Ever wonder why your products aren’t fitting together just right? It might be your injection mold showing its age.
Identify wear and tear in injection molds by noting dimensional deviations, surface quality issues, and reduced shape precision, leading to assembly problems, rough finishes, and irregular product shapes.
I remember the first time I realized my molds were wearing out. It hit me when a batch of products came out with rough surfaces and wouldn’t fit together properly. That’s when I learned that spotting these issues early is crucial. Noticing tiny scratches or increased filling pressure can save you from larger headaches down the line. Once, I spent hours trying to figure out why my production was slowing only to discover that the filling time had extended due to wear. Keeping an eye on these changes can help maintain efficiency and quality in your production line.
Dimensional deviations indicate mold wear.True
Dimensional deviations are a common sign of wear affecting mold precision.
Rough surfaces do not result from mold wear.False
Rough surfaces are a typical defect caused by mold wear over time.
What Are the Early Warning Signs of Mold Wear?
Ever had that moment where something just feels off with your latest project?
Identifying early mold wear signs, such as dimensional deviations and surface quality issues, helps prevent costly repairs and delays, ensuring product quality and manufacturing efficiency.
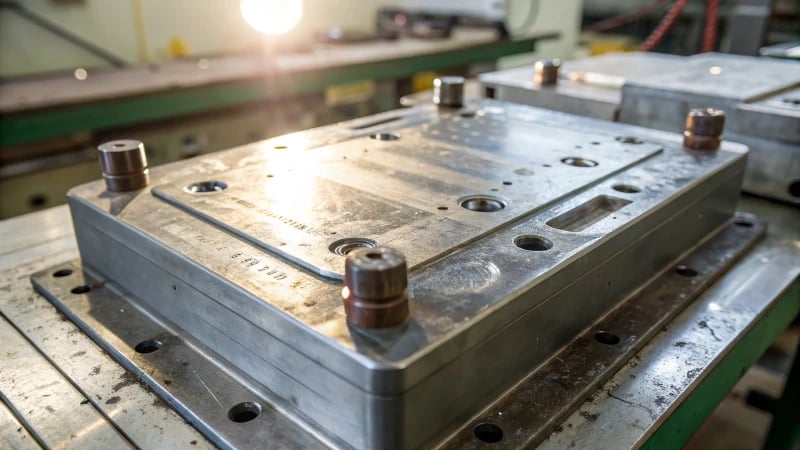
Decline in Product Quality
Let me take you back to the time I was working on a crucial project, crafting parts for a consumer electronics device. I noticed something wasn’t quite right with the fit of our components. That’s when I learned firsthand about the impact of mold wear on dimensional deviation. It was subtle at first—a mere 0.1mm change in the mold cavity size—but enough to disrupt assembly. The lesson was clear: mold wear can sneak up on you and wreak havoc on production.
Dimensional Deviation
In the world of molding, even the smallest deviations can lead to big problems. Imagine the frustration of realizing that a perfectly designed part no longer fits as it should because the mold has worn down. I’ve seen this happen, and it’s a game-changer.
Surface Quality Deterioration
And let’s talk about surface quality. There’s nothing more disheartening than seeing scratches and pockmarks ruining the aesthetics of a product. When the mold’s surface roughness jumps from Ra0.8μm to Ra1.6μm, you end up with lackluster products—quite literally.
Original Roughness | Worn Roughness |
---|---|
Ra0.8μm | Ra1.6μm |
Decrease in Shape Precision
Shape precision is another casualty of mold wear, especially for those high-precision cylindrical shapes that are all the rage in tech design. One day, you’ve got a perfect cylinder, and the next, it’s oddly oval. It’s as frustrating as it sounds.
Abnormalities in the Injection Molding Process
Moving on to the molding process itself, I’ve had my share of battles with increased filling pressure. After mold wear, the once smooth flow becomes a sluggish mess, demanding more pressure—say from 50MPa to 70MPa—to fill every nook and cranny.
Increased Filling Pressure
I’ve watched as the pressure gauge creeps higher and higher, signaling trouble in paradise. It’s like trying to squeeze toothpaste out of a nearly empty tube—frustrating and inefficient.
- Normal Pressure: 50MPa
- After Wear: 70MPa
Extended Filling Time
And don’t get me started on extended filling times. I remember one instance where my team was puzzled over why our production rates were dropping. The culprit? Mold wear slowing down the entire process.
Difficulty in Mold Release
Then there’s the sticky situation of difficult mold releases. I’ve had products stubbornly cling to their molds more times than I’d like to admit, each time risking damage to otherwise perfect pieces.
Changes in Mold Appearance and Parts Condition
Finally, let’s talk about visible signs on the molds themselves. I still recall running my fingers over a worn mold and feeling those tell-tale grooves and scratches.
Mold Surface Wear Traces
These marks are more than cosmetic; they’re clues pointing to deeper issues that could derail production if ignored.
Active Parts Loosening or Stagnation
And when active parts start loosening or stagnating, like sliders becoming wobbly, you know it’s time for maintenance.
For more insights into injection molding process1, I recommend diving into expert opinions and case studies that have saved my bacon more than once when troubleshooting mold wear’s impact on production cycles. Understanding surface quality deterioration2 can also arm you with knowledge to maintain high standards in your work.
Worn molds increase dimensional deviations in products.True
As molds wear, they cause size changes in products, affecting assembly.
Mold wear decreases filling pressure in injection molding.False
Wear increases roughness, requiring more pressure to fill the mold cavity.
How does mold wear affect the injection molding process?
Mold wear isn’t just a technical hiccup in injection molding; it’s a critical concern that can upend quality and efficiency.
Mold wear in injection molding leads to dimensional deviations, surface defects, and increased resistance, affecting product quality. Adjustments in pressure and time are necessary to maintain optimal results.
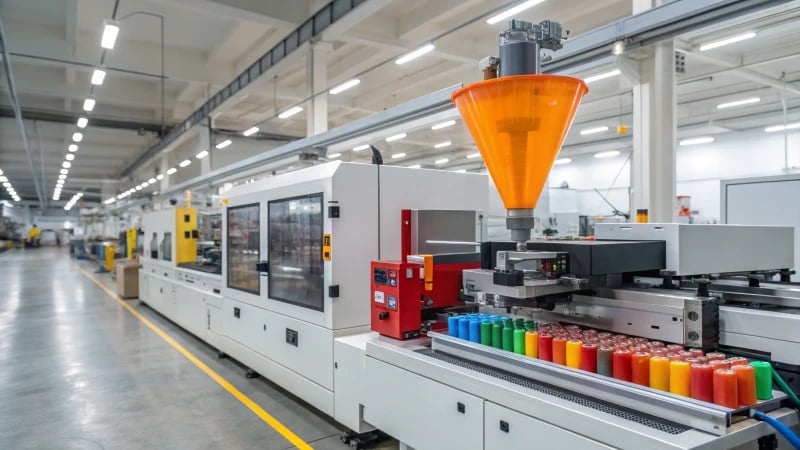
Decline in Product Quality
When I first started dealing with mold wear, it felt like a shadow lurking over my shoulder, subtly affecting everything I did. The quality of the products, once pristine, began to falter. Dimensional deviations were the first red flags—mold cavity sizes would shift, causing parts that should fit together like puzzle pieces to instead mismatch. Imagine expecting a 0.1mm precision and getting a jigsaw piece that just doesn’t fit. Surface quality also took a hit; scratches and blemishes appeared where smooth finishes once gleamed. I remember running my fingers over the product surface, feeling the coarseness that wasn’t there before.
Abnormalities in the Injection Molding Process
Addressing these problems felt like trying to fix a leaky boat while still sailing. Mold wear increased filling pressure requirements because the once-smooth paths for the plastic became rough and resistant. We had to crank up the pressure from 50MPa to 70MPa—no small feat when you’re trying to keep production costs down. Fill times extended too, stretching from 2 seconds to 3. Every extra second felt like an eternity, eating into efficiency and material quality. Mold release difficulties became another thorn; products started sticking stubbornly, and pulling them free risked damage. It’s like trying to pull a stubborn cork from a bottle without breaking it.
Changes in Mold Appearance and Condition
Visible signs of wear were unmistakable. I could see the battle scars on the mold—scratches and grooves etched into its surface, evidence of countless battles fought and lost against wear and tear.
Mold Part | Wear Signs |
---|---|
Parting surface | Scratches, wear grooves |
Core and cavity contact | Obvious scratches, wear grooves |
Active parts | Looseness or stagnation during movement |
These visible marks told stories of their own, showing us exactly where the mold was struggling. Active parts like sliders began to betray their age too, becoming loose or even stalling during operations. Watching them shake or falter was like seeing an old friend who’s just not what they used to be.
To tackle these challenges head-on, injection molding maintenance3 became our lifeline. Regular inspections helped us nip problems in the bud, prolonging mold life and ensuring we didn’t compromise on quality.
Embracing these strategies has been pivotal in maintaining our molding equipment4 and avoiding costly interruptions,
allowing us to continue producing high-quality outputs with minimal defects.
Mold wear increases injection fill pressure.True
Wear narrows gaps and roughens surfaces, raising melt resistance.
Mold wear improves product surface quality.False
Wear causes scratches and pockmarks, reducing surface quality.
What Changes in Mold Appearance Indicate Wear?
Ever found yourself in a bind when your mold starts showing signs of wear? It’s more than just an inconvenience—it’s a potential production nightmare.
Visible scratches, increased roughness, and grooves in a mold indicate wear, potentially leading to product defects such as dimensional deviations and surface issues.
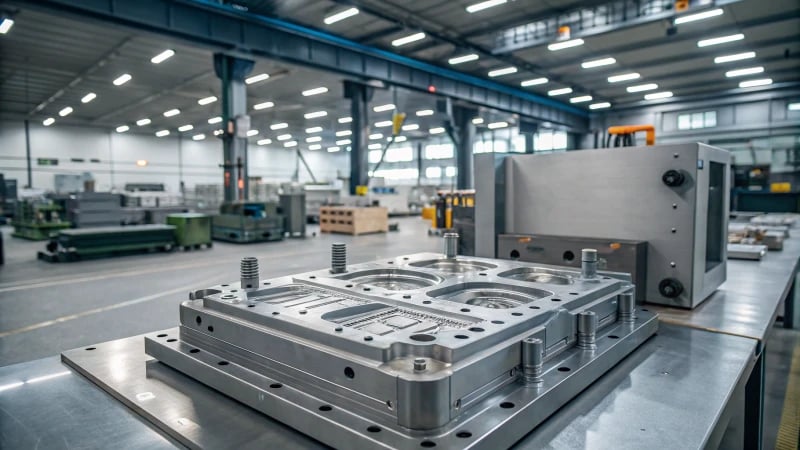
Visual Indicators of Mold Wear
I remember the first time I noticed something was off with one of my molds. It was during a routine check-up when I saw those tiny, almost invisible scratches on the parting line. That’s when it hit me—these were the first signs of wear. When molds start showing these physical changes, it’s like they’re whispering, "Hey, I need some attention!" Scratches and wear grooves5 are not just cosmetic issues; they signal deeper problems.
Mold Feature | Wear Indicator |
---|---|
Parting Line | Scratches |
Cavity | Roughness |
Core | Grooves |
These marks are crucial as they help predict how the quality of my products might start going downhill.
Impact on Product Quality
It’s a bit like that time my favorite sweater got a snag—it just wasn’t the same after that. When a mold wears out, the product quality nosedives too. Dimensional deviations become a real headache. I once had a mold cavity wear by 0.1mm, and suddenly, my products weren’t fitting together anymore.
Another indicator is the deterioration of surface quality6. Imagine your product losing its shine and appeal due to defects like pockmarks.
Injection Molding Process Anomalies
Mold wear also throws a wrench into the injection molding process. I remember being baffled when the filling pressure spiked from 50MPa to 70MPa. It was like trying to push through quicksand! This meant increased resistance during the filling phase and even extended filling times, affecting efficiency and product integrity.
Process Parameter | Normal Value | After Wear |
---|---|---|
Filling Pressure | 50MPa | 70MPa |
Filling Time | 2 seconds | 3 seconds |
Changes in Active Parts
If you’ve ever had a door that creaks every time it opens, you’ll know what I mean when I say wear affects active parts too. For molds with components like sliders or tilt tops, wear means these parts might not move smoothly anymore. Spotting these changes early on can save me a lot of trouble down the line, preserving both the mold’s life and the consistency of my product quality.
Scratches on mold indicate wear.True
Scratches on the mold surface are a clear sign of wear.
Increased filling pressure is unrelated to mold wear.False
Mold wear increases resistance, raising filling pressure.
How can you prevent and manage mold wear efficiently?
Ever stared down at a product and thought, "This doesn’t quite look right?" Mold wear might be the culprit. I’ve learned that understanding how to tackle it head-on can save a lot of headaches.
Prevent mold wear through proper maintenance, durable materials, and precise controls. Manage wear with regular inspections and promptly addressing issues to minimize repair costs and downtime.
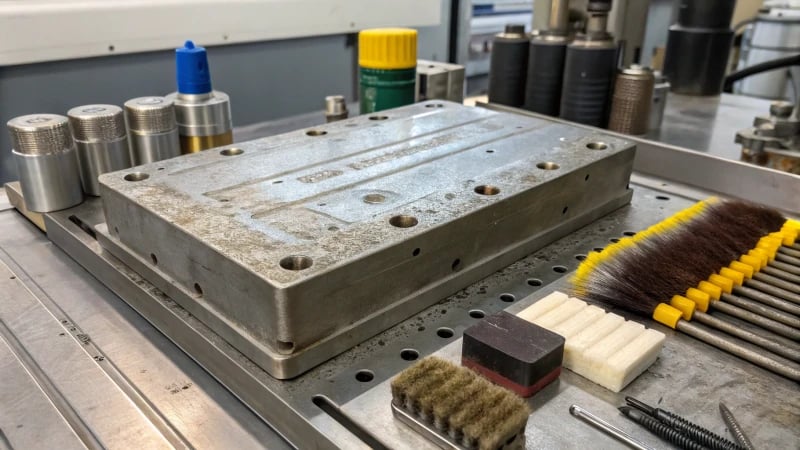
Key Strategies for Prevention
-
Regular Maintenance: I’ve seen firsthand how a little regular check-up can make all the difference. It’s like the old saying goes—an ounce of prevention is worth a pound of cure. By inspecting mold components routinely, you can spot early wear patterns that, if left unchecked, could spiral into something much bigger.
-
Material Selection: Think of it like picking out a good pair of boots—you want something that can withstand a lot of wear and tear. Choosing high-strength alloys for mold construction can help molds endure repeated use without significant deterioration.
-
Environmental Control: Maintaining optimal environmental conditions is like setting the perfect thermostat at home—just right to keep things from going haywire. Controlling temperature and humidity levels helps minimize mold expansion and contraction, preventing excessive wear.
Managing Mold Wear Effectively
-
Timely Inspections:
- Regular checks are your first line of defense against wear, catching things like scratches and grooves before they escalate.
- Utilizing wear detection technology7 can keep you ahead of the game by continuously monitoring mold conditions.
-
Operational Adjustments:
- Adjusting injection parameters, like reducing fill pressure, can help alleviate stress on molds.
- Implementing smart monitoring systems8 to automate adjustments based on real-time data is like having a co-pilot who’s always looking out for you.
-
Replacement of Worn Parts:
- Replacing components showing significant wear maintains precision and quality—think of it as changing the oil in your car to keep it running smoothly.
- Keeping an inventory of essential parts ensures you’re not caught off guard during replacements.
Addressing Quality Decline Due to Mold Wear
-
Dimensional Deviation:
- When I noticed products not fitting together as they should, I turned to precision measuring tools to ensure cavity dimensions stay within tolerance limits.
- Employing advanced simulation software9 for design validation before production has been a game-changer for me.
-
Surface Quality Deterioration:
- Regularly polishing mold surfaces keeps them smooth, just like maintaining a shiny car.
- Applying surface coatings enhances durability and resistance, giving molds that extra layer of protection.
-
Shape Precision Maintenance:
- Conducting regular audits on product shape ensures compliance with design specifications.
- Utilizing CNC machining10 for precise mold component fabrication keeps everything in line with exact specifications.
By weaving these strategies into your routine, you can significantly cut down the risk of mold wear. Consistent updates in technology and practices will further enhance these efforts, ensuring they remain sustainable in the long run. It’s all about staying ahead and keeping things running smoothly.
Regular maintenance prevents severe mold damage.True
Routine inspections help identify early wear patterns, avoiding severe damage.
Ignoring environmental control reduces mold wear.False
Controlling temperature and humidity is crucial to minimize mold wear.
Conclusion
Identify signs of wear in injection molds, including dimensional deviations, surface defects, and increased filling pressure, to maintain product quality and manufacturing efficiency.
-
This link offers detailed insights into how the injection molding process impacts final product quality and efficiency. ↩
-
Clicking this link will provide valuable information about how surface quality deterioration influences manufacturing processes and outcomes. ↩
-
Learn how to properly maintain your injection molding equipment to prevent mold wear and extend its lifespan. ↩
-
Discover why regular inspections are vital for maintaining mold performance and avoiding defects. ↩
-
Provides visual examples of scratches and grooves indicating wear on molds. ↩
-
Explains how mold wear affects product surface quality and potential defects. ↩
-
Discover innovative methods for continuous mold condition monitoring to preemptively address wear issues. ↩
-
Explore how smart systems automate process adjustments based on real-time data, optimizing mold usage. ↩
-
Learn about advanced tools that validate mold designs, ensuring precision and reducing potential wear. ↩
-
Understand how CNC machining provides precision in fabricating mold components, enhancing longevity. ↩