Did you ever think about how those smooth plastic devices we use every day are created?
Plastic injection molding melts plastic and injects it into molds for precise, efficient mass production. Widely used in various industries, this method is crucial for manufacturing diverse products.
Join me on a journey through the amazing world of plastic injection molding. This process is crucial for manufacturers like me. It starts by heating and melting plastic pellets. Then, the liquid plastic goes into molds under high pressure. It creates many things, like smartphone cases and toys. I see how this method brings precision and efficiency in mass production. It shapes our modern lives in surprising ways.
Plastic injection molding is only used for small products.False
This claim is false as plastic injection molding can produce both small and large items across various industries.
The process of plastic injection molding is highly efficient.True
This claim is true because the technique allows for rapid production with high precision, making it efficient for mass manufacturing.
What Are the Advantages of Plastic Injection Molding?
Do you ever think about why plastic injection molding is often chosen for creating plastic parts in many fields? This method really stands out because of its benefits. Let’s explore its advantages and understand how it has shaped my experiences in product design.
Plastic injection molding offers rapid production, cost-efficiency with scale, flexible and complex designs, diverse thermoplastic options, and consistent quality, while minimizing waste through material reuse.
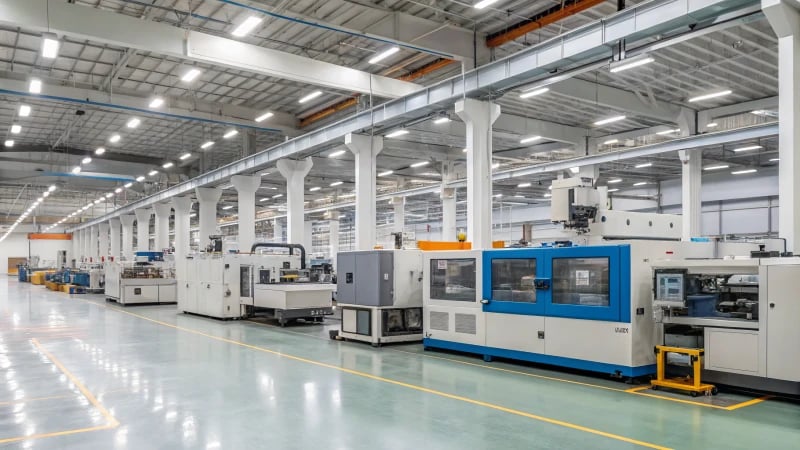
Efficiency and Speed
When I first explored manufacturing, I felt amazed at how plastic injection molding changed product creation. This process impressed me with its efficiency and speed. It quickly produced thousands of parts in just hours. Typical cycle times ranged from 15 to 60 seconds depending on the complexity of the part and the material used. My designs came to life fast, meeting customer needs while keeping costs low. Seeing a concept turn into a real product so quickly was very exciting!
Design Flexibility
Plastic injection molding offers incredible design flexibility. I once worked on a project for a consumer electronics company where we needed to combine looks with function. Injection molding helped us create complex shapes that seemed impossible with old methods. It opened new creative doors for me, allowing me to experiment with mixed colors in designs that were both beautiful and useful. It felt like art combined with engineering.
To learn more about design considerations, check out design strategies1.
Cost-Effectiveness
Now, let’s talk about cost. At first, the setup costs for molds scared me, but I soon learned how cost-effective this process is over time due to its low per-part costs. As production volume increases, the unit cost drops significantly.
Here’s a simple table illustrating cost dynamics:
Production Volume | Estimated Cost per Part |
---|---|
1,000 | $5.00 |
10,000 | $1.50 |
100,000 | $0.50 |
Watching these numbers change made me see how important this method is for large production runs.
Material Versatility
I admire the material versatility of plastic injection molding. Working with different thermoplastics like ABS and PP let me pick materials based on project needs—whether I needed strength, flexibility or resistance to chemicals or heat; there was always a suitable material available.
Consistency and Precision
One comforting part of plastic injection molding is its consistency and precision. Once the mold is ready, it can repeatedly produce parts with amazing accuracy. I remember a project in the automotive field where precision was critical; every component fit together perfectly because they were nearly identical.
This level of detail made me really confident in our final product.
Waste Reduction
Lastly, I can’t ignore the waste reduction benefits of this process. Sustainability is important; plastic injection molding generates very little scrap material since excess plastic can often be reused in future production runs.
This approach helps the environment and lowers material costs—a win-win for any designer!
Plastic injection molding is the fastest method for producing parts.True
This claim highlights the efficiency of plastic injection molding, which allows rapid production cycles, making it ideal for high-volume manufacturing.
Injection molding can only use a single type of plastic material.False
This claim is false as plastic injection molding allows for multiple materials to be used in one mold, enhancing design capabilities.
What Types of Products Can Be Manufactured Using This Process?
Have you ever thought about how things we use every day come into existence? Plastic injection molding uses an interesting process for producing different products. This method really helps in creating a range of items!
Plastic injection molding can produce various products, including consumer electronics housings, automotive parts, household containers, and medical devices like syringes.
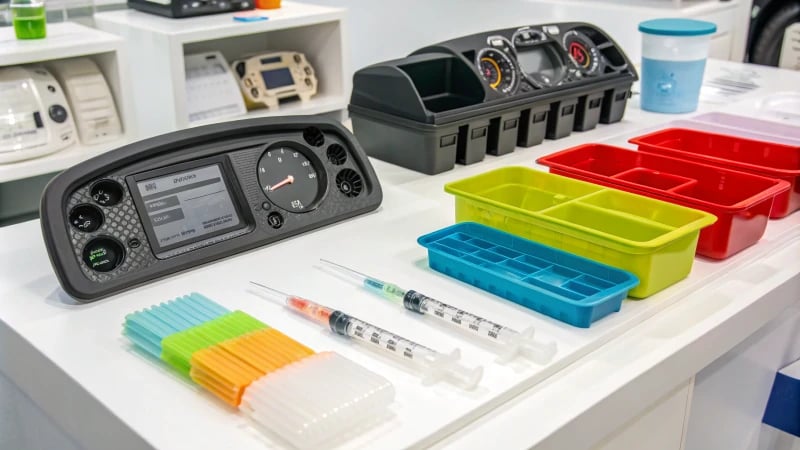
Understanding Plastic Injection Molding
Plastic injection molding acts like magic. It changes raw materials into finished products quickly and exactly. The process starts by heating and melting plastic until it turns liquid. Then, this liquid goes into molds with high pressure and cools to its final shape. I watched the process in a factory, amazed at each product’s detailed emergence, reminding me of an artist’s work.
Common Product Categories
Plastic injection molding produces a wide variety of products. The range is huge and touches our daily lives.
Category | Examples |
---|---|
Household Items | Containers, toys, kitchen utensils |
Automotive Components | Bumpers, dashboards, interior trim |
Consumer Electronics | Housings for phones, remotes, and appliances |
Medical Devices | Syringes, surgical instruments, drug delivery systems |
Industrial Parts | Housings, brackets, gears |
These categories highlight the versatility of plastic injection molding.
Specific Examples of Products
- Consumer Electronics: Products such as mobile phone cases come from injection molding. These items show the method’s precision and strength. Designs must balance looks and use.
- Automotive Parts: Cars use many molded parts like bumpers and dashboards. These parts need to meet strict safety and design rules. Seeing these parts come together shows the skill behind cars.
- Medical Equipment: Syringes and other tools use injection molding too. High precision is vital for these products. They meet tough health standards, proving the method’s value in healthcare.
Advantages of Using Injection Molding
Plastic injection molding offers many benefits:
- Efficiency: It allows for fast production of large amounts, which satisfies demand.
- Consistency: Products are very uniform, keeping quality steady.
- Material Variety: Various plastics allow customization for different needs.
Learning more about these benefits could inspire future design projects.
Exploring Limitations and Considerations
This process has its challenges too:
- High Initial Costs: Developing molds might cost a lot.
- Long Lead Times: Creating molds takes time, slowing schedules.
Understanding these obstacles helps me plan as a designer. If interested in handling these challenges, further resources are available at mold cost management2.
Conclusion
As a product designer, I really admire the versatility of plastic injection molding. It offers endless possibilities across industries. Understanding its strengths and limits helps us create products that meet and delight users.
Plastic injection molding can produce automotive components.True
True, plastic injection molding is widely used for manufacturing automotive parts like bumpers and dashboards.
Injection molding is only suitable for household items.False
False, injection molding is versatile and also produces medical devices and electronics.
How Do Material Choices Affect Injection Molding Outcomes?
Have you ever thought about how the materials we pick change the end products we build? In my adventure in the field of injection molding, I found that the correct material really changes both how something works and how it looks.
Choosing the right materials for injection molding is crucial, as they influence mechanical strength, thermal stability, fluidity, production costs, and the product’s functionality and appearance, making them vital for effective product design.

Understanding Material Properties
Material selection is a thrilling exploration that significantly impacts designs and their success. I often focus on several key properties.
- Mechanical Strength: We once selected polycarbonate3 for safety goggles. This choice wasn’t only about saving money; more importantly, it was about protecting users. Polycarbonate offers high impact resistance. This quality gave me peace of mind, knowing it withstands tough conditions.
- Thermal Stability: Once, we needed heat-resistant materials. Nylon4 was the solution. Some materials like nylon perform perfectly under high temperatures. This performance amazed me during testing.
- Fluidity: For complex designs, Acrylonitrile Butadiene Styrene (ABS)5 was ideal. ABS allows for the creation of intricate shapes, impossible with thicker materials.
The Role of Material Selection
Choosing materials is like setting the stage for a play. It affects durability, costs and timelines. On one project, we chose cheaper plastic to save money. However, the failure rates increased, leading to costly repairs. This mistake hurt our reputation.
Material Type | Cost per kg | Applications | Notes |
---|---|---|---|
Polypropylene | $1.00 | Packaging, automotive | Lightweight, good chemical resistance |
Polycarbonate | $2.50 | Safety goggles, electronics | High impact resistance, good clarity |
Nylon | $1.75 | Gears, bearings | Excellent strength and wear resistance |
ABS | $1.50 | Toys, household items | Good toughness and surface finish |
Impact on Design and Functionality
Material choice steers the feasibility of my designs. A thick material might need stronger machinery, limiting design options. Aesthetics also matter; color and finish can make a simple design striking yet might challenge production.
Considerations for Aesthetic Qualities
- Color Options: I love using masterbatch6 for even coloring. Some materials accept color easily while others need special additives.
- Surface Finish: Texture choice impacts products a lot. Once we aimed for a smooth surface; we invested in tough post-processing steps that added value to our product.
Performance Trade-offs
Choosing materials involves balancing performance and cost. High-performance materials might be complex or expensive; for instance, metals are strong but costly while plastics like Polyethylene7 offer a cheaper easier-to-mold alternative.
- Environmental Factors: Sustainability is vital; I’ve found biodegradable options attractive as they need special processing unlike traditional plastics which excites me and aligns with my values.
In summary, selecting materials wisely optimizes injection molding results by evaluating factors like mechanical properties costs and aesthetics to strive to exceed expectations.
Material choice affects product performance in injection molding.True
Selecting the right material is crucial as it directly influences mechanical strength and thermal stability, impacting overall product performance.
Using cheaper materials always reduces production costs.False
While cheaper materials may lower initial costs, they can lead to higher failure rates and replacements, ultimately increasing long-term expenses.
What Are the Common Challenges in Plastic Injection Molding?
Watching your design turn into something real probably feels thrilling. However, unexpected problems might appear. Plastic injection molding sometimes brings joy, but it has challenges too. Let’s explore some of the usual problems that might happen.
Common challenges in plastic injection molding involve material issues, complex designs, temperature control, injection pressure, cycle time management, and mold maintenance, all essential for enhancing production efficiency and product quality.
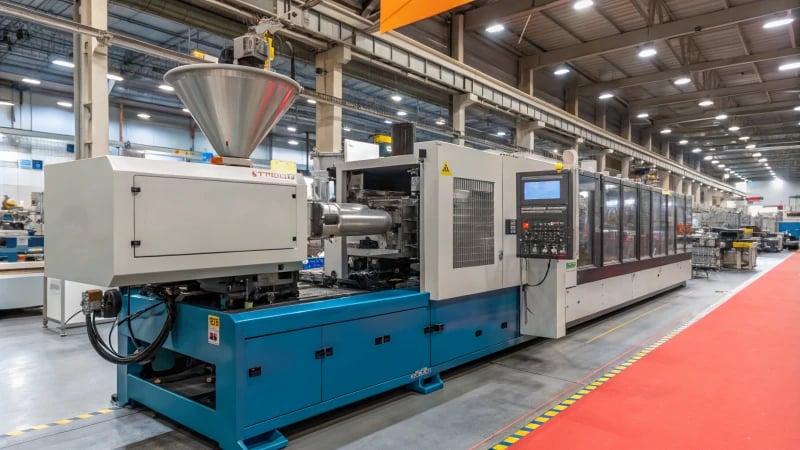
Understanding Common Challenges in Plastic Injection Molding
Plastic injection molding is a fascinating way to create plastic pieces. But, it’s not always easy. Here are some challenges I’ve faced and learned from:
-
Material Issues
Picking the right plastic is tricky. Each type behaves differently when it melts and flows. For instance, I chose polypropylene for a project, but later found out the temperature range of 180-220°C was crucial for success. Wrong material choices lead to defects. I’ve seen many! More tips on material compatibility in injection molding8. -
Design Complexity
Designers, like me, love intricate designs. However, complex designs sometimes cause uneven mold filling. I worked on a complicated design once, resulting in short shots. It was frustrating! Simplicity in design reduces these risks. Explore more on design optimization techniques9. -
Temperature Control
Keeping the right temperature during injection is very important. It’s like walking on a tightrope. A small mistake leads to inconsistencies. I once worried about cooling during production; any error might cause warping.
Stage | Recommended Temperature Range |
---|---|
Feeding | 180-220°C |
Plasticization | Varies based on plastic type |
Cooling | Depends on product thickness |
-
Injection Pressure
Balancing injection pressure is important. Too low pressure leads to incomplete fills; too high causes flash defects. I’ve learned that finding the right balance is key for good flow and filling. Discover more on pressure control in injection molding10. -
Cycle Time Management
Cycle times are very important for productivity. Long cycles increase costs and reduce output rates.
In my early days, I ignored this, causing delays; now I focus on cooling time, injection speed and mold design to ensure smooth operations.
For more on optimizing cycle times, visit cycle time optimization strategies11. -
Mold Maintenance
Regular maintenance is like caring for an old car; without it, you risk misalignment and bad products due to wear and tear.
I found that a proactive schedule saves time and problems.
Learn about mold maintenance best practices12.
By understanding challenges, manufacturers like us tackle issues in plastic injection molding processes. Each challenge is a chance to improve and innovate which ultimately leads to better efficiency and higher quality products.
Material choice affects injection molding quality.True
The type of plastic used impacts melting temperatures and flow, crucial for successful injection molding.
Complex designs guarantee uniform mold filling.False
Intricate designs can hinder even flow in molds, leading to defects like short shots.
Conclusion
Explore the essential process of plastic injection molding, its benefits, challenges, and wide-ranging applications in manufacturing diverse products.
-
Discover how plastic injection molding can enhance your production efficiency and reduce costs. ↩
-
Learn about the benefits and applications of injection molding in various industries. ↩
-
Clicking this link will provide insights into advanced material properties that can enhance your injection molding outcomes. ↩
-
This link offers a detailed comparison of different plastics used in injection molding, helping you make informed choices. ↩
-
Explore this link for tips on optimizing material selection based on product requirements and design specifications. ↩
-
Discover sustainable alternatives in this link that can be used in injection molding processes for eco-friendly designs. ↩
-
This link explains how environmental factors influence material selection in injection molding processes. ↩
-
Discover how common challenges impact injection molding and learn effective solutions to enhance your production processes. ↩
-
Explore innovative approaches to overcome design complexity in injection molding for improved efficiency. ↩
-
Learn about effective temperature control methods to ensure consistent quality in your injection molded products. ↩
-
Find out how to optimize cycle times for better productivity and lower manufacturing costs. ↩
-
Get insights on maintaining molds effectively to prevent production issues and ensure quality. ↩