Ever looked at an injection molded product and asked why those annoying lines remain? I’ve experienced that too, sharing that same frustration.
To minimize parting line traces in injection molding, use techniques like optimized mold design, proper gate placement, uniform mold cooling, and consistent injection pressure. Additionally, selecting the right material and adjusting the parting line location can significantly reduce visible traces.
I recall the first time I understood how important it was to fix parting line traces. The experience taught me a hard lesson when many molded cases failed to meet our client’s visual standards. I then found important strategies that really helped through trial and error. Optimizing the mold design changed everything. Setting the gate in the right places and avoiding rounded corners helped the traces appear much less noticeable. Modifying the injection molding process itself created a big improvement. I adjusted temperatures and pressures until they were just right. Choosing materials with good fluidity helped a lot. It made those lines almost invisible.
Cleanup also matters a lot. Regularly keeping the mold surface clean and using post-processing methods like sanding and polishing really transformed a flawed finish. Each product and mold has unique traits. With patience and some experimentation, I realized a cleaner, polished look is very possible to achieve.
Optimizing mold design reduces parting line traces.True
Proper mold design ensures even material flow, minimizing visible seams.
Post-processing is unnecessary for reducing parting lines.False
Sanding and polishing are vital to smooth out parting line traces.
How can mold design be optimized to reduce parting lines?
Have you ever wondered how to get injection molded products to look perfect?
Reducing parting lines in mold design probably requires optimizing gate positions. Designers might avoid rounded corners. Choosing the correct materials is important. Adjusting injection settings helps a lot. Keeping molds very clean is a key strategy.
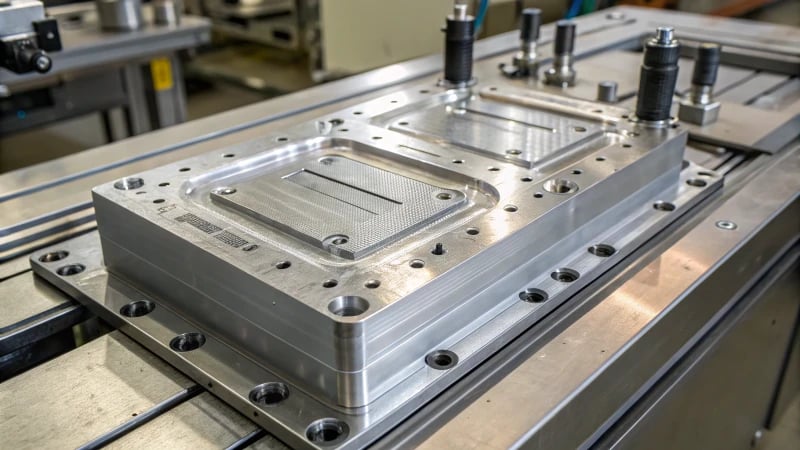
Choose Gate Position Wisely
Placing the gate near the parting line is a clever trick. It’s like putting a zipper where it blends best into the fabric. This lets the plastic melt blend smoothly as it fills, keeping the flow nice and reducing unwanted marks. Explore gate positioning techniques1.
Avoid Using Rounded Corners
Avoiding rounded corners at the parting line is a real game-changer. Parting lines work better on natural edges or corners, making any small burrs less visible. It is really a smart way to use the shape of the product. Learn more about parting line strategies2.
Plan Appearance Strategically
For visible surfaces, placing parting lines discreetly is key—like hiding a scar behind your ear. Avoid important dimensions on the parting surface to enhance product appearance.
Material Choice and Mold Care
Picking plastics with great fluidity has saved me lots of trouble. Regular mold cleaning also reduces line visibility significantly. Trust this: a cleaning schedule is very valuable.
Method | Benefit |
---|---|
Material Choice | Reduces line visibility |
Mold Cleaning | Ensures consistent quality |
Adjust Injection Techniques
Adjusting injection settings was a huge insight for me. Higher mold temperature helps the melt flow more easily, reducing lines. Slower injection speed allows smoother flow and stops chaos. Balancing pressure and holding time produces a really smooth finish.
Find out more about adjusting injection parameters3 for optimal mold performance.
After-Process Techniques
When everything else does not work, post-processing saves the day. Sanding and polishing can change a product from simply useful to truly beautiful—it’s like giving your work a final shine. Explore effective post-processing methods4.
From my work, I know different products need different tweaks, so always stay ready to try new things and learn as you go. Each new project offers new ways to expertly reduce those annoying parting lines.
Gate positioning affects parting line visibility.True
Proper gate placement ensures smooth plastic flow, reducing visible lines.
Rounded corners reduce parting line marks.False
Avoiding rounded corners helps align parting lines with natural edges.
What Process Parameters Affect Parting Line Visibility?
Have you ever looked closely at a plastic item and noticed those annoying lines that spoil its perfect appearance? I have seen them too. Let’s explore together what causes these lines to appear.
Improving mold design reduces parting line visibility. Adjusting injection molding settings helps too. Choosing the right materials is essential. Using post-processing techniques is also very effective. These methods create smoother molded products. They really improve visual appeal.
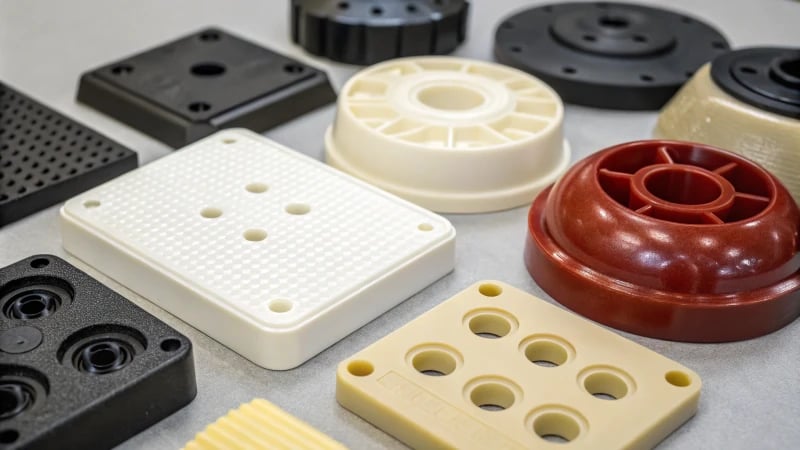
Mold Design Considerations
From my experience, a smart mold design helps reduce visible parting lines. Gate position matters. Placing the gate near the parting line guides the plastic smoothly, reducing unsightly marks.
Rounded corners are crucial. Sometimes, designs hide lines along an edge, making even the smallest burr blend in. Placement is key; keep important areas free of lines when possible.
Injection Molding Parameters
Adjusting injection molding parameters resembles cooking; it involves tweaking heat and time for perfect results. Higher mold temperature smooths out surfaces, like a hot iron on wrinkles.
Injection speed is important. Slower speed leads to less turbulence and smoother flow, resulting in fewer visible lines.
Injection pressure also plays a role; it’s like squeezing toothpaste correctly. More pressure fills everything tightly. Changing holding time and pressure allows plastic to set well, closing gaps during cooling.
Parameter | Effect on Parting Line Visibility |
---|---|
Mold Temperature | Higher temperature enhances flow fusion |
Injection Speed | Lower speed reduces turbulence |
Injection Pressure | Higher pressure tightens melt fusion |
Holding Time & Pressure | Longer time improves melt combination |
Material Selection and Maintenance
Choosing the right materials is vital. I learned this in a project where fluidity was important—opt for plastics that merge well during molding, similar to choosing good clay for pottery; the better it merges, the nicer the result.
Regular mold maintenance is essential. Keep the mold clean5 to avoid disruptions—a spotless mold gives a clean finish; it’s really that simple.
Post-Processing Techniques
Finally, post-processing works wonders. Sanding and polishing can remove stubborn parting lines. Each product may need special methods for a smooth finish.
Through trial and error, you find what works best.
Whether new or experienced in molding, remember to experiment and refine techniques to achieve flawless results for each unique project6.
Higher mold temperature reduces parting line visibility.True
Increasing mold temperature improves plastic flow and fusion, reducing marks.
Rounded corners on parting lines minimize visibility.False
Rounded corners increase visibility; edges make burrs less noticeable.
Why is material selection important for minimizing parting lines?
Do you see those annoying lines where plastic products come together? I do and there’s a solution. Choosing the right material is the key to reducing these lines. Proper materials really help make the surface smooth. Good selection is very important.
Material choice is crucial to reduce parting lines. Different materials have unique flow and shrinkage properties. These characteristics really affect the look and quality of molded parts. The impact is significant.
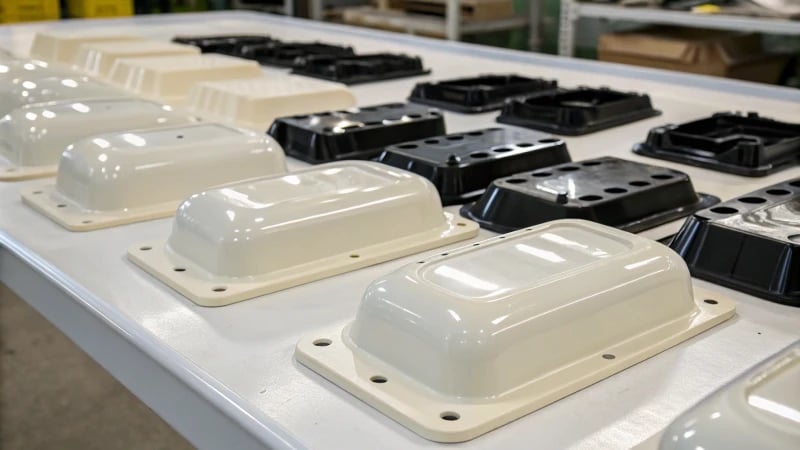
Understanding Material Characteristics
When I first explored injection molding, I noticed that using the right material is very important. Each material has unique traits like fluidity and fusibility. These decide how well it fills the mold. High fluidity materials, such as Polypropylene, provide a more even fill. This often leads to fewer visible lines.
Material Type | Key Characteristics | Effect on Parting Lines |
---|---|---|
Polypropylene | High fluidity, low cost | Reduces visible parting lines |
ABS | Strong, glossy finish | Minimizes noticeable seams |
Nylon | Durable, flexible | Can increase line visibility |
Influence of Shrinkage
Once, I worked on a project where the material shrunk unevenly. It was difficult to keep the product looking smooth. Uneven shrinkage during cooling can cause the material to separate from mold surfaces. This makes those parting lines7 stand out. Choosing materials with predictable shrinkage patterns is really important to keep surfaces smooth.
Role of Mold Design
Material choice is key, but mold design is also very important. Placing the gate near the parting line allows for better plastic merging and fewer marks. I avoid rounded corners at the parting lines as they usually stand out more.
Mold Design Tips:
- Position gates with care for good melt flow.
- Do not place parting lines in visible areas.
- Use design software8 to see material behavior and improve outcomes.
Injection Molding Process Parameters
Tweaking process parameters is like finding the best recipe. Changing temperature, speed, and pressure greatly affects material behavior during molding. Raising mold temperature helps in smoother flow and better merging of the plastic melt. This reduces line traces.
Parameter Adjustments:
- Raise mold temperature for better merging.
- Change holding time for tighter plastic melt merging.
Every material needs specific parameter changes. Understanding these differences greatly improves product quality. Constantly trying new methods and gaining experience are key to perfecting settings for best results.
Explore more on injection molding techniques9.
Polypropylene reduces visible parting lines.True
Polypropylene's high fluidity ensures a uniform fill, minimizing lines.
Nylon increases the visibility of parting lines.True
Nylon's durability and flexibility can lead to uneven shrinkage.
How Can You Conceal Parting Lines in Molded Products?
Do annoying parting lines spoil your finely shaped products? I have experienced that as well! Let’s explore some smart techniques to remove them.
Hide parting lines well by using sanding, polishing or coating methods. These techniques really smooth out imperfections. They improve how your molded products look. Products look better without visible flaws.
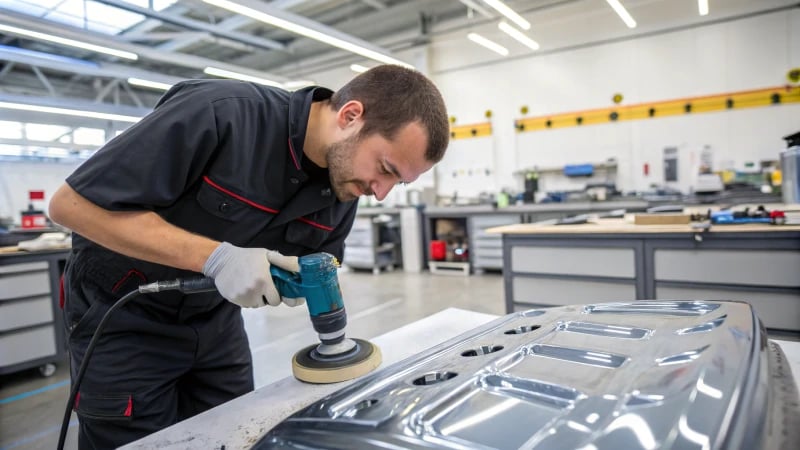
Sanding and Polishing
I often end up with a product that seems nearly perfect, except for those annoying parting lines. Sanding helps in this situation. I usually choose fine grit sandpaper or a sanding block to slowly remove the extra material. It feels similar to smoothing out the edges of a tough day. It needs some time, but it’s worth doing. When dealing with larger areas, I may even use a power sander.
Polishing follows sanding and uses finer abrasives to achieve a smooth, glossy finish. This step resembles giving your product a relaxing spa treatment. Wonderfully smooth and glossy finishes result from using finer abrasives. Different polishing techniques10 are available depending on the material and the final look you desire.
Coating Applications
Sometimes, sanding and polishing aren’t enough. That’s where coatings come in. They act like a fresh coat of paint in a room, hiding flaws and bringing new life.
- Paints and Lacquers: These can mask surface imperfections effectively.
- Powder Coating: Offers a thicker finish that can fill in minor surface defects.
- UV-Curable Coatings: Provide fast curing times and durable finishes.
I know coating options11 are effective as they make products look really appealing and durable.
Thermal Treatments
Thermal treatments work like magic. The first time I used annealing felt magical; carefully heating plastic removes internal stresses, leaving a smoother surface.
- Annealing: Involves heating the plastic to reduce internal stresses and improve surface quality.
- Flame Polishing: Uses a flame to quickly smooth the edges, suitable for certain thermoplastics.
Always think about the material’s thermal properties first when choosing thermal techniques12.
Mechanical Surface Finishing
Sometimes, a mechanical solution is necessary. Vibratory finishing becomes my go-to method; it’s like a mini rollercoaster ride for your product inside a drum with abrasive elements, making surfaces beautifully smooth.
- Tumbling: Involves rotating parts in a drum with abrasive media to smooth surfaces.
- Blasting: Uses high-pressure streams of particles for surface refinement.
Exploring various mechanical methods13 feels like having countless solutions ready for any challenge. By experimenting with these post-processing techniques, I’ve witnessed dramatic improvements in my molded products. It’s about finding what suits your material and design needs. So, see those irritating parting lines? Remember, you have the skills to handle them!
Sanding is the primary method for reducing parting lines.True
Sanding uses abrasives to remove excess material along parting lines.
Thermal treatments are ineffective for parting line reduction.False
Thermal methods like annealing and flame polishing reduce parting lines.
Conclusion
Optimize mold design, adjust injection parameters, select suitable materials, maintain clean molds, and utilize post-processing techniques to minimize parting line traces in injection molded products.
-
Understand how proper gate positioning can minimize parting lines and enhance product quality. ↩
-
Learn effective strategies for placing parting lines to minimize visual impact on finished products. ↩
-
Gain insights into adjusting parameters to reduce defects and improve injection molding quality. ↩
-
Discover how post-processing can enhance product appearance by reducing visible mold lines. ↩
-
Discover methods to maintain a clean mold surface, crucial for reducing impurities that affect parting line formation. ↩
-
Gain insights into effective strategies tailored to specific projects to minimize parting lines. ↩
-
Understanding what parting lines are can help in identifying methods to minimize them. ↩
-
Discover software that can simulate material behavior to optimize mold design. ↩
-
Explore various techniques to enhance the quality of injection molded parts. ↩
-
Discover effective polishing techniques tailored for plastic molding to enhance product surface quality. ↩
-
Explore various coating options to enhance the appearance and durability of plastic surfaces. ↩
-
Learn about thermal treatment methods that effectively reduce parting lines in molded products. ↩
-
Understand different mechanical finishing methods to enhance the surface quality of molded products. ↩