Is your injection mold cooling system ready for improvement? Let’s explore this journey together!
To optimize an injection mold cooling system, select the appropriate cooling method, design even waterway distribution, calculate precise channel sizes, and control flow rates accurately. These strategies ensure effective heat removal, enhancing product quality.
In my early days of mold design, I quickly noticed the importance of the cooling system for excellent quality. Simple cooling methods greatly affect our results. Direct cooling is amazing for easy molds. Complex shapes need smart indirect solutions like cooling rods. Finding the perfect balance is everything! In this blog post, I share insights and strategies that changed my approach. I hope they inspire you to improve your own designs.
Direct cooling methods are always more effective than indirect.False
While direct cooling can be effective, the best method depends on specific mold design requirements and materials used.
Proper flow rate control is essential for efficient cooling.True
Controlling the flow rate of cooling water is critical for maintaining optimal temperatures and improving product quality during the molding process.
- 1. Why Is Effective Cooling Crucial in Injection Molding?
- 2. How Do Different Cooling Methods Affect Mold Performance?
- 3. What Factors Should I Consider When Planning Cooling Waterway Layouts?
- 4. How Can I Accurately Calculate the Size of Cooling Channels?
- 5. How Does Flow Rate Impact Cooling Efficiency?
- 6. How Do Connection and Sealing Designs Impact Cooling System Reliability?
- 7. Conclusion
Why Is Effective Cooling Crucial in Injection Molding?
Have you ever wondered why some products from injection molding look perfect, but others have flaws? Let’s explore the fascinating world of cooling in injection molding. It is very important. This process matters more than you might think!
Effective cooling in injection molding enhances product quality by reducing defects, optimizes cycle times, ensures uniform mold temperatures for consistent shrinkage, and boosts production efficiency.
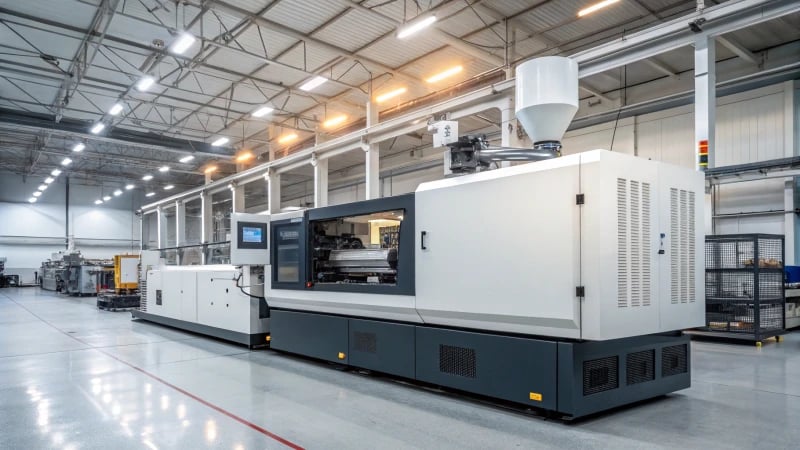
Understanding Cooling in Injection Molding
When I started in injection molding, I quickly saw how vital good cooling is to manufacturing. It’s not only about getting the product out fast; it’s about perfection in every detail, from small curves to the smooth finish. Proper cooling changes a product from disappointing to impressive. I recall a project where bad cooling led to warping—a tough lesson. Grasping how to control cooling not only achieves uniform shrinkage but also cuts down defects like annoying sink marks. Cooling is a crucial step.
Types of Cooling Methods
-
Direct Cooling: I use direct cooling for simple mold shapes often. This method puts cooling waterways right inside the mold, letting water flow near the cavity and absorb heat swiftly. I worked on a small flat mold where waterways helped us finish fast without losing quality. Direct cooling speeds up the process. For more on direct cooling techniques1, click here.
-
Indirect Cooling: With complex molds, I switch to indirect cooling. This uses rods or inserts placed to remove heat effectively. I remember using this on a tough design; seeing it succeed without overheating was satisfying! Learn more about indirect cooling methods2 here.
Layout Planning of Cooling Waterways
A smart design for cooling waterways is vital for heat dissipation.
- Uniform Distribution: Even distribution around the cavity is key. For regular shapes, layouts like a ring or tic-tac-toe can balance cooling. I once designed channels for a round bottle cap mold and seeing those circles was a proud moment.
- Product Shape Consideration: Product shape is crucial; thicker areas need closer channels to avoid shrink marks. On a project with reinforcements, I learned to position channels carefully to prevent slow cooling defects.
Calculating Cooling Channel Size
The size of cooling channels affects cooling efficiency:
Aspect | Details |
---|---|
Diameter | Typically ranges from 6mm to 16mm; larger diameters allow for better flow but occupy more space. |
Length | Must provide sufficient residence time for heat absorption without excessive pressure drop. |
I struggled with the heat balance equation at the start; it’s great for finding the best channel dimensions. Explore more on calculating cooling channel dimensions3.
Flow Rate and Volume Control
Managing cooling water flow has changed my process:
- Flow Rate Control: I keep flow rates between 0.3 – 2 m/s for good heat exchange; too low risks poor cooling while too high means higher costs and pressure issues.
- Flow Calculation: The heat balance equation Q = mc/△T helps calculate flow based on heat load. Delve into flow rate calculations4 for more.
Connection and Sealing Designs
Don’t ignore piping connections:
- Connection Methods: Choose between welding for strength or pipe joints for easier maintenance; each has pros and cons based on needs.
- Sealing Design: A solid seal stops leaks; I tried different materials considering temperature and corrosion resistance. Learn about sealing designs5 here.
Effective cooling reduces defects in injection molded products.True
Proper cooling minimizes issues like warping and sink marks, ensuring higher quality in injection molded items.
Indirect cooling is unnecessary for complex mold structures.False
Complex molds require indirect cooling methods to effectively manage heat without compromising integrity.
How Do Different Cooling Methods Affect Mold Performance?
Do you think about how cooling methods affect the quality of your molded products? Learning about these methods changes the way we deal with manufacturing in injection molding.
Cooling methods significantly impact mold performance by affecting heat transfer, cycle time, and product quality. Optimal layout, sizing, flow control, and seal design are crucial for effective cooling.
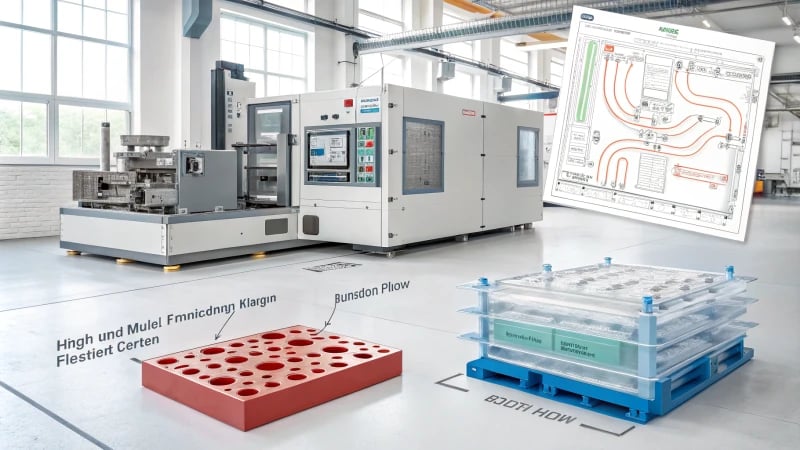
Understanding Cooling Methods in Molding
Cooling methods play a crucial role in the performance of molds, particularly in the injection molding process. The choice of cooling method can significantly impact heat transfer efficiency, cycle times, and overall product quality. Here’s how different cooling methods affect mold performance:
Direct Cooling
Direct cooling is typically employed for simple-shaped molds. This method involves embedding cooling waterways directly into the mold cavity.
- High Efficiency: This method allows cooling water to flow closely along the cavity walls, efficiently absorbing heat.
- Example: In small flat injection molds, evenly distributed cooling waterways on the back of the cavity can rapidly cool the product, reducing cycle times. For instance, cooling efficiency6 can be optimized by designing direct waterways.
Advantages | Disadvantages |
---|---|
High cooling efficiency | Limited to simpler shapes |
Shorter cycle times | Not suitable for complex geometries |
Indirect Cooling
When dealing with complex mold structures where direct cooling is impractical, indirect cooling methods are employed.
- Cooling Rods and Inserts: These are used to transfer heat through conduction from the mold to the cooling medium.
- Example: Metal rods with internal channels can be strategically placed in hard-to-reach areas. This ensures effective cooling while maintaining the mold’s integrity. Exploring indirect cooling techniques7 can help designers like Jacky optimize performance.
Cooling Waterway Layout Planning
Proper planning of the cooling waterway layout is essential for achieving uniform cooling across the mold.
- Uniform Distribution Principle: Evenly spaced waterways ensure that every part of the cavity cools at a similar rate.
- Shape Considerations: For regular shapes, waterways can be designed in circular or grid patterns. For instance, in molds for round plastic bottle caps, concentric circles are effective. You can learn more about waterway design8 here.
Design Type | Application |
---|---|
Circular | Round products |
Grid | Square or rectangular products |
Size Calculation of Cooling Channels
Determining the size and dimensions of cooling channels is critical for effective mold performance.
- Diameter Considerations: The diameter typically ranges from 6mm to 16mm, balancing space and flow efficiency.
- Length Calculations: It should be optimized to provide sufficient residence time for heat absorption without excessive pressure drops. Understanding the size calculation9 is vital for Jacky’s designs.
Flow Rate and Volume Control
Controlling the flow rate and volume of cooling water is crucial for maintaining optimal mold temperatures.
- Flow Rate Management: Ideal flow rates are typically between 0.3 to 2 m/s, ensuring effective heat exchange without energy waste.
- Flow Calculations: Using the heat balance equation helps determine necessary flow rates based on heat load and other factors. Explore more about flow control10 techniques that can enhance cooling efficiency.
Flow Rate Range | Implications |
---|---|
0.3 – 0.5 m/s | Insufficient cooling |
1.0 – 2.0 m/s | Optimal cooling |
Connection and Sealing Design
The design of piping connections and sealing mechanisms is essential to prevent leaks and maintain system efficiency.
- Connection Methods: Options include welding or using pipe joints; each has its advantages and drawbacks regarding maintenance and robustness.
- Sealing Materials: Selecting appropriate materials that resist temperature variations and corrosion is crucial for longevity and reliability. A thorough understanding of sealing designs11 can prevent failures during operation.
By addressing these various factors involved in cooling methods, designers can significantly improve mold performance, ensuring high-quality products while optimizing production efficiency.
Direct cooling is more efficient than indirect cooling methods.True
Direct cooling allows for better heat absorption due to close water flow, enhancing efficiency compared to indirect methods.
Cooling channel diameter affects mold performance significantly.True
The diameter of cooling channels impacts heat transfer efficiency and pressure drops, crucial for effective mold operation.
What Factors Should I Consider When Planning Cooling Waterway Layouts?
Designing cooling waterway layouts involves more than technical details. It combines science with art. Every choice I decide truly impacts performance. Explore the important parts that direct my planning process.
When planning cooling waterway layouts, consider the cooling method (direct/indirect), distribution layout, channel size, flow rate, and sealing designs, as these factors significantly impact heat transfer efficiency.
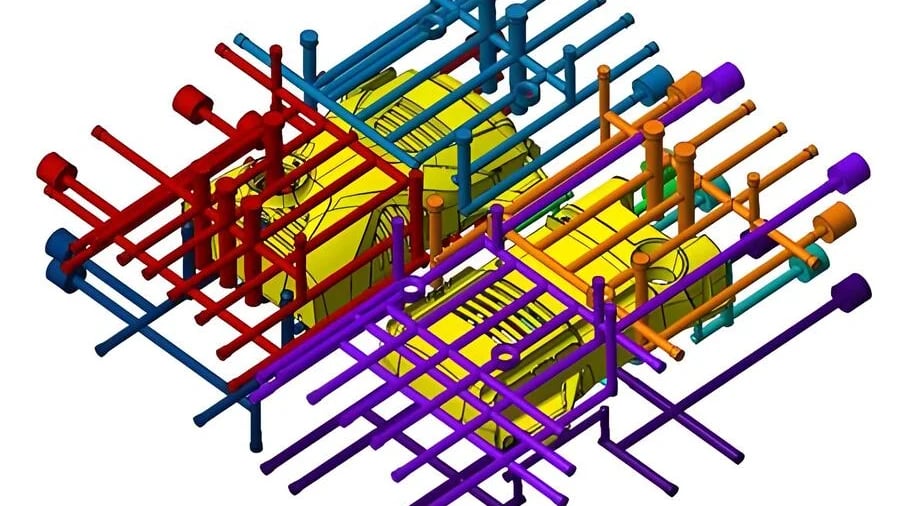
Determine the Cooling Method
When planning a cooling waterway layout, the cooling method is crucial. There are two main approaches:
-
Direct Cooling: This method is effective for simple-shaped molds. It involves placing the cooling waterway directly in the mold cavity to ensure that the cooling water flows close to the cavity wall, enhancing heat transfer.
- Example: In small flat injection molds, evenly distributed waterways at the back of the cavity significantly improve cooling efficiency.
-
Indirect Cooling: This method is used for more complex mold structures. Here, cooling rods or inserts are employed, transferring heat through conduction.
- Example: Metal rods with internal channels can be strategically placed in areas that are difficult to reach directly with cooling waterways.
Cooling Waterway Layout Planning
The layout of cooling waterways must follow specific principles to ensure effective cooling:
- Uniform Distribution: To achieve even cooling across all parts of the mold, waterways should be arranged uniformly around the cavity.
- For Regular Shapes: Molds with symmetrical designs (like round or square) can have concentric or grid-like arrangements of waterways.
- Product Shape Characteristics: The design should consider the product’s shape and wall thickness.
- Example: For products with thicker walls, placing waterways closer to those areas can help reduce cooling times.
Shape Type | Recommended Waterway Design |
---|---|
Regular | Ring or tic-tac-toe pattern |
Irregular | Custom pathways based on geometry |
Calculate the Size of the Cooling Channel
Proper sizing of the cooling channel is vital for optimal performance:
- Determine the Diameter: Typically between 6 – 16mm, depending on the mold size and product requirements. A larger diameter allows for better flow but takes more space.
- Calculate Length: Ensure adequate residence time for cooling without causing excessive pressure drops. The length can be derived from heat balance equations considering several factors, such as:
- Heat capacity of the plastic
- Injection cycle time
- Mold temperature
Consideration of Cooling Water Flow Rate and Volume
The flow rate and volume directly influence cooling efficiency:
- Flow Rate Control: Ideally maintained between 0.3 – 2 m/s to optimize heat exchange. A low flow rate results in inadequate cooling, while a high flow rate may increase energy consumption.
- Flow Calculation: Use the heat balance equation $Q = mc\Delta T$ to determine the necessary flow rate based on:
- Heat load of the mold
- Specific heat capacity of water
Connection and Sealing Design
Effective connection and sealing are critical to prevent leaks:
- Piping Connection Methods: Options include welding and pipe joint connections. Each method has its pros and cons regarding durability and ease of maintenance.
- Sealing Design: Employ materials such as rubber seals that withstand temperature variations and ensure long-term integrity at the interface between pipes and molds.
Connection Method | Advantages | Disadvantages |
---|---|---|
Welding | Strong, durable | Difficult maintenance |
Pipe Joint | Easy to install/remove | May not be as strong |
Direct cooling is best for complex mold shapes.False
This claim is false; direct cooling is effective for simple-shaped molds, not complex ones.
Waterway diameter should be 6 - 16mm for optimal cooling.True
This claim is true; the recommended diameter for cooling channels typically falls within this range for effectiveness.
How Can I Accurately Calculate the Size of Cooling Channels?
Determining the size of cooling channels involves more than just technical work. It plays a very crucial role in the success of my molding processes. Let me explain how I approach this challenge successfully.
To accurately calculate cooling channel size, consider the cooling method, channel layout and design, channel diameter and length, flow rate, and connection design, optimizing each factor for efficient cooling performance.
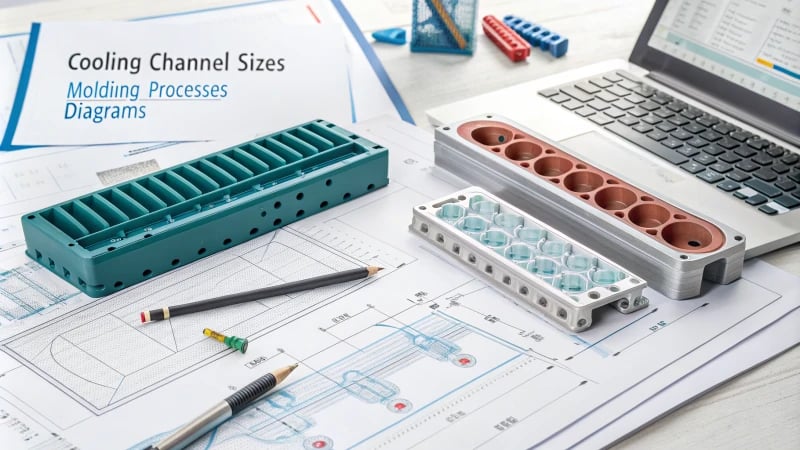
Choosing the Cooling Method
The first step is picking the right cooling method. It really shapes my design.
-
Direct Cooling: This method suits simple-shaped molds. I worked on a project with small flat injection molds. I placed cooling waterways right inside the cavity. Seeing the cooling water flow was really satisfying. It worked efficiently!
-
Indirect Cooling: Sometimes, designs become complex. Direct access is not possible. In such cases, I choose indirect cooling. Once, I used cooling rods in hard-to-reach areas. These rods had internal channels. Watching heat conduction was amazing. It removed heat without direct water flow.
Planning the Cooling Waterway Layout
Next, I plan the layout of cooling waterways. Uniform temperature distribution across the mold is crucial. Precision makes all the difference.
Principle | Description |
---|---|
Uniform Distribution | Evenly distribute waterways around the cavity to ensure all areas cool uniformly. |
Product Shape Characteristics | Designing waterways according to shape is essential; thick areas hold heat longer. |
For example, concentric circular designs work well for round molds like plastic bottle caps.
Calculating the Size of Cooling Channels
Once confident in my cooling method and layout, I calculate cooling channel sizes.
- Determine the Diameter: Diameters usually range from 6mm to 16mm. Larger diameters allow more water flow; however, they also take up space in the mold.
-
Calculate the Length: Length is equally vital; it must absorb enough heat without causing pressure drops. I often use a heat balance equation to guide me:
Q = mc/ΔT
Where:
- Q = heat to be absorbed
- m = mass flow rate
- c = specific heat capacity
- ΔT = change in temperature
Flow Rate and Volume Considerations
Controlling the cooling water flow rate is a game-changer for efficient cooling.
- Flow Rate Control: I aim for a flow rate between 0.3 – 2 m/s. If it’s too low, heat exchange suffers; too high, energy costs rise steeply.
- Flow Calculation: I use heat load and cooling water’s specific heat capacity to find necessary flow rates. Underestimating this can result in inadequate cooling and very anxious moments!
Connection and Sealing Design
Effective piping connections maintain a sealed system.
- Piping Connection Methods: I’ve tried welding and pipe joint methods; each has benefits and drawbacks regarding maintenance and installation.
- Sealing Design: Good sealing prevents leakage by choosing materials that withstand the mold’s conditions; few things ruin a project faster than unexpected leaks!
Considering these details empowers me to calculate cooling channel sizes accurately, optimizing performance in every design I create.
Direct cooling is suitable for complex mold structures.False
Direct cooling is best for simple molds; complex molds require indirect methods.
Cooling channel diameter should range from 6mm to 16mm.True
The diameter of cooling channels typically ranges between 6mm and 16mm for optimal flow.
How Does Flow Rate Impact Cooling Efficiency?
Have you ever thought about why some cooling systems seem almost magical while others have problems? The reason is often something simple but important꞉ the flow rate. This factor plays a big role in cooling efficiency. It is especially important in mold design.
Flow rate significantly influences cooling efficiency by affecting heat transfer and system performance. Optimal flow rates ensure efficient operation and cost-effectiveness by balancing heat removal and energy consumption.
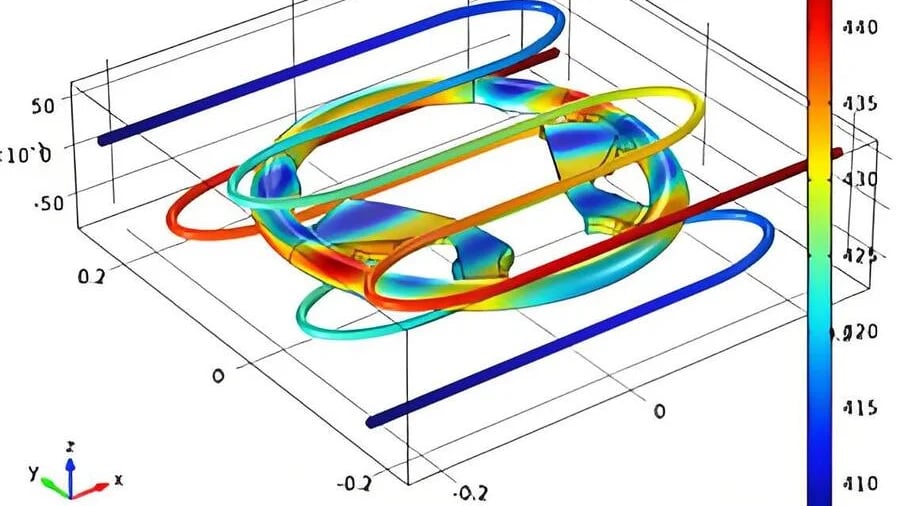
Understanding Flow Rate in Cooling Systems
I truly appreciate the importance of flow rate in cooling systems. Flow rate refers to how much cooling fluid travels through a system in a certain time, usually shown in liters per minute (L/min) or meters per second (m/s). I remember the first time I changed the flow rate in a cooling system; it felt like turning on a switch! The heat exchange quickly became more efficient, and I noticed the quality of molded products improved noticeably.
Flow rate is crucial for heat transfer efficiency in cooling molds. A higher flow rate usually improves heat exchange because more cooling water touches the heated surfaces. However, you need the right balance: an excessively high flow rate causes increased energy costs and unsustainable pressure losses.
Direct vs. Indirect Cooling Methods
Choosing the correct cooling method has been very important for me as a designer. Here’s what I’ve learned:
-
Direct Cooling: Best for simple-shaped molds where cooling waterways directly touch the mold cavity. This allows cooling water to flow close to the cavity walls, efficiently taking away heat. For small flat injection molds, I spread cooling waterways evenly on the cavity’s back, allowing for quick cooling and lovely molded products.
-
Indirect Cooling: Complex molds often can’t use direct cooling. In these cases, I used cooling rods or inserts—metal rods with inside channels that cool through conduction rather than direct flow. This method maintains cooling efficiency even with complex designs.
Importance of Cooling Waterway Layout
Proper planning of the cooling waterway layout is crucial to ensure uniform temperature throughout the mold cavity. Here are key points to consider:
Design Aspect | Description |
---|---|
Uniform Distribution | Cooling waterways should be evenly distributed around the cavity to prevent hot spots. |
Shape Consideration | The layout should reflect the product shape; for instance, concentric circles for round molds. |
Wall Thickness | For uneven wall thickness, waterways should be closer to thicker areas for efficient cooling. |
Flow Rate Control and Its Effects
Keeping a good flow rate is necessary for cooling efficiency:
-
Flow Rate Recommendations: Ideal flow rate ranges from 0.3 to 2 m/s. A low rate can cause poor heat exchange while a high rate leads to unnecessary energy use and higher costs.
-
Pressure Loss: Increased flow rates bring significant pressure losses that affect pump efficiency and overall system performance; balance is key.
Calculating Required Flow Rate
Calculating the needed flow rate based on heat load is very important:
-
Heat Balance Equation: The fundamental equation is:
Q = mc/ΔT
Where:
- Q = Heat (W)
- m = Mass flow rate (kg/s)
- c = Specific heat capacity (J/kg·K)
- ΔT = Temperature change (K)
This equation helps me decide how much cooling water is needed.
Connection and Sealing Design
Good connections and sealing in cooling waterways are crucial for system reliability:
-
Connection Methods: Welding provides strength but complicates maintenance; pipe joints give easier access for repairs and changes.
-
Sealing Materials: Effective sealing prevents leaks and must handle operating temperatures and pressures; choosing the right materials is very important. Rubber seals have been excellent for me, offering long-lasting seals under operational conditions.
Understanding flow rate’s effect on cooling efficiency goes beyond numbers; it involves practical application to design efficient cooling systems. For deeper understanding, these resources are helpful: advanced cooling techniques12 or flow rate calculations13. I’m excited to see how these insights can enrich your projects!
Higher flow rates improve cooling efficiency in molds.True
Increased flow rates enhance heat exchange by maximizing contact between cooling fluid and heated surfaces, improving cooling efficiency in mold applications.
Direct cooling is always more efficient than indirect cooling.False
While direct cooling is effective for simple molds, indirect methods are necessary for complex designs, making direct cooling not universally superior.
How Do Connection and Sealing Designs Impact Cooling System Reliability?
Do you ever think about how tiny design choices really affect a cooling system? Connection and sealing designs play important roles. They are essential in this process. Let me explain why they are so important.
Connection and sealing designs are vital for cooling system reliability, influencing maintenance ease, leak prevention, and performance, ultimately extending system lifespan.
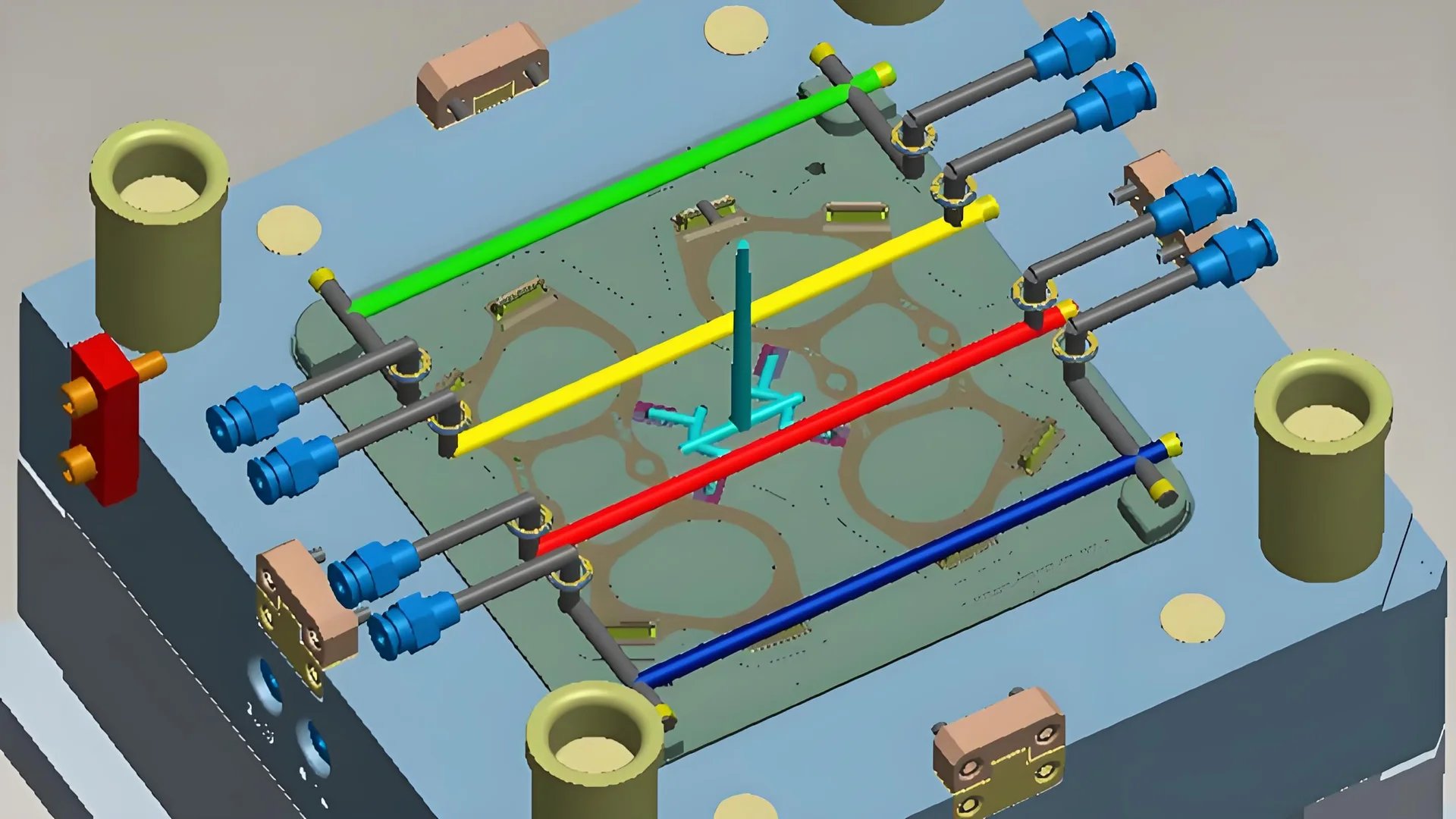
Understanding Connection Methods
The connection methods in cooling systems greatly affect reliability. It’s not just about appearance or ease of installation. It’s really about performance under pressure.
Welding vs. Pipe Joint Connections
Connection Method | Advantages | Disadvantages |
---|---|---|
Welding | Strong and durable | Difficult maintenance |
Pipe Joint | Easy to install and maintain | May not be as strong as welding |
I once chose welding connections for a project. They were incredibly strong. But during maintenance, I wished for pipe joints instead. Pipe joints are excellent for disassembly, especially in industrial places where regular maintenance is important. Selecting the correct connection method probably saves you from future problems.
Importance of Sealing Design
Sealing design is the unsung hero of cooling systems. Good sealing design prevents leaks, avoiding inefficiencies and expensive repairs.
Key Factors in Sealing Material Selection
- Temperature Resistance: The material must handle the heat.
- Corrosion Resistance: It should resist chemicals.
- Performance Longevity: Seals should last long!
For example, I once selected rubber seals for pipe joints. This choice improved our cooling efficiency, preventing leaks and potential overheating disasters. It’s amazing how one choice impacts system reliability.
Designing for Flow Efficiency
Flow efficiency is another very important aspect linked to connection and sealing designs.
Flow Rate Control
Flow Rate (m/s) | Effect on Cooling |
---|---|
< 0.5 | Poor cooling efficiency |
0.5 – 1.5 | Optimal cooling efficiency |
> 2 | Increased energy costs |
In my experience, finding the right flow rate balance is essential. Too slow and cooling is poor. Too fast and energy costs increase! I usually target a flow rate between 0.5 to 1.5 m/s for optimal performance.
Case Studies and Applications
Real-world applications offer valuable lessons. For instance, in data center cooling solutions14, improper sealing caused severe water damage and unexpected downtime. It’s a clear reminder of why proper design is so important.
In contrast, projects with detailed focus on piping and sealing brought impressive cost savings and longer equipment life, such as those seen in industrial processes15 or HVAC systems16. Those successful moments make all the effort worth it.
Welding connections improve cooling system reliability.True
Welding connections provide strong structural integrity, enhancing the reliability of cooling systems. However, they complicate maintenance tasks due to their permanent nature.
Pipe joints are always stronger than welded connections.False
Pipe joint connections are easier to maintain but typically do not offer the same strength as welded connections, making this claim false.
Conclusion
Explore essential strategies for designing efficient injection mold cooling systems, focusing on cooling methods, layout planning, channel sizing, flow rate control, and sealing design.
-
Explore this link to understand how effective cooling impacts injection molding processes and product quality significantly. ↩
-
This resource will provide deeper insights into various cooling methods used in injection molding. ↩
-
Discover best practices for managing flow rates in injection molding’s cooling systems. ↩
-
This article covers essential connection and sealing designs to prevent leaks in cooling systems. ↩
-
Gain insights into how proper layout planning for cooling waterways can improve efficiency in injection molding. ↩
-
Explore this link to discover practical insights into cooling methods and their impact on mold performance, enhancing your design strategies. ↩
-
This resource offers advanced techniques for indirect cooling that can improve your mold designs significantly. ↩
-
Learn about effective layout designs for cooling waterways that ensure uniform temperature distribution across molds. ↩
-
Gain insights into calculating the optimal size for cooling channels to maximize heat transfer efficiency. ↩
-
Understand the importance of flow rate control in optimizing mold temperature and preventing overheating issues. ↩
-
Review sealing design strategies that prevent leaks in cooling systems and ensure durability. ↩
-
Explore how flow rates impact cooling efficiency and learn best practices for optimizing your systems. ↩
-
Find detailed guidelines on calculating necessary flow rates for your cooling applications. ↩
-
Explore best practices for connection and sealing designs to enhance cooling system reliability and performance. ↩
-
Learn how to select sealing materials that ensure effective cooling system operation without leaks. ↩
-
Find out how to calculate optimal flow rates in cooling systems for improved reliability. ↩