Ever wondered how the magic happens with plastic injection molding machines? Let me take you on a journey to understand their capacity.
A plastic injection molding machine’s capacity is determined by its clamping force, shot volume, and production rate. Clamping force keeps the mold closed, shot volume is the plastic injected per cycle, and production rate depends on cycle time and efficiency.
I remember my first deep dive into understanding these machines—picture me in a bustling factory, wide-eyed and curious. Learning that clamping force is expressed in tons was a revelation, as it made me appreciate the muscle behind these machines. Small-scale machines, the kind used for tiny trinkets, might have a clamping force as low as 5 tons. But those industrial giants? They go up to 5,000 tons! Then there’s the shot volume. Imagine the excitement of knowing this capacity dictates how much molten plastic gets injected each cycle. Whether it’s small parts or large industrial components, understanding shot volume is key. Lastly, the production rate, which I found fascinating. It depends on how quickly a machine completes its cycle. Smaller parts might zip through in seconds, while larger, intricate items take longer.
These factors are more than just numbers—they’re the heartbeat of efficient production, guiding us to choose the right machine for every project. Let’s explore these elements in detail and see how they shape the performance and choice of equipment.
Clamping force is measured in kilograms.False
Clamping force is measured in tons, not kilograms.
Shot volume determines the amount of plastic per cycle.True
Shot volume is the maximum plastic injected per cycle.

How Does Clamping Force Affect Machine Capacity?
Ever wondered what keeps those massive molds tightly shut during the injection process? It’s all about the clamping force!
Clamping force in injection molding maintains mold integrity and prevents defects, affecting machine capacity. Machines vary from 5 to over 5,000 tons, influencing production quality and efficiency.

Understanding Clamping Force Capacity
In the world of injection molding1, I’ve learned that clamping force isn’t just a technical term—it’s the unsung hero of machine capacity. Imagine trying to keep a lid on a boiling pot without a good, heavy weight; that’s clamping force for you. It’s measured in tons, and it holds the mold shut while molten plastic is injected, countering intense internal pressures. If the force isn’t enough, it’s like a lid popping off a pot—leading to defective parts.
Machine Type | Clamping Force Range |
---|---|
Small-scale | 5-10 tons |
Large-scale | 1,000-5,000+ tons |
For me, working with small-scale machines feels like handling delicate art pieces—they operate with clamping forces between 5 to 10 tons, perfect for prototyping tiny trinkets. But when I’ve moved to larger industrial settings, where machines demand 1,000 to over 5,000 tons of force, it’s like going from sculpting clay to carving stone. This transition is essential when crafting larger automotive parts or big containers.
The Interplay with Shot Volume
I once faced a project where understanding shot volume2 was crucial. Picture it as how much batter you need to fill your cupcake molds perfectly. This volume dictates how much molten plastic an injection unit can deliver in a single cycle.
- Small Machines: Shot volumes of 1-10 cc, akin to making small toy gears.
- Medium Machines: Shot volumes of 100-500 cc for mid-sized products.
- Large Machines: Several thousand cc for items like industrial pallets.
Influence on Production Rate Capacity
When I think about production rates, it’s like racing against time. Each cycle—from injection to cooling to ejection and mold closing—determines how fast you can go. Smaller parts might have cycle times of mere seconds; it’s exhilarating! A machine with a 5-second cycle can churn out 720 parts an hour—mind-blowing efficiency! Larger parts take longer, reminding me of those slow-baked recipes that require patience but yield results worth waiting for.
And then there are the other players in this race: machine reliability, injection/ejection speed, and cooling efficiency—all factors that can make or break production outcomes.
These insights have been pivotal in my journey to optimize production processes and ensure top-notch quality in plastic manufacturing. Every time I walk into a production floor, I can’t help but feel like I’m both an artist and an engineer, constantly balancing precision with creativity.
Clamping force is measured in tons.True
Clamping force is indeed measured in tons, indicating machine capacity.
Shot volume is measured in liters.False
Shot volume is measured in cubic centimeters (cc), not liters.
How Do You Calculate Shot Volume Capacity?
Ever wondered how much molten plastic your machine can inject per cycle? Understanding shot volume capacity is key to optimizing production in injection molding, minimizing waste, and ensuring quality.
Shot volume capacity is calculated by assessing a machine’s maximum molten plastic injection per cycle, measured in cubic centimeters or ounces, based on machine specifications and product needs.
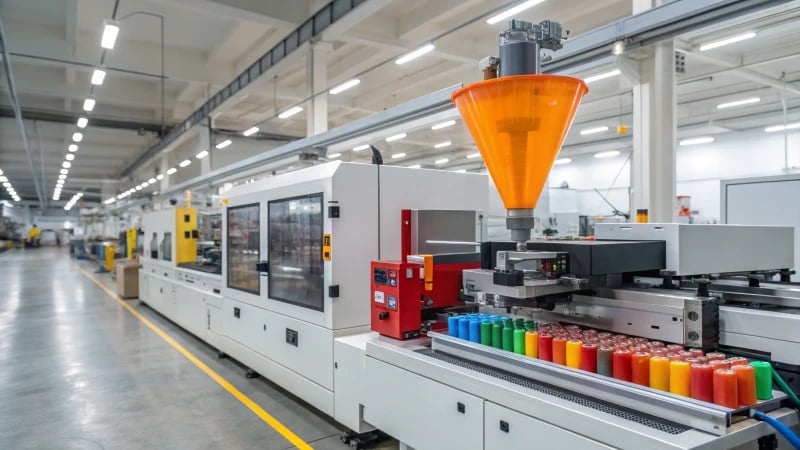
Factors Influencing Shot Volume Calculation
In injection molding3, shot volume capacity defines how much molten plastic can be injected in a single cycle, typically measured in cubic centimeters or ounces. Here’s what I’ve learned about the key factors involved:
-
Injection Unit Specification
The dimensions of the screw and barrel play a crucial role. A larger barrel usually means a greater shot volume, which was a game-changer when we were working on those massive industrial pallets. Ensuring you have the right specs for your project is vital.
Example Table:
Machine Type Screw Diameter (mm) Maximum Shot Volume (cc) Small 15 10 Medium 50 500 Large 120 2000 -
Material Properties
Different plastics have unique melting points and viscosities. I once had to tweak settings for a particularly dense material to hit that sweet spot in shot volume.
-
Mold Design
The complexity and size of your mold can drastically affect the amount of plastic needed per cycle. It reminds me of a challenging project involving intricate designs where every adjustment counted.
Calculating Shot Volume
Here’s a straightforward way to calculate shot volume:
- Step 1: Start by determining your screw diameter and shot length, as these will directly affect your volume capacity.
- Step 2: Use the formula
π × radius² × height
to calculate the cylinder’s volume, making sure to adjust for material density. - Step 3: Consider machine efficiency and desired product quality, which might mean tweaking cycle times for the best results.
Understanding these elements not only boosts resource management but also enhances production efficiency. As designers like Jacky know, leveraging this knowledge can significantly improve product design and manufacturing processes. For more insights, check out how clamping force4 and shot volume work together to ensure machines produce high-quality products without defects. Accurately calculating these parameters is crucial for success in our field.
Larger screw diameters result in higher shot volumes.True
A larger screw diameter increases the barrel's capacity, allowing more plastic per cycle.
Material density does not affect shot volume capacity.False
Material density influences the volume calculation, requiring adjustments for optimal results.
Why Is Production Rate Important in Injection Molding?
Ever wondered why the production rate in injection molding holds such significance? It’s not just about churning out parts faster—it’s the heartbeat of efficient manufacturing.
The production rate in injection molding is vital as it influences efficiency, cost, product quality, delivery, expenses, and machine utilization.
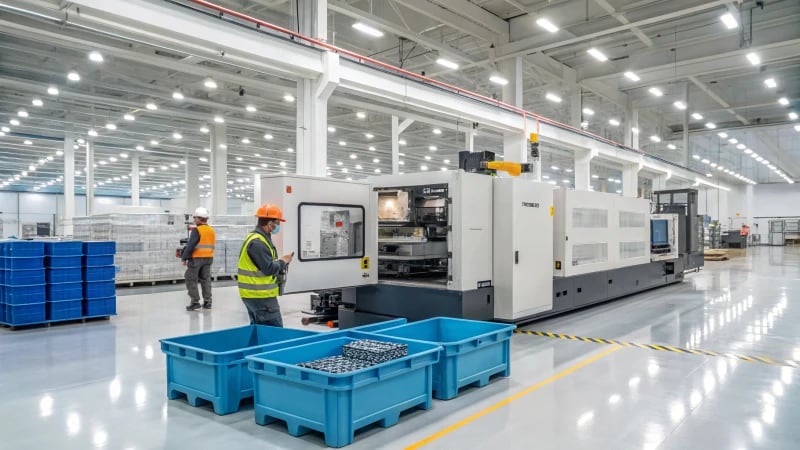
The Role of Production Rate in Manufacturing Efficiency
When I first dipped my toes into the world of injection molding, it was like opening the door to a hidden universe of speed, precision, and strategy. Understanding the production rate felt akin to cracking the code of efficiency. Imagine balancing on a tightrope where each step dictates not only how swiftly you reach the end but also how safely. In the realm of injection molding, this delicate balance defines how quickly and effectively parts are produced, shaping everything from delivery timelines to the bottom line.
Clamping Force Capacity
One day, while observing a large-scale injection machine in action, I marveled at the sheer power needed to keep everything in check. The clamping force capacity, measured in tons, is what ensures the mold stays shut tight during the injection5 phase. I remember thinking about how small machines for tiny trinkets might manage with just 5-10 tons, whereas those colossal giants tackling automotive parts require over 1,000 tons to keep things sealed up snugly.
Machine Scale | Clamping Force (tons) |
---|---|
Small | 5 – 10 |
Medium | 100 – 500 |
Large | 1,000 – 5,000 |
Impact on Cost-effectiveness
I recall a project where trimming even a single second off our cycle time felt like discovering buried treasure. A high production rate slices through labor and overhead costs per part by shaving cycle times down to mere seconds. For instance, reducing the cycle time6 to just 5 seconds allowed us to crank out 720 small caps every hour—a win that kept us competitive.
Influence on Quality
Speed can be a double-edged sword. As we ramped up production rates, maintaining quality became our mantra. Each machine had to strike that perfect chord between rapidity and precision—from injection to cooling—to ensure every piece met our exacting standards. Reliable machinery and top-notch cooling systems became our best friends in this endeavor.
Shot Volume Capacity and Its Effects
Another aspect that fascinates me is shot volume capacity. Measured in cubic centimeters (cc), this determines how much material is injected per cycle. Larger volumes are akin to opening the floodgates for producing bigger items like industrial pallets.
Machine Scale | Shot Volume (cc) |
---|---|
Small | 1 – 10 |
Medium | 100 – 500 |
Large | Several thousand |
Factors Influencing Production Rate
Several factors are at play in mastering the production rate:
- Machine Reliability: A reliable machine is like a steadfast companion; breakdowns can throw production into chaos.
- Injection Speed: It’s all about speed, but too much can compromise quality.
- Cooling Efficiency: Cutting-edge cooling systems are key players in shortening cycle times.
Balancing these elements feels much like orchestrating a symphony where speed and quality harmonize perfectly. For those seeking deeper insights into production optimization7, understanding these nuances is essential.
High production rates reduce labor costs in injection molding.True
High rates minimize cycle times, reducing labor and overhead costs per part.
Large machines in injection molding need over 500 tons clamping force.False
Large machines may require over 1,000 tons for mold closure during injection.
What Additional Factors Affect Machine Performance?
Ever wondered why two machines performing the same task can yield different results?
Machine performance is impacted by clamping force, shot volume, and production rate capacities, essential for maintaining efficiency and quality.
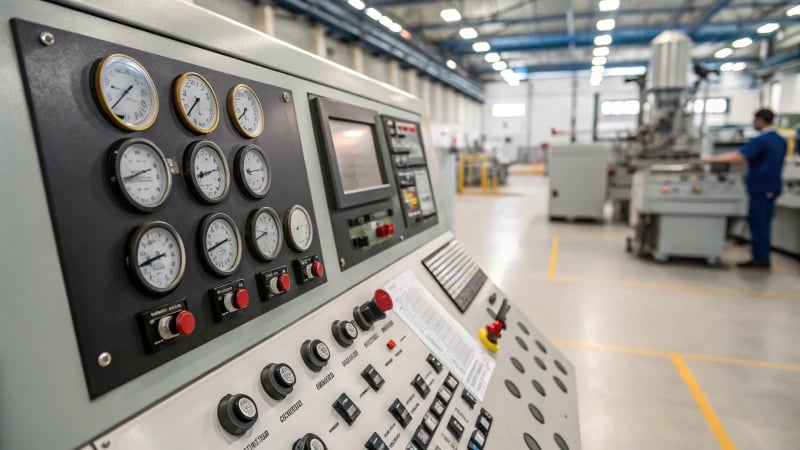
Clamping Force Capacity
Let’s start with a story: I remember my first day at the factory, watching a massive machine clamping down on a mold. The force was astonishing—like seeing a giant grip something with unyielding strength. This clamping force8 is measured in tons and it’s essential. It prevents the mold from opening during the injection of molten plastic, ensuring no defects.
Machine Type | Clamping Force (tons) |
---|---|
Small-scale | 5 – 10 |
Large-scale | 1000 – 5000+ |
Small-scale machines, which I’ve used for prototypes or small trinkets, have a clamping force as low as 5 to 10 tons. In contrast, the industrial giants I’ve worked with, producing large automotive parts, boast forces from 1,000 to over 5,000 tons. It’s all about matching the right force to the job at hand.
Shot Volume Capacity
Ah, shot volume. This one’s like filling up a car’s tank—except the car is a mold, and the fuel is molten plastic. The maximum shot volume a machine can handle in one cycle is pivotal.
- Small machines: 1 – 10 cc
- Medium machines: 100 – 500 cc
- Large machines: Several thousand cc
For tiny parts like toy gears9, you might be looking at a mere 1 to 10 cc. Medium machines handle around 100 to 500 cc—perfect for items like mid-sized containers. And those large-scale machines I mentioned earlier? They can gulp several thousand cc in one go. Choosing the right machine is like picking the perfect ladle size for your soup pot.
Production Rate Capacity
Production rate brings back memories of watching a machine chug away, part after part. The cycle time determines this rate—how fast it can finish one complete cycle, from injection to cooling to ejection.
Part Type | Cycle Time (seconds) | Parts per Hour |
---|---|---|
Simple, small-sized parts | 5 | 720 |
Larger, complex parts | Several minutes | Varies |
Fast machines that I’ve worked with can crank out simple parts every 5 seconds, reaching up to 720 pieces an hour10. Larger or complex parts take longer, sometimes minutes per cycle, reducing output. But oh, the satisfaction of seeing high-quality parts roll out at an efficient pace! It’s a dance of speed and precision that I’ve always admired.
Understanding these factors has helped me select the right machines for my projects. It’s all about optimizing efficiency and ensuring quality—two things I strive for in every piece I design.
Clamping force is measured in tons.True
Clamping force is quantified in tons, indicating the machine's capacity.
Shot volume capacity is expressed in liters.False
Shot volume is typically measured in cubic centimeters or ounces.
Conclusion
The capacity of plastic injection molding machines is determined by clamping force, shot volume, and production rate, essential for efficient manufacturing and quality control.
-
Explore this link to understand the fundamental role of clamping force in maintaining mold integrity during injection molding. ↩
-
Discover how shot volume impacts the production capacity and suitability for various products in injection molding. ↩
-
Learn more about injection molding processes to understand the context of shot volume capacity. ↩
-
Discover how clamping force influences the injection molding process, especially related to shot volume. ↩
-
Learn how clamping force impacts mold sealing and defect prevention. ↩
-
Explore how optimizing cycle time can enhance production speed and cost-effectiveness. ↩
-
Discover strategies to balance speed and quality in injection molding processes. ↩
-
Discover how clamping force impacts mold security during injection, preventing defects. ↩
-
Explore various applications of plastic gears and their importance in small machines. ↩
-
Learn strategies to enhance efficiency and optimize cycle times for better productivity. ↩