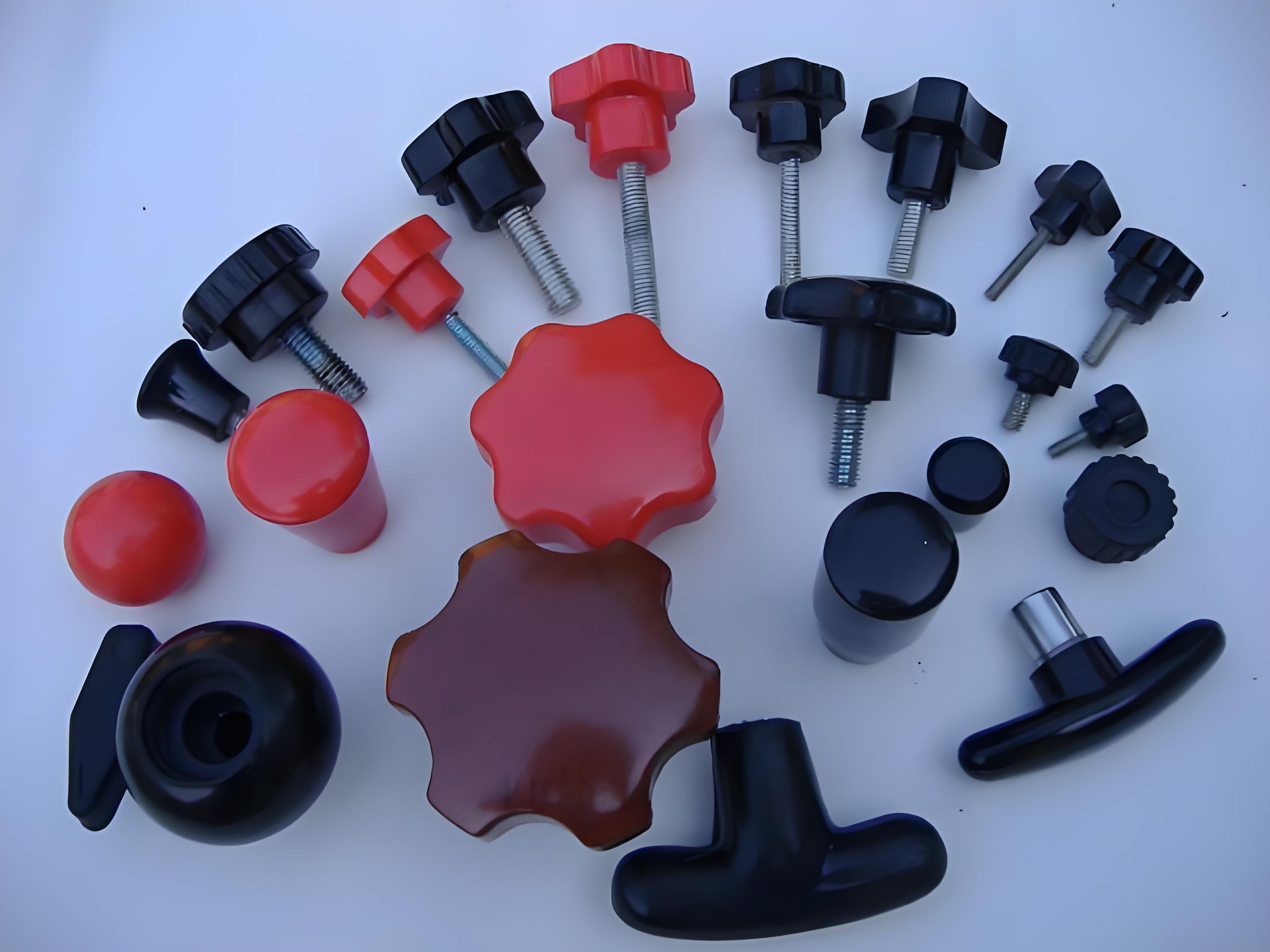
The Importance of Post-Processing in Bakelite Production
Bakelite products undergo several post-processing techniques to achieve their final form. This crucial stage is essential for eliminating imperfections and enhancing the surface quality of the product. Without adequate post-processing, even well-manufactured items might fall short of meeting consumer expectations.
Techniques Used in Post-Processing
1. Flash Removal:
During the demolding phase, excess material known as ‘flash’ may be present around the edges of the product. Removing this is crucial as it not only improves the aesthetic appeal but also ensures the product meets precise dimensional specifications. Techniques such as trimming and sanding are commonly used for effective flash removal.
2. Grinding and Polishing:
Grinding is often employed to smooth out surfaces and remove any minor surface defects. This is followed by polishing, which gives the Bakelite product a glossy finish, enhancing its visual appeal. This step is particularly important for consumer-facing products where appearance plays a significant role in marketability.
Enhancing Functional Attributes
Beyond aesthetics, post-processing can improve functional attributes such as durability and thermal resistance. These enhancements are achieved by refining the surface structure, which can affect how the product interacts with external elements such as heat and mechanical stress.
Impact on Durability:
For example, by ensuring that the product’s surface is free from micro-cracks or uneven textures through post-processing, manufacturers can prevent premature wear and tear. This process also ensures uniformity in product quality across batches, providing consistency that is highly valued in industrial applications.
Quality Inspection and Assurance
Quality control is an integral part of the post-processing phase. Each Bakelite product undergoes stringent inspection to ensure it meets predefined standards. This inspection includes checking for surface finish quality, dimensional accuracy, and the absence of defects.
Employing techniques like automated visual inspection6 can significantly enhance the efficiency and reliability of quality checks. These systems utilize advanced sensors and AI to detect flaws invisible to the human eye.
By investing in comprehensive post-processing and quality control measures, manufacturers can deliver Bakelite products that not only look impeccable but also perform exceptionally well across various applications.
Post-processing improves Bakelite durability.True
Refining surfaces prevents micro-cracks, enhancing durability.
Flash removal is unnecessary in Bakelite production.False
Flash removal is crucial for aesthetics and dimensional accuracy.
Conclusion
By mastering the Bakelite injection molding process, manufacturers can ensure high-quality outcomes tailored to their specific needs.
-
Ensures material integrity and quality during storage.: For such phenolic resin molding materials (I), it is preferred that the stable time in molten state at 100° C. is 250 seconds or more, and this can be attained … ↩
-
Learn about optimizing flow channels to reduce defects.: Standard cooling channel design is best suited for parts with relatively simple geometries to help ensure the entire part is cooled effectively … ↩
-
Discover tips to extend your mold’s service life.: Shop floor control software allows you to easily schedule regular mold maintenance rounds and verify that they have been completed. ↩
-
Learn how to handle phenolic resin effectively to prevent production issues.: The biggest hazard of phenolic resin is these free formaldehyde and phenol. Formaldehyde is a carcinogen, and studies have found that long-term … ↩
-
Discover effective pressure holding techniques to minimize product shrinkage.: Holding pressure is applied after the molten material fills the mold cavity to prevent voids caused by solidification shrinkage or weaknesses at … ↩
-
Learn how automation improves quality control in manufacturing.: Automated visual inspection systems are making our factories smarter by using the Internet of Things (IoT) to detect defects and even configure assembly lines … ↩