Dealing with incomplete products in injection molding frustrates many people. This problem is very common. Short shots cause headaches for manufacturers.
Adjusting injection pressure is very important to stop short shots in injection molding. Manufacturers need to study product shape and material details. They probably also need to adjust mold design for better results. This helps fill the mold completely. Correct pressure stops defects. It compensates for material thickness and complex mold shapes.
Understanding injection pressure is important, but it’s only one part of the whole picture. I recall my first project when I needed to think carefully about the product’s shape and what it was made of. That changed everything for me. Explore how smart mold design can really help get rid of short shots. This also increases efficiency in how you produce things.
Increasing injection pressure reduces short shots.True
Higher pressure ensures complete mold filling, reducing defects.
Injection pressure has no effect on short shots.False
Pressure is crucial for compensating material viscosity and geometry.
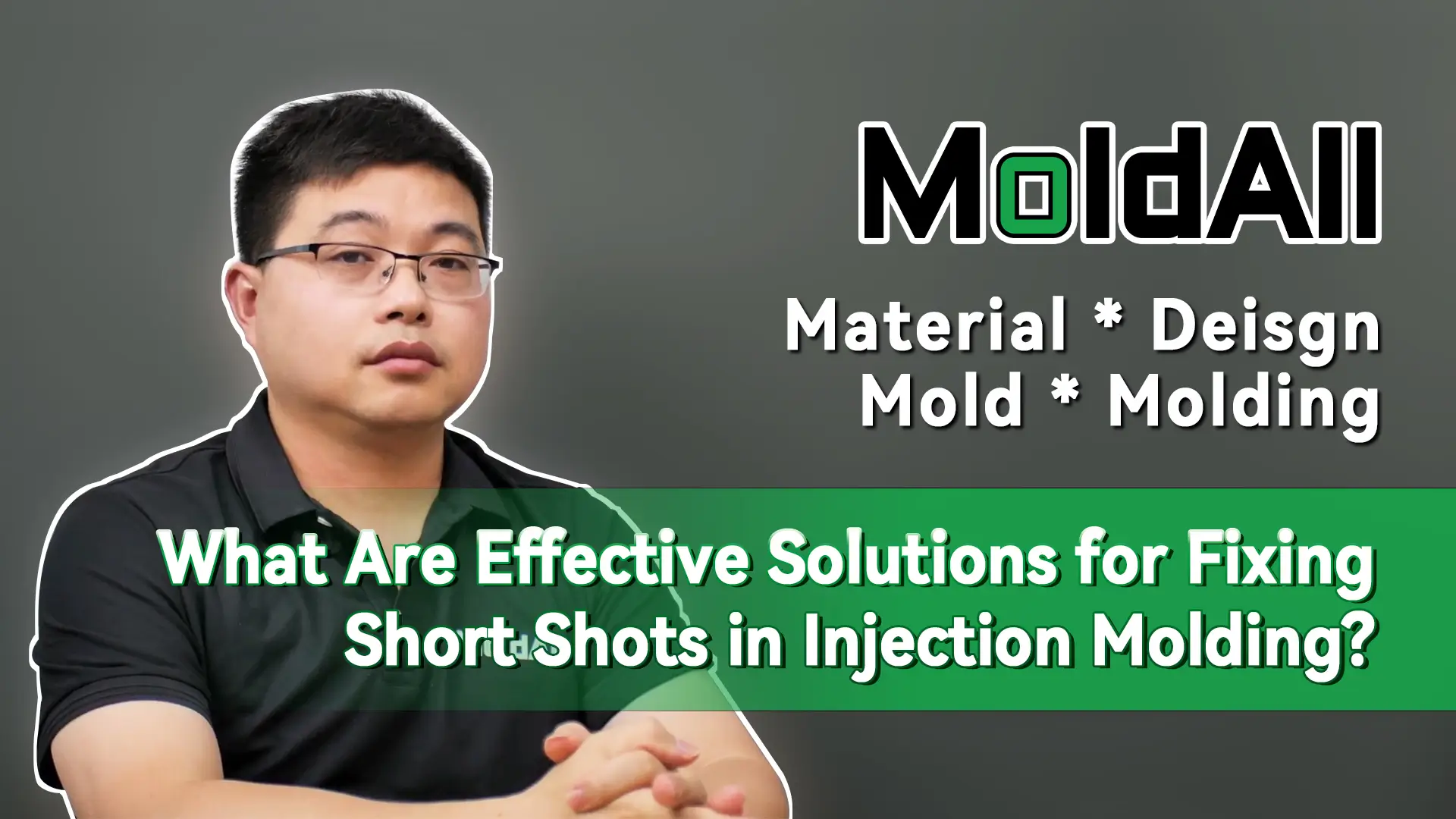
How Does Product Structure Impact Short Shots in Injection Molding?
Do you ever think about how a product’s design affects its production? Let’s explore injection molding and discover how the shape of a product is vital in avoiding problems like short shots. The important role of product design cannot be ignored.
Product structure greatly affects the chance of short shots in injection molding. Key design factors, like wall thickness and complexity, determine how well material fills the mold. This impacts defect rates.
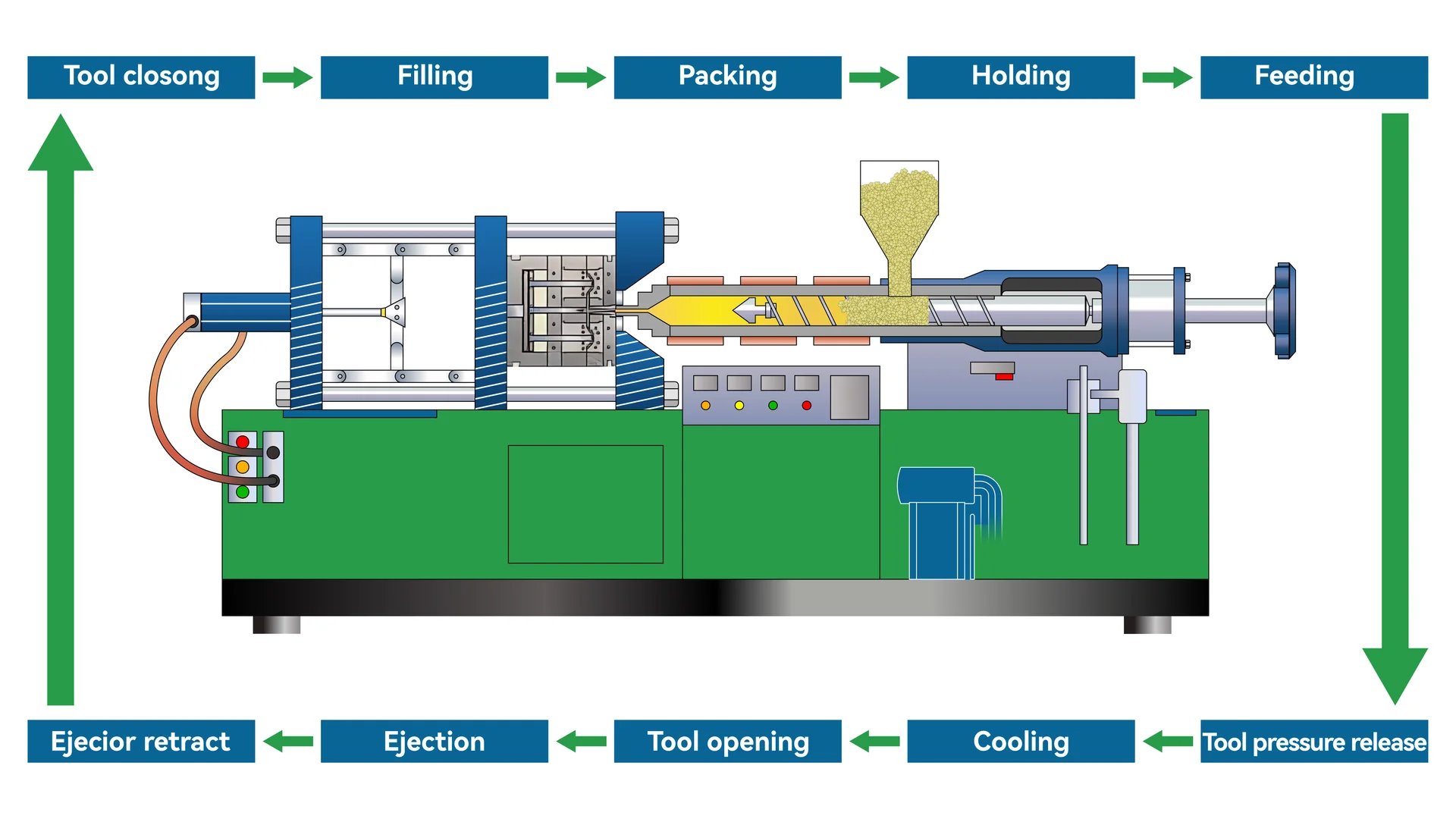
Understanding Product Structure’s Influence
In learning about injection molding, I discovered that product structure goes beyond shape and size. It involves a relationship between these elements and material traits, plus mold design1. Think of filling a slim, long tube with honey; improper technique leads to gaps or air bubbles. That is what we try to avoid – short shots.
Importance of Wall Thickness
I once worked on a project with very thin-walled parts. At first, it seemed easy until uneven fill patterns appeared. For walls only 1-2mm thick with over 50mm flow length, we found increasing the injection pressure by 30-50% helped fill smoothly. Detail is vital here. Really vital.
Wall Thickness | Flow Length | Pressure Increase |
---|---|---|
1-2mm | >50mm | 30-50% |
Complexity of Shapes
Tackling complex shapes feels like solving a puzzle. Deep holes or undercuts can disrupt melt flow. Simulation software2 became crucial, allowing us to set the right injection pressure before actual production.
Material Properties Interaction
Different materials act differently under heat and pressure. High-viscosity materials like polycarbonate (PC) need higher injection pressures. Adjusting barrel temperatures from 260℃ to 280℃ let us lower injection pressure by 10-20%. This was a significant insight for defect prevention3.
Material | Initial Temp | Adjusted Temp | Pressure Reduction |
---|---|---|---|
PC | 260℃ | 280℃ | 10-20% |
Optimizing Mold Design and Parameters
The runner system is another complex piece. Correct runner diameter is essential; too small causes issues. Smaller products suit a runner diameter of 3-5mm, while larger items might need 8-12mm. Hot runners play a crucial role, preserving melt temperature and cutting injection pressure by 10-30%.
Additionally, gate design matters greatly. Picking gates with minimal resistance – like side gates – and placing them near thin-walled zones greatly aids melt distribution4.
By viewing product structure through these various aspects, I predict and lessen short shot risks during production very effectively.
Thin-walled parts require increased injection pressure.True
Parts with 1-2mm thickness need 30-50% more pressure for proper fill.
High-viscosity materials need lower injection pressures.False
High-viscosity materials like PC require higher injection pressures.
How Do Material Properties Influence Injection Pressure Requirements?
Some injection molding projects have problems, while others work smoothly. The reason is understanding the materials used.
Material characteristics such as thickness and crystal formation directly influence the pressure required in molding. High-thickness materials need greater pressures. Crystalline materials involve changes based on how fast they form crystals. Crystal growth really requires adjustments.
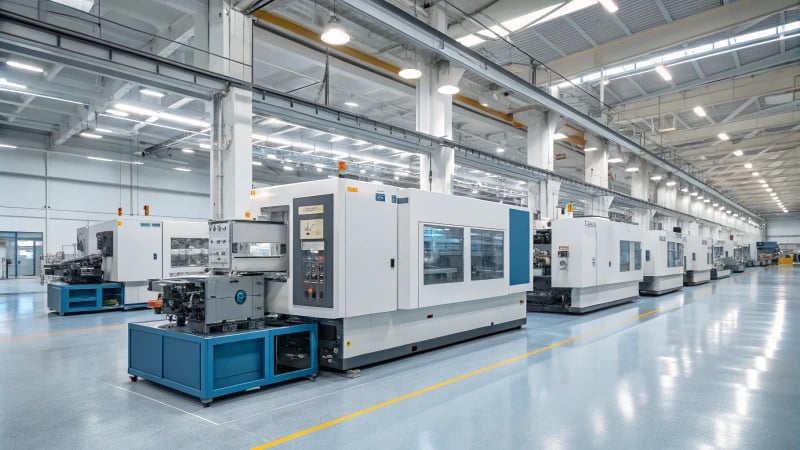
Viscosity and Its Impact
The viscosity of a material significantly influences the injection pressure required. High-viscosity materials once challenged me. Imagine trying to pour thick honey on a cold day; it just moves so slowly. Materials like polycarbonate (PC) and polyphenylene ether (PPO) have high viscosity, making them prone to short shots due to poor fluidity. For these materials, injection pressures should be increased to ensure complete cavity filling. Adjusting barrel temperature can also help reduce viscosity, potentially lowering the required pressure by 10-20%.
Material | Viscosity Level | Recommended Adjustment |
---|---|---|
Polycarbonate | High | Increase temperature |
Polyphenylene Ether | High | Increase temperature |
Crystallization Effects
Working with crystalline materials like nylon (PA) and polypropylene (PP) revealed the effects of crystallization during the injection process. Watching how it changed viscosity was both exciting and hard. A fast crystallization speed increases viscosity, necessitating higher injection pressures to prevent premature solidification before the melt fully fills the cavity.
Consideration of the crystallization process5 is essential. It helps in determining precise adjustments needed in pressure settings to accommodate these changes.
Product Structure Considerations
Evaluating product structure can feel like solving a puzzle, especially for designs with uneven wall thicknesses. Thin-walled sections require higher pressures to maintain flow over extended distances. A design with wall thickness of 1-2mm and flow length over 50mm may require a 30-50% increase in injection pressure.
Deep holes, undercuts, and ribs add complexity to product design, increasing melt flow resistance. Luckily, simulation software helps predict these challenges by analyzing structures to estimate appropriate pressure levels.
Optimizing Mold Parameters
Optimizing mold design is also important as it significantly impacts injection pressure requirements. Getting runner diameters and gate types right reduces flow resistance greatly. Hot runner systems are like secret weapons; they keep the melt warm, lowering cooling risks and needed pressures by up to 30% compared to cold systems.
- Runner Size: Small diameters mean more resistance
- Hot Runner System: Maintains melt temperature, reduces cooling risks
Further Considerations
In mold design and material picking, gate position and mold venting are crucial—it’s like finding the right key for a lock. Everything must fit well to avoid issues.
By wisely looking at product structure6 and material traits, designers can fine-tune injection parameters for optimal results.
High viscosity materials require increased injection pressure.True
Materials like polycarbonate need higher pressure due to poor fluidity.
Hot runner systems increase the required injection pressure.False
Hot runner systems maintain melt temperature, reducing pressure needs.
Why is optimizing mold design crucial for eliminating short shots?
Recall the excitement of receiving a new device, only to discover it is flawed. In injection molding, avoiding these flaws begins with improving mold design. This design acts as the secret weapon against product imperfections. Every item emerges flawless right from the start. Perfection from the beginning.
Improving mold design is important to stop short shots. Better flow of materials helps. Less resistance helps too. Study the product structure. Check the material properties. Look at runner systems. Design gates well. These steps lead to efficient injection molding. Efficient molding is key.
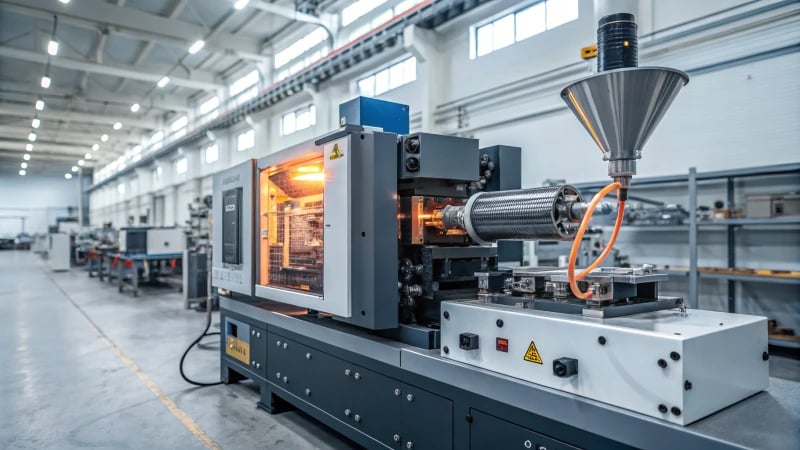
Evaluating Product Structure and Material Properties
I remember my first big task at a mold design company. I needed to discover why new sleek phone cases kept coming out incomplete. The problem was uneven wall thickness causing short shots. Thin parts needed more pressure for proper filling. It is important to focus on both the thickness and flow length of these areas. Thin structures with 1-2mm thickness and flow lengths over 50mm often require a big increase in injection pressure – sometimes by 30-50%.
Complex shapes with deep holes and ribs block the melt flow. Simulation software really helps determine the right injection pressure. Material properties matter too. High-viscosity materials like polycarbonate (PC) really challenge fluidity. Raising the barrel temperature from 260°C to 280°C can lower the pressure needed by 10-20% without losing quality.
Runner System Optimization
Fixing the runner system feels like solving a puzzle. In a small batch of plastic toys, the runner diameter was too narrow, causing flow resistance. Adjusting is key. Small products often need 3-5mm diameters, while larger ones might need 8-12mm. Smooth surfaces reduce friction, helping melt flow.
Switching to a hot runner system has really changed many projects for me. It keeps the melt at the right temperature, reducing solidification risk and lowering injection pressure by up to 30% compared to cold runners.
Gate Design and Adjustment
Gate design is often a tricky issue. Pin-point gates reduce surface traces but increase resistance. In one project, changing to side gates lowered short shots significantly. Adjusting gate size is just as crucial. A small change from 0.8mm to 1.2mm in diameter made a major difference.
Gate Type | Resistance | Adjustment Suggestion |
---|---|---|
Pin-point | High | Consider side gates |
Side | Moderate | Increase diameter |
Latent | Low | Optimize position |
Improving Mold Exhaust Systems
Mold exhaust systems play a very important role in avoiding trapped air that causes short shots. In one memorable task, adding venting grooves of 0.02-0.05mm at parting surfaces greatly improved airflow.
Breathable steel components are really effective for enhancing venting efficiency, reducing short shot risks significantly.
Optimizing mold design is not just about making things fit; it involves balancing structure, materials, runner systems, gate designs, and exhaust systems to achieve a perfect product every time.
For more on these techniques, explore mold design resources7.
Increasing barrel temperature reduces viscosity in polycarbonate.True
Higher temperatures lower viscosity, aiding material flow and reducing short shots.
Hot runner systems increase injection pressure by up to 30%.False
Hot runners decrease injection pressure by up to 30%, improving melt flow.
How Can Advanced Simulation Software Help with Pressure Adjustments?
Visualize having the ability to adjust and refine product designs without ever handling a real-life model.
Advanced simulation programs, such as CFD tools, give engineers a digital space to test pressure changes. Engineers imitate real-life situations with these tools. This technology helps in checking product designs and material traits. Performance and efficiency improve. Performance and efficiency really improve.
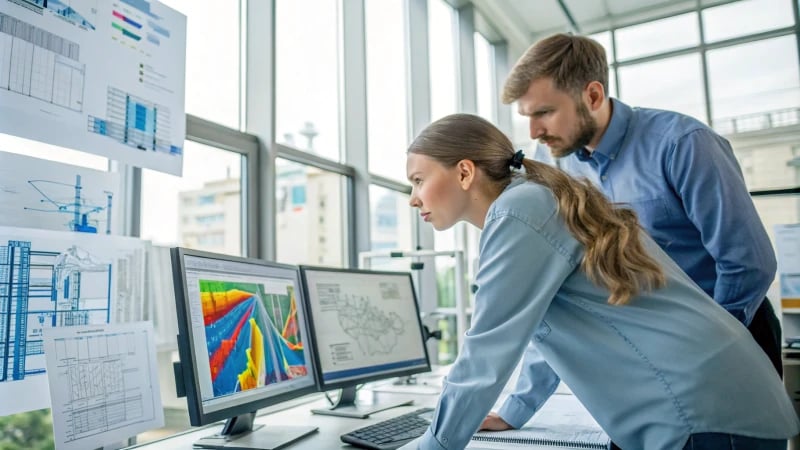
Understanding Simulation Software’s Role
Advanced simulation software amazed me like a magic wand for solving engineering problems. Tools like Computational Fluid Dynamics (CFD)8 opened new worlds where testing pressure settings in a virtual space was possible. It felt very much like a high-stakes video game, focusing on precision and efficiency instead of points.
Evaluating Product Structure and Material Properties
The software let me explore every tiny detail of product structures. Uneven wall thickness reminded me of filling a balloon with a tiny hole. Yet, simulation helped analyze tricky spots and calculate exact injection pressures. I remember a project with polycarbonate, a material known for high viscosity. By slightly changing the barrel temperature from 260°C to 280°C, the pressure dropped by 15%. These moments showed how essential this technology truly felt.
Material Properties:
Materials with high viscosity, like polycarbonate (PC), often face issues due to poor fluidity. Here is an example:
Material | Viscosity | Temperature Adjustment |
---|---|---|
PC | High | Increase to improve flow |
Optimizing Mold Design
This software excelled in optimizing mold designs. I had trouble with a runner system9 that didn’t work smoothly. The simulation allowed tests on different runner sizes and advised switching to a hot runner system. It felt like a knowledgeable mentor whispering solutions.
-
Gate Design:
Choosing the right gate type and size was hard. I recall switching from a pin-point gate to a side gate during a project. This small change was very impactful, cutting resistance and avoiding short shots. -
Mold Exhaust:
Mold exhaust verification seemed vital like unclogging a drain for smooth operation. Using breathable steel components really improved exhaust performance.
Real-World Applications
Industries like automotive and consumer electronics became playgrounds for these simulations. Complex designs felt like puzzles, with deep holes and ribs adding difficulty. Simulation tools were satisfying, pinpointing the precise pressure needed for full cavity filling while cutting costs and time.
In conclusion, using this simulation software mattered not just for efficiency but for peace of mind. It allowed prediction and perfection of designs long before production began.
CFD tools can predict necessary injection pressure accurately.True
CFD tools simulate real-world conditions, allowing precise pressure predictions.
Simulation software reduces trial-and-error in physical testing.True
Simulations optimize designs virtually, minimizing the need for physical tests.
Conclusion
Adjusting injection pressure, optimizing mold design, and understanding material properties are crucial for preventing short shots in injection molding, ensuring complete cavity filling and reducing defects.
-
Explore how mold design impacts injection molding efficiency and defect rates. ↩
-
Learn about the challenges complex shapes present in the molding process. ↩
-
Understand the role of material properties in determining molding conditions. ↩
-
Discover why proper gate design is crucial for achieving high-quality molds. ↩
-
Understanding crystallization helps adjust pressures accurately, preventing defects. ↩
-
Assessing structure ensures optimal pressure settings, reducing defect risks. ↩
-
Learn advanced techniques for mold design optimization to enhance product quality. ↩
-
Understand how simulation tools analyze uneven wall thickness, aiding in pressure estimation. ↩
-
Discover ways to optimize runner systems for better melt flow using simulations. ↩