Ever thought about what it takes to create the ideal injection molding process?
I look at the product’s shape, material qualities and mold performance to decide the right pressure for an injection molding machine. Correct pressure helps fill every part and stops flaws. Proper pressure optimizes how the material moves and keeps the mold lasting longer. Mold durability matters a lot.
It sounds easy, right? But achieving the perfect injection pressure is a complicated task involving many details. Each new design pushes me to explore deeply – considering different materials and the special challenges of complex shapes. It’s like putting together a puzzle where every change brings perfect production closer. Let’s look into those exact changes that lead to success.
Thin-walled parts require higher injection pressure.True
Thin-walled parts need higher pressure to ensure complete filling before cooling.
Polyethylene requires high injection pressure due to low fluidity.False
Polyethylene has good fluidity, allowing for lower injection pressures.
How Do You Determine Injection Pressure Settings?
Ever thought about how the correct injection pressure changes a product’s quality? Discover the basics every mold designer needs to understand.
Pressure settings for injection molding depend on product shape, material thickness, mold design and the quality of the final product. Fine-tuning these settings fills the mold completely. This step is very important to reduce flaws. This is crucial for success in molding.
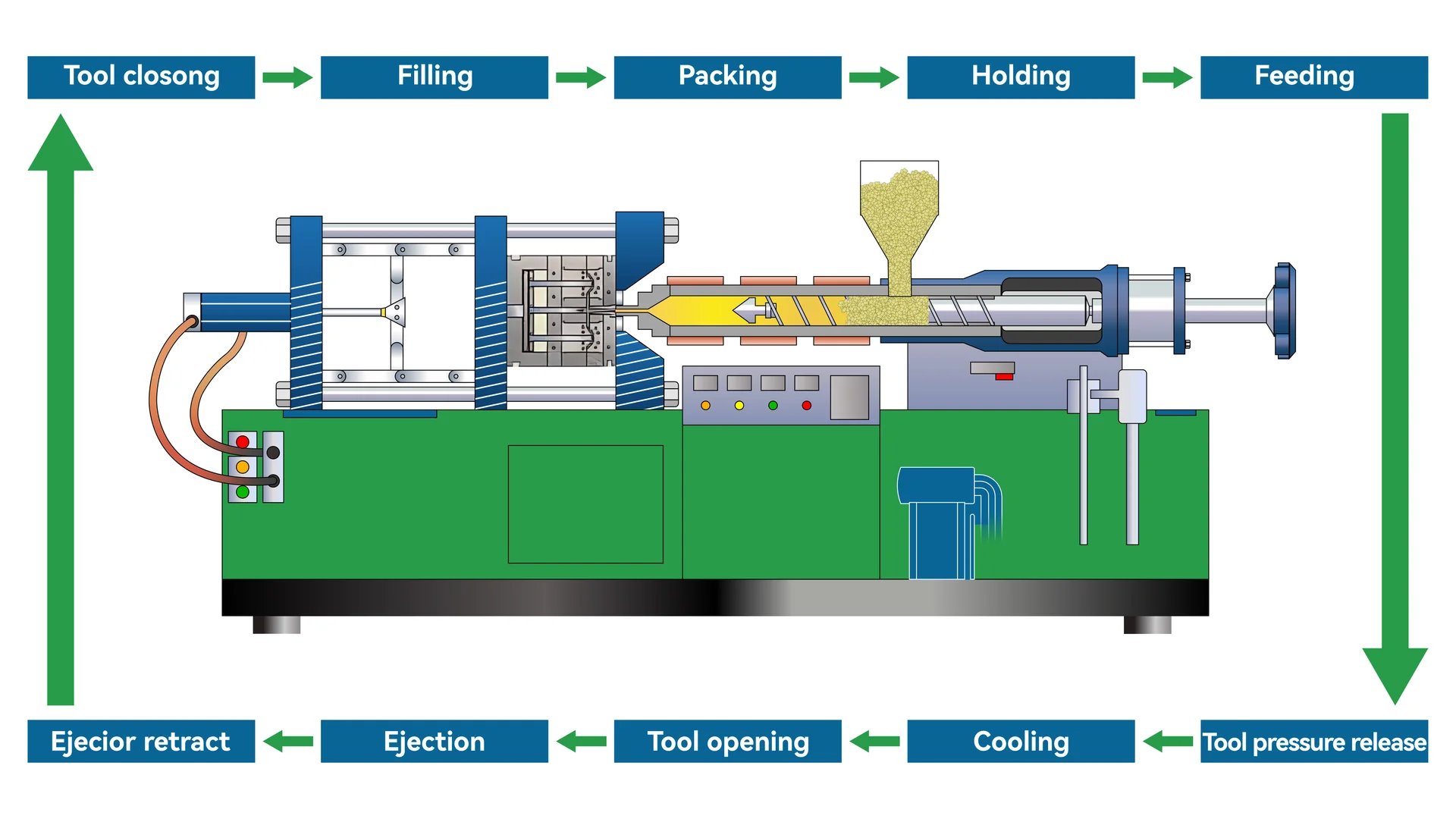
Product Shape and Structure
One project I worked on involved thin-walled plastic containers. Thin sections needed filling before cooling. Adjusting pressure to the right level was nerve-wracking but brought satisfaction. For thick-walled items, the focus shifts. Filling should be gradual and even, without air bubbles to keep them strong.
Product Type | Injection Pressure |
---|---|
Thin-walled | Increased Pressure |
Thick-walled | Gradual Filling |
Material Properties
I often check material specifications. Each type acts differently. Polyethylene flows easily with less pressure, while polycarbonate needs higher pressure to work well. Knowing the flow traits of each material is important—very important.
Material Examples:
- Polyethylene: 40 – 80 MPa
- Polycarbonate: 100 – 140 MPa
Material fluidity1 decides project success.
Preventing Product Defects
Too much pressure causes flying edges or bad flow marks. It’s like finding the ‘just right’ in Goldilocks’ tale. Transparent products, like fancy electronics cases, need smooth surfaces—pristine surfaces are essential.
Defect Type | Pressure Impact |
---|---|
Flying Edges | Lower Pressure Needed |
Surface Defects | Avoid High Pressure |
Mold Performance
Mold design works wonders—or causes issues. I often rethink pressure settings to avoid mold damage. Using 80-90% of mold capacity helps it last longer and keeps product quality.
Considerations include:
- Mold Material Strength
- Gate and Runner Design
Balancing pressure in complex molds is a real challenge. It’s necessary to avoid component damage while managing resistance.
Each of these factors is vital for molding success. Attention to detail leads to excellent, defect-free products.
Thin-walled parts need higher injection pressure.True
Thin-walled parts require higher pressure to fill before cooling.
High viscosity materials need low injection pressure.False
High viscosity materials need high pressure to fill cavities.
How Does Product Design Influence Injection Pressure?
Do you ever think about why some products turn out perfect while others are flawed? Often, this is due to the delicate balance between design and pressure in injection molding.
Product design affects injection pressure. It controls how material moves and spreads within the mold. Shape, structure and material properties are very crucial. These details decide the pressure needed for full, faultless filling. Pressure depends on them.
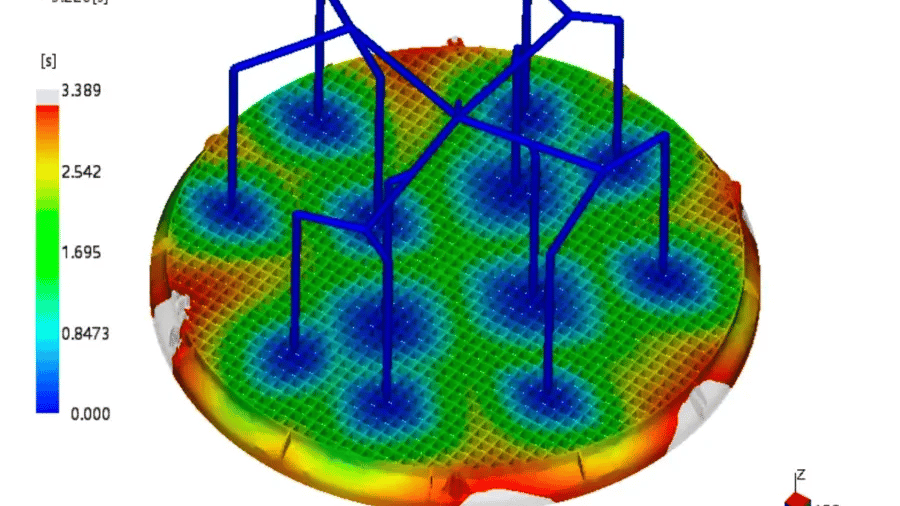
Importance of Shape and Design
The shape and design of a product significantly influence the injection pressure required. I remember the first time I noticed how a product’s shape affected injection pressure. Designing a simple plastic container seemed easy until we tried molding it. Thin walls and intricate parts needed higher pressure to fill the mold before the material cooled. It was a learning process, but understanding this helped us avoid defects, achieving a perfect surface with a flawless finish.
A table detailing different product structures and their typical pressures could be useful here:
Product Type | Wall Thickness | Typical Pressure Range (MPa) |
---|---|---|
Thin-walled | <1 mm | 80-120 |
Thick-walled | >5 mm | 80-120 |
Preventing Quality Defects
I have encountered many issues with quality defects. One time, a project for transparent products had surface flaws; silver lines appeared and ruined the look. Excessive pressure caused unstable flow. Adjusting the pressure helped me keep these marks away, ensuring both quality and appearance stayed intact.
Product design must also account for preventing defects like flying edges or overflow, which occur if the pressure is too high.
Considering Material Properties
Materials behave differently in molding. Different materials require different injection pressures based on their fluidity and viscosity. For example, I used to think one approach worked for all until working with polycarbonate. Its thickness needed much higher pressure compared to more fluid materials like polyethylene.
This variability is illustrated below:
Material | Fluidity | Typical Pressure Range (MPa) |
---|---|---|
Polyethylene | High | 40-80 |
Polycarbonate | Low | 100-140 |
Variety in materials requires varied approaches.
Factors in Mold Performance
The mold plays a silent but important role in determining necessary injection pressure. Our team once dealt with a tricky runner system needing higher pressure; we had to balance this without breaking the mold—imagine inflating a balloon carefully! Understanding these details helped us set the injection settings just right.
The mold’s gate size, runner complexity, and exhaust system all affect how pressure is applied. Smaller gates or complex runners may need increased pressure, but it’s crucial to avoid surpassing the mold’s strength limits to prevent damage.
For more guidance on these topics, explore resources on mold performance2.
Thin-walled parts need higher injection pressure.True
Thin-walled parts require high pressure to fill before cooling.
High injection pressure prevents all product defects.False
Excessive pressure can cause defects like flow marks and silver lines.
Why is material choice crucial for pressure adjustment?
Visualize dedicating hours to creating an ideal design, then watching it fall apart because of a bad material choice. Choosing the right material matters greatly. It holds significance beyond being a technical choice. It is vital for the strength and lifespan of our creations. This is essential.
Material choice affects pressure control by influencing flow, sealing and wear resistance. Choosing the right materials helps parts endure working pressures and environmental conditions, reducing the chance of breaking. Efficiency probably increases when materials suit the application.
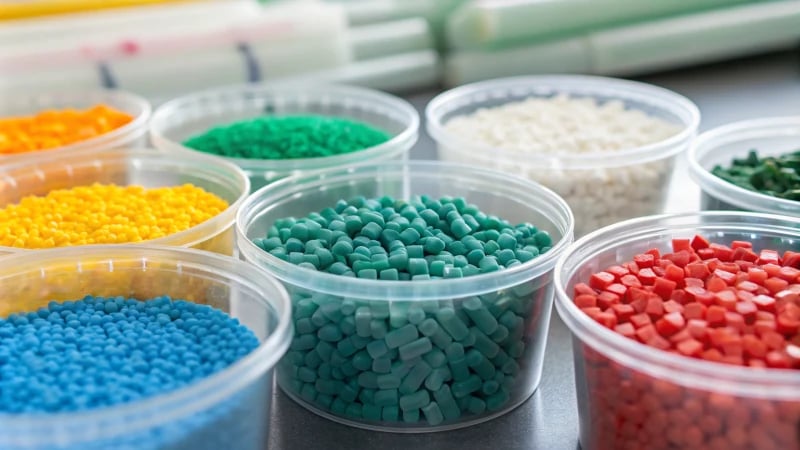
Material Properties and Pressure Dynamics
I recall the first time I understood how important choosing the right material is. During a project with polyethylene, I didn’t expect its high fluidity. It caused a mess, with many defects appearing. This taught me something valuable: materials like polyethylene, which flow easily, need less force to fill without defects. In contrast, working with polycarbonate, which is thick, requires more pressure to avoid empty spaces.
Material | Viscosity | Typical Pressure Range (MPa) |
---|---|---|
Polyethylene | Low | 40 – 80 |
Polycarbonate | High | 100 – 140 |
Temperature sensitivity is also crucial. I discovered that using too much pressure with PVC can cause it to break down. Keeping the right heat while upholding mold strength is very important.
Preventing Quality Defects
Picking the wrong material can be a disaster. Think about crafting a sleek plastic item only to see it ruined by flow marks due to wrong pressure. I have faced silver streaks instead of smooth surfaces. The solution lies in using the right pressure3 to optimize material flow, considering mold and component structure.
- Thin-Walled Structures: Precision in adjusting pressure is crucial to avoid incomplete fills.
- Thick-Walled Products: Filling gradually is vital to stop bubbles or shrinking.
Mold Performance and Material Interactions
The interaction between mold design and material traits adds complexity. I learned how a mold’s details, like gate size or runner complexity, require care in pressure settings. A small gate might need more pressure but can harm the mold if not suited to the material.
Assessing a mold’s toughness against the material’s pressure is crucial. Overstepping can cause expensive damage—a lesson I learned from pushing a mold too far. Aligning materials with what a mold can bear4 is more than durability; it keeps production smooth and mistake-free.
By keeping these aspects in mind, we probably achieve good product quality and production efficiency, avoiding costly mistakes and extending mold life.
Thin-walled parts need higher injection pressure.True
Thin-walled parts require higher pressure to fill before cooling.
High viscosity materials require lower injection pressure.False
High viscosity materials need higher pressure to fill cavities.
How Does Mold Performance Affect Injection Pressure?
Have you ever thought about how mold performance and injection pressure affect your product quality? Quality depends on these factors. They are very important. Sometimes, products look and feel great or they have problems. Mold performance plays a key role. Injection pressure also plays a key role. Bad performance or low pressure leads to poor quality. Good performance and high pressure help create better products. Quality matters. Always.
Mold performance directly influences injection pressure. It sets the exact pressure required to fill a mold cavity properly, avoiding any defects. Mold design plays a big role. Material properties matter too. They are important. Product shape is crucial in finding this balance. High-quality results depend on these factors in injection molding.

The Role of Mold Design
When I first entered the world of mold design, I felt surprised by how small details could change the injection pressure needed. Imagine a mold with twisty runners5 or tiny gates – it feels like trying to push a river through a straw. A lot more pressure is needed to fill every tiny space. However, this pressure must stay within the mold’s limits. Too much pressure could lead to damage.
Material Properties and Their Influence
I worked with different materials and noticed how each one acts in its own special way. Polyethylene flows like a gentle stream, needing less pressure to shape. Polycarbonate is like thick syrup, requiring higher pressure to move smoothly. Learning these traits really helps in setting the right injection settings.
Material Type | Fluidity | Typical Pressure Range (MPa) |
---|---|---|
Polyethylene | High | 40 – 80 |
Polycarbonate | Low | 100 – 140 |
Product Shape Considerations
Thin-walled parts need high accuracy and pressure to fill completely before cooling. Creating these parts is like threading a needle. Thick-walled designs need steady pressure to prevent holes or bubbles. Both shapes present unique challenges.
Mold Integrity and Maintenance
I learned early to respect the mold’s strength. Too much pressure can wear out parts quickly, like ejector pins, and this harms the mold’s life. Regular maintenance checks6 are a must to keep everything working well.
Understanding these elements is like assembling a puzzle. The goal is to find the perfect pressure—not too high to harm molds, not too low to leave spaces. Balance is essential for successful injection molding, and finding this balance is crucial.
Thin-walled parts need higher injection pressure.True
Thin walls require higher pressure to ensure complete filling before cooling.
High viscosity materials require lower injection pressure.False
High viscosity materials need higher pressure to fill the mold cavity.
What Are Common Issues When Setting Injection Pressure?
When I explore injection molding, I often think about the careful balance required to achieve perfection.
Setting injection pressure in molding often brings about problems like incomplete filling, material overflow and harm to the mold. Proper pressure adjustment is crucial. Fully forming parts depends on it. This process reduces defects and helps the mold last longer.
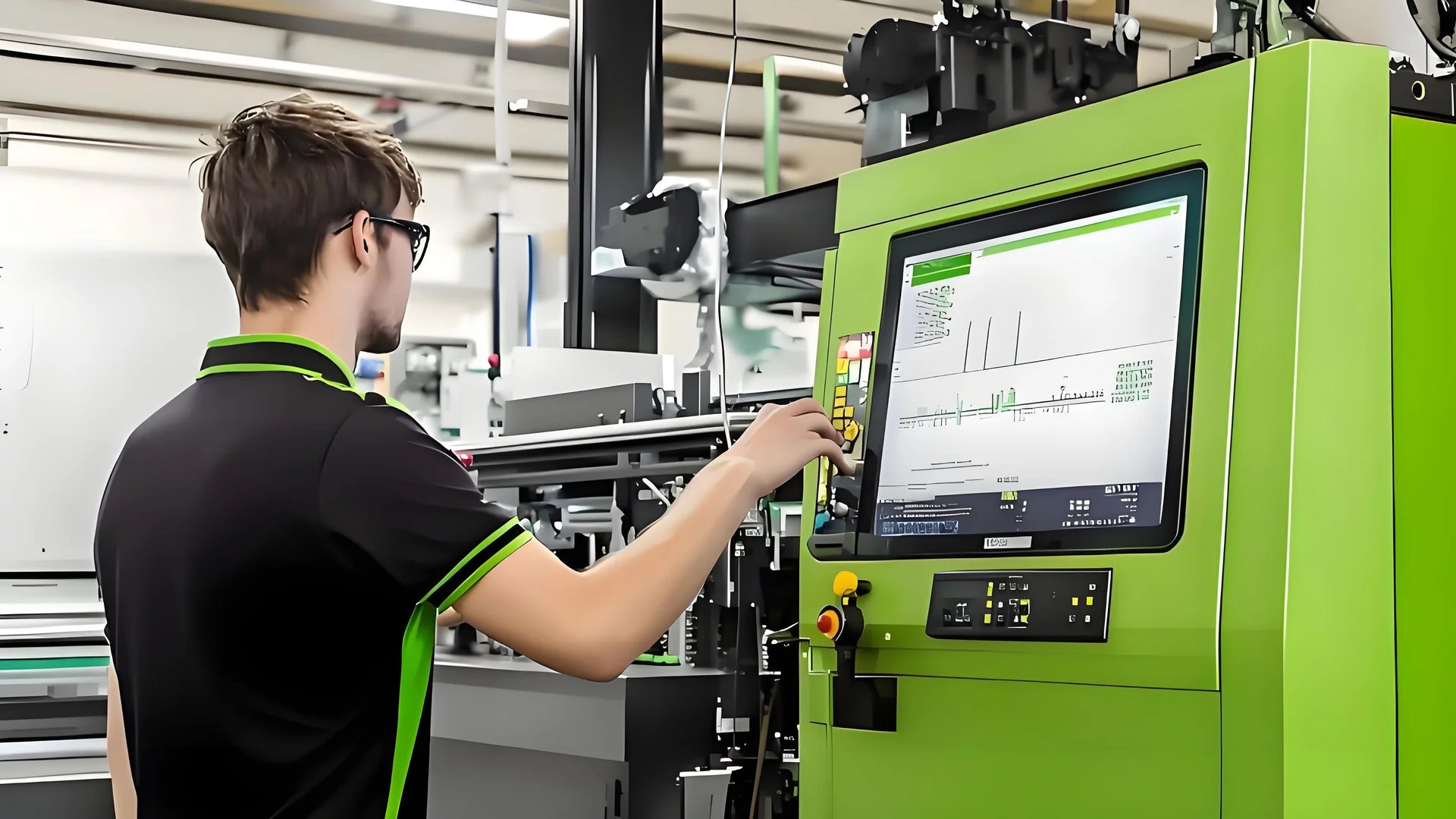
Incomplete Filling of the Mold
Handling incomplete mold filling can be challenging, especially with complex shapes7. Low injection pressure means the melt may not fill every part of the mold, resulting in short shots. Proper pressure adjustment is crucial to capture every detail.
Shape Type | Recommended Pressure Range |
---|---|
Thin-walled | 80-120 MPa |
Thick-walled | 100-140 MPa |
Material Overflow and Defects
Too much pressure causes trouble too. Excessive material can escape the mold, creating flashing. This not only affects aesthetics but can also damage mold components. High pressure might result in surface flaws such as flow marks.
- Tip: With well-flowing materials, use 40-80 MPa pressure to stop overflow.
Mold and Material Considerations
Every material is different. For instance, polycarbonate8 needs more pressure because it is thick. I needed several adjustments to find the correct settings. Molds also have limits; exceeding these can deform them.
- Material Example: Use 100-140 MPa for polycarbonate.
- Mold Lifespan: Never exceed the pressure the mold can handle to avoid harm.
Balancing Pressure and Material Properties
Knowing your material helps a lot, especially for heat-sensitive materials like PVC. High pressure may damage them.
- Recommendation: Use 60-90 MPa pressure for PVC to prevent heat damage.
Understanding these points lets me adjust my methods effectively, improving product quality9. A good balance reduces flaws and extends the life of molds and machines.
Thin-walled parts require higher injection pressure.True
Thin-walled parts need higher pressure to ensure complete filling before cooling.
High injection pressure prevents all product defects.False
Excessive pressure can cause defects like flow marks and silver lines.
Conclusion
Setting injection pressure in molding is crucial for product quality, requiring careful consideration of shape, material properties, and mold performance to prevent defects and ensure complete filling.
-
Understand how material fluidity impacts injection pressure and overall molding efficiency. ↩
-
This link offers detailed information on how mold design elements influence the pressure needed for effective injection molding. ↩
-
Discover techniques to prevent common injection molding defects by adjusting material flow. ↩
-
Understand how to match mold materials with pressure requirements for optimal performance. ↩
-
Exploring this topic helps understand how runner complexity affects pressure requirements, crucial for efficient mold design. ↩
-
Learn why regular maintenance is essential for mold performance, ensuring consistent quality and prolonged mold life. ↩
-
Exploring this link provides insights into handling complex mold shapes, ensuring complete filling without defects. ↩
-
Learn about specific pressure requirements for polycarbonate to avoid common molding issues. ↩
-
Discover strategies to enhance quality by optimizing injection pressure and addressing material properties. ↩